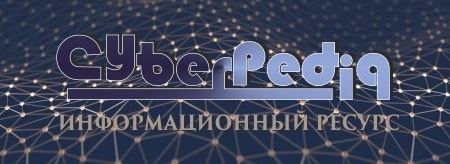
Папиллярные узоры пальцев рук - маркер спортивных способностей: дерматоглифические признаки формируются на 3-5 месяце беременности, не изменяются в течение жизни...
Индивидуальные и групповые автопоилки: для животных. Схемы и конструкции...
Топ:
Методика измерений сопротивления растеканию тока анодного заземления: Анодный заземлитель (анод) – проводник, погруженный в электролитическую среду (грунт, раствор электролита) и подключенный к положительному...
Комплексной системы оценки состояния охраны труда на производственном объекте (КСОТ-П): Цели и задачи Комплексной системы оценки состояния охраны труда и определению факторов рисков по охране труда...
Определение места расположения распределительного центра: Фирма реализует продукцию на рынках сбыта и имеет постоянных поставщиков в разных регионах. Увеличение объема продаж...
Интересное:
Лечение прогрессирующих форм рака: Одним из наиболее важных достижений экспериментальной химиотерапии опухолей, начатой в 60-х и реализованной в 70-х годах, является...
Подходы к решению темы фильма: Существует три основных типа исторического фильма, имеющих между собой много общего...
Берегоукрепление оползневых склонов: На прибрежных склонах основной причиной развития оползневых процессов является подмыв водами рек естественных склонов...
Дисциплины:
![]() |
![]() |
5.00
из
|
Заказать работу |
|
|
Лабораторная работа №4
Тема: ОПРЕДЕЛЕНИЕ КАЧЕСТВА КОТЛОВОЙ И ОХЛАЖДАЮЩЕЙ ВОДЫ МЕТОДИКАМИ DREW MARINE, VECOM MARINE И ЛАБОРАТОРИЕЙ SPECTRAPAK 309
Цель: Определение качества котловой воды с помощью методик Drew Marine, Vecom Marine, рекомендации по водному режиму. Определение качества охлаждающей воды ДВС с помощью судовой лаборатории Spectrapak 309 фирмы UNITOR.
Теоретический материал
В котле происходит преобразование химической энергии топлива в тепловую энергию пара, используемую для совершения работы. Общим для всех котлов является то, что к воде подводится тепло для получения пара, который затем используется для совершения работы на судне.
Дизели зависят от отсутствия накипи на теплопередающих поверхностях, предназначенных для охлаждения.
Их объединяет необходимость решения проблем накипеобразования и коррозии, несмотря на то, что некоторые формы коррозии более характерны для котлов высокого давления, в то время как другие чаще встречаются в дизелях.
Для эффективной эксплуатации оборудования для получения пара и систем охлаждения необходима постоянная обработка воды в связи с тем, что получение воды в испарителе, механическая деаэрация не позволяют удалить из воды все вредные примеси.
Основными целями управляемой программы обработки воды в любой энергетической установке являются:
· Поддержание теплопередающих поверхностей со стороны воды в парообразующих и охлаждающих системах в чистоте и без накипи;
· Предотвращение потери металла из-за коррозии;
· Обеспечение производства пара в котлах без вскипания, пенообразования и уноса примесей;
· Предотвращение образования отложений в системе пар-конденсат;
· Уменьшение потерь тепла при излишнем продувании котлов;
|
· Поддержание всего парообразующего и вспомогательного оборудования и связанных с ним паровых водяных систем на уровне их максимальной эффективности и, таким образом, уменьшение затрат.
Коррозия металлов
В судовых силовых установках в качестве материалов используются как сплавы на основе железа, так и не содержащие железо. Все эти металлы при контакте с водой медленно корродируют, если вода не подвергается надлежащей обработке. Высокая температура и давление увеличивают скорость коррозии. Целью любой комплексной программы обработки воды является защита от коррозии всего оборудования, как во время работы, так и выведенного из эксплуатации.
Коррозия представляет собой результат химического или электрохимического воздействия воды или воздуха на металл. На скорость коррозии оказывают влияние примеси различных веществ, содержащиеся в металле и воде. Обработанные должным образом чистые вода и металл уменьшают скорость коррозии. Если вода не обработана должным образом, в ней коррозируют все металлы. В котельных установках причиной коррозии чаще всего являются растворенные газы, неправильный уровень pH, ионы хлора, и механические причины. Ниже рассмотрены основные химические реакции коррозии.
Газовая коррозия
В программах водообработки в первую очередь принимаются во внимание три газа: кислород, двуокись углерода и аммиак.
Кислород является одним из наиболее нежелательных газов, которые поступают в систему (до котла, непосредственно в котел и после котла). Кислород растворяется в воде и вызывает коррозию, протекающую с высокой скоростью. Скорость кислородной коррозии зависит от концентрации растворенного кислорода, величины pH, и температуры воды.
Кислород вступает в реакцию с железом на поверхности металла с образованием окисла железа красного цвета (Fe3O4). В связи с тем, что этот окисле (ржавчина) является рыхлым и не защищает поверхность металла, процесс коррозии продолжается. Если не будут приняты защитные меры, то в конечном итоге вся металлическая конструкция будет преобразована в окисел.
|
Часто коррозия носит локальный характер, выражающийся в питтинге. До тех пор, пока поверхность металла не будет тщательно очищена химическим или механическим способом, реакция коррозии будет протекать под слоем рыхлого окисла и может носить проникающий характер.
Двуокись углерода: большая часть двуокиси углерода в водяных системах судовых энергетических установках образуется в испарителях. При нагревании морской воды, растворенные в ней карбонаты (CO3) и бикарбонаты (HCO3), разлагаются с образованием двуокиси углерода (CO2).
Углекислый газ вместе с паром выходит из испарительной части и растворяется в дистиллате. Углекислый газ вступает в реакцию с водой с образованием угольной кислоты, которая уменьшает pH воды, ускоряет процессы общей коррозии в питательной воде и в конечном итоге во всей системе пар-конденсат.
Угольная кислота (H2CO3) – это слабая кислота, которая вступает во взаимодействие со сталью в питательной и конденсатной системах с образованием бикарбоната железа (Fe(HCO3)2). Бикарбонат железа представляет собой хорошо растворимое вещество, не обладающее защитным или пассивирующими свойствами.
Угольная кислота вызывает общую коррозию, для которой характерны образование продольных канавок в нижней части труб, общее утонение труб и, в частности потери металла в напряженных частях, таких как изгибы труб и участках, имеющих резьбу.
Аммиак: в присутствии кислорода аммиак вступает во взаимодействие с металлами на основе меди. К коррозии приводит только совместное действие этих газов. Коррозионная активность аммиака может быть минимиризирована исключением содержания кислорода в воде.
Аммиак образуется в результате декомпозиции органических веществ, а также в результате разложения избыточного гидразина.
Основные позиции, которые необходимо контролировать при работе установки, чтобы уменьшить поступление в систему вызывающих коррозию газов:
· Проверьте все точки возможного поступления воздуха в части установки, предназначенные для конденсации и находящиеся под вакуумом (т.е. поврежденные фланцы, прокладки, сальниковые уплотнения клапанов, открытые дренажные клапаны на линиях возврата конденсата, недостаточное давление пара в системе укупорки, неудовлетворительная работа конденсатоотводчиков и т.д.);
|
· Проверьте температуру воды в танках, работающих при атмосферном давлении. В связи с тем, что O2, CO2 в газообразном виде хорошо растворяются в холодной воде, воду в танках под атмосферным давлении следует подогреть до максимально высокой температуры, возможной без опасности образования паровых пробок во всасывающих линиях насосов;
· Избегайте подвода дренажей с высокой концентрацией кислорода в танки или любые другие точки, откуда они могут быть использованы в качестве добавочной воды;
· Проверьте работу деаэрирующего подогревателя. Один термометр должен быть установлен в паровом пространстве, а другой – в водяном пространстве деаэратора. При правильной работе установки значения температур в водяном и паровом пространствах должны отличаться не более, чем на один или два градуса С. Если это условие не выполняется, производите проверку термометров и при необходимости их замените. Если и после проверки разность температур сохранится, установка при первой возможности должна быть вскрыта и осмотрена для установления причины.
· Обеспечьте удаление газов из деаэрирующего подогревателя в атмосферу.
· Проверьте, что распыливающие сопла в деаэраторе не забиты, не изношены и не сломаны, что пружины исправны. Плохой распыл приводит к плохой деаэрации независимо от температуры.
· При вводе в систему добавочной воды: а) вводите добавочную воду как можно медленнее. При слишком быстром вводе добавочной воды деаэратор может быть перегружен, что приведет к невозможности минимизации концентрации O2, CO2. б) более высокая температура в танке добавочной питательной воды уменьшает содержание O2, CO2.
· Для максимальной защиты от остаточного содержания O2, CO2 используйте средства химической обработки воды. В то время, как механическая деаэрация питательной воды является основным средством уменьшения концентрации растворенных кислорода и других газов, вызывающих коррозию, таких как аммиак и двуокись углерода, необходима химическая обработка воды.
|
Кислотная коррозия
Кислотная коррозия трубок и барабанов котлов обычно проявляется в форме общего утонения всей поверхности металла. Кислотная коррозия имеет место в случае, когда в питательную воду попадает вода, содержащая соли, унесенные в испарителе, или протечки морской воды в конденсаторе. При поступлении в систему котловой воды содержащегося в морской воде хлористого магния (MgCl2), происходит диссоциация его с образованием ионов магния и хлора. Ионы хлора взаимодействуют с ионами водорода, что приводит к уменьшению уровня pH котловой воды и кислотной коррозии поверхности металла.
Ионы магния взаимодействуют с фосфатами и ионами гидроксила, если они имеются в воде, с образованием шлама. Ионы магния вступают в реакцию только с ионами фосфатов с образованием фосфата магния – мягкого липкого осадка, который имеет тенденцию удерживать все другие осадки на поверхности труб.
Все отложения на поверхности труб ухудшают передачу тепла и способствуют возникновению условий их разрушения. В воде, удерживаемой на напряженной теплопередающей поверхности под этими отложениями, будет увеличиваться концентрация кислоты или щелочи. В этом случае скорости коррозии становятся очень большими и в течение очень короткого времени происходят серьезные местные повреждения.
Водородное охрупчивание
Этот тип коррозии заключается в охрупчивании или растрескивании металла труб, нарушении структуры металла.
Ионы водорода образуются в результате повышения концентрации кислот под слоем твердого осадка. Ионы водорода – самые маленькие из всех элементов и могут проникать через границы зерен металла труб. Они вступают в реакцию с атомами углерода, имеющимися в стали, с образованием метана.
Метан имеет большие молекулы газа, которые вызывают образование давления внутри металла. Высокое давление, наряду с ослаблением связей, вызванным вымыванием графита, побуждают зерна стали к отделению. Таким образом, в металле образуются трещины.
Водородное охрупчивание развивается очень быстро. Металл труб разрушается, когда поврежденная часть не может более противостоять внутреннему давлению.
Щелочная коррозия
Щелочная коррозия характеризуется неоднородным характером разрушения металла. Ее часто называют «щелочное растрескивание».
Щелочная коррозия является следствием избыточного содержания свободных ионов гидроксила в котловой воде, на что указывает очень высокое значение pH.
Подобно кислотной, щелочная коррозия может возникать под слоем отложений, образующихся на теплопередающих поверхностях, способствующих повышению концентрации ионов гидроксила и вызывающих развитие местной коррозии.
|
Щелочная коррозия имеет место в горизонтальных или наклонных трубах, когда из-за сильного кипения или сепарации пара и воды их внутренняя поверхность оказывается покрытой паром. Котловая вода, содержащая ионы гидроксила, может в виде брызг попадать на покрытые паром поверхности нагрева, на которых после упаривания воды увеличивается концентрация ионов гидроксила.
Каустическое растрескивание
Эта форма коррозии является разновидностью межкристаллитного растрескивания. При вступлении воды, имеющей высокую концентрацию каустической щелочи, в контакт со сталью, испытывающей механические напряжения, возникает межкристаллитная коррозия. (Металлы могут быть подвергнуты релаксации остаточных напряжений). Коррозия этого типа имеет место на границах кристаллов металла или сплава.
Коррозионное растрескивание
Коррозионное растрескивание проявляется в виде ряда тонких трещин на стенках труб. Наличие этих трещин усугубляется условиями, способствующими развитию коррозии других видов, что, в конце концов, приводит к разрушению трубы.
Этот вид коррозии обычно характерен для стенок труб котлов высокого давления. Она обычно возникает в высокотемпературной части труб, где циркуляция носит неустойчивый характер, и материал труб испытывает переменные напряжения.
Накипь
Накипь в ее «чистом виде» представляет собой твердое кристаллическое вещество, которое находится в той точке котла, где оно образуется. Накипь образуется в результате перенасыщения и отложения на поверхности нагрева твердых примесей (солей кальция и магния).
Отложения окислов металлов образуется в результате реакции агрессивных растворов или газов с поверхностью металла в точке нахождения окислов. Они могут поступать из других частей системы и накапливаться в месте обнаружения. Окислы металлов могут образовывать отложения в сочетании с другими примесями. Это является еще одной причиной того, что управление процессами коррозии следует производить как механическими, так и химическими методами.
Шлам
Шлам представляет собой смесь жидких веществ, образованную органическим и/или неорганическими продуктами коррозии. Шламы, являющиеся продуктами реакций водообработки, являются предпочтительными по отношению к накипи, которая образуется в противном случае.
Шламы должны регулярно удаляться из котла, т.к. в противном случае скопления шлама в нижней части котла могут препятствовать раздаче воды, вызывать недостаточное поступление ее к отдельным участкам и, в конце концов, к перегреву металла.
Накипь и спекшийся шлам в любой теплопередающей поверхности действуют как «изолятор», который ухудшает теплопередачу и может привести к повреждению трубки.
Фосфатно-щелочной режим
Фосфатно-щелочной режим с применением противонакипина предназначен для предупреждения накипеобразования и коррозии в котлах с давлением пара до 2 МПа. При использовании этого режима необходимо поддерживать в котловой воде определенное соотношение между щелочностью и общим солесодержанием, получившим название относительной щелочности. Относительная щелочность котловой воды должна быть не выше 20%, т.е. общее солесодержание котловой воды должно быть не менее чем в 5 раз выше ее щелочного числа. Практически это значит, что в паровых котлах, работающих при давлении до 4МПа содержание хлоридов в котловой воде должно превышать значение щелочного числа не менее чем в 3 раза.
В котловой воде кальцинированная сода и тринатрийфосфат частично гидролизуются по уравнениям.
Na2CO3 + H2O = NaOH + NaHCO3
Na3PO4+H2O=Na2HPO4+NaOH
В результате гидролиза в котловой воде образуется щелочность.
Фосфатно – щелочной режим ведется по щелочному числу, которое поддерживается в пределах 150 – 200 мг/дм3 NaOH.
При фосфатно-щелочных режимах:
- соли магния выпадают в твердую фазу в виде гидроокиси магния, которая образуется в результате их реакции со щелочью:
MgSO4+2NaOH=Mg(OH)2+Na2 SO4
- бикарбонаты и оставшиеся в котловой воде карбонаты кальция в присутствии щелочи тринатрийфосфатом переводятся в гидроксилапатит, который выпадает в твердую фазу в виде шлама:
10СаСО3+6 Na3PO4+2NaOH=Ca10(PO4)6(OH)2+10Na2 CO3
10Ca(HCO3)2+ 6Na3PO4=Ca10(PO4)6(OH)2+18NaOH+20CO2
Для полной защиты от щелочной коррозии при фосфатно-щелочном режиме необходимо поддерживать высокое содержание хлоридов.
Если содержание солей в котле не обеспечивает защиту металла от щелочной коррозии, следует переходить на фосфатно-щелочной режим с нитратной пассивацией.
При фосфатно-щелочном режиме рН котловой воды всегда больше 10, что обеспечивает защиту котла от кислородной коррозии.
Назначение продувания котла
При низких давлениях пар не растворяет солей, поэтому при работе котла практически все соли, продукты коррозии и другие примеси, поступившие в котел с питательной водой, остаются в котловой воде. Повышение содержания солей, шлама и других примесей в воде недопустимо.
Соли, взвеси и другие примеси котловой воды способствуют загрязнению пара в результате уноса капель котловой воды с большим содержанием примесей, приводят к набуханию уровня и могут вызвать «вскипание» котла вследствие уменьшения скорости барботажа пара в пароводяном коллекторе, способствует интенсивному накипеобразованию. Для предотвращения роста содержания примесей в котловой воде и поддержания значений технологических показателей качества котловой воды в установленных пределах делается продувание котла.
Продувание котла необходимо делать для того, чтобы в котловой воде поддерживать не выше установленных предельных значений общее солесодержание, щелочность и содержание шлама.
Для удаления шлама делается нижнее продувание. Удаление солей, взвесей, пены производится через верхнее продувание, так как верхний слой в пароводяном коллекторе формируется из воды, выходящей из подъемных труб, которая содержит наибольшее количество примесей. Воронки верхнего продувания устанавливаются так, чтобы удалялся верхний слой и при любом открытии клапанов продувания уровень воды не опускался до опасного предела.
Продувание может быть периодическим и постоянным. Периодическое продувание делается для снижения технологических показателей качества котловой воды до установленных значений.
Постоянное продувание делается верхним. При постоянном продувании поддерживаются значения показателей качества котловой воды в заданных пределах.
Периодическое продувание делается для снижения содержания шлама в котле и для снижения щелочности котловой воды, если она оказалась выше нормы.
Назначение нижней продувки является периодическое удаление из котла выпадающего шлама, а также единовременный вывод больших количеств воды при необходимости резкого изменения ее состава. Если показатели качества котловой воды находятся в пределах норм водно-химического режима, то нижнее продувание котла производится 1 раз в 5-7 дней. На ходу продувание котлов (особенно нижнее) надо выполнять очень осторожно, не допуская сотрясений котла и резкого падения давления пара. Во время продувания прекращается питание котла. Каждое продувание котла отмечается в журнале.
Механик по заведованию осуществляет регулярный контроль качества питательной и котловой воды во всех действующих котлах и с периодичностью, установленными для данных котлов.
Таблица 4.1
Выполнение анализов
Выполнение анализов
Порядок тестирования
1. Заполните флакон до метки 20 мл охлажденной анализируемой водой.
2. Добавьте 4 капли реагента PA1 и взболтайте. Образец должен стать розовым. Если проба не окрасилась в розовый цвет, гидратная щелочность равна нулю. Занесите данные о нулевой щелочности в журнал регистрации.
3. Если проба окрасилась в розовый цвет, добавляйте реагент PA2 по одной капле, осторожно перемешивая до исчезновения розовой окраски. Подсчитайте количество использованных капель.
4. Каждая капля соответствует 40 мг-экв./ л гидратной щелочности, выраженной как СаСО3.
5. Сохраните образец после испытания на щелочность, поскольку он может быть использован для определения хлорида, если требуется.
Капли реагента PA2 | Гидратная щелочность в мг-экв./л CaCO3 | См. «Руководства по обработке» для требуемой концентрации. Общая информация указана ниже. |
1 2 3 4 5 6 7 8 9 10 | 40 80 120 160 200 240 280 320 360 400 | Низкая щелочность; увеличить дозу используемой щелочи для получения дополнительной 100 мг-экв./л гидратной щелочности Нормальный уровень гидратной щелочности Уменьшить уровень гидратной щелочности продуванием |
Общая щелочность (CaCO3)
Для общей щелочности замените реагент PA2 на TA4 в пункте 2.
Изменение цвета в пункте 3 меняется с синего на оранжевый.
Порядок тестирования
1. Заполните колбу до метки 20 мл охлажденного образца анализируемой воды.
Примечание: при измерении кипяченой воды используйте испытуемый образец из пункта 3 теста на щелочность.
2. Добавьте 4 капли реагента BC1 / CC1. Образец станет желтым.
3. Добавляйте капли реагента BC2 по одной, пока не появится бледно-оранжевый цвет. Подсчитать количество использованных капель. Каждая капля эквивалентна 20 мг-экв./л содержанию хлоридов.
4. ИЛИ
5. Добавьте капли реагента CC2 по одной, пока не появится бледно-оранжевый цвет. Подсчитать количество использованных капель. Каждая капля эквивалентна
5 мг-экв /л содержанию хлоридов.
Капли реагента BC2 | Хлорид мг –экв./ л Cl | Примечания |
1 2 3 4 5 6 7 8 9 10 11 12 13 14 15 16 17 18 19 20 | 20 40 60 80 100 120 140 160 180 200 220 240 260 280 300 320 340 360 380 400 | Содержание хлоридов приемлемо при низком давлении в котле Уменьшить количество хлоридов путем продувания |
Определение качества охлаждающей воды ДВС с помощью судовой лаборатории Spectrapak 309 фирмы UNITOR
Вопросы для самоконтроля:
1. Цели управляемой программы обработки воды в СЭУ?
2. Виды присадок к охлаждающей воде ДВС. Достоинства и недостатки.
3. Определение коррозии металла.
4. Характеристики и типы коррозии
5. Виды коррозии.
6. Причины появления коррозии и суть ее протекания.
7. Методы контроля поступления газов.
8. Причины появления накипи и суть ее протекания.
9. Причины появления шлама и суть его протекания.
10. Водные режимы парового котла.
11. Продувание парового котла (назначение, виды).
Лабораторная работа №4
Тема: ОПРЕДЕЛЕНИЕ КАЧЕСТВА КОТЛОВОЙ И ОХЛАЖДАЮЩЕЙ ВОДЫ МЕТОДИКАМИ DREW MARINE, VECOM MARINE И ЛАБОРАТОРИЕЙ SPECTRAPAK 309
Цель: Определение качества котловой воды с помощью методик Drew Marine, Vecom Marine, рекомендации по водному режиму. Определение качества охлаждающей воды ДВС с помощью судовой лаборатории Spectrapak 309 фирмы UNITOR.
Теоретический материал
В котле происходит преобразование химической энергии топлива в тепловую энергию пара, используемую для совершения работы. Общим для всех котлов является то, что к воде подводится тепло для получения пара, который затем используется для совершения работы на судне.
Дизели зависят от отсутствия накипи на теплопередающих поверхностях, предназначенных для охлаждения.
Их объединяет необходимость решения проблем накипеобразования и коррозии, несмотря на то, что некоторые формы коррозии более характерны для котлов высокого давления, в то время как другие чаще встречаются в дизелях.
Для эффективной эксплуатации оборудования для получения пара и систем охлаждения необходима постоянная обработка воды в связи с тем, что получение воды в испарителе, механическая деаэрация не позволяют удалить из воды все вредные примеси.
Основными целями управляемой программы обработки воды в любой энергетической установке являются:
· Поддержание теплопередающих поверхностей со стороны воды в парообразующих и охлаждающих системах в чистоте и без накипи;
· Предотвращение потери металла из-за коррозии;
· Обеспечение производства пара в котлах без вскипания, пенообразования и уноса примесей;
· Предотвращение образования отложений в системе пар-конденсат;
· Уменьшение потерь тепла при излишнем продувании котлов;
· Поддержание всего парообразующего и вспомогательного оборудования и связанных с ним паровых водяных систем на уровне их максимальной эффективности и, таким образом, уменьшение затрат.
Коррозия металлов
В судовых силовых установках в качестве материалов используются как сплавы на основе железа, так и не содержащие железо. Все эти металлы при контакте с водой медленно корродируют, если вода не подвергается надлежащей обработке. Высокая температура и давление увеличивают скорость коррозии. Целью любой комплексной программы обработки воды является защита от коррозии всего оборудования, как во время работы, так и выведенного из эксплуатации.
Коррозия представляет собой результат химического или электрохимического воздействия воды или воздуха на металл. На скорость коррозии оказывают влияние примеси различных веществ, содержащиеся в металле и воде. Обработанные должным образом чистые вода и металл уменьшают скорость коррозии. Если вода не обработана должным образом, в ней коррозируют все металлы. В котельных установках причиной коррозии чаще всего являются растворенные газы, неправильный уровень pH, ионы хлора, и механические причины. Ниже рассмотрены основные химические реакции коррозии.
|
|
Двойное оплодотворение у цветковых растений: Оплодотворение - это процесс слияния мужской и женской половых клеток с образованием зиготы...
Таксономические единицы (категории) растений: Каждая система классификации состоит из определённых соподчиненных друг другу...
Папиллярные узоры пальцев рук - маркер спортивных способностей: дерматоглифические признаки формируются на 3-5 месяце беременности, не изменяются в течение жизни...
Организация стока поверхностных вод: Наибольшее количество влаги на земном шаре испаряется с поверхности морей и океанов (88‰)...
© cyberpedia.su 2017-2024 - Не является автором материалов. Исключительное право сохранено за автором текста.
Если вы не хотите, чтобы данный материал был у нас на сайте, перейдите по ссылке: Нарушение авторских прав. Мы поможем в написании вашей работы!