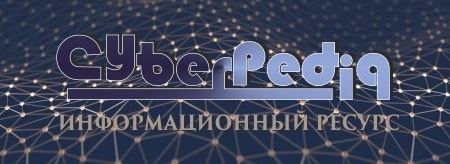
Особенности сооружения опор в сложных условиях: Сооружение ВЛ в районах с суровыми климатическими и тяжелыми геологическими условиями...
Кормораздатчик мобильный электрифицированный: схема и процесс работы устройства...
Топ:
Генеалогическое древо Султанов Османской империи: Османские правители, вначале, будучи еще бейлербеями Анатолии, женились на дочерях византийских императоров...
Устройство и оснащение процедурного кабинета: Решающая роль в обеспечении правильного лечения пациентов отводится процедурной медсестре...
История развития методов оптимизации: теорема Куна-Таккера, метод Лагранжа, роль выпуклости в оптимизации...
Интересное:
Наиболее распространенные виды рака: Раковая опухоль — это самостоятельное новообразование, которое может возникнуть и от повышенного давления...
Лечение прогрессирующих форм рака: Одним из наиболее важных достижений экспериментальной химиотерапии опухолей, начатой в 60-х и реализованной в 70-х годах, является...
Искусственное повышение поверхности территории: Варианты искусственного повышения поверхности территории необходимо выбирать на основе анализа следующих характеристик защищаемой территории...
Дисциплины:
![]() |
![]() |
5.00
из
|
Заказать работу |
|
|
Потребность человека в белке может быть лишь частично удовлетворена с помощью растительных продуктов (зерновых, бобовых). Животные белки по аминокислотному составу в большей мере отвечают потребностям организма в незаменимых аминокислотах. Наиболее дефиицитной аминокислотой в растениях является лизин. В белках животного происхождения - дефиицит по метионину, триптофану, лизину, изолейцину, тирозину. Коэффициент использования животными белковых веществ кормов от 8 до 34 %. Повысить усвояемость продуктов питания человеком и кормов животными можно введением недостающих незаменимых аминокислот и полноценных белков.
Микроорганизмы способны накапливать огромные (до 60-70 % сухой массы) количество белка. Получаемая биомасса непосредственно используется в качестве прекрасного обогатителя кормов или служит сырьем для получения очищенных белковых препаратов.
Технология белковых веществ мало зависит от типа используемого сырья. Технологическая блок–схема получения кормовой биомассы состоит из нескольких отделений.
Производство требует наличия нормативного и аварийного запаса исходных и вспомогательных веществ. Отделение получения засевной культуры (или отделение чистой культуры), служит для выделения чистой культуры посевного материала, используемого для засева, подсева и пересева промышленных ферментеров основной ферментации.
Приготовление посевного материала проводится периодически, осуществляется в несколько стадий и начинается в микробиологической лаборатории. Хранящиеся там штаммы–продуценты из пробирок переносят в конические качалочные колбы со стерильной питательной средой, состав которой соответствует составу среды, используемой в производстве. Чистую культуру переносят в посевной аппарат объемом 50 л. с подготовленной питательной средой (рН 5,5 – 5,8, доводится аммиачной водой или известковым молоком). Одновременно в смеситель подается жидкий источник углерода (субстрат). Среду обогащают автолизатом дрожжей, перемешивают 20-30 минут, стерилизуют в греющей колонне острым паром 10–15 минут, охлаждают в теплообменнике, подают в отстойник. Питательная среда отбирается из основного производства, а не готовится заново.
|
Первоначально в малый посевной аппарат подают около 40 л питательной среды, разбавляют ее в 4–4,5 раза стерильной водой. При интенсивной аэрации добавляют остальное количество питательной среды (80 – 100 л.), поддерживая рН 4,5–5,5 подачей аммиачной воды. Затем из качалочных колб вносят микробную суспензию объемом 1,5–2 л. и проводят процесс культивирования до накопления в среде 3,5–4,0 г клеток/литр по абсолютно сухому веществу (АСВ). Продолжительность процесса не превышает 15–18 часов.
В большом посевном аппарате (4–5 м3) культивирование проводится 10–12 часов. Затем выращивание засевной культуры в ферментере (15–20 м3) продолжается 18–9 часов при интенсивной аэрации. Аппарат заполняется на 10% стерильной водой, добавляется 0,5 м3 питательной среды и перекачивается все содержимое посевного аппарата в ферментер. Затем засевную культуру отбирают на основное производство. Процесс ферментации длится от 5 до 10 суток, а затем цикл приготовления посевного материала возобновляется по мере надобности.
К подготовительным стадиям производства относится приготовление растворов питательных солей и микроэлементов, готовят два раствора, которые параллельно подаются в основной ферментер:1) раствор всех микроэлементов (N,P,K), необходимое количество которых составляет 5–70 г/л; 2) раствор микроэлементов (Mg, Mn, Fe, Zn), концентрация которых не превышает 10 мг/л.
Отделение компримирования воздуха существует только на тех заводах, где установлены ферменты, требующие для работы больших потоков воздуха под избыточным (около 0,3–0,5 Мпа) давлением, и используют центробежные компрессоры большой производительности.
|
Технологические потоки из всех подготовительных отделений поступают на главную стадию производства – стадию ферментации.
В промышленности применяют несколько типов ферментеров, с учетом используемого сырья (жидкое, газообразное, водорастворимое), количества получаемой биомассы и разных технологических схем:
1) батарея параллельно работающих ферментеров. Обеспечивает большую производительность завода. Используется моносубстрат;
2) батарея последовательно работающих ферментеров. Используется сложный субстрат, все компоненты его потребляются штаммом–продуцентом наиболее полно;
3) батарея последовательно работающих ферметеров с дополнительной промежуточной подачей питательной среды (с подпиткой). Высокая концентрация субстрата ингибирует или угнетает рост и развитие микробной популяции, а малая концентрация не позволяет достигнуть экономически оправданной концентрации биомассы в отходящей на стадию сгущения суспензии;
4) батарея последовательно работающих ферментеров с рециркуляцией части суспензии микроорганизмов, используется в случае применения сложного трудноутилизируемого субстрата, когда микроорганизмам требуется длительное время адаптации к одному или нескольким компонентам сырья. Введение уже адаптированных к сырью клеток сокращает время пребывания микроорганизмов в ферментере, увеличивает скорость протока и повышает степень утилизации субстрата;
5) батарея последовательно соединенных ферментеров с подпиткой и рециркуляцией суспензии микроорганизмов. Наиболее полная утилизация многокомпонентного трудноусвояемого субстрата, ингибирующего в высоких концентрациях микробные клетки.
Концентрация микробной суспензии после стадии ферментации - 10–25 кг/ м3 (1–2,5% АСВ), которая поступает в отделение сгущения суспензии микроорганизмов. Основной задачей стадии сгущения или выделения является повышение концентрации биомассы до 12–16% АСВ за счет механического отделения большей части межклеточной влаги за минимальное время. На практике в процессе производства широко используется разделение белковых веществ на центробежных сепараторах или сочетание сепарации с такими малоэнергоемкими методами, как флокуляция, коагуляция, флотация или декантация:
|
Сконцентрированная до 15 – 17% АСВ микробная суспензия должна пройти стадию термообработки, в процессе которой при температуре 75 – 85 0С в течение 10 – 40 мин. погибает штамм – продуцент и практически вся сопутствующая микрофлора.
Дальнейшее концентрирование суспензии в отделении выпаривания до концентрации 23–25% АСВ проводят в 3–корпусной вакуум–выпарной установке, в которой инактивированная биомасса последовательно проходит 3 корпуса вакуум–выпарной установки с выносными греющими камерами, где температура кипения постепенно снижается (1 корпусной – 90 0С, II – 75, III – 60 0С).
Суспензия с концентрацией 22 – 25% АСВ поступает в отделение сушки, где и происходит образование готового продукта с влажностью ~ 10% (по массе).
По технологической схеме сушилки суспензия микроорганизмов непрерывно подается на центробежный распыливающий механизм, разбрызгивается в сушильную камеру. Воздух нагревается в топке до 350 – 450 0С, подается по воздуховоду. При соприкосновении воздуха с каплями суспензии большая часть влаги переходит в пар, что препятствует перегреву твердой частицы. Порошок или гранулы сухой биомассы с температурой около 90 0С опускаются в конусную часть сушилки и по пневмотранспортной линии подаются в циклон–сепаратор, где отделяются от воздуха. Воздух из сушильной камеры проходит через батарею циклонов, где освобождается от белковой пыли и затем направляется на стадию окончательной очистки газовоздушных выбросов.
Сухая биомасса, содержащая 8 – 10% (по массе) влаги представляет собой готовый продукт, и после упаковки направляется на склад к потребителю. Если готовый продукт получают в виде гранул, то в технологический процесс включают отделение грануляции. Гранулы подсушивают в сушилке кипящего слоя до остаточной влажности 8 – 10% горячим воздухом (или топочными газами) с температурой 260 – 300 0С, подаваемым из топки.
Стадия фасовки и упаковки. Готовый продукт в виде гранул или порошка фасуется в бумажные мешки 25 – 30 кг.
|
Контрольные вопросы
1. Технологическая схема получения кормовой биомассы.
2. Опишите назначение и особенности работы различных отделений промышленного предприятия по производству кормовых дрожжей.
3. Технологические параметры производства кормовых дрожжей.
4. Сходство и отличие в технологических схемах по производству кормовых дрожжей и липидов.
Литература
1. Биотехнология: Учебное пособие для вузов в 8 книгах. Под ред. Егорова Н. С., Самуилова В. М. – М: Высшая школа, 1987. С. 1 – 1194.
2. Грачева И. М., Иванова Л. А., Кантере В. М. Технология микробных белковых препаратов, аминокислот и биоэнергия. М., Колос, 1992. С. 1 – 383
3. Основы сельскохозяйственной биотехнологии М., Колос, 1999 г. С. 1 – 380.
Лекция 12. Биотехнология производства источников энергии и биогумуса
Вопросы. 1. Технология получения биогаза из отходов сельскохозяйственного производства. 2. Получение источников энергии из растительного сырья и фотопроизводство водорода. 3. Получение биогумуса.
Получение биогаза. Основу природного газа составляют метан. Процесс образования метана на поверхности Земли – биологический и осуществляется микроорганизмами в анаэробных условиях. Процессы деструкции органических веществ до метана широко распространены в осадочных отложениях в настоящие время. Болотный газ представляет собой смесь из 65% метана, 30% углекислого газа, 1% сероводорода, незначительных количеств азота, кислорода, водорода. Промышленные месторождения природного газа – продукт биологических процессов в прошлые эпохи. Исследование вопросов происхождения природного газа позволило сделать вывод о возможности получения биогаза из биомассы. Биогаз – продукт разложения различных органических веществ фотосинтетического происхождения. Он примерно состоит из 70% метана, 30% углекислого газа, примесей Н2S, N2, О2. Биогаз (биометан) может содержать 50-80% метана и 20-50% диоксида углерода. Он плохо растворим в воде, его теплотворная способность составляет 5–8 тыс. ккал/м3 Он в 1,5–3 раза дешевле электроэнергии. Из одной тонны органического вещества (в сухом весе) образуется 250 – 600 м3 биогаза. В качестве сырья для производства биогаза наиболее перспективно использование органических веществ сточных вод, городского и сельскохозяйственного производства, в частности навоза в сельских районах.
Из 1 т сухого вещества биомассы посредством биоконверсии получают 350-500 м3 биогаза, теплотворная способность которого 5-8 тыс. ккал/м3. Сырьем для биотехнологического производства метана служит биомасса, утилизация которой необходима с санитарно-гигиенической точки зрения для охраны окружающей среды: коэффициент трансформации энергии биомассы в энергию биометана достигает 80%.
|
Наиболее рентабельным является производство из биогаза электроэнергии (общий КПД с учетом образующегося при производстве энергии тепла достигает 80-85 %, а непосредственно в электричество превращается 33% химической энергии биометана). При 200-250 атм. биометан пригоден в качестве топлива для двигателей внутреннего сгорания (октановое число этого горючего 110-115, а нижний предел вспышки - 6450С). В связи с тем, что около 90% углерода биомассы трансформируется в углерод биогаза, метановое брожение является наиболее эффективным способом очистки сточных вод.
Основой биотехнологии утилизации биомассы с получением биогаза является метановое брожение биомассы с участием метангенерирующих бактерий (метаногенов), число выделенных видов которых в настоящее время превышает 20. Метаногены - наиболее древние бактерии.
При проектировании биогазовой установки исходят из того, что от одной коровы массой 500 кг в сутки получают с навозом 4,8 кг сухого органического вещества, из которого при 30-суточной переработке в реакторе образуется 1,0-2,4 м3 биогаза. Эквивалентное количество биогаза получают из навоза, производимого в течение суток девятью свиньями на откорме (живая масса одного животного - 60 кг) или пятью свиноматками.
При использовании коровьего навоза в биогаз превращается одна четвертая часть органического материала. Жидкофазный биометаногенез осуществляется в анаэробных условиях в три этапа: I). Растворение и гидролиз органических соединений; II) ацидогенез; III) метаногенез. В процессе биометаногенеза участвуют три группы бактерий. Первые превращают сложные органические субстраты в масляную пропионовую, бензойную и молочную кислоты; вторые микроорганизмы превращают эти органические кислоты в уксусную кислоту, водород и углекислый газ; метанобразующие бактерии восстанавливают углекислый газ в метан с поглощением водорода. Уксуснокислые и метанообразующие микроорганизмы образуют симбиоз, который ранее считался одним продуцентом и назывался Methanobacillus omelianskii.
|
|
Индивидуальные очистные сооружения: К классу индивидуальных очистных сооружений относят сооружения, пропускная способность которых...
Особенности сооружения опор в сложных условиях: Сооружение ВЛ в районах с суровыми климатическими и тяжелыми геологическими условиями...
История развития хранилищ для нефти: Первые склады нефти появились в XVII веке. Они представляли собой землянные ямы-амбара глубиной 4…5 м...
Общие условия выбора системы дренажа: Система дренажа выбирается в зависимости от характера защищаемого...
© cyberpedia.su 2017-2024 - Не является автором материалов. Исключительное право сохранено за автором текста.
Если вы не хотите, чтобы данный материал был у нас на сайте, перейдите по ссылке: Нарушение авторских прав. Мы поможем в написании вашей работы!