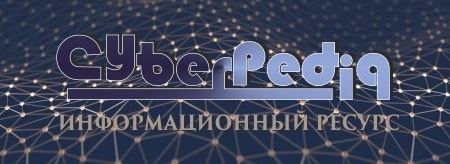
Индивидуальные очистные сооружения: К классу индивидуальных очистных сооружений относят сооружения, пропускная способность которых...
Археология об основании Рима: Новые раскопки проясняют и такой острый дискуссионный вопрос, как дата самого возникновения Рима...
Топ:
Проблема типологии научных революций: Глобальные научные революции и типы научной рациональности...
Определение места расположения распределительного центра: Фирма реализует продукцию на рынках сбыта и имеет постоянных поставщиков в разных регионах. Увеличение объема продаж...
Характеристика АТП и сварочно-жестяницкого участка: Транспорт в настоящее время является одной из важнейших отраслей народного хозяйства...
Интересное:
Распространение рака на другие отдаленные от желудка органы: Характерных симптомов рака желудка не существует. Выраженные симптомы появляются, когда опухоль...
Влияние предпринимательской среды на эффективное функционирование предприятия: Предпринимательская среда – это совокупность внешних и внутренних факторов, оказывающих влияние на функционирование фирмы...
Искусственное повышение поверхности территории: Варианты искусственного повышения поверхности территории необходимо выбирать на основе анализа следующих характеристик защищаемой территории...
Дисциплины:
![]() |
![]() |
5.00
из
|
Заказать работу |
|
|
Технологичность – это комплексный параметр оценивающий целесообразность затрат на производство, эксплуатацию, обслуживание, ремонт и утилизацию изделия.
Проведем анализ технологичности вала редуктора отбора мощности по следующим признакам:
1) Легкосъемность – съем детали затруднен, так как чтобы извлечь деталь необходимо извлечь редуктор отбора мощности, установленный между двигателем и гидротрансформатором;
2) Регулируемость – регулировка прокладками и втулками невозможна;
3) Обслуживаемость – охлаждение и смазывание узла производится через специальный бачок, в который заливается масло;
4) Унификация – в сборочном узле используют унифицированные цилиндрические поверхности и элементы (резьбовые, шлицевые и шпоночные), что упрощает выбор их изготовления;
6) Равнопрочность – при проектировании предусматривается, чтобы ресурс изнашивающихся деталей был не меньше межремонтного ресурса или был кратен ему.
Деталь – вал изготовлена из легированной стали 40Х. Заготовкой для вала служит поковка. С точки зрения механической обработки деталь имеет следующие недостатки: наличие большого количества конструктивных элементов (2 отв.; 8 фасок; 3 резьбы; 1 шпон. паз, 2 выточки,) и минимальная шероховатость Ra=0,32 мкм с точностью IT6.
В остальном деталь достаточно технологична, допускает применения высокопроизводительных режимов обработки, имеет хорошие базовые поверхности для первоначальных операций. Деталь обладает достаточной жесткостью для обеспечения высокой точности обработки. Точность обработки и шероховатость отвечают применяемости для изготовления на используемых в базовом варианте техпроцесса станках. Контролируемые размеры детали доступны для измерения.
|
Разработано несколько вариантов восстановления вала: наплавка под флюсом легированной проволокой, наплавка в ленточным электродом, вибродуговая наплавка в воздушной среде.
Существует два основных способа восстановления резьбы: метод ремонтных размеров (если это возможно) или наплавка с последующим нарезанием новой резьбы требуемого размера.
Шлицевую поверхность восстанавливают наплавкой и последующей обработкой.
Выбор рационального способа устранения дефекта
Анализ типовых технологически процессов восстановления
Детали
Многообразие способов восстановления деталей позволяет один и тот же дефект устранять различными способами. Однако качество и стоимость восстановления будут различными.
Факторы, влияющие на выбор оптимального технологического процесса восстановления и упрочнения детали:
1. Сравнительная износостойкость;
2. Сравнительная усталостная прочность;
3. Прочность сцепления покрытия с основой;
4. Дефицитность и величина затрат на материалы;
5. Трудоемкость операций восстановления
6. Величина производственных затрат на восстановление детали и сопряжения;
7. Относительная себестоимость восстановления детали и сопряжения
Основным показателем оценки экономической эффективности восстановления изношенных деталей и определение целесообразности применения того или иного способа восстановления и упрочнения служит относительная себестоимость. Относительная себестоимость восстановления детали, отнесённая к сроку службы ее после ремонта. Этот показатель является наиболее комплексным и обобщающим, так как он отражает не только все элементы затрат, но и срок службы деталей после их восстановления.
Первоначально для каждого дефекта детали определяется рациональный способ восстановления. Рациональным способы называют такой способ который обеспечивает максимальный ресурс работы детали и минимальные затраты труда и материалов.
|
Восстановление шлицевой поверхности может производиться следующими способами:
1) Ручная наплавка:
1.1) Дуговая;
1.2) Газовая;
1.3) Аргоно-дуговая;
2) Наплавка под слоем флюса:
2.1) Плавленным флюсом;
2.2) Керамическим флюсом;
2.3) Легированной проволокой;
3) Наплавка в среде СО2:
3.1) Без охлаждения;
3.2) С добавкой аргона;
3.3) Ленточным электродом;
4) Вибродуговая наплавка:
4.1) В жидкой среде;
4.2) В среде СО2;
4.3) В среде пара;
4.4) В воздушной среде;
4.5) Порошковой проволокой;
4.6) С термомеханической обработкой;
4.7) Под слоем флюса.
Восстановление резьбы может производиться следующими способами:
1) Ручная наплавка:
1.1) Газовая;
1.2) Аргоно-дуговая;
2) Наплавка в среде СО2:
2.1) Без охлаждения;
2.2) С добавкой аргона;
3) Вибродуговая наплавка:
3.1) В жидкой среде;
3.2) В среде СО2;
3.3) В среде пара;
3.4) В воздушной среде;
3.5) Порошковой проволокой;
3.6) С термомеханической обработкой;
3.7) Под слоем флюса.
4) Методом ремонтных размеров;
Ручная дуговая наплавка производится с использованием пластичных трещиностойких электродов, позволяющих наплавлять неограниченное число слоев. Для придания специальных свойств рабочим поверхностям изношенных деталей, при необходимости, последний слой выполняется специальными электродами. При ручной газовой наплавке расплавление основного и присадочного материала осуществляется теплом, выделяющимся в процессе сгорания горючих газов (ацетилена, пропанбутановых смесей и др.) в среде кислорода. При аргонно-дуговой наплавке в качестве защитного газа используется аргон - инертный газ, надежно защищающий зону наплавки от кислорода и азота (воздуха). В ряде случаев для устойчивости горения дуги к аргону добавляют различные активные газы.
При наплавке под слоем флюса дуга горит не на открытом воздухе, а в закрытой полости, защищенной от действия атмосферы эластичной коркой расплавленного шлака. В этом случае флюс, выполняя роль электродного покрытия, надежно закрывает место сварки и предотвращая возможность разбрызгивания жидкого металла. Этот способ сварки устраняет целый ряд недостатков электродуговой сварки, вследствие чего качество сварного шва получается значительно выше, так как металл более однороден по химическому составу, а плотность шва увеличивается. По способу изготовления флюсы делятся на плавленые, получаемые путем сплавления компонентов шихты в печах, и неплавленые, или керамические. Наличие различных ферросплавов в составе керамического флюса при наплавке способствует получению легированного наплавленного металла, в то время как при использовании плавленых флюсов легирующие примеси вводятся только через легированную электродную проволоку. Также при наплавке под флюсом используют специальные легированные электроды, состоящие из наплавляемого металла, в сердцевине которого имеется флюс.
|
Сущность наплавки в среде СО2 состоит по сути в том, что расплавленный металл защищаются от вредного влияния воздуха струей углекислого газа, подаваемого в сварочную зону. Под действием высокой температуры углекислый газ разлагается на окись углерода и атомарный кислород. Окись углерода не растворима в жидком металле и защищает сварочную ванну от насыщения атмосферными газами, т. е. предупреждает образование пористости шва. Атомарный же кислород взаимодействует с содержащимися в сварочной проволоке элементами-раскислителями (Mn, Si) и образует на поверхности сварочной ванны флюсовую пленку из их окислов. Последняя выполняет роль дополнительной защиты сварочной ванны при случайном нарушении сплошности потока углекислого газа, вызываемой порывами ветра, резкими движениями сварочной горелки и другими причинами.
Сущность вибродуговой наплавки состоит в том, что деталь, вращающаяся в центрах токарного станка, наплавляется с помощью специальной головки. Головка обеспечивает подачу на деталь и вибрацию электродной проволоки диаметром 1,0—3,0 мм. К детали и проволоке подводится напряжение от источника питания. Для уменьшения зоны термического влияния и коробления наплавляемых деталей, а также увеличения твердости наплавленного слоя в зону дуги и на деталь подается охлаждающая жидкость — водный раствор кальцинированной соды. Охлаждающая жидкость защищает также расплавленный металл от окисления и азотирования. Вибрация электрода осуществляется с помощью электромагнитного вибратора, включенного в цепь переменного тока с частотой 50 пер/сек., или с помощью механического вибратора. Частота вибрации электрода при использовании электромагнитного вибратора составляет 100 Гц. Механические вибраторы в зависимости от их конструкций могут обеспечивать различную частоту вибрации. В результате вибрации электрода в процессе наплавки происходит чередование периодов горения дуги и короткого замыкания. Основная часть тепла (98—99,5%), идущая на расплавление электродной проволоки и детали, выделяется при горении дуги. Во время горения дуги на конце электрода образуются капли расплавленного металла, которые переходят на деталь преимущественно при коротких замыканиях. Таким образом, вибрация электрода способствует переносу электродного металла на деталь в виде мелких порций, облегчающих формирование тонких наплавленных слоев. Кроме того, вибрация способствует стабилизации процесса путем частых возбуждений дуговых разрядов, происходящих в каждый момент размыкания цепи (отрыва электрода от детали). В зависимости от среды, бывают различные процессы вибродуговой наплавки.
|
При ремонте методом ремонтных размеров одну из износившихся деталей соединения обрабатывают до исчезновения следов износа или до получения определенного заранее установленного размера, а вторую, чаще всего более дешевую, заменяют новой. Например, изношенную шейку вала обрабатывают до исчезновения следов износа и комплектуют ее с новой втулкой, обеспечивающей с полученным размером шейки вала требуемую посадку. Такой ремонт может производиться последовательно несколько раз, причем диаметр вала постепенно будет уменьшаться, а диаметр отверстия ремонтируемой детали — увеличиваться. Таким образом, детали сопряжения будут иметь размеры, отличающиеся от первоначальных. Эти новые, заранее установленные размеры деталей соединения принято называть ремонтными.
|
|
Эмиссия газов от очистных сооружений канализации: В последние годы внимание мирового сообщества сосредоточено на экологических проблемах...
Двойное оплодотворение у цветковых растений: Оплодотворение - это процесс слияния мужской и женской половых клеток с образованием зиготы...
Архитектура электронного правительства: Единая архитектура – это методологический подход при создании системы управления государства, который строится...
Кормораздатчик мобильный электрифицированный: схема и процесс работы устройства...
© cyberpedia.su 2017-2024 - Не является автором материалов. Исключительное право сохранено за автором текста.
Если вы не хотите, чтобы данный материал был у нас на сайте, перейдите по ссылке: Нарушение авторских прав. Мы поможем в написании вашей работы!