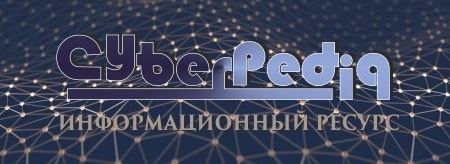
Типы оградительных сооружений в морском порту: По расположению оградительных сооружений в плане различают волноломы, обе оконечности...
Индивидуальные и групповые автопоилки: для животных. Схемы и конструкции...
Топ:
Когда производится ограждение поезда, остановившегося на перегоне: Во всех случаях немедленно должно быть ограждено место препятствия для движения поездов на смежном пути двухпутного...
Определение места расположения распределительного центра: Фирма реализует продукцию на рынках сбыта и имеет постоянных поставщиков в разных регионах. Увеличение объема продаж...
Генеалогическое древо Султанов Османской империи: Османские правители, вначале, будучи еще бейлербеями Анатолии, женились на дочерях византийских императоров...
Интересное:
Влияние предпринимательской среды на эффективное функционирование предприятия: Предпринимательская среда – это совокупность внешних и внутренних факторов, оказывающих влияние на функционирование фирмы...
Аура как энергетическое поле: многослойную ауру человека можно представить себе подобным...
Что нужно делать при лейкемии: Прежде всего, необходимо выяснить, не страдаете ли вы каким-либо душевным недугом...
Дисциплины:
![]() |
![]() |
5.00
из
|
Заказать работу |
|
|
Тормоза являются исключительно ответственным узлом, от работоспособности, эффективности и надежности которого существенно зависит безопасность движения на железных дорогах. В связи с этим совершенствованию тормозной техники уделяют большое внимание. Направления совершенствования тормозной техники на перспективу связаны с тенденциями повышения скоростей движения и весовых норм поездов, требованиями обеспечения безопасности движения, расширения автоматизации процессов управления и обслуживания, повышения надежности конструкций, уменьшения металлоемкости и снижения трудоемкости изготовления и ремонта подвижного состава. Важнейшей задачей совершенствования тормозной техники является повышение надежности и обеспечение полной безотказности работы всех тормозных приборов между плановыми видами ремонтов.
К числу основных проблем, связанных с дальнейшим совершенствованием тормознойтехники, относят: отработку и внедрение в производство комплекса тормозных приборов, обеспечивающих возможность электропневматического управления тормозными процессами в пассажирских и грузовых поездах; достаточную плавность, быстроту и равномерность действия при торможении
150
грузовых поездов весом до 10 000 тс и длиной состава 1300— 1500 м; надежность действия тормозов при температурах окружающего воздуха от —60 до 50° С.
В ближайшие годы предстоит закончить отработку конструкции и начать серийное производство магистральной и главной частей воздухораспределителя, являющегося модернизацией типового воздухораспределителя (усл. № 270). Новый воздухораспределитель (усл. № 483.000) будет иметь улучшенные технические характеристики, в частности увеличенную скорость распространения тормозной волны (не менее 250 м/с) и меньшее время отпуска (не более 30 с).
|
Широкое внедрение электропневматических тормозов позволит повысить управляемость движением поездов в результате четкого регулирования тормозной силы, сократить длину тормозного пути, уменьшить продольные усилия в длинносоставных поездах при изменениях режимов их ведения.
Дальнейшему совершенствованию подлежат приборы автоматического регулирования тормозной силы поезда: авторежимы и противогазные устройства. Создан и осваивается в производстве грузовой авторежим (усл. № 599) с временным контактом. В отличие от серийного прибора (усл. № 265), у которого механизм управляющей части находится в постоянном движении из-за колебаний кузова вагона на упругих элементах рессорного подвешивания, в авторежиме с временным контактом нет постоянных колебаний механизма управляющей части, а нужный режим торможения от погрузки до выгрузки вагона устанавливается один-раз при торможении в процессе полного опробования тормозов. Регулятор с временным контактом менее подвержен износу и более надежен в эксплуатации.
Особое значение в связи с перспективой внедрения восьми-осных вагонов имеет задача создания компактного тормозного привода двухосной тележки грузового вагона с непосредственным расположением на ней тормозной рычажной передачи и тормозного цилиндра. Перспективна также разработка системы тормозного привода с бесподвесочной траверсой, выполняемой за одно целое с тормозными цилиндрами. При такой системе тормозного привода до минимума сводится число его узлов и деталей, существенно уменьшается вес тормоза, освобождается подвагонное пространство. Однако разработка подобной системы тормозного привода может потребовать изменения и конструкции тележки.
Повышение скоростей движения, увеличение длины и веса поездов связано с возрастанием расхода сжатого воздуха для торможения. В связи с этим возникает необходимость сокращения расхода воздуха на утечки и снижения сопротивления движению воздуха в трубопроводах. Существенное значение имеет также задача повышения чистоты воздухопроводов и их коррозийной стойкости. Работы по совершенствованию тормозных воздухопроводов должны быть направлены на сокращение в них количе-
|
151
ства разъемных соединений, отработку сварных конструкций, использование новых материалов (алюминиевых сплавов и нержавеющих сталей), исследование возможности применения облегченных труб, создание новых конструкций разъемных соединений труб, в том числе безрезьбовых, и т. д.
С целью уменьшения металлоемкости и трудоемкости изготовления тормозных цилиндров ведется отработка технологии производства их штампосварных конструкций взамен литых чугунных. Прогрессивной технологией изготовления тормозных цилиндров штампосварной конструкции является метод раскатки штампованных корпусов роликами без последующей механической обработки.
С повышением скоростей движения пассажирских вагонов до 200 км/ч особое значение имеет отработка и внедрение в производство комплекса автотормозной техники для скоростного подвижного состава и прежде всего надежного и эффективного дискового и магнитно-рельсового тормоза. Возникла задача создания компактного привода дискового тормоза в виде единого блока, включающего тормозной цилиндр, клещевые рычаги и регулятор выхода штока.
В последние годы особое значение приобрела проблема отработки автотормозной техники для подвижного состава, предназначенного к эксплуатации на. Байкало-Амурской магистрали. Автотормозное оборудование этого подвижного состава должно безотказно работать при температуре окружающего воздуха от —60 до 50° С. При таких перепадах температур существенно усложняются условия взаимодействия трущихся пар в тормозных устройствах, условия работы резиновых деталей и смазочных масел, металлических деталей и узлов, испытывающих динамические нагрузки. Создание тормозной техники, предназначенной для работы в данных условиях, потребует освоения производства новых материалов, прежде всего специальных сталей с повышенной ударной вязкостью, резин с пониженной температурой затвердевания и масел с меньшей зависимостью вязкости от температуры.
|
152
Глава V АВТОСЦЕПНОЕ ОБОРУДОВАНИЕ ВАГОНОВ
ОСНОВНЫЕ ТРЕБОВАНИЯ К АВТОСЦЕПНОМУ ОБОРУДОВАНИЮ
Все вагоны, выпускаемые в СССР для железных дорог колеи 1520 мм, оборудованы автосцепными устройствами, которые служат для автоматического сцепления вагонов при формировании поезда, передачи продольных сжимающих и растягивающих усилий в поезде, а также ручного расцепления вагонов при маневрах.
В типовое автосцепное устройство (рис. 44) входят автосцепка /, поглощающий аппарат 4, тяговый хомут 3, центрирующий прибор 5, упорные угольники 2 и расцепной привод 6.
Общие требования к автосцепным устройствам и их установке на вагонах магистральных железных дорог определены Правилами технической эксплуатации железных дорог СССР (ПТЭ), ГОСТ 3475—62 и Нормами для расчетов на прочность и проектирование механической части новых и модернизированных вагонов железных дорог МПС колеи 1520 мм (несамоходных).
| Автосцепное устройство вагона согласно ПТЭ и ГОСТ 3475—62 должно быть расположено так, чтобы его высота h над головкой рельса у всех новых вагонов составляла 1040—1080 мм. Для предварительных расчетов вновь проектируемых вагонов эту высоту принимают равной 1060 мм. Автосцепное устройство вагонов должно обеспечивать беспрепятственное прохождение сцепленными вагонами кривых участков пути. Грузовые и пассажирские вагоны общесетевого назначения должны проходить участки сопряжения прямых и кривых радиусами соответственно 80 и 120 м и S-образные кривые радиусами соответственно 120 и 170 м без переходных кривых и прямых вставок. Наибольшее отклонение продольных осей сцепляемых автосцепок в горизонтальной плоскости, при котором обеспечивается автоматическое сцепление вагонов, составляет 175 мм. Конструкция автосцепки при некотором износе ее узлов и деталей должна обеспечивать автоматическое сцепление при вертикальном смещении продольных осей автосцепок до 150 мм. Для гарантии надежности сцепления вагонов в поезде разница по высоте между продольными осями сцепленных автосцепок согласно ПТЭ ограничена до 100 мм.
|
Детали автосцепного устройства по прочности должны удовлетворять следующим основным требованиям:
наибольшие напряжения в корпусе автосцепки от сжимающей
153
Рис. 44. Типовое автосцепное устройство
или растягивающей силы 250 тс при разности уровней осей сцепления 50 мм не должны превышать предела текучести материала 0Т;
напряжения в упорных плитах, тяговых хомутах и клиньях или -валиках тяговых хомутов при наиболее невыгодном приложении продольной сжимающей или растягивающей силы 250 тс не должны превышать 0,75сгт;
| напряжения в передних и задних упорах автосцепного устройства при наиболее невыгодном приложении продольной сжимающей или растягивающей силы 250 тс не должны превышать напряжений, допускаемых для расчетного режима I (см. гл. II). Перемычку, соединяющую угольники упора, рассчитывают на действие перерезывающей силы 100 тс.
Под наиболее невыгодным приложением продольной силы понимают случай ее действия с перекосом, когда разность уровней осей сцепления может достигать 100 мм, а на угольники одного упора передаются усилия разной величины.
К поглощающим аппаратам автосцепного устройства помимо требований по прочности предъявляют специальные требования, определяемые назначением этих устройств. Продольная сила между вагонами, возникающая при трогании с места и осаживании однородного поезда весом до 10 тыс. тс, а также при маневровых соударениях одиночных вагонов со скоростью не менее 7,5 км/ч, не должна превышать 200 тс. Силу закрытия аппарата, на действие которой рассчитывают его прочность, принимают равной 250 тс.
154
Энергоемкость поглощающих аппаратов определяют из расчета на соударение со скоростью не менее 7,5 км/ч полностью загруженных одиночных вагонов данного типа. При этом продольное усилие между вагонами не должно превышать 200 тс. Ориентировочно энергоемкость поглощающего аппарата Э = mv 2 /8, где т — масса вагона брутто; v — скорость соударения. Энергоемкость аппарата пассажирских вагонов должна быть не менее 3 тс-м, а максимальное продольное усилие при их соударении со скоростью до 7,5 км/ч — не более 150 тс.
Отдача поглощающего аппарата грузовых вагонов рекомендована не более 30%, а пассажирских — не более 50%, усилие предварительной затяжки — соответственно не более 20 и 5 тс. При статическом нагружении конечное усилие сопротивления поглощающего аппарата грузового вагона должно быть не менее 100 тс, а пассажирского — не менее 75 тс. Поглощающий аппарат должен обладать достаточно высокой надежностью, износостойкостью, и не допускать ускорений при соударении вагонов, превышающих уровень, определяемый принятыми нормами.
|
Сложные условия эксплуатации автосцепного устройства обусловливают высокие требования не только к конструкции его узлов и деталей, но и к материалу и качеству изготовления. Материал и качество изготовления литых деталей автосцепных устройств регламентированы соответствующими техническими условиями и стандартами. Корпус автосцепки, узлы механизма, тяговый хомут и детали, передающие нагрузку на раму вагона, необходимо изготовлять из соответствующих углеродистой и низколегированной сталей.
Механические свойства металла при этом могут несколько различаться для разных деталей. Так, металл корпуса автосцепки и тягового хомута должен иметь предел прочности 52—55 кгс/мм2 при пределе текучести не менее 30 кгс/мм2, относительном удлинении не менее 18% и ударной вязкости при —60° С не менее 2,5 кгс-м/см2. Металл деталей механизма сцепления и деталей, передающих нагрузку на раму вагона, должен иметь предел прочности не менее 45 кгс/мм2, предел текучести не менее 25 кгс/мм2, ударную вязкость при 20° С не менее 5 кгс-м/см2 и т. д.
Все перечисленные детали автосцепного устройства подвержены весьма интенсивному износу в эксплуатации, поэтому нуждаются в периодическом ремонте для восстановления изношенных мест наплавкой электродами. По этой причине содержание углерода в стали для них ограничено 0,27%. Если в металле этих деталей углерода содержится более 0,25%, то на них ставят знак в виде буквы С, указывающий на необходимость при заварке дефектов или наплавке изношенных поверхностей подогревать ремонтируемую деталь до температуры 250—300° С.
В качестве материала для деталей поглощающего пружинно-фрикционного аппарата применяют углеродистую сталь с повы-
155
шенным содержанием углерода или легированную сталь. В конструкции гидравлических, гидропневматических, резинометалли-ческих и других аппаратов помимо сталей используют и другие материалы: бронзу, резину, пластмассы и т. п. Корпус пружинно-фрикционного поглощающего аппарата отливают из стали 32Х06Л или ЗОГСЛ (ГОСТ 977—75) и подвергают закалке и отпуску до твердости НВ 207—277. Клинья и корпус аппарата изготовляют штамповкой из стали 30 (ГОСТ 1050—74) и подвергают нитроце-ментации или цементации с последующей закалкой и отпуском до твердости HRC 50—64. Допускается изготовлять клинья и конусы из стали 38ХС (ГОСТ 4543—71) с закалкой до твердости НВ 341—477. Клин или валик тягового хомута, а также упорную плиту и подвески центрирующего прибора рекомендуется изготовлять штамповкой из стали 38ХС с последующей закалкой и отпуском до твердости НВ 255—321.
В конструкции магистральных вагонов в зависимости от их типа применяют несколько разновидностей автосцепных устройств. Основную разновидность автосцепного устройства (ГОСТ 3475—62) применяют на четырехосных грузовых вагонах. Характерной особенностью этого устройства является применение типовой автосцепки СА-3 и поглощающего аппарата Ш-1-Тм, устанавливаемого в проем между упорами, равный 625 мм. Ход аппарата 70 мм. Корпус автосцепки опирается на центрирующий прибор без подпружинивания (см. рис. 44).
В пассажирских вагонах (в том числе электропоездов и дизель-поездов) применяют автосцепное устройство, отличающееся от предыдущего типом поглощающего аппарата и центрирующего прибора. В этом устройстве применен резинометаллический поглощающий аппарат Р-2П.
В шести- и восьмиосных вагонах применяют так называемое модернизированное автосцепное устройство (рис. 45), которое существенно отличается от автосцепного устройства четырехосных вагонов по конструкции корпуса автосцепки 1, хомута 3, узла 2 соединения корпуса с хомутом и центрирующего прибора 4. Узел соединения корпуса автосцепки с тяговым хомутом выполнен в отличие от соответствующего узла типового автосцепного устройства не с клином, а с валиком и сферическим вкладышем. Модернизированное автосцепное устройство допускает использование поглощающих аппаратов с ходом до ПО мм при стандартном расстоянии между упорами 625 мм. В модернизированном автосцепном устройстве использован центрирующий прибор с подпружиненной опорой для хвостовика автосцепки.
Автосцепные устройства восьмиосных вагонов, имеющих значительную длину консолей, оборудованы специальным приспособлением для принудительного отклонения автосцепки в кривых участках пути (внутрь кривой) с целью облегчения при этом сцепляемости вагонов. Такое приспособление в виде Л-образного рычага (торсиона) крепят в кронштейнах на хребтовой балке
156
Рис. 45. Модернизированное автосцепное устройство
вагона и соединяют одним плечом с соединительной балкой четырехосной тележки, а другим — с центрирующей балочкои автосцепки.
КОНСТРУКЦИЯ АВТОСЦЕПКИ
В состав автосцепного устройства всех магистральных вагонов входит автосцепка СА-3 (рис. 46), состоящая из корпуса и механизма сцепления. Корпус автосцепки состоит из головной части 2 и хвостовика 1. Два зуба 3 и 5 головной части и зев 4 корпуса в плане имеют очертание, называемое контуром зацепления (ГОСТ 21447—75). Головная часть корпуса автосцепки плавно переходит в полый хвостовик, на конце которого предусмотрено отверстие для установки тягового клина. Торец хвостовика имеет цилиндрическую поверхность, что улучшает условия передачи усилий на упорную плиту при действии на автосцепку сжимающих сил и облегчает поворот автосцепки в плане.
В конструкции модернизированного автосцепного устройства
использована автосцепка с корпусом, отличающимся от корпуса
типовой автосцепки СА-3. Хвостовик корпуса модернизированной
автосцепки соединен с тяговым хомутом не клином, а валиком.
Торец хвостовика имеет сферическую поверхность, соответству
ющую поверхности упорной плиты. Корпус автосцепки в модер
низированном автосцепном устройстве снабжен специальным
предохранительным кронштейном, приваренным снизу малого
зуба. Когда разность уровней продольных осей сцепленных авто
сцепок достигает 145 мм, большой зуб одной автосцепки опирается
на предохранительный кронштейн другой автосцепки, что пре
пятствует их расцеплению.С введением предохранитель
ных кронштейнов и подпружиненных опор для хвостовика нежесткая автосцепка СА-3 становится полуже-
157
|
4 5
Рис. 47. Механизм сцепления
сткой. При взаимных перемещениях продольных осей сцепленных автосцепок по вертикали до 145 мм автосцепка является нежесткой, а при дальнейших перемещениях — жесткой.
В ударной стенке зева расположены большое и малое окна соответственно для замка и замкодержателя. Со стороны малого зуба на головной части сбоку корпуса расположен прилив с отверстиями для валика подъемника и запорного болта валика.
В головной части корпуса автосцепки размещен механизм сцепления (рис. 47), состоящий из замка /, замкодержателя 4, предохранителя замка 5, подъемника 2, валика подъемника 3 и болта с гайкой и двумя шайбами. Замок механизма сцепления автосцепки расположен в кармане корпуса и опирается на соответствующую поверхность кармана радиальной опорой с фиксирующим зубом. Поворачиваясь вокруг этого зуба, замок может уходить внутрь корпуса под действием усилия со стороны автосцепки сцепляемого вагона или выходить из корпуса под действием собственного веса. Последнее может происходить в двух случаях: когда вагоны разведены или когда малые зубья корпусов сцепляемых автосцепок в контуре зацепления занимают крайнее положение. Если при этом механизмы автосцепок не установлены в положение «на буфер», то замки выдвигаются в пространство между малыми зубьями, что приводит к сцеплению автосцепок. На замке со стороны хвостовика корпуса предусмотрен сигнальный отросток, который выходит в специальное отверстие головной части корпуса, когда замок входит в карман.
В верхней части замка размещен цилиндрический шип, на который навешен предохранитель, имеющий вид двуплечного рычага. В свободном состоянии предохранитель опирается своим верхним плечом на специальную полочку в корпусе автосцепки. Замкодержатель навешен на цилиндрический шип внутри корпуса автосцепки и в свободном состоянии его лапа выступает из малого окна в стенке зева. В этом случае противовес замкодер-
158
жателя расположен так, что не препятствует замку в процессе сцепления уходить в карман под действием малого зуба смежной автосцепки. В сцепленном состоянии автосцепок малые зубья нажимают на лапы замкодержателей, утапливая их в малом окне. При этом противовес замкодержателя поднимается и устанавливается против верхнего плеча предохранителя, что предотвращает уход замка внутрь головной части автосцепки и предупреждает самопроизвольное расцепление.
Автосцепки расцепляют поворотом подъемника при помощи валика, связанного цепочкой с расцепным рычагом. При повороте подъемник вначале поднимает верхнее плечо предохранителя выше противовеса замкодержателя, затем поднимает замок и убирает его внутрь головной части автосцепки. В таком положении механизм автосцепки находится до разведения вагонов, после чего автоматически (под действием веса всех деталей) устанавливается в положение, при котором автосцепка готова к новому сцеплению.
В случае ошибочного расцепления вагонов сцепление можно восстановить без разведения вагонов. С этой целью замкодержатель необходимо несколько поднять на шипе, служащем для его навешивания в головной части корпуса. Чтобы замкодержатель можно было поднять, отверстие, которым он навешен на шип, имеет овальную форму, а в корпусе автосцепки со стороны большого зуба предусмотрено специальное отверстие. Через это отверстие металлическим или деревянным стержнем можно поднять замкодержатель. При подъеме замкодержателя все остальные детали механизма резко опускаются вниз, восстанавливая сцепление вагонов.
Механизм автосцепки в положение «на буфер» приводят поворотом расцешюго рычага и установкой его рукоятки на полочку кронштейна. При этом цепь расцепного привода натягивается, удерживая все детали механизма в поднятом положении, что исключает возможность сцепления вагонов при соударениях.
В практике отечественного вагоностроения помимо автосцепки СА-3 известны и другие ее конструкции. Одной из них является автосцепка СА-Д, которую для эксплуатационных испытаний устанавливали на пятивагонных рефрижераторных секциях. Автосцепка СА-Д взаимозаменяема и взаимосцепляема с автосцепкой СА-3 и отличается от последней конструкцией сцепного механизма и его кинематикой. Длительная эксплуатация автосцепок СА-Д не выявила их существенных преимуществ перед автосцепкой СА-3, поэтому переход на их массовое производство не предполагается.
Вагоны метрополитена оборудованы полуавтоматической автосцепкой жесткого типа. Эта автосцепка автоматически сцепляет вагоны и воздухопроводы (тормозную и напорную магистрали). После сцепления вагонов при помощи специального механизма соединяют электрические цепи управления вагонами.
159
ПОГЛОЩАЮЩИЕ АППАРАТЫ
Поглощающий аппарат автосцепного устройства является узлом, обеспечивающим смягчение продольных динамических усилий между вагонами, поглощение и рассеивание энергии удара. Серийное производство ограничено практически поглощающими аппаратами двух типов, один из которых предназначен для оборудования четырехосных грузовых вагонов, а другой — пассажирских вагонов. Помимо серийных поглощающих аппаратов, промышленность в различных количествах производит несколько вариантов опытных аппаратов, которые проходят эксплуатационную проверку.
Основным типом поглощающих аппаратов, производимых промышленностью для четырехосных грузовых вагонов, является пружинно-фрикционный аппарат Ш-1-Тм. Этот аппарат (рис. 48) состоит из корпуса /, наружной 2 и внутренней 3 пружин, нажимного конуса 5, трех фрикционных клиньев 4, шайбы 6 и стяжного болта 7 с гайкой. Габаритные размеры аппарата 615x318x230 мм, ход 70 мм. Масса аппарата Ш-1-Тм составляет 137 кг. Энергоемкость аппарата Ш-1-Тм до приработки равна 2—3 тс-м при полном ходе, а после приработки достигает 5 тс-м при усилии 280 тс, соответствующем полному ходу (закрытию). Средняя энергоемкость аппарата при силе 200 тс составляет 3,4 тс-м. В аппарате использованы заневоленные пружины из стали 55С2. В собранном аппарате пружины сжаты усилием примерно 4,6 тс. Такое предварительное сжатие пружин обеспечивает начальное сопротивление аппарата 23 тс.
Для оборудования восьмиосных грузовых вагонов исполь
зуют пружинно-фрикционные поглощающие аппараты Ш-2-Т,
по конструкции принципиально не отличающиеся от аппаратов
Ш-1-Тм. До приработки энергоемкость аппарата составляет не
менее 2,5 тыс. кгс-м, а после приработки достигает 5,5 тыс. кгс-м
при полном ходе ПО мм. При полном ходе сила сопротивления
аппарата достигает 250 тс. При силе 200 тс энергоемкость аппара
тов Ш-2-Т в среднем составляет 4,4 тыс. кгс-м.
Повышение энергоемкости получено в результате увеличения хода аппарата, что, в свою очередь, стало возможным после отказа от шайбы, поджимающей клинья. Кроме того, усилен комплект пружин, изгото-
160 |
Рис. 49. Поглощающий аппарат
вленных из стали 60С2ХФА (ГОСТ 14959—69), что вы звало увеличение в рабочем положении высоты аппарата на 16 мм (до 246 мм). Пружины предварительно сжаты усилием 4,2 тс. Масса Ш-2-Т составляет 154 кг. Длина аппарата допускает его установку в проем со стандартным расстоянием между упорами 625 мм. Начальное сопротивление аппарата составляет приблизительно 26 тс. Аппарат Ш-2-Т в меньшей степени, чем аппарат Ш-1-Тм, подвержен заклиниванию. Ведутся работы ' по созданию для восьмиосных вагонов поглощающих аппаратов с повышенной энергоемкостью и другими улучшенными параметрами.
Пассажирские вагоны, в том числе вагоны электропоездов и дизель-поездов, производимые в СССР, оборудованы резино-металлическими поглощающими аппаратами Р-2П (рис. 49), рассчитанными на установку в проемы со стандартным расстоянием между упорами 625 мм. Ход аппарата 70 мм. Аппарат состоит из корпуса / и нажимной плиты 2, изготовленных отливкой, резинометаллических упругих элементов 3 и промежуточной плиты 4. Резинометаллический элемент выполнен из двух стальных армирующих листов толщиной 2 мм и завулканизиро-ванной между ними резины. Размеры резинометаллического элемента 265x220x41,5 мм. В элементе использована морозостойкая резина 7-ИРП-1348 (ТУ 38.005204—71) с твердостью 70 ед.
по Шору.
Энергоемкость аппарата Р-2П существенно зависит от скорости деформации резины и при полном динамическом сжатии достигает 2,2 тс • м. При этом усилие не превышает 100 тс. Сила предварительного сжатия аппарата составляет 3—5 тс, что достаточно для поджатая его резинометаллических элементов на 18 мм. Усилие при полном статическом сжатии не менее 75 тс. Коэффициент поглощения энергии достигает 45%. Масса аппарата Р-2П 116 кг. Он имеет большую долговечность, чем пружинно-фрикционные аппараты, не подвержен заклиниванию и отличается хорошей стабильностью работы. Особенностью аппаратов Р-2П является зависимость их параметров от качества резины и окружающей
температуры. тттот
Кроме серийных поглощающих аппаратов ш-1-1м, ш-^-1
и Р-2П, разработаны пружинно-фрикционные (Ш-2-В, Ш-4-Т,
Ш-5-Т0), резинометаллические (Р-4П) и гидрогазовые (ГА-100М и ГА-500).
Аппарат Ш-2-В предназначены для четырехосных грузовых вагонов. Его ход равен 90 мм, энергоемкость в приработанном состоянии и полном ходе составляет 6,3 тс-м, а усилие закрытия аппарата 200 тс. Теоретические исследования аппаратов Ш-2-В позволяют рассчитывать на допускаемую скорость соударения вагонов до 10 км/ч. Для восьмиосных грузовых вагонов создан пружинно-фрикционный поглощающий аппарат Ш-4-Т, аналогичный Ш-2-Т, но предназначенный для установки в автосцепное устройство с расстоянием между задним и передним упорами, равным 880 мм. При сжатии вагонов ход аппарата может достигать 160 мм, а при растяжении равен 100 мм. Теоретически энергоемкость аппарата Ш-4-Т составляет 10,4 тс-м при полном ходе 160 мм и конечном усилии сжатия около 200 тс.
Пружинно-фрикционный поглощающий аппарат Ш-5-ТО, известный также как аппарат ВНИИВ-КВЗ-2, отличается от подобных аппаратов (Ш-1-Тм, Ш-2-Т и др.) тем, что в нем корпус объединен с тяговым хомутом. Аппарат имеет ход 100 мм и предназначен для четырехосных вагонов со стандартным размером между упорами 625 мм. Аппарат закрывается при усилии 220 тс, его расчетная энергоемкость равна 6,5 тс-м. При скорости соударения четырехосных вагонов, оборудованных аппаратами Ш-5-ТО, до 9 км/ч, усилие, передаваемое на вагон, не должно превышать 200 тс.
Резинометаллический поглощающий аппарат Р-4П рекомендован для оборудования рефрижераторных вагонов, т. е. подвижного состава, наиболее остро нуждающегося в совершенных средствах защиты от ударов и других видов динамического воздействия при маневровой и поездной работе. Аппарат Р-4П имеет ход 70 мм и рассчитан на установку в автосцепное устройство со стандартным размером между упорами, равным 625 мм. Его энергоемкость достигает 4,0 тс-м при силе 200 тс; коэффициент поглощения энергии составляет 55%. Аппарат допускает скорость соударения вагонов до 7,5 км/ч, причем усилие, развиваемое между вагонами, не превышает 160 тс.
В конструкции аппарата Р-4П двадцать резинометаллических элементов размерами 265x220x24,2 мм. Через каждые три-четыре элемента в аппарате установлены промежуточные или направляющие плиты, которые уменьшают выпучивание набора элементов при сжатии. Весь комплект резинометаллических элементов, промежуточных и направляющих плит установлен в корпусе аппарата и поджат крышкой, которая одновременно выполняет назначение упорной плиты. В собранном виде и поджатом состоянии аппарат запирается стопорными винтами, которые не препятствуют сжатию аппарата при его установке в автосцепное устройство и работе. Поглощающий аппарат Р-4П можно с успехом применять на платформах для перевозки контейнеров,
162
двухъярусных платформах для перевозки автомобилей, вагонах для перевозки скота и на других специализированных вагонах для легковесных грузов.
В последние годы в отечественной промышленности большое внимание уделяется разработке новых гидравлических, гидропневматических, гидрогазовых, гидрофрикционных, резинометаллических и других поглощающих аппаратов. В частности, для грузовых вагонов создан гидрогазовый поглощающий аппарат ГА-100М. Упругое сопротивление в этих аппаратах достигается за счет сжатого газа (азота), а неупругое — за счет перетекания масла из одной полости в другую через дроссельное отверстие.
Гидрогазовый аппарат ГА-100М взаимозаменяем с аппаратом Ш-1-Тм. Его ход равен 70 мм. Усилие, при котором аппарат начинает сжиматься, составляет 10 тс. Энергоемкость аппарата достигает 9,3 тс-м! Усилие при этом не превышает 200 тс, а скорость соударения груженых вагонов достигает 12 км/ч. Коэффициент поглощения энергии аппаратом ГА-100М зависит от скорости соударения вагонов и составляет 60—90%.
|
|
Типы оградительных сооружений в морском порту: По расположению оградительных сооружений в плане различают волноломы, обе оконечности...
Типы сооружений для обработки осадков: Септиками называются сооружения, в которых одновременно происходят осветление сточной жидкости...
Организация стока поверхностных вод: Наибольшее количество влаги на земном шаре испаряется с поверхности морей и океанов (88‰)...
Своеобразие русской архитектуры: Основной материал – дерево – быстрота постройки, но недолговечность и необходимость деления...
© cyberpedia.su 2017-2024 - Не является автором материалов. Исключительное право сохранено за автором текста.
Если вы не хотите, чтобы данный материал был у нас на сайте, перейдите по ссылке: Нарушение авторских прав. Мы поможем в написании вашей работы!