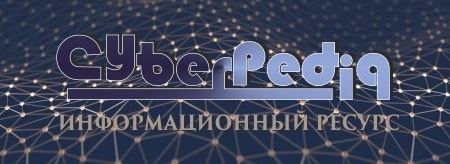
Историки об Елизавете Петровне: Елизавета попала между двумя встречными культурными течениями, воспитывалась среди новых европейских веяний и преданий...
Биохимия спиртового брожения: Основу технологии получения пива составляет спиртовое брожение, - при котором сахар превращается...
Топ:
Определение места расположения распределительного центра: Фирма реализует продукцию на рынках сбыта и имеет постоянных поставщиков в разных регионах. Увеличение объема продаж...
Устройство и оснащение процедурного кабинета: Решающая роль в обеспечении правильного лечения пациентов отводится процедурной медсестре...
История развития методов оптимизации: теорема Куна-Таккера, метод Лагранжа, роль выпуклости в оптимизации...
Интересное:
Отражение на счетах бухгалтерского учета процесса приобретения: Процесс заготовления представляет систему экономических событий, включающих приобретение организацией у поставщиков сырья...
Как мы говорим и как мы слушаем: общение можно сравнить с огромным зонтиком, под которым скрыто все...
Инженерная защита территорий, зданий и сооружений от опасных геологических процессов: Изучение оползневых явлений, оценка устойчивости склонов и проектирование противооползневых сооружений — актуальнейшие задачи, стоящие перед отечественными...
Дисциплины:
![]() |
![]() |
5.00
из
|
Заказать работу |
|
|
При изготовлении литых деталей в кокиль и литьем под давлением необходимо учитывать следующие особенности металлических форм. Формы практически неподатливы. Металл, заливаемый в металлическую форму, охлаждается быстрее, чем при литье в песчаные формы, вследствие чего повышается возможность появления внутренних напряжений в отливке. Поэтому нельзя допускать в отливках резких переходов от толстой стенки к тонкой и острых углов; радиусы галтелей должны быть в 1,5 раза больше, чем радиусы при литье в песчаные формы. Жидкий сплав, протекая по металлической форме, охлаждается интенсивно и теряет жидкотекучесть, поэтому при литье в кокиль минимальная толщина стенок должна быть больше. Необходимо также учитывать особенности литья в металлические формы при определении других конструктивных элементов (уклонов стенок по высоте, размеров отверстий и резьб, глубины резьб) для выполнения отверстий и резьб металлическими стержнями. Меньшие значения относятся к малогабаритным отливкам, большие — к крупногабаритным.
При конструировании деталей изготавливаемых из заготовок получаемых литьём необходимо учитывать способ литья, механические и эксплуатационные свойства. Отливка должна иметь форму близкую к форме готовой детали, высокую размерную точность, минимальный припуск на механическую обработку и требуемую чистоту поверхности. Все литейные сплавы можно разделить на пять групп˸ стали и чугуны; бронзы и латуни; сплавы алюминия; магниевые сплавы; сплавы на базе титана, хрома, цинка и др.
Литье в коки́ль
Процесс заключается в изготовлении отливок из жидкого расплава, свободной его заливкой в многократно используемые металлические формы – кокили, обеспечивающие высокую скорость затвердевания жидкого расплава и позволяющие получать в одной форме от нескольких десяток до нескольких тысяч отливок.
|
Когда полость кокиля заполняется металлом, то газы и воздух выходят через вентиляционную систему, которая образована вентиляционными выпорами, каналами и пробками.
Литьём в кокиль изготовляются основные алюминиевые детали ДВС — поршни, блоки цилиндров, головки и т. д.
Преимущества:
• процесс мало операционный,
• операции кратковременны и просты,
• весь процесс может выполняться автоматической установкой,
• кокиль, что важно, можно использовать многократно,
• повышается производительность,
• хорошее качество отливки,
• уменьшение вредных для здоровья операций.
Недостатки
- Сложность изготовления кокилей, их ограниченный срок службы (особенно при литье черных сплавов).
- Неподатливость кокиля и металлических стержней.
- Затруднен вывод газов из полости формы.
- Высокая стоимость кокиля, сложность и трудоемкость его изготовления
- Ограниченная стойкость кокиля, измеряемая числом годных отливок, которые можно получить в данном кокиле. От стойкости кокиля зависит экономическая эффективность процесса.
- Сложность получения отливок с поднутрениями, для выполнения которых необходимо усложнять конструкцию формы - делать дополнительные разъемы, использовать вставки, разъемные металлические или песчаные стержни.
Литье под давлением
Литьё в пресс-формы происходит под давлением от 35 до 700 МПа, обеспечивающим удаление воздушной пористости.
Высокие скорости впуска обеспечивают хорошее качество поверхностей отливки.
Метода литья под давлением получают детали для которых не требуются вообще или нет в технологии изготовления дальнейшей механической обработки.
Расплавленный металл заливается в камеру прессования, а затем под действием прессующего поршня, перемещающегося в этой камере, через литниковые каналы заполняет с высокой скоростью полость формы.
|
Преимущества:
- Высокое качество отливки
- Высокая производительность, т.к. металл напрямую идет в пресс форму
Недостатки
• Необходимо соблюдать режимы давления при литье
• Специфические требования технологичности конструкций литых деталей
• Высокая стоимость пресс-форм
• Литье под давлением позволяет получать сложные по геометрии тонкостенные отливки, близкие по размерам к конечной продукции. Этот способ литья очень производителен при автоматизации процесса. Наиболее широко применяется литье под давлением для изготовления отливок из магниевых, цинковых и алюминиевых.
Задание 2
1. Изобразите эскизы пяти профилей сортового проката. Перечислите прокатные операции технологического процесса получения сортового проката, начиная с указания исходного материала.
Рисунок 1- Сортовой прокат
Прокат можно разбить на следующие основные четыре группы: сортовой, листовой, трубы, специальные виды проката (бандажи, колеса, периодические профили и пр.). Наиболее разнообразной является группа сортового проката, который подразделяется на простые и фасонные профили.
Прокат в виде круга, квадрата, полос плоского сечения относится к простым профилям. Прокат сложного поперечного сечения относится к фасонным профилям. В зависимости от назначения фасонные профили подразделяются на профили общего или массового потребления (угловой профиль, швеллеры, двутавровые балки, шестигранные профили и др.) и профили специального назначения (рельсы железнодорожные широкой и узкой колеи, рельсы трамвайные, профили сельскохозяйственного машиностроения, электропромышленности, нефтяной промышленности и др.).
Весь сортовой прокат подразделяется на четыре группы: сталь крупносортная, сред несортная, мелкосортная и катанка диаметром от 5,5 до 9мм.
Процесс прокаткиПрокатка металла осуществляется при прохождении его между валками, вращающимися в разных направлениях. При прокатке металл обжимается, в результате чего толщина полосы уменьшается, а её длина и ширина увеличиваются.Опишите технологический процесс изготовления поковки способом ковки на паровоздушном ковочном молоте. При выполнении работы следует: 1) описать сущность процесса ковки и указать область ее применения; 2) изобразить схему пресса и описать его работу; 3) описать механизацию процесса ковки.
|
Сущность процесса ковки.
Ковкой называют процесс горячей обработки металлов давлением, при котором путем многократного действияуниверсального подкладного инструмента или бойков металл заготовки пластически деформируется, постепенно приобретая заданные форму, размеры и свойства.
В процессе ковки предварительно нагретая заготовка укладывается на нижний боек молота или пресса, а верхним бойком наносятся удары либо по самой заготовке, либо по подкладному инструменту. При этом металл свободно течет в стороны, не ограниченные рабочими поверхностями инструмента,
Область применения.
Ковкой получают фасонные заготовки для последующей механической обработки. Эти заготовки называют коваными поковками или просто поковками.
Процесс ковки является малопроизводительным, так как требует многократных перемещений заготовки между бойками. При ковке небольших по массе поковок эти перемещения осуществляются вручную, а тяжелые заготовки перемещаются различными средствами механизации. Поковки, полученные ковкой, имеют большие припуски на механическую обработку.
На предприятиях тяжелого машиностроения ковка является одним из основных заготовительных процессов. Ковка экономически выгодна в единичном и мелкосерийном производствах для получения поковок любой массы. Для крупных деталей машин массой от 2 т. до 250 т. ковка является единственно возможным способом изготовления. Примерами тяжелых поковок могут служить валы гидрогенераторов, турбинных дисков, коленчатых валов судовых двигателей, валков прокатных станов, роторы мощных гидротурбин, валы корабельных двигателей и т. п.
|
Поковки меньшей массы от 0,5 кг до десятков и сотен килограммов, можно изготовлять и ковкой, и штамповкой. Хотя штамповка имеет ряд преимуществ перед ковкой, однако в единичном и мелкосерийном производстве ковка обычно экономически более целесообразна. Объясняется это тем, что при ковке используют универсальный (годный для изготовления различных поковок) инструмент, а изготовление специального инструмента (штампа) при небольшой партии одинаковых поковок экономически невыгодно.
Ковочные молоты. Молоты создают динамическое (ударное) воздействие инструмента (верхнего бойка) на заготовку. Продолжительность деформации при ковке на молотах 10-3с, а скорость деформирования — 6...6,5 м/с. Наибольшее применение получили паровоздушные и приводные молоты.
В паровоздушном молоте (рис. 4) подъем и опускание бабы 10 с закрепленным на ней верхним бойком И по направляющим 7 производится при подаче пара или сжатого воздуха давлением 0,7...0,9 МПа в рабочий цилиндр 5. Подача пара регулируется с помощью золотникового устройства 4. При перемещении золотника 3 с помощью рычага 1 и тяги 2 вверх или вниз пар поступает в верхнюю или нижнюю полость цилиндра 5 и перемещает поршень 6, соединенный штоком 8 с бабой 10. При падении бабы давление пара на верхнюю часть поршня создает дополнительное усилие. Нижний боек 12 неподвижно закреплен на массивной стальной фундаментной плите — шаботе 13, лежащей на дубовой подушке на отдельном фундаменте. Чем больше масса шабота, тем большая часть кинетической энергии падающих частей превращается в энергию деформации заготовки. Обычно она в 15 раз больше массы падающих частей.
Установка станины 9 и шабота 13 на отдельных фундаментах обеспечивает свободный доступ к бойкам, оберегает конструкцию молота от сотрясений, но не гарантирует параллельности бойков. Паровоздушные молоты строят с массой падающих частей 1...8 т.
Из приводных молотов наибольшее применение получили пневматические. В них подъем и опускание поршня, шток которого одновременно является бабой молота и к которому крепится верхний боек, совершается с помощью сжатого воздуха давлением 0,2... 0,3 МПа. Сжатый воздух поступает в рабочий цилиндр от поршневого компрессора, приводимого в движение кривошипно-шатунным механизмом от отдельного электродвигателя. Рабочий и компрессионный цилиндры расположены на одной станине. Пневматические молоты имеют массу падающих частей 50...1000 кг и применяются для ковки мелких поковок (до 20 кг).
Рис. 4. Паровоздушный ковочный молот.
Механизация и автоматизация ковки
Механизация и автоматизация малопроизводительного процесса свободной ковки имеет большое значение.
|
При ковке широко применяют механизмы и устройства, снижающие трудоемкость вспомогательных операций: мостовые краны, ковочные поворотные краны, лебедки, подвесные клещи, электротележки с поворотными столами, электрические кантователи, посадочные машины, манипуляторы и др..
Посадочные машины относят к специальным манипуляторам, управляемым оператором. Применяют их в комплексах «нагревательная печь – ковочная машина» для загрузки и разгрузки заготовок, а также для транспортирования и установки их в рабочую зону оборудования.
Несмотря на нестабильность процессов ковки, в производстве используют и промышленные роботы. Более того, в производстве создаются роботизированные технологические комплексы (РТК) для ковки. РТК называется совокупность единицы технологического оборудования, промышленного робота (ПР) и средств оснащения, автономно функционирующая и осуществляющая многократные циклы. В РТК промышленный робот может быть использован в качестве технологического оборудования. При ковке в состав РТК может входить быстроходный гидравлический пресс (усилие до 50МН) и ПР (типа МКП-25), оснащенный автоматизированной системой числового программного управления (ЧПУ), которая обеспечивает чередование во времени автоматического режима управления с ручным. Система ЧПУ – четырех координатная, она управляет подъемом руки, перемещением руки параллельно рельсам, ротацией клещей и движением бойка пресса.
Задание 3
|
|
Биохимия спиртового брожения: Основу технологии получения пива составляет спиртовое брожение, - при котором сахар превращается...
Двойное оплодотворение у цветковых растений: Оплодотворение - это процесс слияния мужской и женской половых клеток с образованием зиготы...
История развития хранилищ для нефти: Первые склады нефти появились в XVII веке. Они представляли собой землянные ямы-амбара глубиной 4…5 м...
Состав сооружений: решетки и песколовки: Решетки – это первое устройство в схеме очистных сооружений. Они представляют...
© cyberpedia.su 2017-2024 - Не является автором материалов. Исключительное право сохранено за автором текста.
Если вы не хотите, чтобы данный материал был у нас на сайте, перейдите по ссылке: Нарушение авторских прав. Мы поможем в написании вашей работы!