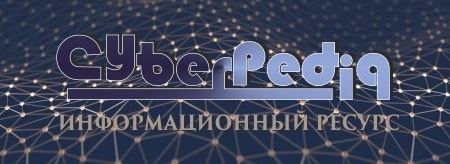
Своеобразие русской архитектуры: Основной материал – дерево – быстрота постройки, но недолговечность и необходимость деления...
Археология об основании Рима: Новые раскопки проясняют и такой острый дискуссионный вопрос, как дата самого возникновения Рима...
Топ:
Оценка эффективности инструментов коммуникационной политики: Внешние коммуникации - обмен информацией между организацией и её внешней средой...
Особенности труда и отдыха в условиях низких температур: К работам при низких температурах на открытом воздухе и в не отапливаемых помещениях допускаются лица не моложе 18 лет, прошедшие...
Выпускная квалификационная работа: Основная часть ВКР, как правило, состоит из двух-трех глав, каждая из которых, в свою очередь...
Интересное:
Влияние предпринимательской среды на эффективное функционирование предприятия: Предпринимательская среда – это совокупность внешних и внутренних факторов, оказывающих влияние на функционирование фирмы...
Берегоукрепление оползневых склонов: На прибрежных склонах основной причиной развития оползневых процессов является подмыв водами рек естественных склонов...
Аура как энергетическое поле: многослойную ауру человека можно представить себе подобным...
Дисциплины:
![]() |
![]() |
5.00
из
|
Заказать работу |
|
|
Резание металлов
Резание — как технологический способ обработки заключается в том, что с обрабатываемой заготовки срезается слой металла специально оставленный для обработки. Этот слой называется припуском. В ряде случаев припуск может быть достаточно большим, и он может сниматься (срезаться) за несколько проходов. В результате чего заготовка превращается в деталь.
Металл, срезаемый с заготовки, пластически деформируется, а затем отделяется от заготовки. Он приобретает определенную форму и размеры, и в таком виде его принято называть стружкой.
Пластическое деформирование и разрушение металлов в процессе резания протекают в особых условиях. Именно это и определяет специфику и закономерности, определяемые физикой этого процесса, которые могут быть отражены зависимостями (частными, в основном), отражающими процесс обработки резанием.
Краткие сведения об обрабатываемых и конструкционных материалах
Обрабатываемость материала резанием — это его способность подвергаться обработке резанием (как правило, на металлорежущих станках). Если в процессе обработки металл удаляется в виде стружки, то инструмент выполняющий эту операцию называется режущим.
Обрабатываемость материала резанием — совокупность свойств определяемая:
Химическим составом материала;
Структурным состоянием;
Механическими свойствами (упругость, пластичность);
Склонностью к образованию стружки;
Способностью сопротивляться резанью (косвенный признак);
Энергетическими затратами на резание;
Тепловыми процессами;
Теплопроводностью материала;
Истираемостью материала.
В настоящее время существует более 300 марок сталей (сплавов, как черных, так и цветных). Их по обрабатываемости подразделяют:
|
Легкие сплавы, как наиболее легко обрабатываемые резанием. Это сплавы на основе алюминия (различные латуни и бронзы);
Средне обрабатываемые стали и сплавы. К ним относятся, углеродистые стали типа: Сталь 20...Сталь 50, чугуны, легированные стали 40Х, 20Х, 20ХН и другие;
Трудно обрабатываемые. Это аустенитные стали, стали легированные хромом (13-20%), специальные сплавы с никелем (Ni) (30-70%), сплавы с ниобием.
Инструментальные материалы
При резании на контактных поверхностях режущего инструмента возникают давления (тысячи атмосфер) и одновременно выделяется много тепла (температура резания сотни, а иногда и тысячи градусов). Также в процессе обработки происходит скольжение и трение обрабатываемого материала по контактным поверхностям режущего инструмента. Поэтому материал режущего инструмента должен обладать свойствами, создающими ему работоспособность. Качество инструментального материала оценивается физико-механическими свойствами, зависящими от структурного состояния или химического состава.
Твердость режущего инструмента (РИ) колеблется в пределах от 62...64 единицы и измеряется, в основном, по шкале HRC, твердомером. При твердости HRC<62 существенно возрастает изнашиваемость лезвий режущего инструмента, а при HRC>64 лезвия выкрашиваются из-за излишней хрупкости. Твердые сплавы и минералокерамика имеют твердость близкую к твердости алмаза. Металлорежущим инструментом (МРИ) из инструментальной стали с твердостью 62...64 HRC обрабатывают, в основном, все конструкционные материалы с твердостью до 30...35 HRC. Наиболее распространенная твердость конструкционных материалов — 12...20 HRC.
Конструкционные материалы с твердостью выше 35...40 HRC обрабатывают твердыми сплавами, минералокерамикой или эльбором (кубический нитрит бора), а в особых случаях алмазами (синтетическими или натуральными).
Прочность. Силы резания, возникающие при работе режущего инструмента, вызывают в материале лезвия и корпуса напряжения сжатия, изгиба, а иногда и кручения. Для того чтобы не произошло разрушение, инструмент должен быть достаточно прочным. Наибольшей прочностью обладают термообработанные, быстрорежущие стали, менее прочные — низколегированные и углеродистые стали.
|
Твердые сплавы, минералокерамика, эльбор и алмаз имеют высокие прочностные показатели при сжатии, но при растяжении они в 4-5 раз меньше. Поэтому при проектировании режущего инструмента необходимо, чтобы лезвие имело напряжения сжатия, а не изгибов.
Теплостойкость. В процессе резания непрерывно выделяется тепловая энергия эквивалентная механической работе затраченной на резание. В инструментальных материалах, из которых изготовлено лезвие и прилегающие к лезвию части корпуса инструмента, создается тепловое поле с максимальной температурой на контактных поверхностях инструмента. Под теплостойкостью понимают способность инструментального материала сохранять при нагреве свою структуру и свойства, необходимые для резания.
Теплостойкость характеризуется температурой, при которой материал сохраняет определенную установленную ранее твердость (температура красно стойкости). Для разных марок инструментальных материалов, в зависимости от структурного и фазового состава, эта температура колеблется от 200...1000 .
Теплопроводность — это способность отводить тепло. Присутствие кобальта (Co) в быстрорежущих сталях и твердых сплавах существенно увеличивает теплопроводность. Для быстрорежущих сталей (БРС) таким же свойством обладает молибден (Mo). А ванадий (V) и вольфрам (W) снижают теплопроводность.
Износостойкость — способность инструментального материала сопротивляться разрушению истиранием. Причиной потери режущих свойств у всех инструментов является износ, то есть диспергирование и унос части инструментального материала составляющего лезвие инструмента, и, следовательно, нарушение исходной формы и геометрических параметров режущего инструмента.
Износ — сложный недостаточно изученный процесс, зависящий от множества факторов. Важнейшие из них: нормальное давление; скорость взаимного скольжения инструментального материала (ИМ) и обрабатываемого материала (ОМ); температура в зоне резания.
Износостойкость количественно выражается работой силы трения затраченной на превращение единицы массы инструментального материала в продукт износа
|
, [6]
где: A — работа силы трения; — масса диспергированного материала; L — путь скольжения; c, m — коэффициенты, зависящие от свойств материала.
Основные понятия о резании
Пусть с заготовки нужно удалить припуск толщиной a, для чего нужно устранить физические связи по плоскости 1-2-3-4 (смотри рисунок 6). Если для формообразования детали используется метод резания, то в качестве режущего инструмента применяется резец. Резец: перемещаясь равномерно в направлении Dr со скоростью V, срезает припуск в виде стружки размером
[9]
и при этом совершается работа равная произведению , где L — путь резания; Pz — сила резания.
Рисунок 6 Схема заготовки Рисунок 7 Схема режущего клина
Эта работа может быть совершена только в том случае, если со стороны резца и заготовки будет приложена необходимая сила резания Pz. Этой же величине работы будет равно количество энергии, затраченное на снятие данного припуска. В случае если величина припуска будет очень большой, то его разделяют на несколько проходов режущего инструмента.
Основа любого режущего инструмента — режущий клин AOB с углом заострения β (смотри рисунок 7). Клин имеет переднюю поверхность OA, контактирующую непосредственно со стружкой, и заднюю поверхность, обращенную к заготовке. Пересечение передней и задней поверхностей режущего инструмента образует главную режущую кромку.
Режимы резания
Режимы резания — совокупность понятий, глубины резания, скорости резания и подачи. Как правило, им соответствуют значения стойкости режущего инструмента, которые непосредственно связаны с параметрами режима резания.
Глубина резания — глубина внедрения режущего лезвия в материал заготовки t [мм]. В большинстве случаев, она определяется как кратчайшее расстояние между обработанной и обрабатываемой поверхностями.
Различают главное движение резания Dr, которое производится с наибольшей скоростью, и вспомогательное движение подачи DS, которое необходимо для распространения движения резания по всей обрабатываемой поверхности (смотри рисунок 10).
|
а) б) а) б)
Рисунок 10 Движения резания Рисунок 11Схема главного движения резания
а-при строгании, б-при точении а- при точении; б- при абразивной обработке
Скоростью резания называют главное движение резания, так как оно определяет направление и скорость деформации в обрабатываемом материале.
Скорость резания может сообщаться как заготовке, так и режущему инструменту. Измеряется:
при лезвийной обработке;
при абразивной обработке.
Если главное движение резания — вращательное, то скорость резания равна линейной скорости относительного движения заготовки и режущего инструмента (смотри рисунок11а).
[10]
При абразивной обработке
, [12]
где D — диаметр; n — число оборотов (смотри рисунок 11б).
Подача (t) — расстояние, пройденное режущей кромкой инструмента в направлении вспомогательного движения DS за время цикла главного движения резания. Иногда используется понятие скорости подачи. Подача, как и скорость резания, может сообщаться как заготовке, так и режущему инструменту.
Различают:
подачу на оборот ;
минутную подачу ;
подачу на зуб — для протяжек и других многозубых агрегатов;
подачу на двойной ход и другие виды.
Стойкость — время жизненного цикла инструмента. Измеряется в минутах, и сильно зависит от подачи S, скорости резания V и глубины резания t.
Углы заточки резца
Углы резца определяют взаимное расположение поверхностей его режущей части, а также остроту режущего клина, форму поперечного сечения срезаемого слоя.
Главный угол в плане (угол φ) — определяется в основной плоскости PO между направлением подачи Sпр и проекцией главной режущей кромки на основную плоскость (смотри рисунок 16).
Вспомогательный угол в плане (угол φ1) — определяется в основной плоскости PO между направлением, обратным направлению подачи DS, и проекцией вспомогательной режущей кромки на основную плоскость (смотри рисунок 16).
Угол при вершине (угол e) - определяется в основной плоскости PO между проекцией главной режущей кромки на основную плоскость и проекцией вспомогательной режущей кромки на основную плоскость
Сумма углов резца в плане равна 180о
[13]
Рисунок 16 Углы резца в плане
Главные углы резца измеряются в главной секущей плоскости «А», которая проходит перпендикулярно к проекции главного режущего лезвия на основную плоскость (смотри рисунок 17, а).
|
Рисунок 17 Углы резца в главной секущей плоскости.
Главным передним углом g называется угол между передней поверхностью резца и плоскостью, перпендикулярной к плоскости резания, проходящую через главное режущее лезвие. Его назначение - уменьшить усилие деформации срезаемого слоя металла (смотри рисунок 17).
Главным задним углом a называется угол между касательной к главной задней поверхности и плоскостью резания. Этот угол служит для уменьшения трения между главной задней поверхностью резца и поверхностью резания (смотри рисунок 17).
Углом резания d называется угол между передней поверхностью резца и плоскостью резания (смотри рисунок 17).
Углом наклона главной режущей кромки l (смотри рисунок 18) называется угол, заключенный между режущим лезвием и линией, проведенной через вершину резца, параллельно основной плоскости. Величина этого угла влияет на направление схода стружки с передней поверхности резца
Рисунок 18 Угол наклона главной режущей кромки
Если поверхности резца криволинейные, то углы измеряются между соответствующими касательными к рассматриваемым поверхностям в точке режущего лезвия.
На режущем лезвии всегда предусматривают радиус скругления режущей кромки ρ для снижения механических и силовых нагрузок на вершине резца.
Основные типы резцов
Наименование резца согласно условно принятой классификации можно установить по следующим признакам:
1. По станку, на котором выполняется работа:
- Токарные;
- Долбежные;
- Строгальные;
- Затыловочные;
- Автоматные.
2.По виду выполняемой работы:
2.1.Точение (смотри рисунок 21,а):
- Проходные (смотри рисунок 21,а, позиции 1,2,6);
- Упорные (смотри рисунок 21,а, позиция 3);
- Подрезные (смотри рисунок 21,а, позиция 7,4);
- Отрезные (смотри рисунок 21,а, позиция 8);
- Прорезные (смотри рисунок 21,а, позиция 5);
- Резьбовые (смотри рисунок 21,а, позиция 9);
- Фасонные (смотри рисунок 21,а, позиция 10 и 11).
2.2.Растачивание:
- Проходные — можно сделать отверстие;
- Подрезные резцы — можно сделать уступ.
2.3.Строгание:
- Проходные;
- Подрезные.
2.4.Долбяки:
- Проходные двух сторонние;
- Прорезные.
3.По направлению подачи (смотри рисунок 21,б):
- Правые;
- Левые.
4.По конструкции рабочей части и ее положению относительно крепежной части:
- Прямой (смотри рисунок 21,а, позиция 1);
- Отогнутый (смотри рисунок 21,а, позиция 2);
- Изогнутый (положительные и отрицательные) (смотри рисунок 21,а, позиция 4);
- Оттянутые (симметричные вправо и влево) (смотри рисунок 21,а, позиция 8).
Рисунок 21 Типы токарных резцов
5.По форме главной режущей кромки:
- Прямолинейные;
- Криволинейные.
6.По форме передней поверхности:
- Плоская;
- Плоская с фаской;
- Криволинейная;
- Криволинейная с фаской.
7.По способу изготовления:
- Цельный;
- Составной;
- Приваренный встык рабочей частью;
- Режущей пластиной;
- Сборный с механическим креплением режущей пластины.
8.По материалам режущей части:
- Быстрорежущая сталь;
- Твердый сплав;
- Минерало-керамика;
- Эльбор
- Алмаз.
9.По поперечному сечению крепежной части:
- Квадратные;
- Прямоугольные;
- Круглые.
Назначение резцов
Различают черновые (обдирочные) и чистовые проходные резцы. Первые используют для черновой обработки деталей, когда нужно снять толстый слой металла. Эти резцы бывают правые, левые, прямые (смотри рисунок 22,а), отогнутые. Чистовые проходные резцы (смотри рисунок 22,б), имеющие значительно больший радиус закругления при вершине, чем обдирочные, применяют для окончательной обработки изделий.
Черновыми и чистовыми подрезными резцами (смотри рисунок 22,в) обрабатывают торцовые поверхности заготовок или уступы при поперечной подаче.
Отрезные резцы (смотри рисунок 22,г ) служат для разделения заготовок на части и выточки кольцевых канавок.
Расточными резцами (смотри рисунок 22,д) обрабатывают сквозные и глухие отверстия; длина этих резцов всегда должна быть больше длины обрабатываемого отверстия.
Резьбовые резцы (смотри рисунок 22,е) по расположению головки относительно тела резца для нарезания наружной резьбы выполняют прямыми, а для внутренней — отогнутыми. Угол при вершине должен соответствовать профилю резьбы.
Рисунок 22 Классификация токарных резцов по назначению
Фасонные резцы предназначены для чистовой обработки фасонных поверхностей. Форма главной режущей кромки резца должна строго соответствовать форме чистовой поверхности детали.
При токарных работах часто применяют специальные резцы, у которых изменена геометрическая форма с целью повышения их стойкости. Такие резцы предложены новаторами производства.
-
Державочные части резцов
Характеризуются формой и размером поперечного сечения, материалом, твердостью. Бывают прямоугольного, квадратного и круглого сечения. B*H=16*10…63*40 мм; a=4…63 мм; d=8…50 мм. Материалы: Сталь 40, Сталь 50, 40Х, 45Х, 48, У10.
Соединение рабочей части с корпусом: 1 — цельный резец; 2 — рабочая часть цельная; 3 — припаянная (приваренная для БРС) пластина твердого сплава. 4 — с механическим креплением. Составные конструкции резцов делают с целью экономии инструментального материала.
Токарные резцы обычно изготовляют из быстрорежущей стали (Р9, Р18, Р18Ф2 и др.), реже из легированной (9ХФ и ХВ5). У составных резцов режущая часть выполнена из твердосплавных металлокерамических и минералокерамических пластинок, а тело резца — из углеродистой стали.
Твердые металлокерамические сплавы марок ВК (карбид вольфрама с кобальтом) применяют для точения, главным образом, чугуна, цветных металлов и их сплавов, а также жаропрочных и нержавеющих сталей; сплавы марок ТК (на основе карбидов титана и вольфрама) используют обычно для точения пластичных металлов.
Для токарных резцов при черновом точении стали применяют пластинки металлокерамических твердых сплавов марок Т5КЮ, Т15К6, Т14К8, Т5К12В, а также ВК8 и ВК6М; для черновой обработки чугуна — ВК6, ВК8, ВК6М, а также ТЗОК4, Т5КЮ, Т14К8, Т15К6 и др. Для получистого и чистого точения стали применяют твердосплавные пластинки марки ВК6М. При чистовой обработке чугуна применяют пластинки марок ВК2, ВКЗ, ВК6, ВК8, а также пластинки из минералокерамического материала марки ЦМ-332.
Для тонкого точения используют алмазные резцы с напаянными алмазами или с механическим их креплением.
Пластинки из твердых металлокерамических сплавов соединяют с державкой резца пайкой, а из металлокерамики закрепляют при помощи различных механических приспособлений. На рисунке 22,ж показано крепление такой пластинки на проходном резце. Пластинка 2 прижимается накладным стружколомом 3 через подкладку 1 к державке 6 резца. Для надежного фиксирования положения пластинки служит упор 4. Стружколом крепят к державке шпилькой 5.
Резец с механическим креплением многогранных (многолезвийных), неперетачиваемых металло- и минералокерамических пластинок показан на рисунке 22,з. При помощи механического крепления 7 пластинка 2 крепится к державке 6 резца. Эти резцы обычно предназначены для наружного обтачивания изделий: они имеют главные углы в плане j = 45; 60; 75 и 90°. Главный задний угол a получают за счет соответствующей установки пластинки на державке резца.
Многолезвийные пластинки изготовляют трех-, четырех-, пяти и шестигранными с диаметром описанной окружности 14—26 мм и рабочей высотой 16—30 мм из вольфрамо-кобальтовых, титано-вольфрамокобальтовых и минералокерамических сплавов. Такие резцы надежны в работе и позволяют осуществлять подачу в диапазоне 0,3—0,8 мм. Благодаря углублению (выкружке) на передней поверхности стружка хорошо завивается и дробится. Резцы с многолезвийными пластинками позволяют последовательно использовать для резания металла без переточки все грани пластинки. Срок их службы по сравнению с напаянными резцами увеличивается на 25—200%.
Резание металлов
Резание — как технологический способ обработки заключается в том, что с обрабатываемой заготовки срезается слой металла специально оставленный для обработки. Этот слой называется припуском. В ряде случаев припуск может быть достаточно большим, и он может сниматься (срезаться) за несколько проходов. В результате чего заготовка превращается в деталь.
Металл, срезаемый с заготовки, пластически деформируется, а затем отделяется от заготовки. Он приобретает определенную форму и размеры, и в таком виде его принято называть стружкой.
Пластическое деформирование и разрушение металлов в процессе резания протекают в особых условиях. Именно это и определяет специфику и закономерности, определяемые физикой этого процесса, которые могут быть отражены зависимостями (частными, в основном), отражающими процесс обработки резанием.
Краткие сведения об обрабатываемых и конструкционных материалах
Обрабатываемость материала резанием — это его способность подвергаться обработке резанием (как правило, на металлорежущих станках). Если в процессе обработки металл удаляется в виде стружки, то инструмент выполняющий эту операцию называется режущим.
Обрабатываемость материала резанием — совокупность свойств определяемая:
Химическим составом материала;
Структурным состоянием;
Механическими свойствами (упругость, пластичность);
Склонностью к образованию стружки;
Способностью сопротивляться резанью (косвенный признак);
Энергетическими затратами на резание;
Тепловыми процессами;
Теплопроводностью материала;
Истираемостью материала.
В настоящее время существует более 300 марок сталей (сплавов, как черных, так и цветных). Их по обрабатываемости подразделяют:
Легкие сплавы, как наиболее легко обрабатываемые резанием. Это сплавы на основе алюминия (различные латуни и бронзы);
Средне обрабатываемые стали и сплавы. К ним относятся, углеродистые стали типа: Сталь 20...Сталь 50, чугуны, легированные стали 40Х, 20Х, 20ХН и другие;
Трудно обрабатываемые. Это аустенитные стали, стали легированные хромом (13-20%), специальные сплавы с никелем (Ni) (30-70%), сплавы с ниобием.
Инструментальные материалы
При резании на контактных поверхностях режущего инструмента возникают давления (тысячи атмосфер) и одновременно выделяется много тепла (температура резания сотни, а иногда и тысячи градусов). Также в процессе обработки происходит скольжение и трение обрабатываемого материала по контактным поверхностям режущего инструмента. Поэтому материал режущего инструмента должен обладать свойствами, создающими ему работоспособность. Качество инструментального материала оценивается физико-механическими свойствами, зависящими от структурного состояния или химического состава.
Твердость режущего инструмента (РИ) колеблется в пределах от 62...64 единицы и измеряется, в основном, по шкале HRC, твердомером. При твердости HRC<62 существенно возрастает изнашиваемость лезвий режущего инструмента, а при HRC>64 лезвия выкрашиваются из-за излишней хрупкости. Твердые сплавы и минералокерамика имеют твердость близкую к твердости алмаза. Металлорежущим инструментом (МРИ) из инструментальной стали с твердостью 62...64 HRC обрабатывают, в основном, все конструкционные материалы с твердостью до 30...35 HRC. Наиболее распространенная твердость конструкционных материалов — 12...20 HRC.
Конструкционные материалы с твердостью выше 35...40 HRC обрабатывают твердыми сплавами, минералокерамикой или эльбором (кубический нитрит бора), а в особых случаях алмазами (синтетическими или натуральными).
Прочность. Силы резания, возникающие при работе режущего инструмента, вызывают в материале лезвия и корпуса напряжения сжатия, изгиба, а иногда и кручения. Для того чтобы не произошло разрушение, инструмент должен быть достаточно прочным. Наибольшей прочностью обладают термообработанные, быстрорежущие стали, менее прочные — низколегированные и углеродистые стали.
Твердые сплавы, минералокерамика, эльбор и алмаз имеют высокие прочностные показатели при сжатии, но при растяжении они в 4-5 раз меньше. Поэтому при проектировании режущего инструмента необходимо, чтобы лезвие имело напряжения сжатия, а не изгибов.
Теплостойкость. В процессе резания непрерывно выделяется тепловая энергия эквивалентная механической работе затраченной на резание. В инструментальных материалах, из которых изготовлено лезвие и прилегающие к лезвию части корпуса инструмента, создается тепловое поле с максимальной температурой на контактных поверхностях инструмента. Под теплостойкостью понимают способность инструментального материала сохранять при нагреве свою структуру и свойства, необходимые для резания.
Теплостойкость характеризуется температурой, при которой материал сохраняет определенную установленную ранее твердость (температура красно стойкости). Для разных марок инструментальных материалов, в зависимости от структурного и фазового состава, эта температура колеблется от 200...1000 .
Теплопроводность — это способность отводить тепло. Присутствие кобальта (Co) в быстрорежущих сталях и твердых сплавах существенно увеличивает теплопроводность. Для быстрорежущих сталей (БРС) таким же свойством обладает молибден (Mo). А ванадий (V) и вольфрам (W) снижают теплопроводность.
Износостойкость — способность инструментального материала сопротивляться разрушению истиранием. Причиной потери режущих свойств у всех инструментов является износ, то есть диспергирование и унос части инструментального материала составляющего лезвие инструмента, и, следовательно, нарушение исходной формы и геометрических параметров режущего инструмента.
Износ — сложный недостаточно изученный процесс, зависящий от множества факторов. Важнейшие из них: нормальное давление; скорость взаимного скольжения инструментального материала (ИМ) и обрабатываемого материала (ОМ); температура в зоне резания.
Износостойкость количественно выражается работой силы трения затраченной на превращение единицы массы инструментального материала в продукт износа
, [6]
где: A — работа силы трения; — масса диспергированного материала; L — путь скольжения; c, m — коэффициенты, зависящие от свойств материала.
|
|
Типы сооружений для обработки осадков: Септиками называются сооружения, в которых одновременно происходят осветление сточной жидкости...
Механическое удерживание земляных масс: Механическое удерживание земляных масс на склоне обеспечивают контрфорсными сооружениями различных конструкций...
Археология об основании Рима: Новые раскопки проясняют и такой острый дискуссионный вопрос, как дата самого возникновения Рима...
Типы оградительных сооружений в морском порту: По расположению оградительных сооружений в плане различают волноломы, обе оконечности...
© cyberpedia.su 2017-2024 - Не является автором материалов. Исключительное право сохранено за автором текста.
Если вы не хотите, чтобы данный материал был у нас на сайте, перейдите по ссылке: Нарушение авторских прав. Мы поможем в написании вашей работы!