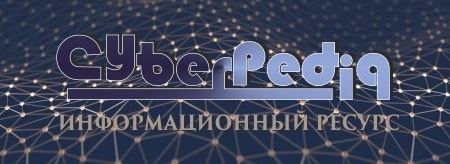
Историки об Елизавете Петровне: Елизавета попала между двумя встречными культурными течениями, воспитывалась среди новых европейских веяний и преданий...
История развития хранилищ для нефти: Первые склады нефти появились в XVII веке. Они представляли собой землянные ямы-амбара глубиной 4…5 м...
Топ:
Особенности труда и отдыха в условиях низких температур: К работам при низких температурах на открытом воздухе и в не отапливаемых помещениях допускаются лица не моложе 18 лет, прошедшие...
Методика измерений сопротивления растеканию тока анодного заземления: Анодный заземлитель (анод) – проводник, погруженный в электролитическую среду (грунт, раствор электролита) и подключенный к положительному...
Когда производится ограждение поезда, остановившегося на перегоне: Во всех случаях немедленно должно быть ограждено место препятствия для движения поездов на смежном пути двухпутного...
Интересное:
Национальное богатство страны и его составляющие: для оценки элементов национального богатства используются...
Как мы говорим и как мы слушаем: общение можно сравнить с огромным зонтиком, под которым скрыто все...
Искусственное повышение поверхности территории: Варианты искусственного повышения поверхности территории необходимо выбирать на основе анализа следующих характеристик защищаемой территории...
Дисциплины:
![]() |
![]() |
5.00
из
|
Заказать работу |
|
|
Неподвижный робот может выполнять следующие основные операции:
1 Погрузочно-разгрузочные (перемещение предметов и их развитие)
2 Изменение облика предметов:
2.1 Нанесение вещества с предмета (окраска, порошковое напыление и т.д)
2.2 Снятие вещества с предмета (механическая обработка, сверление, шлифование, полирование и т.д)
2.3 Изменение формы предмета (ковка, штамповка)
3 Монтаж (сборка нескольких предметов для получения одного целого изделия)
4 Демонтаж (операция, обратная монтажу - разборка изделия на составные части)
5 Фиксация: сборка предметов с окончательным их соединением (склейка, сварка, клепка)
6 Измерения: получение количественной информации о некоторых физических характеристиках объекта.
Некоторые задачи, например установка или сборка изделий, состоят из многих перечисленных выше операций. Другие задачи предполагают мобильность робота, т.е возможность действовать в пространстве, намного превышающем его размеры:
1 Сопровождение (транспортировка предметов между складскими помещениями или между рабочими местами, находящимися на большом расстоянии)
2 Обследование (перемещение органов восприятия, позволяющее передавать на расстояние информацию о среде, в которой находится робот)
3 Сбор, захват и перенос предметов, находящихся в различных местах
4 Воздействия на отдаленные предметы при их осмотре. Выполнение роботом операций зависит не только от типа действий, но и состояния рабочей среды:
1 Ограничений, накладываемых характером обтекания жидкости или газа
2 Вида работы над объектом
Для определения конструкции робота необходимо определить несколько характеристик. Для начала нужно определить основные виды работ, которые должен выполнять робот:
|
1 Изготовление предметов (в металлообрабатывающей, автомобильной, текстильной промышленности)
2 Строительные работы (сооружение зданий, путепроводов, судов)
3 Добыча и переработка сырья (шахты, карьеры, цементные заводы)
4 Сельскохозяйственные и лесные работы
5 Работа в медицинских учреждениях (в больницах, в биологических лабораториях)
Затем следует определить основные характеристики предметов, с которыми робот взаимодействует. К ним можно отнести: форму, объем, массу, температуру, габариты, состояние поверхности, внутреннюю структуру, изменяемость размеров и т.д. Невозможно полностью предсказать поведение робота в процессе эксплуатации. При этом необходимо учитывать различные задачи и условия работы робота, чтобы предвидеть изменение программы решений в соответствии со сложившейся ситуацией.
Конструкции роботов
Возможности робота в значительной степени определяются взаимодействием его рабочего органа с внешней средой. Рабочий орган определяет основные требования ко всем остальным конструктивным элементам робота.
Рабочие органы
В качестве рабочих органов могут быть разнообразные инструменты: клещи, присоски (захват), сопла, горелка (в дуговой сварке) и т.д. При конструировании рабочего органа все операции тщательно анализируются. Рабочий орган обладает следующими свойствами:
1 Является сложной системой, которую редко можно представить в виде единого не поддающегося деформации элемента
2 Относится к типу приспособлений, состоящих из нескольких приводов
З Часто содержит чувствительные датчики, позволяющие обеспечить его адаптацию к конкретным условиям задачи.
Наряду с многофункциональными схватами иногда встречаются мультифункциональные (двойные клещи, четырехоперационные головки)
Звенья
Рабочий орган используется для выполнения заданных движений. Звенья манипулятора образуют механическую систему с изменяемой геометрией, связанную с корпусом робота и позволяющую при помощи движений ограниченной амплитуды перемещать и ориентировать рабочий орган. Движения звеньев манипулятора производятся относительно неподвижной платформы робота. Робот на подвижной платформе представляет собой свободную механическую систему, способную неограниченно перемещаться (автотележка, подводный робот).
|
Манипуляторы
Манипулятором называется механическая система, состоящая из звеньев рабочего органа. Например, существуют манипуляторы для выполнения погрузочно-разгрузочных работ, сварки, шлифовки, и т.д. Промышленный робот может состоять из нескольких манипуляторов, расположенных на одной платформе и управляемых с помощью одной вычислительной машины. Если платформа неподвижна, робот не перемещается (рисунок 1.2), а если робот установлен на тележке, он становится мобильным (рисунок 1.3). Промышленные роботы бывают с одним манипулятором или несколькими (рисунок 1.4)
Рисунок 1.2 – Схема одноманипуляторного робота на неподвижном основании
Рисунок 1.3 – Схема мобильного одноманипуляторного робота
Рисунок 1.4 -Схема трёхманипуляторного робота на неподвижном основании
Для приведения в движение звеньев манипулятора требуется (рисунок 1.5):
1 Распределение первичной энергии (обычно электрической, пневматической, гидравлической)
2 Превращение первичной энергии в механическую
3 Передачу механической энергии звеньям
4 Управление движением (по положению, скорости, усилию, ускорению)
Рисунок 1.5 – Принципиальная схема управления движением звена манипулятора
Управление движением проще всего производить с помощью приводов, каждый из которых непосредственно связан с осью соответствующего сочленения.
Однако это применяется довольно редко по следующим причинам:
1 Многие преобразователи механической энергии по своей конструкции сообщают высокие скорости исполнительным органам, но создают малые усилия, что требует применения редукторов
2 Механизм привода с редуктором имеет большие габариты, что препятствует выполнению задания (в особенности если привод размещается вблизи рабочего органа)
3 Каждый привод имеет массу и момент инерции, которые увеличивают массу и моменты инерции звеньев и всей системы. Эти дополнительные нагрузки необходимо учитывать при выборе приводов, расположенных на звеньях, так как они существенно увеличивают общую массу.
|
При выборе необходимых элементов конструкции и расчете их параметров переходят к проектированию робота. Основные стадии проектирования робота представлены на рисунке 1.6
НМС – несущая механическая система; ИМС – исполнительная механическая система;
ТЗ – техническое задание; ТП – технический проект; РП – рабочий проект;
ЭО – экспериментальный образец; ТД – техническая документация; ОО – опытный образец
Рисунок 1.6 - Основные стадии проектирования ПР и их взаимосвязь
Практическая часть
Задание
Изучить возможности неподвижных и мобильных роботов, конструкции промышленных роботов и стадии их проектирования
Порядок выполнения работы
1 Изучить возможности неподвижных и мобильных роботов, нарисовать принципиальную схему принятия решения роботом (рисунок 1.1)
2 Изучить основные структурные элементы промышленных роботов, нарисовать схему одноманипуляторного робота на неподвижном основании (рисунок 1.2) и мобильного робота (рисунок 1.3)
3 Ознакомиться с основными стадиями проектирования промышленного робота и занести их в отчёт (рисунок 1.6)
4 Оформить отчет по рекомендуемой форме.
Форма отчета
Практическая работа №1
Цель работы:…
Оснащение:…
Выполнение работы:…
Рисунок 1 - Принципиальная схема принятия решения и выполнения действия роботом
![]() |
Рисунок 2- Принципиальная схема одноманипуляторного робота на неподвижном основании
![]() |
Рисунок 3- Принципиальная схема мобильного одноманипуляторного робота
![]() |
Рисунок 4- Основные стадии проектирования промышленного робота
Вывод:…
Контрольные задания
1 Опишите преимущества и недостатки мобильных промышленных
роботов.
2 Перечислите основные конструктивные элементы роботов.
3 Опишите преимущества и недостатки много манипуляторных роботов
Практическая работа №6. Изучение конструкций малогабаритных токарных станков с компьютерным управлением.
|
Цель работы – Дать учащимся представление об общем устройстве токарного станка с ЧПУ.
Теоретическая часть
1. Конструктивные особенности универсальных токарных станков и токарных станков с ЧПУ
Внешний вид типового универсального токарно-винторезного станка представлен на рис. 1. В состав станка входят следующие основные узлы и механизмы:
1 - передняя бабка; 2 - суппорт;
3 - задняя бабка; 4 - станина;
5 - задняя тумба; 6 - фартук;
7 - ходовой винт; 8 - ходовой валик;
9 - передняя тумба; 10 - коробка подач;
11 - гитары сменных шестерен; 12 - электро-пусковая аппаратура; 13 - коробка скоростей; 14 - главный шпиндель.
Токарные станки с ЧПУ имеют большое разнообразие конструктивных решений, так как они обычно не предназначены для непосредственного управления станочником в процессе обработки. Ряд токарных станков с ЧПУ (например, станок модели CC-D6000E, изображенный на рис. 2) допускает работу не только от ЧПУ, но и в качестве универсального станка. Такие станки имеют традиционную для универсальных токарных станков компоновку.
Рис. 1.
Токарный станок модели CC-D6000E относится к категории станков с открытой системой ЧПУ, т.е. он не имеет отдельной стойки ЧПУ и управляется непосредственно с компьютера. Наибольшие внешние отличия данного станка от универсального токарно- винторезного станка проявляются в наличии управляющего компьютера, пульта управления и защитной кабины, полностью закрывающей доступ к рабочей зоне станка - 3 -
при обработке по управляющей программе и защищающей станочника от стружки и разбрызгивания СОЖ.
Основными узлами станка модели CC-D6000E являются: 1 - передняя бабка;
2 - суппорт;
3 - задняя бабка; 4 - станина;
5 - подставка под станок;
6 - револьверная головка;
7 - главный шпиндель;
8 - привод продольной подачи;
9 - привод поперечной подачи;
10 - защитная кабина;
11 - пульт управления;
12 - управляющий компьютер.
Станина 4 (рис. 2) является основным несущим элементом станка, на котором смонтированы все другие узлы и механизмы станка. С целью придания конструкции большей жесткости станина выполнена из серого чугуна и имеет ребра жесткости 1 (рис. 3). Для продольного перемещения исполнительных узлов станка станина оснащена двумя направляющими 2 и 3, каждая из которых имеет классическое для универсальных токарных станков исполнение, включающее в себя два участка с разными профилями (с плоским профилем и треугольным).
Передняя бабка 1 (рис. 4) служит для закрепления или поддержания левого конца обрабатываемой заготовки и для придания заготовке вращения при помощи привода главного шпинделя 2. В зависимости от особенностей процесса обработки для закрепления заготовки на валу главного шпинделя 2 устанавливается либо (как на рис. 4) кулачковый патрон 4, либо какое-то другое зажимное устройство (цанговый патрон, центр и т.п.).
|
С целью обеспечения безопасности при работе передняя бабка 1 снабжена защитным откидным щитком 3, оснащенным блокировкой, отключающей привод главного шпинделя 2 при откинутом положении щитка 3.
Со стороны наружной стенки защитной кабины 2 (рис. 5) на передней бабке под защитным кожухом 1 располагаются коробка скоростей главного шпинделя и гитара.
Коробка скоростей главного шпинделя (рис. 6) включает в себя систему шкивов, кинематически соединенных между собой при помощи ременных передач. В состав коробки скоростей входят ведущий шкив 6, промежуточный шкив 2, шкив 9 на валу шпинделя 10, поликлиновые ремни 3, 4 и 8, натяжное устройство 1 и фотоимпульсный датчик 7, с помощью которого при нарезании резьбы синхронизируется вращение вала шпинделя 10 и перемещения суппорта.
Гитара включает в себя зубчатое колесо 14, систему шкивов 13, 16 и 18, зубчатые ремни 12, 15 и 17, а также натяжное устройство 11.
Задняя бабка 3 (рис. 7) служит для закрепления и подачи инструмента, необходимого при выполнении сверлильной обработки, а также, при необходимости, служит для поддержки или закрепления правого конца обрабатываемой заготовки. Перемещение задней бабки 3 по направляющим 4 и 6 осуществляется вручную. Фиксация задней бабки 3 после перемещения по направляющим 4 и 6 производится с помощью гайки 2, навинченной на резьбовую часть прижима 5.
Для выполнения сверлильных операций задняя бабка 3 оснащена пинолью 8, которая перемещается в продольном направлении относительно задней бабки 3 вручную путем вращения маховика 1. При необходимости пиноль 8 может быть зафиксирована от перемещения в корпусе задней бабки 3 с помощью рукоятки 9.
Вал пиноли 8 имеет внутренний конус 7, в котором может быть установлен сверлильный патрон или какая-то другая оснастка, например, токарный центр.
Суппорт (рис. 8) обеспечивает поперечную и продольную подачу режущего инструмента относительно обрабатываемой заготовки. Конструктивно суппорт выполнен в виде двух частей: продольных салазок 2 и поперечных салазок 11. Продольная подача выполняется путем перемещения продольных салазок 2 по направляющим 3 и 5 станины 7. Поперечная подача инструмента выполняется путем перемещения поперечных салазок 11 по направляющим 1 и 10, установленным на продольных салазках 2. На поперечных салазках 11 смонтирована револьверная головка 12, в посадочных гнездах которой закрепляется необходимый для данной обработки набор режущих инструментов.
При работе станка перемещения суппорта в продольном и поперечном направлении выполняются с помощью соответствующих приводов по командам системы ЧПУ. Привод продольной подачи 9 установлен на станине 7, а привод поперечной подачи 4 - на суппорте. Эти перемещения суппорта могут быть также выполнены вручную с помощью поворотной рукоятки 6 и маховика 8 при выключенном ЧПУ.
Привод продольной подачи 8 (рис. 2) располагается непосредственно на станине 1 станка. Вращение вала шагового двигателя привода 1 (рис. 9) передается через зубчато-ременную передачу 2 на ходовой винт 3 шарико-винтовой передачи, установленный без возможности осевого перемещения в опорах 4 на станине 5.
С помощью гайки качения 3 (рис. 10), установленной неподвижно на продольном суппорте 1, вращение ходового винта 2 преобразуется в поступательное перемещение суппорта 1 в продольном направлении.
Устройство привода продольной подачи позволяет осуществлять перемещение суппорта не только от ЧПУ, но и как на универсальном токарном станке - вручную. С этой целью станок снабжен механизмом ручной продольной подачи, который располагается на станине 1 (рис. 11) и представляет собой коническую зубчатую передачу, ведомое колесо 2 которой установлено на ходовом винте 3 привода продольной подачи, а ведущее колесо 4 вручную приводится во вращение маховиком 1 (рис. 12).
Кроме того, в состав механизма ручной продольной подачи входит стопорная рукоятка 2 (рис. 12) и муфта 5 (рис. 11), которая при повороте рукоятки 2 (рис. 12) блокирует вращение ходового винта 2 (рис. 11). Данная блокировка используется при выполнении операции торцевания, в случае использования станка в качестве универсального токарного станка для изготовления большой партии деталей.
Привод поперечной подачи 9 (рис. 2) располагается на суппорте станка. Вращение вала 3 шагового двигателя 1 привода (рис. 13) передается через расположенную под защитным кожухом 5 зубчато-ременную передачу 2 на ходовой винт 3 (рис. 14) шарико-винтовой передачи.
Ходовой винт 3 (рис. 14) размещен на поперечном суппорте 4 без возможности осевого перемещения в своих опорах. Гайка качения 2 установлена неподвижно на продольном суппорте 1, поэтому вращение ходового винта 3 преобразуется в поступательное перемещение поперечного суппорта 4.
Устройство привода поперечной подачи позволяет осуществлять перемещение суппорта не только от ЧПУ, но и как на универсальном токарном станке – вручную – при помощи поворотной рукоятки 4 (рис. 13), соединенной с ходовым винтом 3 (рис. 14).
Пульт управления служит для подачи электрического тока из сети питания к приводам исполнительных органов станка, а также для коммутации управляющего компьютера с системой управления приводами станка. Пульт управления 1 (рис. 15) установлен на поворотном кронштейне 5, закрепленном на станке 4 при помощи зажимов 2 и 3.
На лицевой панели пульта (рис. 16) располагаются:
1) Двухкнопочный сетевой выключатель 1. При нажатии зеленой (верхней) кнопки производится подключение станка к питающей электрической сети, при нажатии красной (нижней) кнопки – отключение.
2) Потенциометр 2, регулирующий число оборотов шпинделя станка. Шкала потенциометра проградуирована в процентах от 0% до 100%.
3) Выключатель 3 системы подачи СОЖ, с помощью которого производится включение и выключение насоса, подающего СОЖ в зону резания.
4) Кнопка аварийного останова 4, при нажатии которой происходит отключение станка от питающей электрической сети.
5) Переключатель 5 режима управления скоростью вращения шпинделя станка. Переключатель 5 имеет три фиксированных угловых положения:
- левое положение - включен режим задания числа оборотов шпинделя при помощи управляющей программы с возможностью ручной корректировки при помощи потенциометра …;
- правое положение – включен режим ручного управления скоростью вращения шпинделя при помощи потенциометра …;
- среднее положение – управление скоростью вращения шпинделя отсутствует, шпиндель не вращается.
6) Переключатель 6 направления вращения шпинделя. Переключатель 6 имеет три фиксированных угловых положения:
- левое положение – вращение шпинделя имеет направление против часовой стрелки, если смотреть на главный шпиндель со стороны задней бабки;
- правое положение – вращение шпинделя имеет направление по часовой стрелке, если смотреть на главный шпиндель со стороны задней бабки;
- среднее положение – шпиндель не вращается.
7) Панель индикации 7.
Панель индикации (рис. 17) отображает текущее состояние станка при помощи трех светодиодов различных цветов, при этом в зависимости от режима работы станка в активированном состоянии находится только один светодиод. Цветовая гамма, режим свечения и назначение светодиодов следующие:
1) Желтый (нижний) светодиод 3. Он имеет мигающий режим свечения и активируется, когда между станком и управляющим компьютером происходит обмен данными, например, при работе станка по управляющей программе.
2) Зеленый (средний) светодиод 2. Он имеет непрерывный режим свечения и активируется, когда станок включен и готов к работе.
3) Красный (верхний) светодиод 1. Он имеет непрерывный режим свечения и активируется, когда станок включен, но по какой-либо причине не готов к работе.
Кроме светодиодов на панели индикации расположен также аварийный выключатель 4 связи станка с управляющим компьютером. Он имеет два положения:
- верхнее положение, предоставляющее свободный обмен данными между управляющим компьютером и станком;
- нижнее положение, блокирующее обмен данными.
Задняя стенка пульта управления (рис. 18) используется для подключения к пульту электрических кабелей питания и управления. На задней стенке пульта располагаются:
1) Ввод сетевого кабеля 7, по которому осуществляется соединение пульта с сетью электропитания.
2) Кабельные вводы 1 для управления и питания исполнительными элементами станка, не связанными с перемещениями суппорта (главный шпиндель, насос подачи СОЖ, система блокировки).
3) Кабельный разъем 3 для связи пульта с управляющим компьютером.
4) Кабельный разъем 2 для подключения фотоимпульсного датчика главного шпинделя.
5) Кабельный разъем 6 для управления шаговым приводом револьверной головки.
6) Кабельный разъем 5 для управления шаговым приводом поперечной подачи суппорта.
7) Кабельный разъем 4 для управления шаговым приводом продольной подачи суппорта.
Практическая часть
Практическая работа №7. Изучение конструкций малогабаритных фрезерных станков с компьютерным управлением.
Цель работы – описывать устройство и принцип работы основных узлов фрезерного станка с ЧПУ.
Теоретическая часть
Конструкция станка. Станок выполнен в виде С-образной станины в форме стабильной литой конструкции. Качество основания станка позволяет на протяжении всего срока эксплуатации выполнять обработку металла с высокой точностью и большой производительностью. Фиксированные расстояния по осям Y и Z оказывают положительное воздействие на результат фрезерования. Широкая опора на 3х точках устойчивого к вибрациям литого основания, все литые детали, дополнительно укрепленные ребрами и элементами жесткости, а также термосимметрическое конструктивное исполнение обеспечивают высокую жесткость на изгиб и скручивание, высокую температурную устойчивость и точность направляющих. Отличительной особенностью является большое расстояние между направляющими. Тем самым стол станка оснащен жесткой направляющей, которая целиком закреплена в станине станка и обеспечивает высокую нагрузку стола.
Система направляющих по линейным осям. Шариковинтовые пары передают усилие подачи от приводов. Роликоподшипниковые линейные направляющие отличаются малым тепловыделением, низким коэффициентом трения, отсутствием эффекта «прилипания», постоянством точности (низкий износ) и очень низкими потребностью в смазке. Ось X закрыта защитными кожухами, которые обеспечивают хороший отвод стружки.
Централизованная смазка. Система смазки роликоподшипниковых направляющих и ШВП устроена по принципу подачи минимально необходимого количества смазки.
Система измерения. В стандартной комплектации применяется система косвенного измерения перемещений. С опцией “Система прямого измерения линейных перемещений” станок имеет также систему нагнетания воздуха под давлением в линейках для их дополнительной защиты.
Привода подач. Для высокой динамики и малых расходов на обслуживание применяются цифровые привода переменного тока. Быстрое время обратной связи между приводами и ЧПУ обеспечивают высокое значение ускорения и точность, что вместе с линейными роликоподшипниковыми направляющими дает высокое качество обработанной поверхности и точность обработанного контура детали.
Вертикальный шпиндель. Трехфазный электродвигатель напрямую передает вращение на главный шпиндель. Шпиндель имеет воздушное охлаждение. Мощный главный шпиндель имеет жесткую конструкцию и оснащается прецизионными подшипниками с консистентной смазкой. Жесткая конструкция и использование специальных подшипников гарантируют высокие показатели резания.
Температурная компенсация по оси Z. При использовании опции “Система прямого измерения линейных перемещений” применяется электронный температурный датчик (включая узел оценки данных), который компенсирует геометрические изменения, возникающие вследствие нагрева фрезерного шпинделя. Постоянный мониторинг и управление компенсацией производится системой управления. Мощная и хорошо продуманная конструкция главных конструктивных узлов станка помогает уменьшить температурные колебания к минимуму и обеспечить эффективный отвод тепла.
Зажим инструмента. Зажим производится механически механизмом с тарельчатыми пружинами. Цилиндр разжима инструмента активируется пневматикой. Магазин инструмента/Память данных инструмента20-ти позиционный магазин инструмента (дискового типа с карманами) расположен внутри рабочей зоны станка, но при этом хорошо защищен от попадания СОЖ и стружки. При смене инструмента используется двухместный захват, что дает короткий цикл смены. Инструмент располагается в карманах магазина и удерживается пружинными элементами. Инструмент в магазин устанавливается из главного шпинделя. При каждом цикле смены инструмента производится обдув и очистка инструментального конуса шпинделя и инструмента сжатым воздухом под давлением.
Система СОЖ. Возможна обработка с использованием охлаждения при помощи подачи СОЖ в большом объеме. В баке имеются отверстия для грубой фильтрации, поступающей из рабочей зоны СОЖ от стружки, которые легко очищаются. Имеется опция переключения охлаждения СОЖ/сжатый воздух, активируемая через M-функцию.
Защитное ограждение/рабочая зона. Станок оснащен компактной защитной кабиной с откатной дверью рабочей зоны. Оптимальный доступ к рабочей зоне, удобство при уборке и хороший доступ к метам обслуживания станочных узлов являются отличительными особенностями этой серии станков.
Практическая часть
ЗАДАЧИ ПРАКТИЧЕСКОЙ РАБОТЫ:
1. Называть основные узлы станка
2. Описывать принцип работы станка
ЗАДАНИЯ ДЛЯ ПРАКТИЧЕСКОГО ЗАНЯТИЯ:
Дайте краткое описание основных узлов и принципа работы фрезерного станка с ЧПУ.
|
|
Своеобразие русской архитектуры: Основной материал – дерево – быстрота постройки, но недолговечность и необходимость деления...
Индивидуальные и групповые автопоилки: для животных. Схемы и конструкции...
История развития хранилищ для нефти: Первые склады нефти появились в XVII веке. Они представляли собой землянные ямы-амбара глубиной 4…5 м...
Индивидуальные очистные сооружения: К классу индивидуальных очистных сооружений относят сооружения, пропускная способность которых...
© cyberpedia.su 2017-2024 - Не является автором материалов. Исключительное право сохранено за автором текста.
Если вы не хотите, чтобы данный материал был у нас на сайте, перейдите по ссылке: Нарушение авторских прав. Мы поможем в написании вашей работы!