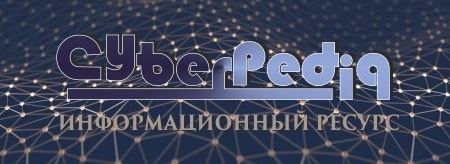
Механическое удерживание земляных масс: Механическое удерживание земляных масс на склоне обеспечивают контрфорсными сооружениями различных конструкций...
Двойное оплодотворение у цветковых растений: Оплодотворение - это процесс слияния мужской и женской половых клеток с образованием зиготы...
Топ:
История развития методов оптимизации: теорема Куна-Таккера, метод Лагранжа, роль выпуклости в оптимизации...
Когда производится ограждение поезда, остановившегося на перегоне: Во всех случаях немедленно должно быть ограждено место препятствия для движения поездов на смежном пути двухпутного...
Организация стока поверхностных вод: Наибольшее количество влаги на земном шаре испаряется с поверхности морей и океанов...
Интересное:
Лечение прогрессирующих форм рака: Одним из наиболее важных достижений экспериментальной химиотерапии опухолей, начатой в 60-х и реализованной в 70-х годах, является...
Принципы управления денежными потоками: одним из методов контроля за состоянием денежной наличности является...
Мероприятия для защиты от морозного пучения грунтов: Инженерная защита от морозного (криогенного) пучения грунтов необходима для легких малоэтажных зданий и других сооружений...
Дисциплины:
![]() |
![]() |
5.00
из
|
Заказать работу |
Нормативный учет может быть использован как целостная концепция, позволяющая проводить анализ общей ситуации и принимать решения. Предприятие может применять его частично, например только блок трудовых или материальных затрат. Нормативные затраты представляют собой тщательно рассчитанные предопределенные затраты, которые выражаются обычно в расчете на единицу готовой продукции. В общем случае нормативные затраты включают три элемента производственных затрат, каждый из которых имеет две составляющие, — натуральную и стоимостную для прямых и переменную и постоянную для косвенных:
1. Прямые материальные затраты:
- нормативная цена основных материалов;
- нормативное количество основных материалов.
2. Прямые затраты труда:
- нормативное рабочее время (по прямым трудозатратам);
- нормативная ставка прямой оплаты труда
3. Общепроизводственные расходы
- нормативный коэффициент переменных общепроизводственных расходов;
- нормативный коэффициент постоянных общепроизводственных расходов.
В таком поэлементном представлении затрат на продукт речь идет о вычислении производственной себестоимости. Если рассчитывается полная себестоимость, то должен появиться еще и четвертый элемент — расходы общехозяйственные, то есть расходы периода, относимые в учете на определенный временной промежуток, а не на физические единицы продукции. Многие нормативы применяются предприятием длительное время без изменений. Пересмотр натуральной части нормативов вызывают изменение конструкции или технологии производства изделия, модификация или освоение нового продукта. Ценовые составляющие нормативных затрат обновляются чаще, чтобы отразить влияние инфляции и других факторов на цены приобретаемых материалов и стоимость рабочей силы. Но предприятию требуется не только создание отчетной базы для нормирования и планирования затрат.
Расчет трудоемкости
Расчет трудоемкости изделия (Тизд) ведется по формуле:
где Тшт - штучное время изготовления сварной сборочной единицы на отдельно стоящем оборудовании, мин.;
Пр - плотность работ (принимать по табл. 3), чел.;
Т1 - трудоемкость изготовления сварной сборочной единицы на линии, чел.-ч;
т, п - количество сварных сборочных единиц, изготавливаемых соответственно на отдельно стоящем оборудовании и линиях, шт.
Штучное время изготовления (Тшт.) на отдельно стоящем оборудовании подсчитывается по формуле:
Тшт. = Топ × К,
где Топ - время на одну операцию (оперативное), мин.;
К - поправочный коэффициент, учитывающий время на организационно-техническое обслуживание рабочего места и перерывы на отдых и личные надобности (принимать по табл. 2).
Операционное время (Топ) определяется по формуле:
Топ = Тосн. + Твсп.,
где Тосн. - основное машинное время для всех видов контактной сварки, сварки трением; время горения дуги при всех видах дуговой сварки; время, затраченное на образование сварного шва (реза) при газовой сварке (резке) и т.д., мин.;
Твсп. - вспомогательное время, затраченное на сборку деталей, их фиксацию, крепеж, подсборку, подгонку, съем готовой сварной сборочной единицы с последующей ее укладкой в тару или навеску на конвейер, мин.
Основное (Тосн.) и вспомогательное (Твсп.) время принимается на основании пооперационного нормирования технологического процесса на сварочные и слесарно-сборочные работы.
Поправочный коэффициент (К) определяется по формуле:
где Аобс - время на организационно-техническое обслуживание;
Аотл - время на перерывы, на отдых и личные надобности.
Время на обслуживание рабочего места (Аобс.) и личные надобности (Аотл.) в процентах от оперативного времени и поправочный коэффициент (К) принимать по справочнику.
3. Методы и приёмы организации труда, эксплуатации оборудования, оснастки, средств механизации для повышения эффективности производства.
Основными задачами организации труда являются: увеличения производительности труда на основе применения передовой техники, технологии и обмена производственным опытом, улучшение условий труда и его облегчение путем механизации и автоматизации работ, улучшение санитарно-гигиенических условий труда, состояния техники безопасности, повышение квалификации и культурно-технического уровня рабочих, укрепление трудовой дисциплины и широкое развитие социалистического соревнования.
Повышение производительности труда в значительной мере зависит от правильной организации рабочего места. Мероприятия по правильной и рациональной организации рабочего места должны обязательно предусматриваться в планах научной организации труда (НОТ).
Рабочее место должно быть оборудовано шкафом для хранения инструмента, электродов и чертежей, сборочно-сварочными приспособлениями, сварочными столами. Все инструменты следует располагать в определенном порядке, чтобы они всегда находились под рукой.
В зависимости от размеров изделий и характера сварочных работ рабочее место может быть расположено в отдельной кабине или в цехе у сварочного стенда, или на монтажной площадке. Размеры кабины в плане 2X2 или 2x2,5 м. Если кабина расположена на поточной линии или конвейере, то в боковых стенках ее делаются проемы для прохождения конвейера с деталями, закрываемые дверцами или брезентовыми шторами.
При сварке в монтажных условиях рабочее место должно быть защищено от ветра, дождя, снега и иметь ограждения. При частой смене места работы необходимы приспособления для быстрого перемещения источника сварочного тока, провода, запаса электродов и сварочного инструмента (тележки, ящики для инструмента и электродов, ящики для сбора огарков и пр.).
2.4 Организация ремонта сварочного оборудование по системе Предупредительно-планового ремонта
Срок службы оборудования, бесперебойность в работе, производительность и качество сварки в большой степени зависят от наладки, технического обслуживания и своевременного ремонта сварочного оборудования.
Система планово-предупредительного ремонта оборудования — это совокупность запланированных организационных и технических мероприятий по уходу, надзору за оборудованием, его обслуживанию и ремонту. Цель этих мероприятий — предотвращение прогрессивно нарастающего износа, предупреждение аварий и поддержание оборудования в постоянной готовности к работе. Система ППР предполагает проведение профилактических мероприятий по техническому обслуживанию и плановому ремонту оборудования через определенное число часов его работы, при этом чередование и периодичность мероприятий определяются особенностями оборудования и условиями его эксплуатации.
Система ППР включает
· техническое обслуживание
· и плановый ремонт оборудования.
Текущее межремонтное обслуживание заключается в повседневном наблюдении за состоянием оборудования и соблюдении правил его эксплуатации, своевременном регулировании механизмов и устранении возникающих мелких неисправностей. Эти работы выполняются основными рабочими и дежурным ремонтным персоналом (слесарями, смазчиками, электриками), как правило без простоя оборудования.
Периодические профилактические ремонтные операции регламентированы и выполняются ремонтным персоналом по заранее разработанному графику без простоя оборудования. К числу таких операций относятся
· осмотры, проводимые для выявления дефектов, подлежащих устранению немедленно или при ближайшем плановом ремонте;
· промывка и смена масла, предусмотренные для оборудования с централизованной и картерной системой смазки;
· проверка точности, выполняемая персоналом отделов технического контроля и главного механика.
Плановый ремонт включает
· текущий ремонт
· и капитальный ремонт.
Текущий ремонт производится в процессе эксплуатации оборудования с целью обеспечения его работоспособности до очередного планового ремонта (следующего текущего или капитального). Текущий ремонт состоит в замене или восстановлении отдельных частей (деталей, сборочных единиц) оборудования и выполнении регулировки его механизмов.
Капитальный ремонт проводится с целью восстановления полного или близкого к полному ресурса оборудования (точности, мощности, производительности). Капитальный ремонт, как правило, требует проведения ремонтных работ в стационарных условиях и применения специальных средств технологического оснащения. Поэтому обычно требуется снятие оборудования с фундамента на месте эксплуатации и его доставка в специализированное подразделение, где проводится капитальный ремонт. При капитальном ремонте производится полная разборка оборудования с проверкой всех его частей, заменой и восстановлением изношенных деталей, выверкой координат и т.д.
Ремонтный цикл — это период времени от момента ввода оборудования в эксплуатацию до первого капитального ремонта или между двумя последовательно выполняемыми капитальными ремонтами. Ремонтный цикл представляет собой наименьший повторяющийся период эксплуатации оборудования, в течение которого осуществляются в установленной последовательности все виды технического обслуживания и ремонта в соответствии со структурой ремонтного цикла. Структура ремонтного цикла устанавливает перечень, количество и последовательность выполнения ремонта оборудования в течение ремонтного цикла.
Ремонтный цикл измеряется оперативным временем работы оборудования, время простоя в ремонте в цикл не включается. Длительность ремонтного цикла определяется сроком службы основных механизмов и деталей, замена или ремонт которых могут быть осуществлены во время полной разборки оборудования. Износ основных деталей зависит от многих факторов, основными из которых являются:
· тип производства, от которого зависит интенсивность использования оборудования;
· физико-механические свойства обрабатываемого материала, от которых зависит интенсивность износа оборудования и его частей;
· условия эксплуатации, такие, как повышенная влажность, запыленность и загазованность;
· класс точности оборудования, определяющий уровень требований к контролю за техническим состоянием оборудования;
· размер оборудования (категория массы — до 10 т, от 10 до 100 т, свыше 100 т), от чего зависит доля машинного времени в общем времени.
Категория ремонтной сложности — это степень сложности ремонта оборудования. Категория ремонтной сложности оборудования определяется по числу единиц сложности ремонта, присвоенных данной группе
4.Организовывать ремонт и техническое обслуживание сварочного производства по Единой системе планово – предупредительного ремонта.
Планово-предупредительная форма организации ремонта технологического оборудования во всем мире признана наиболее эффективной и нашла наибольшее распространение. Разработка системы планово-предупредительного ремонта оборудования начата в СССР в 1923 г. В настоящее время различные варианты системы ППР являются основой организации технического обслуживания и ремонта оборудования на предприятиях большинства отраслей сферы материального производства и сервиса.
Система планово-предупредительного ремонта оборудования — это совокупность запланированных организационных и технических мероприятий по уходу, надзору за оборудованием, его обслуживанию и ремонту. Цель этих мероприятий — предотвращение прогрессивно нарастающего износа, предупреждение аварий и поддержание оборудования в постоянной готовности к работе. Система ППР предполагает проведение профилактических мероприятий по техническому обслуживанию и плановому ремонту оборудования через определенное число часов его работы, при этом чередование и периодичность мероприятий определяются особенностями оборудования и условиями его эксплуатации.
Система ППР включает
· техническое обслуживание
· и плановый ремонт оборудования.
Техническое обслуживание — это комплекс операций по поддержанию работоспособности оборудования при использовании его по назначению, при хранении и транспортировке. Техническое обслуживание включает
· текущее межремонтное обслуживание
· и периодические профилактические ремонтные операции.
Текущее межремонтное обслуживание заключается в повседневном наблюдении за состоянием оборудования и соблюдении правил его эксплуатации, своевременном регулировании механизмов и устранении возникающих мелких неисправностей. Эти работы выполняются основными рабочими и дежурным ремонтным персоналом (слесарями, смазчиками, электриками), как правило без простоя оборудования. Периодические профилактические ремонтные операции регламентированы и выполняются ремонтным персоналом по заранее разработанному графику без простоя оборудования. К числу таких операций относятся
· осмотры, проводимые для выявления дефектов, подлежащих устранению немедленно или при ближайшем плановом ремонте;
· промывка и смена масла, предусмотренные для оборудования с централизованной и картерной системой смазки;
· проверка точности, выполняемая персоналом отделов технического контроля и главного механика.
Плановый ремонт включает
· текущий ремонт
· и капитальный ремонт.
Текущий ремонт производится в процессе эксплуатации оборудования с целью обеспечения его работоспособности до очередного планового ремонта (следующего текущего или капитального). Текущий ремонт состоит в замене или восстановлении отдельных частей (деталей, сборочных единиц) оборудования и выполнении регулировки его механизмов. Капитальный ремонт проводится с целью восстановления полного или близкого к полному ресурса оборудования (точности, мощности, производительности). Капитальный ремонт, как правило, требует проведения ремонтных работ в стационарных условиях и применения специальных средств технологического оснащения. Поэтому обычно требуется снятие оборудования с фундамента на месте эксплуатации и его доставка в специализированное подразделение, где проводится капитальный ремонт. При капитальном ремонте производится полная разборка оборудования с проверкой всех его частей, заменой и восстановлением изношенных деталей, выверкой координат и т.д.
Система ремонта и технического обслуживания в зависимости от характера и условий эксплуатации оборудования может функционировать в различных организационных формах:
· в виде послеосмотровой системы,
· системы периодического ремонта
· или системы стандартного ремонта.
Послеосмотровая система предполагает проведение по заранее разработанному графику осмотров оборудования, в ходе которых устанавливается его состояние и составляется ведомость дефектов. На основании данных осмотра определяются сроки и содержание предстоящего ремонта. Эта система применяется для некоторых видов оборудования, работающего в стабильных условиях.
Система периодического ремонта предполагает планирование сроков и объемов ремонтных работ всех видов на основе развитой нормативной базы. Фактический объем работ корректируется относительно нормативного по результатам осмотра. Эта система наиболее распространена в машиностроении.
Система стандартного ремонта предполагает планирование объема и содержания ремонтных работ на основе точно установленных нормативов и строгое соблюдение планов ремонта независимо от фактического состояния оборудования. Эта система применяется к оборудованию, неплановая остановка которого недопустима или опасна (например, подъемно-транспортные устройства).
Эффективность системы ППР в значительной степени определяется развитостью ее нормативной базы и точностью установленных нормативов. Нормативы системы ППР предприятия дифференцируются по группам оборудования. Основными ремонтными нормативами являются
· ремонтные циклы и их структура,
· категории сложности ремонта,
· трудоемкость и материалоемкость ремонтных работ,
· материальные запасы для ремонтных нужд.
Износ основных деталей зависит от многих факторов, основными из которых являются
· тип производства, от которого зависит интенсивность использования оборудования;
· физико-механические свойства обрабатываемого материала, от которых зависит интенсивность износа оборудования и его частей;
· условия эксплуатации, такие, как повышенная влажность, запыленность и загазованность;
· класс точности оборудования, определяющий уровень требований к контролю за техническим состоянием оборудования;
· размер оборудования (категория массы — до 10 т, от 10 до 100 т, свыше 100 т), от чего зависит доля машинного времени в общем времени.
Длительность ремонтного цикла Т определяется в отработанных машино-часах расчетным способом по эмпирическим зависимостям, учитывающим влияние многих факторов, в том числе перечисленных выше:
Длительность ремонтного цикла, межремонтного периода и периодичности технического обслуживания может быть выражена в годах или месяцах, если известна сменность работы оборудования. Правильный уход за оборудованием в процессе его эксплуатации, проведение организационно-технических мероприятий, продлевающих срок службы деталей и частей оборудования, способствуют изменению фактической длительности ремонтного цикла и межремонтных периодов по сравнению с нормативными. Сроки службы быстроизнашивающихся деталей и частей оборудования короче длительности межремонтного периода. Поэтому их целесообразно заменять по мере износа в межремонтный период. Трудоемкость ремонта при этом сокращается, объем работ по межремонтному обслуживанию увеличивается.
Поперечные профили набережных и береговой полосы: На городских территориях берегоукрепление проектируют с учетом технических и экономических требований, но особое значение придают эстетическим...
Наброски и зарисовки растений, плодов, цветов: Освоить конструктивное построение структуры дерева через зарисовки отдельных деревьев, группы деревьев...
Семя – орган полового размножения и расселения растений: наружи у семян имеется плотный покров – кожура...
Опора деревянной одностоечной и способы укрепление угловых опор: Опоры ВЛ - конструкции, предназначенные для поддерживания проводов на необходимой высоте над землей, водой...
© cyberpedia.su 2017-2024 - Не является автором материалов. Исключительное право сохранено за автором текста.
Если вы не хотите, чтобы данный материал был у нас на сайте, перейдите по ссылке: Нарушение авторских прав. Мы поможем в написании вашей работы!