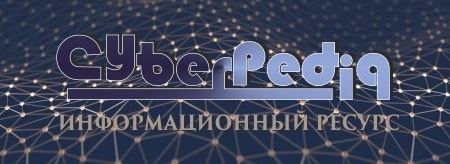
Наброски и зарисовки растений, плодов, цветов: Освоить конструктивное построение структуры дерева через зарисовки отдельных деревьев, группы деревьев...
История развития пистолетов-пулеметов: Предпосылкой для возникновения пистолетов-пулеметов послужила давняя тенденция тяготения винтовок...
Топ:
Эволюция кровеносной системы позвоночных животных: Биологическая эволюция – необратимый процесс исторического развития живой природы...
Устройство и оснащение процедурного кабинета: Решающая роль в обеспечении правильного лечения пациентов отводится процедурной медсестре...
Интересное:
Средства для ингаляционного наркоза: Наркоз наступает в результате вдыхания (ингаляции) средств, которое осуществляют или с помощью маски...
Уполаживание и террасирование склонов: Если глубина оврага более 5 м необходимо устройство берм. Варианты использования оврагов для градостроительных целей...
Лечение прогрессирующих форм рака: Одним из наиболее важных достижений экспериментальной химиотерапии опухолей, начатой в 60-х и реализованной в 70-х годах, является...
Дисциплины:
![]() |
![]() |
5.00
из
|
Заказать работу |
|
|
ОП.15. Станки с ЧПУ и РТК
По специальности: 15.02.08 «Технология машиностроения»
201 г.
Методические указания к выполнению практических работ по учебной дисциплине ОП.15 «Станки с ЧПУ и РТК» разработаны на основе Федерального государственного образовательного стандарта (далее – ФГОС) по специальности (специальностям) среднего профессионального образования (далее СПО) 15.02.08 «Технология машиностроения» для профессиональных образовательных организаций.
Автор:
Чемезов Денис Александрович, преподаватель.
Рецензенты:
СОДЕРЖАНИЕ
1. Краткая характеристика дисциплины, ее цели и задачи. Место практических работ в курсе дисциплины | 4 |
2. Организация и порядок проведения практических работ | 4 |
3. Техника безопасности при выполнении практических работ | 4 |
4. Общие указания по выполнению практических работ | 5 |
5. Основные требования к обработке результатов расчетов и оформлению отчетов | 5 |
6. Перечень практических заданий | 7 |
7. Методические указания к выполнению практических работ | 8 |
8. Библиографический список | 131 |
КРАТКАЯ ХАРАКТЕРИСТИКА ДИСЦИПЛИНЫ, ЕЕ ЦЕЛИ И ЗАДАЧИ. МЕСТО ПРАКТИЧЕСКИХ РАБОТ В КУРСЕ ДИСЦИПЛИНЫ
Станки с ЧПУ и РТК изучается как вариативный учебный предмет при освоении специальности СПО «Технология машиностроения».
Содержание рабочей программы дисциплины, согласовано с требованиями Федерального государственного образовательного стандарта (далее – ФГОС) по специальности СПО 15.02.08 «Технология машиностроения».
Практические занятия составляют 43 часа.
Выполнение практических работ поможет студентам освоить обязательный минимум содержания дисциплины, подготовиться к сдаче дифференцированного зачета.
|
ОРГАНИЗАЦИЯ И ПОРЯДОК ПРОВЕДЕНИЯ ПРАКТИЧЕСКИХ РАБОТ
Практические работы проводятся после изучения теоретического материала в учебном кабинете специальных дисциплин. Обучающиеся должны иметь методические рекомендации по выполнению практических работ, конспекты лекций, измерительные и чертежные инструменты, средство для вычислений.
ТЕХНИКА БЕЗОПАСНОСТИ ПРИ ВЫПОЛНЕНИИ ПРАКТИЧЕСКИХ РАБОТ
При работе в учебном кабинете запрещается:
• находиться в кабинете в отсутствии преподавателя и на перемене;
• вставать со своего места и ходить по кабинету без разрешения преподавателя;
• размещать на рабочем месте посторонние предметы.
• Обучающийся обязан:
• спокойно, не торопясь, не задевая столы, входить в кабинет и занять отведенное ему место,
• во время перемены покинуть кабинет,
• работать на одном, закрепленном за ним месте,
• приступать к работе по указанию преподавателя,
• по окончанию работы сдать выданные материалы преподавателю,
• привести свое рабочее место в порядок.
ОБЩИЕ УКАЗАНИЯ ПО ВЫПОЛНЕНИЮ ПРАКТИЧЕСКИХ РАБОТ
Обучающийся должен решить задачи по варианту, номер которого укажет преподаватель.
При выполнении практических работ надо придерживаться следующих правил:
1. Практическую работу следует выполнять в тетради чернилами черного или синего цвета, оставляя поля.
2. На обложке тетради должны быть ясно написаны фамилия обучающегося, его инициалы, номер специальности, название дисциплины, номер подгруппы.
3. В заголовке работы должны быть указаны номер практической работы, тема практической работы, номер варианта.
4. В работу должны быть включены задачи, указанные в практической работе, строго по предложенному варианту.
5. Перед решением каждой задачи надо выписать полностью ее условие.
6. Решение задач следует излагать подробно и аккуратно, объясняя и мотивируя все действия по ходу решения и делая необходимые рисунки.
|
7. После получения проверенной работы, студент должен исправить все отмеченные ошибки.
ОСНОВНЫЕ ТРЕБОВАНИЯ К ОБРАБОТКЕ РЕЗУЛЬТАТОВ РАСЧЕТОВ И ОФОРМЛЕНИЮ ОТЧЕТОВ
Отчет по практической работе должен содержать:
1. Номер и тему практической работы, номер варианта.
2. Номер задачи и ее условие.
3. Подробное решение каждой задачи.
4. Полный ответ к каждой задаче.
Критериями оценки результатов работы студентов являются:
• уровень усвоения студентом учебного материала;
• умение студента использовать теоретические знания при выполнении практических задач;
• сформированность ключевых компетенций;
• обоснованность и четкость изложения материала;
• уровень оформления работы.
Анализ результатов.
Если практическая работа выполнена в полном объеме и правильно оформлена, то ставится оценка «5».
Если практическая работа выполнена более чем на 75%, ставится оценка «4».
Если практическая работа выполнена более чем на 60%, ставится оценка «3».
В противном случае работа не засчитывается.
Дидактический материал для выполнения практической работы:
Методические рекомендации для выполнения практических работ, тетрадь для практических работ, конспект лекций.
ПЕРЕЧЕНЬ ПРАКТИЧЕСКИХ ЗАДАНИЙ ПО ДИСЦИПЛИНЕ «СТАНКИ С ЧПУ И РТК»
1. Практическая работа №1. Понятие о роботизированном технологическом комплексе. Структуры и компоновки РТК.
2. Практическая работа №2. Характеристика и особенности станков с ЧПУ. Функциональная схема станка с ЧПУ.
3. Практическая работа №3. Системы координат станков с ЧПУ. Способы и начало отсчета координат.
4. Практическая работа №4. Изучение конструкции роботизированной сборочной единицы системы с компьютерным управлением.
5. Практическая работа №5. Изучение конструкции промышленного робота.
6. Практическая работа №6. Изучение конструкций малогабаритных токарных станков с компьютерным управлением.
7. Практическая работа №7. Изучение конструкций малогабаритных фрезерных станков с компьютерным управлением.
8. Практическая работа №8. Изучение специализированных компьютерных программ для управления малогабаритными станками.
9. Практическая работа №9. Конструкция и кинематика токарного станка с ЧПУ.
|
10. Практическая работа №10. Конструкция и кинематика многоцелевого станка с ЧПУ.
11. Практическая работа №11. Изучение устройства ЧПУ для управления токарным станком.
12. Практическая работа №12. Построение слов в кадре управляющей программы.
13. Практическая работа №13. Автоматизация проектирования управляющей программы.
14. Практическая работа №14. Программирование для малогабаритных токарных станков с компьютерным управлением.
15. Практическая работа №15. Программирование для малогабаритных фрезерных станков с компьютерным управлением.
16. Практическая работа №16. Программирование для малогабаритных станков с компьютерным управлением в автоматизированной системе ADEM.
17. Практическая работа №17. Программирование токарных станков с устройством ЧПУ Siemens Sinumerik.
Теоретическая часть
Процессу внедрения промышленных роботов (ПР) в производство предшествует этап технологической подготовки, связанный со спецификой использования робота. Эта специфика существенным образом отражается на компоновке оборудования РТСК. Возможны два варианта компоновки:
1) ПР встраивается в существующую технологическую линию, когда требуется большая универсальность самого робота и наличие у него элементов адаптации, а также доработка технологического оборудования под применяемый тип робота;
2) ПР проектируется совместно с технологической линией как составная часть сборочного технологического оборудования.
Последний вариант наиболее рационален и перспективен, так как позволяет в максимальной степени использовать преимущества модульного принципа построения ПР и принцип агрегатирования из унифицированных элементов при создании РТСК. Особое значение этот фактор имеет при разработке РТСК, учитывая разнообразие сборочных процессов. Особенности роботизируемого процесса оказывают одновременно влияние и на кинематику обслуживающих роботов, и на размещение технологического оборудования и компоновку ПСРТК в целом.
Путем анализа сборочных операций, выполняемых с применением ПР, получено четыре типовых варианта компоновки сборочных РТК, представленные на рис.1. Все РТК включают в себя следующие типовые элементы: ПР 2; рабочие позиции 4 (на которых выполняются операции сборки); питатели 1 (служащие для подачи собираемых деталей в ориентированном положении); магазины 3 с комплектами сборочных инструментов.
|
В РТК (рис.1, а) технологический процесс сборки делится на две операции, причем операция 2 выполняется по двум позициям. В связи с этим возникает необходимость в организации трех одинаковых позиций сборки для обеспечения требуемой производительности отдельных операций. Передача полуфабрикатов после выполнения операции 1 на позицию, где выполняется операция 2, осуществляется (в таре) общецеховым транспортом. Такая компоновка обеспечивает сокращение простоев оборудования и, как следствие, повышение производительности РТК.
В РТК (рис.1, б) один ПР последовательно выполняет все операции сборки до получения полностью собранного изделия. При такой компоновке используют универсальные ПР и рабочие позиции в целях их быстрой переналадки при переходе на сборку другого изделия.
В РТК (рис.1, в) используют специальные ПР упрощенной конструкции с небольшим числом степеней подвижности. Собираемые детали перемещаются транспортером 5 между несколькими позициями сборки, работающими параллельно. Линейное расположение оборудования обеспечивает выполнение технологических функций и пустоту транспортной системы. Жесткая связь между рабочими позициями обусловливает остановку РТК при выходе из строя ПР или другого оборудования.
Особенностью РТК (рис.1, г) является то, что сборочные операции (с учетом их специфики) максимально сконцентрированы на отдельных рабочих позициях, причем на ряде позиций сборочные операции выполняются одновременно несколькими ПР. Транспортирование полуфабрикатов между рабочими позициями 4 осуществляется конвейером 5. Связь между отдельными рабочими позициями гибкая.
Варианты компоновки РТСК. На рис.2, а оборудование расставлено по дуге окружности, и для его обслуживания плечо робота 4 осуществляет возвратно-поступательные и вращательные движения. При переукладке деталей (узлов) с подводящего конвейера (позиция А) на конвейер (позиция D) стационарный робот 4 на фиксированных позициях 1, 2, 3 осуществляет сопутствующие, вспомогательные или контрольные операции: лужение, мойку, травление, гибку, рихтовку, контроль параметров и др. Компоновка комплекса по схеме рис.2, б предусматривает расположение оборудования в линию, и робот 4 снабжен модулем глобального перемещения между транспортными конвейерами А, В и D. Такая компоновка оборудования предполагает автоматизацию основных (5,6) и вспомогательных (1, 2,3) операций, которые обслуживает робот.
|
Наличие упорядоченной среды позволяет роботу 4 (рис.2, в) не только обслуживать ее, аналогично схеме (рис.2, а), но и транспортировать узел, укомплектованный на позициях 1, 2, 3, на позицию 5, 6 фиксирующей операции (развальцовка, пайка, сварка, запрессовка), операции контроля, подгонки, покраски и т.п. В отдельных случаях робот может выполнять эти операции самостоятельно.
Если синхронизация транспортных и основных операций невозможна или когда время, отведенное на операцию, не позволяет осуществлять последовательную комплектацию сборочной единицы за счет повторных возвратно-поступательных и вращательных движений рабочих органов робота, то обслуживаемая среда организуется по схеме, показанной на рис.2, г. Здесь роботы 4 и 11 попеременно в синхронизированном ритме устанавливают на позицию сборки б укомплектованные сборочные единицы, которые окончательно собираются в изделие специализированным сборочным оборудованием или одним из роботов. Кассеты с комплектующими деталями подаются на позиции 1, 3, 8, 10 конвейерами А, В, А' и В'.
Укомплектованной (собранное) изделие поступает на отводящий конвейер D. Позиции 2, 5 и 7, 9 используются для выполнения вспомогательных и сопутствующих операций. Технологический цикл РТК может быть сокращен за счет уменьшения вспомогательного времени, вызванного загрузкой и разгрузкой рабочих машин и межпозиционным транспортированием объектов (деталей, узлов). С этой целью используются двурукие ПР (рис.2, д, е), таким образом цикл обслуживания рабочих позиций сокращается вдвое за счет исключения двойных поворотных ходов плеч робота 4.
Рис.1 - Типовые варианты компоновок сборочных РТК
Рис.2 - Варианты компоновки РТСК.
Практическая часть
Ответить на контрольные вопросы:
1. Устройство РТК.
2. Роли роботов в РТК.
3. Компоновки РТК.
Практическая работа №2. Характеристика и особенности станков с ЧПУ. Функциональная схема станка с ЧПУ.
Цель работы – ознакомление с характеристикой и особенностями станков с ЧПУ.
Теоретическая часть
Классификация систем с ЧПУ
Как уже отмечалось, на станке с ЧПУ в систему автоматического управления вводится информация в виде чисел, характеризующих все элементы его работы, включая траекторию движения и позиционирование заготовки или инструмента. По технологическому назначению различают контурное управление, позиционное управление и комбинированное.
При контурном (непрерывном) управлении в каждый момент времени обеспечивается координация относительного расположения инструмента и заготовки, как по пути, так и по скорости перемещения.
Таким образом, программируется не только величина перемещения по каждой координате, но и закон перемещения, что особенно важно для обработки фасонных поверхностей. Контурные устройства с ЧПУ предназначены для токарных и фрезерных станков, обрабатывающих изделия со сложным контуром.
При позиционном (координатном) управлении обеспечивается лишь относительное перемещение инструмента и заготовки в заданную позицию.
Таким образом, программируются отдельные дискретные положения инструмента на плоскости или в пространстве. Позиционные системы используют на сверлильных, координатно-расточных и т.п. станках.
Обозначение станков с ЧПУ
Основное обозначение аналогично традиционным станкам с ручным управлением. К основному обозначению добавляется информация в следующем порядке:
а) конструктивная особенность:
Р – смена инструмента поворотом револьверной головки;
М – смена инструмента из магазина инструментов;
б) разновидность системы ЧПУ:
Ц – цикловое управление;
Ф1 – управление цифровой индикацией положения рабочих органов и ручным вводом данных (преднабором координат);
Ф2 – позиционное управление;
Ф3 – контурное управление;
Ф4 – смешанное, или комбинированное управление.
Примеры полных обозначений некоторых станков с ЧПУ приведены в конце лекции.
Практическая часть
Ответить на контрольные вопросы:
1. В чём преимущества и недостатки станков с кулачковой системой управления в сравнении со станками с ручным управлением?
2. В чём общность и различия между кулачковой и числовой системами программного управления?
3. В чём преимущества станков с ЧПУ в сравнении со станками с ручным управлением?
4. Каковы особенности токарно-револьверного станка модели 1325Ф30?
5. Каковы особенности вертикально-сверлильного станка модели 2Р135Ф2?
6. Что влияет на выбор последовательности обработки отверстий на станке 2Р135Ф2?
7. Сравните станки моделей 1325Ф30 и 2Р135Ф2: по инструменту, обрабатываемым заготовкам, системам управления, приспособлениям, видам движений.
8. Каковы особенности вертикально-фрезерного станка модели 6Р13Ф3?
9. Какая дополнительная информация указывается в обозначении моделей станков с ЧПУ?
10. В чём принципиальное различие между контурной и позиционной системами ЧПУ?
11. В чём особенность вспомогательного инструмента для станков с ЧПУ?
12. Укажите 34 требования к технологичности изделий, обрабатываемых на токарных станках с ЧПУ.
13. Укажите 34 требования к технологичности изделий, обрабатываемых на фрезерных и сверлильных станках с ЧПУ.
14. Дать краткую характеристику технологической оснастки для станков с ЧПУ.
15. Поясните назначение и принцип действия быстросменного патрона с шариковым захватом.
Практическая работа №3. Системы координат станков с ЧПУ. Способы и начало отсчета координат.
Цель работы:
Дать учащимся понятие о системе координат токарного станка с ЧПУ.
Научить определять координаты точек в системе координат токарного станка с ЧПУ.
Научить назначать координаты характерных точек у заданного профиля токарной детали.
Теоретическая часть
Обработка заготовки на станке с ЧПУ производится по командам управляющей программы, которая в числовом выражении задает величину каждого перемещения исполнительных органов. Поэтому работа станка с ЧПУ в принципе невозможна без определенной системы координат, с помощью которой определяются координаты любой точки в пространстве в границах рабочей зоны станка. При этом система ЧПУ станка должна распознавать закодированные координаты характерных точек, с помощью которых описываются движения исполнительных органов станка.
Декартова система координат
Для станков с ЧПУ принята единая система координат, рекомендуемая Международной организацией по стандартизации ИСО: прямоугольная система координат, которую часто называют также декартовой системой координат. Эта система координат в общем случае содержит три оси X, Y и Z, имеющие общую точку пересечения и одинаковый геометрический масштаб, и расположенные взаимно перпендикулярно друг к другу в пространстве.
Координатные оси в станках с ЧПУ всегда располагаются параллельно направляющим станка. В зависимости от типа станка расположение осей координат в пространстве может быть различным, но есть следующие общие правила:
1) Ось Z всегда совмещена с осью вращения шпинделя. Ее положительное направление всегда совпадает с направлением перемещения от устройства для крепления заготовки к режущему инструменту.
2) Если у станка есть хотя бы одна горизонтальная ось, то
(если это не ось шпинделя) это будет обязательно ось X.
3) Если ось Z расположена горизонтально, то положительным направлением оси X является направление вправо, если встать лицом к левому, относительно передней плоскости, торцу станка. Передняя плоскость станка – сторона, с которой располагаются пульт и основные органы управления станком.
4) Если ось Z расположена вертикально, то положительным направлением оси X является направление вправо, если встать лицом к передней плоскости станка.
Для определения положительного направления оси Y необходимо повернуть ось X на 90 вокруг оси Z по часовой стрелке, если смотреть вдоль оси Z в положительном направлении.
Нулевая (начальная) точка системы координат – точка пересечения координатных осей. Координаты точки пересечения по каждой оси всегда равны нулю.
Дана плоская система координат с осями X и Y.
Точка Р1 имеет следующие координаты: X = 20 Y = 30, то есть ее расположение на плоскости можно найти, отложив 20 единиц от нулевой точки системы координат в положительном направлении оси Х и 30 единиц – в положительном направлении оси Y. Соответственно точки Р2 и Р3 имеют следующие координаты:
Р2: X = -20 Y = 15 Р3: X = 40 Y = -25
Пример: P1: X=20, Y=30
P2: X=-20, Y=15 P3: X=40, Y=-25
В токарных станках, как правило, применяется декартова система координат с двумя осями. Эти оси всегда лежат в одной плоскости, поэтому такая система координат также называется плоской системой координат. В соответствии с правилами расположения осей декартовой системы координат плоская система координат в этом случае имеет оси X и Z.
Большинство токарных станков с ЧПУ имеет традиционную для универсальных станков компоновку, поэтому у них ось Z расположена горизонтально по оси вращения шпинделя, а ось Х относится к диаметру детали и на эскизах обычно изображается вертикально. Расстояние от данной точки до оси Z определяется как координата X, а расстояние до оси X как координата Z. Значения координат точек в токарных станках с ЧПУ могут иметь как положительные, так и отрицательные значения.
Внимание: Отсчет перемещений по оси X у токарного станка с ЧПУ модели CC-D6000E производится не в абсолютных значениях, а относительно диаметра. Другими словами, если требуется переместить суппорт по оси X на 5 мм, необходимо запрограммировать перемещение по оси X на 10 мм, так как при этом произойдет изменение диаметра заготовки на 10 мм.
Практическая часть
ЗАДАНИЕ
Практическая работа №4. Изучение конструкции роботизированной сборочной единицы системы с компьютерным управлением.
Цель работы – Познакомиться с назначением, устройством, техническими характеристиками и принципом работы РТК.
Теоретическая часть
Станок (группа станков), обслуживаемый ПР, составляет так называемый роботизированный технологический комплекс (РТК).
В состав типовых РТК включаются:
1. Промышленные роботы.
2. Металлорежущие станки.
3. Вспомогательное транспортное оборудование, включающее накопители, магазины заготовок и изделий и т.п.
В зависимости от числа станков, обслуживаемых одним ПР, различают:
1. одностаночные РТК;
2. многостаночные РТК.
Помимо указанного оборудования в состав любого РТК входят устройства управления как отдельным ПР, так и всем РТК. Число устройств управления, как правило, равно числу станков и других технологических машин (в том числе и ПР), входящих в состав РТК.
Вместе с тем для управления одностаночного РТК в ряде случаев используют общую систему управления, особенно тогда, когда управление станком и ПР осуществляется раздельно во времени.
С помощью ПР автоматизируют операции установки - снятия и межстаночного транспортирования деталей, конструкции которых должны отвечать определенным требованиям.
Детали следует группировать по конструктивно-технологическим признакам в целях использования:
1. типовых форм организации производства;
2. типовых технологических процессов обработки;
3. типового основного и вспомогательного оборудования.
Детали должны иметь ярко выраженные технологические базы и признаки ориентации, позволяющие организовать их транспортирование и складирование в ориентированном виде с использованием стандартизованной оснастки.
Сгруппированные детали должны иметь однородные по форме и расположению поверхности для базирования и захвата, позволяющие без дополнительной выверки устанавливать их в рабочую зону, где для их базирования и закрепления должна использоваться широкоуниверсальная технологическая оснастка.
Конструкция детали должна обеспечивать ее надежное захватывание, удержание и перенос с помощью ПР. Группирование деталей по конструктивно-технологическим признакам должно предусматривать также ограничение номенклатуры захватных устройств, допускать возможность применения широкодиапазонных захватов. В пределах одного РТК переход от манипулирования деталями одного типоразмера к манипулированию деталями другого типоразмера должен сопровождаться минимальным числом смен захватных устройств и переналадок ПР.
Для манипулирования деталями сложной конфигурации (вилки рычаги, кулисы, сложные корпуса и т.п.) в условиях многономенклатурной обработки следует создавать специальные установочные, базирующие и захватные устройства.
Для установки - снятия деталей массой свыше 500 кг целесообразно использовать манипуляторы с ручным управлением или подъемно-транспортные средства, имеющиеся в цеху.
Для комплектации РТК используют модернизированные серийные станки или станки-полуавтоматы, специально разработанные для встраивания в РТК.
Требования к станкам, встраиваемым в РТК.
Станки, встраиваемые в РТК, должны отвечать следующим требованиям.
Общие требования:
1. высокая производительность и высокий уровень концентрации операций:
2. автоматическая смена инструментов, совмещенная по времени с выполнением холостых ходов:
3. удобный отвод стружки из зоны резания, наличие устройств для дробления и уборки стружки.
Специальные требования, обусловленные работой станков совместно с ПР:
1. автоматический зажим детали;
2. автоматический поджим заготовки к патрону для правильного ее базирования;
3. автоматическое открывание и закрывание защитных экранов (щитков), ограждающих зону обработки;
4. обдув или обмыв под давлением базовых поверхностей сменных устройств для закрепления заготовок, патронов, центров, тисков, столов и т.д.;
5. контроль правильности и надежности базирования деталей в зажимных приспособлениях.
В системах управления станками необходимо предусмотреть каналы для обмена с ПР информацией о выполнении всех взаимосвязанных операций. |
Важную роль в обеспечении требуемых эксплуатационных характеристик РТК играет размерный контроль как заготовок и полуфабрикатов, поступающих на вход РТК, так и готовых изделий. На РТК первого поколения такой контроль осуществляется, как правило, рабочим-оператором (что снижает производительность РТК), а на РТК второго поколения - с помощью ПР или специальными устройствами активного контроля, которыми укомплектованы станки.
Для металлорежущих станков, используемых в составе РТК, характерно наличие разнообразной технологической оснастки, обеспечивающей требуемую точность обработки.
Универсальную станочную оснастку необходимо предварительно проверять и в ряде случаев дорабатывать для возможности ее использования в РТК. Без дополнительной конструктивной доработки можно применять: в токарных станках - центры, поводковые патроны с плавающими центрами, торцовые поводковые патроны, самоцентрирующие трехкулачковые патроны: во фрезерных, сверлильных, центровальных и протяжных станках - автоматические самозажимные тиски и приспособления с угловой фиксацией детали.
Станки ряда моделей комплектуются магнитными столами, автоматическими прихватами и т.п., которые также не нуждаются в доработке.
Стыковка ПР с металлорежущими станками, серийно выпускаемыми промышленностью, требует проведения работ по их модернизации, особенно в части электроавтоматики. Для обслуживания металлорежущих станков наиболее применимы ПР мод. М20Ц48.01, СМ40Ф2.80.01, УМ 160.80.01.
Вспомогательное оборудование, включаемое, в состав РТК:
1. транспортно-накопительные устройства, обеспечивающие накопление, хранение, ориентацию, поштучную выдачу и транспортирование деталей внутри или между РТК; базирующие (ориентирующие);
2. контрольно-измерительные устройства;
3. средства обеспечения безопасности труда и безаварийной работы оборудования.
Транспортно-накопительные устройства, как правило, не имеют между собой информационных связей и обмениваются командами с основным технологическим оборудованием и ПР, но сопрягаются с общезаводским и внутрицеховым транспортом.
Устройства, обеспечивающие безаварийную работу оборудования, служат для предотвращения аварийных ситуаций при работе ПР, а также для уменьшения тяжести последствий аварийных ситуаций, если они возникли.
Типовые РТК "станок-робот"
Вариант 1. РТК мод. АСВР-041 (рис.1), созданный на базе ПР мод СМ40Ф2. 80.01, предназначен для обработки валов диаметром до 200 и длиной до 710 мм и массой до 40 кг.
Предусмотрены три варианта работы РТК:
1. последовательная обработка деталей на станках, налаженных на выполнение разных операции;
2. параллельная обработка деталей одного наименования на станках, налаженных на выполнение одинаковой операции;
3. параллельная обработка деталей двух наименований на станках, налаженных на выполнение соответствующих операций.
Магазины (заготовок и готовых изделий) сварной конструкции выполнены в виде коробчатых направляющих, к которым крепятся планки с призматическими пазами. Планки могут устанавливаться в различных положениях для возможности размещения валов разной длины. Шаг пазов выбирается исходя из диаметра заготовок с учетом промежутков, необходимых для прохода губок захватного устройства.
Промежуточные магазины представляют собой сварные металлические конструкции с двумя направляющими, к которым крепятся планки с двумя призматическими пазами. Планки могут устанавливаться в различных положениях для возможности установки валов разной длины. Наличие валов в магазине контролируется путевыми выключателями, промежуточный магазин имеет две позиции: для вала, устанавливаемого на станке: для вала, снятого со станка. На первой позиции промежуточного магазина предусмотрен конечный выключатель, контролирующий осевое положение вала. Наличие промежуточных магазинов в РТК уменьшает время загрузки станков.
Рис.1. Планировка РТК мод. АСВР-041; 1-ПР мод. СМ40Ф2.80.01, 2-токарный станок с ЧПУ мод. 16К20Т1, 3-промежуточная позиция, 4-магазин, 5-система светозащиты, 6-электрошкаф, 7 – гидростанция ПР.
Для обеспечения безопасности обслуживающего персонала РТК оснащен информационной системой и соответствующими каналами связи с УЧПУ, что позволяет исключить возможность движения ПР в зоне нахождения человека.
Вариант 2. В РТК мод. АСВР-01, созданном на базе ПР мод. УМ160Ф2.81.01 (рис. 2), станки располагаются вдоль монорельса ПР (между его опорными колоннами).
Рис.2. Планировка РТК мод.АСВР-01; 1- магазин, 2- промежуточная позиция, 3- фрезерно-центровальный станок мод.МР-179, 4- гидростанция ПР, 5- электрошкаф, 6- ПР мод.УМ160Ф2, 7- ситстема светозащиты, 8- токарный станок с ЧПУ мод.1Б732Ф2.
Непосредственно перед станками расположены промежуточные загрузочные позиции, представляющие собой планки с парой призматических вырезов, закрепленные на направляющей плите, по которой их можно переставлять для настройки на валы нужной длины. Магазины выполнены в виде коробчатых направляющих, к которым крепятся планки с рядами призматических выемок (шаг выемок 90мм). Планки можно устанавливать в различных положениях для размещения валов разной длины. Станки в РТК работают последовательно или последовательно - параллельно, а в отдельных случаях параллельно.
РТК работает следующим образом: ПР налаживается на программы разгрузки - загрузки каждого из станков (в случае параллельной работы станков добавляются циклы перебазирования). В программах работы станков предусматриваются команды "Вызов ПР", поэтому ПР обслуживает станки в порядке поступления вызовов.
Оператор с помощью консольного крана загружает магазин заготовок и разгружает магазин готовых изделий. Краны используются также для загрузки станков при наладке или в случае остановки ПР.
РТК оснащен системой светозащиты, которая состоит из четырех секций (три с фронтальной стороны и одна с боковой, где возможен проход), создающих три зоны. Границы между зонами не ограждаются, так как проходы между ними заняты магазинами.
Вариант 3. РТК мод. И5.01 (рис. 3), предназначенный для обработки корпусов гидроблоков, по комплексности охвата технологического процесса приближается к гибкой производственной системе. РТК включает в себя склад-накопитель (что в сочетании с большим временем цикла обработки деталей характерно для тяжелых корпусных деталей), обеспечивает длительное по времени функционирование комплекса без остановок для восстановления запаса заготовок.
Рис. 3. Планировка РТК мод.ИР5.02: 1- ПР мод.УМ160Ф2, 2- многоцелевой станок мод.ИР500МФ4, 3- манипулятор, 4- роликовый конвейер, 5- поворотный стол, 6- ограждение,7- кран-штабелер, 8- склад - накопитель.
Вариант 4. РТК мод. БРСК-01 (рис.4) предназначен для токарной обработки (в патроне) широкой номенклатуры деталей диаметром 40-160 мм и массой до 10 кг в условиях мелкосерийного и серийного производства. В состав РТК входят токарно-револьверный станок мод. 1В340ФЗО, ПР мод. М20Ц48.01, дисковый магазин для деталей и ограждение, обеспечивающее безопасность работы.
Рис.4. Планировка РТК мод. БРСК - 1: 1 - ПР мод. М20Ц48.01.2, 2 - магазин-накопитель(поворотный стол), 3 - токарно-револьверный станок мод. 1В340Ф30 с ЧПУ, 4 - устройство управления ПР.
Практическая часть
Ответить на контрольные вопросы:
1. Назначение и классификация РТК. Место РТК в гибкой автоматизации производства.
2. Организационные уровни сложности ГПС
3. Основные схемы взаимодействия промышленных роботов с основным и вспомогательным оборудованием. Единичное обслуживание оборудования
4.Типовые структуры и состав технологического оборудования РТК
5. Ориентирующие устройства. Классификация и основные узлы
6. Бункерные загрузочно-ориентирующие устройства
7. Накопительные и питательные устройства
8. Транспортные устройства
9. Другие вспомогательные устройства РТК
Практическая работа №5. Изучение конструкции промышленного робота.
Цель работы – Ознакомиться с возможностями промышленных роботов, основными элементами конструкций промышленных роботов.
Теоретическая часть
Общие сведения о роботах
В широком понимании робот может быть определен как техническая система, способная замещать человека или помогать ему в выполнении различных задач. Робот выполняет две функции, реализуемые различными устройствами: информационными и исполнительными.
Информационные устройства вырабатывают команды в зависимости от результатов обработки поступающей информации трех видов: цели выполняемой задачи, измерений текущего состояния исполнительного устройства и наблюдений над рабочей средой, находящейся в непосредственной близости или на расстоянии от робота.
Исполнительные устройства воздействуют на рабочую среду в соответствии с командами путем преобразования и расходования получаемой извне энергии. Они состоят из следующих конструктивных элемен
|
|
Особенности сооружения опор в сложных условиях: Сооружение ВЛ в районах с суровыми климатическими и тяжелыми геологическими условиями...
История развития пистолетов-пулеметов: Предпосылкой для возникновения пистолетов-пулеметов послужила давняя тенденция тяготения винтовок...
Эмиссия газов от очистных сооружений канализации: В последние годы внимание мирового сообщества сосредоточено на экологических проблемах...
Общие условия выбора системы дренажа: Система дренажа выбирается в зависимости от характера защищаемого...
© cyberpedia.su 2017-2024 - Не является автором материалов. Исключительное право сохранено за автором текста.
Если вы не хотите, чтобы данный материал был у нас на сайте, перейдите по ссылке: Нарушение авторских прав. Мы поможем в написании вашей работы!