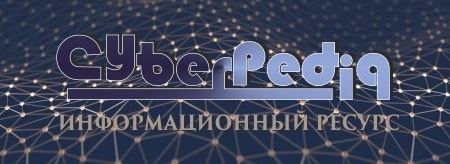
Археология об основании Рима: Новые раскопки проясняют и такой острый дискуссионный вопрос, как дата самого возникновения Рима...
Наброски и зарисовки растений, плодов, цветов: Освоить конструктивное построение структуры дерева через зарисовки отдельных деревьев, группы деревьев...
Топ:
Основы обеспечения единства измерений: Обеспечение единства измерений - деятельность метрологических служб, направленная на достижение...
Выпускная квалификационная работа: Основная часть ВКР, как правило, состоит из двух-трех глав, каждая из которых, в свою очередь...
Интересное:
Инженерная защита территорий, зданий и сооружений от опасных геологических процессов: Изучение оползневых явлений, оценка устойчивости склонов и проектирование противооползневых сооружений — актуальнейшие задачи, стоящие перед отечественными...
Мероприятия для защиты от морозного пучения грунтов: Инженерная защита от морозного (криогенного) пучения грунтов необходима для легких малоэтажных зданий и других сооружений...
Как мы говорим и как мы слушаем: общение можно сравнить с огромным зонтиком, под которым скрыто все...
Дисциплины:
![]() |
![]() |
5.00
из
|
Заказать работу |
|
|
Одной из важнейших эксплуатационных характеристик газоперека-чивающего агрегата является его надежность. Под понятием надеж ность агрегата понимается его свойство выполнять заданные функции, сохраняя во времени значения установленных эксплуатационных показателей в заданных пределах, соответствующих режимам и условиям использования, технического обслуживания, ремонтов, хранения и транспортировки.
Как видно из приведенного определения, надежность агрегата является комплексным свойством, которое в зависимости от назначения и условий работы агрегата включает в себя такие понятия, как работоспособность, неисправность, наработка на отказ, ремонтопригодность. Надежность агрегата в общем случае определяется надежностью его элементов, систем, его обслуживающих, и характером их взаимодействия.
Под понятием работоспособность эксплуатации агрегата понимается способность агрегата выполнять заданные функции эксплуатации в пределах, допустимых нормативно-технической документацией и инструкциями по его эксплуатации.
Под понятием неисправность агрегата понимается состояние, при котором агрегат не соответствует хотя бы одному из требований, установленных нормативно-технической документацией, даже в том случае, если эта неисправность и не приводит сразу к отказу в его работе.
Под понятием отказ понимается событие, заключающееся в полной или частичной потере работоспособности агрегата. Поэтому безотказностью агрегата называется его свойство непрерывно сохранять работоспособность в течение заданного времени эксплуатации.
Отказы в работе агрегата на КС возникают по разным причинам: из-за недостатков в конструкции узла или агрегата, так называемые кон-
|
Показатель надежности, диагностика и снижение энергозатрат ГПА 239
структивные отказы; из-за нарушения правил технологии изготовления или монтажа агрегата на станции, так называемые технологические отказы, и эксплуатационные отказы - из-за нарушения правил эксплуатации агрегатов на станции. Отсюда и возникает очень важное для эксплуатации понятие как наработка на отказ, одно из основных понятий надежности агрегатов при их эксплуатации на газопроводах.
Кроме приведенных определений отказов в работе оборудования, можно различать еще отказы систематические, полные, частичные, внезапные и постепенные.
К систематическим отказам можно отнести отказы элементов, узлов и обслуживающих вспомогательных систем ГПА, долговечность которых во много раз меньше, чем долговечность самого агрегата, например, работа систем разного рода уплотнений, износ масляных и воздушных фильтров и т.п., требующих периодического ремонта и замены; обычно эти дефекты устраняются на станции силами обслуживающего персонала.
Под понятием полного отказа понимается нарушение работоспособного состояния агрегата в целом, требующее длительной его остановки, замены или сложного ремонта.
Под понятием частичного отказа понимается состояние, после возникновения которого агрегат может использоваться по назначению, но с меньшей эффективностью, например, при разгерметизации регенераторов, утечке масла и т.п.
Внезапный отказ характеризуется скачкообразным изменением одного или нескольких параметров, определяющих работу ГПА. Внезапный отказ практически мгновенно переводит агрегат из работоспособного состояния в состояние отказа.
Постепенный отказ характеризуется монотонным изменением одного или нескольких заданных параметров ГПА, например, снижением мощности агрегата из-за износа узлов и деталей.
Под понятием долговечность понимается способность агрегата сохранять свою работоспособность при установленной системе технического обслуживания и ремонта до наступления предельного состояния. Под предельным состоянием агрегата понимается состояние, когда его дальнейшая эксплуатация должна быть прекращена вследствие неустранимого отклонения заданных параметров от установленных пределов или неустранимого снижения эффективности эксплуатации ниже допустимой, или неустранимого нарушения требований техники безопасности, или необходимости проведения капитального ремонта.
|
Под понятием ремонтопригодность агрегата понимается его приспособленность к предупреждению и обнаружению причин возникнове-
240 |
глава 5 |
Показатель надежности, диагностика и снижение энергозатрат ГПА 241
ния отказов, повреждений и устранения их последствий путем проведения ремонтов и технического обслуживания.
Под понятием сохраняемость понимается свойство агрегатов сохранять исправное и работоспособное состояние в течение хранения и после транспортировки.
В настоящее время оценка показателей надежности ГП А на газопроводах осуществляется системой показателей, основанных на определении времени нахождения агрегата в том или ином эксплуатационном состоянии: суммарном времени нахождения агрегата в работе Т за отчетный период Тк; времени нахождения агрегата в резерве Т; времени нахождения агрегата в плановом ремонте Тпп; времени вынужденного простоя Г агрегата за отчетный период Г. Обычно за отчетный период принимается календарный год
Гк=^+Гез+Гпр+Гв = 365 дней.
На основе сопоставления приведенных временных состояний агрегата и определяются показатели его надежности:
1. Коэффициент технического использования агрегата, определяемый как отношение времени пребывания ГПА в работе ко времени пребывания агрегата в работоспособном состоянии, времени его вынужденных простоев и ремонтов за рассматриваемый период эксплуатации
(5.1) |
К
т +т +т
у ппр ' -1 в
4. Коэффициент, характеризующий среднюю наработку агрегата на число отказов (/•) в отчетном отрезке времени:
(5.4) |
Т = -
1 о
Т в — г |
5. Коэффициент, характеризующий время восстановления работоспособности агрегата, определяемый как отношение общего времени вынужденного простоя ГПА к числу отказов за рассматриваемый отрезок времени:
|
(5.5)
Опыт эксплуатации газотурбинных агрегатов на газопроводах показывает: численные значения коэффициентов технического использования для ГПА различных типов изменяются в диапазоне 0,75-0,95; коэффициент готовности в диапазоне 0,80-0,96; коэффициент оперативной готовности - в диапазоне 0,84-0,88.
Наработка газотурбинных ГПА на один отказ в целом по парку агрегатов находится в среднем за последние пять лет эксплуатации на уровне 2600-2900 ч. По типам агрегатов этот показатель, как один из основных показателей надежности ГПА в условиях эксплуатации, распределяется примерно следующим образом (табл. 5.1).
Таблица 5.1 Наработка на отказ у ряда ГПА с газотурбинным приводом
2. Коэффициент готовности агрегата, определяемый как отношение времени нахождения ГПА в работоспособном состоянии к сумме времени нахождения его в рабочем состоянии и времени вынужденного простоя
(5.2) |
т +т
р в
Тип ГПА | Количество ГПА, шт. | Наработка на отказ, ч |
ГТ-750-6 | 100 | 4500 |
ГТ-6-750 | 140 | 9800 |
ГТН-6 | 80 | 11500 |
ГТК-10 | 790 | 7900 |
ГПУ-10 | 270 | 6200 |
3. Коэффициент оперативной готовности, определяемый как отношение времени нахождения ГПА в работе или в резерве, к общему календарному отрезку времени
(5.3)
Опыт эксплуатации агрегатов на газопроводах показывает, что в настоящее время к агрегатам нового поколения, поступающим на газопроводы, могут быть предъявлены следующие требования (не менее): коэффициент технического использования на уровне 0,93-0,95; коэффициент готовности на уровне 0,98-0,985; коэффициент наработ-
16. А. Н. Козаченко |
242 |
глава 5
ки на отказ на уровне 3,5-4,5 тыс. ч; ресурс между средними ремонтами 10-13 тыс. ч; ресурс между капитальными ремонтами 20 -25 тыс. ч; полный ресурс до списания ГПА 100 тыс. ч.
5.2. Техническая диагностика газоперекачивающих агрегатов
Диагностика происходит от греческого слова diagnostikos - способность распознавать. В соответствии с ГОСТ 20911-75 техническая диагностика призвана разрабатывать методы и приборы для определения, технического состояния объектов диагностирования (агрегатов) по параметрам, характеризующим протекание процессов в этом агрегате.
|
В зависимости от постановки задачи можно различать следующие виды диагностики: функциональную, связанную с определением изменения основных энергетических показателей агрегата (например, его мощности и КПД); структурную, оценивающую характер и степень повреждений деталей механизма; визуальную, оценивающую причины разрушения деталей при их осмотре, и прогнозную, предсказывающую характер протекания износа деталей и время выхода их из строя.
В настоящее время в эксплуатационных условиях в той или иной мере применяют следующие виды диагностики: параметрическую, вибрационную, по анализу отработанного масла, оптические и акустические методы для обследования узлов и деталей ГТУ и др.
В условиях оценки состояния и работы ГТУ на газопроводах важное значение имеют практически все виды диагностики, прежде всего потому, что агрегаты на КС непрерывно работают в течение многих сотен и тысяч часов без остановки. Именно в этих условиях, не имея возможности в ряде случаев по технологическим причинам остановить агрегат, особенно важно оценить его текущее состояние и предсказать ход изменения его основных характеристик (мощность, КПД) на перспективу.
В условиях КС в настоящее время заложена постоянно действующая система замера параметров работающих агрегатов по ГТУ и нагнетателю. На станциях периодически измеряют параметры рабочего тела Р, Т по тракту ГТУ, параметры газа Р, Тпо тракту нагнетателя, параметры окружающей среды. Однако на КС еще не организована до конца надежная система комплексной оценки состояния агрегатов, например, по мощности или по расходу топливного газа и т.п., прежде всего из-за сложности достоверного определения расхода рабочего тела по ГТУ или транспортируемого газа по нагнетателю.
Показатель надежности, диагностика и снижение энергозатрат ГПА 243
Следует отметить, что состояние агрегатов можно и целесообразно оценивать не только значениями измеряемых параметров, такими как Р и Г, но и такими характеристиками, как шум, вибрация, утечки рабочего тела по тракту агрегата и т.д.
Шум работающего агрегата представляет собой хороший источник диагностической информации, характеризующий сложный спектр шумов аэродинамического и механического происхождения, изменяющийся в зависимости от изменения состояния двигателя, Как известно, основными источниками шума в работающем двигателе являются компрессор, процесс горения топлива в камере сгорания, газовая турбина, вращающиеся детали вспомогательных механизмов ГТУ, обслуживающих агрегат. Если в этих условиях определять составляющие спектра шума от агрегата и отслеживать его изменения во времени, то диагностирование ГПА по спектру шума может быть весьма эффективным в условиях эксплуатации для оценки состояния агрегата.
|
При работе газотурбинного агрегата все его узлы и детали совершают вынужденные и резонансные колебания механического и аэродинамического происхождения, что вызывает так называемую вибрацию двигателя. К источникам колебаний механического происхождения можно отнести разного рода соударения и взаимодействие различных деталей двигателя. К источникам колебаний аэродинамического происхождения можно отнести пульсацию потока газов по газовоздушному тракту ГТУ, турбулентность процесса горения топлива в камере сгорания и т.п.
В зависимости от конструктивного исполнения ГТУ, ее сборки и монтажа, условий эксплуатации, вибрация элементов установки может быть самой различной. В некоторых случаях вибрация может стать такой значительной, что заставит пойти на вынужденную остановку агрегата. В противном случае повышенная вибрация может привести к быстрому износу и разрушению узлов двигателя, прежде всего тех, которые в наибольшей степени подвержены вибрации (лопатки, подшипники, узлы крепления корпуса двигателя и т.п.)
Все это вместе взятое приводит к необходимости измерять на КС вибрацию каждой ГТУ, чтобы на базе большого числа замеров установить спектры характерных неисправностей двигателей и разработать критерии эффективной эксплуатации ГТУ на КС.
Кроме указанных методов, в условиях эксплуатации проводится диагностика температурного состояния деталей агрегата, прежде всего лопаток турбины, визуально-оптическая диагностика, позволяющая выявлять разрывы материала, трещины, неплотности, деформации, нарушение покрытий и изоляции камер сгорания, газовой турбины и т.п.
С помощью того или иного метода диагностики ГПА можно и весьма целесообразно прогнозировать изменение технического состояния агре-
244 |
глава 5
гата с целью предупреждения вынужденных остановок ГПА, повышения эффективности их эксплуатации, определения видов и сроков проведения ремонтов.
Техническое состояние газоперекачивающего агрегата существен-ным образом сказывается на всей технологии транспорта газов по газопроводу. Можно всегда утверждать, что, если при данном расходе топливного газа по агрегату снизилась производительность нагнетателя, то при прочих равных условиях это могло произойти из-за ухудшения состояния ГТУ, нагнетателя или того и другого вместе.
Одним из основных направлений технической диагностики ГПА является метод параметрической диагностики, как наиболее перспективный и имеющий значительный опыт использования в авиационной и других отраслях промышленности. Основой метода параметрической диагностики является определение изменения параметров технического состояния агрегата или его отдельных элементов по изменению его технологических и топливоэнергетических показателей - мощности, производительности, КПД привода и нагнетателя в процессе эксплуатации.
Об изменении технического состояния агрегата или его отдельных элементов судят по изменению характеристик их рабочих режимов. Само изменение обычно оценивается сравнением характеристик, построенных для данного момента, и времени, принятого за исходное. В качестве исходного может быть принято время проведения стендовых, сдаточных или других видов испытаний агрегата. Неизменность характеристик агрегата будет говорить о его нормальном состоянии; «расслоение» характеристик будет свидетельствовать об изменениях, происходящих в ГПА.
В качестве количественных оценок смещения характеристик ГПА, ГТУ или нагнетателя иногда принимаются коэффициенты технического состояния по КПД К „или по мощности KN:
(5.6)
где ц, N - соответственно, КПД и мощность агрегата (нагнетателя) в данный момент времени; т|0 и N 0 - соответственно, КПД и мощность в исходном состоянии агрегата (нагнетателя) в начале их эксплуатации на КС или после проведения очередного ремонта. В условиях эксплуатации могут использоваться и другие показатели, определяющие изме-' нения состояния ГПА и его элементов, в основе которых лежит принцип определения «расслоения» характеристик.
Технические сложности в непосредственном измерении мощности и, следовательно, КПД энергопривода и нагнетателя приводят к необходимости их определения косвенным путем, используя доступные и измеряемые пара-
Показатель надежности, диагностика и снижение энергозатрат ГПА 245
метры, такие как: давление, температура, расход рабочего тела, связанные между собой известными соотношениями термодинамики. На рис.5.1 показана примерная схема измерений при проведении теплотехнических испытаний ГПА с двухвальным газотурбинным приводом и регенератором.
Опыт использования метода параметрической диагностики для оценки технического состояния эксплуатируемых ГПА показал, что для ее эффективного применения необходимо решить две принципиальные задачи:
• обеспечить необходимый объем и требуемую точность измерений параметров ГПА;
• разработать методическое и программное обеспечение для автоматизированных расчетов по определению технического состояния ГПА с использованием ПЭВМ.
Большинство эксплуатируемых ГПА имеют объем штатных измеряемых параметров, используемых для контроля и управления агрегата, достаточный для проведения его диагностических исследований. Однако общая точность применяемой штатной измерительной аппаратуры не удовлетворяет современным требованиям оценки технического состояния ГПА. На практике необходимо использовать лабораторные образцовые приборы. Характеристики некоторых из них, представлены в табл. 5.2.
Следует заметить, что препарирование агрегата с использованием указанных измерительных приборов влечет за собой большой объем подготовительных работ, соизмеримый с объемом проведения непосредственно экспериментальных исследований.
Что касается методического и программного обеспечения, то в настоящее время эта задача практически решена для всех типов ГПА, находящихся в эксплуатации. Использование метода параметрической диагностики для оценки технического состояния ГПА позволяет решить следующие задачи:
• оценить качество ремонта ГПА путем определения показателей его технического состояния до и непосредственно после вывода агрегата из ремонта;
• обосновать сроки проведения очередного ремонта ГПА;
• оперативно определить узел ГПА (ГТУ или ЦБН), явившийся причиной ухудшения технологических и топливо-энергетических показателей агрегата;
• определить фактические теплотехнические и газодинамические характеристики модернизированных ГПА (замена СПЧ нагнетателя, элементов проточной части ГТУ, установка - замена регенератора, совершенствование камеры сгорания и т.д.).
|
глава 5 |
246 |
S о, с >я I и о X о S р. |
Показатель надежности, диагностика и снижение энергозатрат ГПА 247
Таблица 5.2 Характеристики измерительных приборов для оценки состояния ГПА
Измеряемый параметр | Прибор, предел измерения | Класс точности (погрешность измерения) |
Температура наружного воздуха, воздуха на выходе ОК, газа на входе и выходе нагнетателя, газа перед диафрагмой замерного узла технологического газа | Термометр лабораторный типа ТЛ-4, ГОСТ 21 5 -73 | ± 0,1 + 0,2 'С |
Давление газа на входе нагнетателя, перед диафрагмой замерного узла | Манометр, образцовый 0.....60 кгс/см | кл. 0,4 |
Давление газа на выходе нагнетателя | Манометр, образцовый 0.....100 кгс/см | кл. 0,4 |
Давление воздуха за ОК | Манометр, образцовый 0.....16 кгс/ см | кл. 0,4 |
Давление газа навыходе нагнетателя | Манометр, образцовый 0..... 1 6 кгс/см | кл. 0,4 |
Частота вращения роторов ГТУ | Частотомер | кл. 0,4 ± Юс |
|
|
Состав сооружений: решетки и песколовки: Решетки – это первое устройство в схеме очистных сооружений. Они представляют...
Эмиссия газов от очистных сооружений канализации: В последние годы внимание мирового сообщества сосредоточено на экологических проблемах...
Организация стока поверхностных вод: Наибольшее количество влаги на земном шаре испаряется с поверхности морей и океанов (88‰)...
Семя – орган полового размножения и расселения растений: наружи у семян имеется плотный покров – кожура...
© cyberpedia.su 2017-2024 - Не является автором материалов. Исключительное право сохранено за автором текста.
Если вы не хотите, чтобы данный материал был у нас на сайте, перейдите по ссылке: Нарушение авторских прав. Мы поможем в написании вашей работы!