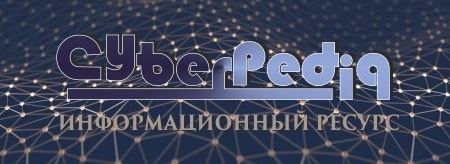
История развития хранилищ для нефти: Первые склады нефти появились в XVII веке. Они представляли собой землянные ямы-амбара глубиной 4…5 м...
Эмиссия газов от очистных сооружений канализации: В последние годы внимание мирового сообщества сосредоточено на экологических проблемах...
Топ:
История развития методов оптимизации: теорема Куна-Таккера, метод Лагранжа, роль выпуклости в оптимизации...
Эволюция кровеносной системы позвоночных животных: Биологическая эволюция – необратимый процесс исторического развития живой природы...
Интересное:
Финансовый рынок и его значение в управлении денежными потоками на современном этапе: любому предприятию для расширения производства и увеличения прибыли нужны...
Что нужно делать при лейкемии: Прежде всего, необходимо выяснить, не страдаете ли вы каким-либо душевным недугом...
Берегоукрепление оползневых склонов: На прибрежных склонах основной причиной развития оползневых процессов является подмыв водами рек естественных склонов...
Дисциплины:
![]() |
![]() |
5.00
из
|
Заказать работу |
|
|
К технико-экономическим показателям потока относят:
1) выпуск изделий на потоке в смену (М, ед);
2) такт потока (, с);
3) время изготовления изделия (Т, с);
4) количество рабочих в потоке: расчетное и фактическое (Nр, Nф, чел);
5) средний тарифный коэффициент определяется по формуле:
,
где Qср – средний тарифный коэффициент;
ΣQ – сумма тарифных коэффициентов;
Nр – расчетное количество рабочих, чел.
6) средний тарифный разряд определяется по формуле:
,
где rср – средний тарифный разряд;
Σr – сумма тарифных разрядов.
7) среднерасчетная сдельная расценка на единицу изделия определяется по формуле:
,
где Рср – среднерасчетная сдельная расценка, руб;
ДТС1 – дневная тарифная ставка 1-го разряда, руб;
М – выпуск изделий в смену, ед.
8) производительность труда определяется по формуле:
,
9) коэффициент согласования, Кс
10) коэффициент механизации потока определяется по формуле:
,
где Кмех – коэффициент механизации;
Σtм, Σtc, Σtn, Σta – сумма времени механизированных работ, выполняемых соответственно на машинах, спецмашинах, прессах, полуавтоматах, с.
11) коэффициент использования оборудования определяется по формуле:
,
где Σtмех – сумма затрат времени на выполнение всех механизированных (кроме прессовых) опе-
раций, с;
nф - количество машин, установленных в потоке (с учетом резервных).
12) фактическая площадь, приходящаяся на одного рабочего в цехе (Sп.ф.) определяется по формуле:
,
где Sц – площадь цеха, м2.
5 Проектирование планировки швейного цеха
5.1 Производственные требования к планировке рабочих мест и потоков в швейном цехе
|
План размещения основного потока выполняют на основании технологической схемы, монтажного графика и предварительного расчета потока, решая следующие задачи:
¨ выбор типа и размеров рабочих мест;
¨ размещение технологического оборудования и операций по рабочим местам;
¨ расположение рабочих мест и поточных линий;
¨ определение движения полуфабриката и готовых изделий по поточным линиям;
¨ уточнение средств транспортирования;
¨ размещение потоков на плане цеха.
При выполнении плана размещения потоков необходимо соблюдать правила производственной санитарии, техники безопасности и нормативной документации.
В процессе этой работы уточняют некоторые параметры потока (длину поточной линии, конфигурацию участков и т. п.) Определенное предварительным расчетом расхождение в параметрах предварительного и окончательного расчетов потока должно быть незначительным (в пределах 1-2%), но оно возможно, так как предварительный расчет производится по средним значениям Кср, загрузки потока и пр.
Типы и размеры рабочих мест выбирают в зависимости от вида изготавляемых изделий и наличия транспортных средств. Размеры рабочих столов выбирают в соответствии с характером выполняемых операций, видом и размером обрабатываемых полуфабрикатов (табл. 12).
Таблица 12 Размеры рабочих столов
Рабочие места и их назначение | Изготавливаемые изделия | Размеры стола,мм | |
Длина | Ширина | ||
1 | 2 | 3 | 4 |
Машинные для универсальных машин | Пальто и костюмы Белье, платья, сорочки, блузы | 1200 1100 | 650 600 |
Ручные для обработки изделий в развернутом виде на столе | Пальто и костюмы Белье, платья, сорочки, блузы | 1400 1200 | 800-1400 650 |
Ручные для расположения изделий на коленях | Пальто и костюмы Белье, платья, сорочки, блузы | 1200 1100 | 400 400 |
Ручные для проверки и подрезки выкроенных деталей | Пальто Костюмы, платья, сорочки, блузы | 1500-1600 1200 | 900-1000 600 |
Ручные или машинные для пришивания талонов при подготовке выкроенных деталей к пошиву | То же | 1200 | 650 |
Утюжильные для обработки основных деталей и готовых изделий | Пальто и костюмы | 1400 | 800 |
Утюжильные для обработки мелких деталей | То же, белье, платья, сорочки, блузы | 1100 | 600 |
Утюжильные СУ-I пл. для окончательной ВТО платьев | Женское платье | 1400 | 490 |
Утюжильные СУ-ОП для внутрипроцессной и окончательной ВТО | Пальто | 1800 | 1035 |
Утюжильные СУ-ОК для внутрипроцессной и окончательной ВТО | Костюмы | 1395 | 850 |
Прессовые: | |||
ПЛП (легкий пневматический) для внутрипроцессной и окончательной ВТО | Пальто и костюмы | 1060 | 1120 |
ПСП (средний пневматический) для внутрипроцессной и окончательной ВТО | То же | 1140 | 1400 |
ПТП (тяжелый пневматический) для внутрипроцессной и окончательной ВТО | 1100 | 1600 | |
ПГП (гидравлический) для внутрипроцессной и окончательной ВТО | 1166 | 1600 | |
ПВ-I (пневматический) для вывертывания и приутюживания воротников | Мужские сорочки | 660 | 746 |
СПР-I (пневматический) для приутюживания окатов рукавов | Пальто и костюмы | 850 | 710 |
Продолжение таблицы 12 | |||
1 | 2 | 3 | 4 |
С-311 (электромеханический) для внутрипроцессной и окончательной ВТО | Пальто и костюмы | 1200 | 1260 |
ПВМГ-I (паровоздушный манекен) для окончательной ВТО | То же | 1400 | 500 |
Столы для приемщиков готовой продукции | Пальто | 1800 | 1000 |
Механические щетки | Костюмы, детские пальто, белье, платья, сорочки, блузы Пальто | 1200 1400 | 900-1000 1200 |
|
В каждом потоке должен предусматриваться стол запуска, на котором осуществляют проверку деталей и узлов, их учет. Стол запуска имеет чаще всего прямоугольную форму. При использовании длинного общего междустолья стол запуска может быть разделенным (рис.13а) и сплошным (рис. 13б).
Рисунок 13 - Стол запуска: а) разделенный, б) сплошной
Кроме рабочих мест в потоке предусматривают места для хранения кроя, деталей и готовых изделий. Детали кроя и полуфабрикаты хранят в тележках-контейнерах, либо на полках-стеллажах.
Расположение рабочих мест должно обеспечивать непрерывное и равномерное перемещение деталей от исполнителя к исполнителю по кратчайшему пути с минимальным применением транспортных средств. В состав рабочего места входят рабочий стол или другое оборудование, а также рабочая зона для размещения исполнителя. Размеры рабочей зоны зависят от рабочей позы исполнителя (стоя, сидя), а также вида выполняемых работ, технологического оборудования.
|
В групповых потоках рабочие места располагают по группам обработки узлов изделий. Расположение рабочих мест может быть линейным, под прямым углом к продольной оси агрегата или под углом 45° и 60°. (обеспечивает экономию площади по ширине цеха, что бывает необходимо при реорганизации и реконструкции действующих цехов).
Расположение поточных линий и групп на плане цеха зависит от типа потока и применяемых транспортных средств. Во всех случаях оно должно обеспечить рациональное использование площади цеха в соответствии с нормативами и техникой безопасности. Направление движения полуфабриката и готовых изделий по поточным линиям должно обеспечить непрерывность потока от места подачи кроя до сдачи готовой продукции. В связи с этим места запуска следует располагать со стороны подачи кроя, места выпуска – со стороны подачи готовой продукции на склад. Надо стремиться к тому, чтобы не было пересечения линий перемещения кроя, полуфабриката готовых изделий и движения людей.
Для размещения потоков на плане цеха фабрики-новостройки подбирают необходимый вариант типового здания. В настоящее время приняты следующие типовые здания для предприятий легкой промышленности: трех-, четырехэтажные размером от 18х36 м для предприятий малой мощности, четырехэтажные размером от 36х36 до 36х72 м для предприятий средней мощности и четырехэтажные размером 36х120 м, Г-и П-образной формы для предприятий большой мощности с сеткой коллон 6х6 и 6х9м. Сетка колонн для одноэтажных зданий такова: 6х18; 6х12 и 12х12 м. Длина агрегата для обеспечения нормального движения людских потоков не должна превышать 35м.
Расстояние по длине цеха от торцевых стен до агрегатов (торцов машинных столов) должно быть равным 3,5¸4,4 м для организации зон запуска и выпуска, 2¸2,5м при отсутствии запуска и выпуска, между секциями 2¸2,5м, между группами - 0,8¸1,2м. Расстояние по ширине цеха от стен до агрегатов (от наиболее выступающей точки колонны) должно быть равным 1,1¸1,2м, между агрегатами 1,5¸2м. Обязательно наличие главного прохода шириной 3÷3,5м.
|
Планировка выполняется в масштабе 1:100. На каждом рабочем месте указывается номер организационной операции, специальность. Стрелками указывают направление движения полуфабриката. При выполнении планировки потока необходимо помнить, что рабочий должен брать изделие левой рукой (на кратных операциях допускается и правой). При этом расстояние между соседними столами не должно быть меньше:
· 0,5м – на утюжильных и ручных операциях, выполняемых стоя;
· 0,55м – на машинных, ручных и утюжильных операциях, выполняемых сидя, при расположении обрабатываемых деталей на столе;
· 0,75м – на ручных операциях, выполняемых сидя, при расположении обрабатываемых деталей на коленях;
· 0,8м – расстояние между прессами, обслуживаемыми одним рабочим;
· 0,2 - 0,3м – расстояние между прессом и соседним рабочим местом для установки термоизоляционного щита.
При проектировании потоков необходимо выбирать такие транспортные средства, которые обеспечивают непрерывность передачи полуфабрикатов, т.е. рабочие места и транспортные средства должны быть взаимосвязаны таким образом, чтобы каждый исполнитель имел возможность взять полуфабрикат для обработки с предыдущей операции и передать на последующую, не меняя своей основной рабочей позы.
Кроме того, для удобства обслуживания следует выбирать минимально необходимое количество видов транспортных средств для одного потока, цеха. Применение конвейера с автоматическим адресованием возможно на всех участках потоков при изготовлении всех видов изделий, однако ограничено его высокой стоимостью. Таким образом, учитывая, что приобретение автоматизированных конвейерных установок и их монтаж в швейных цехах требует больших финансовых затрат, предпочтение следует отдавать более простым и дешевым транспортным средствам.
На рисунке 11 показано размещение рабочих мест в конвейерном потоке.
Рисунок 14 – Размещение рабочих мест в конвейерном потоке (l – шаг ячейки
конвейера, мм; b – ширина ленты конвейера, мм)
При проектировании группового расположения рабочих мест целесообразно пользоваться схемами расположения рабочих мест в групповых потоках, представленных на рисунке 15.
|
Условные обозначения:
- рабочее место - скат
- междустолье - желоб
|
Рисунок 15 – Варианты расположения рабочих мест в групповых потоков
Кроме того, следует помнить, что в потоках необходимо предусматривать запасные рабочие места. Их количество определяется из расчета: одно запасное на каждые 4 - 5 одинаковых подряд идущих основных рабочих мест. При линейном расположении запасные места устанавливают после 4 - 5 основных, а при групповом – в конце групп.
В конце участка, с которого производится выпуск готовой продукции, необходимо предусмотреть рабочие места контролеров ОТК. В зависимости от применяемых транспортных средств они могут быть пристроены к основному участку или отделены от него. Количество контролеров определяется исходя из их нормы выработки. Для того чтобы правильно осуществить выбор транспортных средств можно воспользоваться таблицей 13.
Таблица 13 Выбор транспортных средств
Условия выбора транспортных средств | ||||
Вид изделия | Специали- зация участка | Максим. кратность операций | Наличие возвратов* | Рекомендуемые транспортные средства |
1 | 2 | 3 | 4 | 5 |
Пальто, полупальто, пиджаки и т.п. | заготовка | 2 | нет | бесприводные средства для агрегатного расположения рабочих мест |
есть | бесприводные средства для группового расположения рабочих мест | |||
монтаж | 2 | нет | ленточный или подвесной конвейер, бесприводные средства для агрегатного расположения рабочих мест | |
есть | транспортер с автоматическим адресованием | |||
более 2-х | нет | конвейер КМ | ||
есть | транспортер с автоматическим адресованием | |||
брюки, | заготовка, | нет | зажимные устройства | |
сорочки и т. п. | монтаж | 2 | есть | бесприводные средства для группового расположения рабочих мест |
платья, блузки и т. п. | заготовка, монтаж | 2 | нет | бесприводные средства для агрегатного расположения рабочих мест |
есть | бесприводные средства для группового расположения рабочих мест | |||
пальто, п/пальто, брюки, сорочки, | заготовка | 3 в начале или конце участка | не имеет значения | бесприводные средства для группового расположения рабочих мест |
платья, блузки и т. п. | 3 в середине участка или более 3-х | не имеет значения | транспортер с автоматическим адресованием | |
пальто, п/пальто, | отделка | 2 | нет | подвесной цепной (винтовой) транспортер |
пиджаки и т. п. | более 2-х | нет | подвесной транспортер с автоматическим адресованием | |
платья, сороч- | 2 | нет | передвижение тележки (кронштейны) | |
ки, блузки, брюки и т. п. | отделка | более 2-х | нет | передвижной транспортер с автоматическим адресованием |
* – возвраты, нарушающие непрерывность передачи полуфабрикатов.
5.2 Проектирование неосновных потоков
Если в проектируемом цехе имеются потоки, аналогичные основному, то указывается, сколько таких потоков в цехе, выпуск изделий в каждом и количество рабочих. Если же дополнительный поток не аналогичен основному, выполняется его расчет по укрупненным показателям без составления технологической последовательности и технологической схемы. Для расчета таких потоков должны быть известны вид изделия и затраты времени на его изготовление. При выборе изделия для дополнительного потока следует стремиться кспециализации цеха и в то же время к разнообразию ассортимента в пределах специализации.
Расчет производят в следующем порядке:
1. Определяют количество рабочих в цехе по формуле:
где N ц - количество рабочих в цехе, чел.;
S ц - площадь цеха, м2;
S н - типовая норма площади, приходящаяся на одного рабочего, м2
2. Определяют количество основных рабочих в дополнительном потоке по формуле:
N доп.пот. = Nц - N осн.пот.
3. Исходя из количества рабочих в дополнительном потоке, определяют его такт и мощность.
4. Далее по уточненным данным подсчитывается суммарная сдельная расценка изготовления, которая равна отношению среднего тарифного коэффициента, умноженного на дневную ставку 1-гo разряда, к норме выработки одного рабочего в смену.
Суммарная сдельная расценка или средний тарифный коэффициент для ее подсчета, а также итоговая графа сводной таблицы численности рабочей силы (которая потребуется в дальнейшем) берутся по данным действующего предприятия или из нормативных данных.
5. Затем производится распределение численности рабочих дополнительного потока по специальностям. Для этого по итоговой строке сводной таблицы рабочей силы с удельным весом численности рабочих по специальностям (в %) определяется число рабочих по каждой специальности.
Количество рабочих в дополнительном потоке принимается за 100%.
Рассмотрим этот расчет на примере.
Пример: Определить численность рабочих по специальностям и количество оборудования в дополнительном потоке, рассчитываемом по укрупненным показателям.
Исходные данные:
· изделие - брюки школьные;
· количество рабочих в потоке 45 чел. (по расчету);
· удельный вес количества рабочих по специальностям (в %) по данным предприятия:
М - 44,6 %; С - 23,58 %; П - 13 %;
У - 6,02 %; P - 12,8 %; Всего -100 %
Находим численность рабочих, занятых
· на машинных операциях (N м):
чел.
· на специальных операциях (Nс):
чел
и т.д.
Результат расчетов сводятся в таблицу 14.
Таблица 14 Численность рабочих по специальности
Всего | В том числе занятых на операциях | ||||||||||
машинных | спецмашинных | ручных | утюжильных | прессовых | |||||||
% | кол-во | % | кол-во | % | кол-во | % | кол-во | % | кол-во | % | кол-во |
1 | 2 | 3 | 4 | 5 | 6 | 7 | 8 | 9 | 10 | 11 | 12 |
100 | 45,00 | 44,00 | 20,06 | 23,58 | 10,90 | 12,80 | 5,48 | 6,02 | 2,71 | 13,00 | 5,85 |
6. С использованием данных таблицы 15 составляется сводная таблица технологического оборудования. Количество оборудования должно равняться числу рабочих соответствующих специальностей.
Так как число рабочих на машинных операциях равно 20,06 (по расчету), то количество универсальных машин принимаем равным 20. Число рабочих на прессовых работах 5,85, количество прессов - 6. Количество прессов и спецмашин по классам и типам устанавливается по аналогии с действующими потоками.
6 Совершенствование организации швейного производства
|
|
Двойное оплодотворение у цветковых растений: Оплодотворение - это процесс слияния мужской и женской половых клеток с образованием зиготы...
Биохимия спиртового брожения: Основу технологии получения пива составляет спиртовое брожение, - при котором сахар превращается...
Общие условия выбора системы дренажа: Система дренажа выбирается в зависимости от характера защищаемого...
Индивидуальные очистные сооружения: К классу индивидуальных очистных сооружений относят сооружения, пропускная способность которых...
© cyberpedia.su 2017-2024 - Не является автором материалов. Исключительное право сохранено за автором текста.
Если вы не хотите, чтобы данный материал был у нас на сайте, перейдите по ссылке: Нарушение авторских прав. Мы поможем в написании вашей работы!