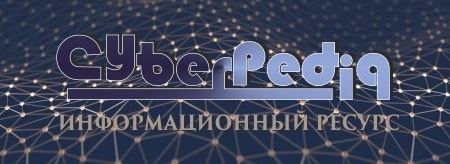
Наброски и зарисовки растений, плодов, цветов: Освоить конструктивное построение структуры дерева через зарисовки отдельных деревьев, группы деревьев...
История создания датчика движения: Первый прибор для обнаружения движения был изобретен немецким физиком Генрихом Герцем...
Топ:
Выпускная квалификационная работа: Основная часть ВКР, как правило, состоит из двух-трех глав, каждая из которых, в свою очередь...
Генеалогическое древо Султанов Османской империи: Османские правители, вначале, будучи еще бейлербеями Анатолии, женились на дочерях византийских императоров...
Определение места расположения распределительного центра: Фирма реализует продукцию на рынках сбыта и имеет постоянных поставщиков в разных регионах. Увеличение объема продаж...
Интересное:
Влияние предпринимательской среды на эффективное функционирование предприятия: Предпринимательская среда – это совокупность внешних и внутренних факторов, оказывающих влияние на функционирование фирмы...
Берегоукрепление оползневых склонов: На прибрежных склонах основной причиной развития оползневых процессов является подмыв водами рек естественных склонов...
Что нужно делать при лейкемии: Прежде всего, необходимо выяснить, не страдаете ли вы каким-либо душевным недугом...
Дисциплины:
![]() |
![]() |
5.00
из
|
Заказать работу |
|
|
По функциональному назначению классификация может быть предварительная, для удаления из питания мельницы готового продукта, и поверочная для возврата недоизмельченного материала в мельницу. Классификация может осуществляться в два приема, тогда вторая операция называется контрольной. Такое разделение операций позволяет оптимизировать условия классификации: первый прием проводится в спиральных классификаторах в скальпирующем режиме или на грохоте, контрольная – в гидроциклонах.
Количество стадий измельчения определяется крупностью конечного продукта. В наиболее простом случае организации схемы вся работа измельчения совершается до начала обогатительных операций. В этом случае следуют следующим правилам:
при крупности измельчения до 60-65% -0,074 мм используют одностадиальную схему либо, если ожидаются затруднения с получением достаточно тонкого слива, схему.
при крупности измельчения до 80% используют двухстадиальные схемы.
при крупности измельчения 80-95% используют трехстадиальную схему.
![]() |
Рисунок 2‑2Одностадиальная схема измельчения
Цехи дробления
На основе данных базового расчета выполняется предварительный выбор дробилок и грохотов, далее рассчитывается их производительность в заданных условиях и, в процессе сравнительного анализа, выбирается окончательный вариант установки оборудования. При необходимости производится корректировка базового расчета – режима работы цехов и распределения общей степени дробления по стадиям схемы – и повторный расчет и выбор оборудования.
|
Методы расчета гранулометрического состава продуктов дробления
Традиционно же для целей проектирования используются упрощенные методы на основе типовых гранулометрических характеристик. При этом принято считать, что:
· -материал мельче ширины разгрузочного отверстия дробилки не дробится;
· материал крупнее ширины разгрузочного отверстия дробилки дробится;
причем продукт дробления имеет типовой для данного типа дробилки грансостав вне зависимости от размера исходного крупного класса.
В соответствии с этими упрощениями, содержание класса крупности в продукте стадии дробления определяется соотношениями:
(14)
где - суммарная гранулометрическая характеристика по минусу дробленого продукта;
- суммарная гранулометрическая характеристика по минусу питания стадии дробления;
- выход классов питания крупнее ширины разгрузочной щели дробилки;
- типовая гранулометрическая характеристика дробилки.
Выбор и расчет дробилок
Для дробления руд средней крепости и крепких применяются конусные дробилки, а также, на стадии крупного дробления, щековые дробилки с простым качанием щеки. Последние годы за рубежом разработаны и выпускаются также щековые дробилки со сложным качанием щеки с большим размером загрузочной щели для крупного дробления.
Для последующего сравнительного анализа предварительно отбираются дробилки, соответствующие требованиям табл.26 и табл.28 [[1]]. Отбираются дробилки, у которых размер загрузочного отверстия превышает заданный и диапазон регулировки разгрузочной щели включает заданную. У дробилок крупного дробления в каталогах указывается только номинальная разгрузочная щель. В этом случае считается, что диапазон регулировки составляет 40 %.
Для предварительно выбранных дробилок рассчитывается производительность в заданных условиях работы. Расчет производится по формуле:
(15)
где - поправочные коэффициенты соответственно на крупность питания, крепость и влажность
|
Поправочные коэффициенты определяются по следующим выражениям:
(16)
где
- номинальная крупность питания дробилки, мм
f – коэффициент крепости по Протодьяконову
w – влажность руды, %
Окончательный выбор варианта установки дробильного оборудования производится в результате сравнительного технико-экономического анализа, исходные данные и результаты которого сводятся в таблицу (Ошибка! Источник ссылки не найден. 3-3). Количество оборудования для установки определяется по формуле:
(17)
где Qп – нагрузка на дробилку, м3/час
Q – производительность дробилки, м3/час
Коэффициент загрузки оборудования по производительности определяется выражением:
(18)
Количество N дробилок для установки выбираем ближайшим большим целым от n.
Сравнение рассчитанных вариантов производим по общей установленной мощности оборудования и общей массе.
Таблица 3‑1 Расчет качественно-количественной схемы дробления
Номер по схеме | Продукт | Крупность, мм | Разгрузочная щель i, мм | Содержание класса +i в питании стадии, % | Содержание класса крупности -d (мм), % | Выход продукта | |||||||
5 | 10 | 28 | 57 | 130 | 261 | 1200 | % | м3/час | |||||
1 | Исходная руда | 1 200 |
|
| 1,2 | 2,3 | 6,4 | 12,4 | 26,2 | 45,6 | 93,9 | 100 | 812,3 |
| Грохочение | 1 200 |
|
|
|
|
|
|
| 45,6 | 93,9 |
|
|
2 | Крупнодробленая руда | 261 | 174 | 66,6 | 3,8 | 7,5 | 20,3 | 37,6 | 71,5 | 97,1 |
| 100 | 812,3 |
4 | Питание дробилок 2 стадии |
|
|
|
|
|
|
|
|
|
| 100,0 | 812,3 |
6 | Среднедробленая руда | 57 | 30 | 78,8 | 9,8 | 20,5 | 62,8 | 97,0 |
|
|
| 100 | 812,3 |
7 | Питание грохотов 3 стадии |
|
|
| 28,12 | 56,2 |
|
|
|
|
| 209,2 | 1699,5 |
8 | Питание дробилок 3 стадии |
|
|
|
|
|
|
|
|
|
| 109,2 | 887,1 |
10 | Мелкодробленая руда | 12 | 12 | 75,3 | 43,0 | 89,6 |
|
|
|
|
| 100 | 812,3 |
Таблица 3‑2 Результаты предварительного выбора дробилок и расчет производительности
Модель
Рагрузочная щель, ОТ-ДО, мм
Объемная производительность,
ОТ-ДО, м3/час
Производительность дробилки Q при принятых i и B и значениях поправочных коэффициентов
|
ЩДП 12х15
1200
155
0
310
0
160
116
186
1380
1200
0,80
0,88
328,0
ККД-1200/150
1200
180
0
680
0
320
240
186
1380
1200
0,80
0,88
619,5
КСД-2200Гр
350
60
30
610
360
250
86
29
300
308
0,92
1,01
357,7
КСД-3000Т
475
50
25
850
425
400
217
29
300
308
1,15
1,27
629,1
КМД-1750Гр
130
20
9
130
95
160
53
12
64
56
1,37
1,51
157,9
КМД-1750Т
80
15
5
110
85
160
53
12
64
56
1,11
1,22
124,7
КМД-2200Гр
140
20
10
260
220
250
97
12
64
56
1,40
1,54
352,0
КМД-2200Т1
100
15
5
220
160
250
97
12
64
56
1,24
1,37
276,6
КМД-2200Т2
85
15
7
210
150
320
93
12
64
56
1,15
1,26
236,6
КМД-3000Т
95
20
6
440
320
400
220
12
64
56
1,22
1,34
496,7
Таблица 3‑3 Сравнительный анализ вариантов установки дробильного оборудования
Тип | Параметры дробилки | Нагрузка на дробилку, м3/час | Количество | Характеристика варианта | |||||
Производительность, м3/час | Масса, тонн | Установленная мощность, квт | по расчету | Выбран-ное число | Масса, тонн | Установленная мощность, квт | Коэффициент загрузки | ||
ЩДП 12х15 | 328,0 | 116 | 160 | 812,3 | 2,48 | 3 | 348 | 480 | 0,83 |
ККД-1200/150 | 619,5 | 240 | 320 | 812,3 | 1,31 | 2 | 480 | 640 | 0,66 |
КСД-2200Гр | 357,7 | 86 | 250 | 812,3 | 2,27 | 3 | 258 | 750 | 0,76 |
КСД-3000Т | 629,1 | 217 | 400 | 812,3 | 1,29 | 2 | 434 | 800 | 0,65 |
КМД-1750Гр | 157,9 | 53 | 160 | 887,6 | 5,62 | 6 | 318 | 960 | 0,94 |
КМД-1750Т | 124,7 | 53 | 160 | 887,6 | 7,12 | 8 | 424 | 1280 | 0,89 |
КМД-2200Гр | 352,0 | 97 | 250 | 887,6 | 2,52 | 3 | 291 | 750 | 0,84 |
КМД-2200Т1 | 276,6 | 97 | 250 | 887,6 | 3,21 | 4 | 388 | 1000 | 0,80 |
КМД-2200Т2 | 236,6 | 93 | 320 | 887,6 | 3,75 | 4 | 372 | 1280 | 0,94 |
КМД-3000Т | 496,7 | 220 | 400 | 887,6 | 1,79 | 2 | 440 | 800 | 0,89 |
Выбранный вариант установки дробильного оборудования | |||||||||
ККД-1200/150 | 619,5 | 240 | 320 | 812,3 | 1,31 | 2 | 480 | 640 | 0,66 |
КСД-3000Т | 629,1 | 217 | 400 | 812,3 | 1,29 | 2 | 434 | 800 | 0,65 |
КМД-2200Гр | 352,0 | 97 | 250 | 887,6 | 2,52 | 3 | 291 | 750 | 0,84 |
По результатам таблицы 3-3 предварительно выбраны дробилки:
ККД- 1200/1500 – 2 шт. К=0,66
КСД 3000Т - 2 шт. К=0,65
КМД 2200Гр – 3 шт. К=0,84
3.4 Выбор и расчет грохотов
В цехах дробления рудных обогатительных фабрик используются вибрационные грохоты в среднем и тяжелом исполнении, необходимая площадь грохочения которых рассчитывается по формуле:
(19)
|
где F – площадь грохочения, м2
Q –нагрузка на грохоты, м3/час
q – удельная производительность грохота, м3/м2час [7]
k, l, m, n, o, p –поправочные коэффициенты [1, табл. 30, стр. 223]
Все параметры и результаты расчета сводятся в таблицу (табл.3.4)
Предварительный выбор грохотов из каталога производится по допускаемой крупности исходного материала, числу ярусов сит и размеру отверстий сит. Последний параметр не является жестким ограничением. Результаты сводятся в таблицу.
Таблица 3.4 –значение поправочных коэффициентов и расчет площадь
Условия грохочения, учитываемые коэффициентом | Коэффи-циент | Условия по стадиям | Значения коэффициентов по стадиям | ||
2 | 3 | 2 | 3 | ||
Удельная производительность, м3/м2*час (при заданном размере ячейки грохота, мм) | q | 56 | 12 | 47 | 21 |
Содержание в исходном материале зерен размером менее половины размера отверстий сита, % | k | 18,0 | 28,1 | 0,58 | 0,76 |
Содержание в исходном материале зерен размером более размера отверстий сита, % | l | 66,3 | 43,8 | 1,46 | 1,12 |
Эффективность грохочения, % | m | 85,0 | 85,0 | 1 | 1 |
Форма зерен | n | руда | руда | 1 | 1 |
Влажность материала | o | сухой | сухой | 1 | 1 |
Способ грохочения | p | сухое | сухое | 1 | 1 |
Нагрузка на грохоты, м3/час |
|
|
| 812,3 | 1699,9 |
Площадь просеивающей поверхности, м2 |
|
|
| 20,4 | 94,5 |
Таблица 3.5 –Поправочные коэффициенты для расчета производительности грохотов
Содержание в исходном материале зерен размером менее половины размера отверстий сита, % | 0 | 10 | 20 | 30 | 40 | 50 | 60 | 70 | 80 | 90 |
Коэффициент k | 0,4 | 0,5 | 0,6 | 0,8 | 1 | 1,2 | 1,4 | 1,6 | 1,8 | 2 |
Содержание в исходном материале зерен размером более размера отверстий сита, % | 10 | 20 | 25 | 30 | 40 | 50 | 60 | 70 | 80 | 90 |
Коэффициент l | 0,94 | 0,97 | 1 | 1,03 | 1,09 | 1,18 | 1,32 | 1,55 | 2 | 3,36 |
Эффективность грохочения, % | 40 | 50 | 60 | 70 | 80 | 90 | 92 | 94 | ||
Коэффициент m | 2,3 | 2,1 | 1,9 | 1,65 | 1,35 | 1 | 0,9 | 0,8 | ||
Форма зерен | Дробленый материал разный (кроме угля) | Округленная (например.морская галька) | Уголь | |||||||
Коэффициент n | 1 | 1,25 | 1,5 | |||||||
Влажность материала | Для отверстий сита менее 25 мм | Для отверстий сита более 25 мм | ||||||||
Сухой | Влажный | Комкующийся | В зависимости от влажности | |||||||
Коэффициент o | 1 | 0.75–0.85 | 0.2–0.6 | 0.9–1.0 | ||||||
Способ грохочения | Для отверстий сита менее 25 мм | Для отверстий сита более 25 мм | ||||||||
Сухое | Мокрое с орошением | Любое | ||||||||
Коэффициент p | 1 | 1.25–1.40 | 1 |
Таблица 3.6- Результаты предварительного выбора грохотов
Модель | Площадь одного сита, м2 | Мощность электродвигателя, кВт | Масса грохота, кг | Размеры просеивающей поверхности, мм: | Размеры отверстий сит (решеток), мм: | Допускаемая крупность исходного материала, мм | Количество грохотов | Установленная мощность, т | Масса, т
| Коэффициент загрузки | ||||
ширина | длина | верхнего | нижнего | расчет | принято | |||||||||
Стадия мелкого дробления |
|
|
| |||||||||||
ГСТ51 | 7,875 |
| 4650 | 1750 | 4500 | Перфорированный лист 30, щелевидное сито 1,6; сетка 10 × 10 | – | 120 | 2,65 | 3 | 0 | 13,95 | 0,88 | |
ГСТ61 | 10 |
| 6000 | 2000 | 5000 | 8; 12;16; 20 | – | 200 | 9,45 | 10 | 0 | 60 | 0,94 | |
ГСТ61 (259Гр) | 8 |
| 6200 | 2000 | 4000 | 2–25 | – | 100 | 11,81 | 12 | 0 | 74,4 | 0,98 | |
ГСТ61 (253Гр) | 10 |
| 5700 | 2000 | 5000 | 2–25 | – | 100 | 9,45 | 10 | 0 | 57 | 0,94 | |
ГСТ81 | 18 | 18000 | 3000 | 6000 | - | - | 120 | 5,25 | 6 | 0 | 108 | 0,87 | ||
ГИС 62 | 10 | 17 | 5100 | 2000 | 5000 | – | – | 150 | 9,45 | 10 | 170 | 51 | 0,94 | |
|
|
|
| |||||||||||
Продолжение таблицы 3.6 | ||||||||||||||
Стадия среднего дробления |
|
|
|
| ||||||||||
|
|
|
|
| ||||||||||
ГИТ 52М | 6,755 | 22 | 1700 | 1750 | 3860 | 8–100 | – | 400 | 13,98 | 14 | 308 | 23,8 | 1,00 | |
ГИТ 51 | 6,125 | 22 | 6000–9000 | 1750 | 3500 | 50–300 | – | 400 | 3,40 | 4 | 88 | 32 | 0,85 | |
ГИТ 51M | 6,755 | 17 | 800 | 1750 | 3860 | 8–100 | – | 400 | 3,09 | 4 | 68 | 3,2 | 0,77 | |
ГИТ 71 | 13,2 | 30 | 1750 | 2500 | 5300 | 25–150 | – | 800 | 1,58 | 2 | 60 | 3,5 | 0,79 |
Таблица 3.7- Окончательный выбор грохотов
Модель | Площадь одного сита, м2 | Мощность электродвигателя, кВт | Масса грохота, кг | Размеры просеивающей поверхности, мм: | Размеры отверстий сит (решеток), мм: | Допускаемая крупность исходного материала, мм | Количество грохотов | Установленная мощность, т | Масса, т | Коэффициент загрузки | |||
ширина | длина | верхнего | нижнего | расчет | принято | ||||||||
Стадия мелкого дробления |
|
|
|
|
|
|
|
|
|
|
|
|
|
ГСТ51 | 7,875 | 0 | 4650 | 1750 | 4500 | Перфорированный лист 30, щелевидное сито 1,6; сетка 10 × 10 | – | 120 | 2,65 | 3 | 0 | 13,95 | 0,88 |
Стадия среднего дробления |
|
|
|
| |||||||||
ГИТ 71 | 13,2 | 30 | 1750 | 2500 | 5300 | 25–150 | – | 800 | 1,58 | 2 | 60 | 3,5 | 0,79 |
Исходя из таблицы расчетов грохотов на 2 дробилки КСД-3000Т выбрал2 грохотаГИТ71.
На 3 дробилки мелкого дробления КМД-2200Гр выбрал 3 грохотовГСТ51.
4 Измельчительное отделение
|
|
Особенности сооружения опор в сложных условиях: Сооружение ВЛ в районах с суровыми климатическими и тяжелыми геологическими условиями...
Типы сооружений для обработки осадков: Септиками называются сооружения, в которых одновременно происходят осветление сточной жидкости...
Семя – орган полового размножения и расселения растений: наружи у семян имеется плотный покров – кожура...
История создания датчика движения: Первый прибор для обнаружения движения был изобретен немецким физиком Генрихом Герцем...
© cyberpedia.su 2017-2024 - Не является автором материалов. Исключительное право сохранено за автором текста.
Если вы не хотите, чтобы данный материал был у нас на сайте, перейдите по ссылке: Нарушение авторских прав. Мы поможем в написании вашей работы!