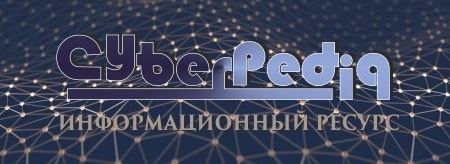
Кормораздатчик мобильный электрифицированный: схема и процесс работы устройства...
Особенности сооружения опор в сложных условиях: Сооружение ВЛ в районах с суровыми климатическими и тяжелыми геологическими условиями...
Топ:
Оснащения врачебно-сестринской бригады.
Процедура выполнения команд. Рабочий цикл процессора: Функционирование процессора в основном состоит из повторяющихся рабочих циклов, каждый из которых соответствует...
Интересное:
Распространение рака на другие отдаленные от желудка органы: Характерных симптомов рака желудка не существует. Выраженные симптомы появляются, когда опухоль...
Как мы говорим и как мы слушаем: общение можно сравнить с огромным зонтиком, под которым скрыто все...
Уполаживание и террасирование склонов: Если глубина оврага более 5 м необходимо устройство берм. Варианты использования оврагов для градостроительных целей...
Дисциплины:
![]() |
![]() |
5.00
из
|
Заказать работу |
|
|
The term Orbital-Welding is based on the Latin word ORBIS = circle. This has been adopted primarily by aerospace and used in terms of Orbit (noun) or Orbital (adjective) for the trajectory of a man-made or natural satellite or around a celestial body. The combination Orbital Weldingspecifies a process by which an arc travels circumferentially around a work piece (usually a tube or pipe). The concept Orbital Weldingis basically a loosely defined term that is usually used for processes only, where the arc is travels at least 360 degrees around the work piece without interruption. Consequently, processes, which interrupt the full 360-weld sequence such as for better puddle control (often used for MIG/MAG welding, using the downhand welding sequence in 2 half-circles), can not truly be called orbital welding.
Possibilities and Limitations
From welding terminology Orbital Welding belongs to the category semi-mechanized (TIG-) welding. Because of the need for good control of the weld puddle, the Orbital-Welding process is only practiced with the TIG process and relevant rules like selection of gases, cleanness, weldability of specific materials and consequential mechanical strength specifications such as tensile and bend loading, are very important.
Orbital-welding is presently used whenever the quality of the weld joint has the highest priority. These demands are not only limited to mechanical strength and X-ray qualification, but also to the important aspects of the aesthetics of the weld seam. For any users a uniform, flat and smooth root-pass is the main reason for using this process. Consequently, it is favoured in the following areas: chemical industry, pharmaceutical industry, bio-technology, high-purity water systems, semiconductor industry, aircraft- and aerospace industry. Moreover, because of the weld joint's uniform outside shape and almost complete absence of need for any post-polishing, Orbital-welding is even used for bends on door-handles, hand-guards, or in dead foot-elements for champagne-glasses! Interested applicants for this technology should certainly note that they have to confirm a couple of indispensable premises.
The following presents the basic rules for this process, valid for all manufacturers and systems.
Even knowing that some competitors are announcing features, which would potentially violate the basic physical laws of nature and knowledge, moreover, making promises and statements which are at least detected as impossible to meet when the welding system must work under high dutycycle production conditions.Indiscriminate and exactly defined dimensions with tolerances must be thorough and complete. The much liked standpoint, that the welded tubes and pipes are in accordance to DIN or ASME standards are not acceptable criteria. These qualifications only define tolerances in percentage to the wall thickness relating to pressure loading and not to weldability using the Orbital-Welding-Process.
For the Orbital-Welding-Process absolute tolerance values are necessary, and furthermore, the more complicated the application, the tighter the tolerances must be. This means, that for an easy application like welding a stainless steel tube of 53 x 1,5 mm, a tolerance in alignment of about 0,5 mm (about 30% of the wall thickness) can be compensated, but for much more critical applications like welding a carbon-steel pipe of 114,3 x 3,6 mm, the same percentage can result in unacceptable weld quality. Therefore, the question of acceptable tolerances should be researched and defined for each application individually.
|
That Orbital-Welding can be used successfully and economically is proven by the constantly increasing number of users. Field experience has shown that Orbital-welding can be justified based upon economic reasons alone, where the welds can be done in squared-butt no-gap preparation utilizing a single pass. With advanced digital welding systems this is possible up to a wall-thickness of 4 mm, and with welding systems with lower performance capabilities (limited levels, no pulse-synchronized cold-wirefeeding), up to 3 mm.
Joint preparation is simple but requires high quality with an exact 90\'b0 angle to the tube/pipe axis; a high quality saw cut is usually enough. Of course, the joints should be deburred and cleaned out of corrosion, oil, tinder, etc. With appropriate quality-demands, this should be even obvious for manual welds! The tube joints will be then fit together without any visible gap. This can be done with small autogenous tack-welds or with internal or external clamping fixtures. For larger wall-thickness it is necessary to bevel the weld-joints, far as possible in a U-shape. Since a very precise and uniform root pass is important, a weld joint is prepared with an. I.D. related and fixed bevelling-machine. Manual grinding or the use of bevelling saw blades is not precise enough for repeatable welding results. Because an Orbital-Welding job usually requires a lot in time and money, the Orbitalmulti-pass-welding is not used very often and only where it is strictly recommended on quality reasons. A good qualified manual welder will, in most cases, be faster than an Orbital-welding-system. Additionally, an Orbital-system for multi-pass welds will be much more expensive and even more complicated than a system without this option.
Visual inspections of the weld-seam clone can never be sufficient as the sole criterion. Other quality controls, such as, corrosion, consistency, mechanical strength must also be considered. Also, allowed tolerances in contents of alloys on specific materials, such as sulphur content, can result in significantly different welding results, even when the material code is the same. Usually, you can expect that stainless steel materials up to 3 mm wallthickness can be done without filler-wire. For higher wall-thickness applications, you have to decide on a case-by-case basis. In some eventualities even carbon steel can be done without filler-material, although it's even recommended on the thinner wall-thickness to use filler-wire in any way.
After reading activity
Find the English equivalents in the text for the following word combinations:
противоречить законам физики, обращаться вокруг обрабатываемой детали, иметь первостепенное значение, контроль сварочной ванны, красивый внешний вид сварного шва, гладкий и ровный проход при заварке корня шва, шлифовка вручную, приемлемый допуск, недопустимое качество сварки, квалифицированный сварщик, содержание серы, механическая прочность, искусственный спутник, система высокой очистки воды, обязательное условие.
|
Characterize orbital welding by filling in the right side of the following table:
Parameter | Description |
Model: Principle of the process | An arc travels circumferentially around a work piece (usually a tube or pipe). |
Category | |
Application areas | |
Limitations |
Speaking
True or false?
1. Orbital Weldingis a process, where the arc travels at least 360 degrees around the work piece with some interruptions.
2. MIG/MAG welding, using the down-hand welding sequence in 2 halfcircles, refers to orbital welding.
3. Puddle control is very important for Orbital welding.
4. The number of Orbit Welding users stays the same for a long period of time.
5. Aerospace industry is the only area of Orbital Welding application.
6. Joint preparation is not necessary.
7. Orbital-welding-system is very fast and cheap.
8. Filler-wire is used for all wall thickness applications.
Describe Orbital welding by completing the following sentences:
1. The term Orbital comes from the Latin word ORBIS and means …. 2. The Orbital Weldingisa process in which an arc travels …. 3. By category it belongs to …. 4. It is practiced only with …. 5.Orbital-welding is presently used in such areas as …. 6. It is used to produce …. 7. The basic rules for this process are …. 8. Absolute tolerances in Orbital-Welding Process are important because …. 9. Wall-thickness of 4 mm is possible …. 10. Joint preparation includes …. 11. Orbital-multi-pass-welding is rather expensive and its use is only justified when …. 12. Filler-wire is necessary to use only ….
Additional Reading
|
|
Кормораздатчик мобильный электрифицированный: схема и процесс работы устройства...
Состав сооружений: решетки и песколовки: Решетки – это первое устройство в схеме очистных сооружений. Они представляют...
Автоматическое растормаживание колес: Тормозные устройства колес предназначены для уменьшения длины пробега и улучшения маневрирования ВС при...
Двойное оплодотворение у цветковых растений: Оплодотворение - это процесс слияния мужской и женской половых клеток с образованием зиготы...
© cyberpedia.su 2017-2024 - Не является автором материалов. Исключительное право сохранено за автором текста.
Если вы не хотите, чтобы данный материал был у нас на сайте, перейдите по ссылке: Нарушение авторских прав. Мы поможем в написании вашей работы!