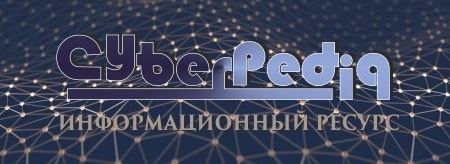
История развития хранилищ для нефти: Первые склады нефти появились в XVII веке. Они представляли собой землянные ямы-амбара глубиной 4…5 м...
Своеобразие русской архитектуры: Основной материал – дерево – быстрота постройки, но недолговечность и необходимость деления...
Топ:
Эволюция кровеносной системы позвоночных животных: Биологическая эволюция – необратимый процесс исторического развития живой природы...
Оценка эффективности инструментов коммуникационной политики: Внешние коммуникации - обмен информацией между организацией и её внешней средой...
Проблема типологии научных революций: Глобальные научные революции и типы научной рациональности...
Интересное:
Инженерная защита территорий, зданий и сооружений от опасных геологических процессов: Изучение оползневых явлений, оценка устойчивости склонов и проектирование противооползневых сооружений — актуальнейшие задачи, стоящие перед отечественными...
Что нужно делать при лейкемии: Прежде всего, необходимо выяснить, не страдаете ли вы каким-либо душевным недугом...
Лечение прогрессирующих форм рака: Одним из наиболее важных достижений экспериментальной химиотерапии опухолей, начатой в 60-х и реализованной в 70-х годах, является...
Дисциплины:
![]() |
![]() |
5.00
из
|
Заказать работу |
|
|
Кафедра МТиО
КУРСОВАЯ РАБОТА (ПРОЕКТ)
По дисциплине «Инженерное обеспечение производства сварных конструкций»
На тему «Разработка технологического процесса сборки и сварки борта»
Специальность (направление подготовки) 15.03.01 «Машиностроение»
Автор работы (проекта) ст. гр. СП-01м, Крыгин М.Н.
Руководитель работы (проекта) к.т.н., доцент Чернышев Ю.В.
Работа (проект) защищена __________________
Оценка _______________
Председатель комиссии __________________ к.т.н., доцент Чернышев Ю.В.
Члены комиссии __________________ __________________
__________________ __________________
__________________ __________________
Курск 2019г.
Минобрнауки России
Федеральное государственное бюджетное учреждение
высшего образования
«Юго-Западный государственный университет»
(ЮЗГУ)
Кафедра МТиО
ЗАДАНИЕ НА КУРСОВУЮ РАБОТУ (ПРОЕКТ)
Студент (слушатель) Крыгин М.Н. шифр 15.03.01 группа СП-01м
1.Тема «Разработка технологического процесса сборки и сварки борта»
2.Срок представления работы (проекта) к защите «» __ _____ г.
3.Исходные данные (для проектирования, для научного исследования):
4.Содержание пояснительной записки курсовой работы (проекта):
4.1 Характеристика изделия
4.2 Анализ варианта и выбор способа изготовления изделия
4.3 Расчёт параметров процесса и выбор типового оборудования
|
4.4 Выбор метода контроля
4.5 Разработка маршрутно-операционной технологии
5.Приложение
5.1 Технологические особенности изготовления борта
5.2 Анализ возможных способов сварки стыковых соединений
5.3 Стол для сборки и сварки борта
5.4 Деталировка основных элементотв борта
5.5 Установка для сварки борта
5.6 Выбор метода контроля сварных соединений борта
Руководитель работы (проекта) _____________________ к.т.н., доцент Чернышов Ю.В.
Задание принял к исполнению _____________________ студент, Крыгин М.Н.
Содержание
Введение 6
1. Характеристика изделия 7
1.1 Назначение и условия работы каркаса 8
1.2 Выбор материала для каркаса 8
1.3 Анализ способа сварки каркаса 12
1.3.1 Полуавтоматическая сварка в среде СО2 12
1.3.2 Автоматическая сварка по слоем флюса 15
1.4 Анализ технологии изготовления каркаса 17
1.5 Постановка задачи на проектирование 18
2. Анализ вариантов конструктивного исполнения швов 19
2.1 Расчет параметров процесса 19
2.2 Расчет режимов аргонодуговой сварки 19
2.3 Расчет параметров режима автоматической сварки под флюсом 22
3. Выбор оборудования для аргонодуговой сварки 25
4. Выбор метода контроля 26
5. Разработка маршрутно-операционной технологии 30
|
5.1 Технологический процесс изготовления изделия 30
5.2 Нормирование сборки металлоконструкции под сварку 31
5.3 Расчет количества постов для сборки. 32
5.4 Нормирование сварки в среде аргона 33
5.5 Расчёт количества сварных постов при сварке в среде аргона 34
Заключение 36
Список используемой литературы 37
Приложение 38
РЕФЕРАТ
Курсовой проект на тему: «Разработка технологического процесса сборки и сварки борта» содержит: 4 чертежа формата А1, 44 листа расчетно-пояснительной записки, 5 рисунков, 1 таблицу, 6 источников, 2 листа спецификации формата А4.
В результате работы произведена разработка технологического процесса сборки и сварки борта.
В курсовом проекте представлены результаты разработки технологического процесса сборки и сварки борта, включая: анализ вариантов и способ изготовления изделия; расчет параметров процесса и выбор типового оборудования; расчет режимов сварки в среде углекислого газа; расчет режимов сварки под флюсом; выбор оборудования для сварки в углекислом газе; технологический процесс изготовления; нормирование сборки металлоконструкции под сварку; расчет количества постов для сборки, план сборочно-сварочного участка.
SUMMARY
Course project on the topic: "Development of the technological process of Assembly and welding of the Board" contains: 4 drawings of A1 format, 44 sheets of calculation and explanatory notes, 5 figures, 1 table, 6 sources, 2 sheets of A4 specification.
As a result, the development of the technological process of Assembly and welding of the Board was made.
In the course project presents the development of the technological process of Assembly and welding Board, including: an analysis of options and the method of manufacture of the product; calculation of process parameters and selection of standard equipment; the calculation of the modes of welding in carbon dioxide environment; calculation of modes of submerged arc welding; selection of equipment for welding in carbon dioxide; manufacturing process; regulation of assemblies of metal for welding; calculating the number of positions for Assembly, the plan for Assembly and welding station.
Введение
Курсовой проект по дисциплине "Расчет и проектирование сварных конструкций" выполняется на IV курсе после сдачи экзаменов.
Целью курсового проекта является углубление и закрепление знаний в области технологии, механизации и автоматизации.
|
В задачи проектирования входит:
· Оценка технологичности конструкции, выбор и подробная разработка технологической последовательности изготовления деталей, узлов и под- узлов, включая заготовительные, сборочные и сварочные операции, контроль;
· Выбор способа и метода сварки;
· Выбор оборудования из номенклатуры выпускаемого серийно, наиболее рационального для выполнения тех или иных операций и развитие навыков в проектировании специальной технологической оснастки и инструмента.
В качестве заданий для курсового проекта предлагаются:
1) Чертеж изделия борта;
2) Годовая программа выпуска - 20шт.
Характеристика изделия
Бортовая платформа - неразборная конструкция, предназначеная для перевозки сыпучих грузов и строительных материалов.
Борт выполняется из высокопрочной стали и покрывается специльной полимерной краской, которая обеспечивает повышенную защиту от коррозии, сочетает надежность, легкость, прочность и долговечность.
Рисунок 1 - Чертеж борта
1.1 Назначение и условия работы каркаса.
Бортовые платформы предназначены для перевозок грузов, не требующих особых температурных условий и защиты от воздействия окружающей среды и могут быть изготовлены с тентом или без него, с откидными боковыми и задним бортом, с высокими передним бортом, сдвижной или стационарной тентованной крышей.
Конструкция состоит из решетчатого стального каркаса, оснащенного лонжеронами увеличенной толщины.
Основные несущие элементы изготовлены с использованием прочной низколегированной стали, все соединения являются сварными или выполненными с помощью заклепок.
Преимущества бортовых платформ:
1. Универсальность - бортовые грузовики применяются для перевозки самых различных грузов, кроме тех, которые требуют поддержания специальных условий во время транспортировки.
2. Неприхотливость - простая конструкция этого оборудования не требует особого технического обслуживания и легко выдерживает высокие эксплуатационные нагрузки;
3. Вместительность - оборудованные бортами платформы позволяют перевозить крупногабаритные грузы или большие партии продукции.
|
1.2 Выбор материала для каркаса
В изготовлении бортовых платформ используется Сталь 3.
Сталь Ст3 не склонна к отпускной хрупкости, свариваемость без ограничений.
Качество конструкционной стали определяется коррозионной стойкостью, механическими свойствами и свариваемостью. По своим механическим характеристикам стали делят на группы: сталь обычной, повышенной и высокой прочности.
Основные свойства стали непосредственно зависят от химического элементов, входящих в состав сплава и технологических особенностей производства.
Основой структуры стали является феррит. Он является малопрочным и пластичным, цементит напротив, хрупок и тверд, а перлит обладает промежуточными свойствами. Свойства феррита не позволяют применять его в строительных конструкциях в чистом виде. Для повышения прочности феррита сталь насыщают углеродом (стали обычной прочности, малоуглеродистые), легируют добавками хрома, никеля, кремния, марганца и других элементов (низколегированные стали с высоким коэффициентом прочности) и легируют с дополнительным термическим упрочнением (высокопрочные стали).
К вредным примесям относятся фосфор и сера. Фосфор образует раствор с ферритом, таким образом снижает пластичность металла при высоких температурах и повышает хрупкость при низких. Образование сернистого железа при избытке серы приводит к красноломкости металла. В составе стали ст3 допускается не более 0,05% серы и 0,04 % фосфора.
При температурах, недостаточных для образования ферритной структуры возможно выделение углерода и его скопления между зернами и возле дефектов кристаллической решетки. Такие изменения в структуре стали понижают сопротивление хрупкому разрушению, повышают предел текучести и временного сопротивления. Это явление называют старением, в связи с длительностью процесса структурных изменений. Старение ускоряется при наличии колебаний температуры и механических воздействиях. Насыщенные газами и загрязненные стали подвержены старению в наибольшей степени.
Конструкционные стали производят мартеновским и конвертерным способами. Качество и механические свойства сталей кислородно-конвертерного и мартеновского производства практически не отличаются, но кислородно-конвертерный способ проще и дешевле.
По степени раскисления различают спокойные, полуспокойные и кипящие стали. Кипящие стали - нераскисленные. При разливке в изложницы они кипят и насыщаются газами. Для повышения качества малоуглеродистых сталей используют раскислители - добавки кремния (0,12 - 0,3%) или алюминия (до 0,1 %). Раскислители связывают свободный кислород, а образующиеся при этом алюминаты и силикаты увеличивают количество очагов кристаллизации, способствуя образованию мелкозернистой структуры. Раскисленные стали называют спокойными, т.к. они не кипят при разливке. Спокойные стали более однородны, менее хрупкие, лучше свариваются и хорошо противостоят динамическим нагрузкам. Их применяют при изготовлении ответственных конструкций. Ограничивает применение спокойной стали высокая стоимость и по технико-экономическим соображениям наиболее распространенным конструкционным материалом является полуспокойная сталь. Для раскисления полуспокойной стали используется меньшее количество раскислителя, преимущественно кремния. По качеству и цене полуспокойные стали занимают промежуточное положение между кипящими и спокойными.
|
Из группы малоуглеродистых сталей обычной мощности (ГОСТ 380-71, с изм.) для строительных конструкций применяют сталь марок Ст3 и Ст3Гпс. Сталь ст3 производится спокойной, полуспокойной и кипящей.
В зависимости от эксплуатационных требований и вида конструкций, сталь должна отвечать требованиям ГОСТ 380-71. Углеродистая сталь подразделяется на 6 категорий. При поставке стали марок ВСт3Гпс и ВСт3 всех категорий требуется гарантированный химический состав, относительное удлинение, предел текучести, временное сопротивление, изгиб в холодном состоянии.
Требования ударной вязкости различаются по категориям.
При маркировке стали согласно ГОСТ 380-71 (с изм.) вначале ставят обозначение группы поставки, далее марки, степени раскисления и категории.
По ГОСТ 23570-79 устанавливаются более строгий контроль качества стали и ограничения содержания мышьяка и азота. Обозначение марки включает процентное содержание углерода (в сотых долях процента), степень раскисления и буква Г для марганцовистых сталей.
Углеродистые стали - самый распространенный конструкционный материал. По объему применения стали этого класса превосходят все остальные. К углеродистым относятся стали с содержанием 0,1-0,7% С, при содержании остальных элементов не более: 0,8% Мn, 0,4% Si, 0,05% Р, 0,05% S, 0,5% Си, 0,3% Сг, 0,3% Ni..
По способу производства различают мартеновскую и конвертерную стали, по степени раскисления (в порядке возрастания) кипящую, полуспокойную и спокойную.
Спокойные углеродистые стали поступают в промышленность в виде отливок и поковок по ГОСТ 977-75, в виде горячекатаной стали обыкновенного качества по ГОСТ 380-71, качественных конструкционных горячекатаных сортовых сталей по ГОСТ 1050-74. Главным отличительным признаком этих сталей является содержание в них углерода.
Прочностные характеристики углеродистых сталей повышаются с увеличением содержания углерода, при этом их свариваемость ухудшается, так как возрастает опасность образования горячих трещин в шве. При содержании свыше 0,5% С стали практически не свариваются электрошлаковой сваркой без специальных приемов.
Чувствительность к горячим трещинам в шве возрастает с увеличением жесткости свариваемых конструкций. Предварительный и сопутствующий подогрев могут существенно снизить опасность появления трещин даже при сварке жестких стыков (например, на участке замыкания кольцевого шва). Одним из радикальных средств по предотвращению горячих трещин служит снижение скорости подачи электродной проволоки.
Углеродистые стали в настоящее время сваривают проволочными электродами, электродами большого сечения или плавящимися мундштуками. Наиболее широко применяют проволочные электроды и плавящиеся мундштуки.
1.3 Анализ способа сварки каркаса
Сварка является одним из основных технологических процессов обработки металлов и сплавов. Большие преимущества сварки обес-печили ей широкое применение в промышленности; без нее сегоднянемыслимо производство автомобилей, тракторов, дорожных машин идругих изделий, и конструкций. Так, в автомобилях масса сварныхконструкций составляет 45-50% от общей массы. При сборке кузововавтомобилей ВАЗ используют до 10 тыс. сварных точек.
Сваркой называется процесс получения неразъемных соединений конструкционных материалов путем местного приложениятермической, термомеханической или механической энергии. Соединение металлов происходит за счет межмолекулярных или межатомных связей (сил сцепления).
Согласно ГОСТ 2601-84 все способы сварки разделяют на трикласса: термической, термомеханической и механической.
К термическому классу относят газовую и все виды дуговойсварки: ручная дуговая плавящимися и неплавящимися электродами,автоматическая под слоем флюса, ручная и автоматическая в среде защитных газов.
К термомеханическому классу относят все виды контактнойсварки: стыковая, точечная, шовная (роликовая), а также индукционно-прессовая и диффузионная.
К механическому классу относят сварку: давлением, трением,взрывом, магнитно-импульсная и ультразвуковая.
1.3.1 Полуавтоматическая сварка в среде СО2
При сварке и наплавке в среде защитных газов в зону горения дуги под небольшим давлением подается газ, который вытесняет воздух из этой зоны и защищает сварочную ванну от кислорода и азота воздуха.
В зависимости от применяемого газа сварка разделяется на сварку в активных (СО2, Н2, О2, и др.) и инертных (He, Ar, Ar+He и др.) газах. Сварку (наплавку) можно осуществлять как плавящимся, так и неплавящимся электродами.
Наибольшее распространение при восстановлении деталей подвижного состава получили сварка и наплавка в среде углекислого газа (СО2) – сварка плавящимся электродом (проволокой) с защитой сварочной ванны от воздуха углекислым газом.
Такой способ является самым дешевым при сварке углеродистых и низколегированных сталей. Поэтому по объему производства он занимает одно из первых мест среди механизированных способов сварки плавлением.
Принцип действия для полуавтоматической сварки в режиме углекислоты очень схож с методом газовой сварки с газом и без. То есть, варить можно двумя способами - использую защитный газ или нет.
Сущность рассматриваемого способа заключается в элементарной химии. В сварочную зону под давлением подается углекислый газ (СО2). Сварочная дуга обеспечивает высокую температуру, за счет чего происходит реакция разложения и газ распадается на кислород (О2) и угарный газ (2СО).
В результате этой реакции сварочная ванна защищена тремя газами – начальным углекислым газом и конечными продуктами реакции – кислородом и угарным газом
Углекислый газ имеет свойство к окислению с железом и углеродом, находящимся в металле. Чтобы защитить металл изделия от этого процесса, рекомендуется для сварочного аппарата применять проволоку с повышенным уровнем марганца и кремния. Эти компоненты химически активнее, чем железо, поэтому сначала окисляются они, тем самым принимая на себя «удар» и защищают изделие. Пока в сварочной зоне присутствуют эти два элемента, железо и углерод не будут окисляться. Отходы, то есть оксиды марганца и кремния, которые образуются при воздействии высокой температуры и окислительной реакции представляют собой легкоплавкое соединение, которое всплывает на поверхность сварочной ванны и кристаллизируется в виде шлака. Этот компонент никак не влияет на качество шва.
Для сварки в среде углекислого газа одного стандартного баллона на 25 кг углекислоты хватает на 15 сварочных часов. С учетом реакции из одного килограмма получается почти 500 литров готового газа. При полноценной работе затраты в среднем считаются от 10 до 50 литров в минуту. Но расход зависит от многих факторов – давления, типа сварки, типа шва, применяемого аппарата, погодных условий и так далее.
Такой метод называется сварка tig, то есть, это работы это соединение металлов с помощью электродов в среде защитного газа. Электрод может быть вольфрамовым или графитовым.
Полуавтоматическая сварка в среде углекислого газа отлично подходит для новичков. Основной особенностью данного метода является применение обратной полярности постоянного тока. Это позволяет удерживать дугу. Если же наоборот, применить прямую полярность, то увеличивается риск потери дуги, что негативно отразится на качестве спаивания.
Работая на обратной полярности, можно избежать разбрызгивания электрода. Если же нужно наплавить металл, тогда лучше применить прямую, так и КПД будет в 1,5-почти 2 раза выше.
Режимы сварки, которые выставляются в настройках аппарата, зависят от многих факторов. Рассмотрим таблицу, где подробно расписаны возможные варианты настроек, отталкиваясь от толщины металла, из которого сделаны заготовки для сваривания.
Полуавтоматическую сварку в газовой среде можно выполнять следующими методиками:
- углом вперед (справа налево) используется для тонколистового металла;
- углом назад (слева направо) обеспечивает глубокий провар, но шов при этом не будет широким.
Рисунок 2 - Схема полуавтоматической сварки в среде СО2
Когда шов полностью готов, нельзя сразу отключать подачу газа, так как это чревато окислением. Сначала останавливается подача проводной проволоки, потом подача тока, а затем уже подача газа. Как раз за это время шов успевает кристаллизоваться. По завершению работы нужно сбить шлак со шва.
1.3.2 Автоматическая сварка под флюсом
Автоматическая дуговая сварка под слоем флюса - это технология, суть которой ничем не отличается от классической дуговой сварки. Металл плавится из-за высокой температуры, которая формируется благодаря электрической дуге. Ниже изображена схема автоматической дуговой сварки под флюсом.
Рисунок 3 - Схема автоматической сварки под слоем флюса
Отличие автоматической сварки от любой другой заключается лишь в том, что большинство процессов выполняется не вручную, а с помощью специальных станков. Например, подача проволоки и движение дуги. Ну а в нашем конкретном случае все эти операции производятся под слоем флюса, нанесенного на поверхность металла.
Автоматическая наплавка под флюсом применяется во многих сферах. С ее помощью можно организовать быстрое крупносерийное производство, в том числе конвейерное. По этой причине данная технология незаменима при сборке кораблей, производстве крупногабаритных труб и емкостей для нефтеперерабатывающей отрасли. Автоматическая сварка обеспечивает высокое качество швов, поэтому завоевала свое уважение в таких ответственных отраслях.
Флюс - это специальное вещество (может выпускаться в виде порошка, гранул, паст и жидкостей), обладающее положительными свойствами. Флюсы толстым слоем подаются прямо в сварочную зону, защищая ее от негативного влияния кислорода. Также флюс защищает сам металл, способствует устойчивому горению дуги, уменьшает вероятность разбрызгивания металла и даже изменяет химический состав шва при необходимости.
У автоматической сварки с применением флюса есть много плюсов. Ее главное достоинство - возможность полной автоматизации процесса сварки. От сварщика не нужно даже уметь варить, достаточно знать, как настроить оборудование. Также такой метод сварки гарантирует отличное качество сварочных соединений, поскольку отсутствует человеческий фактор.
У технологии сварки деталей автоматической наплавкой под слоем флюса есть и недостатки. Во-первых, вы сможете варить только нижний шов. Также детали должны быть очень точно подогнаны, ведь машина формирует шов в четко заданном месте, и любая ошибка при стыковке приведет к браку. Кроме того, нужна очень тщательная подготовка металла перед сваркой.
Технология сварки под флюсом проста за счет того, что многие процессы выполняет не человек, а машина. Мастеру не нужна зажигать дугу, следить за ее стабильностью, выбирать скорость подачи проволоки и так далее. Все, что от вас требуется - правильно настроить режимы сварки под флюсом. По сути, задать машине программу действий.
1.4 Анализ технологии изготовления бортовой платформы
Процесс сварки металла состоит из трех этапов: подготовки деталей, сварки, зачистки.
Основной металл до сборки должен быть очищен в местах сварки от ржавчины, масла, влаги, краски, рыхлого слоя окалины, льда и т. д., могущих привести к образованию дефектов в сварном шве. С поверхности металла необходимо удалить рыхлый слой окалины, ржавчины и других загрязнений, даже если они расположены вне места сварки, так как при кантовке и транспортировке загрязнения могут попасть в разделку шва.
Резку прокатной стали производят механическим способом на ножницах, зубчатых пилах и газопламенным способом ручными резаками и полуавтоматами.
Сборку выполняют в приспособлениях (кондукторах, кантователях, на стеллажах) или с использованием прихваток - коротких швов.
1.5 Постановка задачи на проектирование
технологического процесса
На основании вышеприведенного анализа были сделаны следующие выводы:
- применение конструкции каркаса значительно повышает прочность и устойчивость объекта.
На основании сделанных выводов были поставлены следующие задачи на проектирование технологического процесса:
- рассчитать режимы сварки;
- выбрать необходимые сварочные материалы, на основании этого подобрать необходимое оборудование;
- выбрать метод контроля.
Исходными данными для проектирования являются чертеж боорта и годовая программа выпуска 20 шт. Материал Ст3.
2. Анализ вариантов конструктивного исполнения швов
2.1 Расчет параметров процесса
Расчет параметров процесса сварки является важнейшей частью проектирования технологического процесса сварки.
Режимы сварки определяют следующие параметры сварочный ток, напряжение на дуге, диаметр электродной проволоки, скорость сварки (скорость перемещения проволоки) и скорость подачи проволоки. Эти параметры оказывают решающее влияние на форму шва и качество сварного соединения. Режим определяет поперечный профиль шва, т. е. глубину проплавления, усиление и ширину шва, долю участия основного и электродного металла в образовании шва. Форма шва также зависит от рода тока и полярности, наклона электрода относительно изделия, вылета электрода из мундштука, конструктивной формы соединения, величины зазора.
Форма сечения шва в различной степени зависит от всех параметров технологического режима. Однако наибольшее влияние на нее оказывает обобщенный технологический фактор - погонная энергия, которая представляет собой отношение тепловой мощности источника нагрева к скорости сварки,т.е. к скорости перемещения источника нагрева относительно свариваемого изделия
2.2 Расчет режимов полуавтоматической сварки в среде СО2
По ГОСТ 14771-76 выбираем форму и конструктивные элементы подготовки кромок под сварку, размеры выполненных швов (рисунок 3).
Рисунок 4 - Подготовка кромок под полуавтоматическую сварку в среде СО2
На основе заданного значения катета шва определяем площадь поперечного сечения металла шва:
, (1)
где - коэффициент увеличения, учитывающий наличие зазора и выпуклости шва,
- катет шва (принимаем k = 5 мм).
Выбираем диаметр электродной проволоки:
Определяем силу тока:
, (2)
где - плотность тока (принимаем
).
Принимаем силу сварочного тока
Определяем напряжение на дуге:
(3)
Определяем скорость сварки:
, (4)
где - коэффициент наплавки, принимаем
Определяем погонную энергию сварки:
, (5)
где - эффективный КПД дуги, для сварки в СО2
;
- скорость сварки в см/с;
Определяем скорость подачи электродной проволоки:
, (6)
где - скорость сварки, м/час;
- площадь наплавки, мм2;
- площадь поперечного сечения электрода, мм2.
Расчет размеров угловых сварных швов:
Определяют глубину провара, при сварке СО2:
При сварке постоянным током обратной полярности во всем диапазоне плотность тока =0,92.
Определяют ширину шва:
(7)
Оценивается высота выпуклости шва:
; (8)
Определяется общая высота шва:
(9)
2.3 Расчет параметров режима автоматической сварки под флюсом
По ГОСТ 8713-79 выбираем форму и конструктивные элементы подготовки кромок под сварку, размеры выполненных швов (рисунок 3).
Рисунок 5 - Подготовка кромок под флюсом
На основе заданного значения катета шва определяем площадь поперечного сечения металла шва:
, (10)
где - коэффициент увеличения, учитывающий наличие зазора и выпуклости шва,
- катет шва (принимаем k = 5 мм).
Выбираем диаметр электродной проволоки:
Определяем силу тока:
, (11)
где - плотность тока (принимаем
).
Принимаем силу сварочного тока
Определяем напряжение на дуге:
(12)
Определяем скорость сварки:
, (13)
где - коэффициент наплавки, принимаем
Определяем погонную энергию сварки:
, (14)
где - эффективный КПД дуги, для сварки в СО2
;
- скорость сварки в см/с;
Определяем скорость подачи электродной проволоки:
, (15)
где - скорость сварки, м/час;
- площадь наплавки, мм2;
- площадь поперечного сечения электрода, мм2.
Определяем мгновенную скорость охлаждения З.Т.В. при температуре наименьшей устойчивости аустенита:
(16)
Определяют ширину шва
(17)
Оценивается высота выпуклости шва:
(18)
13) Определяется общая высота шва:
(19)
Выбор метода контроля
Сварные конструкции контролируют на всех этапах их изготовления. Кроме того, систематически проверяют приспособления и оборудование. При предварительном контроле подвергаются проверке основные и вспомогательные материалы, устанавливается их соответствие чертежу и техническим условиям. Наиболее ответственным моментом является текущий контроль выполнения сварки. Организация контроля сварочных работ может производиться в двух направлениях: контролируют сами процессы сварки либо полученные изделия.
Тщательный контроль и приемка деталей и готовых изделий проводят на всех стадиях производства сварных конструкций.
В стадии обработки проверяют:
- соответствие применяемого металла чертежу на основании сертификата завода-изготовителя или путем заводского лабораторного испытания;
- отсутствие внешних пороков металла: раковин, плен, волосовин, закатов, расслоений;
- соблюдение формы и внешнего вида элементов сварных конструкций после заготовительных операций в соответствии с чертежами и техническими условиями, например, точность размеров, качество разделки кромок, зачистка после газовой резки и пр.
В собранной сварной конструкции проверяют:
- соответствие геометрических и основных размеров рабочим чертежам и соблюдение допусков;
- правильность подготовки металла под наложение сварочных швов, зазоры, разделка кромок и прочее;
- чистоту металла в месте наложения сварных швов, отсутствие окалины, ржавчины, масла и других загрязнений.
В процессе сварки проверяют выборочно:
- порядок наложения швов в соответствии с технологическим процессом;
- тщательность зачистки предыдущих слоев шва перед наложением последующего слоя;
- соответствие чертежным размерам наложенных швов и марки применяемой сварочной проволоки;
- соответствие режимов сварки и квалификации сварщиков, указанных в техпроцессе.
Выбор методов контроля обуславливается требованиями технических условий на изготовление сварных конструкций и зависит от степени ответственности данной конструкции при эксплуатации, глубины и места расположения предполагаемых дефектов, толщины, конфигурации и материала деталей и других факторов.
Контроль сварных соединений заключается в качественной или количественной оценке основных признаков, характеризующих их работоспособность.
Анализ качества сварного соединения закладной детали осуществляется методами неразрушающего контроля, а именно, внешним осмотром и нагружением. Эти методы позволяют наиболее качественно определить состояние сварного соединения.
Внешний осмотр заключается в выявлении дефектов соединений невооруженным
|
|
Индивидуальные и групповые автопоилки: для животных. Схемы и конструкции...
Опора деревянной одностоечной и способы укрепление угловых опор: Опоры ВЛ - конструкции, предназначенные для поддерживания проводов на необходимой высоте над землей, водой...
История создания датчика движения: Первый прибор для обнаружения движения был изобретен немецким физиком Генрихом Герцем...
Адаптации растений и животных к жизни в горах: Большое значение для жизни организмов в горах имеют степень расчленения, крутизна и экспозиционные различия склонов...
© cyberpedia.su 2017-2024 - Не является автором материалов. Исключительное право сохранено за автором текста.
Если вы не хотите, чтобы данный материал был у нас на сайте, перейдите по ссылке: Нарушение авторских прав. Мы поможем в написании вашей работы!