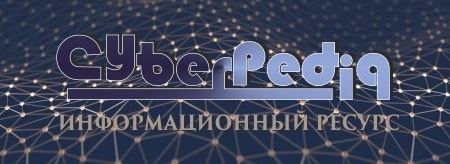
Своеобразие русской архитектуры: Основной материал – дерево – быстрота постройки, но недолговечность и необходимость деления...
Типы оградительных сооружений в морском порту: По расположению оградительных сооружений в плане различают волноломы, обе оконечности...
Топ:
Когда производится ограждение поезда, остановившегося на перегоне: Во всех случаях немедленно должно быть ограждено место препятствия для движения поездов на смежном пути двухпутного...
Выпускная квалификационная работа: Основная часть ВКР, как правило, состоит из двух-трех глав, каждая из которых, в свою очередь...
Процедура выполнения команд. Рабочий цикл процессора: Функционирование процессора в основном состоит из повторяющихся рабочих циклов, каждый из которых соответствует...
Интересное:
Влияние предпринимательской среды на эффективное функционирование предприятия: Предпринимательская среда – это совокупность внешних и внутренних факторов, оказывающих влияние на функционирование фирмы...
Наиболее распространенные виды рака: Раковая опухоль — это самостоятельное новообразование, которое может возникнуть и от повышенного давления...
Аура как энергетическое поле: многослойную ауру человека можно представить себе подобным...
Дисциплины:
![]() |
![]() |
5.00
из
|
Заказать работу |
|
|
При разработке ТП автоматической сборки технолог-сборщик илигруппа технологов должны определить состав выпускаемого изделия,технологический маршрут операций и приемы сборки, выбрать оборудованиеили разработать структуру сборочного оборудования, выполнитьэкономический анализ, обоснование и расчет выбранного варианта автоматизации,рассчитать режимы оборудования, осуществить специальныеисследования.
Должны быть детально проработаны вопросы ориентации,базирования, транспортирования и контроля качества изделий, атакже разработки технических заданий на конструирование специальныхисполнительных устройств и оснастки. Проектные работы выполняютобычным способом или с использованием средств автоматизации проектированияТП.
Разработанный ТП автоматической сборки является основой конструкторской,строительной, транспортной, энергетической и организационнойчастей проекта.
На основе технологии определяют потребность воборудовании, производственную площадь, рабочую силу, основные ивспомогательные материалы, решают вопросы специализации, кооперированиясборочного производства.
Технологический процесс автоматической сборки изделия включаетследующие этапы: подготовку деталей и комплектующих изделий (промывка,очистка, деконсервация, предварительный или 100 % -ный контроль комплектованияи т. д.); загрузку сопрягаемых деталей в бункерные, магазинные,кассетные и другие загрузочные устройства в предварительно или окончательноориентированном; захват, отсекание и подачу сопрягаемых деталейв ориентирующие и базирующие устройства сборочного приспособления;ориентацию сопрягаемых деталей на сборочной позиции с точностью,обеспечивающей собираемость соединений; соединение и фиксацию сопряженныхдеталей с требуемой точностью; контроль требуемой точности относительногоположения сопряженных деталей или сборочной единицы; выполнениепослесборочных операций (например, контроль на выходе, заправкасмазочными материалами, топливом, испытание, регулирование, балансировка,маркировка, упаковка, счет, учет).
|
Построение ТП зависит, прежде всего, от конструктивных особенностей выпускаемых изделий — габаритных размеров, числа входящих визделие деталей и сборочных единиц, характера и сложности соединений.
Особенности собираемого изделия и программа выпуска определяютструктурную схему ТП автоматической сборки, последовательностьвыполнения его операций, их повторяемость, параметры автоматическогооборудования и условия его настройки.
Нерационально спроектированнаятехнология вызывает потери времени при эксплуатации сборочногооборудования. При проектировании ТП автоматической сборкинеобходимо учитывать: программу выпуска изделий; технологичностьконструкции изделия и составляющих его элементов; обеспечение качествасобираемого изделия; распределение переходов по сборочным позициямпо времени их выполнения; точность и надежность относительнойориентации сопрягаемых деталей соединений; надежность выполнениясоединений; контроль качества собираемого изделия или его частей; наладочныепараметры сборочных устройств; организацию производства.
Последовательность этапов проектирования технологии сборки показанана рис. 25.
Рис. 25. Последовательность этапов проектирования технологии сборки
Сбор исходных данных. К исходным данным для проектирования ТПавтоматической сборки относятся: информация сборочных чертежей итехнических условий или формализованное описание объектов сборки;технико-экономические требования, содержащие сведения о номенклатуреи программе выпуска изделий, производительности и стоимости сборочногооборудования, сроках освоения выпуска, допустимом временисборки; технические требования (точность сборки, условие работы изделияи т. д.).
|
Анализ исходных данных. В сборочном чертеже изделия должны бытьприведены: нужные проекции и разрезы; спецификация составляющих егоэлементов; посадки в сопряжениях; масса изделия и его составных частей.
В технических условиях должны быть указаны: точность сборки,качество сопряжений, их герметичность, жесткость стыков, моменты затяжкирезьбовых соединений, точность балансировки вращающихся частей,методы выполнения соединений, желательная последовательностьсборки, методы промежуточного и окончательного контроля изделий.
Наоснове рекомендаций по технологичности конструкции изделий определяют,необходимы ли конструктивные изменения, обеспечивающие автоматическуюсборку. Если изменения внести невозможно, сборку даннойчасти изделия (на данной операции) выполняют вручную или с использованиемсредств механизации. Анализ конструкции изделия и составляющихего деталей позволяет определить, какой вид сборки по степени автоматизациирациональнее применить.
Составление технологических схем автоматической сборки. Анализконструкции и изучение технических условий на изделие заканчивают составлениемтехнологических схем общей и узловой сборки изделия.
Этопервый этап разработки ТП. Технологические схемы сборки составляютна основе анализа сборочных чертежей изделия. Они отражают маршрутсборки изделия и его составных частей.
На этом этапе выявляют оптимальнуюстепень расчленения изделия на составляющие элементы и выбираютвозможные методы автоматической сборки различных соединений.
Разрабатываютразличные технологические варианты схем сборки, содержащиесведения о целесообразности дифференциации и концентрации операций,возможных вариантах схем базирования, относительной ориентациидеталей и их закрепления. Рассчитывают условия собираемости деталей.
Выбирают бункерные ориентирующие, транспортные, контрольные и другиеустройства. На основе технико-экономического анализа выбираютнаиболее рациональный вариант оборудования для сборки.
Последовательность сборки определяют на основе анализа размерныхцепей изделия, каждая из которых предназначена для решения конкретнойзадачи. Определяя последовательность сборки, учитывают функциональнуювзаимосвязь элементов изделия, конструкцию базовых элементов,размеры и массу присоединяемых элементов, степень их взаимозаменяемости,а также то, что легко повреждаемые элементы желательноустанавливать в конце сборки.
|
Определение типа производства. Типы производства в сборочном цехеопределяют отдельно для изделия и его составных частей, так как онимогут быть различными. При поточно-массовом производстве автоматическуюсборку изделий выполняют на высокопроизводительных специальныхавтоматических линиях, в том числе переналаживаемых. Присреднесерийном производстве сборку осуществляют партиями на автоматическомоборудовании. Используют также переменно-поточные илигрупповые автоматические линии для конструктивно или технологическисходных изделий.
Гибкие автоматические линии строят на базе гибкихпроизводственных модулей (ГПМ), автоматизированного транспортногооборудования и автоматизированных рабочих мест (АРМ) с управлениемот центральной ЭВМ. Для ГАЛ характерны поточные методы организациисборки, высокие синхронизация операций и производительность.
В мелкосерийном многономенклатурном производстве сборку выполняютна оборудовании с микропроцессорным управлением, обслуживаемымавтоматизированной транспортной системой, которая вместе с ЭВМобразует гибкий автоматизированный участок сборки.
При поточном методе работы штучное время на операцию должнобыть несколько меньше темпа сборки для создания резерва на случайзадержек сборки или кратно темпу. Коэффициент загрузки оборудования должен быть высоким (не менее 0,95). На первых операциях поточнойлинии его нужно брать меньше, чем на последних операциях сборки.
Этообеспечивает большую надежность работы линии в случае отказов оборудования.
Выбор организационной формы автоматической сборки. Организационнуюформу сборки следует выбирать в зависимости от конструкцииизделия, его размеров, массы, программы и срока выпуска. Организационнуюформу сборки устанавливают раздельно для изделия и его составныхчастей. В общем случае они могут быть разными. Вариант организационнойформы автоматической сборки конкретного изделия выбираютна основе расчетов себестоимости сборки с учетом сроков подготовки иоснащения производства необходимым оборудованием.
|
В зависимости от организационных форм различают автоматическуюсборку, стационарную и конвейерную. Стационарную сборку выполняютна специальном оборудовании или посредством ПР. Ее в основном используютв массовом и серийном производстве для сборки небольших узлов.
Конвейерную сборку на автоматических линиях в большинстве случаеввыполняют с периодической остановкой собираемого изделия. Сборкас непрерывным перемещением изделия осуществляется на конвейерах,ьоснащенных ПР, а также на роторных автоматических линиях.
Разработка маршрутной технологии общей и узловой автоматической сборки. Маршрутную технологию составляют на основе технологическихсхем сборки. Она включает в себя все технологические, контрольныеи вспомогательные операции, выполняемые автоматически иливручную. Содержание операций устанавливают в зависимости от выбранноготипа производства и темпа сборки. При построении маршрутнойтехнологии нужно стремиться к одновременному выполнению (объединению)нескольких операций, что обеспечивает сокращение цикла сборки ипотребности в производственных площадях. При массовом производствеодержание операции должно быть таким, чтобы ее длительность была несколько меньше темпа сборки или кратна ему.
При построении маршрутной технологии необходимо выделить операциис большой вероятностью отказов и предусмотреть на данном этапепроизводственные заделы. На основе маршрутной технологии разрабатываюттехническое задание средств автоматизации.
При разработке определяюттип технологического и транспортного оборудования, которое затемуточняют на последующих этапах проектирования технологии сборки.
Выбор технологических баз, схем базирования изделия при узловой иобщей автоматической сборке. Ответственным этапом проектированияТП автоматической сборки является выбор технологических баз и схембазирования, которые должны обеспечить заданную точность сборки,удобство ее выполнения, простоту конструкций приспособлений, оборудования и транспортных средств. При выборе технологических баз стремятсявыдержать принципы совмещения, постоянства и последовательностисмены баз. В каждом конкретном случае может быть использованонесколько схем базирования.
При анализе схем рассчитывают погрешностиустановки. Если предусмотрена организованная смена баз, то пересчитываютсоответствующие размеры и допуски на них, определяютдопуски на параметры технологических баз. Для сокращения числа вариантовсхем базирования следует применять типовые решения.
|
Технологическиебазы выбирают с учетом обеспечения удобства установки иснятия собираемого изделия, надежности и удобства его закрепления,возможности подвода с разных сторон присоединяемых деталей и сборочныхинструментов. Различают базирование базовой детали изделияили отдельной его части при их установке в сборочное приспособление иазирование сопрягаемых деталей при узловой или общей сборке.
Используют стационарные позиционные приспособления или приспособления- спутники. В обоих случаях следует соблюдать принципы совмещенияи постоянства баз. Соединение двух деталей при автоматическойсборке должно обеспечить их 100 %-ную собираемость.
Построение операций автоматической сборки. Этап построения операцийсборки является наиболее трудоемким и сложным при проектированиитехнологии автоматической сборки. Он включает: уточнение содержанияопераций; повышение степени концентрации переходов; четкоеразграничение всех составляющих элементов операции — от ориентациисопрягаемых деталей до удаления собираемой части изделия илиего самого; технологические расчеты; определение сил запрессовки, затяжкирезьбовых соединений, клепки и т. д.; определение штучного временипо элементам изделия и в целом.
На этом этапе определяют основную технологическую характеристикунеобходимого сборочного оборудования: структурную схему; кинематическиеи динамические параметры; размер рабочей зоны для размещениясобираемого изделия с оснасткой; систему управления; степень автоматизациирабочего цикла; способность к переналадке.
При отсутствии серийновыпускаемого оборудования разрабатывают техническое задание наего проектирование, при его наличии выбирают модель.
Разрабатывают техническое задание на конструирование специальныхсборочных инструментов, сборочного приспособления с указаниемпринятых схем базирования, способов автоматической подачи и ориентациидеталей и снятия готового изделия. Определяют методы необходимогоконтроля выполнения сборки, тип блокировочных устройств, предупреждающихаварийные ситуации и брак.
При проектировании операции сборки на многопозиционных станкахи АЛ определяют загрузку оборудования по отдельным позициям,строят циклограммы работы, устанавливают структуру и тип линии, необходимыезаделы и накопители, конфигурацию линии в плане для еестыковки со сложными участками сборочного цеха. Составляют техническоезадание на проектирование линии.
Нормы времени на сборочные операции определяют расчетно-аналитическим методом.
Вопросы для самоподготовки:
1. В чем заключаются особенности автоматизации подготовки управляющих программдля станков с ЧПУ?
2. Какие системы автоматизации программирования существуют в настоящее время?
3. Дайте определение структуры и перечислите основныехарактеристики производственногопроцесса?
4. Перечислите необходимые условия для реализации процессов автоматической сборки?
5. Из каких этапов состоит последовательность проектированиятехнологического процесса автоматической сборки?
СПИСОК ЛИТЕРАТУРЫ
1. Автоматизация проектирования технологических процессов в машиностроении/Под ред. Н.М. Капустина. — М.: Машиностроение, 1985.
2. Автоматизация проектирования технологических процессов и средствоснащения /Под ред. А.Г. Раковича. Г.К. Горанский, Л.В. Губич, В.И. Махнач идр. — Минск, ИТК АН Беларусь 1997.
3. Автоматизированные системы проектирования технологических процессовмеханосборочного производства / Под ред. Н.М. Капустина. — М.: Машиностроение,1979.
4. Андреев Г.Н., Новиков В.Н., Схиртладзе А.Г. Проектирование технологическойоснастки машиностроительного производства. — М.: Высшая школа, 2002.
5. Андрющенко В.А. Следящие системы автоматизированного сборочного оборудования.— Л.: Машиностроение, 1979.
6. Башарин А.В., Новиков В.А., Соколовский Г. Г. Управление электроприводами.— Л.: Энергоиздат. Ленинградское отделение, 1982.
7. Вентцель Е.С. Исследование операций: задачи, примеры, методология. — М.:Наука, 1988.
8. Вороненко В.П., Схиртладзе А.Г., Брюханов В.П. Автоматизированное производство.— М.: Высшая школа, 2001.
9. Гибкие производственные комплексы /Под ред. П.Н. Белянина, В.А. Лещенко. — М.: Машиностроение, 1984.
10. Гжиров Р.И., Серебреницкий П.П. Программирование обработки на станках сЧПУ. — Л.: Машиностроение, 1990.
11. Диалоговое проектирование технологических процессов. Н.М. Капустин,В.В. Павлов, Л.А. Козлов и др. — М.: Машиностроение, 1983.
12. Евгенев Г.Б. Системология инженерных знаний. — М.: Изд-во. МГТУ им.Баумана, 2001.
13. Капустин Н.М. Разработка технологических процессов обработки деталей настанках с помощью ЭВМ. — М.: Машиностроение, 1976.
14. Капустин Н.М., Васильев Г.Н. Автоматизация конструкторского и технологическогопроектирования. Система автоматизированного проектирования. В 9 кн.Кн. 6. — М.: Высшая школа, 1986.
15. Капустин Н.М., Дьяконова Н.П., Кузнецов П.М. Автоматизация машиностроения/Под ред. Н.М. Капустина. — М.: Высшая школа, 2002.
16. Капустин Н.М., Кузнецов П.М. Структурный синтез при автоматизированномпроектировании технологических процессов деталей с использованием генетическихалгоритмов // Информационные технологии, 1998. № 4. С. 34-37.
15. Капустин Н.М., Кузнецов П.М. Формирование виртуальной производственнойсистемы для выпуска изделий в распределенных системах //Машиностроитель.2002. № 6. С. 42-46
16. Козырев Ю.Г. Промышленные роботы: Справочник. — М.: Машиностроение,1988.414
17. Кузнецов М.М., Усов Б.А., Стародубов B.C. Проектирование автоматизированногопроизводственного оборудования. — М.: Машиностроение, 1987.
18. Металлорежущие станки и автоматы / Под. ред. А.С. Проникова. — М.:Машиностроение 1981.
19. Куропаткин П.В. Оптимальные и адаптивные системы. — М.: Высшая школа,1980.
20. Моделирование робототехнических систем и гибких автоматизированныхпроизводств/Под ред. Н.М. Макарова. В 9 кн. Кн. 5. — М.: Высшая школа, 1986.
22. Машиностроение. Энциклопедия. Раздел III. Технология производства машин/ Под ред. П.Н. Белянина. — М.: Машиностроение, 2000.
23. Мухин А.В. Новые концепции организации промышленного производства //Наука производству. 2001. №5. С. 2 - 7.
24. Норенков И.П. Принципы построения и структура. Системы автоматизированногопроектирования. В 9 кн. Кн. 1. — М.: Высшая школа, 1986.
25. Норенков И.П. Разработка САПР. — М.: Изд-во МГТУ им. Н. Э. Баумана.1994.
26. Норенков И. П. Основы автоматизированного проектирования. — М.: Изд-воМГТУ им. Н. Э. Баумана, 2000.
27. Основы автоматизации машиностроительного производства /Под. ред. Ю.М.Соломенцева. — М.: Высшая школа, 1999.
28. Норенков И.П., Кузьмин П.К. Информация поддержки наукоемких изделий. —М.: Изд-во МГТУ им. Н. Э. Баумана, 2002.
29. Павлов В.В. Типовые математические модели в САПР ТП. — М.: Мосстанкин,1989.
30. Павлов В. В. CALS-технологии в машиностроении (математические модели).— М.: Изд-во МГТУ Станкин, 2002.
31. Программное управление станками / Под ред. В.Л. Сосонкина. — М.: Машиностроение,1981.
32. Павлов В.В. CALS-технологии в машиностроении (математические модели).— М.: Изд-во МГТУ Станкин, 2002.
33. Роботизированные производственные комплексы/Под ред. Ю.Г. Козырева,А.А. Кудинова. — М.: Машиностроение, 1987.
34. Справочник технолога машиностроителя / Под ред. A.M. Дальского. В 2 т.— М.: Машиностроение, 2001. «Издательство машиностроение - 1».
35. Схиртладзе А.Г., Соколов В.И., Фадеев В.А. Металлорежущие станки с программнымуправлением и подготовки программ. — Харьков: Высшая школа, 1992.
36. Технология машиностроения. Основы технологии машиностроения/Под ред.A.M. Дальского. В 2 т. Т. 1. — М.: Изд-во МГТУ им. Н. Э. Баумана, 1997.
37. Технология машиностроения. Производство машин/Под ред.Г.Н. Мельникова.В 2 т. Т. 2. - М.: Изд-во МГТУ им. Н. Э. Баумана, 1998.
38. Технология производства гусеничных и колесных машин / Под ред. Н.М. Капустина.— М.: Машиностроение, 1989.
39. Трудоношин В.А., Пивоварова Н.В. Математические модели технических объектов.В 9 кн. Кн. 4. — М.: Высшая школа, 1986.
СОДЕРЖАНИЕ
ВВЕДЕНИЕ.. 3
Лекция №1 Особенности проектирования технологического процесса в автоматизированном производстве 5
1.1. Основы автоматизации технологических процессов. 5
1.2. Требования к металлорежущему оборудованию и производственным процессам, подлежащим автоматизации. 7
1.3. Типовые и групповые технологические процессы.. 9
Лекция №2Производительность автоматизированных систем и средства их оснащения. 14
2.1. Промышленные роботы.. 14
2.2. Роботизированные технологические комплексы.. 18
2.3. Роботизированные системы для обслуживания станков. 19
2.4. Типовые компоновки РТК.. 20
2.5. Технологическое оснащение и станочные приспособления. 22
Лекция №3Надежность, контроль и диагностика в автоматизированном производстве. 28
3.1. Состояния объекта и физический смысл понятий в области надежности. 28
3.2. Физика отказов и их особенности. 29
3.3. Показатели оценки надежности. 29
3.4. Связь надежности с производительностью.. 30
3.5. Специфика формирования показателей надежности и их связь с производительностью.. 30
3.6. Зависимость показателей надежности и производительности от времени эксплуатации станков 31
3.5. Анализ последствий отказов. 32
3.6. Методы повышения надежности автоматизированных систем.. 32
3.7. Принятие решений на начальных стадиях проектирования. 33
3.8. Избыточность и резервирование. 33
3.9. Повышение информативности. 34
Лекция №4 Автоматизация операций изготовления деталей на станках с ЧПУ. Особенности автоматизированной сборки изделий. 36
4.1. Автоматизация подготовки управляющих программ.. 36
для станков с ЧПУ.. 36
4.2. Системы автоматизации программирования. 38
4.3. Определение структуры и основных характеристик производственного процесса. 39
4.4. Условия применения автоматической сборки. 41
4.5. Последовательность проектирования технологического процесса автоматической сборки 41
СПИСОК ЛИТЕРАТУРЫ... 46
Учебное издание
Сергей Леонидович Новокщёнов,
Валерий Иванович Корнеев
АвТОМАТИЗАЦИЯ ПРОИЗВОДСТВЕННЫХ ПРОЦЕССОВ В МАШИНОСТРОЕНИИ
В авторской редакции
Компьютерный набор С. Л. Новокщёнова
Подписано к изданию 06.07.2015
5,6уч.-изд. л. «С»
ФГБОУ ВПО «Воронежский государственный технический университет»
|
|
Биохимия спиртового брожения: Основу технологии получения пива составляет спиртовое брожение, - при котором сахар превращается...
Типы сооружений для обработки осадков: Септиками называются сооружения, в которых одновременно происходят осветление сточной жидкости...
История создания датчика движения: Первый прибор для обнаружения движения был изобретен немецким физиком Генрихом Герцем...
Поперечные профили набережных и береговой полосы: На городских территориях берегоукрепление проектируют с учетом технических и экономических требований, но особое значение придают эстетическим...
© cyberpedia.su 2017-2024 - Не является автором материалов. Исключительное право сохранено за автором текста.
Если вы не хотите, чтобы данный материал был у нас на сайте, перейдите по ссылке: Нарушение авторских прав. Мы поможем в написании вашей работы!