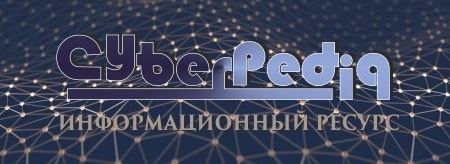
Индивидуальные и групповые автопоилки: для животных. Схемы и конструкции...
Общие условия выбора системы дренажа: Система дренажа выбирается в зависимости от характера защищаемого...
Топ:
Организация стока поверхностных вод: Наибольшее количество влаги на земном шаре испаряется с поверхности морей и океанов...
Техника безопасности при работе на пароконвектомате: К обслуживанию пароконвектомата допускаются лица, прошедшие технический минимум по эксплуатации оборудования...
Устройство и оснащение процедурного кабинета: Решающая роль в обеспечении правильного лечения пациентов отводится процедурной медсестре...
Интересное:
Инженерная защита территорий, зданий и сооружений от опасных геологических процессов: Изучение оползневых явлений, оценка устойчивости склонов и проектирование противооползневых сооружений — актуальнейшие задачи, стоящие перед отечественными...
Подходы к решению темы фильма: Существует три основных типа исторического фильма, имеющих между собой много общего...
Уполаживание и террасирование склонов: Если глубина оврага более 5 м необходимо устройство берм. Варианты использования оврагов для градостроительных целей...
Дисциплины:
![]() |
![]() |
5.00
из
|
Заказать работу |
|
|
ПРИМЕР РАЗРАБОТКИ СПЕЦИАЛЬНОГО СТАНОЧНОГО ПРИСПОСОБЛЕНИЯ
В качестве исходных данных для конструирования приспособлений необходимо иметь чертежи исходной заготовки и готовой детали, технические требования на ее приемку, а также ТП изготовления данной детали. Последний содержит следующую необходимую для конструктора информацию: последовательность выполнения и содержание операций; форму, размеры и сведения по точности и шероховатости изготовления промежуточной заготовки до и после выполнения операции; принятую схему установки заготовки; используемое оборудование и инструменты; назначенные режимы резания.
Разработку приспособления начинают с нанесения на лист контуров промежуточной заготовки в том виде, какой она имеет по окончании выполнения операции. Далее разработку конструкции ведут методом последовательного вычерчивания отдельных элементов приспособления вокруг контуров заготовки. Сначала вычерчивают основные и вспомогательные опоры, затем зажимные устройства, детали для направления и настройки режущего инструмента и вспомогательные элементы. В заключение вычерчивают корпус приспособления, который объединяет все перечисленные выше элементы. На чертеже указывают габаритные, присоединительные и основные посадочные размеры.
При назначении технических требований конструктор должен установить допуски на основные размеры приспособления. Здесь можно выделить три группы размеров.
К первой группе относятся размеры сопряжений и требования взаимного положения элементов, от точности которых зависит точность выдерживаемых на данной операции параметров.
Допуски на размеры этой группы назначают в зависимости от требований к точности изготовления готовой детали. При приближенных расчетах погрешность приспособления ∆п принимают в долях от допуска на обработку детали. На основании промышленного опыта проектирования приспособлений установлено (ГОСТ 24643-81):
|
для 3-8-й степеней точности параметров детали;
для 9-12-й степеней точности параметров детали;
Степени точности параметров определяют в соответствии с допусками расположения, указанными на чертеже готовой детали.
Пусть заданы допуски (Тдет1, Тдет2) на расположение поверхностей готовой детали (рис. 2.48, а) и схема основных поверхностей приспособления для установки заготовки (рис. 2.48, б). Согласно ГОСТ 24643—81, допускам на расположение поверхностей детали соответствуют следующие степени точности:
8-я степень точности;
9-я степень точности;
Рис. 2.48. Взаимосвязь параметров взаимного расположения поверхностей у детали и приспособления: а — эскиз детали и основные требования к взаимному расположению ее поверхностей; 6 — схема обработки заготовки в приспособлении; в — схема приспособления с параметрами взаимного расположения его поверхностей
Зная допуски точности Тдет1, Тдет2 взаимного расположения поверхностей готовой детали, можно определить допустимые погрешности ∆п1 и ∆п2 изготовления приспособления. Так, для рассматриваемого примера отклонению от параллельности плоскости паза относительно базовой поверхности А (см. рис. 2.48, а) будет соответствовать отклонение от параллельности установочной плоскости В (см. рис. 2.48, бив) относительно поверхности П1 приспособления:
Отклонению от параллельности боковой поверхности паза относительно плоскости Б (см. рис. 2.48, а) будет соответствовать отклонение от параллельности боковой поверхности приспособления Г относительно боковой поверхности направляющей шпонки П2 (см. рис. 2.48, б и в):
Полученные значения ∆п1 и ∆п2 наносим на чертеж общего вида приспособления (см. рис. 2.48, в).
|
Ко второй группе относятся размеры ответственных для нормальной работы приспособления сопряжений, погрешности которых не влияют на точность обработки (их берут в основном по IT6...IT8).
К третьей группе относятся свободные размеры, выполняемые по IT12...IT14.
Рассмотрим пример разработки в мелкосерийном производстве специального одноместного однопозиционного приспособления для фрезерования треугольного контура заготовки (рис. 2.49, а) на вертикально-фрезерном станке с ЧПУ модели 6Р11ФЗ-1. Остальные поверхности заготовки обработаны окончательно на предыдущих операциях. Схема установки заготовки и выдерживаемые размеры показаны на рис. 2.49, б. Заготовка изготовлена из стали 45. Фреза концевая диаметром 20 мм, материал фрезы 6РМ5, число зубьев z = 5, угол наклона зубьев
ω = 35°. Режим резания: скорость ν = 40 м/мин; подача Sz = 0,1 мм/зуб; глубина резания t = 5,5 мм; ширина фрезерования В = 3 мм.
Рис. 2.49. Исходные данные для проектирования приспособления (а, б) и его установочный элемент (в)
Определим погрешность базирования заготовки на жесткой оправке при выдерживании размера 13 ±0,3 мм:
где ,
— соответственно допуски на изготовление базового отверстия и оправки приспособления, равные 0,021 и 0,013 мм соответственно;
— допуск на износ оправки.
Задавшись точностью изготовления оправки (посадка 6) и приняв = 0,2Топр,
= 0,02, имеем
= 0,021 + 0,013 + 0,003 + 0,02 = 0,057 мм.
Учитывая, что погрешность базирования не должна превышать десятую часть от допуска на выдерживаемый размер, принимаем
предложенную схему установки, для чего используем установочный элемент специальной конструкции (рис. 2.49, в).
Вычислим составляющие силы резания при цилиндрическом фрезеровании1 (рис. 2.50):
где Ср — эмпирический коэффициент; х, у, к', q, w — эмпирические показатели степени; D фр— диаметр фрезы; п — частота вращения фрезы; КМ р — коэффициент, характеризующий качество обрабатываемого материала.
Учитывая мелкосерийный тип производства, выбираем ручной винтовой зажим с шайбой. Тогда расчетная схема для определения силы закрепления соответствует схеме, представленной на рис. 2.18, б.
Определим силу закрепления для этого случая. Внешний момент М = Ph (I + с), где l = 13 мм — расстояние от плоскости фрезерования до оси заготовки; с — расстояние от плоскости фрезерования до точки приложения силы (см. рис. 2.50). Осевая сила Рх = 108 Н. Из схемы, приведенной на рис. 2.50, имеем
|
Рис. 2.50. Расчетная схема для определения сил резания при встречном фрезеровании
с= ОЛ- ОК;
ОЛ= /2.
Из треугольника ОК N находим
а из треугольника ОNА получаем
или
Таким образом,
Коэффициент запаса вычисляем по данным табл. 2.2.
= 1,5-1,75-1,3-1,5 = 5,1.
Ввиду того, что жесткости и
неизвестны, принимаем
=0,3
=0,6
Учитывая, что опорная база является обработанной поверхностью, считаем . Вычисляем силу закрепления (рис. 2.51):
=
=7805Н
Приняв = 90, определяем номинальный диаметр резьбы:
Выбираем стандартную резьбу М 14x1,5. Средний диаметр резьбы d ср = 12,7 мм, угол подъема = 3,02°. Принимая
= 10,5°,
= 0,15, D = 1,7 d, определяем момент на рукоятке ключа:
H
мм ≈ 23,2 Н
м.
2.51. Расчетная схема для определения силы
закрепления Q
Обычно во фрезерных приспособлениях применяют устано- вы для размерной наладки инструмента. Однако, учитывая что в рассматриваемом случае операцию производят на станке с ЧПУ, наладку можно выполнить совмещением оси вращения шпинделя с базовой поверхностью приспособления путем обкатки последней центроискателем.
Ввиду того что приспособление имеет ограниченное число элементов, выбираем простейший вариант конструкции корпуса в виде плиты из листового проката. Заготовка при установке не требует углового базирования вокруг вертикальной оси, поэтому в корпусе не следует предусматривать элементы для его ориентирования относительно этой оси. Общий вид приспособления в двух проекциях представлен на рис. 2.52.
Обоснуем основные технические требования: отклонение от перпендикулярности оси поверхности диаметром 22f6 относительно базового торца В и отклонение от параллельности В относительно А.
Первое требование вытекает из условия обеспечения надежного прилегания базового торца заготовки к установочному элементу. Поэтому отклонение от перпендикулярности не должно превысить минимального зазора = 0,02 мм. Учитывая допуск 0,01 мм на отклонение от перпендикулярности базового отверстия диаметром 22Н7 заготовки относительно базового торца, окончательно принимаем искомый допуск для приспособления равным 0,01 мм.
|
Рис. 2.52. Общий вид приспособления для мелкосерийного производства
Второе требование обеспечивает необходимое отклонение от перпендикулярности обрабатываемой поверхности относительно базового торца. Принимая допуск на отклонение от перпендикулярности в пределах половины поля допуска выдерживаемого размера 13 ± 0,3, назначаем соответствующий допуск для приспособления равным 0,1 мм.
Рассмотрим теперь расчет автоматизированного зажимного устройства для закрепления и обработки этой же детали с помощью гидроцилиндра для условий серийного производства на станке с ЧПУ.
Поскольку условия обработки те же, что и в предыдущем примере, составляющие силы резания будут прежние: Pz = 623 Н; Ph = 748 Н; Рх = 108 Н. Расчетная схема для определения силы закрепления соответствует представленной на рис. 2.18, б, но
только для автоматизированного, не самотормозящего зажимного устройства. Тогда имеем
откуда
Как и в предыдущем случае принимаем коэффициент запаса k = 5,1. Коэффициенты трения =
= 0,16. Следовательно,
H.
Для обеспечения такой силы закрепления необходимо выбрать гидроцилиндр. Примем давление в гидроцилиндре р = 6 М Па, тогда его диаметр должен быть
мм,
где = 0,92 — КПД гидроцилиндра.
Округлим полученное значение диаметра гидроцилиндра до
d = 45 мм. Основные технические требования к базовым поверхностям приспособления сохраним из предыдущего расчета для условий мелкосерийного производства. Общий вид конструкции приспособления представлен на рис. 2.53.
Рис. 2.53. Общий вид приспособления для серийного производства
|
|
Поперечные профили набережных и береговой полосы: На городских территориях берегоукрепление проектируют с учетом технических и экономических требований, но особое значение придают эстетическим...
Историки об Елизавете Петровне: Елизавета попала между двумя встречными культурными течениями, воспитывалась среди новых европейских веяний и преданий...
Индивидуальные и групповые автопоилки: для животных. Схемы и конструкции...
Кормораздатчик мобильный электрифицированный: схема и процесс работы устройства...
© cyberpedia.su 2017-2024 - Не является автором материалов. Исключительное право сохранено за автором текста.
Если вы не хотите, чтобы данный материал был у нас на сайте, перейдите по ссылке: Нарушение авторских прав. Мы поможем в написании вашей работы!