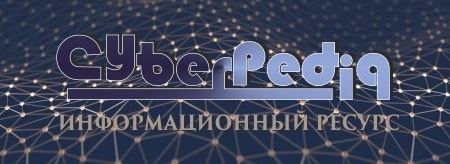
Семя – орган полового размножения и расселения растений: наружи у семян имеется плотный покров – кожура...
Автоматическое растормаживание колес: Тормозные устройства колес предназначены для уменьшения длины пробега и улучшения маневрирования ВС при...
Топ:
Методика измерений сопротивления растеканию тока анодного заземления: Анодный заземлитель (анод) – проводник, погруженный в электролитическую среду (грунт, раствор электролита) и подключенный к положительному...
Марксистская теория происхождения государства: По мнению Маркса и Энгельса, в основе развития общества, происходящих в нем изменений лежит...
Проблема типологии научных революций: Глобальные научные революции и типы научной рациональности...
Интересное:
Распространение рака на другие отдаленные от желудка органы: Характерных симптомов рака желудка не существует. Выраженные симптомы появляются, когда опухоль...
Наиболее распространенные виды рака: Раковая опухоль — это самостоятельное новообразование, которое может возникнуть и от повышенного давления...
Инженерная защита территорий, зданий и сооружений от опасных геологических процессов: Изучение оползневых явлений, оценка устойчивости склонов и проектирование противооползневых сооружений — актуальнейшие задачи, стоящие перед отечественными...
Дисциплины:
![]() |
![]() |
5.00
из
|
Заказать работу |
|
|
В машиностроительном производстве выработаны принципы организации производственного процесса, определяющие его эффективность. Она проявляется в высоком уровне производительности труда, минимальном при прочих равных условиях уровне себестоимости продукции и ее высоком качестве, минимальных сроках изготовления изделий и др.
Организация производственного процесса на любом машиностроительном предприятии, в цехе или на участке базируется на рациональном сочетании во времени и в пространстве всех основных, вспомогательных
и обслуживающих процессов. Это позволяет выпускать продукцию при минимальных затратах живого и овеществленного труда. Особенности
и методы такого сочетания различны в разных производственных условиях и представляют собой исходные положения, на основе которых осуществляются построение, функционирование и развитие производственных процессов.
Рациональная организация производства должна строиться на принципах дифференциации, специализации, пропорциональности, параллельности, непрерывности, прямоточности, ритмичности и автоматичности.
Принцип дифференциации предполагает разделение производственного процесса на отдельные технологические процессы, которые в свою очередь подразделяются на операции, переходы, приемы и движения, что способствует выбору наилучших условий для его осуществления и обеспечивает минимизацию суммарных затрат всех видов ресурсов.
Выделение непродолжительных по времени выполнения операций позволяет упрощать организацию и технологическое оснащение производства, совершенствовать навыки рабочих, увеличивать производительность их труда. Однако чрезмерная дифференциация за счет монотонности и высокой интенсивности процессов производства повышает утомляемость рабочих на ручных операциях. А большое число операций приводит к излишним затратам на перемещение предметов труда между рабочими местами, их установку, закрепление и снятие с рабочих мест после окончания операций.
|
Специализация – это одна из форм разделения труда, которая заключается в том, что предприятие в целом и его подразделения производят продукцию ограниченного ассортимента, при этом используются специальные материалы и оборудование.
Принцип специализации обусловливает выделение на предприятии цехов, участков, линий и отдельных рабочих мест. Они отличаются особым производственным процессом. Специализация процесса (рабочих мест) связана с сокращением количества наименований работ, операций на каждом рабочем месте.
Специализированными могут быть процессы изготовления как отдельных групп деталей, так и серий.
Количественно уровень специализации процесса производства характеризуется коэффициентом специализации k сп:
k сп =
где т доп – количество деталеопераций, обрабатываемых в производственном подразделении за анализируемый промежуток времени (месяц, год); С р.м– количество рабочих мест в производственном подразделении (участке, цехе).
Принцип пропорциональности – это принцип, реализация которого обеспечивает равную пропускную способность всех рабочих мест одного технологического процесса, пропорциональное обеспечение рабочих мест необходимыми ресурсами (материальными, кадровыми и другими (в зависимости от процесса). Принцип пропорциональности также предполагает равную пропускную способность всех производственных подразделений, выполняющих основные, вспомогательные и обслуживающие процессы.
Таким образом, под пропорциональностью производственного процесса понимается такое его состояние, при котором все производственные подразделения предприятия, участвующие в нем, работают с одинаковой производительностью, способствующей выполнению в установленные сроки производственной программы, которая предусмотрена планом. Пропорциональность должна обеспечиваться не только между основными производственными процессами, но и между основными, вспомогательными и обслуживающими процессами.
|
Пропорциональность процессов позволяет эффективно использовать ресурсы за счет полной загрузки производственных мощностей и трудовых ресурсов, технических средств и информации.
Нарушение принципа пропорциональности приводит к возникновению узких мест в производстве или, наоборот, к неполной загрузке отдельных рабочих мест, участков, цехов, а также к снижению эффективности функционирования всего предприятия. Поэтому для обеспечения пропорциональности необходимо проведение расчетов производственной мощности как по стадиям производства, так и по группам оборудования и производственным площадям.
Основными направлениями обеспечения пропорциональности являются проектно-конструкторские, технологические и организационные мероприятия.
Рассмотрим пример. Первоначальная мощность рабочих мест (штук в смену) по изготовлению партии деталей из четырех операций была следующей (рис. 3.4).
![]() |
М1 = 20 М2 = 30 М3 = 12 М4 = 20
Рис. 3.4. Схема технологического процесса из четырех операций
Пропускная способность (мощность) технологической цепочки по узкому – третьему – рабочему месту составила 12 штук в смену. Мощность второго рабочего места используется на 40 % (, а мощности первого и четвертого – на 60 % (
.
Примем как исходное условие, что производственная потребность
в деталях составляет 20 штук в смену. Тогда для реализации принципа пропорциональности третье рабочее место требует установки еще одного аналогичного станка с такой же производительностью, после чего мощность этого рабочего места увеличится до 24 штук в смену. В этом случае потребуется дозагрузка второго и третьего рабочих мест.
Если известны объем выпуска деталей в заданный период N з и норма штучного времени t шт, то можно определить загрузку i -й группы оборудования:
и пропускную способность этой группы оборудования:
где F з – фонд времени в заданный период; k см – коэффициент сменности. Затем необходимо сопоставить загрузку и пропускную способность
i -й группы оборудования и вычислить коэффициент его загрузки:
|
где Pi – пропускная способность. Предпочтительным вариантом является такой, при которой и Qi = Р i.
Рассмотрим оценку пропорциональности на примере технологической цепочки по разряду работ (табл. 3.3).
Таблица 3.3
Пример оценки пропорциональности
Показатель
| Рабочие места | |||
1 | 2 | 3 | 4 | |
Разряд работ по технологии | 4 | 3 | 3 | 5 |
Разряд рабочего | 3 | 3 | 4 | 3 |
Анализ данных табл. 3.3 показывает, что на первом и четвертом рабочих местах разряд рабочего ниже требуемого разряда работ по технологии, значит велика вероятность брака. На третьем рабочем месте, наоборот, работы третьего разряда выполняет рабочий четвертого. В этом случае можно получить перерасход заработной платы, если оплату рабочему производить с учетом его разряда. На последнем рабочем месте выполняется финишная, чистовая операция, соответствующая пятому разряду, но эту работу выполняет рабочий третьего разряда. Экономия на заработной плате здесь противопоставляется значительному риску появления брака из-за недостаточной квалификации исполнителя. Четвертое рабочее место выступает наиболее узким местом, для которого пропорциональность технологической цепочки равна %.
В целом следует отметить, что реализация принципа пропорциональности обеспечивает равную пропускную способность всех рабочих мест одного технологического процесса, пропорциональное обеспечение рабочих мест информацией, материальными ресурсами, кадрами и т. д. Пропорциональность производства исключает перегрузку одних участков, т. е. возникновение узких мест, и недоиспользование мощностей на других участках, является предпосылкой равномерной работы предприятия и обеспечивает бесперебойный ход производства.
Уровень пропорциональности оценивается коэффициентом k пр:
k пр =
где М min и М max – соответственно минимальная и максимальная пропускная способность, или параметр рабочего места в технологической цепочке (например, мощность, производительность, обеспеченность ресурсами, разряд работ и т. п.).
|
В идеальном случае значение коэффициента пропорциональности должно стремиться к единице. Для этого применяются следующие проектно-конструкторские, технологические и организационные мероприятия:
– пересмотр конструкции детали с целью обеспечения пропорциональности операций по трудоемкости;
– пересмотр технологического процесса, режимов обработки;
– разработка и реализация организационных мероприятий по замене оборудования, перепланировке участка;
– дозагрузку рабочих мест другой аналогичной деталью.
Как отмечалось ранее, обеспечение пропорциональности процессов позволяет эффективно использовать ресурсы за счет полной загрузки производственных мощностей и трудовых ресурсов.
Одним из методов поддержания пропорциональности в производстве является оперативно-календарное планирование, которое позволяет разрабатывать задания для каждого производственного звена с учетом, с одной стороны, комплексного выпуска его продукции, а с другой – наиболее полного использования возможностей производственного аппарата.
Для достижения пропорциональности процессов необходимо проводить оптимизационные расчеты загрузки технологического оборудования, надежности разрабатываемых объектов, их производительности (пропускной способности). Для условий крупносерийного и массового производства выполняются детальные оптимизационные расчеты, а для условий единичного производства – укрупненные расчеты.
Усложнение продукции, использование полуавтоматического и автоматического оборудования, углубление разделения труда увеличивает число параллельно проводимых процессов по изготовлению одного продукта, органическое сочетание которых необходимо обеспечить, т. е. дополняет пропорциональность принципом параллельности.
Принцип параллельности – это принцип, который заключается в обеспечении максимально возможного одновременного выполнения частичных производственных процессов в их общем комплексе при изготовлении изделий. Чем шире фронт работ, тем меньше при прочих равных условиях длительность изготовления продукции.
Принциппараллельностипредполагает одновременное выполнение отдельных производственных процессов и операций над аналогичными деталями и частями изделия на различных рабочих местах, т. е. создание широкого фронта работ по изготовлению данного изделия. В сложных изделиях сотни и тысячи деталей обрабатываются одновременно, прежде чем они будут направлены на окончательную сборку. Параллельность реализуется на всех уровнях организации производства и в различных формах. Параллельное выполнение основных процессов обеспечивается при одновременном изготовлении заготовок и обработке деталей, их многопредметной обработке, выполнении сборочно-монтажных операций над одинаковыми или различными объектами. Параллельность в выполнении основных и вспомогательных элементов операции заключается в совмещении времени машинной обработки со временем установки и съема деталей, проведения контрольных промеров и т. п.
|
Реализация принципа параллельности способствует сокращению продолжительности производственного цикла и, как следствие, экономию рабочего времени. Чем больше совмещений, тем сложнее организация процесса, но тем короче его длительность. Параллельность процесса характеризуется степенью совмещения операций во времени и оценивается коэффициентом :
где и
– времена технологического цикла при параллельном
и последовательном сочетании операций соответственно.
Обеспечение параллельности процессов является важнейшей задачей при организации производства, так как оно позволяет сократить длительность производственных и управленческих циклов во времени.
Принцип непрерывности означает, что рабочий трудится без простоев, оборудование работает без перерывов, а предметы труда не пролеживают на рабочих местах. Принцип непрерывности – это принцип рациональной организации процесса, определяемый отношением рабочего времени к общей продолжительности процесса.
Соблюдение принципа непрерывности производственного процесса позволяет повысить удельное значение технологического времени
и уменьшить общую продолжительность изготовления изделия, что в значительной мере способствует повышению интенсификации производства.
Сущность принципа непрерывности состоит в том, что производственный процесс должен организовываться таким образом, чтобы в нем либо вовсе отсутствовали перерывы, либо они были минимальными. В машиностроении реализация этого принципа связана с большими трудностями и полностью достигается лишь тогда, когда при производстве какого-либо изделия все технологические операции по продолжительности равны или кратны друг другу. Это обеспечивает одновременную передачу деталей с одного рабочего места на другое, а следовательно, и непрерывность производственного процесса в целом.
Принцип непрерывности как принцип рациональной организации процесса оценивается коэффициентом непрерывности, который определяется отношением рабочего времени к общей продолжительности этого процесса:
k непр =
где Т раб – рабочее время; Т цикл – общая продолжительность процесса, включающая простои или пролеживания предмета труда на рабочих местах и/или между ними. Наиболее полно этот принцип реализуется в массовом или крупносерийном производстве при организации поточных методов производства, в частности при организации одно- и многопредметных непрерывно-поточных линий.
Повышение непрерывности – важнейшее направление интенсификации производства, способствующее ускорению оборачиваемости средств.
Непрерывность производства рассматривается в аспекте непрерывного участия в процессе производства предметов труда и аспекте непрерывной загрузки оборудования и рационального использования рабочего времени. Реализация принципа непрерывности движения предметов труда должна одновременно сочетаться с минимизацией остановок оборудования для переналадки, в ожидании поступления материалов и т. п. Это требует повышения однообразия работ, выполняемых на каждом рабочем месте, а также использования быстропереналаживаемого оборудования (станков с программным управлением), копировальных станков и т. д.
Одним из принципов, обеспечивающих непрерывность производственного процесса, является принцип прямоточности в организации производства. Прямоточность направлена на достижение кратчайшего пути прохождения изделием всех стадий и операций производственного процесса – от запуска в производство исходных материалов и до выхода готовой продукции. Прямоточность характеризует оптимальность пути прохождения предмета труда, информации и т. п., исключающей бессмысленные возвраты на старое место из-за неорганизованности процесса.
В соответствии с принципом прямоточности взаимное расположение зданий и сооружений на территории предприятия, а также размещение
основных цехов должно соответствовать требованиям производственного процесса. Поток материалов, полуфабрикатов и изделий должен быть поступательным и кратчайшим, без встречных и возвратных движений. Вспомогательные цехи и склады должны размещаться по возможности ближе к обслуживаемым ими основным цехам.
Для анализа соблюдения принципа прямоточности используется коэффициент прямоточности важнейших производственных и управленческих процессов:
где
– оптимальная и фактическая (проектная) длина прохождения предмета труда по i -му процессу соответственно.
Обеспечение прямоточности процессов позволяет сокращать длительность производственных и управленческих циклов в пространстве
и времени.
Основными факторами оптимизации прямоточности процессов явля-ются:
– расположение подразделений организационной и производственной структур по ходу соответствующих процессов;
– концентрация процессов под одной крышей;
– сокращение расстояния между компонентами процессов;
– системный анализ и оптимизация коэффициента прямоточности единичных управленческих и производственных процессов;
– обеспечение пропорциональности частичных процессов;
– анализ рационализации структур и процессов.
Следующий принцип – это принцип ритмичности.
Ритмичность производства, являющаяся основополагающим принципом его организации, имеет особое значение для наиболее полного использования оборудования, материально-энергетических ресурсов и рабочего времени. Принцип ритмичности предполагает равномерный выпуск продукции и ритмичный ход производства.
Равномерный выпуск продукции означает изготовление в равные промежутки времени одинакового или постепенно возрастающего количества продукции. Ритмичность производства выражается в повторении через равные промежутки времени частных производственных процессов на всех стадиях производства и осуществлении на каждом рабочем месте
в равные промежутки времени одинакового объема работ, содержание которых в зависимости от метода организации рабочих мест может быть одинаковым или различным.
Обеспечение ритмичности процессов позволяет равномерно загружать рабочие места во времени, лучше координировать их взаимодействие в пространстве и времени, снижать брак в работе, повышать качество продукции.
Равномерная (ритмичная) работа предприятия зависит от ряда условий, прежде всего от правильной организации оперативного планирования производства.
Уровень ритмичности может быть охарактеризован коэффициен-
том k ритм:
где ,
– фактический объем работ за анализируемый период (декаду, месяц, квартал) в пределах плана (сверх плана не учитывается) и плановый объем выполненной работы за соответствующий период.
Рассмотрим пример оценки ритмичности. Исходные данные приведены в табл. 3.4.
Таблица 3.4
Исходные данные к примеру оценки ритмичности
Показатели | Выпуск по декадам, млн руб. | Всего за месяц | ||
1 | 2 | 3 | ||
Плановый объем | 20 | 20 | 20 | 60 |
Фактический объем | 5 | 10 | 50 | 65 |
Коэффициент ритмичности в этом случае будет
k ритм = =
= 0,58.
Анализ данных табл. 3.4 показывает, что хотя за месяц план и был перевыполнен на 8 %, коллектив работал плохо, так как 84 % плана было произведено в последнюю декаду.
Обеспечение ритмичной работы является обязательным для всех подразделений производства: основных, обслуживающих и вспомогательных цехов, материально-технического снабжения. Неритмичная работа каждого звена приводит к нарушению нормального хода производства. Для исключения этого необходимо улучшать качество технологических и организационных проектов, искать конкурентоспособных, надежных поставщиков и повышать надежность технологического оборудования.
Особую значимость в организации машиностроительного производства имеет автоматизация процессов, которая приводит к увеличению объемов выпуска деталей и изделий, повышению качества работ, сокращению затрат живого труда, замене непривлекательного ручного труда более интеллектуальным трудом высококвалифицированных рабочих (наладчиков, операторов), исключению ручного труда на работах с вредными условиями, замене рабочих роботами.
Автоматизация процессов характеризуется принципомавтоматичности, определяющим максимальное выполнение операций производственного процесса автоматически, т. е. без непосредственного участия в нем рабочего либо под его наблюдением и контролем. Требование принципа автоматичностисостоит в том, чтобы в наибольшей мере освободить рабочего (оператора), других исполнителей от затрат ручного малопроизводительного труда при выполнении технологических операций и других работ.
Особенно важна автоматизация обслуживающих процессов. Автоматизированные транспортные средства и склады не только выполняют функции по передаче и хранению объектов производства, но и могут регламентировать ритм всего производства. Общий уровень автоматизации процессов производства определяется долей работ, выполняемых автоматически на основном, вспомогательном и обслуживающем производствах, в общем объеме работ предприятия:
Уавт =
где Тавт – трудоемкость работ, выполняемых автоматическим или автоматизированным способом; Тобщ – общая трудоемкость работ на предприятии (цехе) за определенный период времени.
Уровень автоматизации может быть рассчитан как суммарно по всему предприятию, так и по каждому подразделению отдельно.
Использование в современном производстве средств вычислительной техники и робототехники позволяет в значительной мере сократить затраты ручного труда и соединить производственный процесс с процессом управления им.
|
|
Автоматическое растормаживание колес: Тормозные устройства колес предназначены для уменьшения длины пробега и улучшения маневрирования ВС при...
Кормораздатчик мобильный электрифицированный: схема и процесс работы устройства...
Архитектура электронного правительства: Единая архитектура – это методологический подход при создании системы управления государства, который строится...
Папиллярные узоры пальцев рук - маркер спортивных способностей: дерматоглифические признаки формируются на 3-5 месяце беременности, не изменяются в течение жизни...
© cyberpedia.su 2017-2024 - Не является автором материалов. Исключительное право сохранено за автором текста.
Если вы не хотите, чтобы данный материал был у нас на сайте, перейдите по ссылке: Нарушение авторских прав. Мы поможем в написании вашей работы!