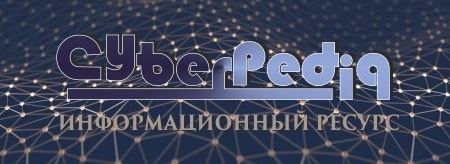
Архитектура электронного правительства: Единая архитектура – это методологический подход при создании системы управления государства, который строится...
Общие условия выбора системы дренажа: Система дренажа выбирается в зависимости от характера защищаемого...
Топ:
Характеристика АТП и сварочно-жестяницкого участка: Транспорт в настоящее время является одной из важнейших отраслей народного...
Устройство и оснащение процедурного кабинета: Решающая роль в обеспечении правильного лечения пациентов отводится процедурной медсестре...
Организация стока поверхностных вод: Наибольшее количество влаги на земном шаре испаряется с поверхности морей и океанов...
Интересное:
Влияние предпринимательской среды на эффективное функционирование предприятия: Предпринимательская среда – это совокупность внешних и внутренних факторов, оказывающих влияние на функционирование фирмы...
Берегоукрепление оползневых склонов: На прибрежных склонах основной причиной развития оползневых процессов является подмыв водами рек естественных склонов...
Принципы управления денежными потоками: одним из методов контроля за состоянием денежной наличности является...
Дисциплины:
![]() |
![]() |
5.00
из
|
Заказать работу |
|
|
ПРАКТИЧЕСКАЯ РАБОТА № 2
ТЕМА: «Нормирование точностигладких элементов деталей и соединений»
Цель: Освоение системы построения допусков и посадок на гладкие соединения.
Оснащение:
1. Методические указания по проведению работы.
2. Единая система допусков и посадок СЭВ в машиностроении и приборостроении: Справочник, М.: Издательство стандартов, 1989.
3. ГОСТ 25347-82Единая система допусков и посадок.
Порядок выполнения работы:
1. Ознакомиться с целью работы и порядком её выполнения.
2. Рассчитать и графически изобразить 3 поля допуска для вала и 3 поля допуска для отверстия.
3. Рассчитать и графически изобразить 3 посадки.
Самостоятельная внеаудиторная работа.
4. Оформление отчёта и подготовка его к сдаче.
Краткий теоретический материал:
СТ СЭВ 145—88 устанавливает основные определения допусков и посадок для элементов деталей и их соединений, имеющих гладкие цилиндрические или плоские параллельные поверхности.
Внутренние цилиндрические поверхности называют отверстиями. Диаметры отверстий обозначают D. Наружные поверхности называют валами и обозначают d.
Размеры выражают числовые значения линейных величин (диаметров, длин и т. д.) и делятся на номинальные, действительные и предельные. В машино- и приборостроении все размеры в технической документации задают и указывают в миллиметрах.
Номинальный размер(D, d) — размер, относительно которого определяют предельные размеры и отсчитывают отклонения. Номинальные размеры являются основными размерами деталей или их соединений. Сопрягаемые поверхности имеют общий номинальный размер.
Действительный размер () — размер, установленный измерением с допустимой погрешностью. Погрешность измерения, а следовательно, и выбор измерительных средств необходимо согласовывать с точностью, которая требуется для данного размера.
|
Предельные размеры — два предельно допустимых размера, между которыми должен находиться или которым может быть равен действительный размер. Больший из двух предельных размеров называют наибольшим предельным размером (Dmax, dmax), а меньший — наименьшим предельным размером (Dnm, dmln).
Отклонением называют алгебраическую разность между размером (действительным, предельным) и соответствующим номинальным размером. Отклонения отверстий обозначают Е, валов е.
Действительное отклонение (,
) равно алгебраической разности действительного и номинального размеров.
;
Предельное отклонение равно алгебраической разности предельного и номинального размеров. Различают верхнее и нижнее отклонения. Верхнее отклонение (ES, es) равно алгебраической разности наибольшего предельного и номинального размеров:
;
Нижнее отклонение (EI, ei) равно алгебраической разности наименьшего предельного и номинального размеров:
;
.
Следовательно
Разброс действительных размеров неизбежен, но при этом не должна нарушаться работоспособность деталей и их соединений, т. е. действительные размеры годных деталей должны находиться в допустимых пределах, которые в каждом конкретном случае определяются предельными размерами или предельными отклонениями. Отсюда и происходит такое понятие как допуск размера.
Допуск (I Т — общее обозначение, ITD — отверстия, ITd — вала) равен разности наибольшего и наименьшего предельных размеров или абсолютной величине алгебраической разности верхнего и нижнего отклонений
При создании механизмов машин возникает необходимость соединения двух или нескольких деталей друг с другом. Характер соединений диктуется их функциональным назначением и определяет степень допустимости их относительных перемещений после сборки. Соединение отверстий с валами образует сопряжение или, как часто говорят, «посадку».
|
Посадка — характер соединения деталей, определяемый значениями получающихся в ней зазоров и натягов.
Зазором S называют разность размеров отверстия и вала, если размер отверстия больше размера вала, т. е. S = D — d.
Натягом N называют разность размеров вала и отверстия до сборки, если размер вала больше размера отверстия.При подобном соотношении диаметров d и D натяг можно считать отрицательным зазором, т. е.
N= -S= -(D-d)=d-D.
Посадки с зазором характеризуются предельными зазорами — наибольшим и наименьшим. Они обеспечивают зазор в соединении (поле допуска отверстия расположено над полем допуска вала).
Наибольший зазор Smax равен разности наибольшего предельного размера отверстия и наименьшего предельного размера вала
Наименьший зазор Smn равен разности наименьшего предельного размера отверстия и наибольшего предельного размера вала
Формулы можно преобразовать для вычисления через отклонения
Smax = ES-ei
Smln = EI-es
Посадки с натягом обеспечивают натяг в соединении (поле допуска вала расположено над полем допуска отверстия)
Наибольший натяг равен разности наибольшего предельного размера вала и наименьшего предельного размера отверстия; наименьший натяг
равен разности наименьшего предельного размера вала и наибольшего предельного размера отверстия:
Предельные натяги, как и предельные зазоры, удобно вычислять через предельные отклонения:
Переходные посадки дают возможность получать в соединении как зазор, так и натяг (поля допусков отверстия и вала перекрываются)
Переходные посадкихарактеризуются наибольшими зазорами и наибольшими натягами
Деталь, у которой положение поля допуска не зави cum от вида посадки, называют основной деталью системы.
В зависимости от того, какая из двух сопрягаемых деталей является основной, системы допусков и посадок включают два ряда посадок: посадки в системе отверстия — различные зазоры и натяги получаются соединением различных валов с основным отверстием; посадки в системе вала — различные зазоры и натяги поручаются соединением различных отверстий с основным валом.
|
Исходные данные:
1. Номинальный размер (диаметр вала и отверстия)
2. Основные отклонения (три для вала и три для отверстия)
3. Квалитет
4. Посадки
Таблица 1.1 - Исходные данные.
№ варианта | Основные отклонения | Квалитет | Посадки | |
валов | отверстий | |||
1 | а, f, m | A, F, M | 5 | H6/g5; H5/js4; D8/h8 |
2 | b, g, n | B, G, N | 6 | H7/d8; H5/m4; E8/h8 |
3 | c, js, p | C, Js, P | 7 | H7/e8; H6/m5; F8/h8 |
4 | d, k, r | D, K, R | 8 | H7/f7; H6/js5; H8/h8 |
5 | e, j, s | E, J, S | 9 | H8/d9; H6/n5; A11/h11 |
6 | f, k,t | F, K, T | 10 | H8/f7; H7/js6; B11/h11 |
7 | h, a, u | H, A, U | 11 | H9/d9; H7/k6; C11/h11 |
8 | d, js, v | D, Js, V | 5 | H9/f9; H7/n6; F9/h9 |
9 | c, h, z | C, H, Z | 6 | H11/a11; H8/js7; E9/h9 |
10 | b, k, x | B, K, X | 7 | H11/d11; H5/js4; H11/h11 |
Пример выполнения задания:
1. Номинальный размер: Ø350
2. Основное отклонение: f
3. Квалитет: 7
4. Посадка: Н7/f7
Решение:
1. Ø350f7 - вал
Значение допуска:
ITd=57мкм=0,057мм
Одно из отклонений:
es=-62мкм=-0,062мм
Нижнее отклонение:
ei= es-ITd=-0.062-0.057=-0.119мм
Предельные размеры:
dmax=d+es=350+(-0.062)=349,938мм
dmin=d+ei=350+(-0,119)=349,881мм
Построение поля допуска:
Рисунок 1. 1 – Схема поля допуска вала Ø350f7
2. Посадка Ø350Н7/f7 - в системе отверстия.
Предельные отклонения:
Для отверстия Ø350Н7 ES=+0.057мм
EI=0
Для вала Ø350f7 es=-0,062мм
ei=-0.119мм
Предельные размеры:
Для отверстия Dmax=D+ES=350+ 0.057=350,057 мм
Dmin =D+EI=350 + 0=350 мм
Для вала dmax = d + es =350+(-0,062)=349,938 мм
dmin=d+ei =350+(-0,119)=349,881 мм
Допуск:
Отверстия TD=ES-EI=0,057- 0=0.057мм
Вала Td=es-ei= -0,062-(-0,119)=0.057 мм
Схема полей допусков:
Рисунок 1.2 – Схема полей допуска соединения Ø350Н7/f7
Расчёт предельных зазоров:
Smax = ES-ei=0.057-(-0.119) =0.176 мм
Smin= EI-es=0-(-0,062) =0,062 мм
Допуск посадки:
IТП=ITD+ITd=0,057+0,057=0,114мм
Контрольные вопросы:
1. Что такое размер: действительный, предельный и номинальный?
2. Что такое отклонения: нижние и верхние? Какое отклонение называется основным?
3. Что такое допуск и его взаимосвязь с экономикой производства?
4. Принцип построения графического изображения размеров и отклонений. Что означает нулевая линия? Как поле допуска изображается графически?
5. Какие элементы детали называются отверстием и валом?
|
6. Что такое посадки и какие посадки бывают?
7. Что такое зазор и натяг?
8. Чем характеризуются посадки с зазором, натягом и переходные?
9. Что такое посадки в системе отверстия и системе вала?
10. Какая из систем посадок (система отверстия или система вала) является предпочтительной и почему?
11. Как наносятся предельные размеры на чертежах?
ПРАКТИЧЕСКАЯ РАБОТА № 3
Порядок выполнения работы:
1. Ознакомиться с целью работы и порядком её выполнения.
2. Изобразить условные знаки для обозначения допусков формы и расположения поверхностей и записать словами их смысловое значение (согласно заданному варианту).
3. Сделать эскиз вала и нанести размеры в соответствии с требованиями ЕСТД (согласно заданному варианту)
4. Для вала необходимо задать три допуска формы и три допуска расположения поверхностей.
5. Заданные допуски свести в таблицу.
Таблица 2. 1 - Отчёт о проделанной работе.
Условное обозначение допуска | Смысловое значение | База | Степень точности |
6. Сделать вывод о проделанной работе.
Самостоятельная внеаудиторная работа.
7. Оформление отчёта и подготовка его к сдаче.
Краткий теоретический материал:
Под погрешностью формы понимается отклонение фактически допустимой формы при обработке от идеальной номинально заданной.
Под погрешностью расположения понимается отклонение фактически допустимого расположения поверхностей и элементов деталей от номинально заданных.
Действительные отклонения формы и расположения на чертежах ограничиваются допусками.
ЕСДП СЭВ устанавливает 3 группы допусков:
1.Отклонением формы поверхности или профиля называют отклонение формы реальной поверхности (реального профиля) от формы номинальной поверхности (номинального профиля).
1) отклонение и допуск прямолинейности (-). Задаётся к прямой в плоскости, к прямой в пространстве (ось вала), к прямой в заданном направлении. Частные случаи – выпуклость и вогнутость.
2) отклонение и допуск плоскостности ( ) Задаётся к плоским поверхностям.Частными видами отклонений от плоскостности являются выпуклость и вогнутость.
3)отклонение и допуск цилиндричности () Комплексно характеризует отклонение формы в поперечном и продольном сечениях цилиндрической поверхности.
4) отклонение и допуск круглости(О). Задаётся в сечении, перпендикулярном оси поверхности вращения. Частные случаи – овальность и огранка.
5) отклонение и допуск профиля продольного сечения цилиндрической поверхности (=). Задаётся к образующим цилиндрической поверхности, лежащим в плоскости продольного сечения. Частные случаи: конусообразность, бочкообразность, седлообразность.
|
2. Отклонения расположения поверхностей называют отклонение реального расположения поверхности, оси или профиля от номинального расположения.
1) Отклонение и допуск параллельности ()задаётся к параллельной плоскости для прямой и плоскости, для прямых в плоскости, для двух прямых или осей в пространстве.
2) Отклонение и допуск перпендикулярности () задаётся для перпендикулярных плоскостей, для плоскости и прямой, для двух прямых в плоскости, для двух прямых в пространстве.
3) Отклонение и допуск наклона ().Задаётся к углу наклона плоскостей, к прямой и плоскости, к прямой и плоскости в пространстве.
4) Отклонение и допуск соосности ().Задаётся к осям поверхностей вращения и различают:
-отклонение от соосности относительно оси базовой поверхности;
-отклонение от соосности относительно общей оси;
5)Отклонение и допуск симметричности ().Задаётся для симметричных элементов (боковые поверхности шпоночного паза). Может задаваться относительно базовой плоскости симметрии и относительно общей плоскости симметрии.
6)Позиционное отклонение и допуск()- условные названия отклонения и допуска на смещение оси или плоскости относительно номинального расположения. Задаётся для расположения элементов, участвующих в сборке изделия.
7) Отклонение и допуск пересечения осей (). Задаётся для пересекающихся осей поверхностей вращения.
3. Суммарное отклонение (допуск) формы и расположения(табл.8.7,8.8)
- отклонение (допуск), которое одновременно учитывает (ограничивает) отклонения формы и расположения рассматриваемой реальной поверхности (профиля) относительно заданных баз.
1) Допуск биения ().
-Радиальное биение- разность наибольшего и наименьшего расстояний от точек реального профиля поверхности вращения до базовой оси в сечении плоскостью, перпендикулярной базовой оси.Оно возникает в результате отклонений от круглости и соосности с указанной осью профиля проверяемого сечения.
-Торцовое биение - разность наибольшего и наименьшего расстояний от точек реального профиля торцевой поверхности до плоскости, перпендикулярной базовой оси. Его определяют в сечении торцовой поверхности цилиндром заданного диаметра d.
-Биение в заданном направлении- разность наибольшего и наименьшего расстояний от точек реального профиля поверхности вращения в сечении рассматриваемой поверхности конусом, ось которого совпадает с базовой осью, а образующая имеет заданное направление, до вершины этого конуса.
2)Допуск полного биения()
-Полное радиальное биение цилиндрической поверхности появляется в результате отклонений проверяемой поверхности от цилиндричности и соосности с базовой осью.
- Полное торцовое биение определяют аналогично торцовому, но в пределах всей торцовой поверхности.
Задаётся: радиальное - к цилиндрическим поверхностям; торцовое- к плоским.
3) Отклонение и допуск формы заданного профиля().Задаётся к криволинейным профилям(спираль Архимеда, винтовая линия)
4) Отклонение и допуск формы заданной поверхности().Задаётся к сложным криволинейным поверхностям.
Исходные данные:
Таблица 2. 2 - Исходные данные.
Рисунок 2. 1 - Чертёж вала.
Пример выполнения задания:
1. О – допуск круглости.
2, 3.
4.
Таблица 2. 3 - Отчёт о проделанной работе.
Условное обозначение допуска | Смысловое значение | База | Степень точности |
![]() | Допуск круглости цилиндрической поверхности Ø340f7равен 0,016мм | - | 6 |
![]() | Допуск радиального биения наружной поверхности Ø350m6 | Б | 5 |
Контрольные вопросы:
1. Что такое отклонение формы?
2. Что такое прилегающая поверхность?
3. Понятие о частных видах отклонения формы.
4. Виды отклонений формы, условные знаки для указания их допусков на чертежах. Примеры.
5. Отклонение от плоскостности.
6. Отклонения формы цилиндрических деталей. Комплексные и частные виды этих отклонений.
7. Отклонения расположения и условные знаки их допусков на чертежах.
8. Зависимые и независимые допуски расположения.
9. Суммарные отклонения формы и расположения элементов деталей. Их виды и условные знаки указания допусков на чертеже.
ПРАКТИЧЕСКАЯ РАБОТА № 4
ТЕМА: «Нормирование требований к шероховатости поверхностей»
Цель:
Научиться нормировать шероховатость поверхностей деталей машин.
Научиться обозначать шероховатость поверхностей начерте же.
Оснащение:
1. Методические указания по проведению работы.
2. Эскиз вала с заданными размерами (практическая работа № 2).
3. Единая система допусков и посадок СЭВ в машиностроении и приборостроении: Справочник, М.: Издательство стандартов, 1989.
Порядок выполнения работы:
1. Ознакомиться с целью работы и порядком её выполнения.
2. Для каждой поверхности детали (вала), исходя из ее назначения и точности размеров, формы и расположения поверхностей нормировать требования к ее шероховатости.
3. Обозначить параметры шероховатости поверхностей детали на эскизе. Самостоятельная внеаудиторная работа.
4. Оформление отчёта и подготовка его к сдаче.
Краткий теоретический материал:
При механической обработке на поверхности изделия всегда образуется множество неровностей с различными высотами и шагами.
Один из способов условного разделения отклонений на макро- (погрешность формы, волнистость) и микрогеометрические (шероховатость) основан на оценке отношения шага между неровностями l и высотой h (рис. 3.1).
Рисунок 3. 1 – Схема метода условного разделения макрогеометри-ческих и микрогеометрических отклонений на плоских поверхностях.
Если отношение l / h > 1000, то это отклонение условно относят к единичному макрогеометрическому отклонению от правильной геометрической формы (погрешность формы), при 1000 > l / h > 50 — к волнистости, а при l / h < 50 — к микрогеометрическим отклонениям (шероховатость поверхностного слоя).
Под шероховатостью поверхности понимают совокупность выступов и впадин на базовой длине l. Причиной возникновения шероховатости являются случайные погрешности при обработке.
Рисунок 3. 2 – Профилограмма и основные параметры поверхности.
Неровности поверхности нормируются геометрическими параметрами. В мировой практике разработано около 50 различных параметров, но наиболее широкое практическое применение находят шесть из них:
• три вертикальных параметра:
Ra — среднее арифметическое отклонение профиля;
Rz — высота неровностей профиля по десяти точкам;
— наибольшая высота профиля;
• два горизонтальных параметра:
S — средний шаг местных выступов профиля;
Sm — средний шаг неровностей профиля;
• один комплексный параметр:
tp — относительная опорная длина профиля.
Базовая длина l — длина средней линии профиля, используемая для вы- деления неровностей, характеризующих шероховатость поверхности.
Методы определения параметров шероховатости:
1) Визуальный (осуществляется путём сравнения обработанной поверхности либо с образцовой деталью, либо с эталонами образцов шероховатости).
2) Измерительный (используется в лабораториях с помощью приборов профилометров и профилографов).
3) Числовые значения параметров даны в таблицах 9.3,…, 9.6
С учетом изменений, принятых Межгосударственным советом по стандартизации, метрологии и сертификации, структура обозначения шероховатости поверхности приведена на рис. 3. 3.
Рисунок 3.3 – Структура условного обозначения шероховатости на чертежах.
Исходные данные:
1. Эскиз вала в практической работе № 2.
2. По результатам работы заполняется таблица 3.1.
Таблица 3. 1 – Нормирование требований к шероховатости поверхностей.
№ | Поверхность, основной размер | Поле допуска, предельные отклонения | Квалитет | Параметры шероховатости, мкм | |
Ra | Rz | ||||
1 |
Пример выполнения задания:
Таблица 3. 1 – Нормирование требований к шероховатости поверхностей.
№ | Поверхность, основной размер | Поле допуска, предельные отклонения | Квалитет | Параметры шероховатости, мкм | |
Ra | Rz | ||||
1 | Наружная цилиндрическая ∅340, l=70 |
∅340f ![]() | 7 | 0,8 | 6,3 |
2 |
Контрольные вопросы:
1. Что такое макро и микронеровности?
2. Факторы, влияющие на чистоту поверхности?
3. Какие параметры шероховатости вы знаете?
ПРАКТИЧЕСКАЯ РАБОТА № 5
Порядок выполнения работы:
1. Ознакомиться с целью работы и порядком её выполнения.
2. Выполнить расчётную схему размерной цепи.
3. Произвести анализ звеньев размерной цепи.
4. Рассчитать параметры замыкающего звена.
Самостоятельная внеаудиторная работа.
5. Оформление отчёта и подготовка его к сдаче.
Краткий теоретический материал:
Качество машин определяется не только точностью отдельных составных частей, но и их взаимным расположением. Это важно в условиях массового и серийного производств. Требуемое их взаимное расположение при сборке должно осуществляться без подгонки, с минимальной регулировкой в условиях взаимозаменяемости.
Размерные цепи
Линейные Угловые
Детальные Сборочные
Плоские Пространственные
Звенья размерной цепи
Сотавляющие Замыкающие (исходные)
Увеличивающие Уменьшающие
Размерная цепь – совокупность размеров, образующих замкнутый контур и непосредственно участвующих в решении задач.
Звено размерной цепи – один из размеров, образующих размерную цепь.
Замыкающее звено – получается последним в процессе изготовления или при сборке.
Величина замыкающего звена определяется величинами составляющих звеньев.
Для линейной детальной плоской размерной цепи расчётная схема выглядит так:
Рисунок 4. 1- Схема размерной цепи.
Составляющее звено А i _- звено, изменение которого вызывает изменение замыкающего звена.
Увеличивающее звено – звено, с увеличением которого увеличивается замыкающее звено.
Уменьшающее звено – звено, с увеличением которого уменьшается замыкающее звено.
Линейная размерная цепь – размерная цепь, звенья которой являются линейные размеры.
Угловая размерная цепь – размерная цепь, звенья которой являются угловые размеры.
Плоская размерная цепь – размерная цепь, звенья которой расположены в одной или нескольких параллельных плоскостях.
Пространственная размерная цепь – размерная цепь, звенья которой расположены в пространстве под различными углами.
Для решения проверочной задачи необходимо найти:
1. Номинальный размер замыкающего звена
А0= ,
Где n и p- число уменьшающих и увеличивающих звеньев.
2. Предельные размеры замыкающего звена
А0max=
А0min=
3. Предельные отклонения замыкающего звена
Es(A0)= ; Es(A0)=А0max-A0;
Ei(A0)= ; Ei(A0)=А0min-A0;
4. Допуск замыкающего звена
IT(A0)=A0 max - A0 min
IT(A0)=Es(A0) - Ei(A0)
IT(A0)=
Исходные данные:
Линейная размерная цепь из практической работы №2.
Пример выполнения задания:
По заданным номинальным размерам и предельным отклонениям составляющих звеньев определить номинальный размер и предельные отклонения замыкающего звена. Составляющие звенья: А1=120 ± 0,027; А2= 40 ; А3=20-0,021;
А4=30 ;
Рисунок 4. 2- Схема размерной цепи.
Решение:
1. Уравнение размерной цепи:
А0=(А1+А2)-(А3+А4)
2. Звенья А1 и А2 –увеличивающие; А3 и А4 – уменьшающие.
3. Номинальный размер замыкающего звена:
А0=(120+40)-(20+30)=110 мм
4. Верхнее отклонение замыкающего звена:
ES(A0)= ∑ ES(Ai ув)-∑ EI(Ajум) =(0,027+0,019)-(-0,021+(-0,195))=0,262 мм
5. Нижнее отклонение замыкающего звена:
EI(A0) = ∑ EI(Ajув)- ∑ ES(Ai ум)= (-0,027+0,08)-(0+(-0,065))=0,118 мм
6. Допуск замыкающего звена:
TA0= ES(A0)- EI(A0)=0,262-0,118=0,144 мм.
7. А0= 110()
Контрольные вопросы:
1. Что такое размерная цепь?
2. Что такое замыкающее звено размерной цепи?
3. Виды размерных цепей по назначению и по расположению.
4. Задачи, решаемые при расчете точности размерных цепей.
5. Последовательность расчета размерных цепей при обеспечении полной взаимозаменяемости (расчет на максимум-минимум).
6. Чему равен допуск замыкающего звена и допуск любого звена при расчете размерных цепей на полную взаимозаменяемость?
ПРАКТИЧЕСКАЯ РАБОТА № 6
Порядок выполнения работы:
1. Ознакомиться с целью работы и порядком её выполнения
2. Для заданного диаметра выбрать размеры призматической шпонки.
3. Рассчитать шпоночное соединение.
4. Изобразить шпоночное соединение и обозначить все его элементы.
Самостоятельная внеаудиторная работа.
5. Оформление отчёта и подготовка его к сдаче.
Краткий теоретический материал:
Шпоночные соединения предназначены для передачи крутящего момента от вала к втулке и наоборот.
Шпоночные соединения по назначению бывают:
2) неподвижные;
3) подвижные (имеет место перемещение втулки вдоль вала).
По форме и назначению шпонки бывают:
1) призматические (применяются для подвижных и неподвижных соединений
в× h ×l);
2) клиновые (имеют уклон 1/100, применяются для неподвижных соединений)
3) сегментные (применяются для неподвижных соединений, предназначены для передачи крутящего момента и фиксации деталей);
4) тангенциальные.
Параметры призматических шпоночных соединений:
Рисунок 5. 1- Шпоночное соединение призматическими шпонками.
d – диаметр вала (от него выбирают размеры шпонки)
в – ширина шпонки, ширина шпоночного паза втулки, ширина шпоночного паза вала.
h – высота шпонки;
t1 – глубина шпоночного паза вала;
t2 - глубина шпоночного паза втулки;
l – длина шпонки;
В шпоночном соединении участвует 3 детали и 2 посадки по параметру в. Работоспособность шпоночных соединений определяется в основном точностью посадок по ширине шпонки b.
Остальные размеры задают так, чтобы исключить возможность защемления шпонки по высоте или чрезмерное занижение поверхностей соприкосновения боковых сторон.
По ширине для призматических шпонок предусмотрено три варианта соединения: свободное, нормальное и плотное (табл. 5.1).
Таблица 5.1 – Предельные отклонения по ширине в шпоночных соединений с призматическими шпонками.
Соединение | Ширина шпонки в | Паз | |
На валу в | Во втулке в | ||
Свободное |
h9 | H9 | D10 |
Нормальное | N9 | Js9 | |
Плотное | P9 | P9 |
Свободное соединение применяется в нереверсивных, нагруженных, подвижных соединениях при затруднённой сборке.
Нормальное соединение применяется для нереверсивных, нагруженных, неподвижных соединений при редкой разборке.
Плотное соединение применяется при реверсивных нагрузках, в нагруженных соединениях, при редкой разборке. Сборка осуществляется запрессовкой.
Сечение шпонок (b xh) зависит от диаметра вала.
К несопрягаемым размерам призматических шпонок относятся высота шпонки h и длина шпонки l.
Высоту призматических шпонок выполняют по h 11 (при высоте 2—6 мм — по h 9), длину l — по h 14, длину пазов — по H 15. Отклонения по указанным элементам всегда направлены «в тело», что гарантирует собираемость соединения.
Шпонка 16×10×80 ГОСТ 23360-78.
Исходные данные:
1. Номинальный размер вала из практической работы №1.
2. Вариант соединения выбирается из таблицы.
Таблица 5. 2 – Варианты соединения.
№ варианта | Соединение |
1, 4, 7, 10, 13, 16, 19, 22, 25, 28 | Свободное |
2, 5, 8, 11, 14, 17, 20, 23, 26, 29 | Нормальное |
3, 6, 9, 12, 15, 18, 21, 24, 27, 30 | Плотное |
Пример выполнения задания:
Дано:d=40мм;; соединение нормальное.
Выбираем шпонку призматическую b × h × l =12× 8× 45
1) Посадка: шпоночный паз вала – шпонка
12 - посадка в системе вала переходная.
Рисунок 5. 2- Схема полей допуска соединения шпоночный паз вала – шпонка.
2) Посадка: шпоночный паз втулки- шпонка
12 - посадка переходная в системе вала.
Рисунок 5. 3- Схема полей допуска соединения шпоночный паз втулки – шпонка.
3)Шпонка: 12h9 × 8h11
× 50h14
4) Поперечное сечение вала и втулки:
d-t1=40-5=35
d+ t2=40+3.3=43.3
Рисунок 5. 4- Шпоночное соединение.
Контрольные вопросы:
1. Что такое шпоночное соединение и каково его назначение? 2. В чем особенность шпоночных соединений по сравнению с обычными цилиндрическими соединениями?
3. Какие группы шпоночных соединений с призматическими шпонками предусмотрены по ГОСТ 25347-82?
4. Какие поля допусков используются для шпоночных соединений?
5. В какой системе (системе отверстия или вала) осуществляются шпоночные соединения и почему?
6. В чем отличие соединения сегментными шпонками от соединения призматическими шпонками?
7. В чем особенность шпоночного соединения клиновыми шпонками?
ПРАКТИЧЕСКАЯ РАБОТА № 7
Порядок выполнения работы:
1) Ознакомиться с целью работы и порядком её выполнения.
2) Для заданных условий назначить посадки по всем поверхностям соединения.
3) Определить систему задания и характер соединения по всем поверхностям.
4) Изобразить поля допусков по всем элементам.
5) Изобразить и обозначить комплексно и поэлементно вал со шлицевым участком и втулку со шлицевым отверстием.
Самостоятельная внеаудиторная работа.
6) Оформление отчёта и подготовка его к сдаче.
Краткий теоретический материал:
Шлицевое соединение аналогично шпоночному, но передаёт больший крутящий момент.
По назначению различают:
- подвижные (для осевого перемещения втулок по валу);
- неподвижные.
Рисунок 6. 1 – Прямобочное шлицевое соединение.
Прямобочные шлицевые соединениянаиболее распространены, просты в изготовлении, предназначены для больших нагрузок. Применяются в подвижных и неподвижных соединениях.
Размеры и допуски прямобочных шлицевых соединений регламентируются ГОСТ1139-80 «Основные нормы взаимозаменяемости. Соединения шлицевые прямобочные. Размеры и допуски».
Соединение имеет параметры:
z –число зубьев или шлицев;
d – внутренний диаметр;
D – наружный диаметр;
b – толщина зуба вала (для втулки- ширина впадины втулки)
Для сложной шлицевой поверхности принято осуществлять центрирование (соединение, сопряжение) вала и втулки по одному из элементов:
1. Центрирование по D, применяется для подвижных и неподвижных соединений с небольшим крутящим моментом.
2. Центрирование по d, применяется в подвижных соединениях, обеспечивает повышенную точность соединения.
3. Центрирование по b (по боковым сторонам шлица), применяется в реверсивных передачах с большим крутящим моментом. Недостаток - невысокая точность центрировани
|
|
Адаптации растений и животных к жизни в горах: Большое значение для жизни организмов в горах имеют степень расчленения, крутизна и экспозиционные различия склонов...
Кормораздатчик мобильный электрифицированный: схема и процесс работы устройства...
Опора деревянной одностоечной и способы укрепление угловых опор: Опоры ВЛ - конструкции, предназначенные для поддерживания проводов на необходимой высоте над землей, водой...
Механическое удерживание земляных масс: Механическое удерживание земляных масс на склоне обеспечивают контрфорсными сооружениями различных конструкций...
© cyberpedia.su 2017-2024 - Не является автором материалов. Исключительное право сохранено за автором текста.
Если вы не хотите, чтобы данный материал был у нас на сайте, перейдите по ссылке: Нарушение авторских прав. Мы поможем в написании вашей работы!