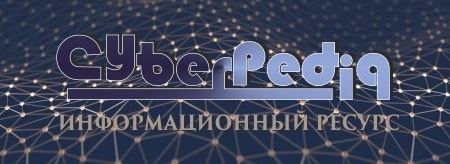
Двойное оплодотворение у цветковых растений: Оплодотворение - это процесс слияния мужской и женской половых клеток с образованием зиготы...
История развития хранилищ для нефти: Первые склады нефти появились в XVII веке. Они представляли собой землянные ямы-амбара глубиной 4…5 м...
Топ:
Характеристика АТП и сварочно-жестяницкого участка: Транспорт в настоящее время является одной из важнейших отраслей народного...
Когда производится ограждение поезда, остановившегося на перегоне: Во всех случаях немедленно должно быть ограждено место препятствия для движения поездов на смежном пути двухпутного...
Техника безопасности при работе на пароконвектомате: К обслуживанию пароконвектомата допускаются лица, прошедшие технический минимум по эксплуатации оборудования...
Интересное:
Что нужно делать при лейкемии: Прежде всего, необходимо выяснить, не страдаете ли вы каким-либо душевным недугом...
Влияние предпринимательской среды на эффективное функционирование предприятия: Предпринимательская среда – это совокупность внешних и внутренних факторов, оказывающих влияние на функционирование фирмы...
Искусственное повышение поверхности территории: Варианты искусственного повышения поверхности территории необходимо выбирать на основе анализа следующих характеристик защищаемой территории...
Дисциплины:
![]() |
![]() |
5.00
из
|
Заказать работу |
|
|
В таблицах 3.3.1, 3.3.2 приведены нормы расхода электроэнергии в пищевой промышленности и основные направления снижения расхода энергоносителей на предприятиях пищевой промышленности.
Таблица 3.3.1
Удельные расходы электроэнергии на производство в пищевой
промышленности
Вид продукции | Ед. изм. | Удельный расход, кВт·ч/ед. прод. (по различ- ным источникам информации) | ||
Мука | т | 5188 | 5060 | 5070 |
Крупа | т | 3032 | 3040 | 2530 |
Сушка зерна | т | 1013 | | |
Сахарный песок | т | 2430 | 2530 | 2530 |
Мясо и субпродукты | т | 5560 | 5560 | 50 |
Колбасные изделия | т | 7490 | 7590 | 6580 |
Консервы мясные | 1000 усл. банок | 2025 | 2326 | 50 |
Растительное масло | т | 132184 | 130180 | 175 |
Хлебобулочные изделия | т | | | 2040 |
Таблица 3.3.2
Удельные нормы расхода холода, пара, воды и электроэнергии на выпуск молочной продукции
Вид продукции | Норма расхода (на 1 т готовой продукции) | ||||
Холода, тыс. стандартных ккал | Пара, т/ч |
Воды, м3 |
Эл/эн, кВт·ч | ||
На техно- логические нужды | На венти- ляцию | ||||
творог | 342 | 1,4 | 2,5 | 53 | 930 |
молоко | 22 | 0,1 | 0,1 | 4 | 84 |
простокваша | 107 | 0,4 | 0,35 | 15 | 226 |
кефир | 69 | 0,3 | 0,35 | 11 | 125 |
ряженка | 110 | 0,8 | 0,5 | 19 | 193 |
сливки | 76 | 0,5 | 0,5 | 29 | 142 |
сметана | 113 | 1,0 | 0,73 | 27 | 237 |
сырки | 265 | 1,7 | 2,3 | 33 | 696 |
сыр | 750 | 2,5 | 3,3 | 79 | 1488 |
Масло сливоч- ное | 326 | 2,6 | 0,5 | 53 | 667 |
Энергосбережение в нефтеперерабатывающей промыш- ленности
В таблицах 3.3.3, 3.3.4 приведены удельные расходы топлива, теп- ловой энергии и электрической энергии по некоторым установкам и вы- пускаемой продукции предприятий нефтепереработки.
Таблица 3.3.3
Удельные расходы топлива и тепловой энергии по некоторым ус- тановкам предприятий нефтепереработки
|
Наименование установки | Удельный расход топлива, кг у.т./т | Удельный расход теплоэнергии, МДж/т |
Первичная переработка | 30,3 | 82,8 |
Гидрокрекинг | 173,2 | 81,3 |
Термический крекинг | 48,4 | 96,4 |
Каталитический крекинг | 54,6 | 207 |
Каталитический крекинг на облагораживание | 94,7 | 136 |
Производство масел | 212,0 | 2763 |
Коксование | 75.6 | 222 |
Гидроочистка топлива | 25,0 | 17,5 |
Таблица 3.3.4 Удельные расходы электроэнергии по некоторым установкам предприятий нефтепереработки (в среднем по отрасли)
Наименование процесса | Удельный расход, кВт·ч/т | ||
По различным источникам инфор- мации | |||
Переработка нефти | 31,3 | 29,5 | |
Первичная переработка нефти | 14,5 | 13,8 | |
Термический крекинг нефти | 14,8 | 13,9 | 1115 |
Каталитический крекинг нефти | 59,6 | 60 | 60 |
Каталитический риформинг | 83,4 | 80 | |
Производство катализатора | 2368 | 2100 | |
Пиролиз нефти | 20,5 | 19 | |
Коксование | 30,4 | 27 | 3040 |
Производство масел | 284 | 295 | |
– использование низкопотенциальной сбросной теплоты для теп- лоснабжения (дает экономию топлива до 20 %).
Основными способами снижения расходов энергоресурсов в неф- тепереработке являются:
– применение ЭВМ для управления технологическими процессами;
– повышение эффективности утилизации сбросной теплоты;
– увеличение КПД печей;
– увеличение КПД дистилляционной установки путем использо- вания дополнительных стадий;
– усовершенствование тепловых насосов.
Энергосбережение при работе тепломассообменного обору-
Дования
Выпарные установки
Выпаривание представляет собой термический процесс кипения раствора с выделением паров растворителей в практически чистом виде (если не считаться с уносом жидкости); при этом растворимое нелетучее вещество (твердое тело, например соль, или вязкая жидкость, например вазелин) остается в концентрированном виде в аппарате. Получаемые при выпаривании пары удаляются в атмосферу или в конденсирующее устройство.
|
Превращаться в пар растворитель может при кипении жидкости или при поверхностном испарении ее. В выпарных аппаратах применя- ется более интенсивный из этих способов превращения растворителя в пар, а именно кипение.
Чтобы правильно спроектировать выпарную установку для задан- ного раствора, необходимо экономически обоснованно и технологиче- ски оптимально выбрать:
• схему подогрева раствора;
• схему питания аппаратов раствором;
• оптимальное число ступеней установки;
• рациональную систему использования вторичного тепла.
Как известно, применением выпаривания в многоступенчатой выпарной установке достигается значительная экономия греющего па- ра. С учетом потерь тепла расход греющего пара D в установке с п сту- пенями выражается приближенно формулой:
|
0,85× n
(3.4.1)
где W количество выпариваемого растворителя во всех ступенях ус- тановки.
Таким образом, увеличение числа ступеней в обратной пропорции снижает расход пара на установку, однако в прямой пропорции увели- чивает поверхность нагрева выпарных аппаратов, т. е. капитальные за- траты. Обычно бывают трех- или четырехступенчатые выпарные уста- новки.
Разработана методика технико-экономического анализа и опреде- ления наивыгоднейшего числа ступеней по эксплуатационным затратам в зависимости от стоимости обслуживания установки, а также расходов на пар, воду и электроэнергию. Оптимальное число ступеней выпарной
установки n опт
приближенно можно определить по формуле:
é ù0,5
n = ê k п0×п(J - t)
´ æ B +
C × i п ¢
öú
, (3.4.2)
опт ê é
G × c
ù ç 0,85 t ¢
- t ¢ ÷ú
ê A c ê(i п ¢ - t п0)п-
0 0 × (t
- t)ú è
вод вод øú
ëê ë W û úû
где k п коэффициент теплопередачи в последней ступени,
ккал/м2·ч·град;
c поправочный коэффициент, учитывающий уменьшение коэф- фициента теплопередачи от корпуса к корпусу;
J температура греющего пара на входе в установку, град;
0пи t
– t температура кипения раствора в первой и в последней
ступенях, град;
i п ¢ энтальпия пара в последней ступени, ккал/кг;
|
0 и G 0 н c ачальные вес (кг) и теплоемкость (ккал/кг·град) раствора;
A стоимость обслуживания, ремонта и автоматизации 1 м 2 по- верхности нагрева, руб./м2·ч;
B стоимость пара, руб./кг;
C стоимость воды, руб./кг;
E стоимость электроэнергии в формуле в окончательном виде выпадает за малостью по сравнению с другими членами.
Приведенная формула пригодна для определения наивыгоднейшего числа ступеней только с точки зрения технико-экономических показа- телей; в ней не учитываются условия работы отдельных аппаратов.
Ректификационные установки
Ректификация представляет собой такой термический процесс раз- деления жидких смесей на их составные части, в котором из кипящей смеси выделяются пары, содержащие те же компоненты, но в другой пропорции.
Процесс ректификации основан на различной летучести состав- ляющих смесь компонентов, т. е. на различии в температурах кипения компонентов при одинаковом давлении.
Расход тепла на ректификацию жидких смесей весьма велик, при- чем большая часть его обусловливается повторным испарением флегмы, возвращаемой в колонну. Тепло, уносимое из колонны кубовым остат- ком и дистиллятом, относительно невелико и в значительной степени может быть использовано в пределах самой установки на нагревание исходной жидкой смеси.
Наибольшего эффекта в экономии тепла можно достичь путем ис- пользования скрытой теплоты испарения уходящих из колонны паров низкокипящего компонента. Используя тепло этих паров, можно резко сократить расход охлаждающей воды в дефлегматоре и конденсаторе- холодильнике.
Однако давление паров из колонны невелико (около 1 ат), и поэто- му их нельзя транспортировать на значительные расстояния. Вследствие этого иногда представляется целесообразным применение теплового на- соса для повышения давления и температуры паров низкокипящего компонента с целью использования их в качестве теплоносителя в дис- тилляционном кубе ректификационной колонны (рис. 3.4.1, а).
После отдачи парами тепла и их конденсации часть жидкости на- правляют в виде флегмы в колонну, а часть выводят из установки в ка- честве готового продукта. Следует, однако, иметь в виду, что степень, сжатия паров в описываемой схеме может оказаться выше экономиче- ски целесообразной, так как при равных давлениях температура кипе- ния кубового остатка всегда выше температуры кипения низкокипящего компонента. Тепловой насос не выгоден при степени сжатия выше двух, поэтому область его рационального применения ограничена процессами ректификации смесей с близкими температурами кипения чистых ком- понентов.
|
В некоторых случаях может оказаться целесообразным использо- вание эффекта самовскипания конденсата греющего пара из трубчатки дистилляционного куба и последующего сжатия пара самовскипания при помощи струйного насоса (рис. 3.4.1, б). Расчеты показали, что применение инжектора экономически выгодно до тех пор, пока требуе- мое повышение температуры конденсации сжимаемого пара не превы- шает 1015 °С.
Рис. 3.4.1. Схемы ректификационных установок с тепловыми насосами а использование тепла пара низкокипящего компонента; б использование пара вторичного вскипания конденсата из греющей трубчатки дистилляционного куба;
1 турбокомпрессор; 2 инжектор
Может оказаться выгодным использование скрытой теплоты ухо- дящих из колонны паров низкокипящего компонента для испарения во- ды в дефлегматоре, т. е. совмещение дефлегмации с производством во- дяного пара. Образующийся в дефлегматоре водяной пар может быть использован после сжатия его в компрессоре для обогрева дистилляци- онного куба. Применение такой схемы должно быть обосновано эконо- мическим расчетом.
Наконец, во всех случаях следует сводить к минимуму потери теп- ла в окружающую среду через стенки колонны вопреки существующему мнению, что потери тепла в окружающую среду, обусловливая увели- чение количества стекающей в колонне флегмы, улучшают работу ко- лонны.
Сушильные установки
Сушкой называется термический процесс удаления из твердых ма- териалов или растворов содержащейся в них влаги путем ее испарения.
![]() |
Рис. 3.4.2. Схема сушилки с рециркуляцией воздуха и процесс сушки на Hd -диаграмме
По выходе из сушилки поток отработавшего влажного воздуха с
параметрами, соответствующими точке C или
C 1, разветвляется: часть
воздуха выпускается в атмосферу, а другая возвращается к вентилятору. Вместо выброшенного отработавшего воздуха в систему подается такое же количество свежего воздуха с параметрами, соответствующими точ- ке А. Свежий воздух смешивается с отработавшим. Полученная смесь с параметрами точки М нагревается в калорифере до состояния, характе- ризующегося точкой, B 1 и поступает в сушилку. По выходе из сушиль-
|
ной камеры поток смеси снова разветвляется и т. д. На Hd -диаграмме процесс в такой теоретической сушилке изображается линией AMB 1 C 1 M. Расходы свежего и выбрасываемого из системы отработав-
шего воздуха для такой теоретической сушки одинаковы и выражаются формулой:
l = 1000
= 1000,кг на 1кг влаги,
(3.4.3)
DC 1 M d
d T - d
2 0
так как всю испаренную влагу уносит только удаляемый отработавший воздух.
Количество циркулирующего воздуха в сушилке определяется из условия, что 1 кг смеси увеличивает в сушилке свое влагосодержание с
d см
до 2, d
l ц =
1000
= 1000, кг на 1 кг влаги.
(3.4.4)
D 1¢ C 1 M d
d T - d
2см
Как видно из последней формулы, возврат отработавшего воздуха значительно увеличивает количество циркулирующего воздуха, а сле- довательно, и расход энергии на вентилятор.
Так как на 1 кг влаги.
AB / DC 1 = MB 1 / D ¢ C 1, то расход тепла
(1 0) q, кД l ж I I = -
Рециркуляция сушильного агента применяется, как правило, при
сушке деформирующихся материалов, досок, деревянных и керамиче- ских изделий и тому подобных материалов, требующих во избежание их растрескивания значительного содержания влаги в сушильном агенте для уменьшения интенсивности испарения влаги с поверхности мате- риала.
При работе без рециркуляции необходимо было бы увлажнять су- шильный агент перед вводом в сушильную камеру и затрачивать на это дополнительно тепло. Применение рециркуляции позволяет вести суш- ку при высоких влагосодержаниях сушильного агента без расхода тепла на его увлажнение. Кроме того, при рециркуляции возможно регулиро- вание влажности воздуха в сушильной камере, благодаря чему улучша- ется качество высушенного материала.
При рециркуляции увеличивается скорость воздуха относительно материала, повышается коэффициент теплообмена и сокращается про- должительность сушки материалов, не склонных к растрескиванию, что приводит к уменьшению расхода тепла. При выборе кратности цирку- ляции сушильного агента в рециркуляционной сушилке экономию теп- ла и сокращение других эксплуатационных расходов на нее необходимо сравнить с увеличением расхода средств на электрическую энергию для привода вентилятора значительно большей производительности.
Контрольные вопросы
1. Перечислите потенциальные возможности энергосбережения на предприятиях.
2. Перечислите и охарактеризуйте пути экономии ТЭР.
3. Что понимается под ВЭР?
4. Назовите и охарактеризуйте виды ВЭР.
5. Причины использования ВЭР.
6. Перечислите основные направления использования ВЭР.
7. С помощью каких показателей определяется эффективность ме- роприятий по использованию ВЭР?
чах.
8. Способы переработки ТБО.
9. Преимущества и недостатки ТБО.
10. Пути снижения удельных расходов энергии в электрических пе-
11. За счет чего можно улучшить технологию электросварки?
12. Пути снижения энергопотребления зданий на отопление.
13. Факторы, влияющие на расход тепловой и электрической энергии
в зданиях.
14. Основные составляющие теплового баланса здания.
15. Пути повышения эффективного использования тепловой энергии в системах отопления.
16. Перечислите основные мероприятия по снижению расхода элек- троэнергии в вентиляционных установках.
17. Основные показатели эффективности осветительных установок.
18. Показатели эффективности использования энергоресурсов в пред- приятиях машиностроения.
19. Что представляет собой процесс выпаривания?
20. Какой из процессов происходит при выпаривании: кипение или испарение раствора?
21. Что представляет собой процесс ректификации?
22. Перечислите пути экономии тепла в ректификационных уста- новках.
23. В чем заключается процесс сушки материала?
24. Что дает применение рециркуляции в сушильных установках?
4. ЭНЕРГОСБЕРЕЖЕНИЕ ПРИ ТРАНСПОРТИРОВКЕ ЭНЕРГОРЕСУРСОВ
Насосные установки
В зависимости от назначения и рода перекачиваемой жидкости на- сосные установки подразделяются на: водопроводные, канализацион- ные, мелиоративные, теплофикационные, нефтеперекачивающие и др.
На современных насосных установках набольшее распространение получили лопастные насосы: центробежные и осевые.
Центробежные насосы регулируются изменением частоты враще- ния рабочих колес или изменением степени открытия задвижки (затво- ра) на напорной линии (рис. 4.1.1). Прикрывая или открывая затвор, из- меняют крутизну характеристики GH трубопровода, которая зависит от его гидравлического сопротивления.
![]() |
Рис. 4.1.1. Регулирование режима работы центробежного насоса:
1 характеристика насоса при номинальной частоте вращения; 2 то же при уменьшенной частоте вращения; 3 характеристика трубопровода при полном от-
крытии затвора; 4 то же при уменьшении степени открытия затвора
Прикрывая затвор, увеличивают крутизну характеристики, при этом рабочая точка насоса А 1 перемещается в положение А 2, подача уменьшается до значения G 2. Напор, развиваемый насосом, возрастает до значения Н 2, а напор на трубопроводе за затвором снижается до зна-
чения H 2¢ за счет потерь напора D Н n в затворе.
Увеличивая степень открытия затвора, уменьшают крутизну харак- теристики трубопровода. Этот способ регулирования считается мало- экономичным, так как на преодоление дополнительного гидравлическо-
го сопротивления в затворе требуются дополнительные затраты энер- гии.
При изменении частоты вращения насоса изменяется положение характеристики GН насоса. Уменьшая частоту вращения, перемещают характеристику вниз параллельно самой себе. При этом рабочая точка, перемещаясь по характеристике трубопровода, занимает положение А' 2 следовательно, подача уменьшается также, как и напор в сети и напор, развиваемый насосом.
Мощность электродвигателя насоса, кВт, определяется по врыже- нию:
P = k з × G н × (H с + D H)× g ,
н 367200 ×hн ×hэ.д
(4.1.1)
где G -н
k -з
подача насоса, м3/ч;
коэффициент запаса (при G н < 100 м 3/ч, k з =1,2÷1,3; при G н >
100 м3/ч,
H -с
м вод.ст.;
k з =1,1÷1,5);
статический напор (сумма высот всасывания и нагнетания),
D H - потери напора в трубопроводах, м вод.ст.;
hн - КПД насоса;
hэ.д - КПД электродвигателя;
g - плотность жидкости, кг/м3.
Удельный расход электроэнергии в насосных установках определя- ется по выражению, кВт·ч/м2:
w = 0, 00272 (H с
H ×) + D
.
(4.2.2)
уд hн ×hэ.д
Как видно из данного рисунка, экономии электроэнергии в насос- ных установках можно добиться правильным выбором характеристик насосного агрегата (GmH).
При работе насосной установки с подачей меньше расчетной воз- никает несоответствие между напором, развиваемым насосом, и напо- ром, требуемым для подачи того или иного количества жидкости (т. е. превышение напора насоса). Из рисунка видно, что при уменьшении подачи требуемый для сети напор уменьшается, а развиваемый насосом напор увеличивается. Разность значений этих напоров:
D Н n = Н н - Н с.
(4.2.3)
Из графика совместной работы насоса и трубопровода видно, что
значение
D Н n
тем больше, чем круче характеристики насоса и трубо-
провода и чем меньше фактическая подача насоса по сравнению с рас- четной.
Годовые потери электроэнергии за счет повышения напора соста- вят, кВт·ч:
D W =
k з × G н × D Hn × g
367200 ×hн ×hэ.д
× T г ,
(4.2.4)
где
T г- годовое время работы насоса с повышением напора на
D Н n .
Если насос работает с переменным напором и давлением, то
D W =
k з × g
× (G
× D H
× T),
(4.2.5)
|
н i ni г i
н э.д i =1
где
G н- i
H D ni
T г- i
подача насоса на i -м интервале времени; п-овышение напора на i -м интервале времени;
годовая продолжительность i -го интервала;
n - число интервалов изменения напоров.
|
|
Состав сооружений: решетки и песколовки: Решетки – это первое устройство в схеме очистных сооружений. Они представляют...
Двойное оплодотворение у цветковых растений: Оплодотворение - это процесс слияния мужской и женской половых клеток с образованием зиготы...
Индивидуальные очистные сооружения: К классу индивидуальных очистных сооружений относят сооружения, пропускная способность которых...
История развития хранилищ для нефти: Первые склады нефти появились в XVII веке. Они представляли собой землянные ямы-амбара глубиной 4…5 м...
© cyberpedia.su 2017-2024 - Не является автором материалов. Исключительное право сохранено за автором текста.
Если вы не хотите, чтобы данный материал был у нас на сайте, перейдите по ссылке: Нарушение авторских прав. Мы поможем в написании вашей работы!