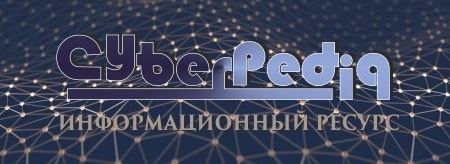
Таксономические единицы (категории) растений: Каждая система классификации состоит из определённых соподчиненных друг другу...
Папиллярные узоры пальцев рук - маркер спортивных способностей: дерматоглифические признаки формируются на 3-5 месяце беременности, не изменяются в течение жизни...
Топ:
Методика измерений сопротивления растеканию тока анодного заземления: Анодный заземлитель (анод) – проводник, погруженный в электролитическую среду (грунт, раствор электролита) и подключенный к положительному...
Интересное:
Принципы управления денежными потоками: одним из методов контроля за состоянием денежной наличности является...
Средства для ингаляционного наркоза: Наркоз наступает в результате вдыхания (ингаляции) средств, которое осуществляют или с помощью маски...
Инженерная защита территорий, зданий и сооружений от опасных геологических процессов: Изучение оползневых явлений, оценка устойчивости склонов и проектирование противооползневых сооружений — актуальнейшие задачи, стоящие перед отечественными...
Дисциплины:
![]() |
![]() |
5.00
из
|
Заказать работу |
|
|
Рис.12. Штифтовый барабан (разрез):
1, 3 – торцевые диски; 2 – штифты; 4 – вал; 5 – обойма; 6 – секция.
3.1.1. Определяется подача хлебной массы
Q = 0,01×B×V×(U+ Qc×b2), кг/с.
где Qc – урожайность соломы, Qc = Ub1; b2 = 0,8–0,9 – коэффициент учитывающий полноту сбора соломы с поля.
Максимальная подача хлебной массы, вызванная неравномерностью поступления в барабан в реальных условиях на поле
Q1 = 1,33Q, кг/с.
3.2.1. Определяются размеры барабана
Длина барабана
, м
где S – зазор между барабаном и декой, S = 0,004 м; j - коэффициент неравномерности заполнения зазора S хлебной массой, = 1,4; g - объёмный вес хлебной массы, = 40 кг/м3;
Число Z штифтов Z = Q1 / q.
Число К штифтов, идущих по 1 следу (число заходов винтовой линии)
Справка: К = 2...5; Z должно быть кратным К; при корректировке К изменять его нужно в сторону увеличения.
Уточняется длина барабана
, мм (м).
Длина планки барабана
Lп = L + 2D l,
где D l – расстояние от торца до крайнего отверстия под штифт, D l = 18-22 мм.
Выбирается число планок барабана: М (четное значение из ряда 6, 8, 10, 12).
Определяется диаметр барабана по концам штифтов (рис.11).
Для определения диаметра барабана задаются минимальным расстоянием t1 по дуге между двумя соседними планками: t1 = (100... 120), мм
Диаметр барабана по концам штифтов:
, мм (м)
Справка: у большинства комбайнов Д = (590...750), мм.
|
3.3.1. Определяются кинематические параметры:
- число оборотов барабана:
n = 60×Vб /p×D, мин–1.
- угловая скорость барабана:
w = 2Vб /D, с–1.
- мощность, затрачиваемая на холостой ход барабана:
Nx = A×w + B1×w3, Вт
где А– коэффициент потерь на трение в подшипниках; В1 – коэффициент потерь на
Рис.12. Развертка:
а - 4-заходного штифтового барабана с 12-тью планками; б – 4-рядного подбарабанья.
преодоление сопротивления воздуха. Для штифтового барабана представлены следующие значения: А= 2,6 Н×м, В1 = L× 0,73×10–3 Н×м×с2, где L в м.
3.4.1 – 3.7.1: Силовые характеристики, масса барабана, затраты мощности на единицу переработанной массы, параметры для построения графических зависимостей выполняются аналогично пунктам 3.4 – 3.7.
3.8. Размещение штифтов на планках барабана
Способ размещения штифтов на барабане заключается в использовании многозаходной винтовой линии. Зная число планок M, их шаг t1, диаметр по основанию штифтов d = Мt1/p, расстояние между следами а и число заходов К, строится развертка барабана (рис.12а). Для этого проводят М + 1 параллельных горизонтальных линий на расстоянии t1 одна от другой. Отложив на линии 11о шаг винтовой линии, равный t1 = Ma, вычерчивают ее развертку. Затем параллельно ей на расстоянии b = Ma / К одну от другой проводят наклонные линии, представляющие собой развертки других винтовых линий. Точки пересечения наклонных и горизонтальных линий определяют месторасположение штифтов барабана.
Число следов, изображенных на схеме пунктирными линиями, составляет
С = L/а + 1.
По одному следу за каждый оборот барабана проходит столько штифтов, сколько заходов имеет винтовая линия. С ростом числа заходов винтовой линии увеличивается число штифтов на барабане и возрастает его производительность.
Число планок обязательно должно быть кратным числу заходов винтовой линии, чтобы развертка барабана делилась на целое число частей и по каждому следу проходило одинаковое число штифтов. Это способствует более равномерной обработке материала при обмолоте.
|
В зубовых молотильных аппаратах штифты на подбарабанье устанавливают в 4...6 рядов. В рядах расстояние между штифтами равно удвоенному расстоянию между следами штифтов барабана (ад = 2а), а в первом ряду с целью облегчения вхождения обмолачиваемой массы в промежуток между барабаном и подбарабаньем принимают ад1 = 4а. Штифты размещают в шахматном порядке, добиваясь такого положения, чтобы штифты одного ряда находились в одних междуследьях барабана, а второго - в смежных. Расстояние между рядами штифтов на деке определяется углом охвата подбарабанья, а также зависит от диаметра барабана и числа планок с укрепленными на них штифтами. Длина подбарабанья составляет
Д = p(D + 2d)a/360о,
где a - угол охвата подбарабанья, a = 85-100о; d - радиальный зазор между штифтом барабана и планкой подбарабанья, d = 10-20 мм.
Соломотряс
В существующих зерноуборочных комбайнах наибольшее применение находят клавишные соломотрясы. Известны комбайны с платформенным, конвейерно-роторным соломотрясом и роторным соломоотделителем.
Клавишные соломотрясы бывают с тремя и более клавишами. Каждая клавиша представляет собой корпус 4 (рис. 13) с решетчатой рабочей поверхностью 3, выполненной в виде каскадов. Мелкий ворох, просыпавшийся сквозь отверстия решетки клавиш, по желобу корпуса попадает на очистку. Клавиши с боков несут выступающие над рабочей поверхностью гребенки 1, а некоторые каскады снабжены граблинами 2. Борта и граблины препятствуют скольжению соломы назад, улучшают ее растаскивание и способствуют более равномерному перемещению соломы к выходу из молотилки.
Рис. 13. Схема клавишного соломотряса:
а - двухвального; б - расположение колен четырехклавишного соломотряса; 1 - гребенка; 2 - граблина; 3 - решетчатая поверхность; 4 - корпус клавиши.
Таблица 8. Исходные данные для расчёта соломотряса
Значения параметров
Вариант (последняя цифра шифра)
4
|
5
Значения параметров
Вариант (предпоследняя цифра шифра)
Требуется определить:
1. Угловую скорость вращения w коленчатого вала
2. Параметры траектории полёта соломы
3. Среднюю скорость перемещения соломы по клавише
4. Ширину клавиши
5. Длину клавиши.
Исходные данные определяются по табл.8.
Вычертить:
1. Траектория полёта соломы
2. Эскиз клавиши соломотряса.
Порядок расчета
4.1. Определяется параметры для графического построения траектории полёта соломы.
Угловая скорость вращения w коленчатого вала
, с-1
где g – ускорение свободного падения, g = 9,81 м/с2.
Фазовый угол jо (jо = wt0) подбрасывания соломы
jо = arcsin(C cos(a) / k),
где С = 1,2-1,8 – коэффициент, учитывающий запаздывание подбрасывания вороха.
Для построения траектории полёта соломы откладывается угол wt0 (рис. 14) и находим точку А её отрыва. Начало координат располагаем в точке А. Оторвавшись от клавиш, солома, если пренебречь сопротивлением воздуха, будет совершать свободный полет. Начальные условия полёта:
Vx0 = w r sin wt0, м/с;
Vy0 = w r cos wt0, м/с.
Проекции ускорений на оси x и y:
ax = - g sin a, м/с2;
ay = - g cos a, м/с2.
Уравнение движения соломы:
X = Vx0× t – (gt2sin a) / 2, м
Y = Vy0× t – (gt2cos a) / 2, м.
Путь, пройденный соломой за один оборот вала, определяется графически путём построения траектории её полёта. Для построения точек 1,2,3 и т.д траектории задаются значения времени t с интервалами Dt = 0,03 - 0,04 с и производится расчёт по вышеприведённым уравнениям с занесением полученных значений в таблицу 9.
|
На графике (рис. 14) откладываются точки 1,2,3 и т.д. и по ним строится траектория. На окружности, как и на траектории полёта частицы, точками 1’, 2’,3’ и т.д. отмечаются положения точки А отрыва частицы, через интервалы времени ∆t, 2∆t и т.д. Для того чтобы установить положение этих точек, определяется угол
φ1 = ωΔt×180/p, о
и по нему откладывают на окружности точку 1/ и далее точки 2/, 3/ и т.д. Встреча частицы с клавишами произойдёт тогда, когда одноимённые точки траектории и окружности будут находиться на одной ординате. Из предполагаемой точки встречи проводят линию, параллельную оси OX. Если вторая одноимённая точка отклонена
от этой линии, то момент встречи одноимённых точек уточняют путём интерполяции. Расстояние S между одноимёнными точками (на рис.14 точки 6/ и 6) в масштабе m является дальностью перемещения соломы за одно подбрасывание.
При пятиклавишном соломотрясе две группы клавиш расположены на ко-ленчатом валу через 1800. Солома подбрасывается одной группой клавиш (двумя –
Таблица 9. Расчётные данные по траектории полёта соломы
№ | t, с | X, м | Y, м |
1 | 0,035 | ||
2 | 0,07 | ||
3 | 0,105 | ||
4 | 0,14 | ||
5 | 0,175 | ||
6 | 0,21 | ||
7 | 0,245 | ||
8 | 0,28 | ||
9 | 0,315 | ||
10 | 0,35 |
тремя), а падает на вторую. Поэтому после того, как клавиши пройдут ось коленчатого вала, начинается отсчёт времени для второй поднимающейся группы (рис. 14 б)
Согласно измерению величина S составит:
S = м×s, м.
где м – масштаб графика, м/мм.
4.2. Средняя скорость перемещения соломы по соломотрясу
Vср = S ω/ 2π, м/с.
4.3. Подача хлебной массы в молотильный аппарат
Q = 0,01×B×V×(U+ Qc×b2), кг/с.
где Qc – урожайность соломы, Qc = Ub1; b1 - отношение веса соломы к весу зерна (см. табл. 6); b2 = 0,8–0,9 – коэффициент учитывающий полноту сбора соломы с поля. Максимальная подача хлебной массы, вызванная неравномерностью поступления в молотильный аппарат в реальных условиях на поле
q = 1,33Q, кг/с.
4.4. Размерные характеристики
Ширина соломотряса
B = (1,1…1,15)Lб, м.
Ширина клавиши
b = (B – a(z + 1))/z, м
где а – боковой зазор между клавишами, а = 0,003–0,005 м, z – количество клавиш.
Толщина слоя соломы на соломотрясе
|
h = q(1 – δ)/(B Vср γ), м.
Коэффициент сепарации:
μ = μ0 (h0 / h)m,
где m = 0,8-1,2 большие значения относятся к тяжёлым условиям, меньшие клёгким. Согласно исследованиям [3], коэффициент сепарации для клавишных соломотрясов при толщине слоя соломы h0 = 20 см равен μ0 = 0,018 см-1.
Длина соломотряса
, см
где e - коэффициент сепарации зерна декой; p – процент допустимых потерь соломотрясом грубого вороха, p = 0,25%:
а б
Рис. 14. Траектория полёта соломы на соломотрясе:
а – для 4-х клавишного; б – для 5-ти клавишного.
Рис. 15. Клавиша соломотряса:
L – длина клавиши; Lг – габаритный размер, Lг=1,025L; l 1, l 2, l 3 – длина каскадов, l 1=0,27L, l 2=0,17L, l 3=0,19L; t1, t2, t3 – величина перехода; aо – угол наклона линии начала каскадов, aо=2о; a1, a2, a3, a4 – углы наклона решёт каскадов, a1=a2=a+6о, a3=a, a4=a-2о; a5 – угол наклона днища, a5=a+2о; a - угол наклона клавиши; b – ширина клавиши; c, d – размеры проходного отверстия решета c = 60-70 мм, d = 25-30 мм.
Вентилятор
Вентиляторы бывают радиальные (центробежные), диаметральные и осевые, низкого (Н≤1кПа), среднего (1кПа<Н≤3кПа) и высокого (3кПа<Н) давления. (Здесь Н–полный напор воздуха).
Вентилятор состоит из рабочего колеса, кожуха и приводного механизма. В рабочем колесе имеются лопасти, которые могут быть радиальными, отогнутыми назад или вперед, а также прямолинейными и криволинейными.
Центробежные вентиляторывыпускаются как с односторонним, так и с двусторонним подводом воздуха.
Требуется определить:
1.Параметры воздушного потока
2. Размерные характеристики центробежного вентилятора
3. Мощность потребляемую вентилятором
Исходные данные определяются по табл.10.
Вычертить:
Эскиз кожуха двустороннего центробежного вентилятора.
Таблица 10. Исходные данные для расчёта вентилятора
Значения параметров
Вариант (последняя цифра шифра)
Значения параметров
Вариант (предпоследняя цифра шифра)
Порядок расчета
5.1. Необходимый расход воздуха для сепарации
Q = m / rm, м3/с
где m – масса компонентов (кг/с), которые должны быть удалены за 1 с; r – плотность воздуха, r = 1,21 кг/м3; μ– показатель допустимой концентрации удалённых компонентов в воздушном потоке, μ = 0,2-0,3.
Масса компонентов
m = q×e, кг/с,
где q - пропускная способность молотилки; ε – коэффициент, показывающий долю половы в хлебной массе,ε = 0,2-0,25;
q = 0,0133×B×V×U(1+b1×b2), кг/с
где B,V,U – см. табл. 1; b1 - отношение веса соломы к весу зерна (см. табл. 6); b2 = 0,8–0,9 – коэффициент учитывающий полноту сбора соломы с поля.
5.2. Скорость воздушного потока:
Vв = a×Vкр, м/с
где a – коэффициент сопротивления решет; Vкр – критическая скорость лёгкой фракции м/с.
5.3. Напор воздушного потока
Полный напор:
Н = hc + hд, кг/м2
где hc – статический напор, hд – динамический напор.
Динамический напор
hд = r×Vв2/2×g, кг/м2.
Статический напор
hc =(2-3)hд, кг/м2.
Теоретический напор
Нт = Н/h, кг/м2,
где h - к. п. д. Вентилятора.
5.4. Коэффициент режима работы
5.5. Размерные характеристики
Диаметр входного отверстия вентилятора рассчитывается из условия получения наименьших потерь энергии воздуха при входе на колесо:
где ∆ – коэффициент использования входного отверстия; λ – отношение диаметров входного отверстия и колеса вентилятора, λ = Do/D1 = 0,9; n - частота вращения колеса; μо - коэффициент поджати потока,μо = 0,8-0,9; φ – коэффициент предварительного закручивания потока; Q - расход воздуха.
Начальный (r1), конечный (r2) радиус лопаток принимается из соотношений:
r1 = 0,5Do, м;
r2 = (1,5-2,0)×r1, м.
Площадь выходного отверстия:
Ширина выходного патрубка
Вв = (0,9-1,0)×Lб, м.
Высота выходного отверстия
Ав = F/Вв, м.
5.6. Кожух вентилятора
Спираль кожуха строят по конструкторскому квадрату. При этом вначале определяют размер Ак (рис. 15) из выражения: Ак = 0,8×Ав, м.
Величина конструкторского квадрата определяется: а = 0,25Ак, м.
Строят квадрат со сторонами а, вершины которого служат центрами окружностей при построении спирали. Радиусы окружностей для построения кожуха вентилятора определяются по формулам:
R1 = r2 + a/2, м;
R2 = r2 + 3a/2, м;
R3 = r2 + 5a/2, м;
R4 = r2 + 7a/2, м.
Рис. 15. Кожух вентилятора
5.7. Мощность потребляемая вентилятором
Nв = 9,81×Нт×Q Вт
Решетная очистка комбайна
Исходные данные выбираются в соответствии с вариантом по таблице 11.
Порядок выполнения
В зависимости от соотношения сил, материальные частицы будут либо лежать неподвижно на поверхности решета (при малых значениях w2r), либо скользить по его поверхности только вниз, или скользить вниз и вверх.
6.1. Определяется ускорение, при котором начинается:
- скольжение материала вниз
j1 = - g tg (j1 - a), м/с2;
где j1 - угол трения зерна по решету при его обдувании встречным воздушным потоком, j1 = j + 150; a - угол наклона решета к горизонту.
- скольжение материала вверх
j2 = g tg (j2 + a), м/с2;
где j2 - угол трения зерна по решету при его обдувании попутным воздушным потоком, j2 = j - 150;
Таблица 11. Значение исходных параметров решетной очистки комбайна
Значения параметров
Вариант (последняя цифра шифра)
Значения параметров
Вариант (предпоследняя цифра шифра)
- отрыв материала от плоскости
jо = g сtg a, м/с2.
6.2. Рабочая частота вращения приводного вала решета w устанавливается, исходя из условий движения по решету хлебного вороха без отрыва от плоскости со скольжением вверх и вниз по формуле:
w = (j / r)1/2, с-1,
где j выбирается в пределах: jо > j > j2.
6.3. Определяются максимальная скорость и ускорение решета при рабочем режиме v max=w r, м/с,
j max =w2 r, м/с2.
6.4. Определяется средняя скорость относительного движения вороха по решету v ср v ср = (Sн - Sв) w/ 2p, м/с,
где Sн - перемещение вороха вниз по решету за одно колебание решета, м; Sв - перемещение вороха вверх по решету за одно колебание решета, м. Аналитическое определение величины перемещения Sн и Sв сопряжено с определенными трудностями. Поэтому значения Sн и Sв рекомендуется определять графически. Для этого
необходимо построить диаграмму изменения скорости и ускорения решета в зависимости от угла поворота кривошипа (рис.16) согласно формул:
v =w r sin w t, м/с,
j =w2 r cos w t, м/с2.
Время полного оборота кривошипа составит t = 2p/w, с.
6.5. Построение диаграммы
На листе миллиметровой бумаги произвольно вычерчивается прямоугольник АBСD с соотношением сторон АB: АD = 2, сторона АD делится пополам точкой Е и проводится горизонталь EF, отрезки АЕ, ЕD делятся, в свою очередь, пополам и проводятся оси абсцисс О-w t, О1-w t; отрезок АВ делится на 7 равных частей, точки деления соответствуют углам поворота кривошипа 0; 0,5p; p; 1,5p; 2p; 2,5p; 3p; 3,5p;
через точки деления проводятся вертикали по всей высоте диаграммы; на верхнем прямоугольнике EDCF вычерчивается график абсолютного ускорения j =w2 r cos w t, на нижнем (AEFB) - график абсолютной скорости решета v =w r sin w t (эти графики отличаются между собой тем, что кривые смещены на 0,5p: sin 0 = 0; cos 0 = 1; sin 0,5p = 1; cos 0,5p = 0; максимальное значение v max, j max соответствует отрезкам
ординат ОЕ, О1D. Определяются масштабы:
- масштаб времени mt находится по отрезку О1О2, соответствующему углу поворота кривошипа
j = wt = 0,5p; t = 0,5p/w,: mt = 0,5p/(w О1О2), с/мм;
![]() |
Рис. 16. Диаграмма сдвига зерна вниз-вверх по решету
m v = v max / ОЕ, м/с-мм;
- масштаб ускорения mj определяется по отрезку О1D, соответствующему максимальному ускорению j max =w2 r:
mj = j max / О1D, м/с2-мм.
На диаграмме (рис. 16) определяется момент начала сдвига зернового вороха вниз и вверх, и соответствующие скорости решета v 1 и v 2. Для этого на графике j = f(w t) в масштабе вниз откладывается ускорение j1, а вверх - j2 (отрезки О1О3 = j1/(mj); О1О5 = j2/(mj)) и проводятся линии, параллельные оси абсцисс. Точки пересечения (А, А/ и т.д.) линии - j1 с косинусоидой определяют момент времени tн начала сдвига вороха вниз. Через точки А, А/ опускаются вниз вертикали и часть их, заключенная между осью абсцисс графика v = f(w t) и синусоидой, определит величину скорости v 1 = А0О6·m v решета, при которой произойдет сдвиг вороха вниз. Точка С/1 пересечения линии - j2 с косинусоидой определяет момент времени tв начала сдвига вороха вверх. Через точку С/1 опускаются вертикаль и часть ее, заключенная между осью абсцисс графика v = f(w t) и синусоидой, определит величину скорости v 2 = С0О7·m v решета, при которой произойдет сдвиг вороха вверх. Далее определяется время t1 и t2, через которое (от tн и tв) скорость абсолютного движения вороха станет равной нулю: t1 = v 1 / j1, с; t2 = v 2 / j2, с.
От точки О6 по оси О-w t откладывается в масштабе отрезок О6М = t1 / mt, мм; а от точки О7 - отрезок О7Н = t2 / mt, мм. Через точки А0 и М, а также С0 и Н проводятся линии, которые должны быть касательными к синусоиде в точках А0 и С0. Линия А0М является графиком абсолютной скорости движения вороха вниз по решету, а линия С0Н - графиком абсолютной скорости движения вороха вверх по решету; скорости относительного движения вороха вниз - вверх по решету изображаются отрезками вертикалей (ординат), заключенных между синусоидой v =w r sin w t и касательными А0М и С0Н соответственно.
Если точка О7 лежит на оси абсцисс правее точки М или совмещены, то это свидетельствует о том, что между концом сдвига вороха вниз и началом сдвига вверх по решету имеется некоторый промежуток времени или сдвиг вниз без разрыва во времени переходит в сдвиг вверх и в этом случае диаграмму можно использовать для дальнейших расчетов. Если точка О7 находится левее точки М (как изображено на рис.2), то в этом случае необходимо диаграмму привести к виду установившегося движения. Приведение диаграммы осуществляется следующим образом: через точку М проводится линия ММ/, параллельная С0Н и на пересечении ее с синусоидой обозначается точка М//, из которой проводится линия М//М///, параллельная А0М.
6.6. Определяется величина перемещения вороха вниз и вверх по решету из диаграммы
Sн = d1W1·m v ·mt, м; Sв = d2W2·m v ·mt, м,
где d1 = cos(j - a) / cosj; d2 = cos(j + a) / cosj;
W1 - площадь между синусоидой и линией М//М///, W2 - площадь между синусоидой и линией М/М//. Площади W1 и W2 (на миллиметровой бумаге) замеряются следующим образом: в контурах, ограниченных синусоидой и касательными М//М///, М/М//, подсчитывается сначала количество целых квадратных сантиметров (имея ввиду, что 1 см2 = 100 мм2), затем кол-во целых (не пересеченных линией контура) квадратных милли-метров, наконец кол-во пересеченных квадратных миллиметров вдоль контура, последнее делится пополам; производится суммирование и соответствующие площади W1, W2 выражаются в мм2. Найденные численные значения Sн и Sв подставляются в формулу и определяется средняя скорость относительного движения вороха по решету v ср.
6.7. Находится толщина слоя вороха на решете
h = Qp / Вр v ср gв, м,
где Qp = Q1bз / bв - секундная подача вороха на решето, кг/с; Q1 - секундная подача хлебной массы в молотильный барабан, кг/с (см. п.3.1.1. и табл.1); bз - коэффициент, характеризующий содержание зерна в хлебной массе, bз = 0,33-0,6; bв - коэффициент, характеризующий содержание зерна в ворохе, поступающем на решето, bв = 0,6-0,8; Вр = 0,9Вс - ширина решета, м; Вс - ширина соломотряса, м; gв - объемный вес вороха, движущегося по поверхности решета, gв = 50-60 кг/м3.
6.8. Определяется необходимое число встряхиваний решета для достижения зерном, находящимся на поверхности слоя мелкого вороха в начале решета, рабочей поверхности решета (физическое условие возможности сепарации)
nвс = noh / ho,
где no = 60-80 для пробивных решет, no = 20-30 для жалюзийных регулируемых решет при ho = (0,1-0,12), м.
6.9. Устанавливается необходимая длина решета
Lp ³ nвс(Sн - Sв), м.
6.10. Фактическая удельная нагрузка на решето
qф = Qp / Вр Lp, кг/с·м2.
Фактическая нагрузка qф сравнивается с допустимой удельной нагрузкой, зависящей от типа решета, т.е.: qф £ [ q ],
где [ q ] - для жалюзийных регулируемых решет составляет: 0,9-1,1 кг/с·м2; для плетеных с отверстиями 20´20 мм: 0,7-0,85 кг/с·м2; для пробивных с отверстиями 16-20 мм: 0,3-0,4 кг/с·м2.
|
|
Индивидуальные очистные сооружения: К классу индивидуальных очистных сооружений относят сооружения, пропускная способность которых...
Адаптации растений и животных к жизни в горах: Большое значение для жизни организмов в горах имеют степень расчленения, крутизна и экспозиционные различия склонов...
Поперечные профили набережных и береговой полосы: На городских территориях берегоукрепление проектируют с учетом технических и экономических требований, но особое значение придают эстетическим...
Таксономические единицы (категории) растений: Каждая система классификации состоит из определённых соподчиненных друг другу...
© cyberpedia.su 2017-2024 - Не является автором материалов. Исключительное право сохранено за автором текста.
Если вы не хотите, чтобы данный материал был у нас на сайте, перейдите по ссылке: Нарушение авторских прав. Мы поможем в написании вашей работы!