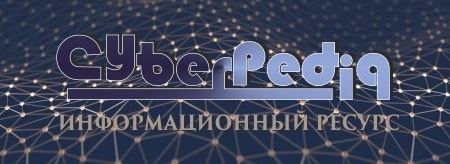
Автоматическое растормаживание колес: Тормозные устройства колес предназначены для уменьшения длины пробега и улучшения маневрирования ВС при...
История развития пистолетов-пулеметов: Предпосылкой для возникновения пистолетов-пулеметов послужила давняя тенденция тяготения винтовок...
Топ:
Характеристика АТП и сварочно-жестяницкого участка: Транспорт в настоящее время является одной из важнейших отраслей народного...
Основы обеспечения единства измерений: Обеспечение единства измерений - деятельность метрологических служб, направленная на достижение...
Интересное:
Принципы управления денежными потоками: одним из методов контроля за состоянием денежной наличности является...
Мероприятия для защиты от морозного пучения грунтов: Инженерная защита от морозного (криогенного) пучения грунтов необходима для легких малоэтажных зданий и других сооружений...
Подходы к решению темы фильма: Существует три основных типа исторического фильма, имеющих между собой много общего...
Дисциплины:
![]() |
![]() |
5.00
из
|
Заказать работу |
|
|
В. Н. Шиловский, Н. И. Серебрянский
Ремонт машин и оборудования
Учебное пособие для студентов инженерных специальностей
Петрозаводск
Издательство ПетрГУ
2007
ББК 43.904/906
Ш353
УДК 630.2 + 630.3
Рецензенты:
доктор технических наук, доцент В. С. Сюнёв;
кандидат технических наук Г. А. Борисов
Шиловский В. Н.
Ш353 Ремонт машин и оборудования: Учеб. пособие для студентов инженерных специальностей / В. Н. Шиловский, Н. И. Серебрянский. – Петрозаводск: Изд-во ПетрГУ, 2007. – 219 с.
ISBN 978-5-8021-0721-8
В учебном пособии изложен краткий курс лекций по ремонту машин и оборудования. Отражены вопросы организации и технологии ремонта элементов лесозаготовительных, транспортных, сельскохозяйственных машин и промышленного оборудования. Базовые положения пособия могут быть использованы при изучении организации технической эксплуатации машин и оборудования горных карьеров.
Учебное пособие предназначено для студентов лесоинженерных и сельскохозяйственных специальностей.
ББК 43.904/906
УДК 630.2 + 630.3
ISBN 978-5-8021-0721-8 © В. Н. Шиловский,
Н. И. Серебрянский, 2008
© Петрозаводский государственный университет, 2008
СОДЕРЖАНИЕ
ВВЕДЕНИЕ………………………….………………. | 7 |
ГЛАВА 1. ВИДЫ, ОРГАНИЗАЦИЯ, УЧЕТ И ОЦЕНКА РАБОТЫ РЕМОНТНЫХ ПРЕДПРИЯТИЙ……. | 9 |
1.1. Классификация и виды ремонтного производства………………………………………………………. | 10 |
1.2. Показатели для учета и оценки работы ремонтного производства………………………………….. | 12 |
1.3. Определение объемов ремонтного производства и обоснование параметров объектов технического сервиса машин и оборудования…………… | 16 |
ГЛАВА 2. ТРЕНИЕ И ИЗНАШИВАНИЕ ДЕТАЛЕЙ………... | 22 |
2.1. Основы теории трения. Виды трения. Гидродинамическая теория смазки………………………… | 22 |
2.2. Изнашивание деталей. Классификация видов изнашивания. Методы определения величины износа……………………………………………………. | 26 |
ГЛАВА 3. ТЕХНОЛОГИЯ РЕМОНТА ЭЛЕМЕНТОВ ЛЕСОЗАГОТОВИТЕЛЬНЫХ, ТРАНСПОРТНЫХ И СЕЛЬСКОХОЗЯЙСТВЕННЫХ МАШИН…… | 31 |
3.1. Понятие типового и рабочего технологического процесса ремонта машин и оборудования и восстановления их типовых деталей………………… | 31 |
3.2. Очистка, наружная мойка полнокомплектных машин и оборудования, агрегатов, узлов, деталей…………………………………………………….. | 33 |
3.3 Контроль и сортировка деталей. Магнитный, ультразвуковой, люминесцентный контроль деталей………………………………………………….. | 37 |
3.4. Технологии восстановления деталей машин и оборудования………………………………………… | 42 |
3.4.1. Восстановление сопряжений под ремонтные размеры…………………………………... | 42 |
3.4.2. Ручная электродуговая сварка и наплавка стальных, чугунных деталей и деталей из алюминиевых сплавов………………………. | 44 |
3.4.3. Восстановление деталей механизированной наплавкой под флюсом и вибродуговой наплавкой……………………………………... | 48 |
3.4.4. Восстановление деталей осталиванием….. | 52 |
3.4.5. Другие способы восстановления деталей…. | 55 |
3.5. Особенности сборки резьбовых соединений и соединений с натягом………………………………… | 57 |
3.5.1. Особенности сборки резьбовых соединений. | 57 |
3.5.2. Сборка соединений с натягом………………. | 62 |
3.6. Ремонт двигателей внутреннего сгорания……….. | 65 |
3.6.1. Ремонт элементов системы питания карбюраторных двигателей……………………. | 65 |
3.6.2. Ремонт системы охлаждения……………… | 68 |
3.6.3. Ремонт элементов системы смазки………. | 71 |
3.6.4. Ремонт элементов системы питания дизельных двигателей…………………………. | 74 |
3.6.5. Ремонт элементов системы зажигания….. | 80 |
3.6.6. Ремонт агрегатов и элементов электрооборудования…………………………………. | 83 |
3.6.7. Ремонт блок-картера, головки блок-карте-ра и блока цилиндров двигателя…………… | 91 |
3.6.8. Ремонт элементов кривошипно-шатунно-го механизма…………………………………. | 96 |
3.6.9. Ремонт элементов газораспределительного механизма……………………………………. | 100 |
3.6.10. Сборка, обкатка и испытание двигателей. | 102 |
3.7. Ремонт элементов гидросистем…………………… | 107 |
3.8. Окраска объектов ремонта………………………… | 113 |
ГЛАВА 4. ОРГАНИЗАЦИЯ МОНТАЖНЫХ РАБОТ ПРОМЫШЛЕННОГО ОБОРУДОВАНИЯ………….. | 118 |
4.1. Подготовительные работы для монтажа оборудования………………………………………………. | 118 |
4.2. Контроль качества монтажных работ……………. | 119 |
4.3. Основные этапы и документация технологического процесса монтажа оборудования………...... | 122 |
4.4. Фундаменты под оборудование……………………. | 124 |
4.4.1. Назначение фундаментов и общие требования к ним…………………………………… | 124 |
4.4.2. Фундаменты под металлорежущие станки. | 126 |
4.4.3. Виброизоляция фундаментов………………. | 129 |
4.5. Такелажные работы при монтаже оборудования. | 130 |
4.5.1. Технические средства для монтажа оборудования………………………………………... | 130 |
4.6. Монтаж металлорежущих станков……………….. | 133 |
ГЛАВА 5. УСЛОВИЯ ЭКСПЛУАТАЦИИ, ПРИСПОСОБЛЕНИЯ И ОСНАСТКА ДЛЯ ПРОВЕРКИ ТЕХНИЧЕСКОГО СОСТОЯНИЯ ЭЛЕМЕНТОВ МЕТАЛЛОРЕЖУЩИХ СТАНКОВ……………… | 136 |
5.1. Условия эксплуатации и изнашивания элементов станков………………………………………….. | 136 |
5.2. Универсально-сборные контрольно-измеритель-ные приспособления………………………………. | 138 |
5.3. Оптические средства контроля точности направляющих металлорежущих станков………… | 139 |
5.4. Приспособление для контроля натяжения ремней приводов………………………………………… | 143 |
ГЛАВА 6. ТЕХНОЛОГИЧЕСКИЙ ПРОЦЕСС КАПИТАЛЬ-НОГО РЕМОНТА МЕТАЛЛОРЕЖУЩЕГО СТАНКА……………………………………………… | 145 |
6.1. Разборка-сборка оборудования……………………. | 145 |
6.2. Очистка, мойка оборудования и его элементов, агрегатов, деталей………………………………….. | 147 |
6.3. Особенности контроля и сортировки узлов и деталей металлорежущих станков….………………. | 147 |
6.4. График капитального ремонта металлорежущего станка……………………………………………... | 149 |
6.5. Способы ремонта направляющих металлорежущего станка…………………………………………. | 150 |
6.6. Виброобкатывание направляющих станин станков……………………………………………………. | 150 |
6.7. Закалка направляющих станин…………………… | 153 |
6.7.1. Поверхностная закалка с индукционным нагревом токами высокой частоты……… | 153 |
6.7.2. Газопламенная закалка направляющих станин………………………………………... | 154 |
ГЛАВА 7. РЕМОНТ И ТЕХНИЧЕСКОЕ ОБСЛУЖИВАНИЕ ЦЕЛЛЮЛОЗНО-БУМАЖНОГО ОБОРУДОВАНИЯ……………………………………………………. | 155 |
7.1. Система технического обслуживания и ремонта целлюлозно-бумажного оборудовния……………… | 155 |
7.2. Графики ППР………………………………………….. | 155 |
7.3. Задачи и состав службы отдела главного механика предприятия………………………………………... | 156 |
7.4. Эксплуатационная и ремонтная документация….. | 157 |
7.5. Монтаж оборудования для производства бумаги… | 159 |
ГЛАВА 8. ПРОЕКТИРОВАНИЕ РЕМОНТНОЙ БАЗЫ ПРОМЫШЛЕННОГО ПРЕДПРИЯТИЯ……………….. | 164 |
8.1. Расчет годовой программы и трудоемкости работ. Составление графика планово-предупредитель-ного ремонта.………………………………………….. | 164 |
8.1.1. Краткая характеристика ремонтируемого оборудования…………………………………… | 164 |
8.1.2. Расчет ремонтосложности оборудования… | 165 |
8.1.3. Определение структурной схемы и объемов ремонта и обслуживания оборудования……. | 172 |
8.2. Расчет количества работающих..…………………… | 185 |
8.3. Расчет основного и вспомогательного оборудования……………………………………………………… | 188 |
8.4. Расчет площади ремонтной базы…………………… | 193 |
8.5. Составление плана расстановки оборудования и общей планировки…………………………………… | 199 |
8.6. Описание технологического процесса технического обслуживания и ремонта оборудования……….. | 202 |
8.7. Расчет вентиляции и освещения……………………. | 202 |
8.8. Расчет расхода электроэнергии и потребного количества топлива на отопление….…………………. | 204 |
8.9. Разработка технологического процесса ремонта детали…………………………………………………... | 205 |
СПИСОК ИСПОЛЬЗОВАННЫХ И РЕКОМЕНДУЕМЫХ ИСТОЧНИКОВ…………………………………………………… | 206 |
приложениЕ…………………………………………………... | 210 |
|
|
|
|
ВВЕДЕНИЕ
При организации ремонта машин в рыночных условиях необходимо решение ряда вопросов, связанных с определением номенклатуры и объема ремонтных работ в зависимости от места проведения, вида и способа ремонта.
В настоящее время крупные ремонтные предприятия не находят былого объема работ по капитальному ремонту лесозаготовительных, транспортных, сельскохозяйственных машин и их агрегатов. Объемы капитального ремонта выполняются самими эксплуатирующими организациями путем периодической замены достигших предельного состояния отдельных агрегатов и базовых деталей. Былые объемы работ по восстановлению деталей машин, ремонтируемых в условиях специализированных ремонтных предприятий, практически сведены к нулю. Восстановление работоспособности объектов в основном осуществляется путем использования новых запасных частей взамен вышедших из строя штатных основных деталей. Зачастую это объясняется не совсем верным бытующим мнением, что за рубежом техника и ее элементы не восстанавливаются, не ремонтируются и эксплуатируются до предельного состояния, после которого сразу утилизируются.
На самом деле, например в той же Финляндии, существует ремонтное производство по восстановлению подержанной техники с целью дальнейшей ее продажи по более низким ценам, чем цена новой машины. Целесообразность восстановления определяется объемами ремонтно-восстановительных работ, наличием технологий и оснащением оборудованием по качественному восстановлению деталей машин и оборудования.
Таким образом, актуальность и практическая ценность решения проблемы экономически эффективного восстановления работоспособности вышедших из строя и подержанных машин и их элементов не снижается, требует популяризации, разработки и внедрения эффективной организации всех видов ремонта, в том числе с использованием восстановленных деталей, а не только новых запчастей.
В данном учебном пособии изложены виды и способы организации ремонта машин и оборудования в зависимости от конкретных условий эксплуатации техники и возможности проведения ремонтно-восстано-вительных работ разного уровня.
Любой потребитель машин и оборудования, каждый предприниматель, инвестор может организовать любые работы, предусмотренные техническим сервисом, используя существующие технологии восстановления работоспособного состояния как отдельной детали, агрегата, так и машины в целом.
|
Поэтому существующие научно-технические разработки по технологиям, методам, способам организации восстановления деталей машин должны быть известны специалистам по техническому сервису машин и должны ими внедряться, развиваться и совершенствоваться при их практической деятельности с учетом конкретных технико-экономи-ческих условий.
РЕМОНТНЫХ ПРЕДПРИЯТИЙ
Ремонтное производство в нашей стране непрерывно изменяется. В этих условиях большое значение имеют вопросы по оценке эффективности ремонтного предприятия. Основной задачей при оценке деятельности мастерской или завода является определение степени технического совершенства производства. Последняя зависит от многих факторов. К их числу можно отнести: техническую оснащенность, уровень профессиональной подготовки производственного коллектива, условия труда, соблюдение пропорциональностей между производительностью труда и уровнем заработной платы, между мощностью предприятия и его программой и т. д. Поэтому систему учета для оценки ремонтных предприятий (производств, фирм) следует рассматривать, охватывая совокупность технико-экономических вопросов по ремонту машин, агрегатов и деталей.
Основными элементами, влияющими на техническое совершенство ремонтного производства, являются: исполнитель работы (рабочий-ремонтник), объект ремонта (полнокомплектная машина, агрегат, узел, деталь) и ремонтное предприятие (рис. 1.1).
Рис. 1.1. Основные элементы совершенствования
ремонтного производства
В настоящее время ремонтная база страны включает в себя различные ремонтные производства по мощности, степени специализации, техническому совершенству.
Показатели учета и оценки могут быть общими для всех типов ремонтного производства и частными, которые характеризуют специфику каждого из них.
Необходимо различать виды ремонтного производства и соответственно применять систему показателей их оценки.
Ремонтного производства
Основными показателями при оценке работы исполнителя являются: качество продукта труда (отремонтированная машина, агрегат, узел, деталь), производительность и ремонтно-техническая себестоимость (рис. 1.2).
Рис. 1.2. Показатели учета и оценки работы ремонтного производства (один из вариантов)
На рис. 1.2 представлена схема оценки качества ремонта техники. Основные показатели качества, и в первую очередь бездефектность труда исполнителя, зависят от технического совершенства ремонтного производства, его организационной структуры, от состояния исполнителей и условий их труда.
Рис. 1.3. Показатели качества ремонта (один из вариантов)
Каждый вид ремонтного производства в целом наряду с показателями качества исполнителей работы характеризуется обобщенными количественными, качественными и экономическими показателями, приведенными на рис. 1.4, 1.5, 1.6.
Проектирование ремонтных предприятий и оценка действующих начинается с рассмотрения их программы. В литературе, в источнике [3], рассмотрено шесть способов определения программы ремонтного предприятия.
Рис. 1.4. Показатели оценки индивидуального ремонтного
производства (один из возможных вариантов)
Для индивидуального ремонтного производства приемлем способ, при котором количество ремонтов (технических воздействий) может быть определено для каждого отдельного объекта (трактора, автомобиля, лесозаготовительной машины).
Для предприятий с организованными формами построения технологических процессов и индустриальными методами ремонта программу следует определять по обобщающим данным с привлечением положений теории вероятностей, примеры чего будут представлены далее.
Рис. 1.5. Оценка ремонтных предприятий
с организационными формами производства
Один из методов подсчета числа ремонтов () может быть основан на использовании теории восстановления:
, (1.8)
где – количество объектов ремонта, поставляемых по годам;
– число ремонтов объекта
-го выпуска в
-ом году, которое получается, согласно работе [1], из рекуррентного выражения:
, (1.9)
где ,
– плотность распределения соответственного доремонтного и
-го межремонтного технического среднего ресурса объекта
-го выпуска;
– число интервалов в полном техническом ресурсе.
Рис. 1.6. Показатели и оценка ремонтного производства
индустриального типа (один из возможных вариантов)
Их типовых деталей
Технологический процесс восстановления (ремонта) предусматривает нормативно-техническую документацию (НТД) и технические требования на восстановление; оборудование, организационную и технологическую оснастку; последовательность выполнения подготовительных, основных и заключительных операций; режимы восстановления; контроль качества (как пооперационный, так и заключительный).
Существуют типовые (рамочные) технологические инструкции, технологические процессы капитального ремонта машин, оборудования и их агрегатов, а также типовые технологические инструкции по восстановлению типовых деталей машин, т. е. по устранению типовых дефектов, неисправностей, отказов – износов, трещин, поломок, деформаций, изменивших первоначальную форму элементов машин [13].
Типовые инструкции, технологические процессы включают в себя общий принцип восстановления типовой детали с учетом всех возможных отклонений ее от конструкторской и нормативно-технической документации, с учетом всех возможных и конкретного выбранного способа восстановления; определяют требования к оборудованию организационной и технологической оснасток, перечню нормативно-технической документации, квалификации рабочих; включают основные операции технологического процесса и контроля качества, оговаривают вопросы техники безопасности, противопожарной безопасности, охраны труда, требования экологии и энергономики.
Рабочий технологический процесс восстановления той или иной детали предусматривает конкретные (а не рамочные) показатели режимов обработки с учетом параметров (габаритов, массы, материала и т. п.) конкретной детали, конкретное оборудование и оснастку, конкретные показатели качества и контроля восстановления.
Поэтому восстановление деталей может рассматриваться с учетом их вида (валы, шестерни, корпусные элементы и т. п.) и с учетом их типовых дефектов (трещины корпуса, износ резьбы, износ сопрягаемых поверхностей любой формы как подвижных, так и неподвижных соединений и т. п.).
Для восстановления типовых элементов (деталей) с типовыми отказами могут рассматриваться типовые технологии восстановления (ремонта): восстановление способом ремонтных размеров, сваркой, различными видами наплавки (под флюсом, вибродуговой и др.), электроискровым способом, гальваническим наращиванием, пластмассами, металлизацией и др.
Существуют типовые технологии устранения конкретных видов отказов, вызванных трещинами, это: установка ввертышей, заварка, восстановление эпоксидными смолами, пайкой и др.
Выбор конкретного способа восстановления определяется его эффективной областью применения для конкретных деталей, работающих в конкретных условиях (нагрузка, температура, скорость перемещения, точность – прецензионность сопряжений, величина максимального предельного износа; вид термообработки поверхности, определяемый требованиями износостойкости и т. п.).
При рассмотрении технологии восстановления (ремонта) первоначально следует разбирать типовые процессы восстановления типовых деталей с типовыми отказами с последующим рассмотрением примеров конкретных, так называемых рабочих, технологических процессов восстановления деталей, например в виде справочных материалов, приводимых в различных Технических требованиях (ТР), Технических условиях (ТУ), Типовых дефектовочных ведомостях на ремонт деталей конкретных машин и оборудования.
Инженер, в первую очередь, должен знать типовые инструкции и технологические процессы восстановления деталей машин и оборудования, на их основе (базе) разрабатывать рабочие технологические процессы восстановления конкретных деталей, должен знать справочную литературу по существующим, разработанным рабочим процессам ремонта машин и оборудования.
При разработке технологических процессов ремонта элементов машин и оборудования необходимо использовать современные ресурсо-сберегающие технологии восстановления деталей машин [14].
Пример общей схемы типового процесса капитального ремонта машин и оборудования представлен на рис. 3.1.
Рис. 3.1. Схема типового процесса капитального ремонта
машин и оборудования
И соединений с натягом
Сборка соединений с натягом
Все неподвижные неразъемные соединения с гарантированным натягом условно делят на поперечно-прессовые и продольно-прессовые.
Поперечно-прессовые осуществляют одним из следующих способов: нагреванием охватывающей детали перед сборкой, охлаждением охватываемой; путем пластической деформации (например, развальцовки); приданием упругости охватываемой детали.
При продольно-прессовом соединении охватываемая деталь запрессовывается в охватывающую в продольном направлении с натягом, в результате которого в соединении возникают силы трения, обеспечивающие относительную неподвижность деталей.
Трудоемкость таких соединений составляет 10…15% от общей трудоемкости сборочных работ.
Охватываемая деталь имеет наружный диаметр больший, чем диаметр отверстия охватывающей детали, в результате чего на поверхности контакта возникают значительные нормальные давления и сила трения, которые препятствуют сдвигу этих деталей. Способность прессовых соединений выдерживать значительные нагрузки зависит от натяга. Натяг одновременно является основным показателем, определяющим величину усилия запрессовки, Для определения действительного натяга (с учетом микрогеометрии) необходимо знать максимальную высоту неровностей обеих сопрягаемых поверхностей.
Номинальный натяг в сопряжении равен:
, (3.23)
где – диаметр вала;
– диаметр отверстия.
Действительный натяг равен:
, (3.24)
где – максимальная высота микронеровностей,
– средняя высота микронеровностей.
Условно принимая , получаем:
. (3.25)
Использование в процессе запрессовки смазки способствует повышению прочности соединения. Обычная скорость запрессовки не более 5–7 мм/сек.
Наибольшее усилие запрессовки продольно-прессового соединения с гарантийным натягом равно:
, кг, (3.26)
где – коэффициент трения;
– диаметр охватываемой детали, мм;
– длина запрессовки, мм;
– напряжение сжатия на контактной поверхности, кг/мм2.
Напряжение можно определить по формуле:
, (3.27)
где – натяг в мкм;
– модули упругости материала соответственно охватываемой и охватывающей детали, кг/мм2;
– коэффициенты, учитывающие параметры и свойства материала детали.
;
, (3.28)
где – коэффициенты (для стальных деталей
.
Коэффициент трения для стальной втулки ; чугунной –
; латунной –
.
Соединения с нагревом охватывающей детали или охлаждением охватываемой при передаче крутящего момента имеют прочность в 2–3 раза большую, чем прочность обычных прессовых посадок.
Температура, до которой следует нагреть охватывающую деталь, определяется из условия, что натяг будет меньше произведения:
, (3.29)
где – коэффициент линейного расширения материала охватывающей детали;
– температура нагрева (прибавляется к начальной температуре детали);
– диаметр соответственно охватывающей и охватываемой детали.
Температура нагрева охватывающей детали должна быть равна:
. (3.30)
Если принять, что изменение натяга подчиняется зависимости:
, (3.31)
то минимальная температура нагрева должна быть равна:
. (3.32)
Для стальных деталей эта формула может быть упрощена:
0С. (3.33)
Температура охлаждения охватываемой детали может быть определена по формуле:
, (3.34)
где – конечная температура охлаждения детали с учетом ее начальной температуры (отнимается от начальной температуры);
– значение минимального зазора, позволяющего ввести охватываемую деталь в охватывающую (берется из таблиц справочных материалов).
Карбюраторных двигателей
Бензонасос диафрагменного типа
Основные дефекты, повреждения, отказы: разрыв диафрагмы, нарушение плотности прилегания клапанов к седлам, ослабление или поломка пружины диафрагмы, износ рычага в сопряжении с осью и эксцентриком, повреждения корпуса и крышки.
Диафрагмы, имеющие разрыв, заменяют. Клапаны притирают к седлам пастами, неисправные клапаны заменяют. Изношенную поверхность гнезда клапана фрезеруют специальной торцевой фрезой до выведения следов износа. В случае полного снятия торцевого выступа седла после фрезерования гнездо восстанавливают рассверливанием корпуса и запрессовкой (постановкой на клее) другого стального седла.
При изменении длины и упругости пружины диафрагмы свыше установленных величин пружину заменяют.
При износе отверстия в рычаге под ось отверстие рассверливают и ставят втулку. Изношенную поверхность подпятника рычага восстанавливают наплавкой и обработкой по шаблону.
Корпус и крышку насоса, имеющие неровность плоскостей разъема более 0,08 мм, пришабривают и притирают на плите пастами.
Изношенную резьбу под штуцер углубляют. Корпус и крышку насоса, имеющие трещины и обломы, выбраковывают. При установке крышки (головки) насоса на корпус соединительные винты следует затягивать при отжатой вниз на определенную величину диафрагме.
Состояние насоса до ремонта и после ремонта определяют испытанием на стенде СО-950.
Карбюратор
Основные дефекты, повреждения, отказы: повреждения поплавкового механизма, корпуса, крышки, изменения пропускной способности жиклеров, упругости пружин, пластин диффузоров; неудовлетворительная плотность игольчатого клапана, клапана экономайзера; износ осей дроссельной и воздушной заслонок; уменьшение производительности насоса-ускорителя.
Техническое состояние элементов карбюратора проверяют с использованием стенда СО-950 и прибора НИИАТ-528.
При разборке карбюратора его детали тщательно промывают керосином, смолистые отложения удаляют ацетоном или скипидаром с использованием волосяной щетки. Прочистка проволокой, ветошью не допускается.
Отказы поплавкого механизма могут быть связаны с нарушением герметичности игольчатого клапана, а также из-за трещин, щелей, вмятин поплавка.
Для обнаружения места неплотности у поплавка его погружают в нагретую до 80…90 0С воду. Если в течение 30 секунд не появятся пузырьки воздуха, поплавок считается годным.
При обнаружении отверстия его расширяют шилом, сливают из поплавка бензин, просушивают (пропаривают), затем запаивают отверстие.
У поплавков, имеющих вмятины, в центр вмятины припаивают стержень, за который вытягивают вмятую часть.
При проверке игольчатого клапана воздухом под давлением 20…30 МПа падение давления за 1 мин должно быть не более 1 кПа. При неудовлетворительной плотности клапана конусная часть его (угол конуса 600) шлифуют на станке, а кромку гнезда в штуцере поправляют сверлом или специальной фрезой вручную коловоротом. После этого притирают клапан к гнезду пастами М10…М15, захватывая иглу державкой.
Аналогично проводят проверку герметичности и ремонт клапана экономайзера.
Состояние калиброванных отверстий (жиклеров) для топлива и воздуха проверяют измерением их пропускной способности. Технические условия на пропускную способность жиклеров задают количеством кубических сантиметров воды, вытекающей из жиклера в минуту при напоре 10 кПа и температуре 20…10 0С. Жиклеры с неудовлетворительной пропускной способностью заменяют либо доводят их пропускную способность до нормы, для чего отверстие жиклера запаивают оловянно-свинцовым припоем, затем рассверливают и доводят до нужной пропускной способности с помощью разверток.
Для проверки производительности насоса-ускорителя поплавковую камеру заполняют топливом (делают 3…4 качка насосом), затем величину топлива, вытекшего в мерную мензурку за десять полных качков насоса, сравнивают с нормативной (табличной), конкретной для каждой марки карбюратора.
У карбюраторов типа К-22, К-124, К-126 момент включения экономайзера устанавливают при полном открытии дроссельной заслонки, а у карбюраторов типа К-84М, К-82МИ и К-88А – при зазоре между нижней кромкой дроссельной заслонки и стенкой смесительной камеры, равной 15,6 мм.
Изношенные оси дроссельной и воздушной заслонок заменяют, а отверстия в карбюраторе под оси рассверливают и в них запрессовывают втулки.
Расстояние от уровня топлива до плоскости разъема карбюратора должно соответствовать техническим условиям, соответствующим конкретной марке карбюратора. Уровень топлива регулируют подгибанием рычажка (язычка) поплавка под клапаном или постановкой или снятием прокладок под корпусом игольчатого клапана.
Баки и топливопроводы низкого давления
Топливные баки имеют следующие дефекты, повреждения, отказы: трещины, пробоины, отверстия от коррозии, вмятины, отпайки горловины. Неисправности определяются испытанием воздухом под давлением 0,02…0,03 МПа, помещая бак в ванну с водой.
Способы восстановления: запайка припоями; приварка или припайка накладок; заварка (газовая или электродуговая в среде углекислого газа); заклеивание или приклеивание накладок с помощью эпоксидного клеевого состава.
Мелкие вмятины оставляют, для исправления крупных вмятин вырезают окно, вводят болванку для правки вмятины, после чего окно заделывают.
Топливные баки до ремонта (при ремонте) промывают сначала 5%-м горячим раствором каустической соды, затем три раза горячей водой или выпаривают горячим паром или выхлопными газами.
Трещины и отверстия на топливопроводах низкого давления устраняют пайкой мягкими или твердыми припоями. Смятые участки трубок отрезают и трубку вновь соединяют, например газовой сваркой.
Ремонт системы охлаждения
Водяной насос двигателей внутреннего сгорания грузовых автомобилей и тракторов (типа СМД, А-01М, ЯМЗ, Д-50 и др.).
Дефекты, повреждения, отказы: трещины в корпусе, срыв резьбы в отверстиях, износ посадочных мест под подшипники и упорную втулку, износ посадочного места на валике под крыльчатку, износ боковой поверхности лопаток, износ поверхностей у валиков в сопряжении со втулками, сальниками и шкивами вентиляторов.
Трещины в чугунных корпусах заваривают газовой сваркой латунными прутками, припоями ЛОК и ЛОМНА и электродуговой сваркой порошковой проволокой ПАНЧ-11. Срыв резьбы исправляют постановкой резьбовых вставок и другими способами, характерными для восстановления резьб.
Изношенные посадочные места корпуса под подшипники и упорную втулку могут быть восстановлены путем отрезания части корпуса с последующими запрессовкой и приваркой вновь изготовленной части или запрессовкой колец с последующей механической обработкой посадочных мест до номинальных размеров. Торцевую поверхность опорной втулки и уплотнительную поверхность шайбы сальника притирают.
При износе крыльчатки старую ступицу отрезают, изготавливают и запрессовывают новую и стопорят двумя штифтами. Изношенные лопатки крыльчатки наплавляют газовой сваркой чугунными прутками и протачивают до требуемой высоты. Крыльчатки можно изготавливать литьем из алюминиевого сплава или капрона. При этом втулка ступицы должна быть стальной.
Изношенные поверхности у валиков восстанавливают наплавкой в среде углекислого газа с последующим хромированием и шлифованием.
После ремонта крыльчатку водяного насоса в сборе с валиком подвергают статической балансировке.
Водяные насосы обкатывают и испытывают на специальном стенде (например, насосы двигателей ЯМЗ-240Б на стенде ОР-8899). У насосов проверяют соответствие техническим требованиям величины зазора
|
|
Типы оградительных сооружений в морском порту: По расположению оградительных сооружений в плане различают волноломы, обе оконечности...
Папиллярные узоры пальцев рук - маркер спортивных способностей: дерматоглифические признаки формируются на 3-5 месяце беременности, не изменяются в течение жизни...
Адаптации растений и животных к жизни в горах: Большое значение для жизни организмов в горах имеют степень расчленения, крутизна и экспозиционные различия склонов...
Опора деревянной одностоечной и способы укрепление угловых опор: Опоры ВЛ - конструкции, предназначенные для поддерживания проводов на необходимой высоте над землей, водой...
© cyberpedia.su 2017-2024 - Не является автором материалов. Исключительное право сохранено за автором текста.
Если вы не хотите, чтобы данный материал был у нас на сайте, перейдите по ссылке: Нарушение авторских прав. Мы поможем в написании вашей работы!