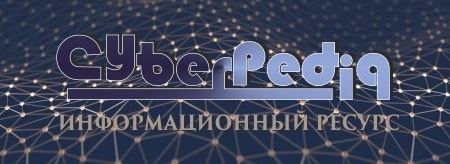
Кормораздатчик мобильный электрифицированный: схема и процесс работы устройства...
Индивидуальные и групповые автопоилки: для животных. Схемы и конструкции...
Топ:
Отражение на счетах бухгалтерского учета процесса приобретения: Процесс заготовления представляет систему экономических событий, включающих приобретение организацией у поставщиков сырья...
Эволюция кровеносной системы позвоночных животных: Биологическая эволюция – необратимый процесс исторического развития живой природы...
Интересное:
Мероприятия для защиты от морозного пучения грунтов: Инженерная защита от морозного (криогенного) пучения грунтов необходима для легких малоэтажных зданий и других сооружений...
Национальное богатство страны и его составляющие: для оценки элементов национального богатства используются...
Принципы управления денежными потоками: одним из методов контроля за состоянием денежной наличности является...
Дисциплины:
![]() |
![]() |
5.00
из
|
Заказать работу |
|
|
СОДЕРЖАНИЕ
стр.
Введение………………………………………………………………….4
1. Спецификация сырья и пиломатериалов…………………………….5
1.1. Характеристика сырья по ГОСТ 9463-88………………………….5
1.2. Характеристика пиломатериалов по ГОСТ 24454-80…………….7
2. Составление и расчет поставов на ЭВМ…………………………….8
2.1. Проверка возможности выполнения задания по объему сырья
и определение процента брусовки………………………………...8
2.2. Расчет поставов на ЭВМ…………………………………………...9
3. Составление плана раскроя сырья…………………………………..9
4. Составление баланса древесины…………………………………...12
4.1. Расчет объема опилок……………………………………………..12
4.2. Расчет объема кусковых отходов и щепы………………………..13
5. Определение количественного, качественного,
спецификационного выхода пиломатериалов………………………..15
6. Выбор и расчет основного технологического оборудования…….16
6.1. Выбор оборудования……………………………………………...16
6.2. Расчет потребности ленточнопильных станков…………………17
6.3. Расчет потребности круглопильных станков……………………18
6.4. Расчет потребности обрезных станков…………………………...19
6.5. Расчет потребности торцовочных станков………………………20
6.6. Расчет потребности окорочных станков…………………………21
6.7. Расчет потребного количества рубительных машин……………22
6.8. Расчет потребного количества машин
для сортировки щепы……………………………………………....23
6.9.Расчет сортировочных устройств для сортировки п/м…………..24
6.10.Расчет потребного количества линий сортировки
пиловочных бревен………………………………………………...26
6.11.Выбор околостоночного оборудования…………………………27
|
7. Расчет транспортных средств и площадей складов……………….27
7.1. Расчет продольного одноцепного конвейера....…………………27
7.2. Расчет ленточного транспортера…………………………………28
7.3. Расчет скребкового транспортера для опилок…………………..29
7.4. Расчет потребного количества автолесовозов…………………...30
7.5. Расчет потребного количества кранов на
складах леса и пиломатериалов…………………………………..31
7.6. Расчёт площади бассейна…………………………………………32
7.7. Расчет площади склада леса……………………………………....33
7.8. Расчет площади склада пиломатериалов………………………...33
8. Расчет режущего, абразивного инструмента и заточных
станков……………………………………………………………….34
8.1. Расчет потребного количества ленточных пил………………….34
8.2. Расчет потребного количества круглых пил…………………….34
8.3. Расчет потребного количества ножей для
рубительной машины……………………………………………..35
8.4. Расчет потребного количества короснимателей………………...35
8.5. Расчет потребного количества абразивного
инструмента………………………………………………………..35
8.6. Расчет потребного количества заточных станков……………….36
9. Расчет потребности электроэнергии на
технологические нужды……………………………………………….38
9.1. Расчет годовой потребности в электроэнергии…………………40
10. Определение количества рабочих………………………………...40
11. Основные технико-экономических показатели………………….42
12. Охрана труда и противопожарная защита………………………..43
Список литературы…………………………………………………….45
ВВЕДЕНИЕ
Ни одна отрасль народного хозяйства не обходится без древесины. Поэтому важную роль в развитии экономики играет лесообрабатывающая отрасль промышленности. Производство пиломатериалов занимает ведущее место в лесопильно-деревообрабатывающей промышленности и является начальной стадией процесса изготовления большинства изделий.
|
С увеличением производства пиломатериалов происходили изменения в технологии, организации и технике. От некогда примитивного способа выработки досок путем раскалывания бревен на две или, в лучшем случае, на три части с последующей оттеской топором пиломатериалы стали вырабатывать путем распиловки бревен ручными, а затем рамными пилами. Рамное пиление бревен на доски в свою очередь совершенствовалось: создавалась новая техника, улучшались организация и механизация всех процессов.
Современные лесопильные заводы представляют собой по преимуществу крупные предприятия, оборудованные новейшими станками и приспособлениями с высокой механизацией всех процессов.
Важнейшие задачи лесопильно-деревообрабатывающей промышленности в перспективный период следующие:
1. улучшение использования древесного сырья в процессах производства пиломатериалов и заготовок;
2. полное использование неизбежных отходов для выработки древесно-плитным и древесных материалов;
3. всемерная механизация и автоматизация всех процессов производства.
Решение этих задач требует создания комбинированных предприятий, включающих цехи производства пиломатериалов, сушки древесины, раскроя пиломатериалов на целые заготовки и заготовки для склейки, производства клееных заготовок и деталей, переработки неизбежных отходов, механической обработки древесины в полноценную продукцию, а в ряде случаев и цехи выпуска готовых изделий.
Решающее условие дальнейшего развития лесной и деревообрабатывающей промышленности - повышение производительности труда, основанное на ускорении научно-технического прогресса. Основное внимание должно быть сосредоточено на бережном отношении к сырью, рациональной и комплексной его переработке, повышении качества продукции и вовлечении в производство всех видов вторичного древесного сырья (технологической щепы, технологических опилок, стружки, коры и др.). Все эти мероприятия направлены на сохранение лесов, на охрану окружающей среды.
СОСТАВЛЕНИЕ ПЛАНА РАСКРОЯ СЫРЬЯ
d=28 см; cсечение 44×125
N=14/0,143=97,902тыс.шт.
Vп/м=42,857·0,143=6,129тыс.м3
Vост=14-6,129=7,871 тыс.м3
V25=42,857·0,065=2,786тыс.м3
V19=42,857·0,06935=2,972тыс.м3
|
d=26 см; cсечение 44×125
N=7,871/0,143=55,042тыс.шт
Nост=74,419-55,042=19,377тыс.шт.
V25=55,042·0,025=1,37605тыс.м3
V19=55,042·0,08836=4,8635тыс.м3
d=26 см; сечение 32×125
N=12/0,156=76,923тыс.шт
Vп/м=19,377·0,156=3,0228тыс.м3
Vост=12-3,0228=8,9772тыс.м3
V19=19,377∙0,10356=2,0067тыс.м3
d=24 см; cсечение 32×125
N=8,9772/0,104=86,319тыс.шт
Nост=105,555-86,319=19,236тыс.шт.
V25=86,319·0,07=6,04233тыс.м3
V19=86,319·0,019=1,64тыс.м3
d=24 см; cсечение 32×100
N=21/0,0832=252,404тыс.шт
Vп/м=19,236·0,0832=1,6004тыс.м3
Vост=21-1,6004=19,3996тыс.м3
V25=19,236·0,09026=1,736тыс.м3
V19=19,236·0,02125=0,4088тыс.м3
d=22 см; cсечение 32×100
N=19,3996/0,0832=233,1683тыс.шт
Vп/м=129,032·0,0832=10,7355тыс.м3
Vост=19,3996-10,7355=8,6641тыс.м3
V19=129,032·0,0133=1,716тыс.м3
План раскроя сырья
Таблица 3
d, см | Кол-во бревен, тыс.м3 тыс. шт | Постав | 44x125 | 32x125 | 32x100
| разные
|
Всего т.м3 | |
25 | 19 | |||||||
28 | 21 42,857 | 19-19-25-125-25-19-19 19-44-44-44-44-44-19 | 6,129 | 2,786 | 2,972 | 11,887 | ||
26 | 23,668 55,042 | 19-19-19-125-19-19-19 25-44-44-44-44-25 | 7,871 | 1,37605 | 4,8635 | 14,11055 | ||
26 | 8,3321 19,377 | 19-19-19-125-19-19-19 19-32-32-32-32-32-32-19 | 3,0228 | 2,0067 | 5,0295 | |||
24 | 31,0784 86,319 | 19-25-125-25-19 25-32-32-32-32-32-25 | 8,9772 | 6,04233 | 1,64 | 16,6595 | ||
24 | 6,925 19,236 | 19-19-19-100-19-19-19 25-32-32-32-32-32-25 | 1,6004 | 0,4088 | 1,736 | 3,7452 | ||
22 | 40 129,032 | 25-25-100-25-25 19-32-32-32-32-32-19 | 10,7355 | 7,9845 | 1,716 | 20,436 | ||
Итого: | 14 | 12 | 12,3359 | 18,5977 | 14,9342 | 71,868 | ||
По заданию | 14 | 12 | 21 | 32 | 79 | |||
Недопил: | 8,6641 | 8,6641 | ||||||
Перепил: | 1,53188 | 1,53188 |
Техническая характеристика
БА-100
7.2. РАСЧЕТ ЛЕНТОЧНОГО ТРАНСПОРТЕРА
Расчет ведется для самого загруженного транспортера. Это – транспор-тер подающий щепу от рубительной машины к сортировке щепы.
Площадь поперечного слоя на ленте:
F = 2×b×h / 3, (7.2.1.)
где F - площадь поперечного слоя на ленте, мм2;
b - ширина слоя массы на ленте, мм; b=0,9В-0,05, или b» В;
В - ширина ленты, мм;
|
h - наибольшая высота посылки, мм; h=0,5b.
Принимаем h=0,5∙400=200 мм, значит b=0,9∙400-0,05=359,95мм.
F = 2×359,95×200 / 3 = 47993,33 мм2.
Скорость движения ленты:
V = Qк.отх. ×106 / (Т×m×F×Кр×Км), (7.2.2.)
где V - скорость движения ленты, м/мин;
Т - время смены, мин;
m - количество рабочих смен в году;
Кр - коэффициент использования рабочего времени, Кр = 0,9;
Км - коэффициент использования машинного времени, Км=0,7;
V = 29976,5×106/ (480×480·47993,33×0,9×0,7) = 4,303 м/мин.= 0,072 м/с
Кз = 0,072/0,72 = 0,1
Принимаем ленточный транспортер КЛ6-400, техническая характеристика которого представлена в таблице 6.11
Таблица 6.11
Техническая характеристика КЛ6-400 | |
Транспортируемый материала, мм: - ширина | 300-600 |
-толщина | до 300 |
-длина | до 6 500 |
Ширина ленты конвейера, мм | 400 |
Скорость движения ленты, м/с | 0.72 |
Мощность, кВт | 4 |
Габариты, м | 6х1.15х0.45 |
Масса, кг | 640 |
7.3. РАСЧЕТ СКРЕБКОВОГО ТРАНСПОРТЕРА ДЛЯ ОПИЛОК
Для транспортировки отходов (опилок) широко используют скребковые транспортеры.
Определим объем опилок, транспортируемым одним скребком по формуле:
q = (1/2×h×B×1/2×lскр) / К, (7.3.1.)
где q - объем опилок и топливных отходов, транспортируемым одним скребком, м3;
h - высота скребка, м, h = 0,065 м;
В - длина скребка, м;
lскр - расстояние между скребками, м, lскр = 0,8 м;
К - коэффициент рыхлости, К = 2,8...3;
q = (1/2×0,065×0,45×1/2×0,8) / 2,8 = 0,002 м3.
Скорость движения транспортера:
V = Qсм.оп ×lскр / (Т×q×Кр×Км), (7.3.2.)
где V - скорость движения транспортера, м/мин;
Qсм.оп. - объем опилок, поступающих на транспортер в смену;
lскр - расстояние между скребками, м;
Т - продолжительность смены, мин;
q - количество опилок и топливных отходов, транспортируемых
одним скребком,м3;
Кр - коэффициент использования рабочего времени; Кр = 0,9;
Км - коэффициент использования машинного времени, Км=0,8;
Qсм.оп. =∑(Qоп. + Q.т.отх.)/m·z, (7.3.3.)
где m- количество рабочих дней в год;
z- количество смен;
Qоп –объём опилок в год;
Qсм.т.отх. - объем топливных отходов, поступающих на транспортер в смену;
Qсм.оп. = (20630,6+5984,3)/480=55,448м3
V = 55,448·0,8 / (480×0,002×0,9×0,8) = 64,175 м/мин = 0,63 м/с.
Кз = 0,63/0,72 = 0,88
Принимаем скребковый транспортер ТОЦ 15, техническая характеристика которого представлена в таблице 6.12
|
Таблица 6.12
Техническая характеристика | |
Наименование показателей | ТОЦ-15 |
Производительность, куб. м/час | До 30 |
Скорость цепи, м/с | 0.72 |
Расстояние между скребками, мм | 800 |
Размеры скребка, мм | 450х66 |
Мощность, кВт | 2.2 |
Габарит, м | 16х1.6х0.65 |
Тип цепи | 14х80 |
Разрывное усилие, т | 12 |
7.4 РАСЧЕТ ПОТРЕБНОГО КОЛИЧЕСТВА АВТОЛЕСОВОЗОВ
Сменная производительность автолесовозов определяется по формуле:
Псм = Т×qп×К / tц, (7.4.1.)
где Псм - сменная производительность автолесовоза, м3/см;
Т - время смены; мин;
tц - время цикла на перевозку одного пакета, мин;
qп - объем одного пакета, qп = 5...8 м3;
К - коэффициент, К = 0,85;
Время цикла на перевозку одного пакета определяется по формуле:
tц = t1 + t2 + t3 + t4, (7.4.2.)
где t1 - время на захват пакета, мин;
t2 - время движения с пакетом, мин;
t3 - время на опускание пакета, мин;
t4 - время возвращения лесовоза, мин;
t1 = t3 = 2 мин.
t2 = S / Vр.х., (7.4.3.)
где S - путь, проходимый автолесовоза с пакетом, м;
Vр.х. - скорость движения лесовоза с грузом:
Vр.х. = 0,25 км/ч = 250 м/мин;
t2 = 500 / 250 = 2 мин
t4 = S / Vx.x., (7.4.4.)
где Vx.x. - скорость автолесовоза без груза:
Vx.x. = 300 м/мин;
t4 = 500 / 300 = 1,67 мин.
t ц = 2 + 2 + 2 + 1,67 = 7,67 мин.
Потребное количество автолесовозов определяется по формуле:
n = (Vc×К) / (Псм×h), (7.4.5.)
где n - потребное количество автолесовозов;
Vc - объем пиломатериалов, складируемых за смену, м3;
Псм - сменная производительность, м3/см;
h - коэффициент использования парка лесовоза, h = 0,7;
К - коэффициент использования грузопотока, К = 1,35.
Псм = (480×7×0,85) / 7,67 = 372,36м3.
Vc = V/ 480, (7.4.6.)
где V- годовой выпуск пиломатериалов, м3;
Vc = 71868/ 480 =149,73 м3/см;
n = (149,73×1,35) / (372,36×0,7) = 0,76.
Кз = 0,76/ 1 = 0,76.
Принимаем один автолесовоз Т-80, техническая характеристика которого представлена в таблице 6.13
Таблица 6.13
Техническая характеристика | |
Подъём груза, м·мин-1 | 30 |
Передвижение тележки,, м·мин-1 | 32 |
Грузоподъёмность, т | 5 |
Высота подъёма крюка, м | 21,5 |
Мощность, кВт | 53,5 |
Масса крана, т | 36 |
|
7.6. РАСЧЁТ ПЛОЩАДИ БАССЕЙНА
Расчет бассейна ведется для реконструируемых предприятий. Для размещения бревен необходимо два дворика на поток и один запасной.
Определим количество сырья распиливаемого в смену:
Qсм= Qгод/Тэф (7.7.1)
где Qгод - годовой объем сырья, м3.
Qсм= 131000/480=272,92 м3.
Длина дворика:
lдв=Qсм·dср/qбр·n·Ku·Kз (7.7.2)
где n - число двориков;
- коэффициент использования дворика,
;
- коэффициент заполнения дворика,
.
lдв=272,92·0,24519/0,383·3·0,7·1,2=69,33 м.
Ширина дворика определяется:
bдв=lбр +1 (7.7.3)
bдв=6,5+1=7,5м
Ширина бассейна:
B= bдв·n (7.7.4)
B=7,5·3=22,5
Длина дворика:
L= lдв+15 (7.7.5)
где 15 – длина приемного отделения.
L= 69,33+15=84,33м.
Принимаем размер бассейна 22,5х84,33 м.
Площадь бассейна 1897,43м2.
7.7. РАСЧЕТ ПЛОЩАДИ СКЛАДА ЛЕСА
Площадь склада сырья рассчитывается по формуле:
Fскл = (Qскл×(lбр + b)×Кз) / (Hшт×lбр×Ки×Кпл), (7.6.1.)
где Qскл - объем сырья, хранящийся на складе, м3;
Ншт - высота штабеля, м; Ншт = 8 м;
lбр - длина бревна, м;
b - расстояние между штабелями, м; b = 2;
Ки - коэффициент использования склада, Ки = 0,7;
Кз - коэффициент запаса, Кз = 1,2;
Кпл - коэффициент использования площади склада, Кпл = 0,67.
Расчет склада ведется на трехмесячный запас (90 дней):
Qскл = 131000/ 4 = 32750 м3.
Fскл = (32750×(6,5+ 2)×1,2) / (8×6,5×0,7×0,67) = 13697,31 м2.
7.8. РАСЧЕТ ПЛОЩАДИ СКЛАДА ПИЛОМАТЕРИАЛОВ
Площадь склада пиломатериалов рассчитывается по формуле:
Fскл = (А×Кз) / (Ншт×Кпл×Ки×Кп), (7.7.1.)
где А - пиломатериалы, подлежащие складированию: А = 15% от общего объема пиломатериалов;
Кз - коэффициент запаса, Кз = 1,2;
Ки - коэффициент использования, Ки = 0,7;
Кпл - коэффициент использования площади складов, Кпл=0,67
Кп - коэффициент плотности укладки, Кп = 0,7.
А = 71868×0,15 = 10780,2 м3,
Fскл = (10780,2×1,2) / (8×0,67×0,7×0,7) = 4925,46 м2.
И ЗАТОЧНЫХ СТАНКОВ
Ленточные пилы
Количество ленточных пил определяется по формуле:
, (8.1.1)
где Р - количество станочного инструмента;
N – количество часов работы инструмента в год;
Оно определяется по формуле:
(8.1.2)
где Т – продолжительность смены
- коэффициент загрузки;
l- число дней работы в году;
а – величина допускаемого стачивания инструмента, мм;
b – величина уменьшения рабочей части инструмента за 1 переточку, мм;
k - коэффициент, учитывающий аварийный износ пил, к=0,85;
t –продолжительность работы инструмента без переточки;
z – число одинаковых инструментов.
Принимаем 47 ленточных пилы марки B376.
Круглые пилы
Принимаем 299 круглых пилы марки 3420-0245.
Рубительные ножи
Принимаем 1057 рубительных ножа марки «Рошаль».
Коросниматели
Принимаем 668 короснимателей марки ГМЗ 08.04.01.
Количество абразивного инструмента рассчитывается отдельно для каждого вида режущего инструмента по формуле:
(8.4.1)
где Ра – потребное количество абразивного инструмента, шт.;
Т эф – эффективный фонд работы оборудования в год;
- удельная норма расхода абразивного инструмента;
= 0,02 – для пил;
= 0,052 – для ножей;
с – количество переточек инструмента в смену.
1) Для ленточных пил
2) Для круглых пил
3) Для рубительных ножей
4) Для короснимателей
Расчет заточных станков ведется для каждого вида инструмента с указанием марки станка:
(8.4.2)
где n зат - количество заточных станков, шт.;
U - количество инструмента, подлежащего заточке в смену:
U = n уст (8.4.3)
где n уст - количество установленного оборудования, шт.;
z n- количество инструмента, одновременно устанавливаемого в станке, шт.;
с - количество заточек в смену.
m– время на заточку инструмента;
Т – продолжительность смены, мин.;
k - коэффициент использования станка, k= 0,35-0,6.
1) Для ленточных пил
U= =4
Принимаем один станок GM 104S, техническая характеристика которого представлена в таблице 8.1
Таблица 8.1
Техническая характеристика
GM 104S
2) Для круглых пил
U= =28
Принимаем два станка СТчПК22, техническая характеристика которого представлена в таблице 8.2
Таблица 8.2
НА ТЕХНОЛОГИЧЕСКИЕ НУЖДЫ Расчет потребности в силовой электроэнергии сводится в табл.6
Расчет годовой потребности в электроэнергии Таблица 6.
Расход силовой энергии на 1м3 пиломатериалов: Э= где Э – расход электроэнергии на выпуск 1 куб. м. пиломатериалов; Э об - общие затраты силовой электроэнергии в год (табл.10): V – выпуск пиломатериалов в год, (табл.3) Э= 5% от общего объема электроэнергии идет на освещение. Общий расход электроэнергии равен:
ПОКАЗАТЕЛИ
Выработка пиломатериалов на чел / день определяется по формуле: где V – годовой объем пиломатериалов, куб. м.; Tэф – эффективный фонд работы цеха в год, дни; p– число рабочих в сфере лесоцеха. Основные технико-экономические показатели представляют в виде табл.8 Основные технико-экономические показатели лесопильного цеха Таблица 8
СПИСОК ЛИТЕРАТУРЫ 1) Ерёмина Л.К. Технология лесопильно-деревообрабатывающих производств: Учебное пособие. – Кострома,2003. – 50 с. 2) Песоцкий А.Н. Лесопильное производство – Москва,1970. – 432 с. 3) Кучеров И.К., Пашков В.К. Станки и инструменты лесопильно-деревообрабатывающего производства. М.: Лесная промышленность, 1970.
СОДЕРЖАНИЕ стр. Введение………………………………………………………………….4 1. Спецификация сырья и пиломатериалов…………………………….5 1.1. Характеристика сырья по ГОСТ 9463-88………………………….5 1.2. Характеристика пиломатериалов по ГОСТ 24454-80…………….7 2. Составление и расчет поставов на ЭВМ…………………………….8 2.1. Проверка возможности выполнения задания по объему сырья и определение процента брусовки………………………………...8 2.2. Расчет поставов на ЭВМ…………………………………………...9 3. Составление плана раскроя сырья…………………………………..9 4. Составление баланса древесины…………………………………...12 4.1. Расчет объема опилок……………………………………………..12 4.2. Расчет объема кусковых отходов и щепы………………………..13 5. Определение количественного, качественного, спецификационного выхода пиломатериалов………………………..15 6. Выбор и расчет основного технологического оборудования…….16 6.1. Выбор оборудования……………………………………………...16 6.2. Расчет потребности ленточнопильных станков…………………17 6.3. Расчет потребности круглопильных станков……………………18 6.4. Расчет потребности обрезных станков…………………………...19 6.5. Расчет потребности торцовочных станков………………………20 6.6. Расчет потребности окорочных станков…………………………21 6.7. Расчет потребного количества рубительных машин……………22 6.8. Расчет потребного количества машин для сортировки щепы……………………………………………....23 6.9.Расчет сортировочных устройств для сортировки п/м…………..24 6.10.Расчет потребного количества линий сортировки пиловочных бревен………………………………………………...26 6.11.Выбор околостоночного оборудования…………………………27 7. Расчет транспортных средств и площадей складов……………….27 7.1. Расчет продольного одноцепного конвейера....…………………27 7.2. Расчет ленточного транспортера…………………………………28 7.3. Расчет скребкового транспортера для опилок…………………..29 7.4. Расчет потребного количества автолесовозов…………………...30 7.5. Расчет потребного количества кранов на складах леса и пиломатериалов…………………………………..31 7.6. Расчёт площади бассейна…………………………………………32 7.7. Расчет площади склада леса……………………………………....33 7.8. Расчет площади склада пиломатериалов………………………...33 8. Расчет режущего, абразивного инструмента и заточных станков……………………………………………………………….34 8.1. Расчет потребного количества ленточных пил………………….34 8.2. Расчет потребного количества круглых пил…………………….34 8.3. Расчет потребного количества ножей для рубительной машины……………………………………………..35 8.4. Расчет потребного количества короснимателей………………...35 8.5. Расчет потребного количества абразивного инструмента………………………………………………………..35 8.6. Расчет потребного количества заточных станков……………….36 9. Расчет потребности электроэнергии на технологические нужды……………………………………………….38 9.1. Расчет годовой потребности в электроэнергии…………………40 10. Определение количества рабочих………………………………...40 11. Основные технико-экономических показатели………………….42 12. Охрана труда и противопожарная защита………………………..43 Список литературы…………………………………………………….45
ВВЕДЕНИЕ
Ни одна отрасль народного хозяйства не обходится без древесины. Поэтому важную роль в развитии экономики играет лесообрабатывающая отрасль промышленности. Производство пиломатериалов занимает ведущее место в лесопильно-деревообрабатывающей промышленности и является начальной стадией процесса изготовления большинства изделий. С увеличением производства пиломатериалов происходили изменения в технологии, организации и технике. От некогда примитивного способа выработки досок путем раскалывания бревен на две или, в лучшем случае, на три части с последующей оттеской топором пиломатериалы стали вырабатывать путем распиловки бревен ручными, а затем рамными пилами. Рамное пиление бревен на доски в свою очередь совершенствовалось: создавалась новая техника, улучшались организация и механизация всех процессов. Современные лесопильные заводы представляют собой по преимуществу крупные предприятия, оборудованные новейшими станками и приспособлениями с высокой механизацией всех процессов. Важнейшие задачи лесопильно-деревообрабатывающей промышленности в перспективный период следующие: 1. улучшение использования древесного сырья в процессах производства пиломатериалов и заготовок; 2. полное использование неизбежных отходов для выработки древесно-плитным и древесных материалов; 3. всемерная механизация и автоматизация всех процессов производства. Решение этих задач требует создания комбинированных предприятий, включающих цехи производства пиломатериалов, сушки древесины, раскроя пиломатериалов на целые заготовки и заготовки для склейки, производства клееных заготовок и деталей, переработки неизбежных отходов, механической обработки древесины в полноценную продукцию, а в ряде случаев и цехи выпуска готовых изделий. Решающее условие дальнейшего развития лесной и деревообрабатывающей промышленности - повышение производительности труда, основанное на ускорении научно-технического прогресса. Основное вним
![]() Индивидуальные и групповые автопоилки: для животных. Схемы и конструкции... ![]() Поперечные профили набережных и береговой полосы: На городских территориях берегоукрепление проектируют с учетом технических и экономических требований, но особое значение придают эстетическим... ![]() Типы оградительных сооружений в морском порту: По расположению оградительных сооружений в плане различают волноломы, обе оконечности... ![]() История создания датчика движения: Первый прибор для обнаружения движения был изобретен немецким физиком Генрихом Герцем... © cyberpedia.su 2017-2024 - Не является автором материалов. Исключительное право сохранено за автором текста. |