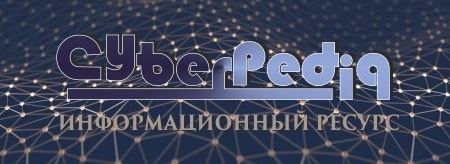
Историки об Елизавете Петровне: Елизавета попала между двумя встречными культурными течениями, воспитывалась среди новых европейских веяний и преданий...
Состав сооружений: решетки и песколовки: Решетки – это первое устройство в схеме очистных сооружений. Они представляют...
Топ:
Характеристика АТП и сварочно-жестяницкого участка: Транспорт в настоящее время является одной из важнейших отраслей народного...
Когда производится ограждение поезда, остановившегося на перегоне: Во всех случаях немедленно должно быть ограждено место препятствия для движения поездов на смежном пути двухпутного...
Характеристика АТП и сварочно-жестяницкого участка: Транспорт в настоящее время является одной из важнейших отраслей народного хозяйства...
Интересное:
Наиболее распространенные виды рака: Раковая опухоль — это самостоятельное новообразование, которое может возникнуть и от повышенного давления...
Финансовый рынок и его значение в управлении денежными потоками на современном этапе: любому предприятию для расширения производства и увеличения прибыли нужны...
Как мы говорим и как мы слушаем: общение можно сравнить с огромным зонтиком, под которым скрыто все...
Дисциплины:
![]() |
![]() |
5.00
из
|
Заказать работу |
|
|
Бетонная смесь для изготовления панелей стеновых наружных должна соответствовать СТБ 1035.
Марка по удобоукладываемости бетонной смеси:
однослойных панелей - П1 (ОК 1-4 см);
трехслойных панелей нижний слой - П2 (ОК 5-9);
трехслойных панелей верхний слой - П1 (ОК 1-4);
Подбор, назначение и корректировка состава бетонной смеси следует производить по СТБ 1182.
Материалы для приготовления бетонной смеси:
в качестве вяжущего материала должен применяться портландцемент соответствующий требованиям ГОСТ 31108 - ЦЕМ I 42,5;
в качестве крупного пористого заполнителя должен применяться керамзит щебнеподобный удовлетворяющий требованиям СТБ1217 и щебень из плотных горных пород для строительных работ в соответствии с ГОСТ 8267, ввиде фракций 5-10 мм, 10-20 мм.
в качестве мелкого заполнителя должен применяться песок для строительных работ удовлетворяющий ГОСТ 8736;
вода должна соответствовать СТБ 1114.
применяемые химические добавки должны соответствовать требованиям СТБ 1112 и обладать пластифицирующими свойствами, а также быть ускорителями твердения бетона, улучшать его строительно-технические свойства (морозостойкость, водонепроницаемость, коррозионную стойкость).
Бетонная смесь поступает на технологическую линию изготовления панелей стеновых наружных из бетоносмесительного цеха по ленточному конвейеру. Время от выгрузки бетонной смеси из смесителя до формования изделий должно быть не более 45 мин. Поданная к месту укладки бетонная смесь должна иметь требуемую удобоукладываемость, с отклонениями подвижности не более 30%.
Растворная смесь (РСГП) для образования наружного фактурного слоя и внутреннего отделочного, должна соответствовать требованиям СТБ 1307. Материалы для приготовления растворной смеси:
|
в качестве вяжущего материала должен применяться портландцемент соответствующий требованиям, ГОСТ 31108.
в качестве заполнителей должен применяться песок для строительных работ по ГОСТ 8736.
вода должна соответствовать СТБ 1114.
Режим виброуплотнения:
- амплитуда колебаний - 0,28-0,4 мм
частота колебаний - 3000 кол/мин
продолжительность уплотнения для однослойных панелей 70 -100 сек.
продолжительность уплотнения внутреннего слоя трехслойных панелей 60- 70 сек.
Основные положения проектирования технологии БСЦ
Принимаем смесительный цех циклического действия - одноступенчатый; по схеме расположения смесительных машин в плане - гнездовой; по способу управления - механизированный.
Общий объем одного замеса:
, (1.1)
где Q - производительность предприятия, м3;
Кп.см. - коэффициент, учитывающий потери бетонной смеси;
τр - расчетное число рабочих суток в году;
Nсм - число рабочих смен в сутки;
tсм - длительность рабочей смены, ч;
nз - нормативное число замесов в час;
Кч.н. - коэффициент часовой неравномерности выдачи бетонной смеси.
Принимаем Q=90255 м3, Кп.см. = 0,67 и Кч.н. =0,8 [11], nЗ= 35 [11, с. 13], τР = 255 дней [11], NCМ =2, tСМ= 8 ч.
м3.
Принимаем 2 смесителя.
Объем смесителя по загрузке:
(1.2)
где VЗ - общий объем одного замеса, м3;
nсм - число смесителей;
βб - коэффициент выхода бетонной смеси, βб=0,67 [11, стр.13];
м3.
Принимаем бетоносмеситель типа СБ-141 [6, с.167].
Вместимость по загрузке 375 л;
Объем готового замеса 250 л;
Мощность двигателя 11 кВт.
Дозаторы принимаем циклического действия.
Принимаем для расчета дозаторов и складов заполнителя и цемента по ОНТП 7-80 расход цемента 280 кг/м3[11, стр.5];
Расход песка максимальный для тяжелого бетона 1760·0,3=528 кг/м3[11, стр.3];
Расход щебня максимальный 1660·1,1=1826 кг/м3[11, стр.3].
Определяем расход компонентов на 1 замес.
Коэффициент выхода бетона КС = 0,8 м3;
Емкость смесителя 375 л;
Объем 1 замеса 0,375·0,67 = 0,25 м3;
|
Ц=202,5·0,25= 50,63 кг/замес;
В =139,5·0,25=34,88 кг/замес;
Щ = 1465·0,25 = 366,3 кг/замес;
П = 591·0,25 = 147,8 кг/замес.
Плотность песка и щебня 1500 кг/ м3;
Плотность цемента 1000 кг/м3.
Принимаем дозатор цемента ДЦТ-500; дозатор песка и щебня ДЩТ-800; дозатор воды БВГ-03М.
Вместимость складов заполнителей и цемента определяем по формуле:
, (1.3)
где nсм - число смесителей,
Vсм - объем смесителя;
βб - коэффициент выхода бетонной смеси;
Qсм - расход материала на 1 м3 бетона, м3;
зс - запас заполнителей или цемента на заводских складах, расчетные рабочие сутки.
Для цемента Qсм = 280кг/м3 =0,28 м3/м3;
зс = 10 суток.
Для песка Qсм = 528 кг/м3 = 0,35м3/м3;
зс = 7 суток.
Для щебня Qсм = 1826кг/м3 = 1,22 м3/м3;
зс =10 суток.
м3
С учетом коэффициента заполнения емкостей 0,9: Vскл.цем=875 м3=875 т
Принимаем 5 силосных банок емкостью 200 т каждая.
м3
Учитывая коэффициент заполнения: Vскл.песка=766 м3.
м3
Учитывая коэффициент заполнения: Vскл.щебня=3814 м3.
Вместимость склада заполнителей: м3.
Из вагонов цемент в силоса выгружается разгрузчиком всасывающе-нагнетательным ТА26 с производительностью 20 т/ч. В бетоносмесительной цех цемент подается пневматическим камерным насосом ТА-23 производительностью 30 т/ч.
Заполнители подаются в расходные бункера БСЦ ленточным конвейером ТК-3 с шириной ленты 650 мм и производительностью горизонтального 90 т/ч, наклонного пол углом 18° - 45 т/ч [6, с. 336].
Число отсеков расходных бункеров принимаем равным по ОНТП-7-80[11,с. 14] для цемента - 2, для песка - 2, для щебня - 3.
Объем отсеков расходных бункеров для заполнителей и цемента определяется по формуле:
, (1.4)
где Vсм - объем смесителя по загрузке, м3;
βб - коэффициент выхода бетонной смеси;
nз - нормативное число замесов в час;
зч - запас материалов в расходных бункерах, ч;
Qсм - расход материала на 1 м3 бетона, м3;
nотс - число отсеков.
Для цемента запас - 3ч, для заполнителей - 2 ч.
Для цемента:
м3.
Для песка:
м3.
Для щебня:
м3.
Транспортируется бетонная смесь из БСЦ в формовочный цех по бетоновозной эстакаде, оборудованной тремя тележками.
Механизмами дозировочного управления отделеления и бетоносмесительного отделения управляет оператор с центрального пульта дозирование осуществляется автоматическими циферблатными дозаторами. Они работают в паре со вторичными приборами, установленными в помещении оператора. Управление выпускными заторами дозаторов и бетоносмесителей осуществляется пневмоприводами с электромагнитными клапанами. Всеми производственными процессами управляет оператор из центрального пульта, в котором кроме пульта управления размещен щит технологической световой сигнализнции.
|
Основные положения технологии арматурного цеха
Арматурные изделия должны соответствовать ГОСТ 10922. Для армирования стеновых панелей применяется арматурный блок, состоящий из плоских сварных каркасов и сеток, закладные детали, петли и анкерные выпуска, соответствующие рабочим чертежами проектной документации.
Применяемая арматурная сталь и прокат.Для изготовления сварных арматурных изделий применяют арматуру ненапрягаемую S400 и S500 по СТБ1704;
Для изготовления монтажных петель и анкерных выпусков применяют арматуру с гладким профилем класса S240 марок Ст3пс и Ст3сп по СТБ 1704;
Для изготовления закладных деталей применяют прокат по ГОСТ 103, уголок по ГОСТ 8509 из углеродистой стали обыкновенного качества по ГОСТ 535.
Арматурные изделия доставляют к пролету изготовления панелей стеновых панелей производственного корпуса на межпролётной тележки и с помощью мостового крана осуществляются перемещения на технологической линии. Закладные детали транспортируют в контейнерах (ящиках) рассортированными по маркам. На линии арматурные блоки хранятся в горизонтальном положении на специально отведённых местах.
Стержни классов S 240 диаметром до 12 мм, класса S 400 диаметром до 10 мм включительно изготавливаются в мотках или стержнях, а больших диаметров - в стержнях. Стержни изготавливаются длиной от 6 до 12 м. Для правки арматуры, поступающей в мотках, принимаем правильно-отрезные установки, которые одновременно производят очистку стали.
Принимаем правильно-отрезной станок СМЖ-357 [6, с.25], имеющий следующие характеристики:
диаметр арматуры гладкой 4-10 мм, периодического профиля 6-8 мм;
точность +3; -2;
скорость подачи и правки арматуры 31,5-45 м/мин;
длина отрезаемых стержней 500-1200 мм
габаритные размеры 6100х1500х1210 мм
масса 1500 кг
мощность электродвигателя 12,6 кВт.
А также правильно-отрезной станок И-6118 [6, с.25]:
|
диаметр гладкой арматуры 2,5 - 6,3 мм;
длина отрезаемого металла 100 -6000мм
точность ±2;
скорость правки 25-50 м/мин
число оборотов правильной рамки 1250-2500 об/мин
скорость подачи и правки арматуры 25 м/мин;
мощность электродвигателя 6,9 кВт.
Для резки арматурной стали, поставляемой в прутках, принимаем станок СМЖ-1725, имеющий следующие характеристики:
наибольший диаметр арматуры класса S240 - 40 мм; S400 - 25мм;
число ходов ножа в мин 33;
ход ножа 45 мм;
мощность электродвигателя 3 кВт,
Для гибки стержневой арматуры принимаем станок СМЖ-173А [6, с.37];
максимальный диаметр изгибаемого прутка из стали класса S400- 40мм;
мощность электродвигателя 3 кВт;
габаритные размеры 760x780x780 мм.
Для резки коротких стержней принимаем станок АРС-М [6, с.27]:
диаметр отрезаемых стержней 3-55 мм;
класс арматуры S500;
длина отрезаемых стержней, наименьшая - 50 мм, наибольшая - 1000 мм;
число резов в мин - 42,
мощность электродвигателя 4 кВт;
габаритные размеры 1160x1040x665 мм.
Для сварки сеток и каркасов принимаем крестообразный тип сварных соединений, выполняемых контактной точечной сваркой. Этот способ позволяет механизировать и автоматизировать процесс изготовления плоских сварных изделий. Для сварки сеток принимаем одноточечную сварочную машину МТ-2102[10, с.45]:
наибольший диаметр свариваемой арматуры 18x18 мм;
потребляемая мощность 10кВт.
Для изготовления закладных деталей тавровыми соединениями под флюсом принимаем сварочный аппарат АДФ-2001[13, с.62]:
диаметр свариваемых анкерных стержней 8-40 мм;
производительность 200 сварок/час.
Для изготовления объемных арматурных каркасов принимаем установку СМЖ-56 [6, с. 52]:
положение сборки каркасов - вертикальное;
число одновременно собираемых каркасов -1;
максимальные размеры каркасов 7200x3600x300 мм;
диаметры свариваемой арматуры от 5×5 до 12×16 мм;
габаритные размеры установки 8400x3180x4600 мм.
Для высадки головок стержней напрягаемой арматуры принимаем установку СМЖ-128Б.03 [2, c. 291]:
номинальное напряжение питающей сети 380 В;
частота тока питающей сети 50 Гц;
диаметр арматурных стержней 10-25 мм;
длина стержней 5630- 7620 мм;
расчетное давление сжатого воздуха 0,6 мПа;
производительность 130 шт/ч;
расход воды для охлаждения 800 л/ч;
габаритные размеры установки 9620 х 1800 х1250мм.
Основные положения технологии формовочного цеха
При производстве наружных стеновых панелей принимаем конвейерный способ производства. Основным технологическим оборудованием является стальная форма с металлической рамкой-вкладышем, бетоноукладчик в который поступает бетонная смесь по ленточному конвейеру, столы виброуплотнения и взбалтывания, заглаживающее устройство, установка для сушки железобетонных изделий, тележка для ввоза арматурных элементов, тележка для вывода готовой продукции, кантователь. В пролете работает 2 мостовых крана. Для ускорения твердения принимаем термообработку.
|
В качестве формы принимаем стальную разборную форму. Передвижная форма для изготовления наружных стеновых панелей состоит из поддона, продольного и поперечного бортов. Поддон представляет собой сварную конструкцию из швеллеров, покрытую стальным листом толщиной 8 мм. Колеса предназначены для перекатывания поддона по рельсовому пути от поста к посту. Борта выполнены в виде балок коробчатого сечения, сваренных из швеллеров и стального листа. Поперечные и продольные борта соединяются между собой винтовыми зажимами, обеспечивающими надежное и плотное соединение.
При формовании стеновых панелей с проемами на поддон формы устанавливается металлическая рамка, наружный контур которой соответствует контуру проема. Прижимные щитки предназначены для крепления столярных изделий. Бортовая оснастка позволяет формовать изделие лицевой поверхностью вверх или вниз по отношению к поддону, что достигается соответствующей установкой рамки и прижимных щитков.
При изготовлении панелей следует строго соблюдать толщину слоев.
Формование нижнего слоя (внутреннего при формовании изделия «лицом вверх» и наружного при формовании «лицом вниз»). Производят распределение бетонной смеси бетоноукладчиком и последующее ее разравнивание по поверхности формы с помощью лопаты. Включением вибростола производят виброуплотнение нижнего слоя бетонной смеси. Уплотнение бетонной смеси продолжается до разравнивания слоя и появления на поверхности бетона пузырьков воздуха и прослойки свободной воды. Равномерность и толщина уложенного слоя проверяется специальным щупом или линейкой. Дополнительное разравнивание осуществляется вручную с помощью лопаты.
Укладка теплоизоляционного слоя. Укладка заготовленных плит утеплителя осуществляется согласно схеме укладки пакетов утеплителя. Зазоров между плитами утеплителя не должно быть. Пакеты между собой закрепить металлическими скобами. Одновременно с укладкой утеплителя производится установка деревянных пробок, дискретных связей и минераловатные плиты по периметру проемов.
Армирование верхнего слоя. После укладки утеплителя, установки ДС-1, пробок, минераловатных плит производится армирование фасадного слоя, при формовании панели «лицом вверх», укладываются каркасы, сетки. При формовании панели «лицом вниз», производится армирование внутреннего слоя панели, укладывается перемычный каркас, затем арматурный блок, стержнями большего диаметра вертикальных каркасов ориентированных к внутренней стороне панели. После установки осуществляется увязка всех арматурных элементов, анкеров, петель и анкеров ДС-1 между собой вязальной проволокой.
Формование верхнего слоя. Производят распределение бетонной смеси бетоноукладчиком, и уплотняют бетонную смесь при помощи стола взбалтывания. Уплотнение бетонной смеси продолжается до разравнивания слоя и появления на поверхности бетона пузырьков воздуха и прослойки свободной воды. Поверхность бетонной смеси в форме должна быть ниже бортов на толщину фактурного или внутреннего отделочного слоя, указанной в рабочей документации.
Режим виброуплотнения:
- амплитуда колебаний - 0,28-0,4 мм
частота колебаний - 3000 кол/мин
продолжительность уплотнения для однослойных панелей от 70 до 100 сек.
продолжительность уплотнения внутреннего слоя трехслойных панелей от 60 до 70 сек.
Пост сушки представляет собой стационарную сварную конструкцию и состоит из траверсы, которая имеет возможность устанавливаться на разную высоту, в зависимости от толщины и степени сушки верхней поверхности изделий. На траверсе закреплена рама с нагревательными элементами и защитными щитками.
Порядок работы: Форма-вагонетка с отформованным изделием подается на пост сушки, включаются нагревательные элементы с инфракрасным излучением. Происходит сушка верхней поверхности изделия. Степень сушки поверхности изделия регулируется расстоянием ее до нагревательных элементов и временем нахождения изделия на посту.
После поста подсушивания форма перемещается на отделку при помощи машины отделочной дисковой.
Термообработка изделий панелей стеновых наружных ведется в туннельных камерах конвейерной линии пролета при помощи продуктов сгорания газовоздушной смеси. Для поддержания заданной температуры среды, в камерах входной и выходной проемы оборудованы самозакрывающими шторами из прорезиненной ткани.
Общий цикл тепловой обработки включает следующие периоды:
выдержка 2 час;
подъем температуры 3 часов;
изотермический прогрев 9 часов при температуре 45-50ºС;
остывание 4 часа.
Режим твердения составляет 18 часов.
Рисунок 1.1 - Режим ТВО
Форма с изделием после тепловой обработки подается на пост распалубки изделий, где устанавливается на кантователь переводится в горизонтальное положение. Там форму чистят, смазывают и собирают.
Отделка стеновых наружных панелей после распалубки включает следующие операции:
устранение дефектов поверхности и граней изделий;
устранение на лицевых поверхностях панелей жировых пятен и пятен ржавчины;
очистка закладных изделий, монтажных петель и кромок от наплывов бетона или раствора;
ремонт околов и раковин;
огрунтовка верхних и боковых торцевых граней панели мастикой КН-2.
окраска закладных деталей.
Процесс ремонта околов состоит из двух операций: подготовка бетонной поверхности и укладки бетонной или растворной смесей.
Подготавливают бетонную поверхность тщательной очисткой поверхности старого бетона (в месте его соединения с новым бетоном) от цементной плёнки, пыли и других включений. Затем увлажняют водным раствором эмульсии ПВА (в холодный период ─ 1% раствор противоморозной добавки) подготовленную поверхность перед укладкой. Для ремонта применяют свежеприготовленную полимерцементную растворную смесь (в холодный период - растворную смесь с противоморозной добавкой) или бетонную смесь. Далее послойно при помощи кельмы, тёрки производят укладку смеси в дефектные места и тщательно уплотняют. После чего тёркой доводят поверхность до требуемой категории. Прочность уложенной растворной (бетонной) смеси должна быть выше прочности материала в ремонтируемом изделии.
Ремонт раковин производят затиркой полимерцементной растворной смесью (в холодный период - растворной смесью с противоморозной добавкой) по подготовленной бетонной поверхности.Готовые изделия после отделки тележкой отправляются на склад готовой продукции.
Предприятие-изготовитель должно сопровождать каждую партию изделий паспортом, в котором указываются:
Наименование министерства или ведомства, в систему которого входит предприятие-изготовитель;
Наименование и адрес предприятия-изготовителя;
Номер паспорта и дата его выдачи;
Марка изделия, дата изготовления, приемки ОТК и номер партии;
Проектная марка и отпускная прочность бетона;
Количество изделий в партии;
Номер стандарта.
На плите должны быть четко нанесены следующие маркировочные знаки:
Товарный знак предприятия-изготовителя;
Марка плиты;
Дата изготовления;
Штамп ОТК;
Масса.
Определение необходимой производственной площади
Площадь существующего БСЦ составляет 144 м2.
Производственная площадь арматурного цеха для модернизируемого пролета ориентировочно определяется по формуле:
Sa=ma/Ca, (1.5)
где ma - производство арматурных изделий в год, т;
Са - съем арматурных изделий с 1 м2 площади цеха в год, равный 3 т.
ma=549,85 т
С учетом 3% отходов ma=566,35 т.
Sa=566,35/3=188,78 м2.
Вспомогательная площадь между отделениями арматурного цеха для хранения запаса полуфабрикатов арматурных элементов и размещения в цехе готовых арматурных изделий определяется по формуле:
Sa.з= maза.э/(tрNсмtсм mу.а), (1.6)
где ma - потребность в арматурных изделиях в год, т;
за.э - норма запаса арматурных элементов, ч;
mу.а - усредненная масса арматурных изделий, размещенных на 1 м2 площади цеха, т.
за.э=8 ч; mу.а=0,35 т.[11].
Sа.э.=566,35×8/(255×2×8×0,35) = 3,17 м2.
Площадь для хранения арматурной стали:
Sа.скл= mа за.с/(tрmу.с), (1.7)
где за.с - норма запаса арматурной стали на складе, сут;
mу.с - усредненная масса металла, размещенных на 1 м2 площади склада, т.
за.с=25 суток; mу.с=2,375 т.
Sа.скл=566,35×25/(255×2,375)=23,38 м2.
Вспомогательная площадь для хранения в формовочном цехе запаса арматурных изделий определяется по формуле:
Sпр.а= maзач/(tрNсмtсм mу.а), (1.8)
где зач - норма запаса арматурных элементов в формовочном цехе, зач=4 ч [2].
Sпр.а=566,35×4/(255×2×8×0, 35)=1,59 м2.
Определение потребной численности рабочих и цехового персонала
Штатная ведомость цехов приведена в таблице 1.6.
Таблица 1.6. - Штатная ведомость
№ п/п | Наименование | Число работающих, чел. | Длительность смены, ч. | ||||
1 смена | 2 смена | 3 смена | Всего | ||||
Формовочный цех | |||||||
1 | Производственные рабочие | 46 | 46 | 6 | 98 | 8 | |
Вспомогательные рабочие | 4 | 4 | - | 8 | 8 | ||
ИТР | 3 | 3 | - | 6 | 8 | ||
Арматурный цех | |||||||
2 | Производственные рабочие | 26 | 26 | - | 52 | 8 | |
Вспомогательные рабочие | 1 | 1 | - | 2 | 8 | ||
ИТР | 2 | 1 | - | 3 | 8 | ||
Бетоносмесительный цех | |||||||
3 | Производственные рабочие | 4 | 4 | - | 8 | 8 | |
Вспомогательные рабочие | 5 | 5 | - | 10 | 8 | ||
ИТР | 2 | 1 | - | 3 | 8 | ||
РСУ | |||||||
4 | Вспомогательные рабочие | 15 | - | - | 15 | 8 | |
ИТР | 3 | - | - | 3 | 8 | ||
ЖДУ | |||||||
5 | Вспомогательные рабочие | 5 | 4 | 3 | 12 | 8 | |
ИТР | 4 | 3 | - | 7 | 8 | ||
Лаборатория | |||||||
6 | Вспомогательные рабочие | 3 | 2 | - | 5 | 8 | |
ИТР | 11 | 2 | - | 13 | 8 | ||
АХО, АТУ, охрана | |||||||
7 | Вспомогательные рабочие | 30 | 6 | 6 | 42 | 8 | |
ИТР | 3 | - | - | 3 | 8 | ||
РЭМС, РЭЭС | |||||||
8 | Вспомогательные рабочие | 60 | 14 | - | 74 | 8 | |
ИТР | 6 | 2 | - | 8 | 8 | ||
Заводоуправление | |||||||
9 | ИТР | 47 | - | - | 47 | 8 | |
Итого: производственных рабочих - 158 чел.
Вспомогательных рабочих -168 чел.
ИТР - 93 чел. ИТОГО ПО ЗАВОДУ: 419 чел.
1.4
Организация, планирование и управление предприятием
На предприятии разработана и функционирует система менеджмента качества производства строительно-монтажных работ в соответствии с требованиями СТБ ИСО 90001-2001.
В ОАО «Гомельский ДСК» имеется испытательный комплекс (отдел контроля качества, лаборатория и ОТК на участке КПД). Так же имеется аккредитованная лаборатория по электроизмерениям КИПиА.
При проектировании технологических процессов исходными данными являются: номенклатура изделий; объем выпуска в год; ТУ на изделия, составы бетона, режимы тепловой обработки. Производственный процесс по своей структуре состоит из следующих операций: основные технологические; вспомогательные и общеобслуживающие.
Важнейшими условиями бесперебойного ведения процесса производства является правильная организация работ по ремонту, межремонтному обслуживанию оборудования.
Принимаем централизованную систему организации ремонтной службы, при которой все виды ремонтов и технологический уход за оборудованием осуществляется специальными цеховыми бригадами, находящимися в непосредственном подчинении механика цеха. Состав бригады - 10 человек в каждую смену.
Задачами научной организации труда являются:
Совершенствование методов и приема труда, его разделения и кооперирование путем расчленения операций;
- Улучшение организации рабочих мест и обеспечение благоприятных условий труда;
Повышение квалификации рабочих;
Осуществление мероприятий по совершенствованию нормирования труда.
Работы по внедрению научной организации труда должны производиться в несколько этапов: подготовительно-организационный период; анализ организации труда, составление планов научной организации труда и внедрения мероприятий научной организации труда.
На заводе имеет место коллективная форма организации труда. Особое внимание необходимо уделить улучшению условие труда: снижению уровня шума и вибрации, обеспечению температуры и освещенности и т.д.
Структура управления предприятием следующая. Во главе предприятия стоят гендиректор, главный инженер, которые несут ответственность за работу по изготовлению изделий. Директор осуществляет общее руководство предприятием с помощью ряда служб управления. Заместитель директора выполняет функции административно- хозяйственного управления, производственно-технологического обеспечения и снабжения. Главный инженер - осуществляет общее техническое руководство. Организационно-техническое руководство производством обеспечивают заместители главного инженера. Начальник производственно-технологического отдела и его отдел занимаются вопросами совершенствования внедрения новой технологии изготовления изделий, применения новых материалов и т.п.
2. Архитектурно-строительная часть
Генплан
На генплане решены вопросы наиболее выгодного расположения проектируемых зданий и сооружений в плане протекания функциональных процессов, обеспечения противопожарных и санитарных норм, а также с точки зрения удобства работы.
Предусмотрены уширенные подъезды к основным и вспомогательным помещениям. Все основные помещения находятся во взаимосвязи друг с другом по средствам специальных галерей, конвейеров, трубопроводов и т.д.
На территории завода существует сеть коммуникаций и инженерных сооружений различного назначения. Эти сети связывают в единую систему здания, которые находятся в одном технологическом процессе производства. По ним поставляют сырье в бетоносмесительный участок, арматуру и бетонную смесь в цех формования, производится подача электроэнергии, сжатого воздуха и пара.
На участке предприятия также расположен полигон на котором производят изделия и склад готовой продукции. Также на участке располагаются открытые и закрытые склады.
На территории предусмотрены: скамейки для отдыха возле административно-бытового корпуса, зона для курения.
Также предусмотрена посадка деревьев, кустарников, устройство клумб, обширных газонов. Для озеленения площадки предприятия применяются местные виды древесно-кустарниковых растений; для устройства газонов - местные виды трав. Озеленение территории осуществляется таким образом, чтобы максимально изолировать помещения административно-бытового корпуса от вредных выбросов, которые могут произойти со стороны цехов основного производства и складов сырья и материалов, а также изолировать от выхлопов транспорта.
2.2 Объемно-планировочное решение главного производственного корпуса
Производственный корпус имеет следующие размеры:
длина 156 м;
ширина 96 м;
высота до низа стропильной конструкции 10,8 м;
Производственный корпус имеет четыре пролёта, на которых выпускают различные железобетонные изделия: камни бортовые бетонные и железобетонные, плиты бетонные для тротуаров, перемычки железобетонные, перемычки железобетонные, плиты пенополистирольные теплоизоляционные, элементы входов, плиты лоджий, вентиляционные блоки, плиты покрытия, лестничные ступени, лестничные марши, лестничные площадки, плиты бетонные для тротуаров, панели стеновые внутренние, панели стеновые наружные, ограждение балконов и лоджий железобетонные, плиты перекрытия сплошные из тяжелого бетона, панели стеновые наружные и панели стеновые внутренние и
арматурные изделия, используемые для производства.
Размеры пролетов составляют 156х24 м. К цеху по производству наружно-стеновых панелей примыкают три туннельные камеры размерами 132х6 м.
К зданию также примыкает бетоносмесительный участок. Галерея связывает главный производственный корпус с административно бытовым корпусом.
Промышленное здание имеет простые, лаконичные и четкие композиционные решения. Для объёмно-планировочных и конструктивных решений промздания приняты крупные формы элементов несущих и ограждающих конструкций. Фасад образован чередованием глухих и остекленных участков стены.
Для данного проекта характерно горизонтальное членение фасадов, которое обусловлены применением навесных стен из типовых крупных панелей длиной 6м, а также устройством ленточных световых проёмов, придающих композиции динамичный характер.
Архитектурная выразительность промздания достигнута путём использования таких композиционных средств как цвет и фактура материала. Цветовое решение фасада выполнено в светлых тонах.
Архитектурно-художественная выразительность промышленного здания композиционно увязана и согласована с архитектурно-художественным решением всех сооружений промышленного предприятия. Достигнуто архитектурно-художественное единство - одно из основных требований, предъявляемых к внешнему облику промышленных зданий.
|
|
История развития хранилищ для нефти: Первые склады нефти появились в XVII веке. Они представляли собой землянные ямы-амбара глубиной 4…5 м...
История развития пистолетов-пулеметов: Предпосылкой для возникновения пистолетов-пулеметов послужила давняя тенденция тяготения винтовок...
Поперечные профили набережных и береговой полосы: На городских территориях берегоукрепление проектируют с учетом технических и экономических требований, но особое значение придают эстетическим...
Историки об Елизавете Петровне: Елизавета попала между двумя встречными культурными течениями, воспитывалась среди новых европейских веяний и преданий...
© cyberpedia.su 2017-2024 - Не является автором материалов. Исключительное право сохранено за автором текста.
Если вы не хотите, чтобы данный материал был у нас на сайте, перейдите по ссылке: Нарушение авторских прав. Мы поможем в написании вашей работы!