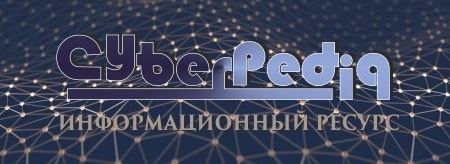
Своеобразие русской архитектуры: Основной материал – дерево – быстрота постройки, но недолговечность и необходимость деления...
История развития пистолетов-пулеметов: Предпосылкой для возникновения пистолетов-пулеметов послужила давняя тенденция тяготения винтовок...
Топ:
Когда производится ограждение поезда, остановившегося на перегоне: Во всех случаях немедленно должно быть ограждено место препятствия для движения поездов на смежном пути двухпутного...
Марксистская теория происхождения государства: По мнению Маркса и Энгельса, в основе развития общества, происходящих в нем изменений лежит...
Интересное:
Средства для ингаляционного наркоза: Наркоз наступает в результате вдыхания (ингаляции) средств, которое осуществляют или с помощью маски...
Мероприятия для защиты от морозного пучения грунтов: Инженерная защита от морозного (криогенного) пучения грунтов необходима для легких малоэтажных зданий и других сооружений...
Берегоукрепление оползневых склонов: На прибрежных склонах основной причиной развития оползневых процессов является подмыв водами рек естественных склонов...
Дисциплины:
![]() |
![]() |
5.00
из
|
Заказать работу |
|
|
Введение
Рост промышленных объектов и городов, открытие новых залежей полезных ископаемых, развитие населенных пунктов - все это видоизменило количественно и качественно грузопотоки и их направление. Возросла потребность в усовершенствованных, в частности, асфальтобетонных покрытиях для автомобильных дорог.
Положительные эксплуатационные качества асфальтобетонных покрытий - бесшумность, ровность, беспыльность, а также относительно длительный срок службы и быстрота устройства - способствует их широкому применению на дорогах I - IV категорий.
Смеси для таких покрытий приготавливают на специализированных производственных предприятиях - асфальтобетонных заводах (АБЗ). АБЗ могут быть сезонные, передвижные, находящиеся на одном месте один, максимум два строительных сезона с минимальным радиусом возки смеси, и стационарные, находящиеся на одном месте до 10 и более лет.
Сезонные АБЗ создаются близ строящейся дороги на базе передвижного оборудования. Основное оборудование сезонного АБЗ комплектуется из агрегатов с технологически законченным процессом, например, узел перемешивания, агрегат питания, газоочистительная установка и др. Они обычно решаются по принципу партерного расположения в виде инвентарных сборно-разборных конструкций, передвижными на пневмотележке. Производительность сезонных заводов достигает 50 т/ч.
Стационарные заводы рекомендуется проектировать производительностью, позволяющей обслуживать строительство в радиусе 50 км. Их производительность достигает 100 т/ч и более.
Режим работы для стационарного и сезонного АБЗ различны и зависят от скорости потока при строительстве дорог, суточной потребности в смеси.
|
Стационарные АБЗ работают длительное время на одном месте и имеют более совершенную механизацию и автоматизацию. Автоматизация технологического процесса на АБЗ обеспечивает точность дозирования минеральных материалов, резкое улучшение и стабильность качества смеси, соблюдение температурного режима, высвобождение рабочей силы, улучшение условий труда.
Поиски прогрессивной технологии приготовления асфальтобетонных смесей, большой размах строительства асфальтобетонных покрытий, потребовали от машиностроения резкого увеличения выпуска смесительных установок.
Возросшие объемы строительства дорог и соответственно потребность в каменных материалах повлекли за собой и перестройку снабжения АБЗ сырьем. Создание цехов по переработке камня для получения щебня и минерального порошка на каждом АБЗ оказалось нерентабельным.
Асфальтобетонный завод (АБЗ) представляет собой комплекс технологического оборудования и складов материалов, предназначенных для приготовления асфальтобетонных смесей, применяемых в дорожном и других видах строительства. В состав АБЗ входят: склады щебня, песка, минерального порошка и битумное хозяйство с оборудованием для разгрузки, складирования и подачи битума; асфальтосмесительные установки, включающие оборудование для сушки и нагрева минеральных материалов, обезвоживания и нагрева битума, оборудование для дозирования и перемешивания всех компонентов асфальтобетонной смеси; оборудования для энерго-, воздуха-, и пароснабжения технологических агрегатов АБЗ; лаборатория для контроля качества материалов и процесса приготовление смеси; помещения служебного и бытового назначения.
Для сокращения сроков строительства, повышения его качества и снижения себестоимости необходимым условием является обеспечения полного и эффективного использования всех машин и оборудования, входящего в состав асфальтобетонных заводов. Это особенно важно, поскольку техническое состояние всего комплекта машин непосредственно влияет на качество асфальтобетонных смесей, а следовательно, и на качество и долговечность дорожных покрытий.
|
Производство асфальтобетонных смесей - один самых энергоемких процессов дорожного строительства, а от технического состояния всего парка машин, входящих в состав АБЗ, зависит расход топливно-энергетических ресурсов.
Только всесторонние глубокое знание всего парка машин, входящего в состав АБЗ, создает условия для повышения производительности труда, экономии топливно-энергетических ресурсов, высокой культуры производства, снижения себестоимости и повышения качества дорожного строительства.
Исходные данные для проектирования АБЗ.
Район строительства.
Район строительства АБЗ – Минский.
На основе карты-схемы Минского района, дорожно-климатического графика, розы ветров и расположения ближайшего карьера выбираем место расположения завода город Заславль принадлежащий ДСУ 12 треста № 5.
Тип завода стационарный.
Таблица 1.1 – Расчёт количества рабочих смен за сезон
Месяц | Дк | Д | Дрем | Др | Др.с |
Май | 18 | 1,26 | 1,61 | 15 | 15 |
Июнь | 30 | 1,55 | 4,97 | 23 | 45 |
Июль | 31 | 1,55 | 5,15 | 23 | 47 |
Август | 31 | 1,55 | 5,15 | 23 | 47 |
Сентябрь | 24 | 0,58 | 2,25 | 20 | 20 |
Итого: 174 смены |
Наименование смеси
Единица
Измерения
Кол-во ед.
Измерен.
ТЕХНОЛОГИЧЕСКАЯ ЧАСТЬ
Таблица 2.1 – Характеристики асфальтосмесительных установок
Показатель | Асфальтосмесительные установки | ||||||||
ДС-117-2Е | ДС-117-2К* | Л-645-2Г | «Тельтомат» | ДС-118-4 | ДС-84-2 | ||||
Производительность, т/ч: при влажности песка и |
|
| |||||||
25 | 32/32 | 100 | 100**(60) | 100 | 200 | ||||
Щебня 5 % |
|
| |||||||
при влажности песка и | 30 | 42/42 | 140 | 70 | 140 | 240 | |||
Щебня 3 % и приготов- |
|
| |||||||
лении крупнозернистых |
|
| |||||||
Смесей |
|
| |||||||
Тип смесителя | Цикличного действия
| Непрерывного действия | |||||||
Установленная мощность, кВт: |
| ||||||||
Электродвигателей | 160 | 150/135 | 390 | 370 | 364 | 720 | |||
Электронагревателей | 50 | 35/30 | 160 | 69,2 | 194 | 300 | |||
Общая вместимость бункеров | 16 | 18/18 | 40 | 20,8*** | 40 | 60 | |||
Агрегата питания, м3 |
| ||||||||
Вмест-ть смесителя, кг | 600 | 650/650 | 2000 | 1000 | 2300 | 3500 | |||
" бункера агрегата | 20 | 22/8 | 22 | 21 | 20 | 45 | |||
Минер-ного порошка, м3 |
| ||||||||
Вместимость бункера готовой смеси, т | 30 | 32/- | 100 | 80 | 100 | 200 | |||
| |||||||||
Общая вместимость битумных цистерн, м3 | 30 | 37/12 | 120 | 85 | 120 | 90 | |||
| |||||||||
Расход топлива 320 (мазут 100), кг!ч | 310/310 | 1025 | 942 | 1000 | 2000 | ||||
Масса установки, т | 80 | 71,5/53,5 | 175 | 137 | 125 | 280 | |||
Габаритные размеры установки, м: | |||||||||
Длина | 43,58 | 46,0/31,0 | 55,0 | 45 | 54,4 | 85 | |||
Ширина | 34,00 | 35,6/31,6 | 45,0 | 29 | 28,8 | 67 | |||
Высота | 19,68 | 19,8/19,8 | 17.3 | 30 | 14.8 | 27 | |||
* В числителе приведен первый вариант комплектности установки, в знаменателе — второй.
** Указана паспортная производительность, эксплуатационная производительность на мелкозернистой смеси 60 т/ч, крупнозернистой – 70 т/ч.
*** Для четырех бункеров.
Таблица 2.2 – Технические показатели асфальтосмесительная установка полустационарного типа «Тельтомат»
№ | Показатели | Тельтомат |
1 | Производительность при влажности песка и щебня 5%, т/ч. | 100 |
2 | Установленная мощность электродвигателей и электронагревателей кВт. | 430 |
3 | Расход топлива, м3/ч. (газ) | 15 |
4 | Масса установки, т. | 71,5 |
5 | Число отсеков бункера агрегата питания, шт. | 4 |
6 | Общая вместимость бункеров агрегата питания, м3. | 18 |
7 | Загрузочная вместимость мешалки, кг. | 900 |
8 | Вместимость бункера готовой смеси, т. | 80 |
9 | Тип смесителя. | Циклического Действия |
Количество установок:
n = 199,55 / 100 = 1,99 ~ 2 установки. (2.4)
Агрегаты питания.
|
В состав агрегатов питания входят бункера, дозаторы-питатели, ленточный сборный транспортер. Они классифицируются по конструкции, количеству секций, расположению и компоновке. Агрегаты питания могут собирать из отдельных бункеров или размещать на общей раме в один или два ряда. Количество бункеров определяют необходимым количеством фракций каменных материалов, и оно может быть от трех до шести. Вместимость каждого бункера зависит от производительности асфальтосмесительной установки. Как правило, бункера агрегатов питания загружают с помощью фронтальных погрузчиков из складов асфальтобетонного завода.
На рис. 2.6 показан агрегат питания асфальтосмесительной установки ДС-117-2К, имеющий расходные бункера щебня 7 и 8 и песка 10, расположенные в один ряд. В нижней части каждого бункера установлены дозаторы-питатели 12, непрерывно подающие минеральные материалы в заданном соотношении на ленту сборного конвейера 13, откуда они направляются по наклонному конвейеру в сушильный барабан. Сверху бункера обычно закрывают металлическими решетками для предотвращения попадания негабаритного материала в бункер.
Производительность дозаторов регулируют с помощью специальных устройств. Для дозирования щебня в большинстве случаев применяют ленточные, кареточные, пластинчатые и вибрационные питатели, для дозирования песка - ленточные питатели. Иногда питатели оборудуют контрольно-весовыми устройствами для контрольного замера производительности дозатора за определенный промежуток времени.
Рис. 2.6. - Агрегат питания асфальтосмесительной установки:
1 — электроприводной барабан; 2 — нижний ролик; 3 — желобчатая роликовая опора; 4 — лента; 5 — барабан; 6 — поддерживающий ролик; 7, 8 — бункера щебня; 9 — вибратор; 10—бункер, песка; 11 — ведомый барабан; 12 — дозатор-питатель; 13 — сборный конвейер; 14 — пульт управления
2.6. Сушильные агрегаты.
В сушильных агрегатах просушивание материалов происходит вследствие радиационного излучения факела сгораемого топлива и конвективной передачи тепла при непосредственном контакте горячих газов с песком и щебнем, которые ссыпаются с лопастей сушильного барабана, а также путем кондуктивной передачи тепла от горячих стенок и лопастей сушильного барабана. Специальные лопасти, закрепленные на внутренних стенках сушильного барабана, многократно поднимают и опускают минеральные материалы в процессе их прохождения по всей длине сушильного барабана. Процесс просушивания и нагрева материалов протекает тем эффективнее, чем равномернее распределен материал по поперечному и продольному сечениям барабана.
Сушильный агрегат состоит из сушильного барабана с загрузочной и разгрузочной коробками, привода сушильного барабана, загрузочного устройства, системы очистки уходящих газов, топочного устройства, вентилятора-дымососа и контрольно-измерительных приборов.
|
Сушильные агрегаты в зависимости от типов асфальтосмесительных установок разделяют на стационарные и передвижные.
Барабан 3 стационарного сушильного агрегата асфальтосмесительной установки (рис. 2.7) при вращении опирается на опорные ролики 14 и 19 через бандажи 2 и 5, прикрепленные к наружной поверхности сушильного барабана с помощью температурных компенсаторов. От продольного перемещения барабан удерживается упорными роликами 18. Вращение барабана осуществляется с помощью привода, включающего электродвигатель 17, цепную муфту, редуктор 16 и ведущую шестерню 15, с которой находится в зацеплении зубчатый венец 4. На раме 20 смонтированы опорные ролики, приемное 1 и топочное 8 устройство. Раму устанавливают на фундаментные опоры с таким расчетом, чтобы угол наклона сушильного барабана в сторону его разгрузки составлял 2,5-3,5°. На асфальтосмесительной установке “ТЕЛЬТОМАТ” установлен сушильный агрегат ТТ – 5.
Рис. 2.7. - Сушильный агрегат асфальтосмесительной установки:
1 — приёмное устройство; 2, 5 - бандажи; 3 - барабан; 4 — зубчатый венец; 6 - компенсатор; 7 - разгрузочная коробка; 8 - топочное устройство; 9 - запальник; 10 - форсунка; 11 - топливный бак; 12 — топливопровод; 13 — лоток; 14, I9 — опорные ролики; 15 — ведущая шестерня; 16 — редуктор; 17 — электродвигатель; 18 — упорный ролик; 20 — рама.
Пылеулавливающие установки.
В процессе приготовления асфальтобетонной смеси на АБЗ образуется большое количество пыли.
Основными зонами наиболее интенсивного пылевыделения являются дымовая труба, разгрузочная и загрузочная коробки сушильного барабана. Пыль образуется также при работе „горячего" элеватора, грохочении сухого песка и щебня, при подаче и дозировании минерального порошка и сухих) горячих каменных материалов. С целью максимально возможного сокращения выделения пыли все уплотнения, предусмотренные конструкцией оборудования, необходимо периодически проверять и восстанавливать.
Для очистки дымовых газов сушильных барабанов применяют различные типы пылеулавливающих установок. Эти установки должны поглощать не менее 99 % выделяемой пыли, работать при температуре уходящих газов не менее 200°С, улавливать пыль с высоким содержанием водяных паров и отдельно крупные (более 100 мкм) и мелкие фракции пылевых частиц и возвращать их в асфальтобетонную смесь. В состав систем пылеулавливающих установок входят пылеуловители различного типа и конструкций с дымососами и газопроводами, пылеосадительные камеры для сбора пыли, устройства для подачи к дозаторам смесительных агрегатов.
В качестве первой ступени очистки для улавливания крупной пыли применяют пылеосадительные камеры и циклоны, установленные на всех отечественных асфальтосмесительных установках; в качестве второй ступени - системы мокрой очистки или тканевые фильтры. С целью повышения эффективности пылеочистки с помощью циклонов их очень часто объединяют в группы по нескольку штук.
На АБЗ установлен пылеулавливающий блок типа BMD – GARANT. Пылеулавливатель состоит из основных групп предварительного отделения (плоскостной охладитель) и тканевого фильтра. Проектирован для очистки горячих пылесодержащих выхлопных газов. Пылесодержащие выхлопные газы сушильного барабана проводятся через соединительный трубопровод предварительного отделения и поступают после этого к тканевому фильтру.
В плоскостном охладителе происходит охлаждение выхлопных газов. При этом выхлопные газы подводятся к внешним стенкам охладительных секций. При одновременной отдаче теплоэнергии атмосферный воздух, необходимый для охлаждения подаётся с помощью осевого вентилятора горизонтально через охладительные секции. Поток выхлопных газов проходит через охладительные секции вертикально сверху вниз и обратно. В точках поворота, в области фюзеляжа сборки пыли происходит отделение крупной пыли. Отделенная крупная пыль подводится транспортирующим червяком к концевому элеватору горячего материала.
В тканевом фильтре происходит отделение мелкой пыли за счет фильтрования выхлопных газов через фильтровальную ткань. При помощи установленных дистанционных матов внутри фильтровальных карманов проходят очищенные газы из передней части фильтровальных карманов в отсек очищенных газов.
Чистка отдельных фильтровальных карманов происходит обратной продувкой с помощью продувочного сопла от отсека очищенных газов, таким образом, обеспечивается постоянная загрузка плоскостного фильтра.
Отделённая мелкая пыль подводится в большинстве случаев посредством транспортирующего червяка концевого элеватора собственного наполнителя.
Техническое оборудование устройства предусмотрено таким образом, что может происходить автоматический режим работы. В это входит регулировка температуры группы охлаждения и предохранительного клапана свежего воздуха для защиты фильтровальных карманов от перегрева.
Очищенные газы проходят через соединительные трубопроводы в основной отсасывающий вентилятор и отсюда в камин выходящих газов.
Общий пылеулавливающий блок соответствует современному уровню техники безопасности и надзора. Он спроектирован таким образом, что требует минимального ухода, как, например обычный контроль чистки фильтровальных карманов и смазка транспортирующих червяков.
Дозаторы.
По способу (методу) дозирования в технологическом процессе приготовления смесей дозаторы делятся на дозаторы цикличного и непрерывного действия, а по принципу действия - на объемные и дозаторы по массе. Объемные дозаторы менее точны в работе, однако значительно проще по конструкции, не требуют систематической настройки и проверки. Они находят применение при дозировании каменных материалов в установках непрерывного действия и для дозирования битума.
Принцип действия порционного дозатора по массе цикличного действия основан на автоматическом уравновешивании массы материала, который находится в грузоприемном устройстве, квадрантным механизмом с циферблатным указателем. Питающие устройства дозаторов по массе могут быть различных типов, например без принудительной подачи материалов (гравитационные) или с принудительной подачей материалов (винтовые, вибрационные, ленточные). В качестве грузоприемных устройств дозаторов цикличного действия применяют бункера различной конструкции, а в дозаторах непрерывного действия - ленточные конвейеры. При этом материал подается сплошным потоком постоянной массы. Такие дозаторы применяют в
асфальтосмесительных установках непрерывного действия. В асфальтосмесительных установках цикличного действия для дозирования каменных материалов применяют дозаторы по массе цикличного действия с погрешностью дозирования ±2 %.
Рис. 2.8. - Дозатор по массе минеральных материалов:
1 — тарная гиря; 2 — тарная рейка; 3 — ограничить хода; 4 — весовая головка; 5 — регулировочный механизм; 6 — тяга; 7 — коромысло; 8, 11 — грузоподъемные рычаги; 9 — поперечная рейка; 10 — подвеска; 12 — подвесные серьги; 13 — весовой бункер; 14 — затвор.
На рис. 2.8 приведена схема дозатора по массе минеральных материалов. Весовой бункер 13 подвешен к нижней части верхнего блока смесительного отделения с помощью подвески 10 и системы грузоподъемных рычагов 8 и 11. Рычаги через коромысло 7, тягу 6 и тарную гирю 1 связаны с весовой головкой 4. В нижней части весового бункера смонтирован секторный затвор 14, с помощью которого отдозированную порцию материала подают в смеситель.
СТРОИТЕЛЬНАЯ ЧАСТЬ
Таблица 3.1 - Минимальные нормы запасов материалов
Наименование Материалов и изделий |
Автомобильным на расстояние | ||
свыше 50 км | До 50 км | ||
Битумы, деготь, битумные эмульсии, сталь арматурная, химические материалы | 25-30 | 15-20 | 12 |
Цемент, минеральный порошок, известь | 20-25 | 10-15 | 8-12 |
Щебень, гравий, песок, шлак, сборные железобетонные конструкции | 15-20 | 7-20 | 5-10 |
Максимальный запас - это предельное количество материалов, которое можно хранить на складах; определяется по формуле:
V 2 =Vo*m*K П, (3.2)
где V0 - общая потребность в данном материале на сезон (устанавливается расчетом, приложение 2);
m - максимальная норма хранения материалов;
принимается для привозных каменных материалов 0,3; при собственной заготовке в притрассовых карьерах – 0,5-0,7; для порошкообразных – 0,15-0,25; жидких органических вяжущих – 0,3; горюче смазочных – 0,10; лесоматериалов – 0,20;
Kп - коэффициент, учитывающий потери, равный 1,01-1,03.
Текущий запас V характеризует количество хранимого в данный момент материала. Очевидно, что
V1<=V<=V2
V - скорость ленты, м/с
Kt – коэффициент, учитывающий величину угла наклона конвейера приведён в табл. 3.2.
В зависимости от транспортера может быть лотковая и плоская.
лотковая F=0,11*В2; плоская F=0,6*В2; В - ширина ленты, определяется по формуле:
Таблица 3.2 – Зависимость угла наклона и коэффициента К t
Угол наклона транспортера | 0-10° | 11-15° | 16-18° | 18-22° |
Kt | 1,0 | 0,95 | 0,9 | 0,85-0,8 |
Для перемещения и подачи минерального порошка используем винтовые конвейеры, которые могут перемещать материалы на расстояние 40-50м. Они состоят из металлического желоба или трубы и вращающегося в ней винта, который установлен в промежуточных и упорных подшипниках. Винтовые конвейеры перемещают материал в горизонтальном направлении с уклоном < 20°. Наиболее распространенные шнеки d200, 400, 500мм.
Производительность шнекового конвейера определяется по формуле:
Q =60 * d * F * n * j; т/ч (3.6)
F= П d2/4 * K1 * K2
d - диаметр винта (150-600мм.);
K1 - коэффициент заполнения поперечного сечения (0,45);
К2 - коэффициент снижения наполнения (0,65-1,0),в зависимости от наклона;
j - шаг винта (0,8-1,0)d;
n - частота вращения винта 80 об/мин;
F - площадь поперечного сечения материалов в желобе:
F=3.14*0.5*0.5*0.45*0.65/4=0.057,м2
Q= 60 * 0,5 * 0,057 * 80 * 0,5 = 68,9 т/ч
Мощность двигателя винтового конвейера определяется по формуле:
N =0,003 Q * M +0,003 Lc б +0,02* K 3* qn * L * V * w, кВт (3.7)
М - высота подъема материала, м;
L - длина конвейера, м;
w - коэффициент трения (1,2 для неабразивного, 3,2 для абразивного);
qn - погонная масса вращающихся частей винтовых конвейеров (80);
К3 - коэффициент характеризующий перемещение рабочих органов (0,15);
V - весовая скорость перемещающихся материалов приведена в табл. 3.3:
V = S * n /60=0.5*80/60=0.67, м/с.
Для ленточного конвейера имеем:
Допустимый угол наклона зависит от рода транспортируемого материала:
Таблица 3.3 – Скорость и угол транспортёра в зависимости от рода транспортируемого материала
V, м/c | L, гpaд. | |
щебень | 2,5 | 18° |
песок | 3 | 18-20° |
ГПС | 2,5 | 18-20° |
B ≥ 2 dmax + 200,0 мм, где
dmax - максимальный размер транспортируемой фракции щебня;
В≥ 2 * 40 + 200 = 280 мм
F= 0,6 * 280 * 280 = 47040 мм2 = 470,4 см2
V= 2,5 м/с
Kt= 0,9
Q = 3600 * 0,047 * 2,5 * 0,9 = 380,7 мЗ/час
Потребляемая мощность определяется:
N =(Q * H + f * q * L + Q * V /2* q * n)/367,кВт (3.8)
Q - производительность конвейера, т/ч Q = 580,7 * 1,6 = 609,1 т/ч
Н - высота подъема материала 1,5-15 м;
L - длина конвейера 5,7-80,5 м;
f=0,05;
V=2,5 м/с;
n - коэффициент полезного действия 0,6;
q=9,81 м/с2
N = 609.1*4+.05*609.1*40+609.1*2.5/2*9.81*0.6)/367=10.84,кВт
Тепловой расчет битумохранилища.
Рис. 3.1 - Битумохранилище (склад битума):
1 - железнодорожный бункер; 2 - битум; 3 - приямок;
4 - битумопровод; 5 - битумный насос; 6 – нагреватель приямка.
Наглядный вид битумохранилища приведён на рис. 3.1.
Тепловой расчет битумохранилища включает:
а) Определение требуемого количества тепла и параметров нагревательных приборов. При этом следует установить количество тепла, полезно расходуемого для нагрева битума.
б) Определение потерь тепла при разогреве битума в битумохранилище.
в) Поверхность нагревательных приборов и необходимую длину труб.
г) Расход пара или электроэнергии и выбор источника тепла.
При двухступенчатой схеме нагрева битума расчет производится по каждой ступени отдельно. Сначала определяем расход тепла на разогрев битума в битумохранилище. Для обеспечения его отекания в приямок, затем расход тепла на разогрев в приямке для перекачки его по трубопроводу.
Количество тепла, необходимое для разогрева битума:
Q = Q1 + Q2 (3.9)
Q1 - тепло на плавление битума;
Q2 - тепло на подогрев битума в приямке.
Потери тепла при разогреве битума происходят от зеркала битума, через стенки и дно хранилища, от нагретого битума в приямке, от нагрева и испарения воды в битуме.
Полный расход тепла на предварительный разогрев битума:
Qxp = Q1 + Q2 + Q3 (3.10)
Q3 - потери тепла.
Полный расход тепла для разогрева битума в приемнике:
Qnp = Q4 + Q5 (3.11)
Q4 - количество тепла, необходимое для разогрева битума в приемнике;
Q5 - потери тепла при этом
Полный расход тепла в отсеке битумохранилища:
Qn = Qxp + Qnp (3.12)
Проектируемый АБЗ должен изготавливать в смену 1596,4т. а/б смеси. При максимальном расходе битума 5,61 на 100т. а/б смеси в час.
Сменная потребность в приготовлении битума 15,964 * 5,61 ~ 90т.
В соответствии с типовыми проектами, при 30 дневном нормативном запасе битума:
ёмкость битумохранилища 30 * 90 = 2700т.
Принимаем битумохранилище емкостью 3000т, состоящее из 6-х секций по 500т каждая с донным подогревом.
Разогрев битума в битумохранилище производим в два этапа:
1-й этап - разогрев битума донными нагревателями уложенными на дне хранилища до 60°С.
2-й этап - разогрев битума в приямке до 90°С.
Нагретый до этой температуры битум с помощью насоса, установленного в приёмке, перекачивается в битумоплавильные котлы.
Q1= G* C*(t1- t2)* n* Nb/ T p =3000*1765*(80-0)*1,15*2/4=121,785,МДж (3.13)
где
G - количество битума, разогреваемое в вагоне;
С - теплоемкость битума 1765кДж/кг*°С;
t2 - конечная температура, при которой возможна разгрузка битума 80°С;
t1 - начальная температура битума: летом +10°С, зимой –10°С
n - коэффициент теплопотерь 1,15;
Nb - количество одновременно разгружаемых вагонов;
Тр - время разгрузки вагона 4ч.
P2=Q2/q (3.14)
Для разогрева в хранилище определяют количество тепла для предварительного разогрева битума и количество тепла, необходимого для плавления битума.
Определение количества тепла для предварительного разогрева битума.
Q2’ = G*C б *(t2-t1) (3.15)
где
G - производительность битумохранилища;
Сб - теплоемкость битума 1,47 кДж/кг;
t2 - конечная температура текучести битума 60°С;
t1 - начальная температура 10°С;
Q2' = 11500 * 1,47 * (60-10) = 845250,кДж/ч = 845,25,МДж/ч
Количество тепла, необходимое для плавления битума.
Q2" = m * G (3.16)
где
m - скрытая теплота плавления 126 кДж/ч;
Q2" = 126 * 11500 = 1449000 кДж/ч =1449,МДж/ч
Потери тепла в окружающую среду при нагреве битума в резервуаре:
Q 2"'= L дн * F дн * (t 1- t 0) + L бит * (t2-t1) * F б (3.17)
Lдн - коэффициент теплоотдачи от битума ко дну хранилища 0,465 Вт/м2 *С°;
Fдн - площадь дна битумохранилища;
Fб - площадь битумохранилища;
t0 - температура дна хранилища;
t2 - температура нагрева битума в момент его отекания в приямок 60°С;
t1-температура стенок t1 = t0 = 10°С;
Lбит - коэффициент теплоотдачи в вышележащие слои битума 0,73 Дж/м2*C°
Fб - площадь битумохранилища
Q 2'" = 0,463 * 750 * (60-10) + 0,73 * (60-10)*750 = 44737,5 кДж/ч = 44.7375,МДж/ч
Определяем полный расход тепла для разогрева битума в хранилище:
Qxp = Q 2’ + Q2" + Q2'" = 845.25 + 1449 + 44.7375 = 2338,9875,мДж/ч
Площадь приямка 10-15 м2.
Расход тепла для нагрева битума в приямке:
Q2"" = G * Сб * (t 3 - t 2) = 11500 * 1,47 * (90-60) = 507150,кДж/ч = 507,15,МДж/ч
G - часовая производительность битумохранилища;
Сб - теплоёмкость битума;
t3 - температура битума в приямке при которой возможна перекачка 90°С.
Потери тепла в приямке:
Q2"'" = L дн * F дн *(t 3- t 0) + Lc т * Fc т * (t 3- t 0) + L зер * F зер * (t 2- t 1)
Q2'"" = 0,463 * 15 * (90-10) + 25,6 * 62 * (90-10) + 0,057 * 15 * (90-10) = =127600 кДж/ч = 127,6,МДж/ч;
L cт – коэффициент теплоотдачи через стенку приямка L ст = 25,6кДж/м2*ч*°С
Fст - площадь стенок приямка;
Lзер - коэффициент теплоотдачи от битума воздуху 0,0663 Вт/м2*°С;
Fзер=15,м2
Определяем количество тепла для нагрева битума в приемнике:
Qnp = Q2"" + Q2"'" = 507,15 + 127,6 = 634,75,МДж/ч
Общий расход тепла для работы битумохранилища:
Q2 = Q2' + Q2" + Q2'" + Q2"' + Q2"" + Q2""' Q2 = 2338,9875 + 634,75 = =2973,7375,МДж/ч = 708032,7 кКал/ч (1 кКал=4,2кДж)
Расход пара для нормальной работы битумохранилища:
N= Q2/q= 708032.7/662.3=1069.1,кг,
где
q - теплосодержание пара 662,3 кКал/кг.
Поверхность нагрева паровых труб для нагрева днища битумохранилища:
Fнагр= Q хр/(К*((Tk + T 0)/2-(t 1+ t 2)/2)) (3.18)
Fнагр = 2338987,5 / (168 * (169,6 + 119,6) / 2 - (10 + 60) / 2) = 127 кВ(м2)
Тк - температура насыщения пара при данном давлении (0,8МПа - 169,6°С) То T0 - температура конденсата (0,2МПа - 119,6°С);
К - коэффициент теплопередачи через стенки стальных труб (168кДж/м2 ч °С при t < 100°С);
Принимаем трубы d 250 мм, тогда необходимая длина трубы:
L тр = F нагр/ f (3.19)
f = П * D * I = 3,14 * 0,25 * 1 = 0,393
Lтp = 127 / 0,785 = 161.8 = 162 м.
Определение количества битумоплавильных установок.
Битумоплавильные установки предназначены для плавления, обезвоживания и нагрева битума до рабочей температуры.
Для битума БНД 40/60 60/90 - t = 140-160°С, для БНД 90/130 - t = 130-150°С
Битумоплавильные установки могут быть стационарными и передвижными, периодического и непрерывного действия технические характеристики для некоторых из них приведены в табл. 3.4.
Таблица 3.4 - Технические характеристики битумоплавильных установок.
Показатели | ДС-17 | ДС-28А | ДС-45 | ДС-81 | ДС-6 |
Тип агрегата | непрерывного действия
| ||||
Расход котлов, м3 | 30*2 | 30*2 | 30*3 | 30*5 | 10,2 |
Производительность т/час | 3 | 6 | 10 | 16,5 | 0,25-0,6 |
Расход топлива при влажности битума до 5% кг/час | до 40 | До 45 | до 102 | До 105,5 | 26 |
Мощность электродвигателей | 17,1 | 19,5 | 24,5 | 35,9 | 9,6 |
Мощность электронагревателей | нет | 176 | 189 | 90 | нет |
Суточная потребность в битуме АБЗ определяется исходя из max выпуска а/б смеси:
Пб=(Р*Б)/100,т (3.20)
Р. – сменный выпуск а/б смеси, т.
Б – содержание битума в смеси % (5,61%)
Количество битумоплавильных котлов:
N к=(Пб*Кп)/Пк (3.21)
Кп – коэффициент неравномерности потребления битума (1,0 –1,2);
Пк – производительность котла;
Пк=(Т*60*Кв* Vk *Кн)/(t 3+ tm + tb),т/ч (3.22)
Vk – геометрическая емкость котла, м3;
Кн – коэффициент наполнения котла (0,75 – 0,8);
Кв – коэффициент использования котла во времени (0,85 - 0,9);
t3 – время на заполнение котла, мин.
t 3=(Vk * K н)/Пн =60*0,8/0,8=60,мин
Пн – производительность насоса при загружении котла.
Д.-171А — Пн = 400 л/мин.
Д.-379 — Пн = 800 л/мин.
Д.-725 — Пн = 500 л/мин.
tн – время для выпаривания и нагрева битума до рабочей температуры (4-5) ч. tb – время выгрузки битума из котла (4-5) ч.
Т – количество часов работы установки в сутках.
Пб=(Р*Б)/100 =5,61*1596,4/100=89,56, т
Пк=8,2*60*0,85*0,8/(0,88+4,5+4,5)=33,86 т/смен
Пк = 89,56/33,86 = 2,64 ~ 3шт.
Для работы АБЗ необходимо 3 битумоплавильных установки ДС-17 (Д. - 506).
Расчет потребности энергоресурсов на АБЗ.
В состав энергети
|
|
Двойное оплодотворение у цветковых растений: Оплодотворение - это процесс слияния мужской и женской половых клеток с образованием зиготы...
Археология об основании Рима: Новые раскопки проясняют и такой острый дискуссионный вопрос, как дата самого возникновения Рима...
История развития хранилищ для нефти: Первые склады нефти появились в XVII веке. Они представляли собой землянные ямы-амбара глубиной 4…5 м...
Поперечные профили набережных и береговой полосы: На городских территориях берегоукрепление проектируют с учетом технических и экономических требований, но особое значение придают эстетическим...
© cyberpedia.su 2017-2024 - Не является автором материалов. Исключительное право сохранено за автором текста.
Если вы не хотите, чтобы данный материал был у нас на сайте, перейдите по ссылке: Нарушение авторских прав. Мы поможем в написании вашей работы!