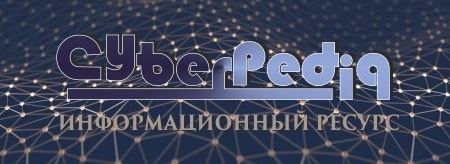
Эмиссия газов от очистных сооружений канализации: В последние годы внимание мирового сообщества сосредоточено на экологических проблемах...
Индивидуальные очистные сооружения: К классу индивидуальных очистных сооружений относят сооружения, пропускная способность которых...
Топ:
Отражение на счетах бухгалтерского учета процесса приобретения: Процесс заготовления представляет систему экономических событий, включающих приобретение организацией у поставщиков сырья...
Процедура выполнения команд. Рабочий цикл процессора: Функционирование процессора в основном состоит из повторяющихся рабочих циклов, каждый из которых соответствует...
Установка замедленного коксования: Чем выше температура и ниже давление, тем место разрыва углеродной цепи всё больше смещается к её концу и значительно возрастает...
Интересное:
Искусственное повышение поверхности территории: Варианты искусственного повышения поверхности территории необходимо выбирать на основе анализа следующих характеристик защищаемой территории...
Средства для ингаляционного наркоза: Наркоз наступает в результате вдыхания (ингаляции) средств, которое осуществляют или с помощью маски...
Мероприятия для защиты от морозного пучения грунтов: Инженерная защита от морозного (криогенного) пучения грунтов необходима для легких малоэтажных зданий и других сооружений...
Дисциплины:
![]() |
![]() |
5.00
из
|
Заказать работу |
|
|
План лекции:
1. Схема комплекса кислородно-взвешенной плавки
2. Технико-экономические показатели кислородно-взвешенной плавки.
3. Плавка во взвешенном состоянии на подогретом дутье
4. Основные технико-экономические показатели взвешенной плавки с подогревом дутья
Автогенный процесс плавки сульфидного сырья с использованием в качестве дутья технологического кислорода называют кислородно-взвешенной (факельной) плавкой (КВП или КФП). Этот вид плавки применяют в настоящее время только на двух заводах в мире – в Канаде на заводе «Коппер-Клиф» и на Алмалыкском ГМК.
Отличительной особенностью плавки во взвешенном состоянии на кислородном дутье является использование для ее осуществления печей с горизонтальным факелом. Возможность использования в этом виде плавки печей с горизонтальным рабочим пространством обусловлена высокой скоростью окисления сульфидов в чистом кислороде и относительно низкой скоростью газовых потоков в печи вследствие небольшого объема образующихся технологических газов.
Рисунок 2 – Схема комплекса кислородно-взвешенной плавки: 1 – шихтовые бункера; 2 – питатели; 3 – расходомеры; 4 – печь; 5 – газоход; 6 – выпускные желоба; 7 – штейновый ковш; 8 – шлаковоз
Печь для плавки во взвешенном состоянии на кислородном дутье (96–98% O2) представляет собой агрегат типа отражательной печи с горелками на обоих торцах печи и центральным отводом газов. Предварительно высушенная до содержания влаги менее 0,5% шихта (сульфидный концентрат вместе с мелким кварцевым флюсом) подается в струю кислорода горелками, установленными на одной из торцевых стен печи. Штейн отстаивается под слоем шлака, а в шлаковом расплаве протекают реакции взаимодействия сульфидов с оксидами и шлакообразования.
|
На противоположной стороне печи установлены горелки для факельного сжигания в кислороде пирротинового или пиритного концентрата. В этом факеле образуются капли бедного по содержанию меди сульфидного расплава, служащего для промывки шлака перед выпуском с целью его обеднения.
Штейн по мере накопления периодически выпускают через шпур, расположенный на одной из боковых стен печи. Выпуск шлака осуществляют со стороны обеднительного торца. Отходящие газы, содержащие около 80% SO2, направляют в химическое производство.
При сжигании сульфидов в чистом кислороде в факеле развиваются высокие температуры (1550–1600°С), причем если содержание серы в концентрате превышает 26–28%, то количество теплоты, выделяющейся при сжигании сульфидов, оказывается в избытке. Если эту теплоту не отнимать, то печь будет перегреваться, а температура отходящих газов возрастать. Для того чтобы убрать избыточную теплоту и защитить стены и свод от разрушения, кладку печи необходимо охлаждать. С этой целью через каждые два ряда кирпичей устанавливают закладные медные кессоны, охлаждаемые водой.
Окисление сульфидов при КВП протекает при высокой температуре. Поскольку основная масса теплоты выделяется на поверхности сульфидных частиц, их температура существенно выше, чем средняя температура печи и факела. Прямые замеры температуры частиц отсутствуют, однако можно предполагать, что она превышает 1600–1700°С. При такой высокой температуре большинство частиц перерабатываемой шихты плавится. Нерасплавленными остаются только наиболее тугоплавкие оксиды: SiO2, CaO и частицы флюсов.
Характерной особенностью окисления сульфидов при КВП является образование значительных количеств высшего оксида железа (Fе3О4). Условия восстановления магнетита в ванне печи КВП недостаточно благоприятны. Необходима избыточная энергия для преодоления энергетического барьера, связанного с образованием новой фазы (газообразной). Процесс разрушения магнетита фактически полностью зависит от скорости молекулярной диффузии. Поэтому остаточное содержание магнетита в шлаках КВП достигает 15–24%. Это обусловливает повышенную растворимость сульфидов в шлаках и снижает межфазное натяжение на границе шлака со штейном.
|
Газы, выходящие из печи, имеют высокую температуру (>1300°С) и обязательно должны направляться в котлы-утилизаторы. Трудности, которые в этом случае возникают, связаны с высоким содержанием в газах SO2 и большой их запыленностью. С повышением содержания в газах сернистого ангидрида увеличивается опасность конденсации паров серной кислоты, которая вызывает быструю коррозию всех охлаждающих элементов котла. Во избежание этого температура труб и других охлаждающих элементов должна быть выше точки росы. Наиболее эффективно теплота отходящих газов используется при установке котлов-утилизаторов туннельного типа, работающих по принципу испарительного охлаждения. Такие котлы обеспечивают получение пара давлением 7–8 МПа.
Кислородно-взвешенная плавка является значительным шагом вперед в совершенствовании технологии переработки сульфидного медного сырья по сравнению с отражательной плавкой и плавкой в электрических печах. Ее важнейшие достоинства – использование теплоты от окисления сульфидов для процессов плавления и теплоты отходящих газов на получение пара. При КВП в одном аппарате совмещаются процессы обжига и плавления, большая часть серы выделяется в одном агрегате, что приводит к повышению извлечения серы и уменьшению степени загрязнения атмосферы. Применение чистого технологического кислорода или дутья, обогащенного кислородом, обеспечивает получение газов с высоким содержанием SO2, что удешевляет их переработку на элементарную серу или серную кислоту.
Наряду с достоинствами КВП этот процесс имеет ряд принципиальных недостатков. Важнейшими из них являются: сложная и дорогая подготовка шихты к плавке, высокое содержание меди в отвальных шлаках, высокий пылеунос шихты, недостаточная комплексность использования сырья.
Технико-экономические показатели плавки во взвешенном состоянии на кислородном дутье приведены в таблице 3.
Таблица 3 – Технико-экономические показатели кислородно-взвешенной плавки.
|
Показатели | КВП | |
Завод Коппер-Клиф | АГМК | |
Производительность печи, т шихты/сут | ||
Удельный проплав т/м2∙сут | 12,8 | |
Содержание в концентрате, % меди серы | 31,5 | 18,5 35,5 |
Извлечение меди в штейн, % | ||
Содержание меди в штейне, % | ||
Содержание в шлаке, % меди SiO2 железа Fe3O4 | 0,75 28–32 | 0,9–1 33–35 |
Энергетические затраты в перерасчете на условное топливо, кг/т шихты | ||
Десульфуризация, % | 50–55 | 70–75 |
Содержание SO2 в газах, % | 70–75 | |
Выход газов, м3/т шихты | 120–140 | |
Расход технологического кислорода, м3/т шихты |
Плавка во взвешенном состоянии на подогретом дутье
Плавка во взвешенном состоянии на подогретом дутье была почти одновременно с КВП осуществлена в промышленном масштабе финской фирмы «Оутокумпу» на заводе «Харьявалта». В первоначальном варианте для плавки применяли воздушное дутье, подогретое до 400–500°С.
Финскую плавку на сегодня можно считать самым распространенным в промышленности и наиболее технологически и аппаратурно отработанным автогенным процессом плавки сульфидных концентратов.
Все заводы, применяющие этот вид плавки, включая завод «Харьявалта», используют в настоящее время дутье, обогащенное кислородом до 30–40%. Температура нагрева обогащенного дутья на различных заводах колеблется от 200 до 1000°С.
Конструкция печи для плавки во взвешенном состоянии на подогретом дутье достаточно сложна – она сочетает в себе две вертикальные шахты (плавильную и газоход-аптейк) и горизонтальную камеру-отстойник (рисунок 3).
Рисунок 3 – Печь для плавки во взвешенном состоянии с топливным и паровым воздухонагревателями завода «Харьявалта»: 1 – горелка; 2 – реакционная камера; 3 – отстойная ванна; 4 – аптейк; 5 – котел-утилизатор; 6 – паровой воздухоподогреватель; 7 – топливный воздухоподогреватель
Вся печь финской плавки выполнена в виде кладки из магнезитового кирпича. Футеровка плавильной шахты и аптейка заключена в металлические кожухи из листовой стали. В кладку всех элементов печи заложено большое количество водоохлаждаемых элементов, что позволяет значительно удлинить срок службы агрегата. Аптейк непосредственно сочленен с котлом-утилизатором туннельного типа. В боковой стене отстойной камеры установлены две медные водоохлаждаемые плиты с отверстиями для выпуска шлака, а в передней торцевой стене – чугунные шпуры для выпуска штейна.
|
Процесс начинается с прогревания частиц, которое при малых их размерах протекает достаточно быстро. Когда температура частицы достигнет 550–650°С, начинают интенсивно протекать реакции диссоциации высших сульфидов – пирита и халькопирита, идущие с поглощением теплоты. Бурно протекающие эндотермические реакции препятствуют прогреву частиц и, пока не удалится избыточная сера, температура частицы существенно не повысится. Горит на этой стадии только элементарная сера. После практически полного завершения диссоциации высших сульфидов начинается быстрое окисление низших сульфидов. Температура материала при этом быстро возрастает, достигая в зависимости от содержания серы в концентрате, кислорода в дутье и температуры дутья 1300–1500°С.
Окисление сульфидов сопровождается образованием больших количеств магнетита, особенно в поверхностных слоях частиц. Переокисление железа до магнетита зависит также от степени десульфуризации при плавке. С возрастанием степени десульфуризации и получением более богатых штейнов все большая часть железа переводится в форму магнетита.
Управление степенью десульфуризации достигается изменением соотношения между количеством подаваемого с дутьем кислорода и количеством вдуваемого концентрата.
Процесс фирмы «Оутокумпу», как и кислородно-взвешенная плавка, направлен на интенсификацию и без того быстро протекающего окисления сульфидов и плавления легкоплавких составляющих. Для ускорения наиболее медленных стадий технологии (растворения тугоплавких составляющих, коалесценции штейновых частиц и разделения фаз в неподвижной ванне) не созданы благоприятные условия. По этим причинам остаточное содержание меди в шлаке составляет около 1,5%, что требует обязательного дополнительного обеднения шлака либо в электрических печах, либо путем выделения сульфидов из застывших шлаков методом флотации.
При плавке во взвешенном состоянии на подогретом дутье успешно решены вопросы тепловой энергетики и использования газовой серы.
Процесс характеризуется хорошим использованием теплоты от горения сульфидов. Отходящие газы печей завода «Харьявалта» направляют в котлы-утилизаторы туннельного типа для получения энергетического пара давлением 7 МПа и далее в рекуператоры (до 1971 г.) или в автономные воздухонагреватели.
|
Электроэнергия, вырабатываемая за счет пара, не только покрывает потребности завода, включая затраты на получение кислорода, но и позволяет передавать ее избыток в государственную энергетическую систему Финляндии. Пример завода «Харьявалта» убедительно свидетельствует о том, что правильная организация автогенного процесса дает возможность полностью осуществлять всю технологию за счет энергии, получающейся при сжигание сульфидов.
В замыкании энергетического баланса важную роль играет содержание кислорода в дутье. Энергетический баланс успешно замыкается при оптимальной концентрации кислорода в дутье 35–40%, что и принято в настоящее время на заводе «Харьявалта». Температура подогрева дутья снижена с 400–500 (воздушное дутье) до 200°С.
Практически полное использование кислорода на процесс горения сульфидов позволяет получать богатые по содержанию SO2 газы. При воздушном дутье оно составляет 13%, а с увеличением содержания кислорода в дутье до 30–40% возрастает до 18–20%.
Основными достоинствами процесса являются использование тепла сжигания сульфидов и высокое извлечение серы в газы, богатые по содержанию SO2. Главнейшие недостатки процесса: низкая удельная производительность, высокое содержание ценных компонентов в шлаках, необходимость глубокой сушки исходной шихты и связанный с этим большой пылеунос, недостаточная комплексность использования сырья.
Основные технико-экономические показатели взвешенной плавки с использованием подогретого дутья приведены в таблице 4.
Таблица 4 – Основные технико-экономические показатели взвешенной плавки с подогревом дутья
Показатель | «Харьявалта» |
Производительность печи, т/сут | |
Удельный проплав т/м2∙сут | 11,9 |
Содержание О2 в дутье, % | 35–40 |
Температура дутья, ОС | |
Содержание меди, % в штейне в шлаке (после обеднения) | 0,85 |
Содержание SO2 в газах, % | 18–20 |
Пылеунос | 8–10 |
Метод обеднения шлака | Флотация |
Вместе с тем кивцэтный процесс сохраняет и ряд недостатков, важнейшими из которых являются необходимость глубокой сушки материала и низкая суммарная удельная производительность по сравнению с автогенными процессами в расплаве. Кроме того, отсутствуют освоенные плавильные агрегаты большой мощности.
Контрольные вопросы:
1. Объяснить схему комплекса кислородно-взвешенной плавки
2. Описать технико-экономические показатели кислородно-взвешенной плавки.
3. Объяснить плавку во взвешенном состоянии на подогретом дутье
4. Показать основные технико-экономические показатели взвешенной плавки с подогревом дутья
Лекция 17. Общие положения о кислородно-взвешенной электротермической плавке
План лекции:
1. Кивцэтный процесс
2.Основные процессы и аппаратура кивцэтного процесса.
Кивцэтный процесс является усовершенствованной разновидностью плавки во взвешенном состоянии, разработанной советскими металлургами для переработки многих типов сульфидных концентратов (впервые способ КИВЦЭТ был разработан для переработки медно-цинковых коллективных концентратов Николаевского месторождения).
Кивцетный процесс прошел длительные полупромышленные испытания на опытном заводе ВНИИцветмета при переработке многих типов сульфидных концентратов. На основании результатов этих работ была построена и в 1961 г пущена в эксплуатацию опытно-промышленная кивцэтная установка на медном заводе Иртышского полиметаллического комбината. Второй промышленный агрегат КИВЦЭТ-ЦС был пущен в 1985 г на Усть-Каменогорском свинцово-цинковом комбинате (ныне ОАО "Казцинк”) для переработки свинцовых концентратов. Процесс основан на сочетании принципов взвешенной и циклонной плавок и рационального использования технологического кислорода и электроэнергии. Стадии обжига и плавки, разделения продуктов плавки, обеднения шлаков и конденсации цинковых паров протекают в одном объединенном агрегате.
В кивцэтном процессе тщательно высушенный концентрат поступает в циклонную горелку сверху. Кислород с большой скоростью (до 150 м/с) подается в циклон тангенциально. Из-за большой скорости газы получают в циклоне быстрое вращательное движение, в результате чего частицы шихты отбрасываются на стенки камеры. При горении сульфидов в чистом технологическом кислороде развиваются высокие температуры, шихта плавится, образуя тонкую вращающуюся пленку расплава на внутренней стенке циклона, в которой и протекают основные процессы. Перегретый расплав стекает в отстойную камеру, где происходит отделение штейна от шлака. Высокие скорости окисления в чистом кислороде обеспечивают полное использование кислорода и получение газов с высоким содержанием SO2 (75-80%).
Эти газы отводятся отдельно по газоходу, примыкающему к камере отстаивания, и направляются в котлы - утилизаторы для использования теплоты, в электрофильтры для улавливания пыли и далее в химический цех для извлечения серы.
Применение циклонных горелок позволяет резко снизить запыленность газов и устранить таким образом один из недостатков взвешенной плавки.
Шлаковый расплав по мере накопления перетекает во вторую (электротермическую) часть кивцэтного агрегата, которая предназначена для его обеднения и отгонки летучих компонентов путем восстановительной обработки шлака. Для поддержания сильно восстановительной атмосферы и предотвращения окисления паров возгоняемых металлов камеру обеднения тщательно герметизируют. С этой целью камеры обеднения и отстаивания разделяют перегородкой, погруженной в шлак, а места ввода электродов уплотняют и используют специальные загрузочные устройства. Для осуществления процессов восстановления в электротермическую часть агрегата загружают твёрдый восстановитель. В этой части печи происходит разрушение магнетита, восстановление цинка до элементарного состояния и его испарение, возгонка соединений свинца, кадмия, германия и некоторых других редких и рассеянных элементов. При высоком содержании цинка в шихте образующиеся в восстановительной зоне его пары могут быть направлены на конденсацию с получением цинка в виде жидкого металла. Однако такой цинк оказывается очень сильно загрязненным примесями и нуждается в дорогой операции рафинирования. Поэтому более целесообразно возгоны получать в виде оксидов и затем направлять их на гидрометаллургическую переработку.
Контрольные вопросы:
1. Объяснить сущность кивцэтного процесса.
2.Рассказать основные процессы и аппаратуру кивцэтного процесса.
|
|
Особенности сооружения опор в сложных условиях: Сооружение ВЛ в районах с суровыми климатическими и тяжелыми геологическими условиями...
Индивидуальные и групповые автопоилки: для животных. Схемы и конструкции...
Историки об Елизавете Петровне: Елизавета попала между двумя встречными культурными течениями, воспитывалась среди новых европейских веяний и преданий...
Механическое удерживание земляных масс: Механическое удерживание земляных масс на склоне обеспечивают контрфорсными сооружениями различных конструкций...
© cyberpedia.su 2017-2024 - Не является автором материалов. Исключительное право сохранено за автором текста.
Если вы не хотите, чтобы данный материал был у нас на сайте, перейдите по ссылке: Нарушение авторских прав. Мы поможем в написании вашей работы!