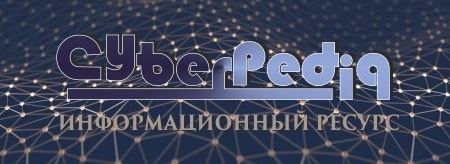
Состав сооружений: решетки и песколовки: Решетки – это первое устройство в схеме очистных сооружений. Они представляют...
Таксономические единицы (категории) растений: Каждая система классификации состоит из определённых соподчиненных друг другу...
Топ:
Основы обеспечения единства измерений: Обеспечение единства измерений - деятельность метрологических служб, направленная на достижение...
Когда производится ограждение поезда, остановившегося на перегоне: Во всех случаях немедленно должно быть ограждено место препятствия для движения поездов на смежном пути двухпутного...
Марксистская теория происхождения государства: По мнению Маркса и Энгельса, в основе развития общества, происходящих в нем изменений лежит...
Интересное:
Подходы к решению темы фильма: Существует три основных типа исторического фильма, имеющих между собой много общего...
Аура как энергетическое поле: многослойную ауру человека можно представить себе подобным...
Искусственное повышение поверхности территории: Варианты искусственного повышения поверхности территории необходимо выбирать на основе анализа следующих характеристик защищаемой территории...
Дисциплины:
![]() |
![]() |
5.00
из
|
Заказать работу |
|
|
Таким образом, к числу важнейших преимуществ станков с ЧПУ, в сравнении со станками с ручным управлением, следует отнести следующие:
1. Доля основного (машинного) времени, в общем, штучном времени изготовления детали на станке, вырастает до 50 % (в сравнении с 10-12 % для станков с ручным управлением). Сроки подготовки производства и общая продолжительность изготовления снижаются на 50-75 %.
2. Станки с ЧПУ обладают большей точностью. Например, принято считать, что экономическая точность токарных и фрезерных станков общего назначения лежит в пределах 9-11 квалитетов, а станков с ЧПУ – 6-9 квалитетов.
3. Большая жёсткость и точность конструкции станков привела к большей точности изготовления изделий, а устранение вмешательства человека в ход обработки привело к увеличению стабильности процесса обработки.
4. Появилась возможность многостаночного обслуживания.
5. Отпала необходимость в применении сложных, фасонных режущих инструментов и различных приспособлений к ним, за счёт обеспечения сложной траектории движения относительно простого режущего инструмента по программе (т.н. инструменты для контурной обработки).
6. Изменилась конструкция вспомогательных приспособлений для установки режущего инструмента на станке. Было сокращено их разнообразие и создан единый ряд унифицированных конструкций посадочной и хвостовой части.
7. Появилась возможность предварительной настройки режущих инструментов вне станка с использованием специальных приборов с отсчётными микроскопами. В связи с этим повысились требования к качеству изготовления и заточки режущих инструментов.
8. Был создан новый тип шаговых двигателей для привода исполнительных органов станка по программе. Если в обычных станках для переключения подач и скоростей шпинделя используют зубчатые муфты, переключаемые вручную, то в станках с ЧПУ эти переключения производятся электромагнитными муфтами. Это обеспечило, в частности, бесступенчатое регулирование оборотов шпинделя и подач. Большое распространение нашли, в частности, шариковые винтовые пары для беззазорной передачи движения от привода к исполнительному органу. Таким образом, в приводах подач устранены люфты, которые имеют место в станках с ручным управлением.
|
9. Изменилась структура операции. Высокая точность позиционирования, а также возможность различных поворотов и перемещений режущего инструмента и заготовки, привели к уменьшению числа установов за счёт увеличения числа позиций.
10. Изменились требования в отношении квалификации станочника и наладчика: к первому – упростились (за ним остались действия по установке и снятию изделий, а также наблюдение за ходом процесса), ко второму – возросли (основная работа связана с настройкой инструмента, его установкой на станке и программированием).
11. Повысилась культура производства, снизилась утомляемость станочника. Особенно это касается сверлильных работ, которые, среди всех видов работ на металлорежущих станках с ручным управлением, являются наиболее утомительными.
12. Изменились требования к технологичности заготовок, поступающих на станок, и деталей, изготавливаемых на станках с ЧПУ. К заготовкам требования стали более жёсткими (отсутствие литейной корки и неоднородностей материала по глубине, наличие малых припусков и незначительных отклонений размеров, формы и расположения поверхностей).
Требования к деталям, наоборот, снизились: допускается и приветствуется наличие сложных поверхностей с высокой точностью и малой шероховатостью.
Функциональная схема станка с ЧПУ.
Практическая часть
Ответить на контрольные вопросы:
|
1. В чём преимущества и недостатки станков с кулачковой системой управления в сравнении со станками с ручным управлением?
2. В чём общность и различия между кулачковой и числовой системами программного управления?
3. В чём преимущества станков с ЧПУ в сравнении со станками с ручным управлением?
4. Каковы особенности токарно-револьверного станка модели 1325Ф30?
5. Каковы особенности вертикально-сверлильного станка модели 2Р135Ф2?
6. Что влияет на выбор последовательности обработки отверстий на станке 2Р135Ф2?
7. Сравните станки моделей 1325Ф30 и 2Р135Ф2: по инструменту, обрабатываемым заготовкам, системам управления, приспособлениям, видам движений.
8. Каковы особенности вертикально-фрезерного станка модели 6Р13Ф3?
9. Какая дополнительная информация указывается в обозначении моделей станков с ЧПУ?
10. В чём принципиальное различие между контурной и позиционной системами ЧПУ?
11. В чём особенность вспомогательного инструмента для станков с ЧПУ?
12. Укажите 34 требования к технологичности изделий, обрабатываемых на токарных станках с ЧПУ.
13. Укажите 34 требования к технологичности изделий, обрабатываемых на фрезерных и сверлильных станках с ЧПУ.
14. Дать краткую характеристику технологической оснастки для станков с ЧПУ.
15. Поясните назначение и принцип действия быстросменного патрона с шариковым захватом.
Практическая работа №3. Системы координат станков с ЧПУ. Способы и начало отсчета координат.
Цель работы:
Дать учащимся понятие о системе координат токарного станка с ЧПУ.
Научить определять координаты точек в системе координат токарного станка с ЧПУ.
Научить назначать координаты характерных точек у заданного профиля токарной детали.
Теоретическая часть
Обработка заготовки на станке с ЧПУ производится по командам управляющей программы, которая в числовом выражении задает величину каждого перемещения исполнительных органов. Поэтому работа станка с ЧПУ в принципе невозможна без определенной системы координат, с помощью которой определяются координаты любой точки в пространстве в границах рабочей зоны станка. При этом система ЧПУ станка должна распознавать закодированные координаты характерных точек, с помощью которых описываются движения исполнительных органов станка.
|
Декартова система координат
Для станков с ЧПУ принята единая система координат, рекомендуемая Международной организацией по стандартизации ИСО: прямоугольная система координат, которую часто называют также декартовой системой координат. Эта система координат в общем случае содержит три оси X, Y и Z, имеющие общую точку пересечения и одинаковый геометрический масштаб, и расположенные взаимно перпендикулярно друг к другу в пространстве.
Координатные оси в станках с ЧПУ всегда располагаются параллельно направляющим станка. В зависимости от типа станка расположение осей координат в пространстве может быть различным, но есть следующие общие правила:
1) Ось Z всегда совмещена с осью вращения шпинделя. Ее положительное направление всегда совпадает с направлением перемещения от устройства для крепления заготовки к режущему инструменту.
2) Если у станка есть хотя бы одна горизонтальная ось, то
(если это не ось шпинделя) это будет обязательно ось X.
3) Если ось Z расположена горизонтально, то положительным направлением оси X является направление вправо, если встать лицом к левому, относительно передней плоскости, торцу станка. Передняя плоскость станка – сторона, с которой располагаются пульт и основные органы управления станком.
4) Если ось Z расположена вертикально, то положительным направлением оси X является направление вправо, если встать лицом к передней плоскости станка.
Для определения положительного направления оси Y необходимо повернуть ось X на 90 вокруг оси Z по часовой стрелке, если смотреть вдоль оси Z в положительном направлении.
Нулевая (начальная) точка системы координат – точка пересечения координатных осей. Координаты точки пересечения по каждой оси всегда равны нулю.
Дана плоская система координат с осями X и Y.
Точка Р1 имеет следующие координаты: X = 20 Y = 30, то есть ее расположение на плоскости можно найти, отложив 20 единиц от нулевой точки системы координат в положительном направлении оси Х и 30 единиц – в положительном направлении оси Y. Соответственно точки Р2 и Р3 имеют следующие координаты:
Р2: X = -20 Y = 15 Р3: X = 40 Y = -25
|
Пример: P1: X=20, Y=30
P2: X=-20, Y=15 P3: X=40, Y=-25
В токарных станках, как правило, применяется декартова система координат с двумя осями. Эти оси всегда лежат в одной плоскости, поэтому такая система координат также называется плоской системой координат. В соответствии с правилами расположения осей декартовой системы координат плоская система координат в этом случае имеет оси X и Z.
Большинство токарных станков с ЧПУ имеет традиционную для универсальных станков компоновку, поэтому у них ось Z расположена горизонтально по оси вращения шпинделя, а ось Х относится к диаметру детали и на эскизах обычно изображается вертикально. Расстояние от данной точки до оси Z определяется как координата X, а расстояние до оси X как координата Z. Значения координат точек в токарных станках с ЧПУ могут иметь как положительные, так и отрицательные значения.
Внимание: Отсчет перемещений по оси X у токарного станка с ЧПУ модели CC-D6000E производится не в абсолютных значениях, а относительно диаметра. Другими словами, если требуется переместить суппорт по оси X на 5 мм, необходимо запрограммировать перемещение по оси X на 10 мм, так как при этом произойдет изменение диаметра заготовки на 10 мм.
Практическая часть
ЗАДАНИЕ
Практическая работа №4. Изучение конструкции роботизированной сборочной единицы системы с компьютерным управлением.
Цель работы – Познакомиться с назначением, устройством, техническими характеристиками и принципом работы РТК.
Теоретическая часть
Станок (группа станков), обслуживаемый ПР, составляет так называемый роботизированный технологический комплекс (РТК).
В состав типовых РТК включаются:
1. Промышленные роботы.
2. Металлорежущие станки.
3. Вспомогательное транспортное оборудование, включающее накопители, магазины заготовок и изделий и т.п.
В зависимости от числа станков, обслуживаемых одним ПР, различают:
1. одностаночные РТК;
2. многостаночные РТК.
Помимо указанного оборудования в состав любого РТК входят устройства управления как отдельным ПР, так и всем РТК. Число устройств управления, как правило, равно числу станков и других технологических машин (в том числе и ПР), входящих в состав РТК.
Вместе с тем для управления одностаночного РТК в ряде случаев используют общую систему управления, особенно тогда, когда управление станком и ПР осуществляется раздельно во времени.
С помощью ПР автоматизируют операции установки - снятия и межстаночного транспортирования деталей, конструкции которых должны отвечать определенным требованиям.
Детали следует группировать по конструктивно-технологическим признакам в целях использования:
|
1. типовых форм организации производства;
2. типовых технологических процессов обработки;
3. типового основного и вспомогательного оборудования.
Детали должны иметь ярко выраженные технологические базы и признаки ориентации, позволяющие организовать их транспортирование и складирование в ориентированном виде с использованием стандартизованной оснастки.
Сгруппированные детали должны иметь однородные по форме и расположению поверхности для базирования и захвата, позволяющие без дополнительной выверки устанавливать их в рабочую зону, где для их базирования и закрепления должна использоваться широкоуниверсальная технологическая оснастка.
Конструкция детали должна обеспечивать ее надежное захватывание, удержание и перенос с помощью ПР. Группирование деталей по конструктивно-технологическим признакам должно предусматривать также ограничение номенклатуры захватных устройств, допускать возможность применения широкодиапазонных захватов. В пределах одного РТК переход от манипулирования деталями одного типоразмера к манипулированию деталями другого типоразмера должен сопровождаться минимальным числом смен захватных устройств и переналадок ПР.
Для манипулирования деталями сложной конфигурации (вилки рычаги, кулисы, сложные корпуса и т.п.) в условиях многономенклатурной обработки следует создавать специальные установочные, базирующие и захватные устройства.
Для установки - снятия деталей массой свыше 500 кг целесообразно использовать манипуляторы с ручным управлением или подъемно-транспортные средства, имеющиеся в цеху.
Для комплектации РТК используют модернизированные серийные станки или станки-полуавтоматы, специально разработанные для встраивания в РТК.
Требования к станкам, встраиваемым в РТК.
Станки, встраиваемые в РТК, должны отвечать следующим требованиям.
Общие требования:
1. высокая производительность и высокий уровень концентрации операций:
2. автоматическая смена инструментов, совмещенная по времени с выполнением холостых ходов:
3. удобный отвод стружки из зоны резания, наличие устройств для дробления и уборки стружки.
Специальные требования, обусловленные работой станков совместно с ПР:
1. автоматический зажим детали;
2. автоматический поджим заготовки к патрону для правильного ее базирования;
3. автоматическое открывание и закрывание защитных экранов (щитков), ограждающих зону обработки;
4. обдув или обмыв под давлением базовых поверхностей сменных устройств для закрепления заготовок, патронов, центров, тисков, столов и т.д.;
5. контроль правильности и надежности базирования деталей в зажимных приспособлениях.
В системах управления станками необходимо предусмотреть каналы для обмена с ПР информацией о выполнении всех взаимосвязанных операций. |
Важную роль в обеспечении требуемых эксплуатационных характеристик РТК играет размерный контроль как заготовок и полуфабрикатов, поступающих на вход РТК, так и готовых изделий. На РТК первого поколения такой контроль осуществляется, как правило, рабочим-оператором (что снижает производительность РТК), а на РТК второго поколения - с помощью ПР или специальными устройствами активного контроля, которыми укомплектованы станки.
Для металлорежущих станков, используемых в составе РТК, характерно наличие разнообразной технологической оснастки, обеспечивающей требуемую точность обработки.
Универсальную станочную оснастку необходимо предварительно проверять и в ряде случаев дорабатывать для возможности ее использования в РТК. Без дополнительной конструктивной доработки можно применять: в токарных станках - центры, поводковые патроны с плавающими центрами, торцовые поводковые патроны, самоцентрирующие трехкулачковые патроны: во фрезерных, сверлильных, центровальных и протяжных станках - автоматические самозажимные тиски и приспособления с угловой фиксацией детали.
Станки ряда моделей комплектуются магнитными столами, автоматическими прихватами и т.п., которые также не нуждаются в доработке.
Стыковка ПР с металлорежущими станками, серийно выпускаемыми промышленностью, требует проведения работ по их модернизации, особенно в части электроавтоматики. Для обслуживания металлорежущих станков наиболее применимы ПР мод. М20Ц48.01, СМ40Ф2.80.01, УМ 160.80.01.
Вспомогательное оборудование, включаемое, в состав РТК:
1. транспортно-накопительные устройства, обеспечивающие накопление, хранение, ориентацию, поштучную выдачу и транспортирование деталей внутри или между РТК; базирующие (ориентирующие);
2. контрольно-измерительные устройства;
3. средства обеспечения безопасности труда и безаварийной работы оборудования.
Транспортно-накопительные устройства, как правило, не имеют между собой информационных связей и обмениваются командами с основным технологическим оборудованием и ПР, но сопрягаются с общезаводским и внутрицеховым транспортом.
Устройства, обеспечивающие безаварийную работу оборудования, служат для предотвращения аварийных ситуаций при работе ПР, а также для уменьшения тяжести последствий аварийных ситуаций, если они возникли.
Типовые РТК "станок-робот"
Вариант 1. РТК мод. АСВР-041 (рис.1), созданный на базе ПР мод СМ40Ф2. 80.01, предназначен для обработки валов диаметром до 200 и длиной до 710 мм и массой до 40 кг.
Предусмотрены три варианта работы РТК:
1. последовательная обработка деталей на станках, налаженных на выполнение разных операции;
2. параллельная обработка деталей одного наименования на станках, налаженных на выполнение одинаковой операции;
3. параллельная обработка деталей двух наименований на станках, налаженных на выполнение соответствующих операций.
Магазины (заготовок и готовых изделий) сварной конструкции выполнены в виде коробчатых направляющих, к которым крепятся планки с призматическими пазами. Планки могут устанавливаться в различных положениях для возможности размещения валов разной длины. Шаг пазов выбирается исходя из диаметра заготовок с учетом промежутков, необходимых для прохода губок захватного устройства.
Промежуточные магазины представляют собой сварные металлические конструкции с двумя направляющими, к которым крепятся планки с двумя призматическими пазами. Планки могут устанавливаться в различных положениях для возможности установки валов разной длины. Наличие валов в магазине контролируется путевыми выключателями, промежуточный магазин имеет две позиции: для вала, устанавливаемого на станке: для вала, снятого со станка. На первой позиции промежуточного магазина предусмотрен конечный выключатель, контролирующий осевое положение вала. Наличие промежуточных магазинов в РТК уменьшает время загрузки станков.
Рис.1. Планировка РТК мод. АСВР-041; 1-ПР мод. СМ40Ф2.80.01, 2-токарный станок с ЧПУ мод. 16К20Т1, 3-промежуточная позиция, 4-магазин, 5-система светозащиты, 6-электрошкаф, 7 – гидростанция ПР.
Для обеспечения безопасности обслуживающего персонала РТК оснащен информационной системой и соответствующими каналами связи с УЧПУ, что позволяет исключить возможность движения ПР в зоне нахождения человека.
Вариант 2. В РТК мод. АСВР-01, созданном на базе ПР мод. УМ160Ф2.81.01 (рис. 2), станки располагаются вдоль монорельса ПР (между его опорными колоннами).
Рис.2. Планировка РТК мод.АСВР-01; 1- магазин, 2- промежуточная позиция, 3- фрезерно-центровальный станок мод.МР-179, 4- гидростанция ПР, 5- электрошкаф, 6- ПР мод.УМ160Ф2, 7- ситстема светозащиты, 8- токарный станок с ЧПУ мод.1Б732Ф2.
Непосредственно перед станками расположены промежуточные загрузочные позиции, представляющие собой планки с парой призматических вырезов, закрепленные на направляющей плите, по которой их можно переставлять для настройки на валы нужной длины. Магазины выполнены в виде коробчатых направляющих, к которым крепятся планки с рядами призматических выемок (шаг выемок 90мм). Планки можно устанавливать в различных положениях для размещения валов разной длины. Станки в РТК работают последовательно или последовательно - параллельно, а в отдельных случаях параллельно.
РТК работает следующим образом: ПР налаживается на программы разгрузки - загрузки каждого из станков (в случае параллельной работы станков добавляются циклы перебазирования). В программах работы станков предусматриваются команды "Вызов ПР", поэтому ПР обслуживает станки в порядке поступления вызовов.
Оператор с помощью консольного крана загружает магазин заготовок и разгружает магазин готовых изделий. Краны используются также для загрузки станков при наладке или в случае остановки ПР.
РТК оснащен системой светозащиты, которая состоит из четырех секций (три с фронтальной стороны и одна с боковой, где возможен проход), создающих три зоны. Границы между зонами не ограждаются, так как проходы между ними заняты магазинами.
Вариант 3. РТК мод. И5.01 (рис. 3), предназначенный для обработки корпусов гидроблоков, по комплексности охвата технологического процесса приближается к гибкой производственной системе. РТК включает в себя склад-накопитель (что в сочетании с большим временем цикла обработки деталей характерно для тяжелых корпусных деталей), обеспечивает длительное по времени функционирование комплекса без остановок для восстановления запаса заготовок.
Рис. 3. Планировка РТК мод.ИР5.02: 1- ПР мод.УМ160Ф2, 2- многоцелевой станок мод.ИР500МФ4, 3- манипулятор, 4- роликовый конвейер, 5- поворотный стол, 6- ограждение,7- кран-штабелер, 8- склад - накопитель.
Вариант 4. РТК мод. БРСК-01 (рис.4) предназначен для токарной обработки (в патроне) широкой номенклатуры деталей диаметром 40-160 мм и массой до 10 кг в условиях мелкосерийного и серийного производства. В состав РТК входят токарно-револьверный станок мод. 1В340ФЗО, ПР мод. М20Ц48.01, дисковый магазин для деталей и ограждение, обеспечивающее безопасность работы.
Рис.4. Планировка РТК мод. БРСК - 1: 1 - ПР мод. М20Ц48.01.2, 2 - магазин-накопитель(поворотный стол), 3 - токарно-револьверный станок мод. 1В340Ф30 с ЧПУ, 4 - устройство управления ПР.
Практическая часть
Ответить на контрольные вопросы:
1. Назначение и классификация РТК. Место РТК в гибкой автоматизации производства.
2. Организационные уровни сложности ГПС
3. Основные схемы взаимодействия промышленных роботов с основным и вспомогательным оборудованием. Единичное обслуживание оборудования
4.Типовые структуры и состав технологического оборудования РТК
5. Ориентирующие устройства. Классификация и основные узлы
6. Бункерные загрузочно-ориентирующие устройства
7. Накопительные и питательные устройства
8. Транспортные устройства
9. Другие вспомогательные устройства РТК
Практическая работа №5. Изучение конструкции промышленного робота.
Цель работы – Ознакомиться с возможностями промышленных роботов, основными элементами конструкций промышленных роботов.
Теоретическая часть
Общие сведения о роботах
В широком понимании робот может быть определен как техническая система, способная замещать человека или помогать ему в выполнении различных задач. Робот выполняет две функции, реализуемые различными устройствами: информационными и исполнительными.
Информационные устройства вырабатывают команды в зависимости от результатов обработки поступающей информации трех видов: цели выполняемой задачи, измерений текущего состояния исполнительного устройства и наблюдений над рабочей средой, находящейся в непосредственной близости или на расстоянии от робота.
Исполнительные устройства воздействуют на рабочую среду в соответствии с командами путем преобразования и расходования получаемой извне энергии. Они состоят из следующих конструктивных элементов: органов взаимодействия с рабочей средой, органов манипулятора (звенья, сочленения), модуляторов энергии (усилители, распределители), преобразователей энергии (двигатели, силовые установки), датчиков (рисунок 1.1).
Рисунок 1.1-Принципиальная схема процесса принятия решений
и выполнения действий роботом
|
|
Своеобразие русской архитектуры: Основной материал – дерево – быстрота постройки, но недолговечность и необходимость деления...
История развития пистолетов-пулеметов: Предпосылкой для возникновения пистолетов-пулеметов послужила давняя тенденция тяготения винтовок...
Опора деревянной одностоечной и способы укрепление угловых опор: Опоры ВЛ - конструкции, предназначенные для поддерживания проводов на необходимой высоте над землей, водой...
Архитектура электронного правительства: Единая архитектура – это методологический подход при создании системы управления государства, который строится...
© cyberpedia.su 2017-2024 - Не является автором материалов. Исключительное право сохранено за автором текста.
Если вы не хотите, чтобы данный материал был у нас на сайте, перейдите по ссылке: Нарушение авторских прав. Мы поможем в написании вашей работы!