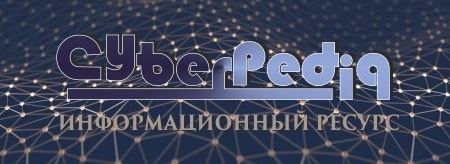
Опора деревянной одностоечной и способы укрепление угловых опор: Опоры ВЛ - конструкции, предназначенные для поддерживания проводов на необходимой высоте над землей, водой...
Типы сооружений для обработки осадков: Септиками называются сооружения, в которых одновременно происходят осветление сточной жидкости...
Топ:
Техника безопасности при работе на пароконвектомате: К обслуживанию пароконвектомата допускаются лица, прошедшие технический минимум по эксплуатации оборудования...
Процедура выполнения команд. Рабочий цикл процессора: Функционирование процессора в основном состоит из повторяющихся рабочих циклов, каждый из которых соответствует...
Характеристика АТП и сварочно-жестяницкого участка: Транспорт в настоящее время является одной из важнейших отраслей народного...
Интересное:
Средства для ингаляционного наркоза: Наркоз наступает в результате вдыхания (ингаляции) средств, которое осуществляют или с помощью маски...
Инженерная защита территорий, зданий и сооружений от опасных геологических процессов: Изучение оползневых явлений, оценка устойчивости склонов и проектирование противооползневых сооружений — актуальнейшие задачи, стоящие перед отечественными...
Национальное богатство страны и его составляющие: для оценки элементов национального богатства используются...
Дисциплины:
![]() |
![]() |
5.00
из
|
Заказать работу |
|
|
Наиболее распространенным видом контактной сварки, автоматизируемой с помощью промышленных роботов, является контактная точечная сварка, которая получила наибольшее распространение в автомобильной промышленности.
Это связано
- с наличием большого объема такой сварки при изготовлении кузовов автомобилей,
- возможностью замены квалифицированного и высокооплачиваемого сварщика машиной,
- улучшением качества сварки,
- повышением стабильности производства,
- возможностью построения гибкого производства с небольшими затратами при переходе на сварку других моделей автомобилей.
Такие же преимущества при использовании производственных роботов в тракторном, сельскохозяйственном, строительно-дорожном машиностроении.
Для осуществления операций контактной точечной сварки чаще всего используются универсальные роботы с позиционной или позиционно-контурной системой управления. Как правило, эти роботы имеют антропоморфную конструкцию.
Большинство промышленных роботов служат для перемещения сварочного инструмента относительно жестко зафиксированного обрабатываемого изделия и выполнения этим инструментом непосредственно операции контактной сварки.
В настоящее время увеличивается количество специализированных моделей роботов. Специализация заключается в особой конструкции головки робота, в особом расположении сварочного трансформатора на руке робота или в его руке.
РОБОТОТЕХНИЧЕСКИЕ КОМПЛЕКСЫ НАНЕСЕНИЯ
ЛАКОКРАСОЧНЫХ ПОКРЫТИЙ
В настоящее время около 80 % промышленных изделий защищается от коррозии с помощью лакокрасочных покрытий.
При этом 70—80 % покрытий наносят методом распыления, причем основная масса работ выполняется вручную. С созданием промышленных роботов появилась реальная возможность автоматизировать процесс окраски.
|
На операциях нанесения лакокрасочных покрытий в настоящее время находят применение специализированные и универсальные окрасочные роботы.
Специализированные окрасочные роботы предназначены для окраски плоских и приводимых к ним поверхностей (крышки, фланцы, боковины и др.). Их применяют в машиностроении в условиях крупносерийного и массового производства.
Специализированные окрасочные роботы представляют собой вертикальные или горизонтальные колонны, на каретке которых укреплены электростатические поступательные краскораспылители. Каретка совершает возвратно-поступательные движения, а рабочий орган (краскораспылитель) имеет горизонтальный или вертикальный ход. Характеристика специализированных окрасочных роботов следующая:
- исполнение вертикальное или горизонтальное;
- скорость перемещения распылителей в пределах от 5 до 90 м/мин;
- бесступенчатое регулирование скоростей.
Универсальные окрасочные роботы представляют собой в общем случае многозвенные шарнирно-сочлененные (антропоморфные) конструкции, способные окрашивать сложные пространственные контуры. Они оснащаются контурными числовыми устройствами управления.
Проблема комплексной автоматизации.процесса нанесения лакокрасочных покрытий является достаточно сложной, так как одновременно необходимо автоматизировать и объединить в единый технологический комплекс подготовку поверхности изделия, установку изделия на конвейер или другую транспортную систему, транспортирование, кантование, нанесение покрытия, подготовку и доставку краски, промывку трубопроводов, разгрузку, диспетчирование и управление комплексом, идентификацию изделий, складирование, очистку и удаление отходов производства.
Большая часть перечисленных операций решается с помощью окрасочных робототехнических комплексов.
|
Типовой окрасочный комплекс в общем случае состоит из следующих основных частей:
- окрасочной камеры,
- промышленного робота, оснащенного краскораспылителем,
- кабины оператора,
- системы подачи краски и подготовки воздуха,
- устройств ориентации и опознавания изделий,
- пульта управления,
- шкафа силовых электрических цепей,
- блока электроавтоматики.
Каждая составная часть окрасочного РТК выполняет определенные функции.
Автоматизация нанесения покрытия на объемные изделия в настоящее время сводится к распылению лакокрасочного материала автоматическим распылителем, движущимся по траектории, идентичной траектории перемещения руки опытного маляра. Эта задача решается с помощью промышленных роботов с контурной системой управления.
В режиме обучения нанесение покрытий на изделие осуществляет опытный маляр, который с помощью съемного пульта окрашивает движущееся на подвесном конвейере изделие автоматическим краскораспылителем, установленным на манипуляторе робота. При этом происходит запись траектории движения звеньев манипулятора в память системы управления окрасочного робота. Перемещение краскораспылителя в этом случае представляется как сумма перемещений всех подвижных звеньев манипулятора. В режиме автоматической окраски (в режиме воспроизведения) система управления робота определяет вид поступающего в окрасочную камеру изделия, автоматически выбирает соответствующую программу и управляет работой краскораспылителя, перемещая его в соответствии с записанной траекторией.
Окрасочная камера в составе РТК может быть проходного или тупикового типа.
Кабина оператора служит для размещения и технического обслуживания оборудования комплекса, которая защищает его от воздействия внешних неблагоприятных факторов.
Система подачи краски и подготовки воздуха предназначена для подачи лакокрасочных материалов к краскораспылителю и их распыления.
Пульт оператора управляет работой РТК.
Устройство опознавания изделия позволяет согласовать тип окрашиваемого изделия с соответствующей программой, записанной в режиме "Обучение".
Окрасочные роботы используются при автоматизации всех вспомогательных операций, предшествующих процессу окраски и завершающих его.
|
РОБОТОТЕХНИЧЕСКИЕ КОМПЛЕКСЫ
СБОРОЧНЫХ ОПЕРАЦИЙ
Сборка - завершающий этап производства, во многом определяющий стоимость и качество продукции.
Сборочные работы в различных отраслях машиностроения составляют 40—50 % общей трудоемкости изготовления изделия, что объясняется низким уровнем их автоматизации и механизации. При этом уровень механизации не превышает 25—40 %, а автоматизации, используемой в основном в условиях крупносерийного и массового производства, 5—7 %.
В условиях серийного производства, удельный вес которого в общем валовом продукте составляет 70 %, стоимость сборки существенно выше, чем в массовом производстве, главным образом вследствие большого объема пригоночных и доводочных операций и значительной трудоемкости межоперационного и межцехового транспортирования.
Стоимость сборки можно уменьшить путем организационно-технических мероприятий, сокращения объема пригоночных и регулировочных операций, применения механизированных сборочных приспособлений и инструмента, увеличения объема автоматизации и механизации сборочных процессов. Причем кардинальным решением совершенствования сборочного производства является его автоматизация.
При применении автоматизированного оборудования к объектам сборки предъявляются специфические требования по их технологичности:
- взаимозаменяемость сборочных единиц, которые, в свою очередь, могут быть собраны независимо| друг от друга;
- возможность проведения последовательной сборки, когда с одной или несколькими базовыми деталями последовательно сопрягаются другие детали;
- минимальное число направлений сборки, простота траекторий движений соединения;
- максимальная свобода доступа сборочного инструмента
Изменяя конструкцию деталей, иногда даже незначительно, можно более эффективно использовать автоматическое сборочное оборудование, уменьшить число сборочных головок, сократить операцию сборки, уменьшив количество сборочных операций и упростив их.
В то же время, изменяя конструкцию изделий, можно усложнять технологический процесс изготовления, поэтому окончательное решение по изменению конструкции объектов сборки должно приниматься по результатам технико-экономических расчетов.
|
К деталям, предназначенным для автоматической сборки, предъявляются следующие требования:
- простота конструкции, обеспечивающая удобство складирования и ориентации;
- наличие на сопрягаемых поверхностях направляющих элементов, облегчающих соединение;
- наличие ярко выраженных базовых поверхностей, размеры которых и расположение их относительно сопрягаемой поверхности должны быть выдержаны с необходимой точностью;
- стойкость к повреждениям при воздействии сборочного инструмента и оснастки;
- унификация и стандартизация;
- гарантия качества деталей.
Тип и конфигурация базовой детали определяют конструкцию сборочного приспособления и схему базирования. Условия сборки, выбор базовых поверхностей для захватывания и установки присоединяемой детали, а также последовательность сборки зависят от пространственного расположения поверхностей сопряжения. Наиболее подготовленными к автоматической сборке являются две типовые схемы.
Одна из таких схем представляет собой комплект с охватывающей базовой деталью, в которую последовательно устанавливаются распорные втулки, уплотнительные манжеты, пружинные кольца и другие детали, или предварительно собранные комплекты или изделия, например подшипники качения. В качестве базовой могут служить детали коробчатой формы, фланцы, блоки зубчатых колес и т.п.
Вторая группа комплектов представляет собой сборочную единицу с базовой деталью типа вала - втулки, на которую устанавливаются отдельные детали или предварительно собранные комплекты и изделия.
Выделение из изделий типовых комплектов позволяет применить методы групповой технологии и повысить эффективность автоматизации сборки в серийном производстве.
Таким образом, от того, на каком уровне и с использованием каких принципов будет сконструирован сборочный узел машины и сама машина, зависит успех автоматизации ее сборки. Процесс автоматической сборки с помощью промышленных роботов подразделяется на несколько этапов:
- накопление в различных устройствах (налетах, магазинах, бункерах, кассетах и т.п.), конструкция которых зависит от конфигурации и габаритов объектов сборки;
- захватывание детали (объекта) роботом, оснащенным захватом или сборочным инструментом;
- транспортирование с помощью промышленного робота на позицию сборки и от нее к позиции накопления (выдачи);
- ориентация, которая может происходить как при предварительной подготовке объектов к сборке, так и в ходе технологического процесса;
- сопряжение деталей с помощью промышленного робота или на специальном сборочном оборудовании.
|
Существует три основные концепции построения робототехнических сборочных систем:
1. Вся сборочная операция расчленяется на элементарные, каждая из которых выполняется узкоспециализированным роботом. Эта концепция нашла широкое распространение при автоматизации массового производства. В этом случае не требуется сложного периферийного оборудования для подачи и ориентации деталей и средств адаптации.
2. Промышленный робот — сборщик располагается в центре комплекса. Вокруг него располагается различное вспомогательное оборудование с необходимым запасом деталей. Робот в соответствии с программой извлекает детали и осуществляет их сборку, используя при этом стационарные монтажные приспособления и оснастку.
3. Весь сборочный процесс расчленяется на группы элементарных операций. При этом для сборки каждой сборочной группы используется специализированный робот. В этом случае работа всех роботов осуществляется центральной управляющей ЭВМ.
Промышленные роботы, применяемые для автоматической сборки изделий машиностроения, выполняют основные и вспомогательные операции, т.е. соединение и транспортирование деталей и изделий.
Для операции соединения промышленные роботы используют захваты, сборочный инструмент и приспособления. Эти устройства вместе с промышленными роботами, а также накопители деталей, транспортирующее, технологическое, контрольное и другое оборудование составляют сборочный РТК. Возможность легкой и быстрой переналадки сборочных| комплексов — главная их особенность, которая является решающей в условиях серийного многономенклатурного производства.
По структурному признаку сборочные РТК подразделяются на однопозиционные и многопозиционные, т.е. с концентрацией или дифференциацией операций процесса сборки.
Компоновка комплекса зависит в первую очередь от числа деталей в сборочной единице, их размеров и массы, а также от годовой программы выпуска и номенклатуры собираемых изделий.
При однопозиционной сборке простых узлов изделий с выпуском 0,5—1 млн. шт / год транспортные операции (такие, как подача деталей из накопителей в сборочное приспособление, установленное на технологическом оборудовании, и удаление собранного изделия) могут осуществляться одним или двумя промышленными роботами с помощью захватов.
При сборке в мелкосерийном производстве узлов изделий в количестве десятков тысяч штук в год предпочтительнее схемы одно- и двухпозиционной сборки, выполняемые одним промышленным роботом последовательно с помощью быстро- сменных захватов и сборочных инструментов. Набор захватов и инструментов, необходимых для сборки партии изделий одного типоразмера, устанавливается в инструментальный магазин при наладке РТК.
Для сборки сложных изделий с годовой программой выпуска порядка нескольких сотен тысяч штук в год может быть применена многопозиционная схема с круговой или линейной траекторией перемещения собираемого изделия соответственно на круглом делительном столе или конвейере, обслуживаемом автоматическими манипуляторами или промышленными роботами, число которых определяется в основном количеством деталей в изделии.
К конструктивным особенностям промышленных роботов для сборки относятся:
- возможность автоматической смены захватов и сборочных инструментов;
- широкий диапазон скоростей перемещения исполнительных звеньев;
- адаптация к определенным условиям захватывания и соединения деталей (возможность встройки различных датчиков и наличие функциональных связей между ними и системой управления промышленным роботом);
- контроль качества сборки (возможность встройки в конечное звено робота датчиков контроля технологических параметров объекта сборки);
- повышенная точность позиционирования или наличие устройств компенсации погрешности позиционирования при соединении деталей.
Специфика условий выполнения операций соединения разнообразных по конструкции деталей с помощью промышленных роботов предопределяет создание специализированного сборочного инструмента достаточно широкой номенклатуры.
В зависимости от области применения используют сменный или быстросменный сборочный инструмент, различающийся местом и способом крепления. С помощью сменного инструмента выполняется одна и та же операция сборки деталей во всей партии собираемых изделий, затем инструмент снимается, и закрепляется в конечном звене промышленного робота вручную при наладке оборудования на сборку очередной партии изделий. Быстросменный инструмент автоматически сменяется в цикле сборки одного изделия и поэтому может применяться для сборки изделий разного типа.
Для успешного соединения деталей с возможно меньшими удельными затратами на единицу продукции и наибольшей производительностью сборочный инструмент для промышленных роботов должен соответствовать следующим требованиям:
- унификация по элементам базирования деталей и месту присоединения к роботу;
- допустимая по условиям сборки погрешность захватывания деталей;
- надежность захватывания и транспортирования детали на сборочную позицию;
- обеспечение компенсации погрешности взаимного расположения сопрягаемых поверхностей перед соединением;
- легкость регулировки и переналадки для присоединения однотипных деталей в установленном диапазоне размеров;
- возможность встраивания элементов контрольных устройств и средств адаптации.
Автоматическое соединение деталей обусловливает высокие требования к точности взаимного расположения сопрягаемых поверхностей и траектории перемещения. Неточность взаимного расположения сопрягаемый поверхностей определяется погрешностями позиционирования подвижных узлов сборочного оборудования, взаимного расположения сопрягаемой и базирующей поверхностей деталей, установки базовой детали в приспособлении и присоединяемой детали в инструменте, базирования деталей в накопителях и транспортно-подающих устройствах.
В связи с трудностью достижения необходимой точности взаимного расположения сопрягаемых поверхностей на переналаживаемом программируемом оборудовании прибегают к компенсации указанных погрешностей.|
Погрешности взаимного расположения деталей при сборке компенсируют двумя принципиально различными способами:
1) активным — с применением датчиков, которые измеряют усилия и моменты, возникающие при сопряжении деталей, и дают команды на дополнительные перемещения узлов робота или оборудования сборочного комплекса;
2) пассивным — с применением кинематических элементов и устройств, устанавливаемых непосредственно на сборочном приспособлении или инструменте и выполняющих автоматический поиск сопрягаемых поверхностей, для чего на сопрягаемых деталях необходимо иметь соответствующие вспомогательные поверхности: фаски, скосы и т.п.
Первый способ наиболее универсален, но применим при оснащении сборочного оборудования соответствующими механизмами перемещения и широким набором средств адаптации. Второй способ менее универсален, но значительно проще и требует меньших затрат времени на выполнение сборочной операции, а средствами очувствления оснащаются лишь устройства поиска детали и контроля ее наличия на сборочной позиции.
Кроме компенсации погрешности расположения деталей при сборке необходим контроль:
- наличия в захватных инструментах сопрягаемых деталей и их правильной ориентации;
- качества сборки, в том числе требуемых усилий сопряжения;
- собираемости деталей, что позволяет осуществить селективную сборку, когда из массы деталей выбираются такие, которые по своим параметрам обеспечивают возможность автоматической сборки. Это также позволяет упростить вспомогательное оборудование, применяя системы, производящие анализ и выбор требуемых деталей в режиме адаптивного управления. Кроме того, используют совместное управление несколькими роботами, согласуя их движения при сборке изделий.
|
|
Поперечные профили набережных и береговой полосы: На городских территориях берегоукрепление проектируют с учетом технических и экономических требований, но особое значение придают эстетическим...
Двойное оплодотворение у цветковых растений: Оплодотворение - это процесс слияния мужской и женской половых клеток с образованием зиготы...
Индивидуальные и групповые автопоилки: для животных. Схемы и конструкции...
Механическое удерживание земляных масс: Механическое удерживание земляных масс на склоне обеспечивают контрфорсными сооружениями различных конструкций...
© cyberpedia.su 2017-2024 - Не является автором материалов. Исключительное право сохранено за автором текста.
Если вы не хотите, чтобы данный материал был у нас на сайте, перейдите по ссылке: Нарушение авторских прав. Мы поможем в написании вашей работы!