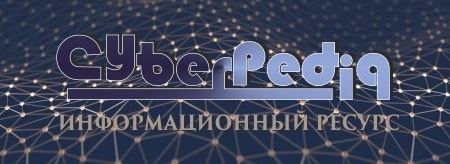
История создания датчика движения: Первый прибор для обнаружения движения был изобретен немецким физиком Генрихом Герцем...
Двойное оплодотворение у цветковых растений: Оплодотворение - это процесс слияния мужской и женской половых клеток с образованием зиготы...
Топ:
Оснащения врачебно-сестринской бригады.
Организация стока поверхностных вод: Наибольшее количество влаги на земном шаре испаряется с поверхности морей и океанов...
Генеалогическое древо Султанов Османской империи: Османские правители, вначале, будучи еще бейлербеями Анатолии, женились на дочерях византийских императоров...
Интересное:
Наиболее распространенные виды рака: Раковая опухоль — это самостоятельное новообразование, которое может возникнуть и от повышенного давления...
Уполаживание и террасирование склонов: Если глубина оврага более 5 м необходимо устройство берм. Варианты использования оврагов для градостроительных целей...
Мероприятия для защиты от морозного пучения грунтов: Инженерная защита от морозного (криогенного) пучения грунтов необходима для легких малоэтажных зданий и других сооружений...
Дисциплины:
![]() |
![]() |
5.00
из
|
Заказать работу |
|
|
Недостатки сварки под слоем флюса можно устранить, используя для защиты зоны сварки газ. Обычно применяют аргон, гелий, углекислый газ или смесь этих газов с кислородом. Характеристики поставки аргона и углекислого газа приведены в табл. 11.2.
Таблица 11.2. Характеристики поставки аргона и углекислого газа | ||||
Защитный газ | Свариваемые материалы | Цвет окраски баллона | Давление газа в баллоне | |
Обозначение | Сорт (чистота газа) | |||
Ar | Высший сорт (99,992%) | Активные и тугоплавкие металлы и сплавы цветных металлов | Серый | 15 МПа |
Первый сорт (99,987%) | Высоколегированные стали | |||
CO2 | Cварочный (99,5%) | Углеродистые и низколегированные стали | Черный | 7 МПа (сжиженный) |
Принципиальная схема установки для сварки в среде углекислого газа показана на рис. 11.5, а. Омедненная сварочная проволока 5 (плавящийся электрод), намотанная на кассету 4, подается роликовым механизмом 3 в зону сварки. Дуга 9 зажигается между заготовкой 1 и сварочной проволокой. Источник питания 8 обеспечивает постоянное напряжение сварки и высокочастотное импульсное напряжение зажигания дуги. Напряжение на сварочную проволоку передается через контактный мундштук 6. Защитный газ из баллона через редуктор подается в зону сварки по патрубку 7.
Рис. 11.5.Сварка в среде защитных газов:
а — установка для сварки в среде углекислого газа; б — установка для сварки в среде аргона; 1 — заготовка; 2 — сварочная ванна; 3 — роликовый механизм; 4 — кассета; 5 — сварочная проволока (электрод); 6 — контактный мундштук; 7 — патрубок; 8 — источник питания; 9 — дуга; 10 — сварной шов; 11 — присадочная проволока
|
Установка для аргонодуговой сварки (АДС) имеет аналогичную схему, но может отличаться применением неплавящегося электрода 5 и подачей в зону сварки присадочной проволоки 11 (рис. 11.5, б).
Сварку в среде углекислого газа проводят на постоянном токе прямой полярности. Под действием высокой температуры дуги углекислый газ разлагается: 2СО2 = 2СО + О2. Поэтому электродная проволока должна содержать элементы-раскислители (сталь Св08ГС, сталь Св10Г2С и др.). Сварку ведут на токах повышенной плотности (80… 100 А/мм2). При сварке наблюдается крупнокапельный перенос металла и значительное разбрызгивание. Для уменьшения разбрызгивания применяют смесь углекислого газа (80%) и кислорода (20%).
Аргонодуговая сварка плавящимся электродом используется для сварки металла толщиной 1…20 мм. Основные параметры: диаметр сварочной проволоки — 0,6…3,0 мм; ток сварки I св = 12…250 А; напряжение дуги U д = 20…30 В; скорость сварки — 0,2… 4,0 м/мин. Сварку выполняют на постоянном токе обратной полярности.
Аргонодуговая сварка неплавящимся электродом используется для сварки металла толщиной 0,8…10,0 мм. Основные параметры: диаметр сварочной проволоки — 0,5…6,5 мм; ток сварки I св = 10…600 А; напряжение дуги U д = 10…30 В; скорость сварки — 0,1…0,8 м/мин. Сварку выполняют на переменном или постоянном токе обратной полярности. Сварку сталей часто производят в смеси газов: аргон и 1% кислорода.
Газовая сварка
Газовая сварка — сварка плавлением, при которой место сварки нагревают высокотемпературным газовым пламенем.
Газовое пламя при сварке получают при сгорании горючего газа (ацетилен, пропан) в атмосфере технически чистого кислорода.
|
Кислород поставляется в баллонах голубого цвета с надписью черного цвета «Кислород». При давлении 15 МПа в баллоне помещается 600 л кислорода.
Кислородная аппаратура не должна контактировать с маслом. При контакте масла с кислородом происходит взрыв с образованием воронки глубиной до 5 м!
Ацетилен поставляется в баллонах белого цвета с надписью красного цвета «Ацетилен».
Ацетилен взрывоопасен!
Поэтому баллон заполнен активированным углем и ацетоном. Растворенный в ацетоне ацетилен, пропитавший пористую массу активированного угля, безопасен. Ацетилен можно получать в ацетиленовых генераторах (при реакции карбида с водой), однако этот способ чрезвычайно взрывоопасен.
Для понижения давления газа применяют газовые редукторы (рис. 11.6). Запорный клапан 3 редуктора находится под давлением запорной пружины 1 и давлением гибкой мембраны 7.
Рис. 11.6.Газовый редуктор:
1 — пружина; 2 — камера высокого давления; 3 — запорный клапан; 4 — камера низкого давления; 5 — нажимной диск; 6 — регулировочная пружина; 7 — гибкая мембрана; 8 — седло клапана; 9 — толкач
При нормальном рабочем давлении редуцированного газа в камере низкого давления 4 устанавливается равновесие, запорный клапан прижимается к седлу 8 запорной пружины и преграждает доступ газа из камеры высокого давления 2 (из баллона). Гибкая мембрана регулировочной пружиной 6 через нажимной диск 5 и толкач 9 воздействует на запорный клапан и стремится открыть его. Изменяя натяжение регулировочной пружины, можно менять рабочее давление.
Для сварки чаще всего используются наиболее безопасные газосварочные горелки инжекторного типа (рис. 11.7). Кислород под давлением 0,1…0,4 МПа через кислородный вентиль 4 поступает в инжектор 6. Выходя с большой скоростью из узкого канала инжектора, кислород подсасывает горючий газ, поступающий через вентиль 5. В смесительной камере 3 получается горючая смесь, которая через мундштук 2 подается к сменному наконечнику 1.
|
Рис. 11.7.Газосварочная инжекторная горелка:
1 — наконечник; 2 — мундштук; 3 — смесительная камера; 4 — кислородный вентиль; 5 — ацетиленовый вентиль; 6 — инжектор
Во избежание взрыва первым открывают кислородный вентиль, а по окончании сварки первым отключают горючий газ.
В сварочном производстве горелки подразделяются на семь номеров (табл. 11.3).
Таблица 11.3. Рекомендации по применению газовых горелок
Внешний вид и температура газового пламени зависят от соотношения объемов ацетилена и кислорода b = V (O2)/ V (C2H2). При b = 1,0…1,3 — нормальное пламя, при b = 1,5…1,7 — окислительное пламя, при b = 0,95 — науглероживающее пламя. Газовое пламя неоднородно по строению (рис. 11.8): зона 1 — ядро пламени; зона 2 — восстановительное пламя; зона 3 — факел.
Рис. 11.8.Строение газового пламени:
1 — ядро; 2 — восстановительное пламя; 3 — факел
Газокислороднаяя резка металлов заключается в сжигании нагретого металла в струе чистого кислорода. Для осуществления процесса резки необходимы следующие условия:
Наиболее полно этим условиям удовлетворяют низкоуглеродистые и низколегированные стали. При концентрации углерода 0,4…0,5% резка усложнена, более 1,2% — резка невозможна; при содержании в стали марганца 4…10% резка усложняется, более 14% — резка невозможна.
Газовый резак отличается от газовой горелки наличием дополнительного кислородного вентиля. Процесс резки осуществляется в два этапа: первый — нагрев зоны резки до температуры горения металла в кислороде (характеризуется появлением большого числа искр); второй — собственно резка (отключаются ацетилен и кислород из основной магистрали; дополнительным вентилем подключается кислород).
|
Электрическая контактная сварка
Контактная сварка — сварка давлением с кратковременным нагревом места соединения проходящим электрическим током (рис. 11.9).
Рис. 11.9.Схема контактной сварки:
F — сила прижима (проковки); R з — омическое сопротивление заготовок; R к — омическое сопротивление стыка; R эл — омическое сопротивление электрической цепи станка
Наибольший нагрев при контактной сварке наблюдается в стыке заготовок (R з + R эл << << R к, R з, Rэл, Rк — омические сопротивления заготовок, электрической цепи станка и стыка соответственно). В результате высокой плотности тока в зоне контакта металл разогревается до термопластического состояния или до оплавления. При непрерывном сдавливании заготовок происходит сближение поверхностей до расстояний, меньших межатомных, — происходит сварка.
Различают стыковую, точечную, шовную и рельефную сварки.
Стыковая сварка
При стыковой сварке заготовки соединяются по всей поверхности соприкосновения. Сварочная машина показана на рис. 11.10. На станине 6 установлены две плиты: неподвижная 7 и подвижная 3, перемещаемая по направляющим 4. Заготовки 2 устанавливаются в прижимах 1. Сварочный ток подается от трансформатора 5.
Рис. 11.10.Машина для стыковой сварки:
1 — прижим; 2 — заготовки; 3 — подвижная плита; 4 — направляющая; 5 — сварочный трансформатор; 6 — станина; 7 — неподвижная плита; F — сила проковки
Различают сварку сопротивлением (нагрев торцов заготовок до термопластического состояния) и сварку оплавлением (нагрев торцов до оплавления).
Процесс сварки сопротивлением идет в три этапа: предварительный прижим заготовок; разогрев торцов; проковка (прижим заготовок и выдержка). Этим способом сваривают заготовки сечением до 100 мм2. Сечения заготовок должны быть одинаковы по форме (рис. 11.11, а), очищены от оксидов и иметь минимальный периметр. Этим методом сваривают низкоуглеродистые и низколегированные стали, алюминиевые и медные сплавы.
Рис. 11.11.Требования к заготовке при стыковой сварке:
а — при сварке сопротивлением; б — при сварке оплавлением; в — появление грата
|
Сварка оплавлением ведется при непрерывном оплавлении торцов заготовок. Для этого между заготовками оставляют небольшой зазор, подключают напряжение и равномерно их сближают. Расплавленный и кипящий металл выбрасывается наружу. После достижения равномерного оплавления по всей поверхности стыка проводят проковку. При прерывистом оплавлении несколько раз сближают и рассоединяют заготовки, прежде чем достигается быстрое оплавление поверхностей стыка, затем проводят проковку.
Сварка оплавлением не требует тщательной подготовки торцов заготовок (рис. 11.11, б), однако расплавленный металл, застывая, образует грат (рис. 11.11, в), который необходимо удалять механическим способом. Сварка оплавлением позволяет сваривать заготовки с различными сечениями из разнородных металлов.
Точечная сварка
Точечная сварка позволяет соединять листовые и иные заготовки внахлест. Перед началом сварки контактные поверхности зачищают и обезжиривают. Заготовки 1 устанавливают между нижним и верхним электродами сварочной машины (рис. 11.12, а). Затем заготовки сжимают и подают ток. Прогрев осуществляют до появления жидкой точки 2 между контактными поверхностями, после чего производят проковку. Для соединения заготовок одновременно в двух точках применяют одностороннюю сварку. Заготовки устанавливают на медную плиту 3 (рис. 11.12, б) и прижимают электродами, расположенными с одной стороны заготовок. Процесс сварки идет в три этапа: предварительный прижим заготовок; разогрев торцов; проковка (прижим заготовок и выдержка). Различают сварку на мягких и жестких режимах (табл. 11.4). Мягкие режимы применяются в бытовых сварочных машинах. В промышленности применяют жесткие режимы, это позволяет сваривать коррозионно-стойкие стали, алюминиевые и медные сплавы.
Рис. 11.12.Точечная сварка:
а — схема сварки; б — схема односторонней сварки; 1 — заготовки; 2 — сварочная точка; 3 — плита; F — сила прижима (проковки)
Таблица 11.4. Режимы точечной сварки | |||
Режим | Плотность тока, А /мм2 | Усилие на электродах, кН | Продолжитель-ность протекания тока, с |
Мягкий | 80…160 | 0,06…1,50 | 0,5…3,0 |
Жесткий | 120…360 | 0,09…3,00 | 0,001…0,01 |
Точечная сварка не позволяет получить непрерывный шов. Минимальное расстояние между сварными точками должно быть более 10 суммарных толщин свариваемых листов. В противном случае произойдет шунтирование, т. е. ток пойдет через ранее полученную сварочную точку.
Роликовая (шовная) сварка
Роликовая сварка предназначена для соединения листовых материалов непрерывным швом. Для этого заготовки размещают между вращающимися роликами-электродами (рис. 11.13, а). Шовную сварку, так же, как и точечную, можно выполнять при одностороннем расположении электродов (рис. 11.13, б).
Рис. 11.13.Роликовая (шовная) сварка:
а — схема сварки: 1 — заготовка; 2 — сварочный шов; б — схема односторонней сварки; F — сила прижима (проковки)
Различают непрерывную (с постоянной подачей сварочного тока) и импульсную (с импульсной подачей сварочного тока) роликовую сварку.
При непрерывной сварке происходит перегрев металла шва и околошовной зоны, что отрицательно сказывается на качестве шва и работоспособности роликов.
При импульсной подаче тока перегрева металла не происходит. Необходимо, чтобы сварочные точки перекрывали друг друга на 1/3 или на 1/4 их диаметра. Из-за большого влияния шунтирования нецелесообразно сваривать листы суммарной толщиной более 3 мм.
Пайка
Пайка — способ образования неподвижных соединений за счет смачивания твердых поверхностей более легкоплавким расплавленным металлом (припоем).
При смачивании устанавливаются межатомные связи между соединяемыми деталями и припоем. С помощью пайки ведут сборку различных типов соединений: внахлест, встык, тавровых, телескопических.
Паяное соединение состоит из трех зон: припой и две диффузионные зоны «припой—соединяемый металл». Для обеспечения смачивания припоем паяных поверхностей необходимо удаление жировых и оксидных пленок. Удаление пленок ведут механическим (стальными щетками, абразивной или ультразвуковой обработкой) или химическим (травление) путем.
Элементами паяного соединения являются:
Технологический процесс пайки включает в себя:
Припой — чистый металл или сплав, вводимый в зазор между паяными поверхностями.
Для низкотемпературной пайки обычно применяют припои на основе сплава «олово—свинец». Припои специального назначения имеют добавки: Ga, In, Bi, Cd, Sb, Cb, Ag, Au. Характеристика и назначение некоторых припоев приведена в табл. 11.5.
Таблица 11.5. Припои | ||||
Вид | Марка | Компоненты, % | Температура плавления, °С | Область применения |
Низкотемпературная пайка | ||||
Оловянисто-свинцовые | ПОС40 | Sn-40 Pb-60 | 220 | Радиаторы автомобилей |
Оловянисто-свинцовые сурьмянистые | ПОССу30-2 | Sn-30 Pb-68 Sb-2 | 250 | Электро- арматура |
Висмутовые | Сплав Вуда | Bi-50, Pb-25 Sn-12,5,Cd-12,5 | 74 | Медь и ее сплавы |
Галлиевые | Г15 | Ga-60, Cu-30 In-10 | — | Паста для пайки Al и его сплавов |
Цинковые | ПКЦ | Zn-60, Cd-40 | 300 | Al и его сплавы |
Высокотемпературная пайка | ||||
Медные | М0 — М4 | Cu около 100 | 1 083 | Сталь, металлокерамика |
Медно-цинковые | Л68 | Cu-68 Zn-32 | 940 | Сталь |
Жаропрочные | ВПр1 | Cu-67,5 Ni-29 Si-1,8 Fe-1,5 B-0,2 | 1 120 | Жаропрочные стали |
Флюсы — химические вещества, используемые для разрушения оксидных пленок; улучшения смачиваемости паяных поверхностей и для их защиты от окисления.
Флюсы должны иметь высокую жидкотекучесть, стабильность химического состава и активность в широком интервале температур расплавленного припоя, минимальное химическое взаимодействие с паяными металлами. Флюсы и продукты их взаимодействия должны легко удаляться промывкой или испарением после пайки.
Для низкотемпературной пайки медных или покрытых серебром проводников применяют канифоль и стеарино-парафиновые (нейтральные) флюсы. Для пайки стали, меди, никеля используют пасты на основе вазелина (10…15% ZnCl2 или NH4Cl); для высоколегированных сталей и нержавеющих сталей применяют 25…30%-ный раствор ZnCl2 в воде (кислотный флюс — хорошо растворяет оксидные пленки, но требует тщательной промывки место спая в воде).
По механизму образования соединения различают:
Нагрев припаиваемых деталей производят:
Восстановление разрушенных и изношенных деталей
|
|
Автоматическое растормаживание колес: Тормозные устройства колес предназначены для уменьшения длины пробега и улучшения маневрирования ВС при...
История развития хранилищ для нефти: Первые склады нефти появились в XVII веке. Они представляли собой землянные ямы-амбара глубиной 4…5 м...
Особенности сооружения опор в сложных условиях: Сооружение ВЛ в районах с суровыми климатическими и тяжелыми геологическими условиями...
Состав сооружений: решетки и песколовки: Решетки – это первое устройство в схеме очистных сооружений. Они представляют...
© cyberpedia.su 2017-2024 - Не является автором материалов. Исключительное право сохранено за автором текста.
Если вы не хотите, чтобы данный материал был у нас на сайте, перейдите по ссылке: Нарушение авторских прав. Мы поможем в написании вашей работы!