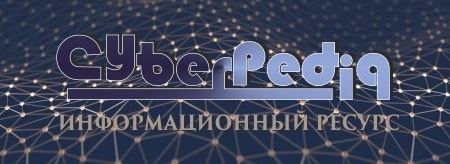
Наброски и зарисовки растений, плодов, цветов: Освоить конструктивное построение структуры дерева через зарисовки отдельных деревьев, группы деревьев...
Общие условия выбора системы дренажа: Система дренажа выбирается в зависимости от характера защищаемого...
Топ:
Определение места расположения распределительного центра: Фирма реализует продукцию на рынках сбыта и имеет постоянных поставщиков в разных регионах. Увеличение объема продаж...
Основы обеспечения единства измерений: Обеспечение единства измерений - деятельность метрологических служб, направленная на достижение...
Установка замедленного коксования: Чем выше температура и ниже давление, тем место разрыва углеродной цепи всё больше смещается к её концу и значительно возрастает...
Интересное:
Лечение прогрессирующих форм рака: Одним из наиболее важных достижений экспериментальной химиотерапии опухолей, начатой в 60-х и реализованной в 70-х годах, является...
Искусственное повышение поверхности территории: Варианты искусственного повышения поверхности территории необходимо выбирать на основе анализа следующих характеристик защищаемой территории...
Подходы к решению темы фильма: Существует три основных типа исторического фильма, имеющих между собой много общего...
Дисциплины:
![]() |
![]() |
5.00
из
|
Заказать работу |
|
|
Свойства получаемого КМ зависят от выбора исходных компонентов и их соотношения, взаимодействия между ними, метода и технологических условий изготовления изделия.
Для обеспечения оптимальных свойств материалы матрицы и наполни-теля следует выбирать по следующим рекомендациям:
- Модуль упругости при растяжении и сдвиге наполнителя должен быть больше чем связующего
- Прочность наполнителя должна быть больше чем связующего
- Удлинение при разрыве наполнителя должно быть несколько меньше чем связующего
- Коэффициенты Пуассона наполнителя и матрицы желательно иметь достаточно близкими, чтобы при деформации композита на границе наполнитель-матрица не возникало напряжений, отрывающих их друг от друга и тем самым снижающих адгезию
- Термические характеристики наполнителя (температура плавления или раз-ложения) должны быть выше температур переработки термопластов и от-верждения реактопластов.
Оптимальная прочность взаимодействия компонентов КМ обеспечивается, если матрица обеспечивает хорошую смачиваемость всей поверхности распределенного в ней наполнителя.
Прочность меньше оптимума не обеспечит передачу нагрузки от матрицы к наполнителю, что приведет к падению общей прочности.
Прочность больше оптимума снижает прочность волокна, что приведет к падению общей прочностью.
29. Критерии конструирования КМ:
• Определить требуемые свойства композита и наиболее подходящие материалы для их реализации;
• Спрогнозировать совместимость компонентов даже в наиболее тяжелых условиях работы, например, они должны одинаково или пропорционально деформироваться;
• Соблюдать определенную геометрию расположения компонентов композита (более прочная составляющая должна иметь вытянутую форму, например волокна, ленты, фольги, а менее прочная составляющая должна ее окружать);
|
• Выбрать наиболее эффективную и экономичную технологию изготовления композита.
После определения конструкции композита - выбора компонентов и распределения их функций, приступают к решению сложной задачи - изготовлению композиционного материала, включающему выбор геометрии армирования (например, различного рода плетения) и наиболее эффективного технологического метода соединения компонентов композита друг с другом (например, золь-гель методы, методы порошковой металлургии, методы осаждения - напыления и другие).
В настоящее время в мировой практике при массовом производстве композитов целевого назначения проводят предварительный системный количественный анализ. Обычно к решению проблем, связанных с производством новых материалов, применяют два метода такого анализа:Многофакторный анализ полезности и метод моделирования процесс- стоимость.
Многофакторный анализ полезности дает возможность определить "ценность" свойств того или иного материала в конкретном применении.
Метод моделирования процесс—стоимость основан на моделировании стоимости производства той или иной детали при ее изготовлении из различных материалов разными технологическими способами.
Модели позволяют определить стоимостные последствия нескольких предполагаемых вариантов и проанализировать "чувствительность" стоимости к изменениям таких переменных, как выход годных изделий и объем производства, например, «конкуренция» между альтернативными формовочными процессами наиболее высока в производстве авиационных двигателей.
Методы анализа свойств КМ
Свойства композита определяются усредненными характеристиками материалов матрицы и наполнителя. Если взять два вещества с близкими свойствами и образовать из них композиционный материал, то свойство КМ будет среднее. По характеру воздействия на материал методы испытаний разделяются на:
|
-прямые - разрушающие и методы, основанные на непосредственном измерении перемещений и деформаций, т. е. методы механических испытаний;
-косвенные - неразрушающие методы.
У неразрушающих методов испытаний выделяются три направления:
-контроль физико-механических характеристик,
-дефектоскопия элементов конструкций
-измерение напряжений.
Косвенные неразрушающие методы исключительно важны, но они должны быть обоснованы и проверены при помощи прямых методов. С помощью прямых методов испытаний получают сведения о свойствах конструкционных материалов, необходимых при проектировании разных конструкций.
Наиболее перспективные прямые методы кратковременных статистических испытаний композитов на растяжение, сжатие, сдвиг и изгиб.
ПРИМЕРЫ:
Определение предела прочности при растяжении и сжатии. Образцы для испытаний на растяжение плоские – в виде двусторонних лопаточек; при испытаниях на сжатие – прямоугольные параллелепипеды.
Испытания на растяжение проводят на образцах, вырезанных в трех направлениях: вдоль и поперек листа и под углом в 45° (рис. 2.24, а). Испытанию на сжатие подвергают образцы, вырезанные параллельно и перпендикулярно направлению слоев (рис. 2.24, б).
Испытания проводятся на обычных универсальных разрывных машинах с применением специальных приспособлений для закрепления образцов, а также на специальных машинах.
Рис. 2.24. Вырезка образцов слоистого пластика для испытаний:
а – на растяжение; б – на сжатие; в – на изгиб
Предел прочности и при растяжении, и при сжатии определяют как отношение разрушающего усилия к площади поперечного сечения образца: σΒ = P/(bh), где Р – разрушающая нагрузка, b и h – ширина и толщина (высота) образца до испытания.
Определение предела прочности при изгибе проводится на образцах прямоугольного сечения, вырезанных как вдоль, так и поперек листа. Испытания проводят при сосредоточенном (трехточечном) изгибе (рис. 2.24, в).
Предел прочности определяется по формуле σизг = M/W, где М – изгибающий момент, М = Р1/ 2; Р – разрушающая сила; I – расстояние между опорами; W – момент сопротивления, W = (bh) 2 / 6; b и h – ширина и высота образца до испытания.
|
Определение ударной вязкости проводится на образцах с надрезом прямоугольной формы и без надреза. Оценивают коэффициент ослабления ударной вязкости – отношение значений ударной вязкости образца с надрезом к образцу без надреза.
Определение твердости выполняется по методу Бринелля,: диаметр шарика 5 мм, нагрузка 250 кгс (2452 H), толщина образцов не менее 5 мм.
Помимо стандартных механических проводится определение специфических свойств (например, прочность кольцевых образцов для композитов, определение температуры хрупкости). Выбор испытаний тех или иных свойств определяется условиями эксплуатации изделий. Ниже рассмотрены некоторые специальные методы испытаний.
Испытания на растяжение и сжатие кольцевых образцов связаны с распространением намоточных технологий формообразования композитов. Одним из методов определения прочности является метод равномерного давления (рис. 2.27, а, б), создаваемого гидравлической системой. При этом предел прочности (П) определяется следующими зависимостями: и
соответственно при растяжении и сжатии, где р – разрушающее давление;
и
– внутренний и наружный диаметр кольца соответственно; h – толщина стенки кольца.
Рис. 2.27. Определение прочности кольцевых образцов на растяжение (а), сжатие (б), прочности при межслойном сдвиге (в)
Испытания на межслойный сдвиг вызваны тем, что большинство слоистых и волокнистых композитов слабо сопротивляются межслойному сдвигу (относительное перемещение слоев композита). Один из методов испытаний – кручение образцов с кольцевой проточкой (рис. 2.27, в). Сопротивление сдвигу () определяют соотношением разрушающего крутящего момента (
) и момента сопротивления кручению:, где
Установлено , что в пределах
отношения
длина рабочей части образца (
) не влияет на значения сдвиговой прочности (
).
|
|
Кормораздатчик мобильный электрифицированный: схема и процесс работы устройства...
Папиллярные узоры пальцев рук - маркер спортивных способностей: дерматоглифические признаки формируются на 3-5 месяце беременности, не изменяются в течение жизни...
Типы оградительных сооружений в морском порту: По расположению оградительных сооружений в плане различают волноломы, обе оконечности...
Состав сооружений: решетки и песколовки: Решетки – это первое устройство в схеме очистных сооружений. Они представляют...
© cyberpedia.su 2017-2024 - Не является автором материалов. Исключительное право сохранено за автором текста.
Если вы не хотите, чтобы данный материал был у нас на сайте, перейдите по ссылке: Нарушение авторских прав. Мы поможем в написании вашей работы!