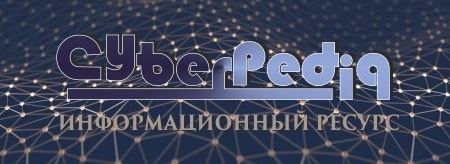
Поперечные профили набережных и береговой полосы: На городских территориях берегоукрепление проектируют с учетом технических и экономических требований, но особое значение придают эстетическим...
Индивидуальные очистные сооружения: К классу индивидуальных очистных сооружений относят сооружения, пропускная способность которых...
Топ:
Техника безопасности при работе на пароконвектомате: К обслуживанию пароконвектомата допускаются лица, прошедшие технический минимум по эксплуатации оборудования...
Определение места расположения распределительного центра: Фирма реализует продукцию на рынках сбыта и имеет постоянных поставщиков в разных регионах. Увеличение объема продаж...
Теоретическая значимость работы: Описание теоретической значимости (ценности) результатов исследования должно присутствовать во введении...
Интересное:
Уполаживание и террасирование склонов: Если глубина оврага более 5 м необходимо устройство берм. Варианты использования оврагов для градостроительных целей...
Распространение рака на другие отдаленные от желудка органы: Характерных симптомов рака желудка не существует. Выраженные симптомы появляются, когда опухоль...
Средства для ингаляционного наркоза: Наркоз наступает в результате вдыхания (ингаляции) средств, которое осуществляют или с помощью маски...
Дисциплины:
![]() |
![]() |
5.00
из
|
Заказать работу |
|
|
Эффективная работа дробилок и бегунов обеспечивается при условии гарантированного зажатия кусков материала между рабочими органами.
Из вышеизложенного следует, что дробилки и бегуны имеют различные по форме и траектории движения рабочие органы. Однако силовое взаимодействие между рабочими органами и измельчаемым материалом в них одинаковое. Это связано с тем, что все они разрушают материал путем сжатия. На рис. 3.7 показаны силы, действующие на кусок, зажатый, например, между вращающимися навстречу друг другу валками.
Касательные AC и AB к окружностям в точках контакта куска с валкамиможно рассматривать как следы рабочих поверхностей камер дробления щековых и конусных дробилок. В то же время взаимодействие между левым валком, куском и неподвижной поверхностью AC иллюстрирует рабочий процесс в бегунах, когда каток перекатывается по поддону. Со стороны рабочих органов машины на кусок материала по нормали к контактирующим поверхностям действуют активные силы Q, равнодействующая которых равна P = 2Qsin(α / 2), где α – угол захвата.
Рис.7 Схема для расчета угла захвата
Эта сила стремится вытеснить кусок из камеры дробления. Силы трения между рабочими органами машин и куском должны удерживать его. Таким образом, гарантированный захват куска будет обеспечен при условии, что силы трения будут больше выталкивающих сил, т.е. при выполнении следующего неравенства:
Где 2 fQcos – проекция сил трения на вертикальную ось. Откуда
следует, что
Выразив коэффициент трения между куском и рабочей поверхностью машин через угол трения ϕ, т.е. f = tg(ϕ), получим, что суммарный угол захвата должен быть меньше двойного угла трения:
|
α ≤ 2 ϕ.
Следовательно, условие захвата справедливо и последующее дробление возможно, когда угол захвата равен или меньше двойного угла трения. Например, при коэффициенте трения f = 0,32 угол трения ϕ = 17°40′ и угол захвата α < 35°.
В щековых и конусных дробилках при измельчении прочных кусков округлой формы угол захвата принимают равным 18...22°.
В валковых дробилках и бегунах целесообразнее использовать прямые соотношения диаметров D валков (катков) с максимально допустимым размером куска d. Из треугольника О2О1А (рис. 3.7) следует, что
откуда
где е – ширина выпускной щели.
Степень измельчения в валковых дробилках в среднем равна четырем. Следовательно, можно принять отношение e / d = 0,25. Практически установлено, что при имеющих место коэффициентах трения ипринятых соответствующих значениях α ≤ 2ϕ при дроблении прочныхматериалов для гладких валков D / d = 17... 20; для рифленых валков
D / d = 10; для зубчатых D / d = 2... 4.
Производительность щековых и конусных дробилок рассчитывается из условия, что разгрузка продукта из камеры дробления происходит при отходе подвижной щеки (подвижного конуса) от неподвижных стенок.
Клушанцев Б.В. предложил формулу расчета производительности с учетом факторов, влияющих на процесс дробления:
где с − коэффициент кинематики, равный для дробилок со сложным движением щеки 1, а для дробилок с простым движением щеки – 0,85; B - ширина камеры дробления в зоне загрузки, м; Sср − средний ход щеки, м; Dсв − средневзвешенный размер кусков в исходном материале, м; для дробилок с B ≤ 600 мм Dсв = В; для дробилок с B > 900 мм (0,3... 0,4).Dсв= B
Из конусных дробилок крупного дробления за одну обкатку подвижного конуса выпадает кольцо материала объемом:
где Dн − диаметр основания подвижного конуса, м; н 2 н S = r - перемещение конуса на уровне выходной щели, м; нr – размах колебаний оси конуса на том же уровне, м.
Техническая производительность дробилок крупного дробления
|
Коэффициент разрыхления для конусных дробилок больше, чем для щековых; его принимают равным kр = 0,7…0,8. Это связано с тем, что перекатывающее движение дробящего конуса способствует лучшему заполнению материалом камеры дробления и площадь выходного отверстия всегда остается постоянной, а изменяется лишь положение подвижного конуса в камере дробления. Геометрические и кинематические параметры конусных дробилок для среднего и мелкогодробления выбирают из условия обеспечения равенства времени оборота конуса и времени, необходимого на прохождение куском параллельной зоны.
При расчете производительности машин КСД и КМД принимают, что за один оборот конуса выгружается кольцевой объем материала с сечением се и средним диаметром кольца Dср. Обычно размер зоны с принимают равной с = Dн /12, а Dср ≈ Dн. Тогда техническая производительность дробилок КСД и КМД.
Из валковых дробилок измельченный материал выходит непрерывной лентой сечением F = B′e cо скоростью, равной окружной скорости валков v = π D n.
Техническая производительность валковых дробилок:
где kp − коэффициент, учитывающий неполноту использования длины валков и разрыхленность материала; при дроблении прочных материалов
kp = 0,2...0,3; при переработке пластичных материалов kp = 0,4...0,6; В′ - длина валков, м; n − частота вращения валков, об/с; е – ширина выходной щели, м.
Производительность бегунов определяют по эмпирическим формулам или по опытным данным. Это объясняется тем, что их производительность зависит от многих факторов, в том числе от свойств материалов и технологических требований к продуктам измельчения.
Оценить эти многочисленные факторы в явном виде практически не представляется возможным.
Частота вращения эксцентрикового вала конусных дробилок крупного дробления определяется из условия равенства времени t1, необходимого на падение материала под действием силытяжести с высоты h, времени t2 = 1/n отхода щеки (конуса) назад. Так как за время отхода щеки происходит свободное падение материала с высоты h, то h = gt2/2 и t = .
Тогда, в соответствие с вышеназванным условием, можно записать:
Учитывая то, что для конусных дробилок h = 2rн/(tgα1 + tgα2). находят оптимальную частоту вращения вала валковых дробилок:
Для крупногабаритных дробилок рассчитанные по формулезначения частот вращения валов следует уменьшить в 0,6…0,75 раза.
|
Это связано с тем, что в исходном материале имеется значительная доля кусков размером, меньшим ширины выходной щели, и целесообразно увеличить время отхода щеки, чтобы мелкие частицы успели выпасть из верхних зон камеры дробления.
Для дробилок КСД и КМД частоту вращения эксцентрика определяют по условию обязательного воздействия дробящих конусов на каждый измельчаемый кусок во время его пребывания в параллельной зоне. Предположив, что движение куска материала массой m вниз по дробящему конусу происходит под действием постоянной силы ma, численно равной разности между составляющей силы тяжести G sin β и силой трения f G cos β, можно записать
m a = m g sin β − f m g cos β,
где а – ускорение куска, м/с2; f – коэффициент трения измельчаемого
материала по дробящему конусу. Как было обусловлено выше, условие нормальной работы конусной дробилки среднего дробления заключается в том, что за время одного оборота конуса t1 = 1/n кусок материала должен пройти расстояние с зоны параллельности. Путь, проходимый телом при равноускоренном движении.
c = 0,5 а t22,
откуда время, необходимое для прохождения зоны параллельности,
Из условия равенства t1= t2, а также с учетом того, что a = g(sin β– f cos β), получают формулу для расчета частоты вращения конуса дробилки
Величина с для конусных дробилок среднего дробления составляет, в среднем, одну десятую диаметра нижнего основания подвижного конуса
c = 0,1Dн. С учетом этого формула преобразуется к виду
Частота вращения валков валковых дробилок не должна превышать некоторого значения, при котором создаются неустойчивые условия захвата материала и возникают нежелательные колебания нагрузок. Следовательно, частота вращения валков ограничена условием отбрасывания материала под действием центробежных сил. ЛевенсонЛ.Б. для расчета частоты вращения валков предложил следующую формулу:
где f – коэффициент трения между валками и материалом; ρ – плотность материала, кг/м3.
Частота вращения поддона бегунов рассчитывается из условия, что центробежные силы, действующие на кусок измельчаемого материала, не отбрасывают его к борту. Следовательно, работоспособность бегунов определяется из условия, что силы трения превышают центробежные силы, т.е.
|
откуда
где R – наружный радиус чаши, м. Изложенные выше основы процессов измельчения показывают, что установить аналитические зависимости между расходом энергии, свойствами материалов и результатами дробления можно только в общем виде. При этом следует также учитывать, что в машинах деформируется не монолитное тело, а конгломерат кусков, структура которого изменяется в зависимости от условий питания, результатовдробления крупных кусков и случайного характера их взаимодействия. Определенная трудность возникает при оценке объема материала, подвергающегося деформированию.
Удельные энергозатраты для различных материалов изменяются в пределах Э0 = 4...8 кВт ⋅ ч/т. В процессе измельчения двигатель щековых дробилок испытывает неравномерные нагрузки. В период рабочего хода щеки возникают максимальные нагрузки и угловая скоростьвала изменяется от ωmax в начале до ωmin в конце рабочего хода. В период холостого хода двигатель практически не нагружен. Для выравнивания нагрузки на двигатель на валу дробилки устанавливают маховики. Они запасают энергию при холостом ходе и отдают ее при рабочем ходе. Энергия, накапливаемая маховиком.
где J – момент инерции маховика.
После преобразований получают:
где - степень неравномерности хода дробилки; принимается равной 0,02…0,035; ωср – средняя угловая скорость вала. Необходимый момент инерции маховика.
Необходимый момент инерции моховика:
Энергию, накапливаемую маховиком, рекомендуется принимать равной половине работы, затрачиваемой на дробление:
где η – кпд привода; ω – угловая скорость вала дробилки.
Мощность привода валковых дробилок рассчитывают по следующей методике. При повороте валков на угол совершается работа
dA = Qdx, Дж,
где Q – распорное усилие, действующее на валки, Н; dx – перемещение точки приложения силы Q в направлении оси x, равное абсолютной деформации материала в данном сечении: dx = εs ( здесь ε – относительная деформация, ε = ds/s); s – расстояние между валками в данном сечении.
Сила, действующая со стороны валка на рассматриваемый элемент материала:
Q = PcpBdy
где Рср – среднее давление валков на материал, Па; B dy – площадь контакта валка с материалом (в проекции на вертикальную плоскость), м2.
Элементарная работа, совершаемая за время dt, соответствующее повороту валков на угол dϕ,
Откуда получим формулу для расчета мощности, необходимой для деформирования материала на всем угле захвата,
При этом имели в виду, что dy / dt = vy – это скорость продвижения материала в направлении оси y, а произведение Bsvy – производительность П.
|
Подставляя в формулу значение производительности валков из формулы, получим
Мощность привода бегунов определяется энергетическими затратами на перекатывание катков по поддону и на преодоление трения скольжения при непрерывном развороте широких катков при движении их по круговой траектории относительно поддона. Каток перекатывается без проскальзывания при движении по прямой (без разворота) под действием следующих сил (рис. 3.7): реакции Q со стороны поддона, равной силе G нажатия катка на поддон и определяющей сопротивление качению, и касательной силы T на ободе катка, обеспечивающей его перекатывание. Условие равновесия катка без учета трения в его цапфе имеет вид
откуда
где а – плечо трения качения; R – радиус катка; fк = а/R – приведенный коэффициент сопротивления качению (для условий работы бегунов fк = 0,1). Фактически каток всегда движется с разворотом. При взаимодействии катка с поддоном любая точка по ширине его обода вращается вокруг собственной оси со скоростью vк = ωкR (где ωк – угловая скорость катка).
Рис.8 Схема для расчета бегунов
Окружная скорость поддона в точке контакта с внешним торцом катка v2п = ωпr2 (где ωп – угловая скорость поддона) будет больше окружной скорости катка при вращении его вокруг собственной оси. Поэтому эта часть катка будет перемещаться юзом по поддону. В точке под внутренним торцом катка скорость поддона v1п = ωпr1 будет меньше окружной скорости катка при вращении его вокруг оси. Всвязи с этим каток на этом участке будет пробуксовывать. Только одно сечение катка, расположенное на некотором расстоянии r0 от центра поддона, будет перекатываться без скольжения. Силы трения Т1 и Т2, приложенные к ободу катка на внутренней и внешней его частях, направлены в разные стороны. При этом сила Т2 стремится вращать каток, а сила Т1 – тормозить его.
Условие равновесия катка в этом случае имеет вид
T2 R −T1 R − G a = 0.
По линии контакта катка с поддоном действует постоянная распределенная нагрузка G/B, которая создает линейно распределенные силы трения,
где µ – коэффициент трения скольжения между катком и поддоном.
Из рис. 3.7 следует, что
С учетом значений Т1 и Т2 получим
откуда расстояние от центра поддона до того сечения катка, которое перекатывается без скольжения
Для приведения рабочих органов бегунов в движение к поддону необходимо приложить вращающий момент
С учетом значений Т1, Т2 и r0 получают формулу для расчета момента
Мощность, необходимая для привода в движение обоих катков,
где ωп – в рад/с.
Следует, что мощность, расходуемая на преодоление скольжения катков, существенно зависит от их ширины и коэффициента трения скольжения между катком и поддоном µ. При расчете мощности двигателя бегунов следует учитывать затраты на перемещение скребков, которые оцениваются вращающим моментом
где Р – сила прижатия скребков к поддону, Н; Rе – радиус размещения скребков, м; z – число скребков.
Тогда мощность двигателя бегунов
где η – кпд привода.
|
|
Индивидуальные очистные сооружения: К классу индивидуальных очистных сооружений относят сооружения, пропускная способность которых...
Состав сооружений: решетки и песколовки: Решетки – это первое устройство в схеме очистных сооружений. Они представляют...
Семя – орган полового размножения и расселения растений: наружи у семян имеется плотный покров – кожура...
Наброски и зарисовки растений, плодов, цветов: Освоить конструктивное построение структуры дерева через зарисовки отдельных деревьев, группы деревьев...
© cyberpedia.su 2017-2024 - Не является автором материалов. Исключительное право сохранено за автором текста.
Если вы не хотите, чтобы данный материал был у нас на сайте, перейдите по ссылке: Нарушение авторских прав. Мы поможем в написании вашей работы!