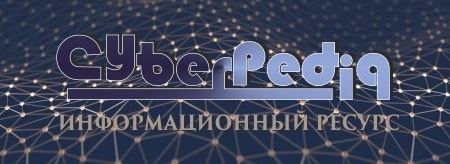
Общие условия выбора системы дренажа: Система дренажа выбирается в зависимости от характера защищаемого...
Архитектура электронного правительства: Единая архитектура – это методологический подход при создании системы управления государства, который строится...
Топ:
Комплексной системы оценки состояния охраны труда на производственном объекте (КСОТ-П): Цели и задачи Комплексной системы оценки состояния охраны труда и определению факторов рисков по охране труда...
Организация стока поверхностных вод: Наибольшее количество влаги на земном шаре испаряется с поверхности морей и океанов...
Процедура выполнения команд. Рабочий цикл процессора: Функционирование процессора в основном состоит из повторяющихся рабочих циклов, каждый из которых соответствует...
Интересное:
Инженерная защита территорий, зданий и сооружений от опасных геологических процессов: Изучение оползневых явлений, оценка устойчивости склонов и проектирование противооползневых сооружений — актуальнейшие задачи, стоящие перед отечественными...
Отражение на счетах бухгалтерского учета процесса приобретения: Процесс заготовления представляет систему экономических событий, включающих приобретение организацией у поставщиков сырья...
Наиболее распространенные виды рака: Раковая опухоль — это самостоятельное новообразование, которое может возникнуть и от повышенного давления...
Дисциплины:
![]() |
![]() |
5.00
из
|
Заказать работу |
|
|
Назначение флюса | Состав, % по массе | |||||
NaCl | KCl | Na3AlF6 | MgCl2KCl | NaF | CaF2 | |
Покровно-защитный для переплавки отходов и стружки | 39 | 50 | 6,6 | – | – | 4,4 |
50 | 35 | 15,0 | – | – | – | |
40 | 50 | – | – | 10 | – | |
Для рафинирования сплавов систем Al-Si, Al- Si -Mg, Al-Cu, Al-Si-Cu | 30 | 47 | 23,0 | – | – | – |
Для рафинирования сплавов систем Al-Mg, Al-Mg-Si, Al- Mg- Zn | – | – | – | 80 | – | 20,0 |
– | – | – | 60 | – | 40,0 |
Покровный флюс (2-3 % от массы шихты) сразу же после загрузки шихты в печь засыпается на ее поверхность. Флюс предохраняет поверхность расплава от окисления и взаимодействия с газами печной атмосферы.
Соли, входящие в состав флюсов, следует предварительно просушивать при температуре 150-200 °С (для удаления гигроскопической влаги) и размалывать.
Широкое применение нашли покровно-рафинирующие флюсы с повышенным содержанием фторидов. Эти флюсы не только защищают расплав от воздействия атмосферы, но и способствуют его дегазации и очистке от оксидных включений.
Рафинирующее воздействие флюсов заключается в том, что они способны адсорбировать до 10 % по массе окcида алюминия. При этом происходит и дегазация расплава, так как водород, образующий комплексы с оксидом алюминия, удаляется вместе с частицами Al2O3. Основной рафинирующей солью большинства флюсов является криолит Na3AlF6.
Сплавы с повышенным содержанием магния в качестве неметаллических включений содержат, в основном, оксид магния, на который криолит не оказывает адсорбирующего воздействия. MgO хорошо адсорбируется хлористым магнием, поэтому рафинирование сплавов на основе системы Al-Mg производится флюсом, содержащим карналлит MgCl2×KCl.
Покровно-рафинирующий флюс (табл.1) в количестве 0,1-0,2 % от массы шихты засыпается на поверхность расплава. При температуре рафинирования производится замешивание флюса в глубь расплава для более полного взаимодействия с металлом. Время замешивания и последующего отстаивания расплава под флюсом устанавливается опытным путем.
|
Все адсорбционные методы рафинирования обладают одним общим недостатком: рафинирующие газы практически не могут охватить весь объем рафинируемого металла и очищают только те участки расплава, через которые они проходят.
Особую группу составляют универсальные флюсы, оказывающие одновременно защитное, рафинирующее и модифицирующее воздействие на сплавы (табл.2).
Таблица 2
Состав универсальных флюсов
Номер флюса | Состав, % по массе | Температура модифицирования, °С | |||
NaF | NaCl | KCl | Na3AlF6 | ||
1 | 60 | 25 | - | 15 | 800-820 |
2 | 40 | 45 | - | 15 | 750-780 |
3 | 30 | 50 | 10 | 10 | 720-740 |
Введением в расплав небольших количеств металлов или их лигатур органических или неорганических соединений можно существенно повлиять на процесс кристаллизации сплавов. В зависимости от природы и количества модификаторов, а также скорости кристаллизации можно достигнуть значительного измельчения зерен твердого раствора основы сплава или первичных кристаллов вторых фаз, или эвтектики, или всей структуры сплава. Например, сплавы, содержащие более 7 % кремния (рис.2); после рафинирования перед разливкой в формы рекомендуется подвергать модифицированию для получения мелкозернистого строения эвтектики a + Si с целью повышения механических свойств сплавов. Для модифицирования эвтектики применяется натрий, который обычно вводится в сплав из смеси галоидных солей натрия и калия.
|
При оптимальном содержании в сплаве натрия (0,08-0,1 %) из жидкости кристаллизуется тройная эвтектика. При этом фазой, ведущей кристаллизацию тройной эвтектики, является алюминий. Дендриты алюминия захватывают в процессе роста кристаллы кремния. В отличие от двойной эвтектики a + Si, где кремний кристаллизуется в грубой, пластинчатой форме, в тройной эвтектике a + Si + NaAlSi4 он кристаллизуется в виде мелких округлых частиц, что способствует повышению прочности и особенно пластичности сплава.
|
Введение в расплав натрия осуществляется при взаимодействии плавящегося модификатора (смеси солей) с расплавом по реакции
3NaF + Al = AlF3 + 3Na.
Предварительно переплавленный, размолотый и просеянный модификатор в количестве 1,5-2 % от массы шихты насыпается на поверхность расплава. Расплав выдерживается под флюсом в течение 10-12 мин.Затем флюс замешивается в расплав на глубину 100-150 мм в течение 2-3 мин.Время после окончания модифицирования до конца разливки сплава не должно превышать 25-30 минво избежании выгорания натрия.
Применение тройного модификатора (62,5 % NaCl, 25 % NaF и 12,5 % KCl) позволяет снизить температуру модифицирования до 725-740 °С.
Лабораторное оборудование. Электрическая печь, нагреватели для сушки шихты и флюсов, вспомогательное оборудование для брикетирования мелких отходов и измельчения флюсов, лабораторный микроскоп и химико-аналитическое оборудование.
Содержание задания. Сведения об используемых шихтовых и флюсовых материалах, рекомендации по технологии плавки, составу и количеству конечного сплава.
Порядок работы
1. В соответствии с заданием выбрать и обосновать технологический режим, необходимый для заготовительно-рафинировочной плавки указанных материалов.
2. Провести расчет количества отдельных компонентов шихты для приготовления сплава данного состава или вторичного алюминия.
3. Для принятой технологической схемы плавки приготовить необходимое количество флюса и модификатора.
4. Мелкие компоненты шихты окусковать путем проковки или брикетирования.
5. Плавильный тигель разогреть вместе с электропечью до необходимой температуры. Контролируя температурный и временной режим, провести плавку шихты и рафинирование расплава.
6. По окончании плавки разлить металл с получением слитка в металлической изложнице или отливки в разъемной металлической форме – кокиле. Разливка металла производится в присутствии преподавателя с соблюдением необходимых мер техники безопасности и противопожарной безопасности. Металлические формы должны быть предварительно очищены от нагара и ржавчины, а также подогреты до температуры 150-200 °С.
|
7. После охлаждения отливки механически очистить ее от шлака и остатков флюса и взвесить. Определить выход годного металла и его угар.
8. Выполнить микроскопическое исследование отливки и сделать заключение о наличии неметаллических примесей и особенностях кристаллической структуры.
9. Провести химический анализ сплава на содержание железа (по указанию преподавателя).
|
Цель работы. Знакомство с технологией производства углеграфитовых изделий и количественной оценкой их устойчивости при электролизе в условиях катодной поляризации.
Основные определения, теория и технология
При электролизе расплавленных сред возникает необходимость обеспечения высокой коррозионной устойчивости и электропроводности ряда конструкционных материалов. Во многих случаях незаменимым материалом становится углерод различных модификаций и изделия на его основе. Из углеграфитовых материалов изготавливают электроды и детали футеровки электролизных ванн в производстве алюминия, магния и других легких металлов.
Основной фактор разрушения угольных анодов – окисление воздухом и выделяющимися газами. Причиной разрушения катодных блоков является их взаимодействие с электролитом и выделяющимися металлами. Обеспечить устойчивую работу углеграфитовых изделий можно за счет улучшения их характеристик в момент изготовления, оптимизации технологического режима электролиза и совершенствования конструкций электролизеров.
В производстве электродов применяют твердые углеродистые материалы, составляющие основу, или «скелет», электрода, и связующие вещества, заполняющие промежутки между зернами твердых углеродистых материалов и соединяющие эти зерна между собой при коксовании в процессе обжига (рис.1).
Согласно современным представлениям, существует несколько аллотропических форм кристаллического углерода: алмаз, графит и фуллерен. Так называемый «аморфный» углерод (угли, антрацит, коксы, сажа и т.д.) не имеет кристаллической структуры.
|
Основу пространственной кристаллической решетки графита (рис.2) составляют плоские сетки, в которых атомы углерода образуют правильные шестиугольники со стороной 0,143 нм. Каждая сетка расположена симметрично относительно промежуточной молекулярной плоскости. Расстояние между ближайшими плоскостями 0,3345 нм, а между симметрично расположенными – 0,669 нм. Трехмерно-упорядоченную кристаллическую структуру имеют только графитированные углеродистые материалы. Структуру неграфитированных углеродистых материалов составляют двумерно-упорядоченные гексагональные сетки, произвольно ориентированные друг относительно друга. Под влиянием высокой температуры происходит графитирование некоторых углеродистых материалов, и они приобретают трехмерно-упорядоченную структуру. Графитированные изделия отличаются от угольных более высокой теплопроводностью и электропроводностью, большей устойчивостью к окислению кислородом, хлором и другими окислителями. Эти свойства делают их применение более эффективным на отдельных этапах производства легких металлов.
|
Твердые углеродистые материалы, используемые при изготовлении электродов, по своему происхождению делятся на естественные (антрацит) и искусственные: термоантрацит, литейный (каменноугольный), нефтяной и пековый кокс. Связующими веществами служат продукты сухой перегонки каменного угля: пек и каменноугольная смола.
|
По способу прессования электродной массы, обладающей пластичностью в нагретом состоянии, различают штампованные электроды, т.е. полученные прессованием в глухую матрицу, и прошивные, прессование которых ведется на проход через формовочный мундштук (рис.3). Для придания «зеленым» электродам достаточной электропроводности, прочности, химической устойчивости и других необходимых характеристик, их подвергают обжигу, в процессе которого происходит коксование связующего.
Придание углеграфитовым изделиям необходимых эксплуатационных свойств обеспечивается технологическим режимом всех этапов производства, а также сочетанием используемых сырьевых материалов и их природой. Если для изготовления анодов и анодной массы определяющим свойством при выборе углеродистого материала (нефтяной и пековый кокс) служит его чистота, т.е. малое содержание зольных примесей, то при выборе материалов для изготовления катодных блоков важнейшую роль играет их устойчивость к расплавленному электролиту и металлам.
В обычных для углерода реакциях (окисление, карбидообразование) требуется разрыв прочных ковалентных связей. При межслойном внедрении атомов, молекул и ионов в решетку углеграфитовых соединений они взаимодействуют не с отдельными атомами углерода, а с макромолекулами ароматического типа (рис.4). Расстояние между слоями атомов углерода, непосредственно связанными с внедрившимся слоем реагента, значительно увеличивается, что служит основной причиной разбухания углеродистого вещества и в ряде случаев полного его разрушения.
|
|
Взаимодействие натрия, выделяющегося на катоде и растворенного в алюминии, с углеродом является решающим для состояния угольных подин алюминиевых электролизеров. Установлено, что по убыванию стойкости в отношении внедряющегося натрия и других щелочных металлов угольные материалы располагаются в следующей последовательности: графит, антрацит, литейный кокс, пековый кокс, нефтяной кокс.
Важным фактором, влияющим на стойкость углеродной подины в условиях работы алюминиевого электролизера, является состав электролита. Быстрое увеличение скорости деформации с ростом концентрации NaF и к.о. свидетельствует о том, что это один из наиболее сильно действующих факторов.
Добавки фторидов кальция, магния, лития и хлорида натрия в различной степени способствуют торможению образования графитида натрия и снижают коэффициент деформации (рис.5). Механизм воздействия добавки NaCl может быть объяснен большей термодинамической устойчивостью хлоридов в присутствии жидкого алюминия:
NaF + Al =
AlF3 + Na,
= 2,85×10-2;
NaCl + Al =
AlCl3 + Na,
= 5,13×10-5,
где K р – константа равновесия соответствующих реакций при температуре электролиза.
Кроме состава электролита, важнейшим фактором деформации подины и металлического кожуха является температура (рис.6).
Таким образом, материал катодных блоков, степень предварительного нагрева угольной подины перед пуском и состав электролита определяют не только стойкость самих катодно-поляризованных угольных блоков, но и состояние конструкции катодной части электролизера в целом.
|
Количественная оценка деформации (устойчивости) катодно-поляризованных углеграфитовых материалов выполняется дилатометрическим способом, разработанным М.Б.Рапопортом. При этом определяется скорость относительной деформации
или обратная ей величина , принятая за показатель стойкости электродных изделий (здесь l и D l – рабочая длина образца и приращение длины соответственно, мм; t – продолжительность испытания, мин).
|
Лабораторное оборудование. Установка для изучения устойчивости катодно-поляризованных углеродистых материалов (рис.7). Основой установки является электрическая печь шахтного типа с регулируемой температурой. В печи установлен тигель с расплавленным электролитом и погруженным в него испытуемым образцом. Ток заданной силы подводится к электролитической ячейке от выпрямителя.
Линейная деформация образца определятся с помощью индикатора.
Содержание задания. Сведения о составе электролита, температуре расплава, плотности тока, материале изучаемых образцов.
Порядок работы
1. Приготовить необходимое количество электролита заданного состава, соблюдая меры техники безопасности при его разогреве и плавлении.
2. Предварительно просушенный при температуре 200 °С образец углеграфитового материала погрузить в расплав и определить рабочую длину образца l. Затем выдержать установку с погруженным образцом при постоянной температуре для выравнивания тепловых полей.
3. Установить индикатор и подать на образец ток заданной силы. Фиксируя во времени величину линейной деформации образца, записать результаты измерений (точность до 0,01 мм) в таблицу.
4. По окончании опыта образец охладить и определить количество внедрившегося металла (по указанию преподавателя). Для этого обработать испытуемую часть образца дистиллированной водой до окончания газовыделения. Раствор отфильтровать и измерить его объем, а затем установить количество щелочного металла, перешедшего в раствор, по результатам титрования 0,1 М раствором HCl.
5. Изменить условия в соответствии с заданием и повторить измерения по пп.2-3. Вычислить скорость деформации.
6. Сформулировать вывод об устойчивости образцов и перечислить основные технологические факторы, вызывающие деформацию углеграфитовых материалов.
|
|
Наброски и зарисовки растений, плодов, цветов: Освоить конструктивное построение структуры дерева через зарисовки отдельных деревьев, группы деревьев...
Двойное оплодотворение у цветковых растений: Оплодотворение - это процесс слияния мужской и женской половых клеток с образованием зиготы...
Состав сооружений: решетки и песколовки: Решетки – это первое устройство в схеме очистных сооружений. Они представляют...
Эмиссия газов от очистных сооружений канализации: В последние годы внимание мирового сообщества сосредоточено на экологических проблемах...
© cyberpedia.su 2017-2024 - Не является автором материалов. Исключительное право сохранено за автором текста.
Если вы не хотите, чтобы данный материал был у нас на сайте, перейдите по ссылке: Нарушение авторских прав. Мы поможем в написании вашей работы!