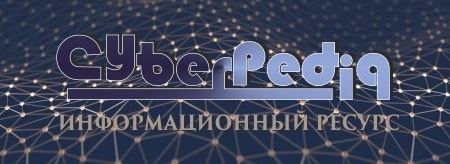
Археология об основании Рима: Новые раскопки проясняют и такой острый дискуссионный вопрос, как дата самого возникновения Рима...
Индивидуальные и групповые автопоилки: для животных. Схемы и конструкции...
Топ:
Теоретическая значимость работы: Описание теоретической значимости (ценности) результатов исследования должно присутствовать во введении...
Оценка эффективности инструментов коммуникационной политики: Внешние коммуникации - обмен информацией между организацией и её внешней средой...
Характеристика АТП и сварочно-жестяницкого участка: Транспорт в настоящее время является одной из важнейших отраслей народного хозяйства...
Интересное:
Берегоукрепление оползневых склонов: На прибрежных склонах основной причиной развития оползневых процессов является подмыв водами рек естественных склонов...
Подходы к решению темы фильма: Существует три основных типа исторического фильма, имеющих между собой много общего...
Уполаживание и террасирование склонов: Если глубина оврага более 5 м необходимо устройство берм. Варианты использования оврагов для градостроительных целей...
Дисциплины:
![]() |
![]() |
5.00
из
|
Заказать работу |
|
|
Методом Бринелля определяют твердость металлов в пределах НВ (80 – 450), но применение шариков из особо твердых сплавов позволяет измерить твердость до НВ 740. Толщина слоя металла, имеющего примерно одинаковую твердость, должна быть не менее 10 глубин вдавливания шарика. Поверхность металла в местах определения твердость должна быть обработана (зачищена) по плоскости.
Этот метод применяется для определения твердости заготовок для деталей (поковок, отливок и др.).
Достоинства метода Бринелля:
1) простота и надежность прибора измерения твердости;
2) отсутствие необходимости тщательной подготовки поверхности металла для измерения;
3) результат измерения определяет среднюю твердость в металлах с неоднородной твердостью зерен (например, чугун), вследствие большого размера отпечатка шарика в металле.
Недостатком этого метода является то, что его нельзя применять для измерения твердости тонких листов, лент, деталей с твердым тонким поверхностным слоем и деталей, на поверхности которых недопустим большой размер отпечатка шарика.
Достоинством метода Роквелла является то, что им можно измерять твердость более тонких и твердых слоев металла, чем методом Бринелля, причем размеры отпечатка на детали и затрата времени на измерение меньше, чем при методе Бринелля.
Недостатки метода Роквелла:
1) тщательная подготовка поверхности металла для измерения;
2) необходимость в специальном помещении (чистота, отсутствие вибрации);
3) на результат измерения из-за малого размера отпечатка сильно влияет неоднородность некоторых металлов.
8. Контрольные вопросы
8.1. Что такое твердость металлов?
8.2. Как изменяется глубина отпечатка на образце в зависимости от твердости материала?
|
8.3. Укажите нагрузку, и диаметр шарика при испытании на твердость заготовку из стали?
8.4. Как обозначается твердость по Роквеллу? Расшифруйте все символы.
8.5. Как изменяется прочность металла при увеличении его твердости.
8.6. Для каких материалов используют метод Виккерса?
8.7. В каких единицах измеряется твердость по Бринеллю, Виккерсу и Роквеллу?
8.8. В чем состоят достоинства и недостатки методов?
8.9. Как определяется твердость по Бринеллю?
8.10. Как определяется твердость по Виккерсу?
8.11. Как определяется твердость по Роквеллу?
8.12. Почему используются разные инденторы?
8.13. Для чего применяется предварительное нагружение в методе Роквелла?
8.14. Как работает индикатор твердомера Роквелла?
8.15. В чем необходимость использования различных методов определения твердости?
Лабораторная работа №3
МАКРОСТРУКТУРНЫЙ И МИКРОСТРУКТУРНЫЙ АНАЛИЗ
МЕТАЛЛОВ И СПЛАВОВ
Ц ель работы
1.1. Изучить методику макроструктурного анализа металлов и сплавов невооруженным глазом или при увеличении до 30…50 раз через лупу.
1.2. Освоить технологию приготовления микрошлифов, ознакомиться с устройством металлографического микроскопа, изучить микроструктуры шлифа до и после травления; уяснить принцип выявления структур и практическое значение данного метода.
Приборы и материалы
2.1. Оборудование: Шлифовальная машина (цеховая), полировальная машина, металлографический микроскоп МИМ – 2.
2.2. Материалы: образцы макрошлифов и изломов, заготовки для микрошлифов из стали 40 (в равновесном состоянии), шлифовальная бумага отечественного производства (под номерами 12, 10, 8, 6, 4), войлочный круг для полировки, 5-% раствор азотной кислоты в этиловом спирте, дисцилированная вода, паста ГОИ или окись хрома, полировочная алмазная паста.
Техника безопасности
3.1. Процесс подготовки микрошлифов следует проводить в спецодежде или в халатах.
|
3.2. Процесс травления микрошлифов производить только под вытяжным шкафом с использованием средств индивидуальной защиты.
3.3. Процесс шлифования и полирования микрошлифов следует производить только с использованием специального приспособления.
3.4. Включение шлифовальной и полировальной машины следует производить только в присутствии преподавателя или учебного мастера.
3.5. Запрещается самостоятельно устранять неисправности оборудования.
Порядок выполнения работы
4.1. Зарисовать по образцам изломы с выявлением размеров зерен, волокнистости, кристалличности, дендритности и др.
4.2. Механически обработать образец для приготовления микрошлифа (шлифование, полирование).
4.3. Изучить микроструктуру шлифа под микроскопом до травления.
4.4. Определить общее увеличение микроскопа.
4.5. Зарисовать схему увеличенной микроструктуры, указав строение сплава (неметаллические включения, металлическую основу). Пользуясь шкалой баллов, определить балл оксидов и сульфидов (ГОСТ 1778—70).
4.6. Протравить шлиф реактивом.
4.7. Изучить микроструктур шлифа под микроскопом после травления.
4.8. Зарисовать схему микроструктуры после травления, указав строение сплава (границы зерен, зерна однородного и неоднородного строения, размер зерна), пользуясь для этого шкалой величины зерна (ГОСТ 5639—65).
Содержание отчета
Вотчет необходимо включить: название работы, цель работы, технологию приготовления микрошлифа; реактив, применяемый для травления стали и чугуна; оптическую схему металлографического микроскопа и ее краткое описание; схемы микроструктур иих описание. В выводах указать особенности строения исследуемого металла, выявленные микроанализом до травления и после травления, наличие неметаллических включений, дефектов, размер, форму зерен и их влияние на свойства (красноломкость), прочность, твердость, пластичность.
Работу выполнил:
ст.-т___________гр._____________
Работу принял:
______________________________
Общие сведения
Современные металлы и сплавы, различаясь по составу и строению, обладают разнообразными свойствами. Независимо от этого, в процессе эксплуатации машин в результате изнашивания, коррозии, усталости материала и других процессов, а так же из-за нарушений режимов эксплуатации, правил обслуживания степень годности бывших в эксплуатации деталей и сборочных единиц к дальнейшему использованию может быть различной. В конкретных условиях трения и изнашивания деталей изменяются геометрические параметры, шероховатость рабочих поверхностей и физико-механические свойства поверхностных слоев материала, а так же возникают и накапливаются усталостные повреждения. В связи с этим для получения достаточной информации о пригодности деталей к дальнейшему использованию результаты, какого либо одного метода испытания, даже очень совершенного, не могут дать полной информации о ресурсах дальнейшей работоспособности деталей. Для решения данных проблем обычно используются несколько методов анализа, которые дополняют друг друга. Однако о работоспособности большинства деталей, бывших в эксплуатации, можно судить и по результатам определенных, даже несложных методов анализа. В данных методических указаниях приведены основные из них.
|
Структурные методы исследования включают методы макроструктурного и микроструктурного анализа. Метод макроструктурного анализа (макроанализ) заключается в изучении строения металлов и сплавов невооруженным глазом или при небольших увеличениях с помощью лупы.
Макроанализ позволяет наблюдать одновременно большую поверхность образца или детали, поэтому при помощи микроструктурного анализа можно установить вид излома (вязкий, хрупкий), величину, форму и расположение зерен и дендритов литого металла, характер предшествующей обработки металла и т. д.
Кроме того, макроанализ дает возможность обнаружить газовые пузыри, усадочные пустоты, трещины, ликвацию серы, фосфора и т. д.
Ликвацией называется неоднородность химического состава в сплавах. Различают три вида ликвации: зональную, по удельному весу и дендритную (внутрикристаллическую).
Зональная ликвация наблюдается в объеме слитка. По мере кристаллизации металл слитка будет все более разделяться по температуре кристаллизации компонентов: вначале кристаллизуются более тугоплавкие составляющие, затем – менее тугоплавкие, поэтому химический состав зон будет различным.Однако в процессе многократной обработки давлением(более 90 – % металлических сплавов в настоящее время подвергаются обработке давлением) начальная зональная ликвация нивелируется и становится малосущественной.
|
Ликвация по плотности (удельному весу) наблюдается при сплавлении металлов, сильно различающихся по плотности. Так, в сплавах системы свинец – сурьма верхняя часть слитка будет обогащена сурьмой, тем самым, отличаясь от среднего состава сплава.
Дендритная ликвация наблюдается в объеме одного зерна. Чем больше температурный интервал между началом и концом кристаллизации сплава, тем больше будут отличаться по составу отдельные участки внутри зерен. В этих случаях в дендритах оси первого порядка бывают обогащены более тугоплавким компонентом и в них содержание различных примесей бывает наиболее низким. Кристаллизующиеся в конце междендритные пространства содержат наибольшее количество более легкоплавких компонентов и различных примесей.
Изучение макроструктуры нередко дополняется так же исследованием излома металла, что позволяет судить о причинах разрушения (усталостный излом, закалочные трещины и т. п.).
Усталостные повреждения нарушают сплошность материала, способствуют возникновению микро- и макротрещин, выкрашиванию металла рабочих поверхностей и излому деталей.
Постепенное накопление повреждений в металлах и сплавах под действием циклических нагрузок, приводящих к образованию трещин и разрушению, называют усталостью, а свойство металлов сопротивляться усталости – выносливостью.
Усталостный излом состоит из места зарождения разрушения, из очага разрушения, зоны стабильного развития трещины и зоны долома – участка развития трещины, связанного с окончательным разрушением. Очаг разрушения обычно расположен вблизи поверхности. Поверхность как наиболее нагруженная часть сечения (при изгибе, кручении) претерпевает микродеформации, а затем в наклепанной зоне образуются подповерхностные трещины. Растет, однако, только та трещина, которая имеет достаточную длину и острую вершину – магистральная трещина. Продвигаясь в глубь металла, усталостная трещина образует глубокий и острый надрез. Скорость роста трещины невелика. Рост трещины продолжается до тех пор, пока сечение не окажется столь малым, что действующие напряжения превысят разрушающие. Тогда происходит быстрое разрушение, что и приводит к образованию зоны долома. Зона долома имеет структуру, характерную для разрушения при однократных разрушениях (хрупкого или вязкого в зависимости от природы материала). Для определения предела выносливости (наибольшее значение напряжения цикла, при действии которого не происходит усталостное разрушение образца после заданного числа циклов нагружения) проводят испытания на усталость по ГОСТ 25502 – 84. Цикл нагружения – это совокупность переменных значений напряжений за один период их изменения.
|
Дефекты шлифования вызываются значительными контактными напряжениями (до 10000 кгс/мм2) и температурами (до 1000 град.), возникающими из-за неблагоприятной формы абразивных зерен (большие углы резания). Одной из главных причин такого напряженного состояния является то обстоятельство, что значительная часть зерен не режет, а проскальзывает из – за того, что радиусы закругления режущего лезвия зерен большие – они быстро притупляются и в при дальнейшей работе зерна не режут, а проскальзывают. В поверхностных слоях обрабатываемых деталей происходят структурные превращения, появляются значительные напряжения. Это приводит к «пережогу» и возникновению трещин, которые являются началом разрушения.
Для макроструктурного анализа не требуется специального, сложного оборудования, достаточно знаний влияния видов выявленных дефектов на работоспособное состояние деталей.
Методом микроструктурного анализа изучают поверхностное строение металлов и сплавов при помощи оптических микроскопов при относительно больших увеличениях - обычно от 50 до 2000 раз. ПРИ таких увеличениях можно обнаружить элементы структуры размером до 0,2 мкм. Изучение микроструктуры проводят на специально приготовленных образцах – микрошлифах. Микрошлифы должны иметь зеркально-блестящую поверхность, потому что структуру металлов и сплавов как тел непрозрачных, рассматривают в отраженном свете (устройство микроскопа приведено ниже).
Под микроскопом на микрошлифе после полирования можно увидеть микротрещины и неметаллические включения (графит в чугунах, оксиды, сульфиды и т. д.). Для выявления самой микроструктуры металла поверхность шлифа травят, т.е. обрабатывают специальными реактивами, состав которых зависит от состава металла. Выявление микроструктуры при травлении основано на том, что различные фазы протравливаются неодинаково и таким образом, окрашиваются по-разному. В результате травления микрошлифов чистых металлов, возможно, выявить форму и размеры отдельных зерен. Микроанализ позволяет установить величину, форму и ориентировку зерен, отдельные фазы и структурные составляющие, изменение внутреннего строения металлов и сплавов в зависимости от условий их получения и обработки и т. д.
Теоретические сведения
При макроанализе применяют два метода исследований: метод изломов и метод макрошлифов.
Метод изломов позволяет установить характер предшествующей обработки металлов давлением, величину зерен, виды чугунов, дефекты внутреннего строения (поры, трещины и др.). Изучение изломов производят визуально или с пользованием лупы 10…30-ти кратного увеличения Исследование излома является очень простым и широко распространенным испытанием металла. Излом стали может быть крупно, средне- и мелкозернистым. Чрезвычайно крупнозернистый излом принято называть сахаровидным, а самый мелкозернистый – фарфоровидным. Кроме того, бывают изломы волокнистые, столбчатые и слоистые (шиферные). Излом можно характеризовать по цвету его, – например темный или светлый, а также по степени его однородности.
Сахаровидные, крупнозернистые изломы отвечают или литому, или перегретому металлу, т. е. условиям, способствующим сильному росту зерна; мелкозернистые изломы отвечают высокому качеству стали.
Обычно низкоуглеродистая мягкая сталь имеет излом более крупнозернистый, нежели высокоуглеродистая. Большое значение имеет способ получения излома: спокойной нагрузкой, ударом или же при усталости; в последнем случае излом очень характерен. В случае местного приложения нагрузки, особенно при ударе надрезанного образца, когда при работе разрушения участвует малый объем стали, излом получается более крупнозернистым. |
Метод макрошлифов дает возможность исследовать структуру, образующуюся в процессе кристаллизации или последующей обработки давлением. Этим способом можно выявить волокнистость, ликвацию серы и фосфора, различного вида дефекты: усадочную раковину, газовые пузыри, поры, трещины и др. Макрошлиф приготовляют шлифованием образца. Подготовленную поверхность травят соответствующим реактивом для выявления структуры.
Дендриты. При затвердевании стали перпендикулярно внешней поверхности (рис. 3.1) образуются дендритные (древовидные – елочные) кристаллы, бедные углеродом и фосфором, остальная же масса обогащается последними. Фотографии стали, протравленной на дендриты, показана на рис. 3.1. Эта первичная (дендритная) кристаллизация остается и после механической и термической обработки ииногда бывает очень ясно выражена. Хорошим реактивом для выявления дендритной структуры является персульфат аммония.
Волокна. При глубоком травлении поверхности шлифа на макроструктуре его появляются волокна, направление которых соответствует деформации
![]() | при прокатке или ковке. Появление волокон обусловливается неоднородностью стали: получившиеся при затвердевании дендриты и неравномерное распределение вредных примесей различно поддаются травлению. Одни волокна стойки и очень мало поддаются разъедающему действию кислот, другие, более богатые примесями, разъедаются глубоко. Лучшим реактивом для травления макроструктуры стали, особенно для выявления волокон, является раствор 1 части технической (не химически чистой) соляной кислоты в 1 части воды. Этот реактив употребляется подогретым до 80°. |
Рисунок 3.1 – Макроструктура стали, протравленной на дендриты. |
При этой температуре реактив действует энергично и не испаряется. Перед травлением образец очищается, нагревается в горячей воде и затем погружается в реактив, нагретый до 80°. Время травления определяется практически. После травления образец промывается и сушится. Для предохранения от окисления поверхность покрывается тонким споем вазелина или прозрачного лака.
На рис. 3.2 приведен пример макроструктуры расположения волокон у шестерен. Изучение направления волокон позволяет определить метод производства изделия, например, правильно или нет коленчатый вал отштампован. Для службы изделия чрезвычайно важно, особенно в опасных сечениях, идут ли волокна вдоль направления действия сил или поперек, если они идут поперек, то может произойти поломка.
Рис. 3.2 Макроструктура правильно откованной шестерни
На практике поломка коленчатых валов, зубьев шестерен, кулаков и пр. зачастую этим и объясняется. В производстве при установлении процессов ковки и штамповки чрезвычайно важно знать расположение волокон в макроструктуре. Одновременно с выявлением волокон глубокое травление оченьхорошо обнаруживает и всякого рода трещины, даже бывшие до травления незаметными (рис. 3.3).
| Зоны закалки, цементации. Эти зоны прекрасно обнаружива ются и измеряются по макроструктуре. Лучшим реактивом для выявления закаленных зон является 10°/о водный раствор азотной кислоты. Зоны цементации и обезуглероживания обычно определя ются по излому или же по шлифу, изготовленному и протравлен ному для исследования под микроскопом. В случае определения глубины цементации по излому, его можно протравить 10% рас твором азотной кислоты в воде или еще лучше - нагреть на металлическом листе до появления синего цвета побежалости у твердого закаленного слоя. Микроанализ. Микроанализ применяют дляизучения внутреннего строения металлов и сплавов на оптическом микроскопе при увеличении от 50 до 1500 раз илина электронном микроскопе при увеличении порядка 5000...20000 раз. | |||
Рисунок 3.3 – Трещины в поковке, обнаруженные глубоким травлением |
(Впервые в мире структуру высококачественной стали исследовал с помощью микроскопа инженер Павел Петрович Аносов в 1831 г.).
Для проведения микроисследования от изучаемой детали или заготовки отрезают образец, который специально обрабатывают для придания одной из его поверхностей прямолинейности и зеркального блеска. Образец, подготовленный к микроанализу, называют микрошлифом. На практике приходится изготовлять шлифы больших размеров (рис. 3.3, а, б) и малых (рис. 3.4, б, г).
Рис. 3.4 Виды металлографических образцов для приготовления микрошлифов:
|
|
При изготовлении микрошлифов из образца малых а и б – без приспособлений; в и г – в приспособлениях (1 – образец; 2 – трубка; 3 – пластмасса, легкоплавкий сплав или сера; 4 – струбцина), размеров (проволока, стружка, листы и др.) для их надежного крепления используют специальные струбцины (см. рис. 3.3, г) или заливают образцы легкоплавким сплавом Вуда (50% Bi, 25% РЬ, 12,5% Sn и 12,5% Cd) с температурой плавления 68 0С, серой или пластмассой (см. рис. 3.3, в).
Для проведения микроанализа необходимо: изготовить шлиф; изучить под микроскопом структуру на полированной поверхности шлифа (до травления); протравить полированную поверхность; изучить под микроскопом структуру протравленной поверхности шлифа.
Изготовление микрошлифа включает следующие операции: отрезку образца, его торцовку, шлифование и полирование.
Отрезка образца нужныхразмеров проводится резцом или ножовкой (при твердости металла НВ<300) ли дисковым шлифовальным или отрезным кругом (при твердости металла НВ >300) с охлаждением водой или эмульсией, чтобы образец не нагревался свыше 150° С и его структура не изменялась.
Торцовка шлифа осуществляется с целью придания прямолинейности одной из его поверхностей и проводится опиловкой напильником или шлифовальным кругом.
Шлифование необходимо для удаления рисок, оставшихся от торцовки. Это достигается обработкой поверхности шлифа шлифовальной бумагой различной зернистости (разных номеров). Шлифовальная бумага отечественного производства имеет следующую нумерацию: 12, 10, 8, 6, 5, 4, 3 (номер обозначает, примеряю величину зерна в сотых долях миллиметра). Для предварительного чернового шлифования берут бумагу первых четырех номеров. Заканчивают шлифование бумагой номерами 5...3 с мелкими абразивными зернами. Шлифование проводят вручную или на специальном шлифовальном станке. Вручную образец шлифуют так: наждачную бумагу кладут на толстое стекло, затем образец (шлиф) прижимают к бумаге и, удерживая его тремя пальцами, перемещают по ней в одном направлении, но обязательно перпендикулярно рискам от предыдущей обработки. Этого правила необходимо придерживаться и при переходе с одного номера шлифовальной бумаги на другой для удобства наблюдений за выведением рисок и ускорения процесса шлифования.
Полирование проводят на быстровращающемся диске с сукном, которое смачивается водой с взвешенными в ней частицами какого-либо абразива (окись хрома или алюминия). Частицы окиси металла весьма тверды, поэтому во время полирования они режут металл образца. Так как эти частицы дисперсные, он способен снимать мельчайшие неровности, делая поверхность шлифа зеркального вида, без рисок даже при рассмотрении под микроскопом. Готовый полированный шлиф последовательно тщательно промывают водой, спиртом и сушат, прикладывая (промокая) фильтровальную бумагу.
|
Изучение полированной поверхности шлифа под микроскопом преследует 'цель определить качество изготовления шлифа (отсутствие следов обработки) и установить характер расположения и размеры микроскопических трещин, неме
таллических включений — графита, сульфидов, оксидов (рис. 3.5) в металлической основе (имеет светлый вид при рассмотрении под микроскопом)
Структуру металлической основы шлифа после полирования выявляют травлением его реактивом. Для стали и чугуна чаще всего применяют 2...5%-ный раствор
а – оксиды; б – сульфиды; в – графит.
Рисунок 3.5 – Неметаллические включения в стали и чугуне
азотной кислоты (HNO3) в этиловом спирте. Полированную поверхность шлифа погружают в реактив на 3...15 с или протирают ватой, смоченной в реактиве, до появления ровного матового оттенка без наличия каких-либо пятен. Затем шлиф промывают спиртом или водой и просушивают фильтровальной бумагой.
Любой металл или сплав является поликристаллическим телом, то есть состоит из большого числа различно ориентированных кристаллитов или зерен. На границах зерен (даже чистейших металлов) обычно располагаются различные примеси. Эти примеси и структурные составляющие двухфазного строения (механические смеси) под действием реактива образуют микроскопические гальванические пары, что способствует более быстрому их растворению. Однофазные структуры (чистые металлы, твердые растворы, химические соединения) травятся медленнее. В результате неодинаковой степени травимости структурных составляющих на поверхности шлифа создается микрорельеф (рис. 3.5).
Изучение протравленной поверхности шлифа под оптическим микроскопом позволяет увидеть микроструктуру металлической основы. Она обычно состоит из светлых и темных участков. Это объясняется неодинаковой степенью отражения света от структурных составляющих. Структура, растворившаяся на большую глубину, под микроскопом имеет темный цвет (см. рис. 3.6, а ), так как дает больше рассеивающих лучей; структура же, растворившаяся меньше, за счет прямого отражения света имеет светлый цвет (см. рис. 3.6, б).
а –зерна во впадинах – темного цвета, выступающие светлого;
б – границы зерен металлов и твердых растворов
Рисунок 3.6 – Схемы, поясняющие видимость под микроскопом
Границы зерен будут видны в виде тонкой темной сетки (см. рис. 3.5, б). Часто зерна металла одного и того же фазового состава под микроскопом могут иметь различные оттенки. Это объясняется тем, что каждое зерно в плоскости шлифа имеет свое сечение кристаллической решетки с различным количеством в нем атомов, а, следовательно, и свойства зерен отличаются одно от другого способностью протравливаться, прочностью и др. Такое явление называется анизотропией.
Строение металла, наблюдаемое в металлографическом микроскопе, называется микроструктурой, которая представляет собой изображение весьма малого участка поверхности, составленное из отраженных от него световых лучей.
Принципиальная оптическая схема металлографического микроскопа МИМ- 7 показана на рисунке 3.7. Увеличение микроскопа определяется произведением увеличения окуляра на увеличение объектива. Объектив дает обратное увеличенное действительное изображение. Окуляр как обычная лупа укрупняет изображение, полученное объективом.
В результате изучения микроструктуры можно установить: количество структурных составляющих сплава и характер их расположения; величину зерен (путем их сопоставления со специально установленной шкалой или непосредственным измерением, зная величину увеличения); вид термической обработки и правильность выбора ее режима (температуры нагрева, скорости охлаждения); приближенное содержание некоторых элементов, например углерода, в отожженных сталях.
Между структурой и свойствами металлов и сплавов существует прямая зависимость. Поэтому в практике металловедения микроанализ является одним из основных методов, позволяющих изучить строение металлов и сплавов, получить сведения об их свойствах.
1 – осветитель (лампа); 2 – коллектор; 3 – зеркало; 4, в, 8 – линза; 5 – апертурная диафрагма; 7 – призма; 9 – отражательная пластинка; 10 – объектив; 11 – объект; 12 – ахроматическая линза; 13 – окуляр; 14, 16 – зеркало; 15 – фотоокуляр; 17 – фотопластинка; 18 – полевая диафрагма; 19 – затвор; 20 – линза для работы в темном поле; 21 – кольцевое зеркало; 22 – параболическое зеркало; 23 – заслонка (включается при работе в темном поле); 24 – поляризатор; 25 – анализатор.
Рисунок 3.7 – Оптическая схема микроскопа МИМ-7
Список рекомендуемой литературы
8.1. Беккерт М., Клемм Х. Способы металлографического травления – М.: Металлургия, 1998.
8.2. Практикум по технологии конструкционных материалов и материаловедениет / Под ред. С.С. Некрасова – М.: Агропромиздат, 1991.
9. Контрольные вопросы
9.1. Что называется микро и макроструктурой металла.
9.2. Основное назначение микроструктурного и макроструктурного анализа. Их отличия.
9.3. Методика подготовка микрошлифа и макрошлифа.
9.4. Для какого вида анализа необходимо изготовить шлиф с зеркальным блеском.
9.5. С какой целью производят травление микро - и макрошлифов.
9.6. Каким образом происходит выделение границ зерен структуры при травлении.
9.7. Для выявления каких дефектов используют метод Баумана.
9.8. Назовите основные реактивы, используемые при травлении микрошлифов.
9.9. Объясните принцип появления видимости микроструктуры по микроскопом.
9.10. С какой целью производят полировки микрошлифа перед травлением.
9.11. Назначение светофильтров в оптической схеме микроскопа.
9.12. Чем отличаются макро и микро анализ?
9.13. В чем преимущества микроанализа?
9.14. Необходимость использования струбцины при шлифовке и полировке образцов?
9.15. С какой целью не допускается перегрев поверхности микрошлифа?
Лабораторная работа №4
|
|
Наброски и зарисовки растений, плодов, цветов: Освоить конструктивное построение структуры дерева через зарисовки отдельных деревьев, группы деревьев...
Типы оградительных сооружений в морском порту: По расположению оградительных сооружений в плане различают волноломы, обе оконечности...
История развития хранилищ для нефти: Первые склады нефти появились в XVII веке. Они представляли собой землянные ямы-амбара глубиной 4…5 м...
История развития пистолетов-пулеметов: Предпосылкой для возникновения пистолетов-пулеметов послужила давняя тенденция тяготения винтовок...
© cyberpedia.su 2017-2024 - Не является автором материалов. Исключительное право сохранено за автором текста.
Если вы не хотите, чтобы данный материал был у нас на сайте, перейдите по ссылке: Нарушение авторских прав. Мы поможем в написании вашей работы!