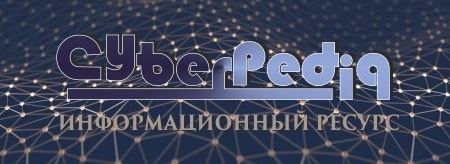
История развития хранилищ для нефти: Первые склады нефти появились в XVII веке. Они представляли собой землянные ямы-амбара глубиной 4…5 м...
Адаптации растений и животных к жизни в горах: Большое значение для жизни организмов в горах имеют степень расчленения, крутизна и экспозиционные различия склонов...
Топ:
Техника безопасности при работе на пароконвектомате: К обслуживанию пароконвектомата допускаются лица, прошедшие технический минимум по эксплуатации оборудования...
Процедура выполнения команд. Рабочий цикл процессора: Функционирование процессора в основном состоит из повторяющихся рабочих циклов, каждый из которых соответствует...
Отражение на счетах бухгалтерского учета процесса приобретения: Процесс заготовления представляет систему экономических событий, включающих приобретение организацией у поставщиков сырья...
Интересное:
Мероприятия для защиты от морозного пучения грунтов: Инженерная защита от морозного (криогенного) пучения грунтов необходима для легких малоэтажных зданий и других сооружений...
Искусственное повышение поверхности территории: Варианты искусственного повышения поверхности территории необходимо выбирать на основе анализа следующих характеристик защищаемой территории...
Уполаживание и террасирование склонов: Если глубина оврага более 5 м необходимо устройство берм. Варианты использования оврагов для градостроительных целей...
Дисциплины:
![]() |
![]() |
5.00
из
|
Заказать работу |
|
|
Данная функция ТПП связана с непосредственной производственной реализацией результатов разработок и ТР. В отличие от функций ТПП, выполняемых до начала непосредственного производства изделия, указанная функция реализуется при производстве изделия в реальном масштабе времени. В связи с этим важнейшими элементами информационного обеспечения, используемого для принятия ТР на этом этапе, являются данные о реальных конструктивно-технологических параметрах поступивших заготовок и уже выпущенных изделий, а также оперативная информация о ходе реализованных ТП.
Основные задачи, решаемые при организации контроля и управления ТП, следующие:
сравнение заданных и фактических значений параметров качества изделий;
анализ причин отклонений параметров качества изделий;
принятие ТР о ликвидации отклонений параметров качества изделий;
разработка и внедрение в производство мероприятий, обеспечивающих стабилизацию параметров качества изделий.
Специфика указанной функции ТПП вводит дополнительный критерий ее выполнения — быстродействие. ТР, направленное на обеспечение качества продукции в действующем производстве, должно быть не только верным, но также принятым и реализованным в минимальные сроки.
При разработке ТП изготовления изделий для каждой операции определяют входные и выходные параметры качества изделия и их допустимые значения, называемые заданными значениями параметров качества. Фактические значения параметров качества изделия, достигнутые при реализации ТП, могут отклоняться от заданных, причем эти отклонения могут превосходить допустимые.
В ходе ТПП невозможно предусмотреть влияние всех факторов, оказывающих дестабилизирующее действие на ход ТП изготовления изделия. К ним можно отнести, например:
|
случайные факторы, действие которых связано с физической природой технологических методов, использующихся для изготовления изделия;
наличие нетехнологичных элементов конструкции изделия, которые не были устранены при отработке конструкции изделия на технологичность;
факторы, связанные с изменяющейся производственной ситуацией, действие которых приводит к необходимости изменения отдельных ТР, заложенных в разработанный ТП (переход на инструменты из других марок инструментальных материалов, замена технологического оборудования на отдельных операциях и т. п.);
необходимость изменения части структуры и параметров ТП, связанная с невозможностью реализации или продолжения разработанного ТП, а также с изменением конструктивно-технологических параметров изделия;
возможные нарушения технологической дисциплины;
ошибочные или нерациональные ТР, принятые при ТПП.
В ходе выполнения функции контроля и управления ТП разрабатывают и внедряют мероприятия, обеспечивающие устранение дестабилизирующего действия отмеченных факторов и приведение к заданным значениям тех параметров качества изделий, отклонения которых превышают допустимые. В некоторых случаях корректируют заданные промежуточные значения параметров качества (например, промежуточные размеры поверхностей деталей и их допуски, шероховатости поверхностей и т. д.) для отдельных этапов ТП.
Как уже отмечалось ранее, рассматриваемая функция ТПП выполняется при изготовлении установочной, контрольной серии изделий, а также в период установившегося производства (последнее относится к серийному и массовому типам).
При изготовлении установочной и контрольной серий изделий разрабатываемые и внедряемые мероприятия направлены на повышение надежности принятых ТР и систем до уровня, обеспечивающего стабильное качество изделий в установившемся производстве. Идет отладка параметров внедряемого ТП; накапливается необходимый статистический материал, который можно использовать при обеспечении заданного качества в период установившегося производства. Проводимые мероприятия по обеспечению качества ориентированы в основном на компенсацию действия случайных факторов физической природы, устранение влияния нетехнологичных элементов конструкций изделия,
|
внесение необходимых изменений в структуру и параметры ТП, выработку у исполнителей строгих правил технологической дисциплины, а также устранение ошибочных и нерациональных решений, принятых при ТПП.
В период установившегося производства изделий главной целью рассматриваемой функции является стабильное обеспечение заданного качества для всего объема выпускаемой продукции. Для стабилизации качества изделий в условиях установившегося серийного производства можно применять различные устройства, выполняющие функции контроля и управления в автоматическом режиме. Для наладки этих устройств можно использовать статистический материал, полученный при изготовлении установочной и контрольной серий. Основное внимание следует уделять быстрому и эффективному реагированию технологических служб на возникающие изменения штатного хода ТП. Такие изменения могут вызвать факторы изменяющейся производственной ситуации, например поступление заготовок с непредусмотренной разработанным ТП неравномерностью припуска, отсутствие режущего инструмента с расчетной геометрией режущей части и т. д.
Сравнение заданных и фактических параметров качества проводят по завершении определенного этапа ТП или даже отдельной технологической операции. Для метрических параметров качества изделий (значения которых могут быть измерены с помощью штатных СТО и выражены числами) при стабильном обеспечении качества должно соблюдаться условие
где Пзад и Пфакт — соответственно заданное и фактическое значения параметра качества изделия; Т — допуск на параметр качества.
Если условие не выполнено, то данный параметр заносят в список параметров качества, по которым отмечены отклонения, превышающие допустимые. Одновременно фиксируют и значения выявленных отклонений.
|
Некоторые параметры качества не могут иметь числового значения, а определяются бинарно: «есть» или «нет», «хорошо» или «плохо». Это, например, наличие покрытия, комплексная оценка его качества и т. д. Сигналом о наличии отклонения здесь является сама бинарная оценка, как правило, негативная.
Анализ причин отклонений качества является важнейшим этапом выполнения рассматриваемой функции ТПП. В ходе анализа необходимо ответить на следующие вопросы.
1) Что явилось причиной отклонения параметра качества от заданного?
2) Почему данная причина вызвала отклонение параметра качества, превышающее допустимое?
3) К каким последствиям может привести дальнейшее действие выявленной причины?
4) Может ли данная причина быть устранена?
5) Можно ли хотя бы приближенно наметить основные мероприятия, позволяющие компенсировать действие выявленной причины?
6) Может ли гарантироваться в дальнейшем невозобновление действия выявленной причины?
Для анализа причин отклонений качества используют аппарат математической статистики, методы регрессионного, дисперсионного, корреляционного анализа и др.
Как правило, хорошие результаты дает численный анализ, однако в ряде случаев его проведение затрудняют невозможность выявления локального множества возможных причин, существование парных взаимовлияний рассматриваемых факторов, существенно-нелинейный характер влияния фактора на качество. Особую сложность представляет установление взаимосвязи между бинарно выражаемым значением параметра качества и метрическим значением действующего возмущающего фактора.
При невозможности количественного (численного) анализа проводят качественный анализ причин отклонений, основывающийся на накопленном технологическом опыте и знаниях. Такой анализ можно выполнять с помощью специализированных автоматизированных систем на базе вычислительной техники.
Принятие ТР связано с углубленным анализом причин отклонения параметров качества. Для каждой отдельно взятой причины предлагают конкретные ТР, направленные на компенсацию или минимизацию возникающих при ее действии отклонений качества. Для некоторых причин возможны альтернативные решения. Число альтернатив может быть значительным. Так, если основной причиной изменения точности диаметрального размера обработанной заготовки при точении является прогрессирующий размерный износ инструмента, то минимизировать его влияние на
|
качество можно следующим образом:
периодической сменой затупившегося инструмента и заменой его новым, идентичным по своим параметрам;
заменой марки инструментального материала на более стойкую;
изменением геометрических параметров режущей части инструмента;
изменением режима обработки в целях повышения оптимизации стойкости инструмента для конкретных условий обработки;
применением устройства автоматической размерной настройки (автоподналадчиков).
Поиск ТР осуществляют на основе накопленного технологического опыта и знаний. Чем выше ответственность и сложность изделия, больше затраты на техническую подготовку его производства и чем большими сериями его выпускают, тем большее число альтернативных ТР рассматривают.
Разработка и внедрение мероприятий по стабилизации качества изделия базируются на множестве принятых ТР. При этом из каждого множества альтернативных для каждой отдельной причины ТР выбирают одно, по возможности оптимальное; стремятся минимизировать ожидаемые затраты на разработку и внедрение технологических мероприятий, а также общее число последних. Технологическое мероприятие отличает от ТР большая глубина и комплексность проработки; охват не только технологических, но и организационных аспектов производства; предписательный (инструктивный) характер содержания; документальное оформление. Таким образом, разработанное на основе принятых ТР технологическое мероприятие следует рассматривать как документально предписанную совокупность действий, ориентированных на непосредственное внедрение в производство.
Мероприятия могут повторять отдельные этапы или даже целые функции ТПП. Полученные результаты отражаются в изменениях ТП изготовления деталей и сборки, а также в возможных изменениях конструкций деталей и сборочных единиц. В случае принятия эти изменения вносят в технологическую и конструкторскую документацию в порядке, предусмотренном стандартами. Указанная работа выполняется при тесном взаимодействии цеховых технологических служб, ОГТ, работников ОТК и заводских лабораторий.
ТЕХНОЛОГИЧЕСКАЯ ПОДГОТОВКА ТЕХНИЧЕСКОГО ПЕРЕВООРУЖЕНИЯ И РЕКОНСТРУКЦИИ УЧАСТКОВ И ЦЕХОВ ПРЕДПРИЯТИЙ
Жесткая конкуренция на рынке машиностроительной продукции предопределяет постоянное совершенствование и развитие производства. Современное производство необходимо рассматривать как сложную динамическую производственную систему, основой которой являются производственные участки и линии предприятия. Для обеспечения функционирования последних предусматривают следующие системы: транспортно-складские, инструментального обеспечения, технического и ремонтного обслуживания, а также административно-управленческие и технические службы (технологическое и планово-диспетчерское бюро, некоторые другие).
|
Необходимость гибко реагировать на изменение спроса как по количеству изготавливаемых изделий, так и по их номенклатуре, а также задачи освоения новых конкурентоспособных изделий требуют при постоянном текущем совершенствовании технологии и организации производства проведения на определенных этапах технического перевооружения или реконструкции производства. С этой целью на предприятиях создают отделы, бюро или группы перспективного проектирования, функциями которых являются разработка предложений по внедрению новой техники и технологии, модернизации и автоматизации производства, разработка и обоснование вариантов технического перевооружения или реконструкции участков (цехов) предприятия.
В зависимости от объема и новизны проектных работ к их выполнению привлекают специалистов проектно-технологических институтов и инженеринговых фирм. Для решения задач перспективного проектирования проводят предпроектное обследование действующего производства для оценки его технического уровня по сравнению с лучшими отечественными и зарубежными производствами-аналогами и выявления так называемых «узких мест» и проблемных вопросов развития производства.
На основе анализа результатов предпроектного обследования принимают решения, определяющие основные направления технического перевооружения или реконструкции производства.
Техническое перевооружение предполагает комплекс мероприятий, связанных с внедрением в производство новых ТП, использованием в этой связи на ряде рабочих мест нового оборудования, совершенствованием структуры и организации работы производственных участков, изменением количества оборудования и его расположения, внедрением средств механизации и автоматизации производства на действующих площадях.
Реконструкция производства дополнительно предусматривает расширение действующих цехов путем пристройки дополнительных пролетов к существующим зданиям цехов или создание новых участков и цехов с возведением новых производственных зданий на месте старых или на свободных площадях.
Разработанные решения, определяющие основные направления технического перевооружения и реконструкции производства, утвержденные руководством предприятия и предполагаемыми инвесторами, оформляют в виде задания на проектирование. В ходе разработки проектов технического перевооружения или реконструкции участков, цехов и предприятия в целом решают комплекс взаимосвязанных вопросов технологического, организационного и строительного проектирования.
Стержневой в проекте считают технологическую часть, поскольку ТП являются основой любого производства, представляющего собой их пространственную реализацию. При разработке технологической части определяющими являются разрабатываемые с разной степенью детализации ТП изготовления деталей и сборки изделий. В проектах участков и цехов массового и крупносерийного производства указанные ТП разрабатывают на все детали, сборочные единицы и изделия особенно подробно. Для условий единичного, мелкосерийного и серийного производства, характеризующихся широкой номенклатурой выпускаемых изделий, в проектах часто ограничиваются детальной разработкой ТП только для деталей- и изделий-представителей. Необходимые для проектирования исходные данные о трудоемкости остальных деталей и изделий определяют методом их сравнения по ряду критериев с деталями- и изделиями-представитедями.
Полученные данные о трудоемкости далее используют для основных технологических расчетов и обоснования проектных решений по количеству оборудования и числу рабочих мест, составу и структуре оборудования производственных участков и линий. Очень важным вопросом в технологической подготовке технического перевооружения и реконструкции производства является выбор вариантов и разработка детальных планов расположения оборудования и рабочих мест, а также определение численности работающих.
Принимаемые проектные решения в значительной степени связаны с выбором прогрессивных видов межоперационного и межцехового транспорта, а также с применяемыми способами хранения заготовок, полуфабрикатов, деталей и изделий на всех стадиях производственного процесса. Технические средства для транспортирования и хранения объектов в процессе их производства вместе с соответствующими системами управления и обслуживающим персоналом рассматривают обычно как единую транспортно-складскую систему, обеспечивающую функционирование производственных участков и линий.
Кроме того, функционирование производства определяет еще ряд систем: инструментального обеспечения, решающая задачу снабжения рабочих мест всеми видами инструментов и приспособлений; контроля качества изделий и управления ходом ТП; ремонтного и технического обслуживания, отвечающая кроме ремонта за снабжение рабочих мест электроэнергией, сжатым воздухом и охлаждающими жидкостями, а также удаление стружки от станков и некоторые другие.
Структура системы обеспечения функционирования, уровень автоматизации технических средств и систем управления, степень их интеграции в единую производственную систему на базе современной вычислительной техники являются в современных условиях важными аспектами при разработке проектов технического перевооружения и реконструкции производства. Создание гибкого автоматизированного производства предполагает поэтапное решение этих проблем.
Проектирование производственных систем ведут последовательно-параллельно, начиная с технологических расчетов по определению трудоемкости разрабатываемых ТП и расчета числа станков и рабочих мест сборки для выпуска изделий, составляющих годовую программу. Далее по мере определения параметров основных производственных процессов фронт проектных работ расширяется, так как становится возможным вести проектирование систем обеспечения функционирования производства.
Процесс проектирования производственных систем на ряде его стадий является итерационным. При проектировании, особенно на начальных этапах, в условиях дефицита исходной информации и естественного отсутствия проектных решений по системам обеспечения функционирования приходится принимать приближенные решения, которые уточняют на последующих этапах проектирования. Например, принимаемые на первых этапах проектирования предварительные проектные решения по расположению оборудования уточняют и конкретизируют по мере определения параметров транспортно-складской системы, инструментального обеспечения, решения вопросов многостаночного обслуживания, удаления стружки и других факторов.
При разработке проектов реконструкции производства возникает необходимость строительного проектирования, а также более углубленной проработки энергетической и санитарно-технической части проекта. К выполнению этих работ обычно привлекают специализированные проектные организации. Заданием на их разработку являются объемно-планировочные решения и необходимые расчетные данные, выполненные в технологической части проекта.
Учитывая высокую стоимость капитальных затрат на техническое перевооружение и реконструкцию производства, проектные разработки требуют тщательного технико-экономического обоснования в бизнес-плане.
АВТОМАТИЗАЦИЯ ТЕХНОЛОГИЧЕСКОЙ ПОДГОТОВКИ ПРОИЗВОДСТВА
1.4.1. Концептуальные модели автоматизированных систем технологической подготовки производства
Автоматизированная система технологической подготовки производства (АСТПП) — это система ТПП, основу организации которой составляет системное применение средств автоматизации инженерно-технических работ, обеспечивающее оптимальное взаимодействие людей, машинных программ и технических средств автоматизации при выполнении функций ТПП. Целью создания АСТПП является совершенствование ТПП на базе математических методов, оптимизации процессов проектирования и управления с применением современных средств вычислительной и организационной техники. Современную АСТПП можно рассматривать как единый программно-аппаратный комплекс на базе вычислительной техники, предназначенный для выполнения функций ТПП. Разработку АСТПП осуществляют на уровне предприятия. Решение об использовании на конкретном предприятии автоматизированной или неавтоматизированной форм выполнения ТПП, а также о степени автоматизации ТПП принимают на основе технико-экономических расчетов.
К АСТПП предъявляют ряд общих требований:
1) обеспечивать выполнение основных функций ТПП, предусмотренных стандартами в составе и объеме, необходимом и достаточном для проведения ТПП предприятия;
2) функционировать в режиме, обеспечивающем анализ промежуточных решений и подготовку на его основе исходных данных для выполнения последующих функций или дальнейшего решения задачи;
3) состоять из подсистем, которые при необходимости можно объединять в различных вариантах или автономно использовать;
4) предусматривать поэтапный ввод подсистем в эксплуатацию присоединением новых по мере их готовности или необходимости;
5) независимо от числа функций, реализуемых в системе, исходные данные должны быть изложены на едином входном языке.
В структуре АСТПП по функциональному назначению выделяют два типа подсистем: общего и специального назначения.
В основной состав подсистем общего назначения входят подсистемы информационного поиска, кодирования, контроля и преобразования информации, формирования исходных данных для автоматизированных систем управления различных уровней, оформления технической документации.
Подсистемы специального назначения применяют при реализации конкретных функций и решений частных задач ТПП, состав которых описан в § 1.2. Состав подсистем специального назначения устанавливают конкретно для каждого предприятия в зависимости от специфики ТПП и экономической целесообразности. Независимо от состава подсистем специального назначения их совместное функционирование обеспечивается едиными подсистемами общего назначения. Обмен информацией между подсистемами осуществляет единая информационная система. Информационную совместимость подсистем гарантирует единая система ввода, вывода, контроля и преобразования информации.
При разработке АСТПП формируется единое для всех подсистем информационное, математическое, методическое, организационное, техническое, лингвистическое и программное обеспечение системы.
Разработку АСТПП как большой технической системы начинают с ее моделирования, выполняемого в три этапа:
1) построение концептуальной модели и ее формализация
2) разработка машинной модели;
3) получение действующей рабочей модели.
Концептуальная модель АСТПП обеспечивает переход от ее
содержательного описания к формальному, т. е. определяют модель системы и строят ее формальную (структурную) схему. Традиционный подход к созданию концептуальных моделей основывается на сохранении в последних всех основных функций и функциональных связей, присущих неавтоматизированному проведению ТПП. Функциональная структура АСТПП соответствует общей структуре системы ТПП, представленной на рис. 1.7 т. 1 настоящего учебника. Каждую функцию можно рассматривать как отдельную подсистему АСТПП. В свою очередь каждую выделенную подсистему можно представлять как систему и для нее таким же образом определять подсистемы, отвечающие задачам ТПП. Такое иерархическое (ступенчатое) деление АСТПП и ее подсистем на составные части можно проводить до любого уровня (обычно до 4-го или 5-го).
Для разработки концептуальных моделей АСТПП используют метод структурного анализа, предполагающий последовательную детализацию изучаемой или проектируемой системы сверху вниз. В отличие от других методов, использующих тот же принцип, предполагается, что на каждом уровне представлено разложение анализируемого объекта, более детализированное, но полностью эквивалентное предшествующему уровню. Описание структурированной таким образом системы представляется в виде набора схем и пояснений к ним, называемого моделью системы.
Обычно он отражает систему только с одной какой-либо точки зрения. Для полного описания системы составляют несколько моделей, между которыми устанавливают взаимные связи.
Объектом анализа может быть либо АСТПП полностью (на верхнем уровне), либо любая ее часть (на более низких уровнях). Объект анализа на схеме представляют в виде прямоугольника и рассматривают не изолированно, а в связи с внешней средой (рис. 1.5). Среду изображают стрелками, направленными либо к прямоугольнику, либо от него, и указывают четыре ее составляющие: вход, выход, управление и механизм.
Рис. 1.5. Изображение, объекта анализа и его среды
Различают два типа объектов анализа — предмет и операция. Если объект анализа — предмет, то операции образуют его внешнюю среду, и наоборот. Так, при рассмотрении АСТПП как комплекса программных средств в качестве предметов рассматривают данные, а в качестве операций — преобразования над ними. При этом объектом анализа могут быть данные в среде преобразований или преобразования в среде данных.
Если объект анализа — операция, то стрелка входа изображает предметы, «перерабатываемые» операцией, стрелка выхода — предметы, получаемые в результате операции, стрелка управления — условия, при которых выполняется операция, а механизм — средства реализации анализируемой операции. Если под операцией понимать разрабатываемое программное средство, то входом будут перерабатываемые им данные, выходом — данные, получаемые в результате выполнения программы, управлением — управляющие данные, а механизмом — средства реализации программы.
Если объект анализа — предмет, то стрелка входа изображает операцию, создающую этот предмет, стрелка выхода — операцию, использующую данный предмет, стрелка управления — условие
существования предмета (может отсутствовать), стрелка механизма — средства воплощения. Так, для данных входом является создавшая их программа, выходом — использующая (перерабатывающая) их программа, управлением — условия существования данных (например, время хранения), а механизмом — устройства запоминания.
Принцип построения структуры концептуальной модели АСТПП показан на рис. 1.6. На верхнем уровне изображена схема, отражающая всю анализируемую систему. Модель представляет собой иерархический набор структурных схем, каждая из которых является детализацией какого-либо объекта (предмета или операции) и окружающей среды из схемы предыдущего (более высокого) уровня. При этом анализируемый объект представлен на схеме в виде набора объектов (обычно не более шести), изображенных в виде прямоугольников, и связей между ними, показанных стрелками входа, выхода, управления и механизма. Части, на которые разложен анализируемый объект, должны в совокупности точно представлять его и, кроме того, не пересекаться. Совокупность стрелок, входящих в схему и выходящих из нее, должна точно совпадать со средой анализируемого объекта, изображенного в виде прямоугольника на схеме предыдущего уровня. К этой среде ничего не должно быть добавлено, но ничего из нее и не должно быть потеряно. В пределах схемы среда может быть представлена более дифференцированно (более подробно).
При формировании концептуальной модели АСТПП могут быть выделены уровни системы, функций и задач.
На уровне системы отражают только наиболее общие сведения о среде — входы, выходы, управление. Уровень функций иллюстрирует состав и взаимосвязь последних, ему соответствует общая структура системы ТПП (см. рис. 1.7 т. 1 настоящего учебника). Уровень задач раскрывается через состав и взаимосвязь задач, решаемых при выполнении каждой отдельно взятой функции ТПП. Представлению уровня задач соответствует структурная диаграмма, изображенная на рис. 1.1. Возможна дальнейшая декомпозиция уровня задач.
Рис. 1.6. Иллюстрация принципа построения структуры концептуальной модели АСТПП
Необходимость дальнейшей декомпозиции и ее завершение определяют разработчики АСТПП.
Идеальной декомпозицией системы следует считать такой уровень ее разложения, который соответствует алгоритмически выполняемой процедуре или, при ее невозможности, процедуре, осуществляемой в интерактивном режиме. Недостатком метода структурного анализа, накладывающим существенные ограничения на число уровней декомпозиции, является резкое возрастание объема работ при переходе с одного уровня на другой, что характерно для всех иерархически построенных структур.
АСТПП можно рассматривать с функциональной, организационной и информационной сторон, каждой из которых соответствуют свои модели.
Функциональная модель отражает связи между отдельными структурными единицами системы и показывает взаимодействие между ними в процессе выполнения основных функций АСТПП, организационная — может быть представлена в виде схемы, в которой указаны производственные подразделения АСТПП и связи между ними, а информационная — отражает информационные универсальный высокоуровневый язык моделей данных «сущность — связь». Практические аспекты создания информационных взаимосвязи элементов АСТПП, возникающие в процессе выполнения ее функций. Информационные модели представляют с помощью языков спецификаций. Наиболее часто используют моделей подробно изложены в специальной литературе, посвященной разработке банков и баз данных.
На основании информационных моделей определяют требования к информационной базе АСТПП (по объему хранимой информации, форме ее ввода и вывода) и способам ее обработки.
Существуют два подхода к проектированию АСТПП:
1) определение перечня задач, решение которых автоматизируется. В дальнейшем такой перечень не пополняется, не предполагается его информационная и управляющая стыковки с системами, автоматизирующими решения других задач ТПП. Тем самым создаются локальные системы для решения постоянного круга задач;
2) расширение перечня решаемых задач в локальной системе и стыковка отдельных локальных систем в единую комплексную, а в дальнейшем и в интегрированную систему. В этом случае все локальные системы следует строить на единой методологической основе, что предполагает единство информационного обеспечения и внешнего представления данных, а также единство математического обеспечения и подхода к выбору технических средств.
Выбор подхода непосредственно связан с объектом автоматизации в области ТПП, которым может быть система ТПП в целом (АСТПП) как совокупность взаимодействующих функциональных подсистем; функциональная подсистема как совокупность задач ТПП, относящихся к рассматриваемой подсистеме или совокупность задач ТПП, решение которых необходимо для обеспечения функционирования системы ТПП. При выборе объекта автоматизации учитывают снижение трудоемкости работ и сокращение сроков ТПП, повышение уровня организации и улучшение качества ТПП, создание предпосылок рациональной организации основного производства, возможность снижения или полной ликвидации непроизводительных расходов.
Технические средства, с помощью которых реализуются АСТПП, объединяют в комплексы. Различают местные, централизованные и интегрированные комплексы.
Местные комплексы позволяют решать в основном простые локальные задачи, возникающие, например, при проектировании СТО (штампов, прессформ и т. п.), расчете режимов резания, нормировании операций и т.д. Пользователем такой системы является один человек: технические средства системы — персональный компьютер, установленный на рабочем месте технолога, или специализированный аппаратный комплекс — автоматизированное рабочее место технолога.
Централизованные комплексы обслуживают отдельные производственные подразделения, т. е. несколько пользователей, и дают возможность решать одну или несколько задач ТПП, например
разрабатывать единичные ТП изготовления деталей на основе процессов-аналогов, выбирать СТО и т. п. Технические средства этих систем — специализированные компьютеры с сетью терминалов ввода-вывода, печатающими и другими периферийными устройствами, установленные в соответствующих отделах и бюро.
Технические средства, объединенные в интегрированные комплексы, позволяют решать достаточно большой объем разнообразных задач и выполнять отдельные функции ТПП в масштабе всего предприятия. Пользователями такой системы являются технологи и конструкторы ОГТ, технических отделов и бюро цехов, а также сотрудники конструкторских бюро предприятия. Доступ к таким системам должен быть дистанционным, а вывод и ввод информации осуществляться через терминалы. Технические средства этих систем — большие универсальные вычислительные машины с высоким быстродействием и значительным объемом памяти, управляющие компьютеры, специализированные рабочие станции, а также персональные компьютеры с периферийными устройствами, объединенные в единую вычислительную систему с помощью специальных каналов связи и образующие локальную сеть.
Основным режимом работы АСТПП следует считать интерактивный (диалоговый) режим. Отдельные задачи или их фрагменты, для которых возможны формальные алгоритмы решения, решают в автоматическом (пакетном) режиме.
На основании созданных концептуальной и информационной моделей разрабатывают и отлаживают программное обеспечение АСТПП, которое после развертывания на технических средствах формирует машинную модель системы.
Учитывая специализированный характер, сложность и предъявляемые высокие требования к качеству принимаемых решений, концептуальные и информационные модели АСТПП эффективно выполнить могут только специалисты-технологи.
1.4.2.Проблемы автоматизации технологической подготовки производства
Создание полноценной, удовлетворяющей современным требованиям АСТПП, обеспечивающей комплексную реализацию функций ТПП и ее высокое качество, является сложной научно-технической проблемой. Для ее решения необходимо, во-первых, исследование процессов принятия ТР в ходе ТПП и создание общей методологии ТПП, что позволило бы представить указанные процессы в виде последовательности формальных процедур, и, во вторых, разработка эффективных средств (программных и аппаратных) представления процессов принятия ТР, позволяющих проводить автоматизацию этих процессов в программно-аппаратных комплексах.
Практически все функции ТПП содержат задачи, решение которых в автоматическом (пакетном) режиме при использовании средств вычислительной техники невозможно в силу недостаточной разработанности и формализации процедур принятия ТР. Отработку конструкций на технологичность (см. рис. 1.1) в значительной мере можно рассматривать как акт творчества, который пока не может быть сведен к последовательности формальных процедур. Задачи, решаемые при разработке единичных ТП изготовления деталей на основе процессов-аналогов (см. рис. 1.2), являются формализуемыми, что нашло отражение в создании значительного числа систем автоматизированного проектирования технологических процессов (САПРТП), использующих принцип типовых решений. Эти системы можно рассматривать как отдельные программные модули, которые могут входить в состав АСТПП.
Наиболее трудно формализуемой задачей, решаемой при разработке единичных ТП изготовления деталей при индивидуальном проектировании (см. рис. 1.4), является создание маршрутной технологии, при разработке которой необходим синтез структуры
маршрутного ТП (определение состава и последовательности технологических операций).
В математической постановке эта задача сводится к поиску вариантов структур в счетных множествах с весьма значительным, хотя и ограниченным числом элементов. Формализация именно таких задач представляет наибольшие трудности. Задачи, решаемые при разработке операционной технологии, являются формализуемыми. Известно значительное число САПР операционной технологии, позволяющих о<
|
|
Индивидуальные очистные сооружения: К классу индивидуальных очистных сооружений относят сооружения, пропускная способность которых...
Особенности сооружения опор в сложных условиях: Сооружение ВЛ в районах с суровыми климатическими и тяжелыми геологическими условиями...
Археология об основании Рима: Новые раскопки проясняют и такой острый дискуссионный вопрос, как дата самого возникновения Рима...
Наброски и зарисовки растений, плодов, цветов: Освоить конструктивное построение структуры дерева через зарисовки отдельных деревьев, группы деревьев...
© cyberpedia.su 2017-2024 - Не является автором материалов. Исключительное право сохранено за автором текста.
Если вы не хотите, чтобы данный материал был у нас на сайте, перейдите по ссылке: Нарушение авторских прав. Мы поможем в написании вашей работы!