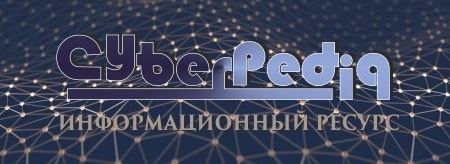
Автоматическое растормаживание колес: Тормозные устройства колес предназначены для уменьшения длины пробега и улучшения маневрирования ВС при...
Кормораздатчик мобильный электрифицированный: схема и процесс работы устройства...
Топ:
Марксистская теория происхождения государства: По мнению Маркса и Энгельса, в основе развития общества, происходящих в нем изменений лежит...
Комплексной системы оценки состояния охраны труда на производственном объекте (КСОТ-П): Цели и задачи Комплексной системы оценки состояния охраны труда и определению факторов рисков по охране труда...
Интересное:
Национальное богатство страны и его составляющие: для оценки элементов национального богатства используются...
Средства для ингаляционного наркоза: Наркоз наступает в результате вдыхания (ингаляции) средств, которое осуществляют или с помощью маски...
Искусственное повышение поверхности территории: Варианты искусственного повышения поверхности территории необходимо выбирать на основе анализа следующих характеристик защищаемой территории...
Дисциплины:
![]() |
![]() |
5.00
из
|
Заказать работу |
|
|
Топлива
Под зарядом твёрдого топлива принято понимать определённое по массе количество твёрдого топлива, имеющее заданную форму, размеры и начальную поверхность горения. Заряд РДТТ – часть ракетного двигателя твёрдого топлива, обеспечивающая требуемый режим газообразования.
Действительно, при постоянной скорости горения u и плотности топлива r m массовый расход РДТТ (u r m S - приход газа с горящей поверхности, равный в стационарном случае расходу через сопло) и, следовательно, его тяга прямо пропорциональны изменению площади горящей поверхности заряда S по мере выгорания его свода.
Заряд твёрдого топлива характеризуется рядом показателей: масса, длина, диаметр наружный, диаметр канала, площадь горящей поверхности, толщина горящего свода, коэффициент объёмного заполнения камеры двигателя топливом. Придавая заряду твёрдого топлива определённую форму, можно программировать зависимость изменения тяги от времени работы РДТТ, то есть обеспечивать требуемый закон газообразования.
Заряды, изготавливаемые формованием неотверждённой топливной массы непосредственно в корпус ракетного двигателя и образующие с корпусом неразъёмное соединение, называются скреплёнными зарядами. К скреплённым зарядам РДТТ относятся также заряды, изготовленные вклеиванием детали из твёрдого ракетного топлива в корпус.
Заряд РДТТ, соединяемый с корпусом специальными конструктивными элементами, допускающими его разборку, называется вкладным зарядом.
Шашка РДТТ – деталь, изготовленная из твёрдого ракетного топлива и используемая в качестве вкладного заряда РДТТ или его составной части.
Секционный заряд РДТТ – скреплённый заряд РДТТ, состоящий из нескольких частей.
|
При проектировании РДТТ выбор топлива и формы заряда является важнейшим этапом, определяющим конечный успех выпуска проекта и отработки РДТТ.
К твёрдым ракетным топливам, применяемым в РДТТ, предъявляются следующие основные требования [17, 8]:
- топливо должно обеспечивать высокое значение энергетических показателей РДТТ с учётом потерь в реальной конструкции, при этом продукты его сгорания должны иметь наименьшие температуру и окислительный потенциал и не быть токсичными;
- топливо должно обладать механическими характеристиками, обеспечивающими минимальные габариты двигателя, необходимую прочность заряда, а также длительное хранение и эксплуатацию снаряженного РДТТ без существенного изменения геометрических, баллистических и энергетических характеристик;
- топливо должно обеспечивать возможность регулирования скорости горения в широком диапазоне значений без существенного изменения энергетических и механических свойств, при этом скорость горения должна иметь слабую зависимость от начальной температуры и требуемую зависимость от давления;
- топливо должно быть взрывобезопасным в процессе изготовления и при снаряжении двигателей; механические воздействия при сборке двигателя и эксплуатации ракеты не должны вызывать возгорания заряда;
- технологические свойства топлива должны позволять применять наиболее передовые и экономичные способы его изготовления и снаряжения двигателей с хорошей воспроизводимостью всех характеристик топлива в заряде.
Как следует из изложенного, к твёрдым топливам предъявляются многочисленные и разнообразные требования, удовлетворить которым в полном объёме практически невозможно. В этой связи при назначении требований к топливу выделяются приоритетные характеристики (например, удельный импульс тяги, плотность), а остальные – на уровне допустимых значений в соответствии с назначением, условиями эксплуатации и боевого применения ракеты.
|
Сформулируем основные требования к заряду твёрдого топлива. Форма заряда должна обеспечивать максимальное заполнение корпуса двигателя топливом при условии допустимых скоростей газового потока в камере сгорания для исключения эрозионного горения топлива. Тепловая защита внутренней поверхности корпуса двигателя от воздействия продуктов сгорания должна обеспечиваться, в основном, самим топливом (сводом заряда). В конце горения заряда количество остатков топлива, догорающих на нерасчётном режиме (при низком давлении в камере), должно быть минимальным. Кроме того, заряд должен обеспечить:
- требуемый характер изменения давления в камере сгорания;
- нормальное функционирование при запуске и стабильное горение на основном режиме работы двигателя;
- заданное время работы двигателя на основном режиме и участке спада давления в конце работы двигателя;
- допустимые отклонения площади горящей поверхности и времени работы двигателя от номинальных значений.
Заряд должен быть технологичным в изготовлении и иметь достаточную механическую прочность в течение гарантийного срока и назначенного срока службы ракеты.
Важное значение имеет обеспечение необходимой прочности заряда при хранении и работе двигателя. В случае скреплённых зарядов требования к механическим характеристикам топлива (прочность, относительная деформация, модуль упругости) весьма высокие, особенно для РДТТ, применяемых в широком диапазоне температур. Это обусловлено деформацией поверхности центрального канала заряда и температурными напряжениями, возникающими на границе корпус–заряд (смесевые топлива имеют коэффициент линейного расширения на порядок выше, чем материал корпуса). В узком диапазоне положительных температур требования к механическим характеристикам топлив снижаются [36].
Большинство из вышеперечисленных требований к заряду противоречиво. Из всех возможных вариантов конструктивного решения выбирается такой заряд, который бы наиболее полно отвечал заданным требованиям. Ввиду неоднозначности решения задача проектирования заряда осуществляется в два этапа.
На первом этапе в соответствии с обликом РДТТ устанавливается допустимая масса заряда, время работы двигателя, давление в камере сгорания, накладываются ограничения на его основные габаритные размеры. Учитывая перечисленные условия, задаваясь формой заряда и свойствами твёрдого топлива, можно определить в первом приближении основные размеры заряда: максимальный горящий свод, наружный диаметр, длину и диаметр канала.
|
После определения основных геометрических характеристик, задаваясь марками твёрдого топлива, варьируя геометрическими размерами заряда и величиной скорости горения топлива, подбирают такую комбинацию параметров, которая удовлетворяет условию максимального заполнения камеры сгорания.
Получив несколько вариантов зарядов с разными марками твёрдого топлива, на втором этапе проводят их сравнительный технико-экономический анализ и отбирают те конструктивные решения по заряду и двигателю, которые обеспечивают требуемый закон изменения тяги, допустимые габаритные размеры, необходимое время работы, заданную надёжность в установленных условиях эксплуатации и простоту изготовления при минимальной стоимости [17].
Наиболее распространённой формой камеры сгорания, которая существенно влияет на выбор конструкции заряда, у большинства РДТТ является цилиндрическая со сфероидальными или эллипсоидными днищами, хотя в отдельных случаях камера сгорания может иметь и другую форму, например, сферическую или коническую.
Конструктивно корпус камеры сгорания может выполняться неразъёмным или разъёмным, состоящим из нескольких секций. Это определяется массово-габаритными характеристиками РДТТ [8].
Для большинства маршевых РДТТ требуемый закон изменения тяги по времени близок к постоянному. В некоторых случаях для первых ступеней необходима дегрессивная диаграмма тяги (особенности преодоления ракетой в процессе полёта плотных слоёв атмосферы), а также может быть необходимым длительный спад, определяемый условиями разделения ступеней ракеты при её полёте.
Основным требованиям, предъявляемым к зарядам твёрдого топлива, могут удовлетворять несколько их конструктивных форм, которые делятся: на моноблочные, многошашечные, секционные и составные [8].
По форме горящей поверхности заряды могут быть: без канала; с одним каналом; многоканальные; цилиндрические; конические; цилиндроконические; овальные; сферические; тороидальные и др.
|
Каналы у зарядов твёрдого топлива по форме могут быть: звёздообразные, цилиндрические, щелевые, цилиндрические с кольцевой проточкой и комбинированные.
Рассмотрим основные особенности некоторых из указанных типов зарядов, часто применяемых на практике (рисунок 5.1 [8]).
Наиболее простой формой обладает заряд торцевого горения (рисунок 5.1а). Они бывают как вкладными, так и прочно скреплёнными со стенками камеры сгорания РДТТ.
Первые в практике отечественного ракетостроения торцевые заряды, прочно скреплённые с корпусом, были разработаны в ФНПЦ «АЛТАЙ» для двигателей разведения разделяющихся головных частей межконтинентальных баллистических ракет на жидком топливе 15А14, 15А15, 15А16 [28]. Для снижения температурных напряжений в зарядах корпуса этих двигателей имели оригинальную схему раскрепляющих манжет.
Наружная поверхность и один из торцов вкладного заряда бронируются специальным составом. Торцевой заряд обеспечивает максимальное заполнение камеры сгорания топливом (К v → 1).
а) торцевого горения, скреплённый с корпусом; б) с цилиндрическим каналом (трубчатый), вкладной; в) телескопический; г) канально-щелевой; д) цилиндроконический; е) с цилиндрическим каналом
и наклонной кольцевой проточкой, моноблочный;
ж) со звёздообразным каналом; з) секционный
Рисунок 5.1 - Формы зарядов твёрдого топлива
Торцевой заряд позволяет получить любой из известных законов изменения поверхности. Для получения увеличивающейся или уменьшающейся поверхности горения достаточно изготовить заряды с конической формой и нанести бронирующее покрытие по наружной поверхности и одному из торцов.
Ступенчатое горение можно достигнуть двумя способами: изготовлением двухступенчатого заряда (с двумя различными диаметрами) или заряда из двух последовательно расположенных топлив с разными скоростями горения.
Чтобы устранить смещение центра масс во время работы двигателя, торцевой заряд иногда заменяют двумя полузарядами торцевого горения, обращёнными горящими торцами навстречу друг другу и размещёнными в одной камере сгорания РДТТ. При этом необходимо учитывать возможность появления неустойчивости горения при определённых геометрических соотношениях, которые принимает газовая полость двигателя, если собственные частоты полости окажутся близкими к резонансным частотам зоны горения выбранного состава топлива [36].
Стремление сочетать высокую плотность заряжания с более высокими значениями тяги привело к проектным разработкам торцевого заряда с теплопроводящими элементами (проволочками). При изготовлении такого заряда топливная масса заливается в корпус двигателя, в котором предварительно параллельно продольной оси двигателя с определённой плотностью по поперечному сечению натягиваются проволочки из металлов с большим коэффициентом теплопроводности. По мере выгорания топлива концы проволочек оказываются над поверхностью горения в зоне горячих продуктов реакции. Скорость распространения тепла вдоль проволочки превышает скорость горения топлива, часть тепла от проволочки переходит к прилегающему топливу, повышается его температура, и как следствие, увеличивается местная скорость горения [36].
|
Особенность торцевого заряда состоит в том, что небольшая величина площади горящей поверхности не позволяет создавать с ним РДТТ большой тяги. Поэтому их используют в газогенераторах и двигателях с малой тягой. Кроме того, применение торцевого заряда требует нанесения на стенки камеры сгорания усиленного теплозащитного покрытия (ТЗП), так как значительная часть внутренней поверхности камеры продолжительное время омывается высокотемпературными продуктами сгорания.
Заряд с цилиндрическим каналом (трубчатый заряд) (рису-
нок 5.1б) получил наибольшее распространение из-за простоты формы и освоенности технологии изготовления. Поверхность горения трубчатого заряда представляет собой поверхность полого цилиндра. Уменьшение площади поверхности горения заряда по мере его выгорания происходит вследствие уменьшения длины заряда и площади торцов. Дегрессивность горения рассматриваемого заряда тем меньше, чем длиннее заряд. Трубчатый заряд является основным элементом большинства используемых в настоящее время многошашечных зарядов РДТТ. Он дает возможность получить любую зависимость изменения поверхности горения. В частности, постоянную поверхность горения можно получить путём нанесения бронирующего покрытия на торцы заряда. Область применения данной формы заряда ограничена величиной допустимой относительной длины от 2,5 до 4.
Заряды такой конструкции применяются в двигателях, работающих несколько десятков секунд. Они могут быть как прочно скреплёнными со стенками камеры сгорания, так и вкладными. Для последних возрастает масса конструкции двигателя из-за большой массы ТЗП или бронирующего покрытия и использования специальных элементов для удержания заряда в камере двигателя. Коэффициент объёмного заполнения двигателя с таким зарядом может достигать значения 0,84. Он зависит также от диаметра канала шашек [8].
При плотном размещении шашек в камере получаются следующие соотношения наружного диаметра шашки d и внутреннего диаметра камеры сгорания D [36]:
- при 6–7 шашках d = 0,33 D;
- при 5 шашках d = 0,37 D;
- при 4 шашках d = 0,415 D;
- при 3 шашках d = 0,464 D.
Разновидностью трубчатого заряда является телескопический заряд (рисунок 5.1в). Это многошашечный заряд с концентрическим расположением частей - внешняя часть заряда имеет канал, внутри которого располагается бесканальная часть. Горение заряда организовано по двум внутренним цилиндрическим поверхностям. В этом случае обеспечивается постоянство горящей поверхности. Внешняя часть может выполняться как вкладной, так и прочно скреплённой, которой обеспечивается тепловая защита стенок камеры двигателя.
Особую трудность представляет крепление центральной части телескопического заряда с обеспечением её концентрического расположения и сохранения до конца горения заряда. Возможны следующие способы крепления внутренней части заряда: с помощью выступов или сухарей, расположенных между шашками, с помощью центрального стержня или при помощи решётки. Коэффициент объёмного заполнения камеры двигателя с телескопическим зарядом может достигать значения 0,84 [8].
Канально-щелевой заряд (рисунок 5.1г) имеет поверхность горения, образованную каналом и щелями. Достоинством этого типа зарядов является возможность обеспечить любой из законов выгорания (нейтральный, прогрессивный или дегрессивный). Канальная часть заряда горит с увеличением поверхности горения, щелевая - с уменьшением. Выбором количества и размеров щелей обеспечивается необходимый закон газообразования и изменения тяги.
Широкое распространение на двигателях различного назначения канально-щелевой заряд получил вследствие своей универсальности и технологичности, в частности при изготовлении вкладных зарядов из баллиститных топлив. Полученный прессованием трубчатый заряд бронируется по наружной поверхности, после чего с торца пропиливаются или фрезеруются щели на нужную глубину в необходимом количестве. В условиях применения смесевых топлив и скреплённых зарядов канально-щелевой заряд не утратил своего значения. Например, большинство зарядов маршевых РДТТ боевых межконтинентальных ракет США имеют конструкцию канально-щелевого типа.
В зависимости от условий эксплуатации заряд может быть установлен в камере сгорания щелями, обращенными в сторону сопла или в сторону переднего днища. Первый способ установки заряда предпочтительней, так как позволяет повысить коэффициент объёмного заполнения двигателя до значений 0,89–0,92 в зависимости от относительной длины заряда. Наличие щелей у заднего днища формирует неоднородный гетерогенный поток продуктов сгорания, и для сопел с разгорающимся критическим сечением из армированных пластмасс возможен локальный повышенный унос материалов сопла.
Недостатки таких зарядов: наличие концентраторов напряжений в основаниях щелей, возможность эрозионного горения в них и необходимость нанесения дополнительного слоя ТЗП на стенку камеры сгорания в районе щелей. Ограничение высоты щелей в радиальном направлении позволяет уменьшить время воздействия продуктов сгорания на стенки корпуса РДТТ.
Цилиндроконический заряд (рисунок 5.1д) также относится к зарядам канального горения. Он выполняется прочно скреплённым с корпусом. В случае использования корпуса со съемными днищами заряд состоит из двух частей. Увеличение во время работы двигателя поверхности горения цилиндрического канала компенсируется уменьшением двух конических поверхностей. Поэтому такой заряд иногда называют цилиндрическим зарядом с коническим компенсатором. Варьируя углом наклона и длиной компенсатора, можно обеспечивать необходимый закон изменения тяги. Недостаток такого заряда - необходимость нанесения усиленного слоя ТЗП на внутреннюю поверхность камеры сгорания в районе стыка двух частей заряда [8].
Близким по форме к цилиндроконическому заряду является моноблочный заряд с цилиндрическим каналом и кольцевой проточкой (зонтиком) (рисунок 5.1е). Изменяя угол наклона и длину проточки, можно обеспечить необходимый закон изменения тяги. Создание такого заряда связано с технологическими сложностями по оснастке при его изготовлении. Коэффициент объёмного заполнения цилиндроконического заряда и заряда с кольцевой проточкой может достигать значения 0,92 [8].
В двигателях большой тяги используют заряды со звёздообразным каналом (рисунок 5.1ж). Поверхность горения этого заряда образована внутренним каналом, имеющим поперечное сечение в форме многолучевой звёзды. Применение этих зарядов позволяет обеспечивать заданный закон изменения поверхности горения при любых относительных длинах. Заряды со звёздообразным каналом требуют меньшей теплозащиты корпуса двигателя, чем, например, щелевые. Коэффициент объёмного заполнения двигателя с таким зарядом достигает значения 0,91–0,92.
Однако при прочих равных условиях время работы двигателя с таким зарядом меньше, чем у двигателей с щелевыми и бесщелевыми зарядами. Это объясняется тем, что при одинаковых наружных диаметрах зарядов максимальный свод у заряда со звёздообразным каналом меньше. По сравнению с канально-щелевым зарядом звёздообразный заряд даёт возможность в заданных габаритах получить более высокое значение площади поверхности горения, но меньшее значение отношения толщины свода к диаметру заряда. Его основным недостатком является то, что в конце его работы образуются дегрессивные догорающие остатки, увеличивающие разброс внутрибаллистических характеристик и снижающие полный импульс тяги двигателя.
Остатки топлива, догорающие при низких давлениях в рассматриваемом заряде, составляют 6–10 % от всей массы заряда. Для устранения этого недостатка в корпус двигателя перед заливкой топлива можно разместить вставки из материала с низкой плотностью (например, пенопласта), выполненные по форме догорающих остатков топлива. Он может быть также частично устранен применением составного заряда из топлив с различной скоростью горения. Сложность создания такого заряда связана с необходимостью последовательной заливки и полимеризации топлив [36].
Секционные заряды могут совмещать в себе элементы конструкций как бесканальных, так и канальных зарядов, они состоят из нескольких частей (секций) (рисунок 5.1з). Поэтому достоинства и недостатки, присущие указанным типам зарядов, относятся и к секционным. Двигатели с секционными зарядами имеют на стенках отдельных частей участки теплозащитных покрытий, а в случае вкладных зарядов - дополнительные опорные стаканы и узлы уплотнения для создания застойной зоны. Принцип секционирования целесообразно применять для мощных крупногабаритных РДТТ, главным образом из соображений обеспечения их производства и транспортировок [8].
В особых случаях могут применяться сферические заряды, то есть когда требуется создать двигатель с минимальной массой конструкции и длиной. Для увеличения площади горения на поверхности заряда могут быть выполнены концентрические пропилы. Корпус сферического РДТТ представляет собой по форме либо сферу, либо две полусферы, соединенные короткой цилиндрической частью.
Основное преимущество таких двигателей основывается на том, что сфера при заданном объёме (для двигателя объём эквивалентен запасу топлива) имеет минимальную площадь ограничивающей поверхности (для двигателя - минимальная масса корпуса). Далее по условиям прочности и устойчивости сферическая оболочка является оптимальной. Всё это позволяет снизить массу корпуса. Сферические заряды нашли применение в зарубежной космической технике [36].
В качестве примера заряда с развитой поверхностью горения и малым временем горения можно привести рулонный заряд [36]. Заряд может представлять собой две полосы из смесевого топлива, наклеенные по обе стороны металлической ленты толщиной 0,15 мм.
Полученная таким образом трёхслойная лента сворачивается в спираль вместе со специальной обоймой, которая обеспечивает требуемый зазор между витками и необходимую жёсткость всей конструкции. Заряд вкладывается в камеру, обойма заряда жёстко фиксируется в корпусе двигателя крышкой. Лента из смесевого топлива может быть изготовлена по технологии механического строгания, аналогичной для производства пластмассовых листов из цилиндрических заготовок.
5.2 Особенности работы торцевого заряда,
прочно скреплённого с корпусом
Вернёмся к обсуждению торцевых зарядов. Для вышеупомянутых зарядов торцевого горения (разработанных в ФНПЦ «АЛТАЙ»), прочно скреплённых с корпусом РДТТ в процессе формования, использовались созданные под научным руководством профессора В.Ф. Комарова [21] низкомодульные высокодеформативные топлива.
Как показала практика отработки таких зарядов в начале 70-х годов прошлого века, в заряде возникает радиальное поле скоростей горения. Основные причины этого связаны с миграцией пластификатора топлива в защитно-крепящий слой корпуса из пристеночного слоя топлива, приводящей к избытку окислителя в этом слое и увеличению местной скорости горения. Также имеет место влияние напряжённо-деформированного состояния на границе скрепления заряда с корпусом, возникающего при действии внутрикамерного давления во время работы двигателя, на местную скорость горения, которая пропорциональна второму инварианту девиатора тензора деформаций. Как следствие, слои топлива, прилегающие к корпусу, имеют скорость горения, превышающую скорость горения основной массы топлива. Это приводит в процессе работы двигателя к вырождению начальной поверхности горения в поверхность, близкую к конической.
Факт образования конической поверхности горения из начального плоского торца установлен экспериментально при гашении натурных двигателей во время их работы (рисунок 5.2).
Рисунок 5.2 – Схема развития плоской начальной поверхности горения заряда в коническую
Гашение осуществлялось следующим образом. На металлическом корпусе двигателя до испытания наносился концентратор напряжений в виде тангенциальной риски, затем по периметру этой риски наматывался в несколько витков детонирующий шнур. При работе двигателя по команде с пульта управления испытанием этот шнур инициировался и отсекал часть корпуса с сопловым блоком, которая под действием внутрикамерного давления отлетала в сторону, а на поверхность горения заряда дистанционно подавался интенсивный поток воды.
Водяная пушка заранее монтировалась на огневом дворе и настраивалась перед испытанием. Чтобы пушка не попала в истекающую струю продуктов сгорания, она устанавливалась под углом 25–30 градусов к продольной оси двигателя, установленного в специальном стапеле, препятствующем возможным перемещениям двигателя при срабатывании детонирующего шнура.
Угол наклона a образующей конуса к образующей корпуса определяется соотношением:
(5.1)
где U – скорость горения основной массы топлива;
U прист – скорость горения топлива в тонком пристеночном слое.
При аппроксимации U и U прист общепринятым степенным законом скорости горения выражение (5.1) можно записать так:
(5.2)
где U 1 и – единичные скорости горения основной массы топлива и пристеночного слоя соответственно;
ν и νприст – показатели степени в законе скорости горения.
Из (5.2) следует, что угол наклона образующей конуса к образующей корпуса при ν ¹ νприст зависит от уровня давления в камере.
(5.3)
где .
Зависимость (5.3) экспериментально подтверждена испытаниями зарядов одной партии, то есть с одинаковой скоростью горения, при разных уровнях давления, а также работами на модельных образцах с последовательным гашением в процессе их горения и обмером получаемой поверхности. Замеренные в процессе эксперимента углы формирующихся конусов зависели от уровня давления, а по результатам обработки экспериментальных данных по испытаниям образцов получено, что νприст больше ν топлива.
Общеизвестную формулу Бори для расчёта стационарного давления в камере РДТТ
, (5.4)
где S – поверхность горения заряда;
r т – плотность топлива;
А – коэффициент истечения;
s кр – площадь критического сечения сопла,
можно преобразовать следующим образом.
Поскольку при достижении стационарного давления начальная поверхность горения произвольной формы вырождается в конус, то для заряда цилиндрической формы боковая поверхность образовавшегося конуса запишется в виде
(5.5)
где r – радиус заряда.
Подставляя (5.2) и (5.5) в уравнение сохранения массы
,
получим:
(5.6)
На основе (5.4) построена оценка разбросов баллистических параметров РДТТ. В работе [33] для разбросов давления приведено выражение
(5.7)
где - составляющие разбросов.
Применительно к рассматриваемому случаю (5.7) с учетом (5.6) можно записать:
(5.8)
Из сравнения (5.7) и (5.8) следует, что для торцевого заряда (во всяком случае скреплённого с корпусом) неизбежно получение большего разброса характеристик по сравнению с зарядом канального типа, так как νприст больше ν. Такой вывод подтверждается практикой работ с натурными двигателями.
Для торцевого заряда на характер кривой давления оказывают влияние пограничные эффекты в течение всего времени работы двигателя. Для канальных зарядов – только в конце работы, к моменту выхода фронта горения на корпус. Разбросы характеристик с этого момента времени, как правило, возрастают.
Формула (5.6) по форме записи аналогична формуле Бори и представляет её частный случай для торцевого заряда при вырождении начальной поверхности горения в коническую. Она была получена автором учебного пособия в 1977 г. и опубликована в журнале «Вопросы специального машиностроения», серия 2, выпуск 13(117) в 1979 году. Формула справедлива, если толщина пристеночного слоя топлива много меньше радиуса заряда, что имеет место на практике. Коллеги по работе называли её формулой Бори-Яскина.
Отметим, что аналогичный по математической форме записи результат приведён в книге [36], вышедшей в 1987 г., для стационарного давления в камере РДТТ с торцевым зарядом с увеличенной скоростью распространения фронта горения по оси заряда за счёт размещения на ней теплопроводных металлических нитей. По окончании переходного процесса поверхность горения заряда принимает форму конуса. Но в этом случае конусная поверхность обращена вершиной к переднему днищу двигателя. Для случая увеличенной скорости горения на границе с корпусом образующаяся коническая поверхность горящего торцевого заряда обращена вершиной к соплу ракетного двигателя.
Для получения нейтральной зависимости площади поверхности горения торцевого заряда с увеличенной скоростью горения на границе скрепления с корпусом РДТТ от толщины сгоревшего свода (следовательно и нейтральной диаграммы «давление-время») начальная форма поверхности горения заряда может быть выбрана не в виде плоского торца, а сразу выполнена конической с вершиной, обращённой к соплу ракетного двигателя. Угол наклона образующей начальной конической поверхности заряда к конструктивной базовой оси двигателя выбирается по соотношению (5.3). Величина этого угла должна быть определена экспериментально на модельных образцах.
Бронирующие покрытия
Регулирование изменения поверхности горения заряда может быть осуществлено бронирующими покрытиями. Они наносятся на те поверхности заряда твёрдого топлива, горение которых исключается из процесса горения в течение некоторого времени работы двигателя. Для бронирующих покрытий могут быть сформулированы следующие требования:
- хорошая адгезия с топливным зарядом;
- химическая и физическая стабильность в течение всего срока хранения и эксплуатации заряда;
- низкая теплопроводность для снижения теплового потока в топливо при работе двигателя;
- малая плотность для снижения пассивной массы конструкции двигателя;
- технологичность нанесения бронирующего покрытия на поверхность заряда твёрдого топлива в производственных условиях;
- недефицитность исходного сырья бронирующего покрытия и вспомогательных материалов, используемых в технологическом процессе его нанесения на заряд.
В зависимости от типа топлива выбирается тот или иной состав бронирующего покрытия. Для вкладных зарядов твёрдого топлива применяют смолы (например, эпоксидную) с наполнителем из хлопчатобумажных нитей. Смоченные в смоле нити наматываются на цилиндрическую поверхность заряда твёрдого топлива. На торцевые поверхности наносятся полимерные бронирующие покрытия.
Для смесевых твёрдых топлив в качестве бронирующих покрытий обычно применяют тот же каучук, какой входит в состав заряда в качестве полимерного горючего – связующего. Наполнителем может служить газовая сажа. Толщина бронирующего покрытия выбирается исходя из условия нагрева поверхностного слоя топлива, находящегося в контакте с бронирующим покрытием. Температура нагрева не должна превышать температуры вспышки топлива.
Исходя из допущений, что унос бронирующего покрытия за всё время работы двигателя отсутствует, а количество тепла, поглощённого топливом, мало по сравнению с количеством тепла, поглощённым бронирующим покрытием, рекомендуется следующая зависимость для приближённого определения толщины бронирующего покрытия [3]:
,
где l бп, с бп, r бп - соответственно коэффициент теплопроводности, теплоёмкости и плотность;
Тг - температура продуктов сгорания;
Т 0 - начальная температура заряда и покрытия;
Тдоп -заданная допустимая температура топлива в месте контакта с бронировкой;
t - время работы двигателя.
|
|
Типы сооружений для обработки осадков: Септиками называются сооружения, в которых одновременно происходят осветление сточной жидкости...
Организация стока поверхностных вод: Наибольшее количество влаги на земном шаре испаряется с поверхности морей и океанов (88‰)...
История развития пистолетов-пулеметов: Предпосылкой для возникновения пистолетов-пулеметов послужила давняя тенденция тяготения винтовок...
Своеобразие русской архитектуры: Основной материал – дерево – быстрота постройки, но недолговечность и необходимость деления...
© cyberpedia.su 2017-2024 - Не является автором материалов. Исключительное право сохранено за автором текста.
Если вы не хотите, чтобы данный материал был у нас на сайте, перейдите по ссылке: Нарушение авторских прав. Мы поможем в написании вашей работы!