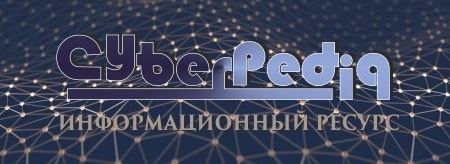
История развития хранилищ для нефти: Первые склады нефти появились в XVII веке. Они представляли собой землянные ямы-амбара глубиной 4…5 м...
Своеобразие русской архитектуры: Основной материал – дерево – быстрота постройки, но недолговечность и необходимость деления...
Топ:
Техника безопасности при работе на пароконвектомате: К обслуживанию пароконвектомата допускаются лица, прошедшие технический минимум по эксплуатации оборудования...
Оснащения врачебно-сестринской бригады.
История развития методов оптимизации: теорема Куна-Таккера, метод Лагранжа, роль выпуклости в оптимизации...
Интересное:
Распространение рака на другие отдаленные от желудка органы: Характерных симптомов рака желудка не существует. Выраженные симптомы появляются, когда опухоль...
Средства для ингаляционного наркоза: Наркоз наступает в результате вдыхания (ингаляции) средств, которое осуществляют или с помощью маски...
Инженерная защита территорий, зданий и сооружений от опасных геологических процессов: Изучение оползневых явлений, оценка устойчивости склонов и проектирование противооползневых сооружений — актуальнейшие задачи, стоящие перед отечественными...
Дисциплины:
![]() |
![]() |
5.00
из
|
Заказать работу |
|
|
Практическая работа №5
Тема: "Технология сварки разнородных и двухслойных сталей"
Цель работы: Приобрести практические навыки при изучении технологии сварки разнородных и двухслойных сталей
Ход выполнения работы:
1. Ознакомление с теоретическими сведениями
2. Самостоятельно изучить тему: «Технология сварки разнородных и двухслойных сталей»
3. Начертить таблицу №1 « Классификация сталей, применяемых в сварных соединениях разнородных сталей»
4. Зарисовать схему комбинированной наплавки свариваемой кромки
5. Ответь на контрольные вопросы.
Теоретические сведения
Назначение комбинированных конструкций и
Классификация разнородных сталей
Для экономии дорогостоящих высоколегированных сталей используют комбинированные конструкции, которые изготавливают из нескольких сталей. Сварка высоколегированных сталей с низко - или средне легированными и углеродными не всегда обеспечивает достаточную прочность соединения
Высоколегированные стали содержат дорогие, дефицитные элементы, что обусловливает необходимость их экономии. Одним из путей экономии высоколегированных сталей является изготовление установок, машин и механизмов из разнородных сталей. Такое изготовление вполне возможно, так как во многих случаях в условиях, требующих применения специальных сталей, работает не вся конструкция, а лишь её отдельные узлы или детали.
Остальная часть конструкции работает в обычных условиях и может быть изготовлена из среднелегированной, низколегированной или обычной углеродистой стали.
Конструкции, сваренные из разнородных сталей, называют комбинированными.
|
Они применяются в тех случаях, когда условия работы отдельных частей конструкции отличаются температурой, агрессивностью среды, особыми механическими воздействиями.
Таблица.1.
Классификация сталей, применяемых в сварных соединениях разнородных сталей.
Класс сталей и сварочных материалов | Группа | Характеристика сталей | Марки (примеры) |
Перлитные и бейнитные
| I | Углеродистые | Ст3, 20 |
II | Низколегированные | 09Г2С, 10ХСНД, 20ХГСА | |
III | Легированные среднеуглеродистые | 30ХГСА, 40Х, 40ХН2МА, 38ХВ | |
IV | Теплоустойчивые (Cr-Mo и Cr-Mo-V) | 12МХ, 12Х1МФ, 15Х1М1Ф | |
V | Хладостойкие (Fe-Ni) | 0Н3, 0Н6, 0Н9 | |
Мартенситные, ферритные, ферритно-мартенситные, аустенитно-мартенситные, ферритно-аустенитные | VI | 12%-е хромистые, жаростойкие | 08Х13, 12Х13 |
VII | Высокохромистые, жаростойкие | 08Х17Т, 15Х25Т, 20Х17Н2 | |
VIII | 12%-е хромистые, жаропрочные | 15Х11МФ, 15Х12ВНМФ | |
IX | Хромоникелевые коррозионностойкие | 12Х21Н5Т | |
Аустенитные стали и сплавы на никелевой основе
| X | Коррозионностойкие аустенитные | 12Х18Н10Т, 10Х17Н13М3Т |
XI | Аустенитные жаропрочные | 10Х15Н35ВТ, 20Х25Н20С2 | |
XII | Аустенитные коррозионностойкие и криогенны | Х18Н20, 06Х23Н28М3Д3Т | |
XIII | Жаропрочные никелевые сплавы | ХН70ВМТЮФ, ХН56ВМТЮ |
Основные трудности при сварке разнородных сталей и
Способы их преодоления
Проблема сварки разнородных сталей (высоколегированных хромоникелевых с низколегированными или углеродистыми) оказалась одной из наиболее сложных в современной сварочной науке и технике.
Трудности при сварке разнородных сталей:
v В процессе изготовления сварного соединения или при его эксплуатации в шве часто образуются трещины, проходящие по его середине или у границы сплавления.
v В зоне сплавления образуется структурная неоднородность, которая приводит
v к механической неоднородности, а её наличие сказывается на работоспособности сварного соединения. Характерным признаком структурной неоднородности в зоне сплавления является наличие обезуглероженной прослойки со стороны менее легированной стали и науглероженной – со стороны высоколегированной. Эти прослойки образуются вследствие перемещения углерода из менее легированной стали в более легированную и образуют механическую неоднородность в виде мягкой и твёрдой прослоек. Влияние таких прослоек на работоспособность соединения зависит от их относительной толщины.
|
v Вследствие существенного различия коэффициентов линейного расширения сплавляемых металлов соединения остаются чрезмерно напряжёнными даже после термообработки, которая в случае сварки однородных металлов снимает такие напряжения.
Появление структурной неоднородности и степень ее развития определяются всеми факторами, способствующими перемещению углерода из менее легированного металла в более легированный. Решающие факторы: последующий нагрев сварного соединения до температур, вызывающих заметную миграцию углерода; время выдержки сварного соединения при этих температурах и химический состав сплавляемых металлов, в особенности содержание в них углерода и карбидообразующих элементов. Структурная неоднородность в зоне сплавления разнородных сталей возникает лишь при нагреве сварного соединения до температуры 350°С. Существенное развитие она получает при более высоких температурах (около 500°С). Наиболее интенсивно развивается эта неоднородность при температуре 600–800°С.
Отмеченные трудности обусловили особенности сварки разнородных сталей. Для получения качественных и надежно работающих в специфических условиях сварных соединений необходимо применять технологию сварки, которая предотвращает образование трещин в металле шва и структурной неоднородности в зоне сплавления, и обеспечивает получение сварных соединений с возможно более близкими коэффициентами линейного расширения сплавляемых металлов.
Поэтому при выборе способов и режимов сварки отдают предпочтение технологии, при которой толщина кристаллизационной прослойки минимальна.
Этого достигают следующими методами:
ü Применением высококонцентрированных источников тепла (электронный луч, лазер, плазма);
ü Разделкой кромок или их наплавкой, уменьшающей долю участия сталей, как показано на рис.1.;
ü Выбором режимов сварки с минимальной глубиной проплавления;
|
ü Переходом к дуговой сварке в защитных газах, обеспечивающей интенсивное перемешивание металла ванны.
Рис.1. Схема комбинированной наплавки свариваемой кромки: 1 – углеродистая сталь; 2 – перлитный стабилизированный слой; 3 – аустенитный слой; 4 – аустенитная сталь
Разных структурных классов
Выбор сварочных материалов должен исключить образование трещин различных видов и обеспечить эксплуатационную надежность сварных соединений. Применяют аустенитные сварочные материалы, обеспечивающие получение композиций наплавленного металла с таким запасом аустенитности, чтобы компенсировать участие в шве перлитной стали и гарантированно получить в высоколегированном шве или наплавке аустенитную структуру.
Большой запас аустенитности металла шва позволяет предотвратить образование малопластичных участков с мартенситной или карбидной структурой в корневых швах и слоях, примыкающих к перлитной стали в условиях неизбежного колебания долей их участия. Однако для этого варианта технологии будет характерна высокая склонность к возникновению горячих трещин в однофазном аустенитном металле шва, образующихся по границам зерен, сформированных в результате миграции. Для их предотвращения в швах со стабильно аустенитной структурой наплавленный металл
легируют элементами, снижающими диффузионные процессы при высоких температурах, применяют электроды типа Х15Н25АМ6, содержащие 6% Мо и 0,2–0,3% N. Они препятствуют развитию высокотемпературной ползучести и межзеренного проскальзывания в твердом металле при сварке, повышая при этом пластичность в температурном интервале хрупкости и тем самым предотвращают образование горячих трещин. При сварке жестких узлов из аустенитной и среднеуглеродистой стали мартенситного класса корневые слои выполняют электродами, содержащими до 60 % Ni и 15 % Мо. Эти электродные материалы с однофазной аустенитной структурой шва применяют и при сварке перлитных сталей с жаропрочными аустенитными сталями и никелевыми сплавами.
В большинстве таких случаев при сварке перлитных и аустенитных сталей IX группы применяют аустенитно-ферритные электроды, образующие в наплавленном металле 10–12% ферритной фазы и допускающие долю участия перлитной стали в металле шва до 30 %. При смешивании материала электрода и расплава в том же соотношении будет получен шов, содержащий 4–6% δ -феррита, что исключает образование горячих трещин, но несколько увеличивает толщину кристаллизационной прослойки.
|
Такой вариант технологии допустим при сварке аустенитных сталей с перлитными (группы II–III), содержащими активные карбидообразователи для ограничения диффузии углерода, либо содержащих весьма малое количество углерода путем его частичной замены азотом. Для сварных узлов, эксплуатирующихся при высоких температурах, необходимо применение высоконикелевых электродов типа ХН60М15. Швы, выполненные такими электродами, хорошо работают в условиях теплосмен из-за равенства коэффициента линейного расширения с перлитной сталью. Этими электродами заваривают дефекты литья сталей групп IV и V без последующей термообработки.
При недостаточности или неприемлемости указанных технологических вариантов прибегают к сварке через проставки или к предварительной наплавке кромки перлитной стали аустенитным металлом с последующей сваркой таких заготовок аустенитно-ферритными сварочными материалами с регламентированным количеством δ-Fe (2–6 %).
При сварке высокохромистых ферритных сталей (гр. VIII) с аустенитными (гр. XI–XIII) возможно применение как аустенитных, аустенитно-ферритных, так и высокохромистых электродов. С повышением температуры эксплуатации выше 500°С предпочтительны высокохромистые электроды.
При сварке перлитных сталей с 12%-ми хромистыми сталями необходимо предотвратить образование мартенсита и холодных трещин, а также развития диффузионных прослоек при отпуске и высокотемпературной эксплуатации. При выборе сварочных материалов следует исключить образование хрупких переходных участков в зонах перемешивания сталей. Для обеспечения наибольшей пластичности шва применяют сварочные материалы перлитного класса. Для снижения размеров диффузионных прослоек перлитный наплавленный металл должен легироваться определенным количеством более активных, чем хром, карбидообразующих элементов.
При сварке деталей больших толщин целесообразно электродами типа Э-ХМ делать наплавку на кромки высоколегированной стали (барьерный слой), а заполнение разделки осуществлять без подогрева электродами типа Э42 или Э50 в зависимости от требований прочности перлитного шва. Температуру предварительного подогрева и отпуска определяют по характеристикам более легированной, т.е. 12%-хромистой стали, но для уменьшения размеров диффузионных прослоек применяют отпуск при минимально допустимой температуре.
|
При сварке перлитных сталей с более высоколегированными хромистыми сталями группы VII, содержащими 17–28 % Cr применяют электроды аустенитно-ферритного, а также аустенитного классов. Однако при этом следует учитывать описанную структурную неоднородность в зоне сплавления аустенитного шва и перлитной стали. Термообработка в этом случае не требуется.
При сварке разнородных сталей одного структурного класса, но различного легирования, как правило, дополнительных требований к выбору способа сварки и режимов не вводят. Это обусловлено тем, что стали имеют близкие теплофизические свойства, а переходные слои в области границ сплавления мало отличаются от металла шва.
При сварке сталей различных структурных классов, особенно перлитной стали с аустенитной, выбирают способ сварки и режимы, обеспечивающие минимальное проплавление соединяемых металлов. Это позволяет получить высоколегированный шов, приближающийся по составу к присадочному металлу.
Во всех случаях сварочные материалы выбирают из условий предотвращения формирования хрупкого металла шва, а также предотвращения возможности образования в зоне сплавления хрупких прослоек: кристаллизационных и диффузионных.
При сварке сталей одного структурного класса в большинстве случаев используют сварочные материалы, близкие по составу к менее легированной стали. В случае выполнения соединений сталей разного структурного класса (например, перлитного с аустенитной) в большинстве случаев используют высоколегированные сварочные материалы, а в некоторых случаях сплавы на никелевой основе, которые позволяют значительно снизить ширину диффузионных прослоек.
Поскольку при сварке легированных сталей в зоне термического влияния возможно формирование структур закалки, то для предотвращения их образования используют подогрев. Температуру подогрева назначают исходя из свойств стали, наиболее склонной к формированию структур закалки. При этом с целью снижения вероятности формирования диффузионных прослоек назначают минимально допустимую температуру подогрева. При выборе температуры подогрева необходимо учитывать не только свойства свариваемых сталей, но и свойства металла шва. В тех случаях, когда в металле шва возможно образование структур закалки, температуру подогрева назначают исходя из свойств металла шва. Структуру металла шва обычно оценивают по структурной диаграмме.
Когда применение подогрева встречает трудности, используют сварочные материалы, обеспечивающие получение аустенитных швов. Пластичный аустенитный шов позволяет снизить внутренние напряжения в зоне сварки и тем самым предотвратить образование холодных трещин. Следует отметить, что аустенитный шов сдвигает температуру мартенситного превращения перлитной (мартенситной) стали в область более высоких температур. Этому способствуют внутренние напряжения, образующиеся из-за различия коэффициентов линейного расширения.
Развитие мартенситного превращения в области высоких температур позволяет получить более пластичный мартенсит, так как проявляется эффект самоотпуска. Иногда для исключения подогрева при выполнении соединения используют предварительную наплавку на сталь, склонную к закалке, слоя незакаливающейся стали. Наплавку слоя ведут с подогревом или используют отпуск наплавленной детали. Толщину наплавленного слоя назначают из условий, чтобы в процессе сварки закаливающаяся сталь в зоне термического влияния не нагревалась выше температуры А1 (обычно толщина слоя до 9 мм).
В некоторых случаях для придания определенных свойств металлу в зоне соединения разнородных сталей или снятия внутренних напряжений назначают термообработку. Однако необходимо иметь в виду, что снятие внутренних напряжений возможно только в соединении разнородных сталей одного структурного класса. В сварных соединениях разнородных сталей различного структурного класса из-за различия в коэффициентах линейного расширения в результате термообработки величина внутренних напряжений может возрасти. При назначении термообработки соединений из разнородных сталей необходимо провести оценку возможности формирования диффузионных прослоек.
Таким образом, при назначении термообработки необходима всесторонняя оценка возможных изменений свойств металла в зоне 140 сварного соединения, а также величины внутренних напряжений. В большинстве сложных случаев термообработку (обычно отпуск) назначают, если это приводит к получению в зоне сварного соединения более пластичного металла. Благодаря повышению пластических свойств снижается вероятность хрупкого разрушения сварного соединения.
Очень часто вместо высокотемпературного отпуска, который приводит к развитию диффузионных прослоек, используют нормализацию, которая позволяет снизить интенсивность развития диффузионных прослоек. Последнее обусловлено, во-первых, снижением скорости диффузии углерода в аустените при нагреве выше точки А3, во-вторых, снижением стойкости карбидов.
Практическая работа №5
Тема: "Технология сварки разнородных и двухслойных сталей"
Цель работы: Приобрести практические навыки при изучении технологии сварки разнородных и двухслойных сталей
Ход выполнения работы:
1. Ознакомление с теоретическими сведениями
2. Самостоятельно изучить тему: «Технология сварки разнородных и двухслойных сталей»
3. Начертить таблицу №1 « Классификация сталей, применяемых в сварных соединениях разнородных сталей»
4. Зарисовать схему комбинированной наплавки свариваемой кромки
5. Ответь на контрольные вопросы.
Теоретические сведения
Назначение комбинированных конструкций и
|
|
Архитектура электронного правительства: Единая архитектура – это методологический подход при создании системы управления государства, который строится...
История развития хранилищ для нефти: Первые склады нефти появились в XVII веке. Они представляли собой землянные ямы-амбара глубиной 4…5 м...
Своеобразие русской архитектуры: Основной материал – дерево – быстрота постройки, но недолговечность и необходимость деления...
Особенности сооружения опор в сложных условиях: Сооружение ВЛ в районах с суровыми климатическими и тяжелыми геологическими условиями...
© cyberpedia.su 2017-2024 - Не является автором материалов. Исключительное право сохранено за автором текста.
Если вы не хотите, чтобы данный материал был у нас на сайте, перейдите по ссылке: Нарушение авторских прав. Мы поможем в написании вашей работы!