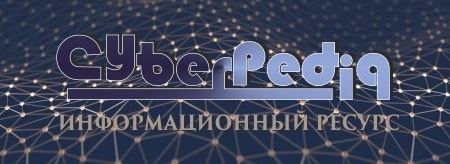
Папиллярные узоры пальцев рук - маркер спортивных способностей: дерматоглифические признаки формируются на 3-5 месяце беременности, не изменяются в течение жизни...
Археология об основании Рима: Новые раскопки проясняют и такой острый дискуссионный вопрос, как дата самого возникновения Рима...
Топ:
Процедура выполнения команд. Рабочий цикл процессора: Функционирование процессора в основном состоит из повторяющихся рабочих циклов, каждый из которых соответствует...
Выпускная квалификационная работа: Основная часть ВКР, как правило, состоит из двух-трех глав, каждая из которых, в свою очередь...
Интересное:
Аура как энергетическое поле: многослойную ауру человека можно представить себе подобным...
Мероприятия для защиты от морозного пучения грунтов: Инженерная защита от морозного (криогенного) пучения грунтов необходима для легких малоэтажных зданий и других сооружений...
Отражение на счетах бухгалтерского учета процесса приобретения: Процесс заготовления представляет систему экономических событий, включающих приобретение организацией у поставщиков сырья...
Дисциплины:
![]() |
![]() |
5.00
из
|
Заказать работу |
|
|
Анализ исходных данных
Плита нижняя представляет собой базовую деталь, на которую устанавливают другие детали и сборочные единицы, точность относительного положения которых должна обеспечиваться как в статике, так и в процессе работы пневмо-гидравлического усилителя под нагрузкой. В соответствии с этим плита нижняя должна иметь требуемую точность и обладать необходимой жесткостью.
Конструктивное исполнение плиты нижней, ее материал и необходимые параметры точности определяем исходя из служебного назначения детали, требований к работе механизма и условиях его эксплуатации. При этом учитываем также технологические факторы, связанные с возможностью получения требуемой конфигурации заготовки, возможностями обработки резанием и удобства сборки, которую начинают с базовой корпусной детали.
Анализ технологичности конструкции обеспечивает улучшение технико-экономических показателей разрабатываемого технологического процесса.
Конструкция детали позволяет одновременно обрабатывать несколько поверхностей. Например, сверление инструментальной головкой трех отверстий с одной стороны и шести отверстий с другой стороны. Это позволяет снизить время обработки детали и применять высокопроизводительные режимы обработки.
Для повышения технологичности используем стандартные, унифицированные элементы: фаски, отверстия под болты. Конструкция детали не имеет труднодоступных мест для обработки. Размеры и форма поверхностей позволяют вести обработку стандартным режущим инструментом.
Одним из критериев технологичности детали является совмещение технологической и измерительной баз. Такие базовые поверхности должны обладать достаточно высокой точностью и низкой шероховатостью.
|
Поверхности различного назначения разделены по точности и шероховатости. Точность и шероховатость обрабатываемых поверхностей соответствуют стандартам.
В целом обработку плиты нижней можно вести на оборудовании нормальной точности. Конструкция детали позволяет использовать стандартные измерительные инструменты для контроля.
Жесткость детали достаточна и не ограничивает режимы резания.
Из всех вышеперечисленных критериев можно сделать вывод, что деталь достаточно технологична и не требует внесения изменений.
Выбор способа сварки
Сталь 15ХСНД можно сваривать практически любыми способами дуговой сварки. Рассмотрим основные способы сварки.
1. Дуговая сварка покрытыми электродами. Сварку можно вести во всех
пространственных положениях. При сварке покрытыми электродами металл шва формируется главным образом за счет вводимого в шов электродного металла и поэтому производительность процесса определяется количеством электродного металла, переходящего в шов за определенный интервал времени. Достаточно большой процент расплавленного электродного металла теряется на разбрызгивание и испарение (5-10%), но если учесть, что при сварке покрытыми электродами до 15-20%о длины стержня электрода теряется в виде не используемых отходов-огарков, то общие потери на угар, разбрызгивание и огарку составят до 30% стержня. Ручную сварку целесообразно применять для коротких швов, расположенных в различных пространственных положениях и при мелкосерийном производстве. Она рациональна для выполнения прихваток при сборке конструкций под сварку и исправления дефектных участков шва небольшой протяженности.
2. Сварка под слоем флюса. При сварке под слоем флюса производительность процесса повышается в 6-12 раз, что даже при коэффициенте использования сварочной установки 0,5 в 3-6 раз превосходит производительность ручной сварки покрытыми электродами. При сварке под слоем флюса обеспечивается высокое и стабильное качество сварки. Это достигается за счет надежной защиты металла шва от воздействия кислорода и азота воздуха, однородности металла шва и сохранения постоянства его размеров. В результате обеспечивается меньшая вероятность образования непроваров и других дефектов формирования шва, отсутствие перерывов в процессе сварки, вызванных сменой электродов. За счет уменьшения доли электродного металла в металле шва в среднем с 30% при сварке покрытыми электродами до 70% при сварке под флюсом и уменьшения потерь на угар, разбрызгивание и огарки, снижается расход электродного металла и электроэнергии. Отпадает необходимость в защите глаз и лица рабочего и несколько уменьшается количество выделяемых вредных газов, что улучшает условия труда.
|
Автоматическую и полуавтоматическую сварку под слоем флюса применяют в заводских и монтажных условиях для выполнения швов, расположенных в нижнем положении. Автоматическую сварку целесообразно применять для прямолинейных швов большой протяженности, а полуавтоматическую сварку можно применять как для криволинейных, так и для прямолинейных швов относительно небольшой протяженности.
3.Сварка в защитных газах. Эта сварка обеспечивает достаточно надежную изоляцию сварочной ванны при работе в заводских условиях, но при работе на открытом пространстве потоки воздуха могут нарушить газовую защиту.
Применение автоматической сварки в среде защитных газов ограничено, так как сварка сопровождается интенсивным разбрызгиванием металла, которое вызывает засорение аппаратуры и свариваемых деталей.
Полуавтоматическую сварку в защитных газах можно выполнять в различных пространственных положениях. Этот способ сварки характеризуется большой производительностью, лучшими условиями труда и меньшими требованиями к квалификации рабочих, посравнению с ручной дуговой сваркой покрытыми электродами. Перед полуавтоматической сваркой под флюсом ее преимущество заключается в возможности визуального наблюдения за положением электрода, отсутствии операции по удержанию и удалению флюса.
Учитывая все достоинства и недостатки этих способов сварки, толщину свариваемых деталей, тип соединения, длины свариваемых швов и их пространственное положение можно сделать следующие выводы:
|
• Наиболее выгодным является сварка под слоем флюса.
Под флюсом будем вести сварку всех швов.
• Применим сварку в углекислом газе при постановке прихваток.
Выбор сварочных материалов
Для сварки под флюсом стали 15ХСНД, назначаем флюс АН-348-АМ и проволоку Св-08-АА. Данное сочетание плавленого высококремнистого и высокомарганцовистого флюса с обычной низкоуглеродистой марганцовистой проволокой, лучше, чем сочетание плавленого высококремнистого безмарганцовистого флюса с низкоуглеродистой марганцовистой проволокой. Положительным свойством высококремнистых марганцовистых флюсов является высокая стойкость сварных швов против образования кристаллизационных трещин. Это обусловлено малым переходом серы из флюсов данного типа в металл шва и сравнительно высоким выгоранием углерода из сварочной ванны.
При сварке под высококремнистыми марганцовистыми флюсами пористость сварных швов меньше. К высококремнистым марганцовистым флюсам относятся флюсы марок АН-348-А, АН-348-АМ, ОСЦ-45, ОСЦ-45М.
Флюс АН-348-АМ отличается от флюса ОСЦ-45М содержанием CaF2. Большое содержание CaF2 во флюсе повышает стойкость металла шва против образования пор. Более высокое содержание CaF2 во флюсе ОСЦ-45М, в сравнении с флюсом АН-348-АМ, вызывает более интенсивное выделение в атмосферу дуги фтористых соединений, предупреждающие образование пор от водорода. Вместе с тем, ухудшается устойчивость горения дуги и гигиенические условия труда.
Таблица 2.2 - Химический состав флюса АН-348-АМ (по ГОСТ 9087-69).
SiO2 | MnO | CaO | MgO | Al2O3 | CaF2 | Fe203 | S | P |
41-44 | 34-38 | 6,5 | 5-7,5 | 4,5 | 3,5-4,5 | 2,0 | 0,15 | 0,12 |
Таблица 2.3 - Химический состав проволоки Св-08-АА (по ГОСТ 2246-70).
С | Мn | Si | Сr | Ni | S | Р |
≤0,1 | 0,35- 0,6 | ≤0,030 | ≤0,10 | ≤0,25 | ≤0,02 | ≤0,02 |
Для сварки в СО2, для обеспечения необходимых механических свойств металла шва и высокой стойкости его против кристаллизационных трещин и пор, при сварке низкоуглеродистых сталей применяют сварочную проволоку Св-08Г2С, легированную Si и Мn.
|
Таблица 2.4 - Химический состав проволоки Св-08Г2С (по ГОСТ 2246-70).
С | Мn | Si | Сr | Ni | S | Р |
≤0,05-0,11 | 1,8-2,10 | ≤0,7-0,95 | ≤0,20 | ≤0,25 | ≤0,025 | ≤0,03 |
Углекислый газ (двуокись углерода), оксид C(IV), высший оксид С, может находится в газообразном, сжиженном, твёрдом состояниях. Плотность СО2 зависит от давления, температуры и агрегатного состояния, в котором он находится. При атмосферном давлении и температуре t = -78,5 °С, минуя жидкое состояние, превращается в белую массу- «сухой лёд».
СО2 - широко распространённый в природе бесцветный газ, имеет слабый кисловатый запах и вкус, хорошо растворяется в воде. В воздухе содержание углекислого газа равно 0,03%. При t=0 °C и давлении в 101,3 кПа плотность углекислоты ρ = 0,001976 г/см и по отношению к воздуху составляет 1,524.
Удельная масса жидкого газа значительно изменяется с температурой, поэтому количество СО2 определяют и продают по массе.
Жидкий СО2 превращается в газ при подводе к нему тепла. При нормальных условиях (t=0°C, p=101,3 кПа) при испарении 1 кг жидкой углекислоты образуется 509 литров газа. СО2 термически устойчив, диссоциирует на СО и О при температуре выше 2000°С. Поскольку для получения швов высокого качества необходим углекислый газ высокой чистоты, то для сварки используют СО2 высшего и первого сортов. Состав двуокиси углерода представлен в табл. 2.5. Согласно ГОСТ 8050-85, СО2 не должнен содержать сероводород, кислоты, органические соединения (спирты, эфиры, альдегиды, органические кислоты), аммиак, этанол амины, ароматические углеводороды.
СО2 не токсичный, не взрывоопасный. Однако, при концентрации более 5% (92 г/куб.м.) газ оказывает вредное влияние на здоровье человека, так как он тяжелее воздуха в 1,5 раза и может накапливаться в слабо проветриваемых помещениях у пола и в приямках, а также во внутренних объёмах оборудования для получения, хранения и перевозки газообразной, жидкой, твёрдой СО2. При этом снижается объёмная доля кислорода в воздухе, что может вызвать явление кислородной недостаточности и удушья. Предельно допустимая концентрация СО2 в воздухе рабочей зоны 9,2 г/куб.м., (0,5 %).
Таблица 2.5 - Состав двуокиси углерода по ГОСТ 8050-85.
Показатель | Сорт высший | Сорт первый |
1. Объёмная доля СО2,%, не менее | 99,8 | 99,5 |
2. Объёмная доля СО | Нет | Нет |
3. Массовая концентрация минеральных масел и мех. примесей, мг/кг | 0,1 | 0,1 |
4. Массовая доля воды | Нет | Нет |
5. Массовая концентрация водяных паров при н.у. | 0,037 | 0,184 |
|
Выбранные сварочные материалы обеспечивают качество шва, его механические свойства и стойкость против образования трещин.
Расчет режимов сварки
К параметрам режима сварки относятся сила сварочного тока, напряжение, скорость перемещения электрода вдоль шва (скорость сварки), род тока, полярность и др.
Диаметр электрода выбирается в зависимости от толщины свариваемого металла, типа сварного соединения и положения шва в пространстве.
При выборе диаметра электрода для сварки можно использовать следующие ориентировочные данные:
В многослойных стыковых швах первый слой выполняют электродом 3–4 мм, последующие слои выполняют электродами большего диаметра.
Сварку в вертикальном положении проводят с применением электродов диаметром не более 5 мм. Потолочные швы выполняют электродами диаметром до 4 мм.
При наплавке изношенной поверхности должна быть компенсирована толщина изношенного слоя плюс 1–1,5 мм на обработку поверхности после наплавки.
Сила сварочного тока, А, рассчитывается по формуле:
где К – коэффициент, равный 25–60 А/мм; dЭ – диаметр электрода, мм.
Коэффициент К в зависимости от диаметра электрода dЭ принимается равным по следующей таблице:
Силу сварочного тока, рассчитанную по этой формуле, следует откорректировать с учетом толщины свариваемых элементов, типа соединения и положения шва в пространстве.
Если толщина металла S ≥ 3dЭ, то значениеIСВ следует увеличить на 10–15%. Если же S ≤ 1,5dЭ, то сварочный ток уменьшают на 10–15%. При сварке угловых швов и наплавке, значение тока должно быть повышено на 10–15%. При сварке в вертикальном или потолочном положении значение сварочного тока должно быть уменьшено на 10–15%.
Для большинства марок электродов, используемых при сварке углеродистых и легированных конструкционных сталей, напряжение дуги UД= 22 ÷ 28 В.
Расчет скорости сварки, м/ч, производится по формуле:
где α Н – коэффициент наплавки, г/А ч (принимают из характеристики выбранного электрода по табл. 9 приложения); FШВ – площадь поперечного сечения шва при однопроходной сварке (или одного слоя валика при многослойном шве), см2; ρ – плотность металла электрода, г/см3 (для стали ρ =7,8 г/см3).
Масса наплавленного металла, г, для ручной дуговой сварки рассчитывается по формуле:
где l – длина шва, см; ρ – плотность наплавленного металла (для стали ρ =7,8 г/см3).
Расчет массы наплавленного металла, г, при ручной дуговой наплавке производится по формуле:
где FНП – площадь наплавляемой поверхности, см2; hН – требуемая высота наплавляемого слоя, см.
Время горения дуги, ч, (основное время) определяется по формуле:
Полное время сварки (наплавки), ч, приближенно определяется по формуле:
где tO – время горения дуги (основное время),ч; kП – коэффициент использования сварочного поста, который принимается для ручной сварки 0,5 ÷ 0,55.
Расход электродов, кг, для ручной дуговой сварки (наплавки) определяется по формуле:
где kЭ – коэффициент, учитывающий расход электродов на 1 кг наплавленного металла (табл. 9 приложения).
Расход электроэнергии, кВт ч, определяется по формуле:
где UД– напряжение дуги, В; η – КПД источника питания сварочной дуги; WO–мощность, расходуемая источником питания сварочной дуги при холостом ходе, кВт; Т– полное время сварки или наплавки, ч.
Значения η источника питания сварочной дуги и WO можно принять по таблице:
Сварка является одним из ведущих технологических процессов обработки металлов. Сварка широко применяется в основных отраслях производства, потребляющих металлопрокат, т.к. резко сокращается расход металла, сроки выполнения работ и трудоёмкость производственных процессов. Выпуск сварных конструкций и уровень механизации сварных процессов постоянно повышается. Успехи в области автоматизации сварочных процессов позволили коренным образом изменить технологию изготовления важных хозяйственных объектов, таких как доменные печи, турбины, химическое оборудование.
Сварочная техника и технология занимают одно из ведущих мест в современном производстве. Свариваются корпуса гигантских супертанкеров и сетчатка человеческого глаза, миниатюрные детали полупроводниковых приборов и кости человека при хирургических операциях. Многие конструкции современных машин и сооружений, например космические ракеты, подводные лодки, газо- и нефтепроводы, изготовить без помощи сварки невозможно. Развитие техники предъявляет все новые требования к способам производства и к оборудованию, которое используется в процессе сварки.
Список литературы
1. Справочник технолога машиностроителя в 2-х т. Т2 / Под редакцией А. Г. Косиловой и Мещерикова. – М.: Машиностроение, 1985 г. 496с.
2. Анурьев В. И. Справочник конструктора-машиностроителя: В 3-х т. Т1. – М.: Машиностроение, 1980 г. – 728с.
3. Лекции по «Технологии машиностроения».
4. Горбацевич А. Ф. Курсовое проектирование по технологии машиностроения: [Учебное пособие для ВУЗов] – 4-е издание, перераб. и доп. – Мн.: Высшая школа, 1983 г. – 256с.
5. Справочник технолога машиностроителя в 2-х т. Т1 / Под редакцией А. Г. Косиловой и Мещерикова. – М.: Машиностроение, 1985 г. 656с.
6. М. П. Новиков Основы технологии сборки машин и механизмов – 5-е издание, перераб. М.: Машиностроение, 1980 г. – 591с.
7. Методические указания «Разработка технологических процессов обработки корпусной детали в условиях массового производства» / А. В. Михайлов, ТолПИ, 1997 г. – 44 с.
8. Методические указания «Разработка технологических процессов сборки изделия» / В. А. Булычев, ТолПИ, 2000 г. – 21 с.
9. Методические указания к практическим занятиям и курсовому проектированию по «Технологии отрасли» «Расчет радиальных сборочных размерных цепей. Синхронизация операций сборки по такту выпуска» / А. В. Михайлов, В. А. Булычев ТолПИ, 1999 г. – 32 с.
10. Методические указания «Обработка на многошпиндельных токарных станках» / А. В. Михайлов, ТолПИ, 1996 г. – 24 с.
Анализ исходных данных
Плита нижняя представляет собой базовую деталь, на которую устанавливают другие детали и сборочные единицы, точность относительного положения которых должна обеспечиваться как в статике, так и в процессе работы пневмо-гидравлического усилителя под нагрузкой. В соответствии с этим плита нижняя должна иметь требуемую точность и обладать необходимой жесткостью.
Конструктивное исполнение плиты нижней, ее материал и необходимые параметры точности определяем исходя из служебного назначения детали, требований к работе механизма и условиях его эксплуатации. При этом учитываем также технологические факторы, связанные с возможностью получения требуемой конфигурации заготовки, возможностями обработки резанием и удобства сборки, которую начинают с базовой корпусной детали.
Анализ технологичности конструкции обеспечивает улучшение технико-экономических показателей разрабатываемого технологического процесса.
Конструкция детали позволяет одновременно обрабатывать несколько поверхностей. Например, сверление инструментальной головкой трех отверстий с одной стороны и шести отверстий с другой стороны. Это позволяет снизить время обработки детали и применять высокопроизводительные режимы обработки.
Для повышения технологичности используем стандартные, унифицированные элементы: фаски, отверстия под болты. Конструкция детали не имеет труднодоступных мест для обработки. Размеры и форма поверхностей позволяют вести обработку стандартным режущим инструментом.
Одним из критериев технологичности детали является совмещение технологической и измерительной баз. Такие базовые поверхности должны обладать достаточно высокой точностью и низкой шероховатостью.
Поверхности различного назначения разделены по точности и шероховатости. Точность и шероховатость обрабатываемых поверхностей соответствуют стандартам.
В целом обработку плиты нижней можно вести на оборудовании нормальной точности. Конструкция детали позволяет использовать стандартные измерительные инструменты для контроля.
Жесткость детали достаточна и не ограничивает режимы резания.
Из всех вышеперечисленных критериев можно сделать вывод, что деталь достаточно технологична и не требует внесения изменений.
Характеристика основного металла
Материалом для изготовления данного изделия является низколегированная низкоуглеродистая конструкционная сталь 15ХСНД.
Таблица 2.1-Химический состав стали 15ХСНД.
С | Si | Мn | Ni | Сu | Сr |
0,12 -0,18% | 0,4 - 0,7% | 0,4 - 0,7% | 0,3 - 0,6% | 0,2 - 0,4% | 0,6 - 0,9% |
Механические свойства:
• Предел текучести σт= 350 МПа.
• Предел прочности при растяжении σр = 500 МПа.
• Относительное удлинение после разрыва δ = 21%.
• Ударная вязкость при -40°С ан-40 = 30 Дж/см. Сталь 15ХСНД - сваривается без ограничений РДС, АДС под флюсом, в газовой защите и ЭШС.
Важное требование при сварке - обеспечение равнопрочности сварного соединения с основным металлом и отсутствие дефектов в сварном соединении. Технология должна обеспечивать максимальную производительность и экономичность сварки при требуемой надежности конструкции.
Химический состав металла шва при сварке рассматриваемой стали незначительно отличается от состава основного металла. Возможное снижение прочности металла шва, вызванное уменьшением содержания в нем углерода, компенсируется легированием металла шва через проволоку, покрытие или флюс, марганцем и кремнием. Таким образом, химический состав металла шва зависит от доли участия основного и присадочного металла в образовании металла шва и взаимодействии между металлом, шлаком и газовой фазой.
Повышенные скорости охлаждения металла шва также способствуют повышению его прочности, однако, при этом снижаются его пластические свойства и ударная вязкость.
Обеспечение равнопрочности металла шва при дуговых способах сварки обычно не вызывает затруднений, но требует применения определенных технологических приемов. Протяженность участков зоны термического влияния, где произошли заметные изменения свойств основного металла под действием термического цикла сварки, зависит от способа и режима сварки, состава и толщины металла. Повышение погонной энергии сварки сопровождается расширением разупрочненной зоны и снижением твердости металла. Это вызвано увеличением объема металла, подвергшегося высокому сварочному нагреву, и замедлением темпа охлаждения. Кроме того, повышение погонной энергии уменьшает скорость охлаждения, что снижает твердость околошовной зоны - вероятное место образования холодных трещин при сварке низколегированных сталей.
В процессе изготовления конструкции на заготовительных операциях и при сварке, в зонах, удаленных от высокотемпературной области, возникает холодная пластическая деформация. Попадая при наложении последующих швов под сварочный нагрев до температур около 300°С, эти зоны становятся участками деформационного старения. Высокий отпуск при 600-650°С в этих случаях служит эффективным средством восстановления свойств металла. Высокий отпуск применяют для снижения сварочных напряжений. Термообработка, кроме закалки сварных соединений, в которых шов и околошовная зона охлаждались с повышенными скоростями, приводившими к образованию на некоторых участках неравновесных закалочных структур, приводит к снижению прочностных и повышению пластических свойств металла на этих участках.
Швы, сваренные на низкоуглеродистых сталях, обладают удовлетворительной стойкостью против образования кристаллизационных трещин. Это обусловлено низким содержанием в них углерода.
Легирующие добавки в низколегированных сталях могут повысить вероятность образования в них кристаллизационных трещин.
Сталь 15ХСНД хорошо сваривается практически всеми способами сварки плавлением.
Влияние химического состава основного металла углеродистых и
низколегированных сталей на сопротивляемость образованию трещин выражается эквивалентом углерода Сэ. Рекомендована эмпирическая формула для приближенной оценки свариваемости стали:
Cэ = C + Mn / 6 + Cr / 5 + Ni / l0 + Cu / 15 + Si / 24
Сэ = 0,12+0,4/6+0,6/5+0,3/10+0,2/15+0,4/24 = 0,47%
Свариваемость стали 15ХСНД: без ограничений.
Выбор способа сварки
Сталь 15ХСНД можно сваривать практически любыми способами дуговой сварки. Рассмотрим основные способы сварки.
1. Дуговая сварка покрытыми электродами. Сварку можно вести во всех
пространственных положениях. При сварке покрытыми электродами металл шва формируется главным образом за счет вводимого в шов электродного металла и поэтому производительность процесса определяется количеством электродного металла, переходящего в шов за определенный интервал времени. Достаточно большой процент расплавленного электродного металла теряется на разбрызгивание и испарение (5-10%), но если учесть, что при сварке покрытыми электродами до 15-20%о длины стержня электрода теряется в виде не используемых отходов-огарков, то общие потери на угар, разбрызгивание и огарку составят до 30% стержня. Ручную сварку целесообразно применять для коротких швов, расположенных в различных пространственных положениях и при мелкосерийном производстве. Она рациональна для выполнения прихваток при сборке конструкций под сварку и исправления дефектных участков шва небольшой протяженности.
2. Сварка под слоем флюса. При сварке под слоем флюса производительность процесса повышается в 6-12 раз, что даже при коэффициенте использования сварочной установки 0,5 в 3-6 раз превосходит производительность ручной сварки покрытыми электродами. При сварке под слоем флюса обеспечивается высокое и стабильное качество сварки. Это достигается за счет надежной защиты металла шва от воздействия кислорода и азота воздуха, однородности металла шва и сохранения постоянства его размеров. В результате обеспечивается меньшая вероятность образования непроваров и других дефектов формирования шва, отсутствие перерывов в процессе сварки, вызванных сменой электродов. За счет уменьшения доли электродного металла в металле шва в среднем с 30% при сварке покрытыми электродами до 70% при сварке под флюсом и уменьшения потерь на угар, разбрызгивание и огарки, снижается расход электродного металла и электроэнергии. Отпадает необходимость в защите глаз и лица рабочего и несколько уменьшается количество выделяемых вредных газов, что улучшает условия труда.
Автоматическую и полуавтоматическую сварку под слоем флюса применяют в заводских и монтажных условиях для выполнения швов, расположенных в нижнем положении. Автоматическую сварку целесообразно применять для прямолинейных швов большой протяженности, а полуавтоматическую сварку можно применять как для криволинейных, так и для прямолинейных швов относительно небольшой протяженности.
3.Сварка в защитных газах. Эта сварка обеспечивает достаточно надежную изоляцию сварочной ванны при работе в заводских условиях, но при работе на открытом пространстве потоки воздуха могут нарушить газовую защиту.
Применение автоматической сварки в среде защитных газов ограничено, так как сварка сопровождается интенсивным разбрызгиванием металла, которое вызывает засорение аппаратуры и свариваемых деталей.
Полуавтоматическую сварку в защитных газах можно выполнять в различных пространственных положениях. Этот способ сварки характеризуется большой производительностью, лучшими условиями труда и меньшими требованиями к квалификации рабочих, посравнению с ручной дуговой сваркой покрытыми электродами. Перед полуавтоматической сваркой под флюсом ее преимущество заключается в возможности визуального наблюдения за положением электрода, отсутствии операции по удержанию и удалению флюса.
Учитывая все достоинства и недостатки этих способов сварки, толщину свариваемых деталей, тип соединения, длины свариваемых швов и их пространственное положение можно сделать следующие выводы:
• Наиболее выгодным является сварка под слоем флюса.
Под флюсом будем вести сварку всех швов.
• Применим сварку в углекислом газе при постановке прихваток.
Выбор сварочных материалов
Для сварки под флюсом стали 15ХСНД, назначаем флюс АН-348-АМ и проволоку Св-08-АА. Данное сочетание плавленого высококремнистого и высокомарганцовистого флюса с обычной низкоуглеродистой марганцовистой проволокой, лучше, чем сочетание плавленого высококремнистого безмарганцовистого флюса с низкоуглеродистой марганцовистой проволокой. Положительным свойством высококремнистых марганцовистых флюсов является высокая стойкость сварных швов против образования кристаллизационных трещин. Это обусловлено малым переходом серы из флюсов данного типа в металл шва и сравнительно высоким выгоранием углерода из сварочной ванны.
При сварке под высококремнистыми марганцовистыми флюсами пористость сварных швов меньше. К высококремнистым марганцовистым флюсам относятся флюсы марок АН-348-А, АН-348-АМ, ОСЦ-45, ОСЦ-45М.
Флюс АН-348-АМ отличается от флюса ОСЦ-45М содержанием CaF2. Большое содержание CaF2 во флюсе повышает стойкость металла шва против образования пор. Более высокое содержание CaF2 во флюсе ОСЦ-45М, в сравнении с флюсом АН-348-АМ, вызывает более интенсивное выделение в атмосферу дуги фтористых соединений, предупреждающие образование пор от водорода. Вместе с тем, ухудшается устойчивость горения дуги и гигиенические условия труда.
Таблица 2.2 - Химический состав флюса АН-348-АМ (по ГОСТ 9087-69).
SiO2 | MnO | CaO | MgO | Al2O3 | CaF2 | Fe203 | S | P |
41-44 | 34-38 | 6,5 | 5-7,5 | 4,5 | 3,5-4,5 | 2,0 | 0,15 | 0,12 |
Таблица 2.3 - Химический состав проволоки Св-08-АА (по ГОСТ 2246-70).
С | Мn | Si | Сr | Ni | S | Р |
≤0,1 | 0,35- 0,6 | ≤0,030 | ≤0,10 | ≤0,25 | ≤0,02 | ≤0,02 |
Для сварки в СО2, для обеспечения необходимых механических свойств металла шва и высокой стойкости его против кристаллизационных трещин и пор, при сварке низкоуглеродистых сталей применяют сварочную проволоку Св-08Г2С, легированную Si и Мn.
Таблица 2.4 - Химический состав проволоки Св-08Г2С (по ГОСТ 2246-70).
С | Мn | Si | Сr | Ni | S | Р |
≤0,05-0,11 | 1,8-2,10 | ≤0,7-0,95 | ≤0,20 | ≤0,25 | ≤0,025 | ≤0,03 |
Углекислый газ (двуокись углерода), оксид C(IV), высший оксид С, может находится в газообразном, сжиженном, твёрдом состояниях. Плотность СО2 зависит от давления, температуры и агрегатного состояния, в котором он находится. При атмосферном давлении и температуре t = -78,5 °С, минуя жидкое состояние, превращается в белую массу- «сухой лёд».
СО2 - широко распространённый в природе бесцветный газ, имеет слабый кисловатый запах и вкус, хорошо растворяется в воде. В воздухе содержание углекислого газа равно 0,03%. При t=0 °C и давлении в 101,3 кПа плотность углекислоты ρ = 0,001976 г/см и по отношению к воздуху составляет 1,524.
Удельная масса жидкого газа значительно изменяется с температурой, поэтому количество СО2 определяют и продают по массе.
Жидкий СО2 превращается в газ при подводе к нему тепла. При нормальных условиях (t=0°C, p=101,3 кПа) при испарении 1 кг жидкой углекислоты образуется 509 литров газа. СО2 термически устойчив, диссоциирует на СО и О при температуре выше 2000°С. Поскольку для получения швов высокого качества необходим углекислый газ высокой чистоты, то для сварки используют СО2 высшего и первого сортов. Состав двуокиси углерода представлен в табл. 2.5. Согласно ГОСТ 8050-85, СО2 не должнен содержать сероводород, кислоты, органические соединения (спирты, эфиры, альдегиды, органические кислоты), аммиак, этанол амины, ароматические углеводороды.
СО2 не токсичный, не взрывоопасный. Однако, при концентрации более 5% (92 г/куб.м.) газ оказывает вредное влияние на здоровье человека, так как он тяжелее воздуха в 1,5 раза и может накапливаться в слабо проветриваемых помещениях у пола и в приямках, а также во внутренних объёмах оборудования для получения, хранения и перевозки газообразной, жидкой, твёрдой СО2. При этом снижается объёмная доля кислорода в воздухе, что может вызвать явление кислородной недостаточности и удушья. Предельно допустимая концентрация СО2 в воздухе рабочей зоны 9,2 г/куб.м., (0,5 %).
Таблица 2.5 - Состав двуокиси углерода по ГОСТ 8050-85.
Показатель | Сорт высший | Сорт первый |
1. Объёмная доля СО2,%, не менее | 99,8 | 99,5 |
2. Объёмная доля СО | Нет | Нет |
3. Массовая концентрация минеральных масел и мех. примесей, мг/кг | 0,1 | 0,1 |
4. Массовая доля воды | Нет | Нет |
5. Массовая концентрация водяных паров при н.у. | 0,037 | 0,184 |
Выбранные сварочные материалы обеспечивают качество шва, его механические свойства и стойкость против образования трещин.
Расчет режимов сварки
К параметрам режима сварки относятся сила сварочного тока, напряжение, скорость перемещения электрода вдоль шва (скорость сварки), род тока, полярность и др.
Диаметр электрода выбирается в зависимости от толщины свариваемого металла, типа сварного соединения и положения шва в пространстве.
При выборе диаметра электрода для сварки можно использовать следующие ориентировочные данные:
В многослойных стыковых швах первый слой выполняют электродом 3–4 мм, последующие слои выполняют электродами большего диаметра.
Сварку в вертикальном положении проводят с применением электродов диаметром не более 5 мм. Потолочные швы выполняют электродами диаметром до 4 мм.
При наплавке изношенной поверхности должна быть компенсирована толщина изношенного слоя плюс 1–1,5 мм на обработку поверхности после наплавки.
Сила сварочного тока, А, рассчитывается по формуле:
где К – коэффициент, равный 25–60 А/мм; dЭ – диаметр электрода, мм.
Коэффициент К в зависимости от диаметра электрода dЭ принимается равным по следующей таблице:
Силу сварочного тока, рассчитанну
|
|
Кормораздатчик мобильный электрифицированный: схема и процесс работы устройства...
Особенности сооружения опор в сложных условиях: Сооружение ВЛ в районах с суровыми климатическими и тяжелыми геологическими условиями...
Историки об Елизавете Петровне: Елизавета попала между двумя встречными культурными течениями, воспитывалась среди новых европейских веяний и преданий...
Археология об основании Рима: Новые раскопки проясняют и такой острый дискуссионный вопрос, как дата самого возникновения Рима...
© cyberpedia.su 2017-2024 - Не является автором материалов. Исключительное право сохранено за автором текста.
Если вы не хотите, чтобы данный материал был у нас на сайте, перейдите по ссылке: Нарушение авторских прав. Мы поможем в написании вашей работы!