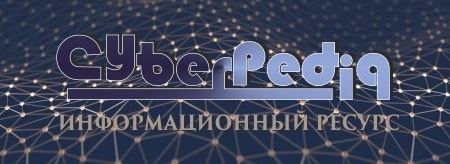
История развития хранилищ для нефти: Первые склады нефти появились в XVII веке. Они представляли собой землянные ямы-амбара глубиной 4…5 м...
Адаптации растений и животных к жизни в горах: Большое значение для жизни организмов в горах имеют степень расчленения, крутизна и экспозиционные различия склонов...
Топ:
Характеристика АТП и сварочно-жестяницкого участка: Транспорт в настоящее время является одной из важнейших отраслей народного хозяйства...
Проблема типологии научных революций: Глобальные научные революции и типы научной рациональности...
Методика измерений сопротивления растеканию тока анодного заземления: Анодный заземлитель (анод) – проводник, погруженный в электролитическую среду (грунт, раствор электролита) и подключенный к положительному...
Интересное:
Мероприятия для защиты от морозного пучения грунтов: Инженерная защита от морозного (криогенного) пучения грунтов необходима для легких малоэтажных зданий и других сооружений...
Влияние предпринимательской среды на эффективное функционирование предприятия: Предпринимательская среда – это совокупность внешних и внутренних факторов, оказывающих влияние на функционирование фирмы...
Искусственное повышение поверхности территории: Варианты искусственного повышения поверхности территории необходимо выбирать на основе анализа следующих характеристик защищаемой территории...
Дисциплины:
![]() |
![]() |
5.00
из
|
Заказать работу |
|
|
Базирующие устройства
Общие сведения о базировании заготовок на машинах. Базированием называется процесс ориентирования обрабатываемой заготовки относительно определенных, называемых установочными, поверхностей машины для обеспечения необходимого ее расположения при обработке.
Заготовки базируются относительно главного обрабатывающего органа с помощью технологических баз заготовки по установочным поверхностям базирующих элементов машины.
Технологической базой называют совокупность поверхностей, линий или точек заготовки, по отношению к которым ориентируются поверхности детали при обработке.
Базирующими элементами машины называют ее устройства, предназначенные для базирования заготовок. Ими могут быть не только столы, каретки, суппорты, направляющие линейки, угольники, упоры, но и другие устройства.
Установочными поверхностями базирующих элементов машины являются поверхности для базирования заготовки, соприкасающиеся с ее технологической базой (рис. 79, а). Для ориентировки тела в пространстве необходимо лишить его шести степеней свободы: трех поступательных перемещений вдоль осей координат х, у, z и трех вращений вокруг этих же осей (рис. 79, б). Заготовку ориентируют с помощью трех установочных поверхностей — главной, направляющей и упорной (рис. 79, в). Нижняя поверхность А заготовки, несущая три базирующие точки 1, 2, 3, соприкасается с главной установочной поверхностью и называется главной базирующей поверхностью. Обычно это поверхность с наибольшими габаритными размерами, т.е. пласть призматической заготовки. Боковая поверхность В заготовки, несущая две базирующие точки 4 и 5, соприкасается с направляющей установочной поверхностью и называется направляющей базирующей поверхностью.
|
В качестве нее выбирается поверхность, отличающаяся наибольшей протяженностью, обычно одна из кромок призматического тела. Торцовую поверхность С заготовки, несущую на себе одну опорную точку 6 и соприкасающуюся с упорной установочной поверхностью, называют упорной базирующей поверхностью.
Виды базирования. В зависимости от характера взаимодействия установочных поверхностей с базирующими поверхностями заготовки различают три способа базирования — неподвижное, подвижное и комбинированное (рис. 80).
Неподвижным называется базирование, при котором базирующие поверхности заготовки в процессе обработки не перемещаются относительно установочных поверхностей базирующих устройств машины. Однако заготовка, оставаясь неподвижной относительно базирующих устройств, движется вместе с ними относительно инструмента (или инструмент относительно заготовки), причем движение может быть поступательным или вращательным.
При позиционной обработке заготовка неподвижна и на нее надвигается инструмент. На рис. 80, а сверлильный суппорт 2 высверливает отверстие в заготовке 1. При проходной обработке деталь вместе с базирующими устройствами перемещается мимо инструмента. На рис. 80, б торцы заготовки 3, закрепленной в суппорте 7, опиливаются пилой 2.
Неподвижное базирование при вращении заготовки возможно в центрах или патроне. В лущильном станке (рис. 80, в) с чурака 3, зажатого центрами 1, надвигающимся ножом 2 срезается шпон.
Подвижным (скользящим) называется базирование, при котором базирующие поверхности заготовки в процессе обработки перемещаются (скользят) относительно установочных поверхностей базирующих устройств машины.
На рис. 80, д показан случай подвижного базирования при поступательном движении. Заготовка 2 главной базирующей поверхностью скользит по установочным поверхностям переднего 1 и заднего 4 столов фуговального станка, базируясь на них в процессе обработки ножами, установленными на валу 3. Случай подвижного базирования при вращательном движении иллюстрирует схема станка для шлифования круглых деталей (рис. 80, ё) и круглопалочного станка (рис. 80, ж).
|
Комбинированным называется базирование, при котором часть базирующих поверхностей заготовки в процессе обработки остается неподвижной, а часть перемещается относительно установочных поверхностей базирующих устройств машины (рис. 80, и, з).
Конструкции базирующих устройств. К системе базирующих устройств относятся: собственно базирующие элементы — установочные базы машины; зажимные и прижимные элементы и средства механизации базирования.
Элементы базирующих устройств могут быть специальными и универсальными. Часто элементы механизмов подачи (конвейеры, суппорты), а иногда и механизмы главного движения (центры, патроны) одновременно являются элементами базирования.
Собственно базирующие элементы машин отличаются большим разнообразием: столы, направляющие линейки, упоры, роликовые конвейеры, каретки, конвейеры, кулачки, патроны и т.д.
Во избежание отхода базирующих поверхностей заготовок от установочных поверхностей машины необходимо обеспечить их плотное и непрерывное соприкосновение силовым замыканием, которое достигается либо собственной массой, либо под действием рук рабочего, либо с помощью специальных приспособлений, прижимных или зажимных устройств.
Прижимными устройствами (прижимами) называют устройства силового замыкания со скользящим контактом с заготовкой, а зажимными (зажимами) — с неподвижным контактом. Зажимные и прижимные устройства по принципу действия можно разделить на четыре вида: винтовые, пневматические, эксцентриковые и пружинные. В современных станках применяют поршневые (пневматические), эксцентриковые и пружинные устройства.
Зажимы пневматические (рис. 81, а) могут быть поршневые и диафрагменные, одно- и двустороннего действия. Эти устройства являются быстродействующими, с легким ручным или автоматизированным управлением. Без учета потерь на трение усилие зажима на штоке для цилиндра двустороннего действия:
где F 3 — усилие на штоке, Н; Р —давление в воздушной сети, 0,5 МПа; D — диаметр поршня, см.
|
Усилие на штоке в одностороннем цилиндре меньше из-за действия силы сопротивления пружины q, Н:
Диафрагменные цилиндры отличаются компактностью, малой массой, отсутствием трущихся поверхностей, но имеют ограниченный ход штока (30...35 мм).
Усилие на штоке диафрагменного одностороннего цилиндра:
где F 3 — усилие на штоке, Н ; D — внутренний диаметр по контуру зажима диафрагмы, см; d — диаметр диска на диафрагме, см; Р — давление в сети, МПа.
Гидравлические зажимы аналогичны пневматическим, но работают при давлении в гидросети 5...6,5 МПа.
Эксцентриковые (рис. 81, б) и кулачковые зажимные устройства работают за счет радиального усилия, развивающегося при изменении расстояния от центра вращения эксцентрика или кулачка до рабочей поверхности. К эксцентриковым относят механизмы с профилем звена, очерченным по дуге окружности, к кулачковым — по математической кривой, когда не требуются большие силы зажима.
Величина зажимного усилия эксцентрикового устройства определяется по формуле
где Q — сила, приложенная к рукоятке, Н; l — плечо, мм; е — эксцентриситет, мм; D — диаметр эксцентрика, мм;/— коэффициент трения на поверхности эксцентрика.
Величина усилия на рычаге обычно принимается Q = 40... 80 Н.
Применяются торцевые кулачки (рис. 81, в), рабочий профиль которых сформирован по винтовой линии. Кулачок снабжается рукояткой. При повороте кулачка двуплечий рычаг зажимает заготовку. Сила зажима определяется, как в винтовых устройствах, с учетом передаточного отношения рычага:
где Q — сила, приложенная к рукоятке, Н; l — плечо, мм; r ср — средний радиус скольжения опорной точки плеча рычага, мм; α — угол подъема линии профиля кулачка; φ — угол трения; а, b — длины плеч рычага.
На станках с проходной обработкой заготовки прижимают к базирующим поверхностям роликовыми элементами (рис. 82, а). Ролик 1 в прижимном устройстве устанавливается на оси штока 4, который перемещается в осевом направлении цилиндра 2. Цилиндр закрепляется на подвижной балке 3, которая при наладке станка может перемещаться по колонне 7в вертикальном направлении. Усилие прижима создается за счет упругости пружины 5 колпачком 6.
|
В некоторых станках в качестве прижимных элементов используются плоские пружины (рис. 82, б). На форматных и шипорезных станках с проходной обработкой применяют прижимные устройства с гибкой лентой (клиновой ремень, рис. 82, в). Несущим элементом устройства является рама 2, на которой смонтированы опоры шкивов 1 и 6. Опора шкива 6 подвижная, что позволяет производить натяжение ленты 4 натяжным механизмом 5. Жесткость ленте придают ролики 7, закрепленные на осях подпружиненных кронштейнов. Рама 2 установлена на суппорте 3, что позволяет производить наладку прижимного устройства.
Базирующие устройства
Общие сведения о базировании заготовок на машинах. Базированием называется процесс ориентирования обрабатываемой заготовки относительно определенных, называемых установочными, поверхностей машины для обеспечения необходимого ее расположения при обработке.
Заготовки базируются относительно главного обрабатывающего органа с помощью технологических баз заготовки по установочным поверхностям базирующих элементов машины.
Технологической базой называют совокупность поверхностей, линий или точек заготовки, по отношению к которым ориентируются поверхности детали при обработке.
Базирующими элементами машины называют ее устройства, предназначенные для базирования заготовок. Ими могут быть не только столы, каретки, суппорты, направляющие линейки, угольники, упоры, но и другие устройства.
Установочными поверхностями базирующих элементов машины являются поверхности для базирования заготовки, соприкасающиеся с ее технологической базой (рис. 79, а). Для ориентировки тела в пространстве необходимо лишить его шести степеней свободы: трех поступательных перемещений вдоль осей координат х, у, z и трех вращений вокруг этих же осей (рис. 79, б). Заготовку ориентируют с помощью трех установочных поверхностей — главной, направляющей и упорной (рис. 79, в). Нижняя поверхность А заготовки, несущая три базирующие точки 1, 2, 3, соприкасается с главной установочной поверхностью и называется главной базирующей поверхностью. Обычно это поверхность с наибольшими габаритными размерами, т.е. пласть призматической заготовки. Боковая поверхность В заготовки, несущая две базирующие точки 4 и 5, соприкасается с направляющей установочной поверхностью и называется направляющей базирующей поверхностью.
В качестве нее выбирается поверхность, отличающаяся наибольшей протяженностью, обычно одна из кромок призматического тела. Торцовую поверхность С заготовки, несущую на себе одну опорную точку 6 и соприкасающуюся с упорной установочной поверхностью, называют упорной базирующей поверхностью.
|
Виды базирования. В зависимости от характера взаимодействия установочных поверхностей с базирующими поверхностями заготовки различают три способа базирования — неподвижное, подвижное и комбинированное (рис. 80).
Неподвижным называется базирование, при котором базирующие поверхности заготовки в процессе обработки не перемещаются относительно установочных поверхностей базирующих устройств машины. Однако заготовка, оставаясь неподвижной относительно базирующих устройств, движется вместе с ними относительно инструмента (или инструмент относительно заготовки), причем движение может быть поступательным или вращательным.
При позиционной обработке заготовка неподвижна и на нее надвигается инструмент. На рис. 80, а сверлильный суппорт 2 высверливает отверстие в заготовке 1. При проходной обработке деталь вместе с базирующими устройствами перемещается мимо инструмента. На рис. 80, б торцы заготовки 3, закрепленной в суппорте 7, опиливаются пилой 2.
Неподвижное базирование при вращении заготовки возможно в центрах или патроне. В лущильном станке (рис. 80, в) с чурака 3, зажатого центрами 1, надвигающимся ножом 2 срезается шпон.
Подвижным (скользящим) называется базирование, при котором базирующие поверхности заготовки в процессе обработки перемещаются (скользят) относительно установочных поверхностей базирующих устройств машины.
На рис. 80, д показан случай подвижного базирования при поступательном движении. Заготовка 2 главной базирующей поверхностью скользит по установочным поверхностям переднего 1 и заднего 4 столов фуговального станка, базируясь на них в процессе обработки ножами, установленными на валу 3. Случай подвижного базирования при вращательном движении иллюстрирует схема станка для шлифования круглых деталей (рис. 80, ё) и круглопалочного станка (рис. 80, ж).
Комбинированным называется базирование, при котором часть базирующих поверхностей заготовки в процессе обработки остается неподвижной, а часть перемещается относительно установочных поверхностей базирующих устройств машины (рис. 80, и, з).
Конструкции базирующих устройств. К системе базирующих устройств относятся: собственно базирующие элементы — установочные базы машины; зажимные и прижимные элементы и средства механизации базирования.
Элементы базирующих устройств могут быть специальными и универсальными. Часто элементы механизмов подачи (конвейеры, суппорты), а иногда и механизмы главного движения (центры, патроны) одновременно являются элементами базирования.
Собственно базирующие элементы машин отличаются большим разнообразием: столы, направляющие линейки, упоры, роликовые конвейеры, каретки, конвейеры, кулачки, патроны и т.д.
Во избежание отхода базирующих поверхностей заготовок от установочных поверхностей машины необходимо обеспечить их плотное и непрерывное соприкосновение силовым замыканием, которое достигается либо собственной массой, либо под действием рук рабочего, либо с помощью специальных приспособлений, прижимных или зажимных устройств.
Прижимными устройствами (прижимами) называют устройства силового замыкания со скользящим контактом с заготовкой, а зажимными (зажимами) — с неподвижным контактом. Зажимные и прижимные устройства по принципу действия можно разделить на четыре вида: винтовые, пневматические, эксцентриковые и пружинные. В современных станках применяют поршневые (пневматические), эксцентриковые и пружинные устройства.
Зажимы пневматические (рис. 81, а) могут быть поршневые и диафрагменные, одно- и двустороннего действия. Эти устройства являются быстродействующими, с легким ручным или автоматизированным управлением. Без учета потерь на трение усилие зажима на штоке для цилиндра двустороннего действия:
где F 3 — усилие на штоке, Н; Р —давление в воздушной сети, 0,5 МПа; D — диаметр поршня, см.
Усилие на штоке в одностороннем цилиндре меньше из-за действия силы сопротивления пружины q, Н:
Диафрагменные цилиндры отличаются компактностью, малой массой, отсутствием трущихся поверхностей, но имеют ограниченный ход штока (30...35 мм).
Усилие на штоке диафрагменного одностороннего цилиндра:
где F 3 — усилие на штоке, Н ; D — внутренний диаметр по контуру зажима диафрагмы, см; d — диаметр диска на диафрагме, см; Р — давление в сети, МПа.
Гидравлические зажимы аналогичны пневматическим, но работают при давлении в гидросети 5...6,5 МПа.
Эксцентриковые (рис. 81, б) и кулачковые зажимные устройства работают за счет радиального усилия, развивающегося при изменении расстояния от центра вращения эксцентрика или кулачка до рабочей поверхности. К эксцентриковым относят механизмы с профилем звена, очерченным по дуге окружности, к кулачковым — по математической кривой, когда не требуются большие силы зажима.
Величина зажимного усилия эксцентрикового устройства определяется по формуле
где Q — сила, приложенная к рукоятке, Н; l — плечо, мм; е — эксцентриситет, мм; D — диаметр эксцентрика, мм;/— коэффициент трения на поверхности эксцентрика.
Величина усилия на рычаге обычно принимается Q = 40... 80 Н.
Применяются торцевые кулачки (рис. 81, в), рабочий профиль которых сформирован по винтовой линии. Кулачок снабжается рукояткой. При повороте кулачка двуплечий рычаг зажимает заготовку. Сила зажима определяется, как в винтовых устройствах, с учетом передаточного отношения рычага:
где Q — сила, приложенная к рукоятке, Н; l — плечо, мм; r ср — средний радиус скольжения опорной точки плеча рычага, мм; α — угол подъема линии профиля кулачка; φ — угол трения; а, b — длины плеч рычага.
На станках с проходной обработкой заготовки прижимают к базирующим поверхностям роликовыми элементами (рис. 82, а). Ролик 1 в прижимном устройстве устанавливается на оси штока 4, который перемещается в осевом направлении цилиндра 2. Цилиндр закрепляется на подвижной балке 3, которая при наладке станка может перемещаться по колонне 7в вертикальном направлении. Усилие прижима создается за счет упругости пружины 5 колпачком 6.
В некоторых станках в качестве прижимных элементов используются плоские пружины (рис. 82, б). На форматных и шипорезных станках с проходной обработкой применяют прижимные устройства с гибкой лентой (клиновой ремень, рис. 82, в). Несущим элементом устройства является рама 2, на которой смонтированы опоры шкивов 1 и 6. Опора шкива 6 подвижная, что позволяет производить натяжение ленты 4 натяжным механизмом 5. Жесткость ленте придают ролики 7, закрепленные на осях подпружиненных кронштейнов. Рама 2 установлена на суппорте 3, что позволяет производить наладку прижимного устройства.
Загрузочно-разгрузочные устройства
Загрузочно-разгрузочные устройства разделяются на две группы: с накопителями и без них. Устройства с накопителями представляют собой механизмы с емкостью для размещения заготовок.
По способу размещения они подразделяются на бункерные, штабельные и магазинные. В бункерных устройствах — неориентированное рядами размещение заготовок, в штабельных — ориентированное размещение заготовок рядами в виде штабеля, в магазинных — ориентированное размещение заготовок в ряд.
Устройства без накопителей предназначены только для загрузки или укладки заготовок. Загрузочно-разгрузочные устройства могут быть встроены в станок, но могут быть независимыми (автономные) и навесными между двумя станками.
На рис. 83 приведены схемы штабельных питателей. Питатель с вертикальным лифтом (рис. 83, а) применяют при укладке материала 2 в штабель 3. Штабель установлен на платформе лифта 1. Над штабелем имеются цепные питатели 7 с упорами. При их перемещении по стрелке A верхний слой материала поступает к роликам 6 продольного конвейера 5, а прокладки — к роликам 4. На продольном конвейере материал перемещается по стрелке Б. Питатель с наклонным лифтом 2 (рис. 83, б) работает в наклонном положении, поэтому верхний слой материала 4 соскальзывает по стрелке А на поперечный приводной конвейер 5, а с него по стрелке Б на ролики 6 продольного конвейера 7. Постепенная разгрузка лифта осуществляется подъемом его платформы 9 с помощью гидроцилиндра 8. В вертикальное нерабочее положение лифт поворачивается с помощью гидроцилиндра 3. Когда лифт находится в этом положении и его платформа 9 опущена, загружается очередной штабель заготовок с помощью приводного напольного роликового конвейера 1.
Магазинные питатели получили в деревообработке наиболее широкое распространение. Питатели для продольной и поперечной выдачи брусков имеют одинаковый принцип действия.
Нижняя заготовка в магазине 1 (рис. 84, а) опирается на направляющие 2, расположенные немного выше звеньев конвейера 3. Заготовка выгружается из магазина только после захвата ее упорами звеньев конвейера. Регулирование положения магазина на высоту заготовки H производится перемещением щитка 4, при этом размер H 1 должен быть на 3... 5 мм больше H. Шаг А между упорами обеспечивает укладку заготовок шириной В на направляющие.
Для загрузки щитов в станки с вальцовой и гусеничной подачей применяются питатели, показанные на рис. 84, б. Для того чтобы уровень H разгрузки был постоянным, питатели оборудуются подъемным механизмом 2, приподнимающим пакет 1 после выгрузки каждой заготовки на ее толщину Н. Схема на рис. 84, в применяется для загрузки и выгрузки щитовых заготовок 2 сверху. Для захвата материала используются вакуум-присосы 1.
На рис. 84, г приведена схема вальцового навесного питателя для выдачи листовых материалов, пристраиваемого к станку, например к клеенамазывающим вальцам 2. Привод осуществляется от пневмоцилиндра 6. Верхний лист 3 шпона, уложенного на платформу 1 подъемного стола, сдвигают со стопы двумя пневматическими вальцами (колесами) 8, приводимыми во вращение зубчатореечным механизмом 7 пневмоцилиндра 6. Колеса фиксируются в нужном положении опорным роликом 4, а во время возврата в исходное положение они приподнимаются пневмоцилиндром 5.
|
|
Таксономические единицы (категории) растений: Каждая система классификации состоит из определённых соподчиненных друг другу...
Индивидуальные очистные сооружения: К классу индивидуальных очистных сооружений относят сооружения, пропускная способность которых...
Состав сооружений: решетки и песколовки: Решетки – это первое устройство в схеме очистных сооружений. Они представляют...
Адаптации растений и животных к жизни в горах: Большое значение для жизни организмов в горах имеют степень расчленения, крутизна и экспозиционные различия склонов...
© cyberpedia.su 2017-2024 - Не является автором материалов. Исключительное право сохранено за автором текста.
Если вы не хотите, чтобы данный материал был у нас на сайте, перейдите по ссылке: Нарушение авторских прав. Мы поможем в написании вашей работы!