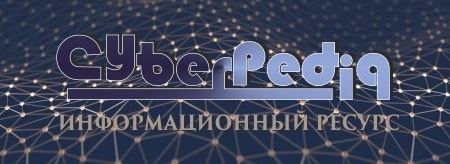
Двойное оплодотворение у цветковых растений: Оплодотворение - это процесс слияния мужской и женской половых клеток с образованием зиготы...
Индивидуальные и групповые автопоилки: для животных. Схемы и конструкции...
Топ:
Оценка эффективности инструментов коммуникационной политики: Внешние коммуникации - обмен информацией между организацией и её внешней средой...
Характеристика АТП и сварочно-жестяницкого участка: Транспорт в настоящее время является одной из важнейших отраслей народного...
Выпускная квалификационная работа: Основная часть ВКР, как правило, состоит из двух-трех глав, каждая из которых, в свою очередь...
Интересное:
Распространение рака на другие отдаленные от желудка органы: Характерных симптомов рака желудка не существует. Выраженные симптомы появляются, когда опухоль...
Подходы к решению темы фильма: Существует три основных типа исторического фильма, имеющих между собой много общего...
Лечение прогрессирующих форм рака: Одним из наиболее важных достижений экспериментальной химиотерапии опухолей, начатой в 60-х и реализованной в 70-х годах, является...
Дисциплины:
![]() |
![]() |
5.00
из
|
Заказать работу |
|
|
Санкт-Петербургский Государственный Политехнический Университет
Энергомашиностроительный факультет
Кафедра компрессорной вакуумной и холодильной техники
КУРСОВОЙ ПРОЕКТ
Дисциплина: турбомашины
«Осевой компрессор стационарного типа»
Выполнил:
студент группы 5036/1 Коленько Г.С.
Проверил:
преподаватель: проф. Зуев А.В.
.
Санкт-Петербург
2013
Содержание.
Техническое задание.
1. Расчетная часть.
1.1 Вариантный расчет лопаточного аппарата.
1.2 Газодинамический расчет оптимального варианта проточной части компрессора.
1.2.1. Первый поступенчатый расчет.
1.2.2 Выполнение эскиза лопаточного аппарата.
1.2.3 Второй поступенчатый расчет.
1.2.4 Определение статических давлений и статических температур в ЛА.
1.2.5 Проектирование всасывающей камеры.
1.2.6 Проектирование выходного диффузора.
1.2.7 Проектирование кольцевых уплотнений.
1.3 Прочностной расчет компрессора.
1.3.1. Расчет осевого усилия, действующего на роторе компрессора.
1.3.2 Расчет подшипников на удельное давление.
1.3.3 Оценка прочности барабана ротора.
1.3.4 Расчет критического числа оборотов ротора.
Описание конструкции.
Литература.
Техническое задание.
Спроектировать по методу ЦКТИ осевой компрессор стационарного типа, сжимающий газовую среду – воздух.
Исходные данные:
показатель адиабатического сжатия k=1,4;
универсальная газовая постоянная R = 287,1 Дж/(кг К);
начальное давление = 98,1 кПа;
температуры = 298 К;
|
отношение давлений машины = 3,7;
массовый расход = 112 кг/сек;
привод: паровая турбина с числом оборотов n = 3300 об/мин.
Расчетная часть.
Проектирование осевых компрессоров выполняется одним из двух возможных методов: метод ЦИАМ и метод ЦКТИ. Первый метод, разработанный московским предприятием, основывается на расчете параметров и проектировании проточной части по обобщенным данным продувок плоских решеток (метод широко используется в авиационной технике). Второй метод (ЦКТИ), ленинградского предприятия, основывается на экспериментальных характеристиках одиночных ступеней, и предназначен для расчета проточных частей воздушных компрессоров стационарного типа производительностью до 300 кг/сек при степени повышения давления до 4,5 и при значении окружной скорости не выше 280 м/с.
Согласно техническому заданию работа по проектированию энергетической машины будет осуществляться по методу ЦКТИ.
Вариантный расчет лопаточного аппарата.
Вследствие наличия входных и выходных патрубков в принципиальной схеме компрессора, значение давления перед и за рабочим колесом, соответственно первой и последней ступеней, будут отличаться на величину потери давлений. Потери давления во всасывающем и нагнетательном патрубках определяются по известным коэффициентам потерь в них.
(1)
где zв – коэффициент потерь во всасывающем патрубке;
– плотность потока перед лопаточным аппаратом, кг/м3.
(2)
где zк – коэффициент потерь в нагнетательном патрубке; – плотность потока за лопаточным аппаратом последней ступени, кг/м3.
При отсутствии данных о коэффициентах потерь в проектируемых патрубках для предварительных расчетов с учетом наличия входного направляющего аппарата и спрямляющего аппарата принимают zв =0,1…0,2 и zк = 0,45…0,6.
|
Значения скоростей в патрубках выбираются из предела (80…130) м/с, при этом значение скорости для выходного патрубка выбирается несколько меньшей, чем для входного с1.
Принимаем значения коэффициентов потерь: zв = 0,15 и zК = 0,5; значения скоростей: =110 м/с и
= 100 м/с.
Плотность воздуха на входе в лопаточный аппарат:
(3)
Оценим величину потерь во всасывающем патрубке (+ВНА) по формуле (1):
Тогда полное давление перед первой ступенью будет равно:
(4)
Полная температура за лопаточным аппаратом, равная полной температуре за компрессором, определяется по формуле:
(5)
где – коэффициент полезного действия компрессора,
= 0,9
Значение давления за компрессором определяется как:
(6)
Плотность воздуха за лопаточным аппаратом:
(7)
Потери давления в нагнетательном патрубке по формуле (2):
Полное давление за последней ступенью:
(8)
Отношение давлений в лопаточном аппарате:
(9)
Адиабатный напор в лопаточном аппарате:
(10)
Для определения зададимся оптимальными значениями коэффициента расхода φопт*, находящегося в диапазоне величин от 0,42 до 0,52, и минимального втулочного отношения проектируемой машины
– от 0,5 до 0,6.
Задавшись желательными значениями (φопт* = 0,46 и = 0,55) первой ступени, определим наружный диаметр лопаточного аппарата:
(11)
Окружная скорость на наружном диаметре:
(12)
Полученное значение окружной скорости позволяет проводить вариантные расчеты с модельными ступенями со степенью реактивности 0,5. Выполним расчеты вариантов с модельными ступенями К-50-1, К-50-5 (при выборе нужной ступени предпочтительнее та, которая при соответствующих значениях окружной скорости и коэффициента расхода имела наиболее высокий коэффициент напора, при удовлетворительном уровне КПД).
Дальнейшее выполнение курсовой работы сводится к предварительным расчетам выбранных моделей для двух типов проточных частей (первый тип выполнен при постоянном наружном диаметре, второй – при постоянном втулочном диаметре) и выбору из них оптимального.
|
Рассмотрим пример расчета варианта с модельной ступенью К-50-1. В связи с тем, что значения φ* и были заданы произвольно из некоторого предела рекомендованных чисел, необходимо пересчитать значения наружного диаметра лопаточного аппарата и окружной скорости ротора, уточнив значения φ* и
. Данная операция проводится с использованием характеристики выбранной модели (см. рис. 1), и сводится к определению точки на кривой, соответствующей найденной окружной скорости и максимально возможному КПД компрессора (ηст).
Рис. 1 Аэродинамические характеристики модельной ступени К-50-1 при исходных углах установки лопаток.
При окружной скорости =230 м/с находим при ηmax=0,95 φопт=0,48. Минимальное втулочное отношение для данной ступени
= 0,6. Уточняем наружный диаметр и значение окружной скорости:
При новом значении оптимальный коэффициент расхода согласно графику (рис. 1) не изменился.
Выбираем I тип проточной части (Dн=const)
Среднее значение адиабатного напора ступени определяется как:
(13)
где – поправочный коэффициент,
= 0,97…0,98 для первого типа проточной части,
=0,94…0,95 для второго типа проточной части.
Расчетный напор в лопаточном аппарате:
(14)
где α – коэффициент затрачиваемой работы, определяется по графику (рис.2). Для стационарного компрессора сжимающего воздух (k = 1,4) с отношением давлений 4,15 значение коэффициента α=1,032.
Число ступеней компрессора:
(15)
Рис. 2. Зависимость коэффициента затраты работы от степени повышения давления в компрессоре при показателе адиабаты k 1,3…1,66.
Адиабатический КПД лопаточного аппарата:
(16)
где а – коэффициент, учитывающий подвод тепла, выделяемого из-за трения.
(17)
|
Диаметр втулки первой ступени:
(18)
Длина лопатки первой ступени:
(19)
Для проточной части типа I наружный диаметр последней ступени:
Принимаем политропный КПД ЛА и находим плотность воздуха а последней ступенью:
(20)
(21)
Диаметр втулки последней ступени:
(22)
Длина лопатки последней ступени:
(23)
Корневая подрезка последней ступени:
(24)
Таким образом, величина подрезки превышает допускаемую =0,2. Поэтому целесообразно провести расчет других вариантов и добиться уменьшения величины подрезки. Результаты проведенного выше расчета варианта ЛА представлены в таблице 1 под пунктом №1.
Выбираем II тип проточной части (Dвт=const)
Среднее значение адиабатного напора ступени определяем по формуле (13):
Расчетный напор в лопаточном аппарате по формуле (14):
Число ступеней компрессора определяем по формуле (15):
Коэффициент а, учитывающий подвод тепла, выделяемого из-за трения, определяем по формуле (17):
Адиабатический КПД лопаточного аппарата по формуле (16):
Диаметр втулки первой ступени как и длина лопатки первой ступени остаются такими же ,
Плотность воздуха за последней ступенью по формуле (20):
Наружный диаметр последней ступени:
(25)
Длина лопатки на выходе из последней ступени:
(26)
Величина периферийной подрезки:
(27)
При невыполнении условия по подрезке для моделей применяют один из трех методов ее понижения.
Первый метод основан на применении второго расчетного диаметра, значение которого принимается немного меньше, чем первый расчетный диаметр и немного больше, чем среднеарифметическое значение наружных диаметров первой и последней ступеней; при этом повторяются ранее рассмотренные вычисления, где используются среднеарифметические значения коэффициента напора, КПД модели и окружной скорости. Однако данный метод можно применять при переменном значении наружного диаметра, то есть в случае второго типа поточной части.
Второй метод заключается в увеличении втулочного диаметра, начиная с первой ступени, и приводящее к увеличению значения окружной скорости, и, следовательно, применяется в случае, когда имеется запас по окружной скорости.
Третий метод - снижение значения коэффициента расхода на последней ступени по сравнению с оптимальным, соответствующим максимальному КПД модели, при сохранении значения рассчитанной окружной скорости. При этом в ранее описанном расчете используют среднеарифметические значения коэффициента напора и КПД модели, соответствующие значениям оптимального и принятого (пониженного) коэффициента расхода.
|
По результатам вариантных расчетов, представленных в таблице 1, в качестве оптимального выбран вариант ЛА под номером 34, в котором при среднем числе ступеней удовлетворительное значение КПД ЛА и величина подрезки
. Втулочное отношение
.
1.2 Газодинамический расчет оптимального варианта проточной части компрессора.
Газодинамический расчет выбранного вариант лопаточного аппарата включает несколько этапов. Сначала проводится поступенчатый расчет с приближенным учетом отклонения от геометрического и динамического подобия проектируемых и исходных ступеней. Затем выполняется второй поступенчатый расчет после уточнения диаметральных размеров и газодинамических параметров ступеней с учетом отклонения от геометрического и динамического подобия для каждой ступени по ее фактическим параметрам. Далее определяются статические давления и температуры на среднем радиусе перед и за рабочим колесами и характеристики компрессора на расчетном режиме.
Описание конструкции.
Рассчитанный в данном курсовом проекте многоступенчатый осевой стационарный компрессор относится к компрессорам динамического действия, в которых сжатие газа происходит путем сближения молекул динамическим способом вследствие силового взаимодействия вращающейся решетки лопаток с потоком газа.
Проточная часть рассчитанного многоступенчатого осевого компрессора состоит из входного патрубка, конфузора, входного направляющего аппарата, восьми ступеней, спрямляющего аппарата, диффузора и выходного патрубка. Рабочие аппараты ступеней вместе с валом барабанного типа, на котором они расположены, образуют ротор. Направляющие аппараты вместе с корпусом, в котором они закреплены, составляют статор. Ротор компрессора опирается на подшипники, которые воспринимают как радиальные нагрузки от веса ротора и небаланса, так и осевое усилие, возникающее при работе компрессора. Для предотвращения или уменьшения подсоса воздуха из атмосферы в проточную часть и протечек из проточной части в атмосферу служат уплотнения. Входной патрубок служит для равномерного подвода газа из окружающей среды или подводящего трубопровода к кольцевому конфузору. Последний предназначен для ускорения потока и создания равномерного поля скоростей и давлений перед входным направляющим аппаратом. Входной направляющий аппарат создает заданное поле скоростей (по величине и направлению) перед первой ступенью. В ступенях газ сжимается за счет подводимой механической энергии. Спрямляющий аппарат служит для придания газу на входе в диффузор осевого направления. В диффузоре газ продолжает сжиматься за счет понижения его кинетической энергии. Выходной патрубок предназначен для равномерного отвода газа от диффузора и подачи его к нагнетательному трубопроводу.
Сжатие газа в рабочих аппаратах (колесах) осуществляется в результате силового воздействия потока газа с вращающимся лопаточным аппаратом. При этом часть механической энергии идет на повышения давления газа, а часть - на увеличение его кинетической энергии. Направляющий аппарат (на) или промежуточный направляющий аппарат (пна) ступени служит для придания потоку необходимой величины и направления скорости на входе в последующую ступень, а также для сжатия газа за счет понижения его кинетической энергии.
Из соображений аэродинамического качества и технологичности конструкции проектируемого компрессора выбран второй тип проточной части (с постоянным внутренним диаметром). В газодинамическом отношении этот тип проточной части обеспечивает преимущество по сравнению с другими типами, а именно - наибольшую длину лопатки последней ступени. В технологическом отношении при постоянном внутреннем диаметре упрощается изготовление ротора. При выгодно иметь постоянный диаметр ротора, который трудно выполнить коническим, а переменный диаметр цилиндра при таких размерах не вызывает никаких затруднений.
Как уже было сказано выше, в спроектированном компрессоре используется ротор барабанного типа, а именно цельнокованый барабанный ротор. Такой ротор является наиболее простым в конструктивном и технологическом отношении и требует сравнительно небольшой механической обработки. Основным недостатком ротора барабанного типа является чрезмерно большой вес, что может создать трудности с получением необходимого критического числа оборотов, так как в осевых компрессорах применение гибких роторов не является желательным из-за малых величин зазоров между лопаточным венцом и корпусом. В стационарных установках применение таких роторов является предпочтительным. Цельнокованые роторы имеют высокую прочность и допуск
ают большие окружные скорости: 250-300м/сек на внешней поверхности барабана. Для облегчения веса и соответственно повышения критического числа оборотов ротор делается с большой выборкой металла изнутри и запрессованной по горячей посадке со стороны всасывания цапфой. В целях страховки цапфа, помимо горячей посадки, стопорится штифтами. Помимо облегчения веса, такая конструкция позволяет более тщательно проконтролировать качество поковки. В конструкции также есть буртик на цапфе, входящий в зацепление с торцом ротора после остывания барабана, что страхует детали от осевого смещения.
Для динамической балансировки ротора в специальных проточках установлены балансировочные грузы. При динамической балансировке необходимо с помощью грузов создать момент сил, противоположный моменту от неуравновешенных сил. Уравновешивание роторов производится на специальных станках для динамической балансировки.
Поверхность ротора образует гладкую проточную часть. Наименьшие перетечки через концы лопаток достигаются за счет малых радиальных зазоров с ротором. Для избежания наличия замкнутых внутренних пространств полости барабанов соединяются с наружной поверхностью радиальными отверстиями, через которые выливается вода, сконденсировавшаяся из паров влаги во внутренней полости.
Лопатки компрессора имеют сложную конфигурацию, для которой характерно изменение по радиусу толщины профиля и угла его установки (закрученная лопатка). Удовлетворение условиям прочности при большой окружной скорости накладывает на геометрию лопатки следующие ограничения:
Кроме того лопатки компрессора выполнены с высоко точностью, поверхности лопаток гидравлически гладкие, т.е. потери практически не зависят от шероховатости. Лопатки сплошные, т.е. обладают большей жесткостью и изгибной прочностью, а также меньшей уязвимостью в процессе эксплуатации по сравнению с полыми лопатками. Лопатки компрессора изготавливаются отдельными деталями, а затем жестко закрепляются на барабане в специальных фасонных пазах вала, куда они заводятся хвостовиками елочного типа. Лопатки вставляются через специальную прорезь, которая после установки всех лопаток закрывается специальным замком.
Cтатор турбокомпрессора составляют корпус и неподвижные узлы и детали компрессора. К ним относятся неподвижные элементы ступени и компрессора, образующие проточную часть машины, а также другие неподвижные части компрессора, не имеющие прямого отношения к рабочему процессу в машине, как, например, подшипники, уплотнения, фундаментные рамы и прочие. Корпус компрессора изолирует проточную часть от внешней атмосферы и является серединой, расположенной между всасывающей и нагнетательной камерами, которые выполнены отдельно от него. В средней части располагаются ступени. Входное устройство машины - совокупность всасывающей камеры (входной патрубок совместно с конфузором) и входного направляющего аппарата. Выходное устройство – совокупность спрямляющего аппарата и нагнетательной камеры (диффузор с выходным патрубком). Корпус компрессора для удобства изготовления литьем, сборки и разборки машины и проверки проточной части имеет горизонтальный разъем. Входной и выходной патрубки направлены вниз: удобно для эксплуатации, так как это позволяет относительно просто поднимать верхнюю часть статора для осмотра ротора и неподвижных элементов, не разбирая присоединенных к корпусу труб. Корпус опорного подшипника, расположенного со стороны всасывания, выполнен заодно с нижней частью всасывающей камеры. Корпус же опорно-упорного подшипника, расположенного со стороны нагнетания, выполнен отдельно от корпуса машины и установлен на фундаментной раме. Поэтому нижняя половина корпуса машины имеет две опорные лапы со стороны всасывания, которыми она опирается на стойки фундаментной рамы, а со стороны нагнетания машина опирается на раму корпусом подшипника. Корпус стационарного осевого компрессора выполнен литьем из чугуна. Корпус должен быть прочным, чтобы выдержать рабочее давление находящейся в нем среды; стенки корпуса и разъемы должны быть плотными и не пропускать газ, находящийся в нем, наружу; корпус должен быть жестким и не иметь каких-либо деформаций во время работы машины. Верхняя и нижняя половины корпуса компрессора между собой соединяются с помощью шпилек. Для точного соединения частей обычно служат несколько штифтов, которые строго центрируют отдельные элементы корпуса. Для обеспечения герметичности фланцы горизонтального разъема подвергаются тщательной обработке и при сборке уплотняются специальной мастикой. Для разборки корпуса предусмотрены несколько отжимных болтов. Помимо всех перечисленных выше элементов корпуса предусмотрены также специальные шпонки (горизонтальные и вертикальные), служащие для центровки машины в процессе нагрева корпуса и температурных деформаций. В компрессоре отсутствует промежуточное охлаждение газа внутри корпуса, поэтому у корпусов отсутствуют промежуточные устройства для подвода и отвода газа. Форма поперечного сечения патрубков выбирается конструктивно, а величина сечений определяется расчетом. Части корпусов соединяются между собой с помощью болтового соединения. Поскольку корпус выполнен литьем, то для крепления лопаток направляющего аппарата лучше использовать специальные обоймы, которые устанавливаются в проточки корпуса. Для подъема и транспортировки корпуса предусмотрены специальные приливы. Для обеспечения жесткости компрессора предусмотрены наружные ребра на корпусе.
Ротор спроектированного стационарного осевого компрессора изготавливается из качественной углеродистой стали – сталь 40 ГОСТ 1050-60. Заготовкой служит поковка, выполненная методом свободной ковки. Лопатки компрессора изготавливаются из нержавеющей слаболегированной стали 20Х13 ГОСТ 5632-61.
Заготовкой для корпуса компрессора служит отливка из серого чугуна марки СЧ 15-32 ГОСТ 1412-54. Направляющие лопатки изготавливаются из нержавеющей стали 20Х13 ГОСТ 5632-61.
Установка ротора компрессора относительно неподвижных элементов проточной части (статора) производится с помощью подшипников скольжения, воспринимающих осевые и радиальные усилия, обусловленные силой веса ротора, динамическими нагрузками, возникающими при вращении ротора, и аэродинамические нагрузки. При этом радиальную нагрузку на стороне всасывания воспринимает опорный подшипник, а на стороне нагнетания радиальное и осевое усилие воспринимает опорно-упорный подшипник. Подшипники работают на жидкой смазке, в качестве которой используется минеральное масло. Корпус опорно-упорного подшипника отливается отдельно от корпуса машины. Материалом служит отливка из чугуна марки СЧ 15-32 ГОСТ 1412-54. Корпус же упорного подшипника отлит заодно с всасывающей камерой. Корпусы вкладышей подшипников изготавливаются из чугунных отливок чугуна марки СЧ 28-48 ГОСТ 1412-54, т.е. из чугуна повышенной прочности. Заливку вкладышей производят баббитом Б83.
Для уменьшения внешних (концевых) утечек газа и в системах защиты газа от замасливания используются лабиринтные уплотнения на стороне всасывания и на стороне нагнетания, расположенные между уплотняемой внутренней полостью машины и подшипниками.
Для обеспечения маслом узлов трения (подшипников, муфты, уплотнений) и системы регулирования предусмотрена масляная система открытого типа. В открытой масляной системе масляный бак соединяется с атмосферой, и давление над поверхностью масла в баке, таким образом, равно атмосферному. При этом масло совершает следующий путь: масляный бак – фильтр – масляный насос – масляные холодильники – напорная магистраль - к подшипникам – сливной трубопровод – масляный бак.
Литература.
1. Зуев А.В., Огнев В.В., Семеновский В.Б. Теория, расчет и конструирование компрессоров динамического действия. Методика аэродинамического расчета лопаточных аппаратов стационарных осевых компрессоров: Учеб. пособие. СПб.: Изд-во СПбГПУ, 2003. 111с.
2. Селезнев К.П., Галеркин Ю.Б. Теория и расчет турбокомпрессоров: учебное пособие для студентов вузов машиностроителных специальностей. 1986.
3. Скубачевский Г.С. Авиационные газотурбинные двигатели. Конструкция и расчет двигателей. – 5 изд., перераб. и доп. – М.: Машиностроение, 1981. - 550 с., ил.
Санкт-Петербургский Государственный Политехнический Университет
Энергомашиностроительный факультет
Кафедра компрессорной вакуумной и холодильной техники
КУРСОВОЙ ПРОЕКТ
Дисциплина: турбомашины
«Осевой компрессор стационарного типа»
Выполнил:
студент группы 5036/1 Коленько Г.С.
Проверил:
преподаватель: проф. Зуев А.В.
.
Санкт-Петербург
2013
Содержание.
Техническое задание.
1. Расчетная часть.
1.1 Вариантный расчет лопаточного аппарата.
1.2 Газодинамический расчет оптимального варианта проточной части компрессора.
1.2.1. Первый поступенчатый расчет.
1.2.2 Выполнение эскиза лопаточного аппарата.
1.2.3 Второй поступенчатый расчет.
1.2.4 Определение статических давлений и статических температур в ЛА.
1.2.5 Проектирование всасывающей камеры.
1.2.6 Проектирование выходного диффузора.
1.2.7 Проектирование кольцевых уплотнений.
1.3 Прочностной расчет компрессора.
1.3.1. Расчет осевого усилия, действующего на роторе компрессора.
1.3.2 Расчет подшипников на удельное давление.
1.3.3 Оценка прочности барабана ротора.
1.3.4 Расчет критического числа оборотов ротора.
Описание конструкции.
Литература.
Техническое задание.
Спроектировать по методу ЦКТИ осевой компрессор стационарного типа, сжимающий газовую среду – воздух.
Исходные данные:
показатель адиабатического сжатия k=1,4;
универсальная газовая постоянная R = 287,1 Дж/(кг К);
начальное давление = 98,1 кПа;
температуры = 298 К;
отношение давлений машины = 3,7;
массовый расход = 112 кг/сек;
привод: паровая турбина с числом оборотов n = 3300 об/мин.
Расчетная часть.
Проектирование осевых компрессоров выполняется одним из двух возможных методов: метод ЦИАМ и метод ЦКТИ. Первый метод, разработанный московским предприятием, основывается на расчете параметров и проектировании проточной части по обобщенным данным продувок плоских решеток (метод широко используется в авиационной технике). Второй метод (ЦКТИ), ленинградского предприятия, основывается на экспериментальных характеристиках одиночных ступеней, и предназначен для расчета проточных частей воздушных компрессоров стационарного типа производительностью до 300 кг/сек при степени повышения давления до 4,5 и при значении окружной скорости не выше 280 м/с.
Согласно техническому заданию работа по проектированию энергетической машины будет осуществляться по методу ЦКТИ.
Вариантный расчет лопаточного аппарата.
Вследствие наличия входных и выходных патрубков в принципиальной схеме компрессора, значение давления перед и за рабочим колесом, соответственно первой и последней ступеней, будут отличаться на величину потери давлений. Потери давления во всасывающем и нагнетательном патрубках определяются по известным коэффициентам потерь в них.
(1)
где zв – коэффициент потерь во всасывающем патрубке;
– плотность потока перед лопаточным аппаратом, кг/м3.
(2)
где zк – коэффициент потерь в нагнетательном патрубке; – плотность потока за лопаточным аппаратом последней ступени, кг/м3.
При отсутствии данных о коэффициентах потерь в проектируемых патрубках для предварительных расчетов с учетом наличия входного направляющего аппарата и спрямляющего аппарата принимают zв =0,1…0,2 и zк = 0,45…0,6.
Значения скоростей в патрубках выбираются из предела (80…130) м/с, при этом значение скорости для выходного патрубка выбирается несколько меньшей, чем для входного с1.
Принимаем значения коэффициентов потерь: zв = 0,15 и zК = 0,5; значения скоростей: =110 м/с и
= 100 м/с.
Плотность воздуха на входе в лопаточный аппарат:
(3)
Оценим величину потерь во всасывающем патрубке (+ВНА) по формуле (1):
Тогда полное давление перед первой ступенью будет равно:
(4)
Полная температура за лопаточным аппаратом, равная полной температуре за компрессором, определяется по формуле:
(5)
где – коэффициент полезного действия компрессора,
= 0,9
Значение давления за компрессором определяется как:
(6)
Плотность воздуха за лопаточным аппаратом:
(7)
История создания датчика движения: Первый прибор для обнаружения движения был изобретен немецким физиком Генрихом Герцем...
Особенности сооружения опор в сложных условиях: Сооружение ВЛ в районах с суровыми климатическими и тяжелыми геологическими условиями...
Кормораздатчик мобильный электрифицированный: схема и процесс работы устройства...
Автоматическое растормаживание колес: Тормозные устройства колес предназначены для уменьшения длины пробега и улучшения маневрирования ВС при...
© cyberpedia.su 2017-2024 - Не является автором материалов. Исключительное право сохранено за автором текста.
Если вы не хотите, чтобы данный материал был у нас на сайте, перейдите по ссылке: Нарушение авторских прав. Мы поможем в написании вашей работы!