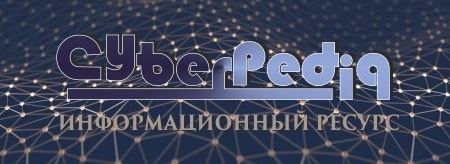
Историки об Елизавете Петровне: Елизавета попала между двумя встречными культурными течениями, воспитывалась среди новых европейских веяний и преданий...
Архитектура электронного правительства: Единая архитектура – это методологический подход при создании системы управления государства, который строится...
Топ:
Определение места расположения распределительного центра: Фирма реализует продукцию на рынках сбыта и имеет постоянных поставщиков в разных регионах. Увеличение объема продаж...
Характеристика АТП и сварочно-жестяницкого участка: Транспорт в настоящее время является одной из важнейших отраслей народного...
Методика измерений сопротивления растеканию тока анодного заземления: Анодный заземлитель (анод) – проводник, погруженный в электролитическую среду (грунт, раствор электролита) и подключенный к положительному...
Интересное:
Влияние предпринимательской среды на эффективное функционирование предприятия: Предпринимательская среда – это совокупность внешних и внутренних факторов, оказывающих влияние на функционирование фирмы...
Отражение на счетах бухгалтерского учета процесса приобретения: Процесс заготовления представляет систему экономических событий, включающих приобретение организацией у поставщиков сырья...
Инженерная защита территорий, зданий и сооружений от опасных геологических процессов: Изучение оползневых явлений, оценка устойчивости склонов и проектирование противооползневых сооружений — актуальнейшие задачи, стоящие перед отечественными...
Дисциплины:
![]() |
![]() |
5.00
из
|
Заказать работу |
|
|
Расчет поршневой группы. Его начинают с предварительного расчета блока цилиндров.
Рабочий объем аксиально-поршневой гидромашины с наклонным диском определяется по выражению:
, м3 (1)
где z – число поршней;
d п – диаметр поршня, (м);
D – диаметр окружности расположения осей цилиндров в блоке, (м);
b – угол наклона диска, (град).
Исходя из рекомендации ([1], c. 117) число поршней выбираем равным z =7.
Основными геометрическими параметрами блока цилиндров аксиально-поршневой гидромашины являются диаметр D окружности расположения осей цилиндров, наружный диаметр D нар блока цилиндров и диаметр d n поршней (цилиндров). При этом:
. (2)
. (3)
Угол наклона диска или блока цилиндров b задается конструктивно и находится в пределах 12…35 градусов, при этом в гидромашинах с наклонным диском угол b составляет 12-22 градусов. Принимаем угол b=17 .
Подставив соотношение (2) в формулу (1), получаем зависимость для определения диаметра блока цилиндров.
Диаметр цилиндров для аксиально-поршневой гидромашины с наклонным диском:
м, (4)
м.
Величина диаметра поршня гидромашины является стандартной, и ее значение устанавливает ГОСТ 12447-80. Согласно данному стандарту принимаем диаметр цилиндра d п=0,018 м.
м.; принимаю
м.
м.; принимаю
м.
м3.
Толщина стенки между цилиндрами в блоке:
м.; принимаю
м (5)
Толщина стенки между цилиндром и наружной поверхностью:
|
м.; принимаю
м. (6)
Рисунок 2 – Геометрические размеры блока цилиндров
Приблизительную длину блока цилиндра находят исходя из следующего соотношения:
, м. (7)
м; принимаю
м.
При проектировании блока цилиндров необходимо обеспечить заделку плунжера при крайнем выдвинутом его положении, чтобы устранить возможность смятия цилиндра под действием боковой силы и обеспечить герметичность соединения. Минимальная величина заделки L поршня в выдвинутом его положении должна быть не менее L > (1,5…2)∙ d.
В соответствии с этим длина цилиндра (глубина расточки в блоке цилиндров):
м, (8)
где h – ход поршня,
, м (9)
м; принимаю
м.
м.
Толщину дна цилиндра рекомендуют принять равной 0,3∙ d, следовательно, длина ротора (цилиндрового блока) составляет:
, м (10)
м.;
Общая длина поршня L п плунжерного типа должна быть такой, чтобы он в утопленном положении выступал из цилиндра на (0,1…0,2) d. В соответствии с этим длина поршня:
м.; (11)
м.
Принимаю м.
Рисунок 3– Эскиз блока цилиндров
Рисунок 4 – Расчётная схема блока цилиндра и плунжера
В случае поршня плунжерного типа диаметр сферической головки рассчитывается по следующей формуле:
м.; принимаю
м.
Размеры питающего окна блока цилиндров, через которые подводится и отводится рабочая жидкость, выбирают исходя из максимальной допустимой скорости потока в питающем окне. Скорость жидкости питающего окна не должна превышать более чем в 2,2-2,5 раза среднюю скорость поршня. Для насосов с подпиткой наибольшая скорость жидкости в окне не должна быть более 8 м/с, для самовсасывающих насосов – 2…4,5 м/с, для гидромоторов может достигать 10-12 м/с. Для расчета необходимо определить расход рабочей жидкости через гидромашину:
|
,м3/с (13)
где V 0 – объемная постоянная гидромашины, м3;
n – номинальная частота вращения вала гидромашины, (об/мин).
Площадь питающего окна равна:
м2 (14)
где Q т – расход рабочей жидкости без учета утечек, (м3/с);
uдоп – допустимая скорость жидкости, (м/с);
Принимаю м/с.
Питающие окна могут иметь круглую (а) или дугообразную (б) форму (рис. 5).
| |
а) | б) |
Рисунок 5 – Формы питающих окон блока цилиндра
В случае круглых окон (см. рисунок 1.6, а) их диаметр d 0 можно определить по формуле:
м. (16)
Принимаю м.
В случае проектирования торцового распределителя, диаметр окружности расположения центров питающих отверстий D рас может совпадать с диаметром D окружности расположения осей цилиндров, D = D рас или же быть меньше D > D рас, т. е. сверлится под некоторым углом.
Во втором случае D рас можно рассчитать по одной из формул:
м. (18)
Приступаем к расчету торцового распределителя.
В аксиально-поршневых ОГМ, как правило, преобладает применение торцевого распределения рабочей жидкости. Торцовый распределитель аксиально-поршневых гидромашин выполняется, как правило, в виде плоского или сферического диска. Поскольку цилиндровый блок у проектируемого насоса вращается, упрощается распределение жидкости, которое обычно выполняется через серпообразные окна в распределительном диске и каналы (отверстия) в донышке блока цилиндров.
При работе насоса торец цилиндрового блока скользит по поверхности распределительного диска. При этом цилиндры попеременно соединяются с окнами распределительного диска и через них – с магистралями всасывания и нагнетания.
Рисунок 6 – Пример внешнего вида плоского распределительного диска
Ширина перемычки между окнами обычно выбирается равной
м. (20)
где d к – диаметр (или большая ось, если отверстие не круглое) канала соединяющий блок цилиндров и распределительный диск.
Принимаю м.
Для обеспечения безударного перехода жидкости из полости всасывания в полость нагнетания и наоборот, в узле распределения выполняют дроссельные канавки, длина которых определяется углом j' = 8...10°, принимаю j' = 9°, ширина – 1...2 мм, принимаю ширину 1,5 мм.
|
Рисунок 7 – Схема к расчету торцового распределителя
Уточненный расчет параметров распределителя выполняют с учетом сил, действующих в стыковом зазоре. На блок цилиндров со стороны поршней направлено усилие, прижимающее блок к распределителю, со стороны распределителя усилие, отжимающее блок. Для нормальной работы распределителя необходимо, чтобы прижимающая сила была несколько больше отжимающей.
Для расчета размеров торцового распределителя необходимо решить систему уравнений:
, (22)
где l = 0,9…0,98 – коэффициент, показывающий соотношение отжимающей и прижимающей сил;
R 1, R 2, R 3, R 4 – размеры торцового распределителя.
Для определения размера R 4 воспользуемся дополнительными условиями:
м.; принимаю
м. (23)
м.; принимаю
м. (24)
Подставив выражения (23-25) в первое уравнение системы (22) и преобразовав, получаем биквадратное уравнение относительно R 4:
(26)
Решим данное уравнение относительно :
Примем
,
Примем м.
м.; принимаю
м. (25)
После определения R 1, R 2, R 3, R 4 и уточнения их в соответствии с рядом нормальных размеров, следует выполнить проверку коэффициента l:
(27)
Рисунок 8 – Схема к расчету углов перекрытия торцового распределителя
В торцовых (плоских) распределителях различают углы перекрытия j1и j2. Эти углы выбирают в основном из условия возможного устранения как чрезмерного разряжения, так и сжатия жидкости и обеспечения минимального перепада давления между полостью цилиндра и того окна распределителя, с которым цилиндр в текущий момент соединен.
При переходе из зоны всасывания в зону нагнетания жидкость предварительно сжимается на участке j1, что способствует устранению «заброса» давления в момент соединения запертой полости с полостью нагнетания, снижению шума, увеличению долговечности машины. Угол перекрытия j1, при котором будет достигнуто требуемое сжатие жидкости в цилиндре:
, (28)
|
где Е– модуль упругости жидкости;
Жидкость- минеральное масло, Гпа.
S – площадь цилиндра; м2.
Rд= Dрас/2 = 0,03 м;
р вс– давление в зоне всасывания; МПа.
рн– давление в зоне нагнетания; МПа.
V– объем жидкости в цилиндре при j = 0 и р = р вс;
м3.
Принимаю
(29)
где V '– объем жидкости в цилиндре при j = 180° и давлении р н.
м3.
Принимаю
После завершения расчета торцового распределителя приступим к проектированию гидростатических подпятников. В аксиально-поршневых машинах используются как плоские гидростатические подпятники, так и гидравлическая разгрузка сферических опор (см. рисунок 2.8).
Рисунок 9 – Поршни двух видов с гидростатической разгрузкой:
а – плунжерного типа; б – шатунного типа.
В случае поршня плунжерного типа диаметр сферической головки рассчитывается по следующей формуле:
м.; принимаю
м.
Рисунок 10 – Сферические головки шатуна
Рассмотрим расчет плоского гидростатического подпятника поршня по рисунку 11.
Рисунок 11 – Эскиз плоского поршневого подпятника
Такая конструкция поршней применяется в гидромашинах бескарданного типа. Опорную поверхность подпятника можно выполнить двояко: с опорными поясками за пределами уплотнительных поясков, или без опорных поясков. В любом случае в упрощенную расчетную формулу входят размеры уплотнительных поясков. Размеры опорных поясков назначаются из конструктивных соображений, преследуя в основном цель обеспечения устойчивости против опрокидывания. Это условие записывается в виде выражения:
, (31)
где lп = 0,97…0,98 коэффициент превышения сил, прижимающих поршень над отжимающими силами.
Из практики проектирования, отношение R / R 0 = 1,2…1,7. Выбрав это отношение в рекомендуемых пределах, преобразуем (31) и получим соотношение для определения R 0:
м. (32)
Принимаем м.
Тогда м.
Рисунок 12 – Схемы гидростатической опоры
Гидростатическая разгрузка – это система, которая включает в себя разгружающую рабочую камеру башмака с (рисунок 12, а), дросселирующие щели между башмаком и опорным диском b, дросселирующие отверстие в плунжере а (выполняет роль регулятора системы). Геометрические формы деталей устройства, свойства рабочей жидкости, жесткость пружины и давление р определяют зависимость величины зазора и динамические особенности системы.
Расчет кольцевых опор производится, исходя из того, что в статических условиях опоры находятся в равновесии под действием следующих сил (давлением жидкости в корпусе насоса пренебрегаем):
а) усилия гидравлического прижима, противоположного реакции N, действующей перпендикулярно к плоскости наклонного диска (12, а):
|
H.(33)
где – сила давления р рабочей жидкости на площадь поршня диаметром
;
– угол наклона диска;
б)усилия пружины – 3 (рис. 12, б), приходящегося на одну опору:
H, (34)
где z – число поршней;
в) усилия отжима кольцевой опоры, возникающего в результате давления р жидкости на поверхности ее выточки
(рисунок 12, а) и среднего давления в зазоре опорного пояска. Усилие
определяется из условия, что в выточке опоры действует рабочее давление р, что обычно и соблюдается, так как утечка жидкости при правильно сконструированной кольцевой опоре пренебрежимо мала.
Практически можно принять, что в торцовом зазоре между кольцевой поверхностью опоры, ограниченной диаметрами и
и поверхностью наклонной шайбы, давление распределяется по линейному закону. Тогда усилие
будет численно равно объему усеченного конуса высотой р с диаметрами оснований
и
:
Для того чтобы максимально устранить утечки через торцовый зазор кольцевой опоры, принимается отношение площади поршня S к площади опорной поверхности S 0 равным , следовательно, площадь опорной поверхности равна:
м,
м2.
м2.
(35)
Принимаю
,
Принимаю м,
(36)
Па
В схеме разгруженного поршня (рисунок 12, а) одновременно осуществляется также и частичная разгрузка сферической головки поршня 2, за счет того, что рабочая жидкость одновременно подводится к камере е, образованной срезом части сферы. Усилие давления жидкости, подводимой в камеру е на площадь среза, а также давление жидкости, проникшей в зазор сферической пары, противодействуют усилию давления на торец поршня.
Фактором, ограничивающим возможность уменьшения площади опорно-уплотнительного пояска башмака, является допустимое смятие материала. С целью увеличения контактной площади поясков башмака при одновременном обеспечении требуемой разгрузки от силы давления жидкости, применяют башмаки, в которых на контактной поверхности выполняется дополнительная разгрузочная канавка b, соединенная радиальными прорезями (каналами) с со сливом (рисунок 12, б).
При конструировании разгрузочной гидростатической опоры поршня следует учитывать, что башмак нагружается опрокидывающим моментом, обусловленным силами трения его по наклонному диску. Этот момент стремится опрокинуть башмак в направлении движения (рисунок 12, в). Величина
зависит для данного коэффициента трения
от усилия R, которым башмак прижимается к диску. Величина усилия R определяется разностью сил (без учета трения поршня в цилиндре):
Н, (37)
где – нормальная составляющая (реакция опоры) силы давления жидкости на поршень (рисунок 12);
Н.
– усилие гидростатической разгрузки (грузоподъемность гидростатического подшипника).
Н.
Сила трения будет стремиться развернуть башмак относительно центра сферы поршня, расстояние h которое от поверхности скольжения является плечом приложения этой силы. В соответствии с этим опрокидывающий момент башмака определится по формуле:
Н∙м. (38)
Следовательно, при увеличении угла и высоты h положения центра, результирующая сил на скользящем башмаке может выйти за пределы опорной его поверхности, что приведет к опрокидыванию башмака. Для устранения этого стремятся понизить коэффициент трения
, а также уменьшают высоту h центра сферы и силу R и ограничивают величину угла наклона
значением 15 – 22°.
Рассмотрим расчет прижимного диска (см. рисунок 13). Радиус r определяется из треугольника O С O 1:
м. (39)
где – наружный диаметр кольцевой опоры;
s – расстояние между опорами(s =1,5-2,5 мм)
рад.
Диаметр окружности D ц (см. рисунок 14), на которой расположены центры отверстий под кольцевые опоры в прижимном диске, определяется по уравнению:
(40)
где – наибольший угол наклона (обычно не превышает
, (см рисунок 2.13)
м.
|
Рисунок 13 – Схемы гидростатической опоры
|
Рисунок 14 –Кинематическая схема насоса (гидромотора) с бесшатунным приводом и кольцевыми гидростатическими опорами
Диаметр отверстия в прижимном диске определяется по выражению (на рисунке 14 обозначено как ):
(41)
где d ш – диаметр шейки кольцевой опоры;
emax– наибольшее смещение центра кольцевой опоры относительно центра отверстия в прижимном диске:
(42)
dmin –минимальный зазор между отверстием в прижимном диске и шейкой кольцевой опоры (dmin = 0,5 - 1,5 мм).
м.
Принимаю м.
Наружный диаметр определяется по выражению (на рисунке 1.15 обозначено как ):
(43)
где – минимальное перекрытие отверстия в прижимном диске кольцевой опорой, обычно
= 1,5-2,5 мм.
м.
Принимаю м.
Наружный диаметр прижимного диска определяется по выражению:
(44)где
– минимальное расстояние от края кольцевой опоры до края прижимного диска, обычно
= 0,5-1,5 мм.
м.
Принимаю м.
Наружный диаметр D н.ш. наклонной шайбы (траверсы) можно принимать:
м. (45)
Диаметр отверстия d н.ш в наклонной шайбе определяется по выражению:
(46)
м.
где – минимальное расстояние от края кольцевой опоры, пересекающей меньшую ось эллиптической траектории, до края отверстия, обычно
= 0,5-1,5 мм.
Прочностной расчет блока цилиндров производится по методике расчета на прочность толстостенных труб с условным наружным диаметром d T:
(47)
(48)
Прочность блока цилиндров оценивается по нормальным напряжениям σ:
(49)
где p Hmax- максимальное давление в рабочей камере:
- для бронзовых блоков цилиндров из БрОФ 10-1 принимают p Hmax=25 МПа.
[σ] – критическое напряжение:
[σ]= 245 МПа - для бронзовых блоков цилиндров из БрОФ 10-1.
Жесткость блока цилиндров определяется по деформации их стенок δ в опасном сечении:
(50)
где Е- модуль упругости:
– для бронзы, меди и латуни Е =(1,0…1,3)·105 МПа;
μ - коэффициент Пуассона:
– для бронзы и медиμ = 0,31…0,35;
δ - деформация стенок в опасном сечении:
– 0,008 мм – бронза, медь, латунь.
м.
|
|
Биохимия спиртового брожения: Основу технологии получения пива составляет спиртовое брожение, - при котором сахар превращается...
Наброски и зарисовки растений, плодов, цветов: Освоить конструктивное построение структуры дерева через зарисовки отдельных деревьев, группы деревьев...
Поперечные профили набережных и береговой полосы: На городских территориях берегоукрепление проектируют с учетом технических и экономических требований, но особое значение придают эстетическим...
Особенности сооружения опор в сложных условиях: Сооружение ВЛ в районах с суровыми климатическими и тяжелыми геологическими условиями...
© cyberpedia.su 2017-2024 - Не является автором материалов. Исключительное право сохранено за автором текста.
Если вы не хотите, чтобы данный материал был у нас на сайте, перейдите по ссылке: Нарушение авторских прав. Мы поможем в написании вашей работы!