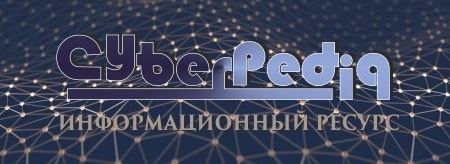
Организация стока поверхностных вод: Наибольшее количество влаги на земном шаре испаряется с поверхности морей и океанов (88‰)...
Индивидуальные и групповые автопоилки: для животных. Схемы и конструкции...
Топ:
Когда производится ограждение поезда, остановившегося на перегоне: Во всех случаях немедленно должно быть ограждено место препятствия для движения поездов на смежном пути двухпутного...
Теоретическая значимость работы: Описание теоретической значимости (ценности) результатов исследования должно присутствовать во введении...
Интересное:
Средства для ингаляционного наркоза: Наркоз наступает в результате вдыхания (ингаляции) средств, которое осуществляют или с помощью маски...
Наиболее распространенные виды рака: Раковая опухоль — это самостоятельное новообразование, которое может возникнуть и от повышенного давления...
Влияние предпринимательской среды на эффективное функционирование предприятия: Предпринимательская среда – это совокупность внешних и внутренних факторов, оказывающих влияние на функционирование фирмы...
Дисциплины:
![]() |
![]() |
5.00
из
|
Заказать работу |
|
|
Месторождения разрабатываются в основном, с применением систем разработки горизонтальных слоев с твердеющей закладкой. Небольшой объем составляют камерные системы разработки с твердеющей закладкой.
Очистные блоки имеют ортовую кольцевую подготовку. К горно-подготовительным работам при сплошной слоевой системе разработки с нисходящей выемкой слоев относится проведение на каждом основном горизонте кольцевых откаточных штреков, откаточных ортов, блоковых восстающих, рудоспусков, заездов на них, а также проходка вентиляционно-закладочных восстающих. Кроме этого на каждом слое проходится слоевой орт.
К нарезным относятся выработки в границах рудных залежей: сбойки, заезды, ниши, загрузо-разгрузочные камеры и т. п. Минимальный объем нарезных выработок определяется параметрами радиуса разворота применяемого оборудования.
Проходка горизонтальных подготовительных и горно-капитальных выработок откаточных горизонтов производится комплексами оборудования, состоящими из установок ЛКР-1У, УПБ, а также буровых кареток УБШ, погрузочных машин ППН-1С, ППН-3, вагонеток ВГ-4с и электровозов К-10. Проходка вертикальных выработок (до 80%) производится комбайнами 2КВ и частично вручную буровзрывным способом и с помощью КПВ-4А.
Крепление выработок весьма разнообразно и зависит от крепости, устойчивости пород и от характера горного давления. В основном используется набрызгбетонная крепь с толщиной в среднем 50мм, особо опасных местах применяется податливая металлическая крепь СВП-17. Также в шахте используется анкерная крепь, деревянная крепь НДО и комбинированные крепи.
Проведение выработок осуществляется с применением буровзрывных работ с использованием взрывчатого вещества Аммонала М-10 и Аммонита 6ЖВ. Способ взрывания – система ИСКРА.
|
Таблица 3 - Характеристика горно-подготовительных выработок
№ п/п | Наименование | Сечение | Вид крепи | Оборудование для их проходки |
1 | Квершлаг | 8,4 | Б/к, СВП17 торкет | ППН-1С, УБШ |
2 | Штрек | 7,8 | Б/к, СВП17 торкет | –//– |
3 | Орт | 7,8 | –//– | –//– |
Система разработки
На руднике при добычи ПИ используется система разработки – нисходящая слоевая выемка с твердеющей закладкой (рисунок 4).
Применяемая система разработки имеет следующие параметры: высота блока – 60 м; длина блока – 100…200 м; ширина блока – равна мощности рудной залежи; высота слоя – 3…3,5 м; ширина заходок – до 4 м; угол наклона заходок – 3…5 °.
Система разработки нисходящей слоевой выемкой с твердеющей закладкой – это система разработки с искусственным поддержанием очистного пространства, при которой блок отрабатывается горизонтальными, слабонаклонными слоями, начиная с верхнего. Каждый слой вынимают под искусственной кровлей из затвердевшего закладочного массива и заполняют твердеющей закладкой по мере отработки.
Эта система разработки предназначена для выемки неустойчивых ценных руд, особенно при высокой возгораемости руд или при необходимости поддержания земной поверхности. Вмещающие породы могут быть любой устойчивости.
Слои отрабатывают заходками, которые проходят из штреков, нарезанных по границе блоков. Заходки проводят с подъёмом, а закладывают с противоположной стороны, т.е. под уклон, что обеспечивает заполнение смесью пространство под кровлей.
Очистные блоки имеют ортовую кольцевую подготовку, блок готовится на откаточном горизонте двумя полевыми штреками и центральным ортом. Горизонты сбиваются блоковыми восстающими и рудоспусками.
Блок отрабатывают горизонтальными слоями, начиная с верхнего под защитой искусственной кровли, которую для каждого очередного слоя образуют из твердеющей закладки по мере выемки вышележачего слоя. Выемка первого слоя блока, а также очистных заходок на других слоях, при несовпадении контуров рудных тел отрабатываемого слоя с контурами вышележачего слоя производится под естественной кровлей. Отработка запасов слоя производится одинарными или спаренными заходками высотой 3…3,5 м по обе стороны от разрезного слоевого орта. Зарезку слоя осуществляют из рудоспуска или восстающего, или по уклону из слоевой выработки. Очистные работы включают отбойку рудного массива, уборку рудной массы в рудоспуски, проветривание и крепление очистного пространства, выпуск и погрузку рудной массы из рудоспусков, установку в отработанных заходках изолирующих перемычек и заполнение выработанного пространства твердеющей закладкой.
|
Отработка слоевых заходок ведется буро-взрывным способом, бурение шпуров производится установками ЛКР-1У и УПБ, а также буровыми каретками УБШ-211 и МИНИБУР 1ФЭ. Проветривание заходок осуществляется вентиляторами местного проветривания ВМ-6 на один магистральный трубопровод D=600 мм.
Рисунок 4 - Система разработки нисходящая слоевая выемка с твердеющей закладкой
Для доставки горной массы в блоках используется в основном погрузочно-доставочные машины ПД-2Э и MICROSCOOP 100E. Крепление очистного пространства в зависимости от прочности и структуры закладочного массива осуществляется рамами НДО, подвесной крепью или контрольными стойками из расчета 20 м2 обнажения кровли на стойку. Кроме того, предусматривается армировка заходок перед закладкой с образованием подвесной крепи, связывающей между собой все заложенные по вертикали заходки и укладкой металлической сетки на почву выработки и ее креплении.
Горная масса из блока доставляется ПДМ до рудоспусков оборудованных вибропитателями типа ПВ-1,2/3,1, емкость рудоспусков до 100 м3 горной массы. Транспортирование горной массы от рудоспусков к выдачным шахтным стволам 8к, 9к, 3р, 3в, 5В осуществляется контактными электровозами К-10 в вагонетках ВГ-4с ёмкостью 2м3.
Погашение выработанного пространства в блоке производится твердеющей закладкой по мере отработки слоевых заходок. Закладку заходок производят секциями, длина секции для жестких и расслаивающихся смесей составляет 15 м (объем секции около 150…200 м3), секции отделяются изолирующими перемычками. Погашению подлежат все горизонтальные слоевые выработки, полнота закладки выработанного пространства должна быть не менее 85 % по объему. Закладочный материал подается с закладочного комплекса на поверхности, по трубопроводам через восстающие в закладочные орты и далее в очистные заходки. Контроль прочности твердеющей закладки осуществляется электрометрическими датчиками контроля прочности.
|
Закладочные работы ведутся согласно технологическим картам на отработку слоя. Сначала заходку на высоту 1,5м заполняют твердеющей закладкой, содержащей 20% цемента, а верхнюю часть – 9% цемента. Смежные заходки отрабатывают при прочности закладки не менее 0,7…1 МПа, а заходки, расположенные под закладкой, разрабатывают при прочности не менее 2,7…3 МПа. Такая прочность достигается через 7…20 суток. Расход компонентов закладочной смеси на 1м3: цемент М400 – 10 кг; ПГС – 1465 кг; вода – 310 кг. Для транспортабельности смеси используют золу.
Средняя производительность блока при системе горизонтальные слои с твердеющей закладкой 1800 м3/мес с учетом нарезных и закладочных работ. Потери руды составляют 3…5 %, разубоживание определяется в зависимости от мощности рудного тела, ширины очистной заходки и содержания металла в руде и колеблется от 6 до 50 %.
Закладочные работы в блоке
Выработанное пространство заполняют смесями, которые состоят из вяжущих материалов, инертных заполнений, добавок и воды, имеют высокое водоцементное (водо-вяжущее) отношение, обладают достаточной пластичностью для транспортировки по трубам и способны с течением времени затвердевать с образованием монолитного массива относительно невысокой прочности (»9,8Мпа). Такие закладочные смеси называют твердеющими.
Применение твердеющей смеси даёт возможность решать ряд сложных горнотехнических проблем – совмещать разработку месторождения открытым и подземным способами; вести безопасную разработку пожароохранных мероприятий; обеспечивать сохранность земной поверхности от сдвижений; вести выемку руды в охранных целиках; осуществлять опережающую разработку наиболее ценных руд; утилизировать и складировать под землёй отходы производства.
|
За последние время твердеющая закладка стала преобладающим видом закладки, поскольку её применения позволяют: обеспечить полноту отработки действующих месторождений, т.е. вести добычу руды при относительно небольших затратах в сравнении с удельными капитальными вложенными на строительство новых рудников в труднодоступных необжитых районах; удовлетворять повышенным требованиям и охране окружающей среды; вести закладочные работы на индустриальной основе, т.е. с высокой производственностью и высокой степенью механизации и автоматизации.
Производство закладочных работ осуществляется по рабочим проектам, утверждённым главным инженером рудоуправления (рудника). После отработки очистных заходок (участков) в слое, выработанное пространство должно быть заполнено твердеющей закладочной полостью. В проекте на закладочные работы должны быть предусмотрены мероприятия, обеспечивающие наибольшую полноту заполнения пустот.
Угол наклона слоевых выработок и очистных заходок выбирается так, чтобы статическая высота напора закладочной смеси на перемычку не превышала 6 м.
Перед вводом твердеющей закладки из закладочной выработки должна быть удалена вода, почва зачищена от отбитой руды и мусора.
Закладочные работы (ввод закладки) должны быть начаты не позднее, чем через 10 календарных дней после окончания очистных работ на закладываемом участке рабочего слоя.
Превышение установленного срока допускается с разрешения главного инженера рудника.
Передача очистных участков слоя под закладку и их приёмку после закладки производит постоянно действующая комиссия рудника, при этом составляются следующие документы:
– акты о передачи участка слоя под закладку;
– акт возврата заложенного участка.
Акты передачи и возврата утверждаются председателем комиссии. Подача закладочной смеси в очистное пространство должна осуществляться без перерывов. Перерывы в подаче закладки более 30 мин подлежат учёту в специальном журнале на закладочном комплексе. Вода от промывки закладочных трубопроводов не должна поступать в очистное пространство, она должна сбрасываться в предусмотренные проектом выработки (камеры).
В случае невозможности такой организации работ объём подаваемой для очистки трубопровода воды должен регламентироваться в зависимости от длины трубопровода и не превышать 3 м3 на одну промывку.
Запрещается на время подачи закладки в блок находиться вблизи изолирующих закладочных перемычек, расположенных в нижней части наклонных закладочных выработок, перемещаться по в/с, которые перекрыты перемычками или имеют выход к выработкам, в которых установлены указанные перемычки.
|
Очистной блок во время закладочных работ должен находиться под постоянным контролем бригадиром или обученного квалифицированного рабочего, имеющих прямую телефонную связь с закладочной установкой. Место нахождения этих людей определяется проектом на производство закладочных работ и указывается в акте на передачу блока под закладку. Работающие на закладке должны пользоваться защитными средствами (очки, щитки).
Осмотр состояния закладочных перемычек осуществляется лицом надзора после прекращения подачи закладки в блок.
Мероприятия по обеспечению полноты заполнения пустот и наименьшей расслаеваемости твердеющей закладки
1. Закладочные выработки (штреки, орты) должны располагаться выше кровли рабочего слоя.
2. Очистные заходки длиной 15…30 м находятся под углом 3…5°.
3. Расстояния подачи закладочного материала в блоке самотёком не должно превышать 20м.
4. При длине отчистных подготовительных выработок более 20м, закладку их необходимо вести с двух точек или секционно.
5. Очистные заходки, слоевые штреки (орты) длиной до 15м разрешается проходить горизонтально.
6. При отработке запасов в охранных целиках подготовительно нарезные выработки находятся под углом 5…8°.
ГОРНО-МЕХАНИЧЕСКАЯ ЧАСТЬ
Внутришахтный транспорт
Для транспортирования горной массы по откаточным выработкам используется электровоз К-10 и вагонетки ВГ-4с. Ширина колеи 750 мм. Тип рельс – Р-33.
Электровозы К-10 по сравнению с машинами тех же сцепных весов значительно улучшены. В ходовой части используются электродвигатели ЭТ-31 (31кВт) с повышенным классом изоляции и улучшенной эксплуатационной характеристикой. Рама электровозов приспособлена для монтажа буфера. Конструкция прицепного устройства позволяет разворачивать головку автосцепки как в горизонтальной, ток и в вертикальной плоскости. Вместо автосцепки может быть установлена штыревая сцепка.
Шахтные вагонетки с глухим неопрокидным кузовом типа ВГ-4С предназначена для транспортирования породы по подземным горным выработкам и на поверхности шахты. Кузов вагонетки сворной конструкции из двух штампованных лобовин и полукруглого днища с боковинами. Рама вагонеток клёпано-сварной конструкции выполнена из двух продольных швеллеров с отогнутыми полками стальных литых кронштейнов.
Рельсовый путь состоит из верхнего и нижнего строения. Верхнее строение постоянного рельсового пути включает в себя рельсы и элементы крепления рельсов между собой и закрепления их к шпалам, шпалы и балластный слой, а также стрелочные переводы. Нижним строением является почва выработки с водоотливной канавки.
Шпалы связывают обе нитки рельсового пути и распределяют массу состава, передаваемую на рельсы на большую площадь. Длина шпал – 1500мм, толщина – 120…180мм, ширина по верху – 100…160мм, по низу – 190…260мм. Расстояние между шпалами – 0,4…0,7мм. Укладывают шпалы на балласт из гальки или щебня. Толщина балласта под шпалами должна быть не менее 100мм. Балласт облегчает правильную укладку шпал.
Между рельсами и шпалами устанавливаются подкладки, через отверстия которых проходят костыли скрепляющие рельсы со шпалами. Зазоры между колёсами и рельсами должны быть до 10 мм.
Высота подвески контактного провода – 1800 мм. Минимальный зазор между проводом и крепью – 200 мм. В выработках околоствольного двора высота подвески контактного провода – 2000…2200 мм.
Шахтный подъём
Комплекс спуска (подъёма) состоит из двух независимых зданий. В здании подъёмной машиной расположен барабан 2Ц6х2.4, пульт управления и механический привод. Движение клетей производится подъёмной машиной с помощью подъёмных канатов, переброшенные через направляющие шкивы на копре. При вращении двигателем органов навивки канатов, один канат навивается, а другой свивается с них, благодаря чему происходит одновременный подъём одной клети и спуск другой.
Скорость спуска и подъёма людей составляет 6 м/с, управление осуществляется оператором с пульта управления на который выводится вся информация. Шахтный ствол имеет диаметр 6 метров. Крепление ствола – бетонное с металлической армировкой.
Для обеспечения требуемой годовой производительности в эксплуатации находятся двухклетьевые подъёмные установки стволов 8К, 9К, 3Р, 3В, 5В. Подъем горной массы осуществляется по вертикальным стволам оборудованным 2х-клетьевыми подъемами в вагонетках ВГ-4м.
Поверхностный разгрузочно-обменный комплекс выполнен в надшахтном здании на отметках +14,+16,+18 м и состоит из комплекса оборудования для разгрузки вагонеток. Выданная на поверхность горная масса разгружается в 4 приемных бункера специальным перестановочным бункером-распределителем на рельсовом ходу. Ёмкость бункеров по 40м3 обеспечивает 2,5 часовую работу подъема в полуавтоматическом режиме.
Определение сортности горной массы производится повагонно в рудоконтролирующих станциях РКС на поверхностных разгрузочно-обменных комплексах шахтных стволов с последующей разгрузкой каждой вагонетки в соответствующий бункер и погрузкой из бункеров в автосамосвалы. Доставка руды, породы и забалансовых руд на отвалы и ГМЗ осуществляется автомобилями БелАЗ 7522, КрАЗ-256 и МАЗ-5549.
Таблица 4 - Характеристика подъёмных установок
Техническая характеристика | Ед. изм |
С т в о л ы | ||||
2К | 3Р | 3В | 8К | 9К | ||
Глубина подъёма Подъём. машина Мощн. двигателя Скорость движения Время подъёма груза Производительность: в сутки в год Расчётная производит-ть в год | м кВт м/с час ваг тонн ваг тонн тыс. т | 260 2Ц6х2.4 2300 8 14 393 864 118000 260000 300 | 395 2Ц6х2.4 1300 8 14 727 1600 222000 490000 830 | 396 2Ц6х2.4 1300 8 18 700 1550 200000 400000 830 | 395 2Ц6х2.4 1300 8 18 890 1960 273000 600000 890 | 500 2Ц6х2.4 1800 8 18 540 1000 154000 340000 750 |
|
|
Биохимия спиртового брожения: Основу технологии получения пива составляет спиртовое брожение, - при котором сахар превращается...
Автоматическое растормаживание колес: Тормозные устройства колес предназначены для уменьшения длины пробега и улучшения маневрирования ВС при...
Опора деревянной одностоечной и способы укрепление угловых опор: Опоры ВЛ - конструкции, предназначенные для поддерживания проводов на необходимой высоте над землей, водой...
Папиллярные узоры пальцев рук - маркер спортивных способностей: дерматоглифические признаки формируются на 3-5 месяце беременности, не изменяются в течение жизни...
© cyberpedia.su 2017-2024 - Не является автором материалов. Исключительное право сохранено за автором текста.
Если вы не хотите, чтобы данный материал был у нас на сайте, перейдите по ссылке: Нарушение авторских прав. Мы поможем в написании вашей работы!