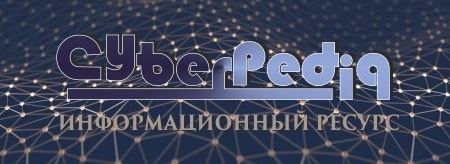
Эмиссия газов от очистных сооружений канализации: В последние годы внимание мирового сообщества сосредоточено на экологических проблемах...
История развития хранилищ для нефти: Первые склады нефти появились в XVII веке. Они представляли собой землянные ямы-амбара глубиной 4…5 м...
Топ:
Комплексной системы оценки состояния охраны труда на производственном объекте (КСОТ-П): Цели и задачи Комплексной системы оценки состояния охраны труда и определению факторов рисков по охране труда...
Особенности труда и отдыха в условиях низких температур: К работам при низких температурах на открытом воздухе и в не отапливаемых помещениях допускаются лица не моложе 18 лет, прошедшие...
Интересное:
Распространение рака на другие отдаленные от желудка органы: Характерных симптомов рака желудка не существует. Выраженные симптомы появляются, когда опухоль...
Аура как энергетическое поле: многослойную ауру человека можно представить себе подобным...
Подходы к решению темы фильма: Существует три основных типа исторического фильма, имеющих между собой много общего...
Дисциплины:
![]() |
![]() |
5.00
из
|
Заказать работу |
|
|
В РДТТ вспомогательного назначения могут быть использованы металлические, стеклопластиковые (или органопластиковые) и комбинированные (металлическая обечайка, усиленная стеклопластиковой или органопластиковой оплёткой) корпуса. Однако наиболее широко в таких РДТТ (особенно импульсных) применяют металлические корпуса. Это объясняется сравнительно небольшими размерами двигателей, высоким уровнем внутрикамерного давления, необходимостью располагать место крепления двигателя в области обечайки [1].
РДТТ вспомогательного назначения часто располагают в местах, где они подвергаются повышенному воздействию внешних тепловых потоков, что обусловливает применение металлических корпусов, выдерживающих более высокие температуры (до 300 °С - для высокопрочных титановых сплавов).
Высокомодульные (с высокой удельной жёсткостью) алюминиевые сплавы целесообразно применять для малогабаритных корпусов, нагруженных внешним избыточным давлением, при крупносерийном и массовом производстве и при отсутствии жёстких ограничений по массе конструкции [1].
Сравнительный анализ показывает, что алюминиевые сплавы уступают сталям и титановым сплавам по удельной прочности, но приближаются к ним по удельной жёсткости.
Высокопрочные титановые сплавы и стали нашли широкое применение в производстве РДТТ. Применение их требует специальных термообработок соединений и целиком изделий после сварки и высокую технологическую культуру. Даже незначительные нарушения процессов изготовления и контроля могут привести к снижению конструктивной прочности.
Основным недостатком высокопрочных сталей является повышенная чувствительность к концентраторам напряжений. Склонность высокопрочных сталей к разрушениям от концентраторов напряжений различна в зависимости от направления надреза относительно проката листов. Концентраторы напряжений на высокопрочных сталях по разному проявляют себя в зависимости от толщины материала. Чем толще испытуемый образец, тем в большей степени проявляется наличие концентратора напряжений. Для уменьшения чувствительности высокопрочных сталей к концентраторам используют вакуумно-дуговую выплавку, электрошлаковый переплав и др. [3].
|
Обечайки из высокопрочных титановых сплавов менее технологичны, чем стальные; это затрудняет их получение с точными размерами по внутренней поверхности. В тех случаях, когда введены жёсткие ограничения по разбросу масс, целесообразно использовать стальные обечайки [1].
Если при анализе технического задания (ТЗ) не выявлено условий, ограничивающих применение корпуса того или иного типа, конструкцию его следует выбирать на основе прямого проектирования и анализа габаритно-массовых характеристик каждого из вариантов.
Для класса вспомогательных РДТТ с большим временем работы характерной является конструкция корпуса двигателя крена, представленная на рисунке 2.19 [1].
К конической обечайке из титанового сплава, получаемой раскаткой из листосварной заготовки, с одной стороны приварено штампованное из титанового сплава эллиптическое днище с цилиндрическим хвостовиком для крепления двигателя, а с другой стороны приварен шпангоут для стыковки с сопловым днищем.
На рисунке 2.20 представлена конструкция корпуса импульсного двигателя отделения [1]. К обечайке из высокопрочной стали типа ЭП, получаемой сваркой из листа и последующей раскаткой, приварены с двух сторон шпангоуты из этой же стали, предназначенные для стыковки с сопловыми днищами. Шпангоуты имеют цилиндрические участки для крепления двигателя.
1 - днище; 2 - коническая обечайка; 3 - теплозащитное покрытие;
4 - манжета (бронирующий чехол); 5 - стыковочный шпангоут;
6 - крепление манжеты к ТЗП
|
Рисунок 2.19 - Конструкция корпуса двигателя крена
1 - стыковочный шпангоут; 2 - обечайка корпуса; 3 - теплозащитное покрытие; 4 - эластичный клин
Рисунок 2.20 - Конструкция корпуса двигателя отделения
Иногда в РДТТ вспомогательного назначения применяют корпуса многоразового использования. В этих случаях при конструировании корпуса необходимо предусматривать уменьшение его толщины при ремонтно-восстановительных работах (например, при пескоструйной обработке корпуса).
При конструкторской разработке вспомогательных РДТТ необходимо обеспечить минимальный разброс значений объёма корпуса и контроля этого объёма для снижения разброса массы заряда.
Днища вспомогательных РДТТ представляют собой штампованные или штампосварные конструкции, в которых посадочные поверхности подвергают механической обработке.
Сопловые днища со сложным пространственным расположением поверхностей часто выполняют литьём из стали или литейных титановых сплавов [1].
Характерным, например, является сопловое днище двигателя крена. Оно выполняется литьём из титанового сплава с последующей механической обработкой посадочных поверхностей. При механической обработке стыковочных поверхностей днищ возможно вскрытие мелких пор, которые не влияют на прочность днища, но могут явиться причиной разгерметизации, если находятся на уплотнительных поверхностях детали.
В некоторых случаях вскрытые дефекты можно исправить (заваркой, заполнением специальными пастами, припоями и т.п.) [1].
Импульсные двигатели с малым временем работы иногда вообще не имеют внутреннего ТЗП, но в каждом подобном случае такая конструктивная схема должна быть тщательно обоснована детальным моделированием.
2.4 Сборка корпуса РДТТ с передней крышкой
и сопловым блоком
Разъёмные соединения
В полярных отверстиях силовой оболочки современных корпусов типа кокона устанавливаются металлические фланцы, связанные с композиционным материалом адгезионным швом (клеевое соединение). Прежде чем перейти к разъёмным соединениям, коротко остановимся на клеевых соединениях. Клеи нашли широкое применение в РДТТ, в том числе для крепления теплозащитных материалов и эрозионностойких элементов конструкций к корпусу, днищам, соплам, воспламенителям. В конструкции РДТТ из всех видов соединений клеевые имеют наибольшее распространение. Основным требованием, предъявляемым к конструкции клеевого соединения, является обеспечение совпадения по направлению максимальных рабочих напряжений с максимальной прочностью клеевого соединения. Склеивание явилось наилучшим, а в некоторых случаях единственным способом соединения элементов конструкции, выполненных из композиционных материалов, с металлами. Крепление с помощью заклёпок, винтов или болтов не может быть использовано, так как сгорание металлических элементов крепления приводит к аварии из-за локального интенсивного прогрева. Поэтому все виды элементов конструкции из композитов и теплозащитных покрытий крепятся к металлическим силовым элементам только клеями [3].
|
Перейдём к разъёмным соединениям. В процессе изготовления РДТТ с использованием металлических фланцев, установленных на корпусе при его намотке, проводится сборка корпуса (после его снаряжения твёрдым топливом) с передней крышкой и сопловым блоком.
В РДТТ нашли применение фланцевые, резьбовые, прутковые, клиновые и другие разъёмные соединения. На начальном этапе разработки крупногабаритных двигателей применялись фланцевые соединения (болтовые, шпилечные) в связи с широким их использованием в общем машиностроении. Эти соединения достаточно просты по конструкции и обеспечивают надёжную работу стыка при больших давлениях, однако они имеют ряд существенных недостатков. Фланцевые соединения характеризуются значительной массой по сравнению с другими соединениями, а для обеспечения прочности и герметичности соединения необходимо большое число крепёжных деталей со строго регламентированной моментной затяжкой их при сборке. К качеству изготовления крепёжных деталей предъявляют особые требования по обеспечению механических характеристик и уменьшению различного рода концентраторов напряжений. Всё это усложняет процесс их изготовления и удлиняет сборку, требуется специальный контроль и, следовательно, ухудшается технологичность конструкции и эксплуатационные характеристики соединении [1, 3].
|
Болтовые соединения, кроме того, характеризуются увеличением габаритных размеров вследствие выступающих над внешними обводами двигателя фланцев. По сравнению с болтовыми шпилечное соединение имеет меньшие массу и габаритные размеры, однако его недостатком является необходимость открытия глухих резьбовых отверстий в высокопрочном материале фланцев. Нарезание резьбы в таком материале весьма трудоёмкий процесс, так как требуются специальные меры по исключению увода и перекоса метчиков [1].
Резьбовые соединения широко используются в РДТТ небольших габаритов. Они просты в изготовлении, быстро собираются и разбираются. В крупногабаритных РДТТ применение резьбовых соединений нецелесообразно из-за сложности нарезания резьбы в высокопрочных и маложёстких шпангоутах, трудности проведения сборки и разборки соединения, особенно после нагружения его внутренним давлением.
Для стыковки элементов крупногабаритных РДТТ могут применяться прутковые соединения. Большинство этих соединений содержит концентрично установленные один в другом шпангоуты соединяемых элементов конструкции с кольцевыми проточками, образующими при стыковке шпангоутов кольцевой ручей, в который через окна в наружном шпангоуте заводится крепящий элемент: гибкий стержень (шпага), рейка или шпонка. Прутковые соединения удовлетворяют требованиям центрирования элементов и их взаимозаменяемости, однако при этом требуются довольно жёсткие допуски для исключения зазоров и специальные меры по обеспечению гарантированной герметичности стыка.
В шпоночном соединении в кольцевой паз, образованный стыкующимися элементами, заводятся шпонки прямоугольного или квадратного сечения и длиной, позволяющей им свободно перемещаться вдоль кольцевого паза. Для сборки и разборки соединения достаточно иметь в наружном шпангоуте два окна. Перед установкой шпонок необходимо обеспечить равномерный прижим шпангоутов по всему периметру.
Отличие клинового соединения от шпажного, реечного и шпоночного заключается в том, что в качестве крепящего элемента в кольцевой паз между шпангоутами через окно в наружном шпангоуте устанавливают определённое число комплектов клиньев. Каждый комплект клиньев состоит из закладного и распорного клиньев. Первым устанавливают закладной клин широким концом вперёд, его положение фиксируют упором, затем тарированным усилием заводится распорный клин. При установке всех комплектов клиньев обеспечивается распор соединения. Клиновое соединение позволяет «выбрать» зазоры и дополнительно создать предварительный натяг. Снижение нагрузки на уплотнительную прокладку в результате нагружения соединения может происходить только вследствие деформации шпангоутов и клиньев. В этом заключаются принципиальные отличия таких соединений [1].
На практике выбор разъёмных соединений для элементов РДТТ как маршевых крупногабаритных, так и вспомогательного назначения во многом определяется традициями, опытом отработки того или иного соединения на предприятии – разработчике ракетного двигателя.
В современных маршевых РДТТ (как и для вспомогательных) обычно используют шпоночные и реже клиновые или болтовые соединения для основных стыков [1].
|
|
Таксономические единицы (категории) растений: Каждая система классификации состоит из определённых соподчиненных друг другу...
Состав сооружений: решетки и песколовки: Решетки – это первое устройство в схеме очистных сооружений. Они представляют...
Общие условия выбора системы дренажа: Система дренажа выбирается в зависимости от характера защищаемого...
История создания датчика движения: Первый прибор для обнаружения движения был изобретен немецким физиком Генрихом Герцем...
© cyberpedia.su 2017-2024 - Не является автором материалов. Исключительное право сохранено за автором текста.
Если вы не хотите, чтобы данный материал был у нас на сайте, перейдите по ссылке: Нарушение авторских прав. Мы поможем в написании вашей работы!