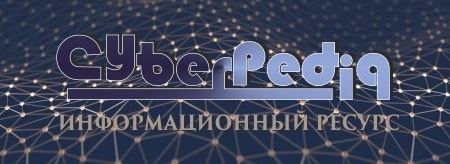
Особенности сооружения опор в сложных условиях: Сооружение ВЛ в районах с суровыми климатическими и тяжелыми геологическими условиями...
Археология об основании Рима: Новые раскопки проясняют и такой острый дискуссионный вопрос, как дата самого возникновения Рима...
Топ:
Оценка эффективности инструментов коммуникационной политики: Внешние коммуникации - обмен информацией между организацией и её внешней средой...
Процедура выполнения команд. Рабочий цикл процессора: Функционирование процессора в основном состоит из повторяющихся рабочих циклов, каждый из которых соответствует...
Генеалогическое древо Султанов Османской империи: Османские правители, вначале, будучи еще бейлербеями Анатолии, женились на дочерях византийских императоров...
Интересное:
Наиболее распространенные виды рака: Раковая опухоль — это самостоятельное новообразование, которое может возникнуть и от повышенного давления...
Средства для ингаляционного наркоза: Наркоз наступает в результате вдыхания (ингаляции) средств, которое осуществляют или с помощью маски...
Аура как энергетическое поле: многослойную ауру человека можно представить себе подобным...
Дисциплины:
![]() |
![]() |
5.00
из
|
Заказать работу |
|
|
Введение
В 1880г. было установлено, что при автоклавной обработке известково-песчаных смесей – твердение в паровой среде при давлении пара 8 ат и более (при температуре выше 1700С) могут быть получены очень прочные, водостойкие и долговечные изделия. В настоящее время силикатная промышленность – одна из наиболее развитых отраслей промышленности строительных материалов.
Сущность превращения известково-песчаной смеси из легко размокающего и малопрочного материала в прочных и водостойкий камень заключается в следующем. При естественных условиях песок в известково-песчаных смесях инертен и не способен химически взаимодействовать с известью. В результате этого приобретение прочности известково-песчаных растворов в естественных условиях достигается только за счет твердения извести. Однако в среде насыщенного пара (100% влажность) при температуре 1700С и выше кремнезем песка приобретает химическую активность и начинает взаимодействовать с известью, образуя гидросиликаты кальция – прочное и водостойкое вещество.
В данном проекте мы производим из такой смеси силикатный кирпич. Силикатный кирпич по своей форме, размерам и основному назначению е отличается от глиняного кирпича. Материалами для изготовления силикатного кирпича являются воздушная известь и кварцевый песок. Известь применяют в виде молодой негашеной, частично загашенной или гашеной гидратной. Известь должна характеризоваться быстрым гашением и не должна содержать более 5% MgO.
Пережог замедляет скорость гашения извести и даже вызывает появление в изделиях трещин, вспучиваний и других дефектов, поэтому для производства автоклавных силикатных изделий известь не должна содержать пережога. Кварцевый песок в производстве силикатных изделий применяют немолотым или в виде смеси немолотого и тонкомолотого, а также грубомолотого с содержанием кремнезема не менее 70%. Равномерно распределенные глинистые примеси допускаются в количестве не более 10%.
|
Состав известково-песчаных смеси для изготовления силикатного кирпича следующий: 92-95% чистого кварцевого песка, 5-8% воздушной извести и примерно 7% воды.
Производство силикатного кирпича ведется двумя способами: барабанным и силосным, отличающимися приготовлением известково-песчаных смеси.
В настоящем проекте используется силосный способ.
При силосном способе предварительно перемешенная и увлажненная масса направляется для гашения в силосы. Гашение в силосах происходит за 7-12 часов, т.е. в 10-15 раз продолжительнее, чем в барабанах, это является существенным технико-экономическим недостатком силосного способа. Хорошо загашенная в барабане или в силосе известково-песчаная масса направляется затем в лопастную мешалку или на бегуны для дополнительного увлажнения и перемешивания, после чего поступает в пресс.
Прессование кирпича производят на механических прессах. Отформованный сырец укладывают на вагонетку, которую направляют в автоклав для твердения.
Автоклав представляет собой стальной цилиндр диаметром 2м и более, длинной 20м с торцов герметически закрывающийся крышками. С повышением температуры ускоряется реакция между известью и песком и при температуре 1700С она протекает в течение 8-10 часов. Быстрое твердение происходит не только при высокой температуре, но и высокой влажности, для этого в автоклав пускают пар под давлением до 8ат и это давление выдерживают 6-8 часов. Давление пара поднимают и снижают в течении 1,5 часа. Цикл запаривания продолжается 10-14 часов.
Под действием высокой температуры и влажности происходит химическая реакция между известью и кремнеземом песка. Образующиеся в результате реакции гидросиликаты срастаются с зернами песка в прочный камень. Однако твердение силикатного кирпича на этом не останавливается. Прочность силикатного кирпича продолжает повышаться после запаривания. Часть извести, не вступившая в химическое взаимодействие с кремнеземом песка, реагирует с углекислотой воздуха, образуя прочный углекислый кальций по реакции.
|
Силикатный кирпич формуют размером 250*120*65 мм. По механической прочности различают марки кирпича: 75, 100 и 150. Водопоглащение силикатного кирпича составляет 8-16%; коэффициент теплопроводности – 0,70-0,75 ккал/м ч град, объемный вес – 1800-1900 кг/м, т.е. несколько выше, чем глиняного кирпича;
морозостойкость – Мрз 15.
Применяют силикатный кирпич там же, где и глиняный кирпич, но с некоторыми ограничениями. Нельзя применять силикатный кирпич для кладки фундаментов и цоколей.
По технико-экономическим показателям силикатный кирпич превосходит кирпич глиняный. На его производство требуется в 2 раза меньше топлива, в 3 раза меньше электроэнергии, в 2,5 раза меньше трудоемкость производства; в конечном итоге себестоимость силикатного кирпича оказывается на 25-35% ниже, чем глиняного кирпича.
1. Общая часть;
1.1 Техническая характеристика изделия;
Наименование | Марка бетона | Объем бетона | Масса изделия | Геометрические размеры, мм | ||
А | В | Н | ||||
Кирпич силикатный | 75 | 0,00195 | 0,0037 | 250 | 120 | 65 |
Таблица №1
Эскиз изделия:
![]() |
Состав бетона:
Вид вяжущего | Расход материалов на куб.м | Средняя плотность, | Влажность, % | |||
И, кг | П, кг | В, л | Начальная W1 | Конечная W2 | ||
Известь | 220 | 1500 | 180 | 1900 | 9,47 | 6 |
Таблица №2
Примечание: В/И – водовяжущее отношение
В/И=180/220=0,81 (1)
Режим работы цеха
Таблица №3
Наименование операции | Количество смеси в сутки | Продолжи тельность смены | Рабочих суток в году | Ки | Годовой фонд рабочего времени | |
сутки | часы | |||||
Формование | 2 | 8 | 253 | 0,949 | 240 | 3840 |
Термообработка | 3 | 8 | 253 | 0,949 | 240 | 5760 |
Примечание: Ки=0,92-0,95 – коэффициент использования оборудования
Производительность цеха
Таблица №4
Наименование изделий | Единицы измерения | Производительность | ||||
В час, Пч | В смену, Псм | В сутки, Псут | В год, Пг | |||
Кирпич силикатный
| Штуки | 6510 | 52083 | 104167 | 25000000 | |
Куб.м | 12,69 | 101,56 | 203,12 | 48750 |
Примечание:
1. Производительность в час: Пч=25000000/3840=6510 шт (2)
2. Производительность в смену: Псм=6510*8=52083 шт (3)
3. Производительность в сутки: Псут=52083*2=104167 шт (4)
Режим термообработки
Таблица №5
Наименование операции | Обозначение | Продолжительность, в часах | Температура, ![]() | Давление, бар |
Загрузка-выгрузка | Z1 | 25 | 1 | 0,9 |
Подъем давления | Z2 | 2 | ||
Изотермическая выдержка | Z3 | 175 | 4 | |
Спуск давления | Z4 | 2 | ||
Охлаждение | Z5 | 40 | 2 |
График термообработки
![]() |
Технологическая часть
Теплотехническая часть
Потери тепла с конденсатом
, кДж (26)
где: - энтальпия пара при заданном давлении (2787), кДж/кг;
- энтальпия конденсата (814), кДж/кг
кДж
Тепловой баланс автоклава
Период
Расход
1.Тепло пара
Qn=Dy*On*(2680-417)
23665841
100
Невязка баланса:
Введение
В 1880г. было установлено, что при автоклавной обработке известково-песчаных смесей – твердение в паровой среде при давлении пара 8 ат и более (при температуре выше 1700С) могут быть получены очень прочные, водостойкие и долговечные изделия. В настоящее время силикатная промышленность – одна из наиболее развитых отраслей промышленности строительных материалов.
Сущность превращения известково-песчаной смеси из легко размокающего и малопрочного материала в прочных и водостойкий камень заключается в следующем. При естественных условиях песок в известково-песчаных смесях инертен и не способен химически взаимодействовать с известью. В результате этого приобретение прочности известково-песчаных растворов в естественных условиях достигается только за счет твердения извести. Однако в среде насыщенного пара (100% влажность) при температуре 1700С и выше кремнезем песка приобретает химическую активность и начинает взаимодействовать с известью, образуя гидросиликаты кальция – прочное и водостойкое вещество.
|
В данном проекте мы производим из такой смеси силикатный кирпич. Силикатный кирпич по своей форме, размерам и основному назначению е отличается от глиняного кирпича. Материалами для изготовления силикатного кирпича являются воздушная известь и кварцевый песок. Известь применяют в виде молодой негашеной, частично загашенной или гашеной гидратной. Известь должна характеризоваться быстрым гашением и не должна содержать более 5% MgO.
Пережог замедляет скорость гашения извести и даже вызывает появление в изделиях трещин, вспучиваний и других дефектов, поэтому для производства автоклавных силикатных изделий известь не должна содержать пережога. Кварцевый песок в производстве силикатных изделий применяют немолотым или в виде смеси немолотого и тонкомолотого, а также грубомолотого с содержанием кремнезема не менее 70%. Равномерно распределенные глинистые примеси допускаются в количестве не более 10%.
Состав известково-песчаных смеси для изготовления силикатного кирпича следующий: 92-95% чистого кварцевого песка, 5-8% воздушной извести и примерно 7% воды.
Производство силикатного кирпича ведется двумя способами: барабанным и силосным, отличающимися приготовлением известково-песчаных смеси.
В настоящем проекте используется силосный способ.
При силосном способе предварительно перемешенная и увлажненная масса направляется для гашения в силосы. Гашение в силосах происходит за 7-12 часов, т.е. в 10-15 раз продолжительнее, чем в барабанах, это является существенным технико-экономическим недостатком силосного способа. Хорошо загашенная в барабане или в силосе известково-песчаная масса направляется затем в лопастную мешалку или на бегуны для дополнительного увлажнения и перемешивания, после чего поступает в пресс.
Прессование кирпича производят на механических прессах. Отформованный сырец укладывают на вагонетку, которую направляют в автоклав для твердения.
Автоклав представляет собой стальной цилиндр диаметром 2м и более, длинной 20м с торцов герметически закрывающийся крышками. С повышением температуры ускоряется реакция между известью и песком и при температуре 1700С она протекает в течение 8-10 часов. Быстрое твердение происходит не только при высокой температуре, но и высокой влажности, для этого в автоклав пускают пар под давлением до 8ат и это давление выдерживают 6-8 часов. Давление пара поднимают и снижают в течении 1,5 часа. Цикл запаривания продолжается 10-14 часов.
|
Под действием высокой температуры и влажности происходит химическая реакция между известью и кремнеземом песка. Образующиеся в результате реакции гидросиликаты срастаются с зернами песка в прочный камень. Однако твердение силикатного кирпича на этом не останавливается. Прочность силикатного кирпича продолжает повышаться после запаривания. Часть извести, не вступившая в химическое взаимодействие с кремнеземом песка, реагирует с углекислотой воздуха, образуя прочный углекислый кальций по реакции.
Силикатный кирпич формуют размером 250*120*65 мм. По механической прочности различают марки кирпича: 75, 100 и 150. Водопоглащение силикатного кирпича составляет 8-16%; коэффициент теплопроводности – 0,70-0,75 ккал/м ч град, объемный вес – 1800-1900 кг/м, т.е. несколько выше, чем глиняного кирпича;
морозостойкость – Мрз 15.
Применяют силикатный кирпич там же, где и глиняный кирпич, но с некоторыми ограничениями. Нельзя применять силикатный кирпич для кладки фундаментов и цоколей.
По технико-экономическим показателям силикатный кирпич превосходит кирпич глиняный. На его производство требуется в 2 раза меньше топлива, в 3 раза меньше электроэнергии, в 2,5 раза меньше трудоемкость производства; в конечном итоге себестоимость силикатного кирпича оказывается на 25-35% ниже, чем глиняного кирпича.
1. Общая часть;
1.1 Техническая характеристика изделия;
Наименование | Марка бетона | Объем бетона | Масса изделия | Геометрические размеры, мм | ||
А | В | Н | ||||
Кирпич силикатный | 75 | 0,00195 | 0,0037 | 250 | 120 | 65 |
Таблица №1
Эскиз изделия:
![]() |
Состав бетона:
Вид вяжущего | Расход материалов на куб.м | Средняя плотность, | Влажность, % | |||
И, кг | П, кг | В, л | Начальная W1 | Конечная W2 | ||
Известь | 220 | 1500 | 180 | 1900 | 9,47 | 6 |
Таблица №2
Примечание: В/И – водовяжущее отношение
В/И=180/220=0,81 (1)
Режим работы цеха
Таблица №3
Наименование операции | Количество смеси в сутки | Продолжи тельность смены | Рабочих суток в году | Ки | Годовой фонд рабочего времени | |
сутки | часы | |||||
Формование | 2 | 8 | 253 | 0,949 | 240 | 3840 |
Термообработка | 3 | 8 | 253 | 0,949 | 240 | 5760 |
Примечание: Ки=0,92-0,95 – коэффициент использования оборудования
Производительность цеха
Таблица №4
Наименование изделий | Единицы измерения | Производительность | |||
В час, Пч | В смену, Псм | В сутки, Псут | В год, Пг | ||
Кирпич силикатный | Штуки | 6510 | 52083 | 104167 | 25000000 |
Куб.м | 12,69 | 101,56 | 203,12 | 48750 |
Примечание:
1. Производительность в час: Пч=25000000/3840=6510 шт (2)
2. Производительность в смену: Псм=6510*8=52083 шт (3)
3. Производительность в сутки: Псут=52083*2=104167 шт (4)
Режим термообработки
Таблица №5
Наименование операции | Обозначение | Продолжительность, в часах | Температура, ![]() | Давление, бар |
Загрузка-выгрузка | Z1 | 25 | 1 | 0,9 |
Подъем давления | Z2 | 2 | ||
Изотермическая выдержка | Z3 | 175 | 4 | |
Спуск давления | Z4 | 2 | ||
Охлаждение | Z5 | 40 | 2 |
График термообработки
![]() |
Технологическая часть
Выбор типа и размера автоклава
· Тип автоклава – тупиковый;
· Внутренний диаметр – 2000 мм;
· Длина корпуса – 19245 мм;
· Рабочее давление – 9бар или 0,9 МПа;
· Рабочая температура – 174,5 ;
· Ширина колеи вагонетки – 750 мм
Габаритные размеры:
o Длина – 20825 мм;
o Ширина – 2078 мм;
o Высота – 4000 мм;
o Масса – 20,57 т
|
|
Археология об основании Рима: Новые раскопки проясняют и такой острый дискуссионный вопрос, как дата самого возникновения Рима...
Папиллярные узоры пальцев рук - маркер спортивных способностей: дерматоглифические признаки формируются на 3-5 месяце беременности, не изменяются в течение жизни...
Типы оградительных сооружений в морском порту: По расположению оградительных сооружений в плане различают волноломы, обе оконечности...
Двойное оплодотворение у цветковых растений: Оплодотворение - это процесс слияния мужской и женской половых клеток с образованием зиготы...
© cyberpedia.su 2017-2024 - Не является автором материалов. Исключительное право сохранено за автором текста.
Если вы не хотите, чтобы данный материал был у нас на сайте, перейдите по ссылке: Нарушение авторских прав. Мы поможем в написании вашей работы!