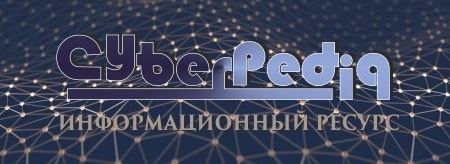
Своеобразие русской архитектуры: Основной материал – дерево – быстрота постройки, но недолговечность и необходимость деления...
Состав сооружений: решетки и песколовки: Решетки – это первое устройство в схеме очистных сооружений. Они представляют...
Топ:
Оценка эффективности инструментов коммуникационной политики: Внешние коммуникации - обмен информацией между организацией и её внешней средой...
История развития методов оптимизации: теорема Куна-Таккера, метод Лагранжа, роль выпуклости в оптимизации...
Интересное:
Наиболее распространенные виды рака: Раковая опухоль — это самостоятельное новообразование, которое может возникнуть и от повышенного давления...
Инженерная защита территорий, зданий и сооружений от опасных геологических процессов: Изучение оползневых явлений, оценка устойчивости склонов и проектирование противооползневых сооружений — актуальнейшие задачи, стоящие перед отечественными...
Принципы управления денежными потоками: одним из методов контроля за состоянием денежной наличности является...
Дисциплины:
![]() |
![]() |
5.00
из
|
Заказать работу |
|
|
НЕРАЗРУШАЮЩЕГО КОНТРОЛЯ
3.1. В результате проведения обследования ТПО ГРС получают информацию о фактических значениях основных влияющих факторов на техническое состояние ТПО ГРС, о состоянии изоляционного покрытия, о наличии повреждений и дефектов, выясняют причины возникновения и развития дефектов (если таковые имеются).
3.2. Обследование проводят по “Типовой программе работ по комплексному диагностическому обследованию технического состояния ТПО ГРС” (см. Приложение Б).
3.3. При проведении обследования ТПО ГРС используют следующие виды контроля:
- визуальный и измерительный контроль [26];
- ультразвуковую толщинометрию [31, 32, 84];
- ультразвуковую дефектоскопию [33 – 36, 88];
- твердометрию [54 - 61];
- магнитную структуроскопию [82];
- вибродиагностический контроль [10, 24-25];
- контроль деформации труб надземной части обвязки [22 – 23, 85-86];
- контроль состояния и выявление мест повреждения изоляции подземных трубопроводов путем проведения электрометрических измерений в соответствии с [16 - 20, 74, 79] на территории и за территорией промплощадки ГРС до охранного крана;
Дополнительно при необходимости могут применяться:
- радиографический контроль [37, 38, 88];
- капиллярная дефектоскопия [41 - 42, 45 - 47];
- ферромагнитный контроль [43, 90];
- метод магнитной памяти металлов [87];
- метод акустической эмиссии [39-40, 89];
- акустическое течеискание;
- другие методы, позволяющие уточнить тип дефекта и его геометрические размеры.
3.4. Неразрушающий контроль проводят с целью обнаружения поверхностных и внутренних дефектов в элементах надземных и подземных трубопроводов.
Ультразвуковой контроль (УЗК) является основным дефектоскопическим методом контроля. Радиографический контроль применяют при необходимости для расшифровки результатов, полученных при ультразвуковом контроле в случае их неоднозначного толкования.
|
3.4.1. Визуальный и измерительный контроль 100% трубопроводов, соединительных деталей, запорной арматуры и опор ТПО проводят с целью выявления несоответствия элементов ТПО требованиям нормативным документам, обнаружения видимых дефектов, возникших в процессе эксплуатации, проведении строительно-монтажных и ремонтных работ, утечек газа, также сбора сведений, позволяющих повысить достоверность и информативность результатов диагностирования ТПО ГРС.
3.4.1.1. На элементах ТПО и запорной арматуре выявляют наличие поверхностных трещин, коррозионных повреждений, отступлений от размеров и формы швов, механических повреждений, подбоев, вмятин, гофр (волнистости), овальности и других изменений геометрии.
3.4.1.2. При осмотре опор ТПО ГРС фиксируют трещины и разрушения опорных конструкций, наличие контакта между опорой и трубопроводом, перекос опорных поверхностей, смещение оси трубопровода относительно центра опоры, наличие и качество вставок, используемых для устранения зазоров.
3.4.1.3. Визуальный контроль состояния наружной поверхности трубопроводов проводят после снятия изоляции с надземных (при ее наличии) и подземных (в шурфах) трубопроводов ГРС. Особое внимание уделяют потенциально опасным участкам и швам приварки сложно нагруженных элементов ТПО ГРС.
При проведении визуального и измерительного контроля (ВИК) используют следующие инструменты: лупа ЛИ-3 - 10х, лупа ЛТ-1 - 4х, шаблон сварщика универсальный, глубиномер ГОСТ 7661-67, штангенциркуль (0 – 125 мм), (0 – 250 мм), рулетка металлическая (500 – 1000 мм). После проведения ВИК заполняется соответствующий формуляр.
3.4.1.4. Контроль геометрических размеров и формы основных элементов трубопроводов проводят с целью получения информации об их изменении по отношению к первоначальным (проектным) геометрическим размерам и форме, при этом контролируют:
|
- овальность цилиндрических элементов путем измерения максимального (Dmax) и минимального (Dmin) наружного диаметров в двух взаимно перпендикулярных направлениях контрольного сечения, а величину овальности в процентах (a) рассчитывают по формуле
;
- общую кривизну участка трубопровода определяют по результатам геодезической съемки или с помощью призм и лески, а местную - путем измерения зазора между поверхностью трубы и приложенной в этом месте линейкой;
В случае обнаружения вмятин в стенках элементов трубопровода измеряют максимальные размеры вмятины (или выпучины) по поверхности элемента в двух (продольном и поперечном) взаимно перпендикулярных направлениях (c) и (d), максимальную ее глубину (прогиб f), при этом глубину вмятины (выпучины) отсчитывают от образующей (или направляющей) недеформированной части элемента и по выполненным измерениям определяют относительный прогиб в процентах
=
х100%,
=
х100%
Допустимые значения овальности и относительных прогибов приведены в таб. 3.
3.4.2. Ультразвуковая толщинометрия
Целью проведения ультразвуковой толщинометрии является определение фактической толщины стенки элементов ТПО.
3.4.2.1. Измерение толщины стенок элементов ТПО проводят в околошовных зонах (зонах зачистки) 100%, на отводах 100% в соответствии с картой измерения толщины (формуляр №5а) и за ними на расстоянии 2 – 3 Ø трубопровода (за сечением 2), в среднем сечении трубопровода между сварными соединениями, а также на нижней поверхности трубопроводов в точках максимального прогиба, где наиболее вероятно скопление водяного конденсата и эрозионное изменение толщины.
3.4.2.2. При обнаружении в отдельной точке измерения значительного отклонения фактической толщины от расчетной производят сканирование вокруг этой точки с целью определения конфигурации и размеров зоны уменьшенной толщины.
Положение этой зоны фиксируется с помощью краски для последующего контроля толщины в процессе эксплуатации.
3.4.2.3. В случае обнаружения расслоения (не точечного характера) определяют его границы и фиксируют на поверхности элемента трубопровода с помощью краски или мела.
3.4.2.4. При проведении измерений допускается использовать УЗ толщиномер любого типа, обеспечивающий погрешность измерения толщины не хуже 0,1 мм в диапазоне толщин 2-30 мм и возможность измерения толщины при кривизне поверхности не более 20 мм.
|
Перед проведение измерений очистить поверхность площадью не менее величины площади рабочей поверхности преобразователя от различных загрязнений, рыхлой ржавчины, краски и нанести на место контроля достаточное количество акустической смазки.
3.4.2.5. Провести измерение толщины стенки объекта контроля, установив преобразователь в соответствующую зону измерения. Ось преобразователя должна быть перпендикулярна поверхности контроля или перпендикулярна касательной в точке контроля. В одной зоне измерения необходимо провести не менее трех замеров.
3.4.2.6. Измерение толщины стенок элементов ТПО проводят на всех элементах ТПО. Расчетная величина толщины стенки трубопровода определяется [50] по формуле:
δрасч= npDн./2(R1+np) (1)
Расчетная величина толщины стенки отвода трубопровода определяется [32] по формуле:
δрасч.отв =[ npDн./2(R1+np)] . ηв (2)
Допустимая величина толщины стенки отвода на выпуклой стороне определяется [32] по формуле:
δдоп.отв.= [ npDн./2(R1+np)] . χ (3)
δn-Δδ
Для отводов малых диаметров при рабочем давлении до 7.4 МПа допустимые толщины стенок приведены в [84].
Расчетная толщина основной трубы тройника δм определяется [50] по формуле
δм =[ npDн./2(R1+np)] . ηв.т. (4)
Расчетная толщина стенки ответвления тройника δо определяется [50] по формуле
δо= δм (R1м/R1o)D0/Dм (5)
Расчетная толщина стенки переходника определяется по формуле 2, по большему диаметру, так как для конических переходников с углом наклона образующей меньше 120 коэффициент несущей способности . ηв =1.
При расчетах толщины стенок элементов ТПО ГРС следует принимать значения коэффициентов: n=1,1; m=0,6; k1=1,55; kн=1,0; ηв=1,15; χ =0,9, ηв.т =1,6.
В формулах 1-5:
n - коэффициент надежности по нагрузке (внутренне давление для газопровода);
P – рабочее давление в Мпа;
Dн – наружный диаметр трубопровода (мм);
ηв – коэффициент несущей способности отвода;
χ - коэффициент несущей способности для выпуклой стороны отвода;
δn- номинальная толщина стенки отвода;
|
Δδ- установленный нормативными документами минусовой допуск на выпуклой стороне отвода от номинальной толщины стенки.
R1- расчетное сопротивление материала, где
R1= R1н.m/(k1 . kн) (6)
R1н- нормативное сопротивление растяжению в МПа, принимаемое равным минимальному значению временного сопротивления материала σв;
m- коэффициент условия работы трубопровода;
k1- коэффициент надежности по материалу;
kн- коэффициент надежности трубопровода по назначению
ηв.т – коэффициент несущей способности тройника зависит от типа тройника (без усиления, штампованные и штампосварные, с усилением), рекомендуемое Приложение [50].
R1м - расчетное сопротивление материала основной трубы тройника.
R1о – расчетное сопротивление материала ответвления тройника.
Do - диаметр трубы ответвления тройника.
Dм - диаметр основной трубы тройника.
Результаты расчетов толщины стенки трубопроводов (катушек), отводов, тройников и переходов в зависимости от их диаметров, материалов, для давления 6,4 МПА, выполненных по формулам 1-5 [50,32] с учетом [84] для отводов малого диаметра, приведены в таблице 1, где S – толщина стенки.
Таблица 1.
Допустимые толщины стенок элементов ТПО
Дмм | материал | Sкатушки | Sотв.на вогн.пов.(расчетная тощина) | Sотв.на вып.пов.Минимально допустимая толщина | Sтр.М. Осн труба. | Sтр.О.доп. ответвление | Переходник |
1 | 2 | 3 | 4 | 5 | 6 | 7 | 8 |
57 | ст.20 | 3 | 3 | 2.7 | 3 | 3 | 3 |
57 | ст.10 | 3 | 3 | 2.7 | 3 | 3 | 3 |
76 | ст.20 | 3 | 3 | 2.9 | 3 | 3 | 3 |
76 | ст.10 | 3 | 3 | 2.9 | 3 | 3 | 3 |
89 | ст.20 | 3 | 3 | 3 | 3 | 3 | 3 |
89 | ст.10 | 3 | 3 | 3 | 3.5 | 3 | 3 |
108 | ст.20 | 3 | 3 | 3.2 | 4,2 | 4 | 3 |
108 | ст.10 | 3 | 3 | 3.2 | 4.2 | 4.0 | 3 |
114 | ст.20 | 3 | 3 | 3.3 | 4,4 | 3,8 | 3 |
114 | ст.10 | 3 | 3.2 | 3.3 | 4.5 | 3.8 | 3 |
133 | ст.20 | 3 | 4 | 3.7 | 5,1 | 4,3 | 3 |
133 | ст.10 | 3.3 | 3.7 | 3.7 | 5.2 | 4.4 | 3.3 |
159 | ст.20 | 3,3 | 4 | 4 | 5,4 | 3,9 | 3,3 |
219 | ст.20 | 4,6 | 5,3 | 4,2 | 7,4 | 3,8 | 4,6 |
325 | ст.20 | 6,8 | 7,9 | 6,2 | 10,5 | 5 | 6,8 |
426 | ст.20 | 8,9 | 10,3 | 8,1 | 14,3 | 7,8 | 8,9 |
530 | 09Г2С | 9,5 | 11 | 8,6 | 15,3 | 12,8 | 9,5 |
530 | 17Г1С | 9 | 10,4 | 8,1 | 14,4 | 12,1 | 9 |
630 | 09Г2С | 11,4 | 13 | 10,2 | 18,2 | 15,9 | 11,4 |
630 | 17Г1С | 10,7 | 12,3 | 9,7 | 17,1 | 15 | 10,7 |
720 | О9Г2С | 13 | 14,9 | 11,7 | 20,2 | 17,7 | 13 |
720 | 17Г1С | 12,3 | 14,1 | 11 | 19,4 | 17,2 | 12,3 |
820 | О9Г2С | 14,8 | 17 | 13,3 | 23,6 | 19 | 14,8 |
820 | 17Г1С | 14 | 16 | 12,6 | 22,3 | 18 | 14 |
1020 | О9Г2С | 18,4 | 21 | 16,5 | 29,4 | 24,6 | 18,4 |
1020 | 17Г1С | 17,4 | 20 | 15,6 | 27,7 | 23,2 | 17,4 |
Расчеты выполнены при следующих значениях коэффициентов:
n=1,1; m=0,6; k1=1,55; kн=1,0; ηв=1,15; χ =0,9, ηв.т =1,6 при Р=6,4 МПа.
Если измеренная толщина стенки отвода превышает расчетную, то контроль толщины следует проводить по программам, разработанным в эксплуатирующей организации (ГТО), но не реже 1 раза в 2 года в зависимости от скорости эрозии [4].
Если минимальная измеренная толщина стенки отвода меньше расчетной, но больше минимально допустимой, то в этих зонах необходимо провести замеры НВ (твердость) и Нс (коэрцитивная сила) для подтверждения физико-механических параметров объекта контроля при расчете на прочность.
|
Если по результатам оперативной диагностики марка стали документально не установлена, то материал считать как Ст20, а для трубопроводов и отводов с Ду больше 500мм материал считать как сталь 09Г2С или 17Г1С.
Если измеренные значения НВ и Нс соответствуют допустимым значениям для этих марок сталей соответствующего элемента ТПО, то измерение толщины стенок этих элементов необходимо проводить каждые 6 месяцев. При несоответствии НВ и Нс для данной марки стали решение о дальнейшей эксплуатации принимается совместно с проектным институтом.
Если измеренная толщина стенки элемента ТПО ГРС меньше минимально допустимой, то дальнейшая эксплуатация элемента при нормативном давлении не допускается, а дефектный участок следует заменить.
В случае отсутствия возможности быстрой замены дефектного участка решение вопроса о временной эксплуатации на пониженном давлении должен принимать проектный институт совместно со специализированными организациями [32]. При этом допускаемое давление рассчитывается по формуле.
(7)
где χ =0,9 для отвода и 1,0 для катушки
3.4.3. Контроль сварных соединений
3.4.3.1. Визуально-измерительный контроль
Внешнему осмотру и измерениям подлежат 100% сварных соединений на предмет выявления в них:
- поверхностных трещин;
- коррозии элементов ТПО;
- наплывов, подрезов, прожогов, незаваренных кратеров, свищей, пористости и других технологических дефектов;
- излома осей соединяемых элементов;
- овальности цилиндрических элементов;
- овальности, наведенной путем подбивки кромок в процессе сварки;
- смещения кромок соединяемых элементов;
- отступлений от геометрических размеров швов, предусмотренных НД и чертежами (по высоте, ширине, равномерности усиления и т. д.).
Осмотр и измерение (при необходимости) сварных соединений производят по всей протяженности швов.
При проведении визуального и измерительного контроля (ВИК) используют следующие инструменты: лупа ЛИ-3 - 10х, лупа ЛТ-1 - 4х, шаблон сварщика универсальный, глубиномер ГОСТ 7661-67, штангенциркуль (0 – 125 мм), (0 – 250 мм), рулетка металлическая (500 – 1000 мм). После проведения ВИК заполняется соответствующий формуляр. Контроль проводят аттестованные специалисты по визуально-измерительному контролю.
3.4.3.2. Ультразвуковой контроль
Ультразвуковой контроль сварных соединений проводят с целью выявления внутренних и наружных дефектов типа трещин, непроваров, пор, шлаковых включений в сварных швах. Ультразвуковой контроль сварных соединений является основным методом проверки сварных соединений.
Объем ультразвукового контроля сварных соединений - 100%.
3.4.3.2.1. Оценка качества сварных соединений
Оценку выявленных дефектов при проведении УЗК сварных соединений проводить в соответствии со стандартом ОАО «Газпром» «По неразрушающим методам контроля качества сварных соединений при строительстве, реконструкции и ремонте магистральных газопроводов и конденсатопроводов» [88]. До ввода в действие стандарта «По неразрушающим методам контроля сварных соединений…» допускается проводить оценку дефектов с учетом их опасности по ВСН 012-88.
3.4.3.2.2. Для проведения УЗ контроля могут использоваться отечественные и зарубежные УЗ дефектоскопы, предназначенные для УЗ дефектоскопии металлов и сварных швов с чувствительностью, обеспечивающей выявление искусственных дефектов в стандартных образцах предприятия (СОПах), табл. 2 [48].
В комплект аппаратуры для проведения УЗК входят:
- УЗ дефектоскоп, СО-1, СО-2, СО-3,
- СОПы на все диапазоны толщин,
- УЗ преобразователи (см. табл. 2).
Допускается применение специализированных УЗ дефектоскопов (в том числе и с автоматической регистрацией результатов контроля) для УЗК кольцевых сварных швов.
3.4.3.2.3. Порядок проведения ультразвуковой дефектоскопии
Разметить краской или мелом зоны контроля сварных швов технологических элементов ГРС. Удалить с поверхности объекта контроля в зонах сварных швов грязь, защитное покрытие, ржавчину. Размер зоны зачистки для соответствующего типа шва указан в таблице 2.
Зачистить поверхность объекта в зоне контроля сварного шва с помощью шлифовальной машинки, напильника или наждачной бумаги до состояния, обеспечивающего проведение ультразвукового дефектоскопического контроля.
Нанести на поверхность объекта в зоне контроля сварного шва контактную смазку.
Подготовку и настройку ультразвукового дефектоскопа к работе провести согласно требованиям инструкции по эксплуатации прибора в соответствии с типом и параметрами контролируемого сварного шва.
Выбрать из комплекта дефектоскопа соответствующий ультразвуковой преобразователь (см. Таблицу 2).
Настроить дефектоскоп на соответствующий СОП, надежно выявляя дефект.
Параметры ультразвукового контроля стыковых сварных соединений выбрать согласно таблице 2.
Перед началом контроля на поверхности контролируемого объекта необходимо нанести зону перемещения преобразователя (мелом, карандашом).
Контроль сварных швов выполнять, устанавливая преобразователь перпендикулярно сварному шву и плавно перемещая вдоль шва, совершая поперечно-продольное сканирование с поворотом преобразователя на угол 20-30 градусов относительно оси, нормальной к опорной поверхности.
Таблица 2.
Параметры ультразвукового контроля стыковых сварных соединений.
Толщина сваренных элементов, мм | Угол наклона акустической оси преобразователя, градус | Рабочая частота, МГц | Искусственный отражатель по ВСН 012-88 | Ширина зоны зачистки от шва, мм |
4,0-5,5 | 53,0 | 5,0 (4,0) | 2 х 0,8 | 55,0 |
6,0-7,5 | 53,0 | 5,0 (4,0) | 2 х 1,0 | 70,0 |
8,0 | 53,0 | 5,0 (4,0) (2,5) | 2 х 1,5 | 65,0 |
10,0 | 53,0 | 5,0 (4,0) (2,5) | 2 х 1,5 | 75,0 |
12,0 | 53,0 | 5,0 (4,0) (2,5) | 2 х 2,0 | 85,0 |
14,0 | 50,0 | 2,5 | 2 х 2,0 | 95,0 |
16,0 | 50,0 | 2,5 | 2,5 х 2,0 | 110,0 |
18,0 | 50,0 | 2,5 | 2,5х 2,0 | 120,0 |
20,0 | 50,0 | 2,5 | 3 х 2,0 | 105,0 |
22,0 | 50,0 | 2,5 | 3 х 2,0 | 115,0 |
26,0 | 50,0 | 2,5 | 3 х 2,5 | 125,0 |
28,0 | 50,0 | 2,5 | 3 х 2,5 | 140,0 |
32,0 | 50,0 | 2,5 | 3 х 2,5 | 160,0 |
36,0 | 50,0; 40,0 | 2,5 | 3 х 2,5 | 175,0 |
40,0 | 50,0; 40,0 | 2,5 | 3 х 2,5 | 190,0 |
3.4.3.4. Радиографический контроль
Радиографический контроль применяют при необходимости для расшифровки результатов, полученных при УЗК сварных соединений в случае их неоднозначного толкования.
3.4.4. Измерение твердости и коэрцитивной силы
3.4.4.1. Измерение твердости по Бринеллю (НВ) проводят:
- во вмятинах, 100%;
- подбивках – 100%.
- на отводах –100%
При проведении измерений твердости применяются твердомеры, обеспечивающие измерение твердости по шкале Бринелля в диапазоне 100-450 НВ, а также меры твердости типа МТБ и МТР Погрешность твердомера при поверке на мерах твердости МТБ ГОСТ 90-31-78 не хуже 3% (например ТЭМП-3).
Для проведения измерений твердости подготовить поверхность в зоне измерения диаметром не менее 20мм, предварительно удалив посторонние загрязнения, ржавчину, смазку, окисную пленку и краску. Протереть зачищенную поверхность ветошью. Подготовить твердомер и провести измерения в соотвествии с требованиями инструкциями по эксплуатации.
В каждой зоне сделать по три измерения, выдерживая между точками измерений расстояние не менее 3 мм.
3.4.4.2. При измерении величины Нс применяются коэрцитиметры, обеспечивающие измерение коэрцитивной силы в диапазоне 1-60 А/см с погрешностью измерения величины Нс не более 5% (например КРМ-Ц).
Для проведения измерений установить преобразователь прибора вдоль образующей цилиндрической поверхности трубопровода. Выполнить подготовительные операции и провести измерения Нс в соответствии с требованиями инструкции по эксплуатации.
3.4.5. Вибрационный контроль проводят с целью определения параметров вибраций. Причиной появления повышенных вибраций может стать:
- увеличение потребления газа и связанное с этим увеличение скорости течения газа после регуляторов давления и пульсации давления, вызванные этим явлением;
- неравномерность регулирования расхода газа задвижками и кранами (характерно для линий дополнительного потребления газа и обводных линий);
- наличие местных геометрических неоднородностей (тупики, регулирующая арматура, тройники, отводы и т.д.);
- отсутствие контакта между газопроводом и опорой.
Оценку уровня вибрации производят путем измерения среднеквадратичных значений виброскорости (Vскз) и виброперемещений в контрольных точках трубопроводов.
При этом следует провести замер виброперемещений (S), что позволит определить приведенную виброчастоту fпр, где fпр= 0,22 Vскз/S
Места измерения (контрольные точки) назначают в местах наибольшей вибрации между опорами в вертикальном, горизонтальном и осевом направлениях. Допустимый уровень вибрации зависит от параметров трубопровода и частот вибрации [10,24,25]. В случае, если значение Vскз превышает допустимую величину, проводят расширенные вибрационные исследования.
Для измерения уровня вибрации применяются виброметры обеспечивающие измерение виброскорости от 0.1 до 70мм/с и виброперемещение в диапазоне от 1 до 700мкм. Частотный диапазон при измерении виброскорости и виброперемещений 10-1500 Гц и 10-300 Гц соответственно (например метрологически аттестованный виброметр ВК-5).
Для проведения измерений отметить на объекте место крепления датчика. Поверхность должна быть ровной без выступов и раковин. Удалить на площади 3х3 см2 слой краски, ржавчину и прочие загрязнения. Установить датчик с магнитным держателем в отмеченном месте. Подготовить виброметр к работе и провести измерения виброскорости в соответствии с требованиями инструкции по эксплуатации.
Оценка уровня вибрации производится в соответствии с зависимостями, приведенными на рис. 1.
При значениях Vскз > 18 мм/c на частотах вибрации более 60 Гц полученные данные, режимы работы, массово-инерционные и геометрические характеристики трубопровода следует направить в специализированную организацию для оценки усталостных повреждений при вибрационном нагружении и допуске трубопровода в эксплуатацию.
3.4.6. Контроль деформаций надземной части ТПО проводят с целью оценки величины и определения места действия максимальных статических изгибных напряжений от действия просадок (выпучиваний) опор и (или) подземных коллекторов.
Места деформаций ТПО ГРС устанавливают при проведении визуально – измерительного контроля.
На рис. 2,3,4 приведены графики зависимости изгибных напряжений от диаметра трубопровода и расстояния между опорами при действии инерционных (весовых) нагрузок (Рис.2), при выпучивании опор для шарнирно опертого трубопровода (Рис.3) и при выпучивании трубопровода при его консольном закреплении (Рис.4) (Приложение 1).
Расчетные соотношения, на основании которых построены вышеприведенные графики, даны в [85, 86].
Измерении величины прогибов при изгибных деформациях элементов ТПО проводят при помощи струны (лески диаметром 1-2мм), туго натянутой между точками перегибов трубопровода, и измерительной линейки. Величину прогиба определяют как максимальное смещение верхней или боковой образующей трубопровода от уровня струны.
Рис. 1 Оценка уровня вибраций
3.4.7. Контроль электрических параметров установки катодной защиты проводят с целью определения эффективности катодной защиты путем оценки:
- степени защищенности трубопроводов ГРС на период обследования;
- влияния на катодную защиту трубопроводов ГРС параллельных или пересекающих трассу трубопроводов ЛЭП (ВЛ – 10...220 кВ);
- взаимного влияния нескольких близко расположенных катодно-защищаемых трубопроводов с точки зрения распределения в них защитных токов (определение фактического распределения токов в системе трубопроводов – вариант совместной защиты);
- состояния изолирующих фланцев.
3.4.7.1. Для оценки степени защищённости трубопроводов выполняют работы по:
- изучению устройства и расположения заземления;
- уточнению с помощью приборов расположения подземных трубопроводов (приступают после ознакомления с исполнительной план-схемой укладки подземных трубопроводов на промплощадке и в охранной зоне ГРС);
- уточнению на план-схеме ТПО положения изолирующих фланцев;
- разметке трассы подземных трубопроводов "вешками";
- разметке непосредственно на поверхности земли зон для проведения электрометрических измерений (при наличии на территории ГРС асфальтового покрытия в этих зонах проделывают отверстия);
- наладке электрического контакта измерительной аппаратуры с трубопроводом в местах отсутствия КИП;
- измерению удельного электрического сопротивления грунта;
- измерению сопротивлений анодного заземления Rаз, контура защитного заземления, корпуса системы катодной защиты (СКЗ), дренажного кабеля, цепи установки катодной защиты (УКЗ);
- измерению защитного и поляризационного потенциалов в намеченных точках (в том числе в точке дренажа) методом выносного электрода с шагом (1 – 3) м;
- измерению градиентов потенциалов (воронок напряжений) в грунте при включенной и выключенной защите;
- измерению средних значений смещений защитных потенциалов трубопровода ГРС, вызванных воздействием переменного тока.
3.4.7.2.Контроль состояния и выявление мест повреждения изоляции проводят с целью оценки степени повреждения изоляционного покрытия на подземных трубопроводах в целом и на отдельных участках путем:
- определения обобщенных сравнительных характеристик состояния изоляции участков ТПО;
- определения мест повреждения покрытия;
- шурфовки трубопровода в местах повреждения изоляции;
- исследования состояния изоляции и масштабов её повреждения в шурфах.
3.4.7.3. Определение обобщённых сравнительных характеристик и мест повреждения изоляционного покрытия ТПО производят по:
- характеру изменения и величинам защитного и поляризационного потенциалов Uт-з, Uт-з.пол вдоль трубопровода при включенных и отключенных средствах электро - химзащиты (ЭХЗ);
- значениям и распределению продольных и поперечных градиентов напряжения от уравновешивающих токов между дефектами изоляции;
- значениям и распределению удельного электрического сопротивления грунта вдоль трубопровода;
- смещению среднего значения разности потенциалов между трубопроводом и электродом сравнения, вызванному действием переменного тока;
- времени деполяризации трубопровода (после отключения от СКЗ);
- результатам обследования изоляции с помощью “искателя повреждений”.
По обобщенным сравнительным характеристикам производят предварительную оценку состояния изоляционного покрытия трубопроводов.
3.4.7.4. Непосредственную оценку состояния изоляционного покрытия производят по результатам обследования трубопроводов в шурфах. Контрольные шурфы выполняют в местах повреждения изоляционного покрытия и в местах переходов «земля-воздух».
3.4.8. Для выявления дефектов в качестве дополнительных методов, при необходимости, могут быть использованы: радиографический, капиллярный, феррозондовый методы, метод магнитной памяти металлов (ММПМ), акустические методы - акустическая эмиссия (АЭ) и ультразвуковой голографический автоматизированный контроль, акустическое течеискание и другие по специально разработанным методикам.
3.4.9. Контроль методом проникающих веществ (методом цветной дефектоскопии (ЦД) применяют для контроля поверхностных дефектов сварных швов и в околошовных зонах в неконтролепригодных для УЗК соединениях.
3.4.10. Феррозондовую дефектоскопию применяют для контроля поверхностных и подповерхностных дефектов сварных швов и околошовных зонах в неконтролепригодных для УЗК соединениях без удаления защитных покрытий (вмятин, подбоев, выборки мест трещин, коррозионных язв и других дефектов.
3.4.11. Объем контроля методами ЦД и феррозондовой дефектоскопии уточняют после проведения оперативной диагностики, визуального и измерительного контроля, ультразвукового контроля сварных соединений.
3.4.12. ММПМ может быть применен для обнаружения на контролируемой поверхности, например в зонах сварных соединений ТПО ГРС, зоны концентрации напряжений с целью последующего контроля этих зон методами НК. В качестве средства контроля может быть использован прибор определения концентрации напряжений типа ИКН-1М аттестованный Госстандартом РФ.
3.4.13. Метод АЭ – контроля позволяет обнаруживать и регистрировать развивающиеся дефекты. Контроль методом АЭ проводят в соответствии с [40, 89].
3.4.14. Определение мест утечек газа на ГРС проводят с помощью акустического течеискателя.
Для этого может применяться течеискатель типа ТАМ –30-01 или аналогичный, имеющий следующие основные технические характеристики:
-сечение дефектного отверстия не менее 0.02мм
-избыточное давление внутри исследуемого объекта не менее 0.1 кГс./см2.
-частотный диапазон 38-45 кГц.
Порядок поиска утечек газа с помощью акустического течеискателя заключается в следующем.
Оператор - дефектоскопист двигается вдоль контролируемого трубопровода, надев головные телефоны и направив микрофон течеискателя в сторону трубопровода. Расстояние от трубопровода до течеискателя 1-2 м. При возникновении характерного шума оператор продолжает движение. Увеличение уровня шума свидетельствует о приближении к месту течи, уменьшение об удалении. Течи между фланцами и в запорной арматуре ищут с расстояния 5-10 см. Поворачивая прибор, фиксируется направление и место утечки газа по максимуму шумового сигнал.
Требования к объекту диагностирования
Поверхность трубопровода в местах контроля сварных швов, и прилегающих к ним участков шириной (таблица №2) по обе стороны от шва, должна быть зачищена с помощью шлифовальной машинки или вручную с помощью металлических щеток, скребков, напильников, абразивной шкурки. На контролируемой поверхности не допускается наличие окалины, следов коррозии, брызг металла от сварочных электродов, крупных неровностей и посторонних наслоений, препятствующих установлению устойчивого акустического контакта между искателем дефектоскопа (толщиномера) и металлом.
3.6. Общие требования к методам контроля и средствам измерения
Средства измерения (аппаратура и приборы), применяемые при проведении диагностирования ТПО ГРС, должны быть регламентированы для соответствующих методов контроля и должны пройти метрологическую аттестацию в соответствии с нормативно – технической документацией Госстандарта РФ.
Требования к предприятиям и специалистам, выполняющим диагностирование трубопроводов обвязки ГРС
3.7.1. Предприятия, осуществляющие техническое диагностирование ТПО ГРС должны иметь разрешение (лицензию) Госгортехнадзора РФ на указанный вид деятельности и необходимые для этого приборы, оборудование и штат аттестованных сотрудников.
3.7.2. Руководители и специалисты, выполняющие диагностические работы, обязаны пройти проверку знаний Правил, норм и инструкций по безопасности в соответствии с [9].
3.7.3. Специалисты, осуществляющие контроль толщины стенки трубопроводов, должны иметь 2 уровень квалификации по ультразвуковым методом контроля.
3.7.4. Специалисты, осуществляющие вибрационный контроль, должны иметь 2 уровень квалификации по методам контроля вибраций.
3.7.5. Специалисты, осуществляющие визуальный и измерительный контроль, а также контроль магнитными, ультразвуковыми, капиллярным, вихретоковым методами с выдачей заключения о качестве, должны иметь квалификацию не ниже II уровня по соответствующим методам контроля.
3.7.6. Специалисты, осуществляющие электрометрические измерения, должны иметь соответствующее удостоверение о том, что они прошли специальное обучение и сдали экзамен на допуск к указанным работам.
3.7.7. Специалисты, осуществляющие диагностирование ТПО ГРС, должны пройти специальное обучение в соответствии с требованиями нормативно-технической документации, норм и правил Госгортехнадзора РФ для специалистов неразрушающего контроля.
Требования к организации работ и охране труда
3.8.1. Для проведения технического диагностирования трубопроводов и обвязок оборудования ГРС организация, выполняющая диагностирование, создает бригаду. В с
|
|
Особенности сооружения опор в сложных условиях: Сооружение ВЛ в районах с суровыми климатическими и тяжелыми геологическими условиями...
Опора деревянной одностоечной и способы укрепление угловых опор: Опоры ВЛ - конструкции, предназначенные для поддерживания проводов на необходимой высоте над землей, водой...
Эмиссия газов от очистных сооружений канализации: В последние годы внимание мирового сообщества сосредоточено на экологических проблемах...
Индивидуальные очистные сооружения: К классу индивидуальных очистных сооружений относят сооружения, пропускная способность которых...
© cyberpedia.su 2017-2024 - Не является автором материалов. Исключительное право сохранено за автором текста.
Если вы не хотите, чтобы данный материал был у нас на сайте, перейдите по ссылке: Нарушение авторских прав. Мы поможем в написании вашей работы!