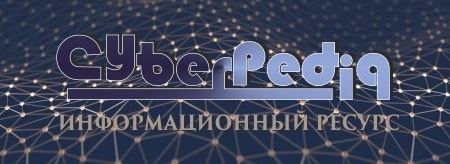
Индивидуальные очистные сооружения: К классу индивидуальных очистных сооружений относят сооружения, пропускная способность которых...
Наброски и зарисовки растений, плодов, цветов: Освоить конструктивное построение структуры дерева через зарисовки отдельных деревьев, группы деревьев...
Топ:
Марксистская теория происхождения государства: По мнению Маркса и Энгельса, в основе развития общества, происходящих в нем изменений лежит...
Оценка эффективности инструментов коммуникационной политики: Внешние коммуникации - обмен информацией между организацией и её внешней средой...
Методика измерений сопротивления растеканию тока анодного заземления: Анодный заземлитель (анод) – проводник, погруженный в электролитическую среду (грунт, раствор электролита) и подключенный к положительному...
Интересное:
Как мы говорим и как мы слушаем: общение можно сравнить с огромным зонтиком, под которым скрыто все...
Инженерная защита территорий, зданий и сооружений от опасных геологических процессов: Изучение оползневых явлений, оценка устойчивости склонов и проектирование противооползневых сооружений — актуальнейшие задачи, стоящие перед отечественными...
Принципы управления денежными потоками: одним из методов контроля за состоянием денежной наличности является...
Дисциплины:
![]() |
![]() |
5.00
из
|
Заказать работу |
|
|
Тепловые процессы, классификация, движущая сила. Виды переноса тепла. Способы интенсификации процессов.
Тепловыми процессами называются такие технологические процессы, в которых материал нагревается или охлаждается, а скорость их протекания определяется скоростью подвода или отвода тепла.К тепловым процессам относятся:
нагревание – процесс повышения температуры материала путем подвода тепла;
охлаждение – процесс понижения температуры материала путем отвода тепла;
испарение – процесс перевода жидкости в парообразное состояние путем подвода тепла;
конденсация – процесс перевода пара в жидкое состояние путем отвода тепла.
Классификация тепловых процессов
Теплопроводность – это перенос тепла вследствие беспорядочного движения микрочастиц непосредственно соприкасающихся друг с другом. Тепло распространяется по всему телу со скоростью, зависящей от свойств тела и разности температур между отдельными его участками.
Конвективный перенос теплоты (конвекция) — процесс переноса теплоты от стенки к движущейся относительно нее жидкости (газу) или от жидкости (газа) к стенке. Таким образом, он обусловлен массовым движением вещества и происходит одновременно путем теплопроводности и конвекции дома батареи греют комнату
Тепловое излучение – перенос энергии с помощью электромагнитных волн инфракрасной части спектра..
Движущей силой всякого переноса массы или энергии является разность потенциалов, характерных для данного процесса. Эта разность является мерой удаленности системы от состояния равновесия.
Задачи интенсификации теплообмена обычно сводятся: - к уменьшению габаритов и массы теплообменных устройств, - к снижению температурного напора, т. е. к снижению температуры стенок при заданной температуре теплоносителя или к увеличению температуры теплоносителя при заданной температуре стенок.
|
Основными способами интенсификации конвективного теплообмена в теплообменных аппаратах являются: 1. Изменение термического сопротивления. 2. Изменение скорости потока. 3. Использование развитых поверхностей теплообмена путем оребрения и ошиповки. Оребрение поверхности применяется со стороны теплоносителя, обладающего меньшим коэффициентом 11 теплоотдачи. 5. Уменьшение геометрических размеров поверхности теплообмена. 6. Применение пластинчатых и спиральных теплообменников.
1.
Перенос тепла за счет теплопроводности. Закон Фурье. Конвективный теплообмен. Закон Ньютона.
Перенос тепла осуществляется в направлении, противоположном градиенту температуры. Закон Фурье устанавливает, что количество тепла Qт, Дж, передаваемое теплопроводностью за время t через поверхность площадью F, перпендикулярную градиенту температуры, пропорционально значениям площади поверхности, времени и градиента температуры:
Теплопроводность веществ зависит от их природы, агрегатного состояния и температуры, а для газов – и от давления.
Дифференциальное уравнение теплопроводности Фурье получают, рассматривая приход и расход тепла через грани элементарного параллелепипеда объёмом dV c рёбрами dx, dy и dz. Полное приращение количества тепла в элементарном объёме dQ представляет собой сумму приращений количества тепла вдоль осей x, y и z x dQ, y dQ и z
При конвекции процесс переноса теплоты неразрывно связан с переносом самой среды. Поэтому конвекция возможна лишь в жидкостях и газах, частицы которых легко могут перемещаться. Передача теплоты конвекцией осуществляется перемещением в пространстве неравномерно нагретых объемов жидкости или газов. Обычно при инженерных расчетах рассматривается конвективный теплообмен между жидкостью (газом) и твердой стенкой, называемый теплоотдачей Согласно закону Ньютона – Рихмана тепловой поток Q*, от жидкости к стенке пропорционален поверхности теплообмена и разности температур между температурой жидкости tж и температурой твердой стенки tc: Q* = a(tж - t с)F, Вт.
|
Тепло- и хладоносители, используемые в пищевой промышленности. Требования предъявляемые к ним, их характеристика. Определение расхода.
Самый распространенный промышленный теплоноситель — насыщенный водяной пар, горячая вода широко используется в качестве теплоносителя. К достоинствам воды как теплоносителя следует отнести доступность и дешевизну, значения коэффициентов теплоотдачи. К недостаткам этого теплоносителя относятся сравнительно небольшая удельная теплоемкость Топочные газы широко используются в схемах утилизации теплоты на предприятиях, имеющих собственные котельные при атмосферном давлении, что позволяет использовать промежуточный теплоноситель для обогрева в теплообменных аппаратах. В качестве промежуточного теплоносителя можно использовать воздух или минеральное масло. К недостаткам топочных газов вызывание загрязнение поверхности теплообмена и низкий коэффициент теплоотдачи.
Расчет теплообменника
Теплообменный аппарат проектируется на основании:
Теплового расчета с определением площадей поверхности теплообменника,
Конструктивного расчета основных геометрических параметров агрегата и его узлов, Гидравлического расчета, определяющего потерю напора, Расчета тепловой изоляции оборудования, Подсчета экономической эффективности.
При расчете агрегата принимается во внимание основное его назначение – обмен тепловыми параметрами теплоносителя и обрабатываемой среды. На основе физических свойств теплоносителей выполняется расчет теплообменника труба в трубе с учетом различных характеристик агрегата и системы в целом. Для этого оцениваются следующие параметры:
уровень тепловых потерь, технологическая и тепловая схема, совокупность сопутствующих факторов, устанавливается расход теплоносителя,
определяются величины начальной и конечной температуры, определяется тепловая нагрузка, составляется баланс работоспособности системы.
Кроме этого необходимо учитывать степень агрессивного воздействия среды на материал, из которого изготавливается теплообменник, токсичность и физико-химические свойства. Важной частью расчета является определение направления движения теплоносителя.
|
Устройство и принцип работы
Корпус теплообменника выполняется в виде трубы, которая производится из одного или нескольких листов стали. Толщина металла зависит от максимального давления рабочей среды и температуры. Кромки кожуха - цилиндрические, объединяются с фланцами, которые необходимы для соединения с крышками и днищем. Устройство предусматривает наличие на поверхности специальных опор. Принцип работы бойлера кожухотрубного заключается в перемещении холодного и горячего теплоносителя по различным каналам. Теплообмен осуществляется между стенками таких каналов.
Расчет параметров
Пока не появились пластинчатые теплообменные агрегаты, кожухотрубные считались одними из самых малогабаритных. К тому же специфика конструкции такая, что температурная разница между кожухом и трубами ведет к образованию температурных напряжений. Чтобы устройство служило в течение длительного времени и соответствовало условиям эксплуатации, важно производить точный расчет. Для вычисления площади агрегата применяется следующая формула:
F – площадь поверхности теплообмена; tср – средняя разница температур между рабочими носителями; K – коэффициент теплопередачи; Q – количество теплоты.
Чтобы правильно выполнить этот расчет, потребуется предоставить инженерам следующие данные: максимальный расход греющей жидкости; физические показатели теплоносителя: плотность, вязкость, теплопроводность, теплоемкость при средней температуре, конечная температура. Перед тем, как купить кожухотрубных теплообменник, нужно знать его технические параметры: исполнение: горизонтальное или вертикальное; диаметр кожуха; тип трубных решеток; давление в кожухе и трубах; климатическое исполнение.
Многокорпусное выпаривание
При многократном выпаривании в качестве греющего используется вторичный пар и, следовательно, достигается значительная экономия тепла. Проведение подобного процесса возможно либо при использовании греющего пара высокого давления, либо при применении вакуума.
|
Сущность процесса состоит в том, что он проводится в несколько соединенных последовательно аппаратах, давление в которых поддерживают так, чтобы вторичный пар предыдущего аппарата мог быть использован как греющий пар в последнем аппарате.
Многокорпусные выпарные установки могут быть прямоточными, противоточными и комбинированными.
Наибольшее распространение в промышленных условиях получили прямоточные выпарные установки (рисунок 3).
Здесь греющий пар и выпариваемый раствор направляют в первый корпус, затем частично упаренный раствор самотеком перетекает во второй корпус и т.д.; вторичный пар первого корпуса направляют в качестве греющего пара во второй корпус и т.д.
Рисунок 3 - Многокорпусная прямоточная выпарная установка
Достоинства:
- нет необходимости в установке насосов для перекачивания кипящих растворов, т.к. перетекание раствора из корпуса в корпус благодаря разности давлений идет самотеком.
- температура кипения раствора и давление вторичных паров в каждом последующем корпусе ниже, чем в предыдущем, поэтому раствор в корпуса (кроме первого) поступает перегретым.
- теплота, которая выделяется при охлаждении раствора до tкип. В последнем корпусе идет на дополнительное испарение растворителя из этого же раствора. Это явление называется самоиспарение.
Недостатки: - понижение tкип и увеличение концентрации раствора от первого корпуса к последнему, что увеличивает вязкость раствора и уменьшает теплоотдачу при кипении, а следовательно, приводит к уменьшению коэффициента теплопередачи и, как следствие, к увеличению общей поверхности теплообменника.
Выбор числа корпусов. С увеличением числа корпусов многокорпусной выпарной установки снижается расход греющего пара на каждый килограмм выпариваемой воды. Как было показано, в однокорпусном выпарном аппарате на выпаривание 1 кг воды приближенно расходуется 1 кг греющего пара. Соответственно в двухкорпусной выпарной установке наименьший расход греющего пара на выпаривание 1 кг воды должен составлять 1/2 кг, в трехкорпусной - 1/3 кг, в четырехкорпусной -.1/4 и т. д.
Т. обр., расход греющего пара на выпаривание 1 кг воды в многокорпусных выпарных установках приближенно обратно пропорционален числу корпусов.
В действительности расход греющего пара на 1 кг выпариваемой воды больше и практически в зависимости от числа корпусов выпарной установки.
Однако основной причиной, определяющей предел числа корпусов выпарной установки, является возрастание температурных потерь с увеличением числа корпусов. Для осуществления теплопередачи необходимо обеспечить в каждом корпусе некоторую полезную разность температур, т. е. разность температур между греющим паром и кипящим раствором, равную обычно не менее 5-7°С для аппаратов с естественной циркуляцией и не менее 3°С для аппаратов с принудительной циркуляцией.
|
Чем выше концентрация выпариваемого раствора, тем больше температурные потери и тем меньшее число корпусов м. б. последовательно соединено в одну установку. Вместе с тем чем интенсивней циркуляция раствора, тем меньше допустимая полезная разность тем-р в каждом корпусе и тем больше предельное число корпусов.
Оптимальное число корпусов можно определять с помощью расчета на ЭВМ.
Уравнение рабочих линий
Поскольку условия работы укрепляющей и исчерпывающей частей ректификационной колонны различны, то рассмотрим материальные балансы для них отдельно.
Для укрепляющей части колонны возьмем произвольное сечение Л—Л (см. рис. 5.30), которому соответствуют текущие концентрации х и у, и составим материальный баланс по НК для верха этой части колонны:
откуда
где L — количество флегмы, стекающей в верхней части колонны, причем
Количество поднимающихся по колонне паров
Так как по принятому допущению^ = хр, то уравнение (5.50) при подстановке в него соответствующих значений L и G принимает вид
откуда получаем уравнение рабочей линии укрепляющей части колонны
При х = хр у = хр, т.е. рабочая линия укрепляющей части колонны пересекает диагональ с абсциссой хр (второе допущение).
Обозначим , а
. Тогда уравнение (5.53) примет
вид соотношения у = Ах + В, которое является уравнением прямой линии. В нем А — тангенс угла наклона рабочей линии к оси абсцисс, а В — отрезок, отсекаемый рабочей линией на оси ординат.
19
Абсорбцией называют процесс поглощения газа жидким поглотителем, в котором газ растворим в той или иной степени. Обратный процесс - выделение растворенного газа из раствора - носит название десорбции.
В абсорбционных процессах (абсорбция, десорбция) участвуют две фазы - жидкая и газовая, и происходит переход вещества из газовой фазы в жидкую (при абсорбции) или, наоборот, из жидкой фазы в газовую (при десорбции). Таким образом, абсорбционные процессы являются одним из видов процессов массопередачи.
Движущая сила
Скорость процесса абсорбции характеризуется уравнением:
M= (2)
где –коэффициент массопередачи;
F–поверхность контакта фаз;
М-масса вещества, переносимого из фазы в фазу в единицу времени(нагрузку аппарата).
–величина средней движущей силы;
И уравнением
M= (3)
В этих уравнениях коэффициенты массопередачи определяются следующим образом:
(4) и
(5)
где –коэффициент массоотдачи от патока газа к поверхности контакта фаз;
–коэффициент массоотдачи от поверхности контакта фаз к потоку жидкости;
m–тангенс угла наклона линии равновесия;
Для хорошо растворимых газов величина m незначительна и мало также для диффузионное сопротивление в жидкой фазе.Тогда >>
и можно принять, что
.Для плохо растворимых газов можно пренебречь диффузионным сопротивлением газовой фазе (в этом случае значения m и
велики). Отсюда
>>
можно полагать, что
.
В уравнении 2 мольные концентрации газовой фазы могут быть заменены парциальным давлением газа, выраженнымв долях общего давления.Тогда
M= (6)
где –средняя движущая сила процесса, выраженная в единицах давления;
– коэффициент массопередачи, отнесённый к единице движущей силы, выражаемой через парциальные давления поглощаемого газа.
Если линия равновесия является прямой, то средняя движущая сила процесса выражается уравнением:
=
(7)
где =
и
=-
–движущая сила на концах абсорбционного аппарата;
– парциальные давления газа на входе в аппарат и на выходе в него;
и
– равновесные парциальные давления газа на входе в аппарат и на выходе из него.
Абсорберы - аппараты, в которых осуществляются абсорбционные процессы. Так как абсорбция протекает поверхности раздела фаз, то абсорберы должны иметь развитую поверхность соприкосновения между жидкостью и газом. По способу образования этой поверхности абсорберы разделяют на: поверхностные, плёночные, тарельчатые и насадочные.
Поверхностные абсорберы используют для поглощения хорошо растворимых газов (например, для поглощения хлористого водорода водой). В них газ проходит над поверхностью неподвижной или медленно движущейся жидкости. Так как поверхность соприкосновения в таких абсорберах мала, то устанавливают несколько последовательно соединённых аппаратов, в которых газ и жидкость движутся друг к другу. Для того чтобы жидкость перемещалась по абсорберам самотёком, каждый последующий по ходу жидкости аппарат располагают несколько ниже предыдущего. Для отвода тепла, выделяющегося при абсорбции, в аппаратах устанавливают змеевики, охлаждаемые водой или другим охлаждающим агентом, либо помещают абсорбер в сосуды с проточной водой.
Пластинчатый абсорбер состоит из двух систем каналов: по каналам большего сечения движутся противотоком газ и абсорбент, по каналам меньшего сечения движется охлаждающий агент (как правило вода). Пластинчатые абсорберы обычно изготавливают из графита, так как он является химически стойким материалом, хорошо проводящим тепло. Поверхностные абсорберы имеют ограниченное применение из-за их малой эффективности и громоздкости.
Плёночные абсорберы более эффективны и компактны, чем поверхностные. В плёночных абсорберах поверхностью контакта фаз является поверхность текущей плёнки жидкости.
В трубчатом абсорбере абсорбент на верхнюю трубную решётку, распределяется по трубам и стекает по их внутренней поверхности в виде тонкой плёнки. В аппаратах с большим числом труб для более равномерной подачи и распределения жидкости по трубам используют специальные распределительные устройства. Газ движется по трубам снизу вверх навстречу стекающей жидкой плёнке. Для отвода тепла по межтрубному пространству пропускают воду или другой охлаждающий агент.
Способы кристаллизации
Политермическая или изогидрическая кристаллизация идет при неизменном содержании воды в системе. Она характерна для веществ, растворимость которых при повышенных температурах заметно превышает их растворимость при более низких температурах, и происходит путем охлаждения пересыщенных растворов. Изотермическая кристаллизация происходит путем удаления растворителя из системы (испарении воды) при постоянной температуре, она характерна для веществ, мало изменяющих свою растворимость при изменении температуры. Испарение воды может производиться интенсивным способом при кипении раствора или при медленном поверхностном испарении. Высаливание - кристаллизация соли может быть достигнута введением в раствор веществ, уменьшающих ее растворимость. Таковыми являются вещества, содержащие одинаковый с данной солью ион, ил связывающие воду. Осаждение веществ из растворов с помощью реагентов - Если при этом образуется практически нерастворимый продукт реакции, он сразу осаждается из быстро пересыщающегося раствора. Если продукт реакции растворим, его кристаллизация начинается после достижения необходимого пересыщения и продолжается по мере подачи реагента (осадителя).
Вымораживание применяется преимущественно для выделения отдельных компонентов из естественных рассолов, например соленых озер, при этом кристаллизацию проводят охлаждением растворов до температуры ниже 0°С. Способ вымораживания используется для концентрирования растворов путем частичного удаления из них растворителя в виде льда. В этом случае кристаллизуется не соль, а растворитель - вода. Концентрируя морскую воду вымораживанием льда, получают 8% раствор соли, который используется для получения хлорида натрия.
Вакуум-кристаллизация. При вакуум-кристаллизации испарение растворителя происходит не путем подвода тепла через стенку, а за счет отдачи раствором своего физического тепла, которое расходуется на испарение части растворителя (приблизительно 10 вес. %). Пары откачиваются вакуум-насосом. Температура поступающего горячего насыщенного раствора снижается до температуры кипения раствора, соответствующей давлению в аппарате. Процесс протекает адиабатически.
Кристаллизация с испарением части растворителя в токе носителя (воздуха). При этом способе часть растворителя испаряется в движущийся непосредственно над раствором воздух. Одновременно раствор охлаждается.
Дробная, или фракционированная, кристаллизация. При наличии в растворе одновременно нескольких подлежащих извлечению веществ его подвергают дробной, или фракционированной, кристаллизации, создавая условия для последовательного осаждения этих веществ путем изменения температуры и концентрации раствора.
22 Материальный и тепловой балансы кристаллизации. Аппаратурное оформление процесса.
В токе инертного газа,
Выпариванием растворов,
В вакууме,
Перегонка. Основные понятия. Способы перегонки
Перегонка - один из наиболее часто используемых химиками методов как для идентификации, так и для очистки органических соединений. Температура кипения, определяемая при перегонке, одно из важных физических свойств соединения. Различные жидкие химические вещества имеют в большинстве случаев разную температуру кипения. Этот факт позволяет использовать дистилляцию для очистки целевого соединения от нелетучих (или менее летучих) примесей.
Наиболее часто в органическом синтезе используются следующие виды перегонки:
Простая перегонка (дистилляция) – способ разделения смеси жидких веществ, основанный на различной температуре кипения компонентов смеси. При этом отогнанный дистиллят обогащается низкокипящим компонентом, а остаток – высоко кипящим.
Область применения
1 Разделение жидких смесей веществ, значительно различающихся по температуре кипения (более 60 °С, менее: см. фракционная перегонка, перегонка с водяным паром, перегонка в вакууме). Но с температурой до 200 °С (более 200 °С вещества разлагаются и следует применять перегонку под вакуумом). Пример: разделение смеси эфир.Отделение жидкого вещества от нелетучих примесей (твердых компонентов). Пример: перегонка эфира над натрием (нелетуч).
2 Наиболее часто простая перегонка используется для очистки продажных растворителей
3 Наиболее часто простая перегонка используется для очистки продажных растворителей, температуры кипения основных химических растворителей можно посмотреть
Фракционная перегонка (дистилляция) – способ разделения смеси жидких веществ, основанный на различной температуре кипения компонентов смеси. При этом отогнанный дистиллят обогащается низкокипящим компонентом, а остаток – высоко кипящим. При этом виде перегонки используется дефлегматор, в котором при неполном охлаждении пара кипящей жидкости происходит частичная конденсация пара более высоко кипящей жидкости, обогащенный высоко кипящим компонентом промежуточный дистиллят (флегма) возвращается в колбу, а пар обогащается более низкокипящим веществом. При этом фракционная перегонка позволяет эффективно разделять смеси веществ с небольшой разницей в температурах кипения (~10-20 °C).
Проведение фракционной перегонки не отличается от проведения простой перегонки.
Область применения
1 Разделение жидких смесей веществ, незначительно различающихся по температуре кипения (менее 60 °С, для различающихся более 60 °С: см. также простая перегонка, перегонка в вакууме). Но с температурой до 200 °С (более 200 °С вещества разлагаются и следует применять перегонку под вакуумом). Пример: разделение смеси ацетон (т. кип. 56 °С)/вода (т. кип. 100 °С).
2 Отделение жидкого вещества от нелетучих примесей (твердых компонентов). Пример: перегонка эфира (т. кип. 35 °С) над натрием (нелетуч).
3 Часто фракционная перегонка используется для очистки продажных реактивов, для очистки и выделения полученных продуктов реакций.
Перегонка под вакуумом – способ разделения смеси жидких веществ, основанный на различной температуре кипения компонентов смеси в вакууме. Особое значение имеет при перегонке термолабильных веществ. В вакууме вещества кипят гораздо с меньшей температурой, приблизительное соответствие температуры в вакууме и при атмосферном давлении можно узнать из этой монограммы.
Область применения
1 Разделение жидких смесей веществ, различающихся по температуре кипения (менее 60 °С – с дефлегматором, с более 60 °С – простая перегонка) и имеющих высокую температуру кипения. Пример: выделение ДМСО из смеси ацетон (т. кип. 56 °С)/диметилсульфоксид (ДМСО) (т. кип. 189 °С с разложением при 1 атм., ~60 °С в вакууме водоструйного насоса без разложения).
2 Отделение высоко кипящего жидкого вещества от нелетучих примесей (твердых компонентов). Пример: перегонка ДМСО над гидридом кальция (не летуч).
3 Разделение смесей неразделимых при атмосферном давлении. Пример: разделение азеотропной смеси этанол/вода. Этанол кипит при 70 мм. рт. ст. при 28 °С без образования азеотропа с водой.
4 Часто перегонка под вакуумом используется для очистки продажных высоко кипящих растворителей, реактивов, для очистки и выделения термолабильных или высоко кипящих продуктов реакций.
Перегонка с водяным паром
Перегонка с водяным паром – способ разделения смеси веществ малорастворимых в воде и не взаимодействующих с ней, обладающих значительным давлением пара при температуре кипения воды. Такая перегонка уменьшает термическое воздействие на разделяемые вещества и приближается к вакуумной перегонке.
Область применения
1 Отделение продуктов реакции от смолообразных веществ. Пример: очистка смол различного состава, смазочных масел, эфирных масел, жирных кислот.
2 Перегонка чувствительных к нагреванию веществ. Пример: лимонен (т. кип. 178 °С) перегоняется с водяным паром (т. кип. 100 °С).
Камерные сушилки.
Эти сушилки являются аппаратами периодического действия, работающими при атмосферном давлении. Они используются в производствах для материалов, допускающих невысокую (до 250-300°С) температуру сушки, например, красителей, пищевых продуктов, лекарственных растительных препаратов. Материал в этих сушилках сушится на лотках, установленных на стеллажах или вагонетках, находящихся внутри сушильной камеры.
Туннельные сушилки.
Эти сушилки отличаются от камерных тем, что в них соединенные друг с другом вагонетки медленно перемещаются на рельсах вдоль очень длинной камеры прямоугольного сечения (коридора). На входе и выходе коридор имеет герметичные двери, которые одновременно периодически открываются для загрузки и выгрузки материала: вагонетка с высушенным материалом удаляется из камеры, а с противоположного конца в нее поступает новая вагонетка с влажным материалом. Перемещение вагонеток производится с помощью троса и механической лебедки. Сушильный агент движется прямотоком или противотоком к высушиваемому материалу.
Ленточные сушилки.
В этих сушилках сушка материалов производится непрерывно при атмосферном давлении. В камере 1 сушилки слой высушиваемого материала движется на бесконечной ленте, натянутой между ведущим и ведомым барабанами. Влажный материал подается на один конец ленты, а подсушенный удаляется с другого конца. Сушка осуществляется горячим воздухом или топочными газами, которые движутся противотоком или перекрестным током к направлению движения материала. В одноленточных сушилках со сплошной лентой обычно наблюдается неравномерное высушивание материала: во внутренней части слоя, обращенной к ленте, конечная влажность выше, чем в его наружной части, омываемой газами или воздухом. Более эффективно применение многоленточных сушилок с лентами из металлической сетки. В них сушильный агент движется перпендикулярно плоскости ленты сквозь находящийся на ней слой материала (перекрестный ток). При пересыпании материала с ленты на ленту увеличивается поверхность его соприкосновения с сушильный агентом, что способствует возрастанию скорости и равномерности сушки. Ленточные сушилки могут работать по различным вариантам сушильного процесса.
Петлевые сушилки.
Сушку пастообразных материалов, а также тонких листовых (например, бумаги) производят в непрерывно действующих петлевых сушилках, работающих при атмосферном давлении. В сушилке для паст питатель подает материал на бесконечную гибкую сетчатую ленту, которая проходит между обогреваемыми паром вальцами, вдавливающими пасту внутрь ячеек ленты. Лента с впрессованным материалом поступает в сушильную камеру, где образует петли. Это достигается с помощью шарнирно соединенных звеньев ленты и расположенных на ней через определенные промежутки поперечных планок, опирающихся на цепной конвейер. С помощью направляющего ролика лента отводится к автоматическому ударному устройству, посредством которого высушенный материал сбрасывается с ленты и выводится из сушилки разгрузочным шнеком. Циркуляция воздуха (или газов) осуществля- ется с помощью осевых вентиляторов, часть которых (на одной стороне камеры) показана на рис. 15-21, причем горячий воздух или газ движется поперек ленты. Сушилка обычно работает по варианту с промежуточным подогревом воздуха и частичной рециркуляцией его по зонам. В петлевых сушилках сушка производится в слое небольшой толщины (равной толщине звеньев ленты, составляющей 5—20 мм) при двустороннем обмывании ленты горячим воздухом и прогреве запрессованного материала металлическим каркасом (сеткой), нагретым вальцами. Это обеспечивает большую скорость сушки по сравнению с камерными сушилками. Вместе с тем петлевые сушилки отличаются сложностью конструкции и требуют значительных эксплуатационных расходов.
Тепловые процессы, классификация, движущая сила. Виды переноса тепла. Способы интенсификации процессов.
Тепловыми процессами называются такие технологические процессы, в которых материал нагревается или охлаждается, а скорость их протекания определяется скоростью подвода или отвода тепла.К тепловым процессам относятся:
нагревание – процесс повышения температуры материала путем подвода тепла;
охлаждение – процесс понижения температуры материала путем отвода тепла;
испарение – процесс перевода жидкости в парообразное состояние путем подвода тепла;
конденсация – процесс перевода пара в жидкое состояние путем отвода тепла.
|
|
Семя – орган полового размножения и расселения растений: наружи у семян имеется плотный покров – кожура...
Двойное оплодотворение у цветковых растений: Оплодотворение - это процесс слияния мужской и женской половых клеток с образованием зиготы...
Поперечные профили набережных и береговой полосы: На городских территориях берегоукрепление проектируют с учетом технических и экономических требований, но особое значение придают эстетическим...
Эмиссия газов от очистных сооружений канализации: В последние годы внимание мирового сообщества сосредоточено на экологических проблемах...
© cyberpedia.su 2017-2024 - Не является автором материалов. Исключительное право сохранено за автором текста.
Если вы не хотите, чтобы данный материал был у нас на сайте, перейдите по ссылке: Нарушение авторских прав. Мы поможем в написании вашей работы!