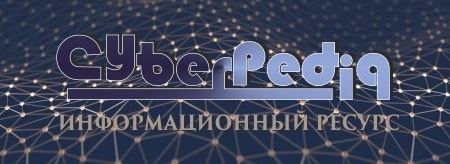
Опора деревянной одностоечной и способы укрепление угловых опор: Опоры ВЛ - конструкции, предназначенные для поддерживания проводов на необходимой высоте над землей, водой...
Кормораздатчик мобильный электрифицированный: схема и процесс работы устройства...
Топ:
Отражение на счетах бухгалтерского учета процесса приобретения: Процесс заготовления представляет систему экономических событий, включающих приобретение организацией у поставщиков сырья...
Определение места расположения распределительного центра: Фирма реализует продукцию на рынках сбыта и имеет постоянных поставщиков в разных регионах. Увеличение объема продаж...
Интересное:
Отражение на счетах бухгалтерского учета процесса приобретения: Процесс заготовления представляет систему экономических событий, включающих приобретение организацией у поставщиков сырья...
Подходы к решению темы фильма: Существует три основных типа исторического фильма, имеющих между собой много общего...
Уполаживание и террасирование склонов: Если глубина оврага более 5 м необходимо устройство берм. Варианты использования оврагов для градостроительных целей...
Дисциплины:
![]() |
![]() |
5.00
из
|
Заказать работу |
ВВЕДЕНИЕ
Процесс ректификации находит широкое применение во многих отраслях химической, пищевой, и нефтеперерабатывающей промышленности. Для проведения ректификационного процесса применяют колонные аппараты различного типа, отличающиеся один от другого способом контакта фаз и видом контактного устройства.
Целью расчета ректификационной установки является определение основных размеров колонны, ее гидравлического сопротивления, поверхности теплообменников, материальных потоков и затрат тепла.
НАЗНАЧЕНИЕ И ОБЛАСТЬ ПРОЕКТИРУЕМОГО ОБЪЕКТА
Колонные аппараты предназначены для проведения процессов тепло- и массообмена: ректификации, дистилляции, абсорбции, десорбции. Корпуса стандартизованных колонных аппаратов изготавливаются в двух исполнениях:
Ø Корпус, собираемый из отдельных царг с фланцевыми соединениями, рассчитан на давление 1,6 МПа.
Ø Корпус цельносварной, рассчитанный на давление до 4 МПа, имеют колонные аппараты диаметром более 1000мм с интервалом изменения диаметра через 200мм. Расстояния между тарелками в зависимости от типов могут изменяться от 300 до 1000мм.
До настоящего времени не выработано обобщенных и достаточно объективных критериев выбора типа тарелки для ведения того или иного процесса. Существенную роль в этом играют сложившиеся в организациях – поставщиках традиции, опирающиеся на многолетний опыт надежной эксплуатации разрабатываемой ими массообменной аппаратуры.
Тарелки с капсульными колпачками получили наиболее широкое распространение, благодаря своей универсальности и высокой эксплуатационной надежности, они достаточно эффективны, но металлоемки и сложны в монтаже.
Тарелки, собираемые из S – образных элементов, устанавливаются преимущественно в колоннах больших диаметров. Их производительность на 20-30% выше, чем у капсульных.
Клапанные тарелки, по сравнению с колпачковыми, имеют более высокую эффективность и на 20-40% большую производительность. Они применяются для обработки жидкостей, не склонных к смолообразованию и полимеризации, во избежание прилипания клапана к тарелке.
Ситчатые тарелки имеют достаточную высокую эффективность, низкое сопротивление и малую металлоемкость. Они применяются преимущественно в колоннах для обработки чистых жидкостей при атмосферном давлении и вакууме.
Решетчатые тарелки провального типа имеют производительность в 1,5 – 2 раза большую, чем колпачковые тарелки, низкую металлоемкость. Их эффективность достаточно высока, но в узком диапазоне рабочих скоростей. Эти тарелки рекомендуется применять при больших нагрузках колонны по жидкости.
Расчет флегмового числа
Минимальное флегмовое число можно рассчитать по формуле
(II.3.1)
где - мольная доля низкокипящего компонента в паре, равновесном с исходной смесью, определяется по диаграмме х-у (рисунок 2).
Для нашего случая Отсюда
Оптимальное флегмовое число найдем из условия получения минимального объема колонны, пропорционального произведению nT(R+1), где nT - число ступеней изменения концентрации (теоретическое число тарелок).
Расчет оптимального флегмового числа выполняем следующим образом:
а) задаемся рядом коэффициента избытка флегмы β в пределах от 1,1 до 5,0; определяем рабочее флегмовое число и величину отрезка
;
б) откладываем отрезок В на оси ординат и проводим линии рабочих концентраций верхней и нижней частей колонны;
в) между равновесной и рабочими линиями в пределах концентраций xW и xD строим ступени, каждая из которых соответствует теоретической тарелке;
г) при каждом значении β определяем число теоретических тарелок nT и величину произведения nT(R+1).Результаты расчета сводим в таблицу 2.
Таблица 2 – Данные для расчета оптимального флегмового числа
β | R | B | nT | nT·(R+1) |
1,1 | 2,464 | 0,241 | 16 | 55,424 |
1,75 | 3,92 | 0,17 | 12 | 59,04 |
2 | 4,48 | 0,15 | 11 | 60,28 |
2,8 | 6,272 | 0,11 | 9 | 65,448 |
3,6 | 8,064 | 0,092 | 8 | 72,512 |
д) по данным таблицы 2 строим график зависимости nT(R+1)=f(R) (рисунок 3) и находим минимальное значение величины nT(R+1). Ему соответствует флегмовое число R=2,5.
Эту величину и принимаем в дальнейших расчетах за оптимальное рабочее число флегмы. Число ступеней изменения концентраций при этом равно 16.
ВЫСОТА КОЛОННЫ
Высоту колонны определяем графо-аналитическим методом, т.е. последовательно рассчитываем коэффициенты массоотдачи, массопередачи, коэффициенты полезного действия тарелок; строим кинетическую кривую и определяем число действительных тарелок.
Коэффициент массоотдачи в паровой фазе
(III.1)
где Dп – коэффициент диффузии паров компонента А в парах компонента В, рассчитывается по формуле
(III.2)
где Т – температура, К; p – абсолютное давление, кгс/см2; МА, МВ – мольные массы компонентов А и В; νА, νВ – мольные объемы компонентов А и В, определяемые как сумма атомных объемов элементов, входящих в состав пара [2].
Rе – критерий Рейнольдса для паровой фазы
(III.3)
где μп – динамический коэффициент вязкости пара, Па·с.
(III.4)
где Мср.п, МА, МВ – мольные массы пара и отдельных компонентов, кг/кмоль; μср.п, μА, μВ – соответствующие им динамические коэффициенты вязкости; уА, уВ – объемные доли компонентов смеси.
Коэффициент диффузии паров ацетона в парах этилового спирта:
а) в верхней части колонны
б) в нижней части колонны
Коэффициент динамической вязкости смеси паров ацетона и этилового спирта:
а) в верхней части колонны при температуре 68,570С, μАп=0,2165 мПа·с, μВп=0,691 мПа·с.
б) в верхней части колонны при температуре 77,570С, μАп=0,203 мПа·с, μВп=0,592 мПа·с.
Критерий Рейнольдса для паровой фазы:
а) в верхней части колонны
б) в нижней части колонны
Коэффициент массоотдачи в паровой фазе:
а) в верхней части колонны
б) в нижней части колонны
Коэффициент массоотдачи в жидкой фазе
,
где Dж – коэффициент диффузии в жидкости, м2/с; Мж.ср – средняя мольная масса жидкости в колонне, кг/кмоль:
а) в верхней части колонны
б) в нижней части колонны
- диффузионный критерий Прандля
(III.5)
Коэффициент диффузии в жидкости при 200С можно вычислить по приближенной формуле
(III.6)
где μж – динамический коэффициент вязкости жидкости, мПа·с;
МА, МВ – мольные массы компонентов А и В,кг/кмоль; νА, νВ – мольные объемы компонентов А и В, кг/кмоль; А и В – коэффициенты зависящие от свойств низкокипящего и высококипящего компонентов.
Коэффициент диффузии пара в жидкости Dt связан с коэффициентом диффузии D20 следующей приближенной зависимостью,
(III.7)
в которой температурный коэффициент b может быть определен по эмпирической формуле
(III.8)
где μ – динамический коэффициент вязкости жидкости при 200С, мПа·с; ρ – плотность жидкости, кг/м3.
Динамический коэффициент вязкости жидкости
(III.9)
а) в верхней части колонны при t=67,250С
μА=0,2195 мПа·с
μВ =0,713 мПа·с
б) в нижней части колонны при t=77,75≈780С
μА=0,203 мПа·с
μВ =0,592 мПа·с
Коэффициент диффузии ацетона в жидком этиловом спирте при t=200С:
а) для верхней части колонны
б) для нижней части колонны
Температурный коэффициент принимаем равным b=0,0234.
Тогда
а) для верхней части колонны
б) для нижней части колонны
Критерий Прандля:
а) для верхней части колонны
б) для нижней части колонны
.
Определяем коэффициенты массоотдачи:
а) для верхней части колонны
б) для нижней части колонны
Коэффициенты массопередачи определяем по уравнению
(III.10)
где m – тангенс угла наклона линии равновесия на рабочем участке.
Для определения угла наклона разбиваем ось х на участки и для каждого их них находим среднее значение тангенса как отношение разности (у*-у) к разности (х-х*) в том же интервале, т.е.
(III.11)
Подставляя найденные значения коэффициентов массоотдачи βп и βж и тангенсов углов наклона линии равновесия в уравнение, находим величину коэффициента массопередачи для каждого значения х в пределах от хW до хD.
Полученные значения Ку используем для определения числа единиц переноса nу в паровой фазе
, (III.12)
где φ – отношение рабочей площади к свободному сечению колонны, примем φ=0,8.
Допуская полное перемешивание на тарелке, имеем
(III.13)
где η – КПД тарелки.
Результаты приведенных выше расчетов, сводим в таблицу 3.
Таблица3 – Параметры, необходимые для построения кинетической кривой
x | xW | 0,13 | 0,19 | xF | 0,3 | 0,5 | 0,7 | 0,8 | xD |
tgα=m | 1,97 | 1,78 | 1,44 | 1,23 | 1,21 | 0,92 | 0,7 | 0,62 | 0,59 |
Ky·10-3 | 4,38 | 4,435 | 4,53 | 4,59 | 4,6 | 4,69 | 4,76 | 4,79 | 4,8 |
ny | 0,134 | 0,136 | 0,138 | 0,14 | 0,141 | 0,144 | 0,146 | 0,1469 | 0,1472 |
η | 0,126 | 0,128 | 0,13 | 0,132 | 0,1321 | 0,1346 | 0,13638 | 0,1371 | 0,1324 |
AC, мм | 26 | 20,5 | 7 | 3,5 | 23 | 49 | 52 | 46,5 | 43 |
AB, мм | 3,3 | 2,6 | 0,91 | 0,462 | 3,04 | 6,59 | 7,12 | 6,38 | 5,9 |
Между кривой равновесия и линиями рабочих концентраций в соответствии с табличными значениями х проводим ряд прямых, параллельных оси ординат (рисунок 4).
Измеряем полученные отрезки А1С1, А2С2, А3С3 и т.д. и делим их в отношении η=АВ/АС, т.е. определяем величину отрезков А1В1, А2В2…….АnBn. Через найденные для каждого значения х точки В проводим кинетическую кривую, отображающую степень приближений фаз на тарелках к равновесию.
Число реальных тарелок nд находим путем построения ступенчатой линии между кинетической кривой и рабочими линиями в пределах от хD до хW.
Получаем 94 тарелок (40 в верхней части колонны, 54 – в нижней), которые и обеспечивают разделение смеси в заданных пределах изменения концентраций.
Высота тарельчатой части колонны
(III.14)
Общая высота колонны
(III.15)
где hсеп – расстояние между верхней тарелкой и крышкой колонны, (высота сепарационного пространства), принимаем 0,8м (приложение А6 [3]); hкуб – расстояние между нижней тарелкой и днищем колонны, (высота кубовой части), принимаем 2м (приложение А6 [3]).
В соответствии с рассчитанным диаметром колонны по каталогу-справочнику [1] подбираем стандартную колонну и тарелки. Принимаем к установке колонный аппарат диаметром 1000мм; колонна компонуется из однопоточных неразборных тарелок типа ТСК – I ОСТ 26-01-282-74 с капсульными стальными колпачками. Общее число колпачков на тарелке – 37. Основные параметры тарелки приведены в таблице 4.
Таблица 4 – Характеристика колпачковой тарелки
Диаметр колонны (внутр.) D, мм | 1000 |
Свободное сечение колонны, м2 | 0,78 |
Длина линии барботажа, м | 9,3 |
Периметр слива Lс, м | 0,8 |
Площадь слива, м2 | 0,05 |
Площадь паровых патрубков, м | 0,073 |
Относительная площадь для прохода паров, % | 9 |
Диаметр колпачка d, мм | 80 |
Шаг t, мм | 110 |
Масса колпачка в кг (при h=20мм, Нt=300мм) для исполнения 1 | 39 |
Дефлегматор
В дефлегматоре конденсируется ацетон с небольшим количеством этилового спирта. Температура конденсации паров дистиллята tD=630C. Температуру воды на входе в теплообменник примем 180С, на выходе 380С.
Составляем температурную схему процесса и определяем движущую силу процесса теплопередачи:
63→63
38←18
По таблице 4.8 [2] коэффициент теплопередачи от конденсирующегося пара органических веществ к воде находится в пределах 340 – 870 Вт/м2∙К. Принимаем наименьший коэффициент теплопередачи К=340 Вт/м2∙К.
Количество тепла, отнимаемого охлаждающей водой от конденсирующегося в дефлегматоре пара
Поверхность дефлегматора находим из основного уравнения теплопередачи
(V.2.1)
С запасом 15-20% принимаем по каталогу [2, таблица XXXІV] двухходовой теплообменник.
Характеристики теплообменника:
поверхность теплообмена……………………………………76м2
диаметр кожуха……………………………………………….600мм
диаметр труб…………………………………………………...25×2
длина труб………………………………………………………4,0м
число труб
общее…………………………………………………………….244
на один ход………………………………………………………122
Холодильник для дистиллята
В холодильнике происходит охлаждение дистиллята от температуры конденсации до 300С
63→30
38←18
Количество тепла, отнимаемого охлаждающей водой от дистиллята в дефлегматоре
(V.3.1)
Принимаем К=300Вт/м2∙К по таблице 4.8 [2].
Поверхность теплообмена холодильника дистиллята
(V.3.2)
По таблице 4.12 [2] принимаем одноходовой теплообменник.
Характеристики теплообменника:
поверхность теплообмена……………………………………4,5м2
диаметр кожуха (наружный)…..…………………………….237мм
диаметр труб…………………………………………………...25×2
длина труб………………………………………………………1,5м
число труб………………………………………………………..37
Подогреватель
tгр.п=1000С
100→100
78,8←20
Принимаем К=150Вт/м2∙К по таблице 4.8 [2].
(V.5.1)
Поверхность теплообмена подогревателя исходной смеси
(V.5.2)
По таблице 4.12 [2] принимаем двухходовой теплообменник.
Характеристики теплообменника:
поверхность теплообмена……………………………………31м2
диаметр кожуха (наружный)…..…………………………….400мм
диаметр труб…………………………………………………...25×2
длина труб………………………………………………………4,0м
число труб………………………………………………………..100
Заключение
В ходе проектирования была разработана ректификационная установка с требуемыми техническим заданием характеристиками.
В пояснительной записке приведены расчёты процессов, подтверждающие работоспособность проектируемого изделия.
Схемы каждого из механизмов приведены в соответствующих разделах пояснительной записки.
В графической части курсового проекта изображены: технологическая схема ректификационной установки, чертёж общего вида.
ВВЕДЕНИЕ
Процесс ректификации находит широкое применение во многих отраслях химической, пищевой, и нефтеперерабатывающей промышленности. Для проведения ректификационного процесса применяют колонные аппараты различного типа, отличающиеся один от другого способом контакта фаз и видом контактного устройства.
Целью расчета ректификационной установки является определение основных размеров колонны, ее гидравлического сопротивления, поверхности теплообменников, материальных потоков и затрат тепла.
НАЗНАЧЕНИЕ И ОБЛАСТЬ ПРОЕКТИРУЕМОГО ОБЪЕКТА
Колонные аппараты предназначены для проведения процессов тепло- и массообмена: ректификации, дистилляции, абсорбции, десорбции. Корпуса стандартизованных колонных аппаратов изготавливаются в двух исполнениях:
Ø Корпус, собираемый из отдельных царг с фланцевыми соединениями, рассчитан на давление 1,6 МПа.
Ø Корпус цельносварной, рассчитанный на давление до 4 МПа, имеют колонные аппараты диаметром более 1000мм с интервалом изменения диаметра через 200мм. Расстояния между тарелками в зависимости от типов могут изменяться от 300 до 1000мм.
До настоящего времени не выработано обобщенных и достаточно объективных критериев выбора типа тарелки для ведения того или иного процесса. Существенную роль в этом играют сложившиеся в организациях – поставщиках традиции, опирающиеся на многолетний опыт надежной эксплуатации разрабатываемой ими массообменной аппаратуры.
Тарелки с капсульными колпачками получили наиболее широкое распространение, благодаря своей универсальности и высокой эксплуатационной надежности, они достаточно эффективны, но металлоемки и сложны в монтаже.
Тарелки, собираемые из S – образных элементов, устанавливаются преимущественно в колоннах больших диаметров. Их производительность на 20-30% выше, чем у капсульных.
Клапанные тарелки, по сравнению с колпачковыми, имеют более высокую эффективность и на 20-40% большую производительность. Они применяются для обработки жидкостей, не склонных к смолообразованию и полимеризации, во избежание прилипания клапана к тарелке.
Ситчатые тарелки имеют достаточную высокую эффективность, низкое сопротивление и малую металлоемкость. Они применяются преимущественно в колоннах для обработки чистых жидкостей при атмосферном давлении и вакууме.
Решетчатые тарелки провального типа имеют производительность в 1,5 – 2 раза большую, чем колпачковые тарелки, низкую металлоемкость. Их эффективность достаточно высока, но в узком диапазоне рабочих скоростей. Эти тарелки рекомендуется применять при больших нагрузках колонны по жидкости.
Двойное оплодотворение у цветковых растений: Оплодотворение - это процесс слияния мужской и женской половых клеток с образованием зиготы...
История развития пистолетов-пулеметов: Предпосылкой для возникновения пистолетов-пулеметов послужила давняя тенденция тяготения винтовок...
Биохимия спиртового брожения: Основу технологии получения пива составляет спиртовое брожение, - при котором сахар превращается...
История создания датчика движения: Первый прибор для обнаружения движения был изобретен немецким физиком Генрихом Герцем...
© cyberpedia.su 2017-2024 - Не является автором материалов. Исключительное право сохранено за автором текста.
Если вы не хотите, чтобы данный материал был у нас на сайте, перейдите по ссылке: Нарушение авторских прав. Мы поможем в написании вашей работы!