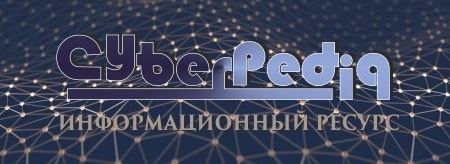
Общие условия выбора системы дренажа: Система дренажа выбирается в зависимости от характера защищаемого...
Двойное оплодотворение у цветковых растений: Оплодотворение - это процесс слияния мужской и женской половых клеток с образованием зиготы...
Топ:
Устройство и оснащение процедурного кабинета: Решающая роль в обеспечении правильного лечения пациентов отводится процедурной медсестре...
Марксистская теория происхождения государства: По мнению Маркса и Энгельса, в основе развития общества, происходящих в нем изменений лежит...
Когда производится ограждение поезда, остановившегося на перегоне: Во всех случаях немедленно должно быть ограждено место препятствия для движения поездов на смежном пути двухпутного...
Интересное:
Отражение на счетах бухгалтерского учета процесса приобретения: Процесс заготовления представляет систему экономических событий, включающих приобретение организацией у поставщиков сырья...
Уполаживание и террасирование склонов: Если глубина оврага более 5 м необходимо устройство берм. Варианты использования оврагов для градостроительных целей...
Как мы говорим и как мы слушаем: общение можно сравнить с огромным зонтиком, под которым скрыто все...
Дисциплины:
![]() |
![]() |
5.00
из
|
Заказать работу |
|
|
Сплавы цветных металлов применяют для изготовления деталей, работающих в условиях агрессивной среды, подвергающихся трению, требующих большой теплопроводности, электропроводности и уменьшенной массы.
Медь— металл красноватого цвета, отличающийся высокой теплопроводностью и стойкостью против атмосферной коррозии. Прочность невысокая: ав = 180......240 МПа при высокой пластичности б>50%.
Латунь — сплав меди с цинком (10...40 %), хорошо поддается холодной прокатке, штамповке, вытягиванию <7ь = 25О...4ОО МПа, 6=35..15%. При маркировке лату-ней (Л96, Л90,..., Л62) цифры указывают на содержание меди в процентах. Кроме того, выпускают латуни многокомпонентные, т. е. с другими элементами (Мп, Sn, Pb, Al).
Бронза — сплав меди с оловом (до 10%), алюминием, марганцем, свинцом и другими элементами. Обладает хорошими литейными свойствами (вентили, краны, люстры). При маркировке бронзы Бр.ОЦСЗ-12-5 отдельные индексы обозначают: Бр — бронза, О — олово, Ц — цинк, С —свинец, цифры 3, 12, 5-—содержание в процентах олова цинка, свинца. Свойства бронзы зависят от состава: бв=15О...21О МПа, б=4...8%, НВ60 (в среднем).
Алюминий — легкий серебристый металл, обладающий низкой прочностью при растяжении — аа = 80......100 МПа, твердостью — НВ20, малой плотностью — 2700 кг/м3, стоек к атмосферной коррозии. В чистом виде в строительстве применяют редко (краски, газооб-разователи, фольга). Для повышения прочности в него вводят легирующие добавки (Мп, Си, Mg, Si, Fe) и используют некоторые технологические приемы. Алюминиевые сплавы делят на литейные, применяемые для отливки изделий (силумины), и деформируемые (дюралюмины), идущие для прокатки профилей, листов и т.п.
Силумины — сплавы алюминия с кремнием (до 14%), они обладают высокими литейными качествами, малой усадкой, прочностью ои = 200 МПа, твердостью НВ50...70 при достаточно высокой пластичности 6== =5...10 %. Механические свойства силуминов можно существенно улучшить путем модифицирования. При этом увеличивается степень дисперсности кристаллов, что повышает прочность и пластичность силуминов.
|
Дюралюмины — сложные сплавы алюминия с медью (до 5,5 %), кремнием (менее 0,8%). марганцем (до 0,8 %), магнием (до 0,8 %) и др. Их свойства улучшают термической обработкой (закалкой при температуре 500...520 ° С с последующим старением). Старение осуществляют на воздухе в течение 4...5 сут при нагреве на 170 ° С в течение 4...5 ч.
Термообработка алюминиевых сплавов основана на дисперсном твердении с выделением твердых дисперсных частиц сложного химического состава. Чем мельче частицы новообразований, тем выше эффект упрочнения сплавов. Предел прочности дюралюминов после закалки и старения составляет 400...480 МПа и может быть повышен до 550...600 МПа в результате наклепа при обработке давлением.
В последнее время алюминий и его сплавы все шире применяют в строительстве для несущих и ограждающих конструкций. Особенно эффективно применение дюралюминов для конструкций в большепролетных сооружениях, в сборно-разборных конструкциях, при сейсмическом строительстве, в конструкциях, предназначенных для работы в агрессивной среде. Начато изготовление трехслойных навесных панелей из листов алюминиевых сплавов с заполнением пенопластовыми материалами. Путем введения газообразователей можно создать высокоэффективный материал пеноалюминий со средней плотностью 100...300 кг/м3
Все алюминиевые сплавы поддаются сварке, но она осуществляется более трудно, чем сварка стали, из-за образования тугоплавких оксидов АЬОз.
Особенностями дюралюмина как конструкционного сплава являются: низкое значение модуля упругости, примерно в 3 раза меньше, чем у стали, влияние температуры (уменьшение прочности при повышении температуры более 400 ° С и увеличение прочности и пластичности при отрицательных температурах); повышенный примерно в 2 раза по сравнению со сталью коэффициент линейного расширения; пониженная свариваемость.
|
Титан за последнее время начал применяться в разных отраслях техники благодаря ценным свойствам: высокой коррозионной стойкости, меньшей плотности (4500 кг/м3) по сравнению со сталью, высоким прочностным свойствам, повышенной теплостойкости. На основе титана создаются легкие и прочные конструкции с уменьшенными габаритами, способные работать при повышенных температурах.
Технологии подготовки поверхности металла
Надёжная антикоррозионная защита металла возможна только при высоком уровне подготовки поверхности.
Перед нанесением антикоррозионного лакокрасочного материала необходимо, прежде всего, выбрать технологию и метод подготовки поверхности металла перед окраской.
Существуют механические и химические методы подготовки поверхности. Механические методы имеют ряд ограничений в применении и не способны обеспечить хорошие защитные свойства лакокрасочных покрытий, особенно при их эксплуатации в жёстких условиях. В настоящее время широкое распространение получили химические методы подготовки поверхности. Данные методы позволяют обрабатывать изделия любой формы и сложности, легко поддаются автоматизации и обеспечивают высокое качество поверхности окрашиваемых изделий.
Как выбрать технологический процесс подготовки поверхности?
Какую схему подготовки поверхности следует выбрать для разных металлов, различных лакокрасочных покрытий и условий эксплуатации? Давайте обо всём по порядку.
Выбор технологии подготовки поверхности зависит от трёх основных факторов: условий эксплуатации окрашенных изделий, типа металла и применяемого лакокрасочного покрытия.
С точки зрения подготовки поверхности металлы можно разделить на две категории:
• чёрные металлы — сталь, чугун и др.;
• цветные металлы — алюминий, сплавы цинка, титана, меди, оцинкованная сталь и др.
Для подготовки поверхности чёрных металлов применяют фосфатирование, для обработки цветных металлов — фосфатирование или хроматирование. При одновременной обработке цинка и алюминия с чёрными металлами предпочтение отдают фосфатированию. Пассивирование применяют на заключительной стадии после операций фосфатирования, хроматирования и обезжиривания.
|
Технологические процессы подготовки поверхности изделий, эксплуатирующихся внутри помещений, могут состоять из 3-5 стадий.
Практически во всех случаях после проведения химической подготовки поверхности изделия сушат от влаги в специальных камерах.
Полный цикл химической подготовки поверхности выглядит так:
• обезжиривание;
• промывка питьевой водой;
• нанесение конверсионного слоя;
• промывка питьевой водой;
• промывка деминерализованной водой;
• пассивация.
Технологический процесс кристаллического фосфатирования предусматривает стадию активации непосредственно перед нанесением конверсионного слоя. При применении хроматирования могут быть введены стадии осветления (при использовании сильнощелочного обезжиривания) или кислотной активации.
Выбор технологии, обеспечивающей высокое качество подготовки поверхности перед окраской, обычно ограничен размерами производственных площадей и финансовыми возможностями. Если таких ограничений нет, то следует выбирать многостадийный технологический процесс, гарантирующий необходимое качество получаемых лакокрасочных покрытий.
Однако, как правило, с ограничивающими факторами приходится считаться. Поэтому для выбора оптимального варианта предварительной обработки поверхности следует провести предварительные испытания предполагаемых покрытий на месте.
Обработка металла распылением. Для обработки металла методом распыления можно применять АХПП как тупикового, так и проходного типов. Высокую производительность обеспечивают агрегаты проходного типа непрерывного действия.
Максимальная скорость движения конвейера в АХПП ограничивается возможностью качественного нанесения ЛКМ в камере окраски и составляет, как правило, не более 2,0м/мин. При возрастании скорости конвейера потребуется расширение производственных площадей.
Большим достоинством АХПП проходного типа является возможность применения единого конвейера для участков подготовки поверхности и окраски изделий.
|
Обработка металла погружением. Для обработки металла методом погружения используют АХПП, состоящие из ряда последовательно расположенных ванн, оборудования перемешивания, транспортёра, разводки трубопроводов, камеры сушки. Изделия транспортируют с помощью тельфера, автооператора или кран-балки. Агрегат обработки погружением занимает значительно меньше производственной площади по сравнению с агрегатом обработки распылением. Но в этом случае после подготовки поверхности потребуется введение дополнительной операции — перевешивания изделий на конвейер окраски.
Пароструйный метод. Для подготовки к окраске крупногабаритных изделий, а также при отсутствии необходимых производственных площадей возможно применение пароструйной обработки металла (обезжиривание с одновременным аморфным фосфатированием). Металлообработка производится оператором вручную стволом-очистителем, из которого на изделия распыляется пароводяная смесь при температуре 140 ° С с добавками специальных химикатов.
Обработка металла
Выбор технологии подготовки поверхности и обработки металла — ответственный этап организации покрасочных работ, так как он во многом определяет качество будущего лакокрасочного покрытия и должен производиться с привлечением квалифицированных специалистов.
Все цветные сплавы при нагреве в значительно больших объемах, чем черные металлы, растворяют газы окружающей атмосферы и химически взаимодействуют со всеми газами, кроме инертных. Особенно активные в этом смысле более тугоплавкие и химически более активные металлы: титан, цирконий, ниобий, тантал, молибден. Эту группу металлов часто выделяют в группу тугоплавких, химически активных металлов.
Одним из самых эффективных методов защиты цветного металла от атмосферной коррозии считается нанесение защитных лакокрасочных материалов. Существуют три группы средств для защиты металлических поверхностей: грунтовки, краски и универсальные препараты «три в одном». Грунтовка — незаменимое средство борьбы с атмосферным окислением, одно- или двухслойное грунтование производится перед окрашиванием, помимо защитных свойств сообщая финишному покрытию лучшую адгезию к основанию. При выборе состава важно знать, что для разных металлов используются разные грунтовки
Для алюминиевых оснований используют специальные грунтовки на цинковой основе либо уретановые краски. Медь, латунь и бронзу обычно не красят — эти металлы поставляются на рынок с заводской обработкой, защищающей поверхность и подчеркивающей ее красоту. Если же целостность такого «фирменного» покрытия со временем нарушается, его лучше полностью удалить с помощью растворителя, после чего основание следует отполировать и покрыть эпоксидным или полиуретановым лаком.
|
Сплавы цветных металлов применяют для изготовления деталей, работающих в условиях агрессивной среды, подвергающихся трению, требующих большой теплопроводности, электропроводности и уменьшенной массы.
Медь— металл красноватого цвета, отличающийся высокой теплопроводностью и стойкостью против атмосферной коррозии. Прочность невысокая: ав = 180......240 МПа при высокой пластичности б>50%.
Латунь — сплав меди с цинком (10...40 %), хорошо поддается холодной прокатке, штамповке, вытягиванию <7ь = 25О...4ОО МПа, 6=35..15%. При маркировке лату-ней (Л96, Л90,..., Л62) цифры указывают на содержание меди в процентах. Кроме того, выпускают латуни многокомпонентные, т. е. с другими элементами (Мп, Sn, Pb, Al).
Бронза — сплав меди с оловом (до 10%), алюминием, марганцем, свинцом и другими элементами. Обладает хорошими литейными свойствами (вентили, краны, люстры). При маркировке бронзы Бр.ОЦСЗ-12-5 отдельные индексы обозначают: Бр — бронза, О — олово, Ц — цинк, С —свинец, цифры 3, 12, 5-—содержание в процентах олова цинка, свинца. Свойства бронзы зависят от состава: бв=15О...21О МПа, б=4...8%, НВ60 (в среднем).
Алюминий — легкий серебристый металл, обладающий низкой прочностью при растяжении — аа = 80......100 МПа, твердостью — НВ20, малой плотностью — 2700 кг/м3, стоек к атмосферной коррозии. В чистом виде в строительстве применяют редко (краски, газооб-разователи, фольга). Для повышения прочности в него вводят легирующие добавки (Мп, Си, Mg, Si, Fe) и используют некоторые технологические приемы. Алюминиевые сплавы делят на литейные, применяемые для отливки изделий (силумины), и деформируемые (дюралюмины), идущие для прокатки профилей, листов и т.п.
Силумины — сплавы алюминия с кремнием (до 14%), они обладают высокими литейными качествами, малой усадкой, прочностью ои = 200 МПа, твердостью НВ50...70 при достаточно высокой пластичности 6== =5...10 %. Механические свойства силуминов можно существенно улучшить путем модифицирования. При этом увеличивается степень дисперсности кристаллов, что повышает прочность и пластичность силуминов.
Дюралюмины — сложные сплавы алюминия с медью (до 5,5 %), кремнием (менее 0,8%). марганцем (до 0,8 %), магнием (до 0,8 %) и др. Их свойства улучшают термической обработкой (закалкой при температуре 500...520 ° С с последующим старением). Старение осуществляют на воздухе в течение 4...5 сут при нагреве на 170 ° С в течение 4...5 ч.
Термообработка алюминиевых сплавов основана на дисперсном твердении с выделением твердых дисперсных частиц сложного химического состава. Чем мельче частицы новообразований, тем выше эффект упрочнения сплавов. Предел прочности дюралюминов после закалки и старения составляет 400...480 МПа и может быть повышен до 550...600 МПа в результате наклепа при обработке давлением.
В последнее время алюминий и его сплавы все шире применяют в строительстве для несущих и ограждающих конструкций. Особенно эффективно применение дюралюминов для конструкций в большепролетных сооружениях, в сборно-разборных конструкциях, при сейсмическом строительстве, в конструкциях, предназначенных для работы в агрессивной среде. Начато изготовление трехслойных навесных панелей из листов алюминиевых сплавов с заполнением пенопластовыми материалами. Путем введения газообразователей можно создать высокоэффективный материал пеноалюминий со средней плотностью 100...300 кг/м3
Все алюминиевые сплавы поддаются сварке, но она осуществляется более трудно, чем сварка стали, из-за образования тугоплавких оксидов АЬОз.
Особенностями дюралюмина как конструкционного сплава являются: низкое значение модуля упругости, примерно в 3 раза меньше, чем у стали, влияние температуры (уменьшение прочности при повышении температуры более 400 ° С и увеличение прочности и пластичности при отрицательных температурах); повышенный примерно в 2 раза по сравнению со сталью коэффициент линейного расширения; пониженная свариваемость.
Титан за последнее время начал применяться в разных отраслях техники благодаря ценным свойствам: высокой коррозионной стойкости, меньшей плотности (4500 кг/м3) по сравнению со сталью, высоким прочностным свойствам, повышенной теплостойкости. На основе титана создаются легкие и прочные конструкции с уменьшенными габаритами, способные работать при повышенных температурах.
Технологии подготовки поверхности металла
Надёжная антикоррозионная защита металла возможна только при высоком уровне подготовки поверхности.
Перед нанесением антикоррозионного лакокрасочного материала необходимо, прежде всего, выбрать технологию и метод подготовки поверхности металла перед окраской.
Существуют механические и химические методы подготовки поверхности. Механические методы имеют ряд ограничений в применении и не способны обеспечить хорошие защитные свойства лакокрасочных покрытий, особенно при их эксплуатации в жёстких условиях. В настоящее время широкое распространение получили химические методы подготовки поверхности. Данные методы позволяют обрабатывать изделия любой формы и сложности, легко поддаются автоматизации и обеспечивают высокое качество поверхности окрашиваемых изделий.
Как выбрать технологический процесс подготовки поверхности?
Какую схему подготовки поверхности следует выбрать для разных металлов, различных лакокрасочных покрытий и условий эксплуатации? Давайте обо всём по порядку.
Выбор технологии подготовки поверхности зависит от трёх основных факторов: условий эксплуатации окрашенных изделий, типа металла и применяемого лакокрасочного покрытия.
С точки зрения подготовки поверхности металлы можно разделить на две категории:
• чёрные металлы — сталь, чугун и др.;
• цветные металлы — алюминий, сплавы цинка, титана, меди, оцинкованная сталь и др.
Для подготовки поверхности чёрных металлов применяют фосфатирование, для обработки цветных металлов — фосфатирование или хроматирование. При одновременной обработке цинка и алюминия с чёрными металлами предпочтение отдают фосфатированию. Пассивирование применяют на заключительной стадии после операций фосфатирования, хроматирования и обезжиривания.
Технологические процессы подготовки поверхности изделий, эксплуатирующихся внутри помещений, могут состоять из 3-5 стадий.
Практически во всех случаях после проведения химической подготовки поверхности изделия сушат от влаги в специальных камерах.
Полный цикл химической подготовки поверхности выглядит так:
• обезжиривание;
• промывка питьевой водой;
• нанесение конверсионного слоя;
• промывка питьевой водой;
• промывка деминерализованной водой;
• пассивация.
Технологический процесс кристаллического фосфатирования предусматривает стадию активации непосредственно перед нанесением конверсионного слоя. При применении хроматирования могут быть введены стадии осветления (при использовании сильнощелочного обезжиривания) или кислотной активации.
Выбор технологии, обеспечивающей высокое качество подготовки поверхности перед окраской, обычно ограничен размерами производственных площадей и финансовыми возможностями. Если таких ограничений нет, то следует выбирать многостадийный технологический процесс, гарантирующий необходимое качество получаемых лакокрасочных покрытий.
Однако, как правило, с ограничивающими факторами приходится считаться. Поэтому для выбора оптимального варианта предварительной обработки поверхности следует провести предварительные испытания предполагаемых покрытий на месте.
|
|
Механическое удерживание земляных масс: Механическое удерживание земляных масс на склоне обеспечивают контрфорсными сооружениями различных конструкций...
Кормораздатчик мобильный электрифицированный: схема и процесс работы устройства...
История развития хранилищ для нефти: Первые склады нефти появились в XVII веке. Они представляли собой землянные ямы-амбара глубиной 4…5 м...
Археология об основании Рима: Новые раскопки проясняют и такой острый дискуссионный вопрос, как дата самого возникновения Рима...
© cyberpedia.su 2017-2024 - Не является автором материалов. Исключительное право сохранено за автором текста.
Если вы не хотите, чтобы данный материал был у нас на сайте, перейдите по ссылке: Нарушение авторских прав. Мы поможем в написании вашей работы!