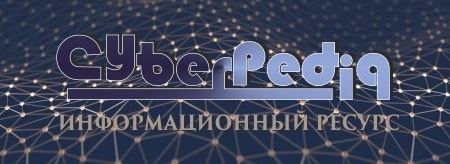
Организация стока поверхностных вод: Наибольшее количество влаги на земном шаре испаряется с поверхности морей и океанов (88‰)...
Биохимия спиртового брожения: Основу технологии получения пива составляет спиртовое брожение, - при котором сахар превращается...
Топ:
Особенности труда и отдыха в условиях низких температур: К работам при низких температурах на открытом воздухе и в не отапливаемых помещениях допускаются лица не моложе 18 лет, прошедшие...
Характеристика АТП и сварочно-жестяницкого участка: Транспорт в настоящее время является одной из важнейших отраслей народного...
Основы обеспечения единства измерений: Обеспечение единства измерений - деятельность метрологических служб, направленная на достижение...
Интересное:
Влияние предпринимательской среды на эффективное функционирование предприятия: Предпринимательская среда – это совокупность внешних и внутренних факторов, оказывающих влияние на функционирование фирмы...
Принципы управления денежными потоками: одним из методов контроля за состоянием денежной наличности является...
Финансовый рынок и его значение в управлении денежными потоками на современном этапе: любому предприятию для расширения производства и увеличения прибыли нужны...
Дисциплины:
![]() |
![]() |
5.00
из
|
Заказать работу |
|
|
Сварные конструкции контролируют на всех этапах их изготовления. Кроме того, систематически проверяют приспособления и оборудование. При предварительном контроле подвергаются проверке основные и вспомогательные материалы, устанавливается их соответствие чертежу и техническим условиям. Наиболее ответственным моментом является текущий контроль выполнения сварки. Организация контроля сварочных работ может производиться в двух направлениях: контролируют сами процессы сварки либо полученные изделия.
Тщательный контроль и приемка деталей и готовых изделий проводят на всех стадиях производства сварных конструкций.
В стадии обработки проверяют:
- соответствие применяемого металла чертежу на основании сертификата завода-изготовителя или путем заводского лабораторного испытания;
- отсутствие внешних пороков металла: раковин, плен, волосовин, закатов, расслоений;
- соблюдение формы и внешнего вида элементов сварных конструкций после заготовительных операций в соответствии с чертежами и техническими условиями, например, точность размеров, качество разделки кромок, зачистка после газовой резки и пр.
В собранной сварной конструкции проверяют:
- соответствие геометрических и основных размеров рабочим чертежам и соблюдение допусков;
- правильность подготовки металла под наложение сварочных швов, зазоры, разделка кромок и прочее;
- чистоту металла в месте наложения сварных швов, отсутствие окалины, ржавчины, масла и других загрязнений.
В процессе сварки проверяют выборочно:
- порядок наложения швов в соответствии с технологическим процессом;
- соответствие чертежным размерам наложенных швов и марки применяемой сварочной проволоки;
|
- соответствие режимов сварки и квалификации сварщиков, указанных в техпроцессе.
Выбор методов контроля обусловливается требованиями технических условий на изготовление сварных конструкций и зависит от степени ответственности данной конструкции при эксплуатации, глубины и места расположения предполагаемых дефектов, толщины, конфигурации и материала деталей и других факторов. Каркас вибростенда является ответственной конструкцией, работающей в условиях повышенных вибронагрузок, что предъявляет повышенные требования к качеству сварных соединений [1].
Контроль качества сварных соединений алюминия и его сплавов имеет свои особенности в связи с повышенной склонностью швов к образованию пористости, а также к возникновению несплавлений; между швами и кромками и между валиками. Несплавления, как правило, не выявляются рентгено- и гаммаграфированием, поэтому следует применять метод ультразвуковой дефектоскопии.
Глубину залегания недопустимых дефектов по результатам просвечивания определяют методом ультразвукового контроля, позволяющего более точно зафиксировать место положения дефекта по толщине шва. Наличие скоплений и цепочек пор на рентгеновских снимках после окончательного просвечивания определяют по результатам послойного ультразвукового контроля. Для сварных швов этих толщин, выполненных плавящимся электродом в среде защитных газов, недопустимы следующие дефекты:
1) трещины, несплавления, незаплавленные кратеры, цепочки и скопления пор, наплывы;
2) поры и включения диаметром более 3 мм, поры и включения диаметром менее 3 мм при суммарной площади их изображения на снимке, составляющей более 2% по отношению к площади шва на любые 100 мм снимка.
Поры и включения, расположенные на глубине менее 5 мм, исправлению не подлежат, так как они переплавляются при наложении последующих валиков.
Браком считают детали, в которых при ультразвуковом контроле обнаружены следующие дефекты:
|
1) с эквивалентной площадью более 4 мм2 при контроле слоя толщиной 40 мм и более 7 мм2 при контроле слоя толщиной 200 м;
2) с условной протяженностью более 10 мм при глубине залегания дефектов до 40 мм и более 15 мм при глубине 40— 150 мм.
Допускаются дефекты с эквивалентной площадью менее 4 мм при суммарной площади менее 2% площади на любых 100 мм длины, не носящие протяженного характера.
Контроль ультразвуком производится с применением существующего для этих целей оборудования — ультразвуковой дефектоскоп DIO 1000 SFE.
Рисунок 14 – Схема ультразвукового контроля
Контроль сварных соединений заключается в качественной или количественной оценке основных признаков, характеризующих их работоспособность.
Контролю внешним осмотром обычно подвергают 100% выполненных швов. Внешние дефекты, такие, как трещины, наплывы, прожоги, незаваренные кратеры, свищи в начале шва (зажигание дуги на основном металле), выводы кратера на основной металл, сплошные сетки или цепочки пор, непровары, подрезы — не допускаются.
Внешний осмотр заключается в выявлении дефектов соединений невооруженным глазом или с помощью лупы 7–10-кратного увеличения. При осмотре проверяют расположение рельефа в соответствии с чертежом, форму, наличие наружных дефектов деформации узла.
Требования к процессу сварки и оборудованию. Задачи работы
Для расширения диапазона толщины свариваемых материалов, повышения производительности при получении неразъемных соединений работая вольфрамовым электродом, и улучшения провара в последнее время были разработаны новые методы аргонодуговой сварки:
1) Работы пульсирующим током. Во время импульса тока металл расплавляется, кристаллизуясь во время паузы. Дуга перемещается с постоянной скоростью или шагами, которые синхронизированы с импульсами сварочного тока. При этом обеспечивается эффективное проплавление во всех пространственных положениях, нечувствительность к мелким недочетам, допущенным при сборке. Периодическое снижение поступления тока не допускает перегрев металла, и следовательно, снижает деформации.
2) Используя подогрев присадочной проволоки. Этот метод существенно увеличивает производительность.
3) Использование нескольких вольфрамовых электродов – эффективный способ получить швы без подреза на высоких скоростях сваривания металла.
|
При сварке плавлением алюминиевых сплавов наиболее рациональным типом соединений являются стыковые. Для устранения окисных включений в металле швов можно использовать удаляемые подкладки из коррозионно-стойкой стали, других металлов с повышенной температурой плавления, а также меди, благодаря ее высокой теплопроводности. Используют также остающиеся подкладки из свариваемого алюминиевого сплава или разделку кромок с обратной стороны шва, что обеспечивает удаление окисных включений из стыка в канавку подкладки.
Рисунок 15 – Положение горелки и прутка относительно плоской поверхности детали
Возбуждение дуги и разогрев электрода осуществляется на графитной пластинке, которую располагают рядом с точкой начала сварки. О готовности электрода к сварке, свидетельствует образование на электроде раскаленного шарика. В дальнейшем на протяжении всей сварки до обрыва дуги электрод должен сохранять такую форму.
К месту сварки горелку переводят быстрым движением. Следует избегать касания раскаленным электродом металла, это приводит к загрязнению вольфрама, нарушению устойчивости горения дуги и ухудшению формируемого шва. Если все же произошло случайное касание раскаленным электродом металла, сварку следует прекратить и очистить электрод от прилипших к нему частиц алюминиевого сплава. Для этого дугу зажигают на графитовой пластинке и выдерживают ее в течение 20-30 с, пока испарятся посторонние включения и на конце электрода вновь появится чистый раскаленный шарик.
Подачу присадочного материала в зону дуги начинают лишь после того, как образуется сварочная ванна с чистой поверхностью. Если сварочная ванна имеет матовый оттенок, а вокруг нее откладывается копоть, то необходимо несколько увеличить подачу аргона. Если же дуга горит неустойчиво, то расход газа следует несколько уменьшить.
Длина дуги должна быть стабильной на протяжении всей сварки и поддерживаться на расстоянии 4-5 мм от поверхности сварочной ванны. При увеличении этого расстояния уменьшается тепловая мощность дуги, увеличивается ширина зоны расплавления, деталь сильнее нагревается, отчего увеличивается ее коробление.
|
При заварке трещины присадочную проволоку, и вольфрамовый электрод располагают вдоль трещины. Конец проволоки не должен во время сварки выходить из зоны газовой защиты и попадать в столб дуги.
Для лучшей видимости процесса сварку ведут справа налево, а присадочную проволоку подают спереди. Шов, наложенный на трещину, должен быть слегка выпуклым и возвышаться над основной поверхностью на 2-3 мм. Поверхность шва должна быть светлой с четко выраженной мелкой чешуйчатостью. Затемненная матовая поверхность или закопченность шва свидетельствуют о ненормальной газовой защите, низком качестве аргона, подсосе воздуха вследствие неплотностей газового тракта. Плохое формирование шва происходит по причине неправильно выбранных режимов сварки или неправильной технике ведения процесса.
Для сварки алюминиевых сплавов также используют сварку вольфрамовым электродом импульсной дугой. При этом можно сваривать алюминиевые сплавы толщиной от 0,2 мм и более. Для сварки импульсной дугой необходимы специализированные источники тока типа ИПКИ-100, ИПКИ-350, ВСВУ- 315, ИСВУ-315-1 и др.
Автоматическую сварку осуществляют без подачи или с подачей присадочной проволоки. При ручной сварке тонких листов неплавящимся электродом без присадки (по отбортовке) или с присадкой в один проход горелку перемещают с наклоном «углом вперед». Угол наклона горелки к плоской поверхности детали 70-800. Присадочная проволока подается под возможно меньшим углом к плоской поверхности детали.
При механизированной или автоматической сварке неплавящимся электродом горелка располагается под прямым углом к поверхности детали, а присадочная проволока подается таким образом, чтобы конец проволоки опирался на край сварочной ванны; скорость подачи меняется от 4-6 до 30-40 м/ч в зависимости от толщины материала [7].
Для сварки алюминиевых сплавов также используют сварку вольфрамовым электродом импульсной дугой. При этом можно сваривать алюминиевые сплавы толщиной от 0,2 мм и более. Имеются специализированные источники тока для сварки импульсной дугой алюминиевых сплавов на переменном токе.
Расширение технологических возможностей при сварке металла больших толщин достигается за счет использования способа дуговой сварки вольфрамовым электродом погруженной дугой. Способ позволяет сваривать за один проход материал толщиной до 20 мм. При этом используют специальные вольфрамовые электроды с добавками иттрия и тантала и сварочные горелки с улучшенной защитой зоны сварки.
Алюминиевые сплавы подвергают трехфазной дуговой сварке вольфрамовыми электродами. Возможности регулирования тепловложения при трехфазной дуговой сварке позволяют использовать ее для металла разных толщин. При трехфазной сварке за один проход успешно сваривают металл толщиной свыше 30 мм.
|
Конструктивные способы уменьшения деформаций и напряжений предусматриваются при проектировании сварного соединения. К ним относятся уменьшение количества сварных швов в изделии, симметричное расположение ребер жесткости, швов, косынок. Для уравновешивания деформаций припуски деталей на усадку должны быть равны усадке с тем, чтобы размеры конструкции после сварки соответствовали проектным. Необходимо предусматривать возможность использования зажимных сборочно-сварочных приспособлений для предотвращения смещения свариваемых кромок относительно друг друга в процессе сварки. Повышенная склонность к деформации свариваемых соединений алюминия и его сплавов способствует появлению в них горячих трещин. Особенно склонны к образованию горячих трещин стыковые швы, близко расположенные друг к другу из-за пересечения зон термического влияния. Необходимо конструктивно располагать швы на максимально возможном удалении друг от друга. Если нельзя разнести швы, соединяемые элементы изготавливают как единое целое.
Не менее важны технологические меры уменьшения деформаций. Необходимо подобрать оптимальный режим сварки, с тем, чтобы зона термического влияния была минимальной. Для этого стремятся использовать методы сварки, обеспечивающие высокую концентрацию энергии в дуге, а соединения сваривают на повышенных скоростях. На деформацию соединения существенно влияет порядок выполнения швов. При выполнении швов большой протяженности целесообразно использовать обратно-ступенчатый способ сварки. Сварку конструкций, имеющих несколько последовательно расположенных швов, целесообразно начинать со среднего шва, а затем поочередно, с каждой стороны, выполнять остальные швы, двигаясь к краям конструкции. Также необходимо учитывать, что соединения со скосом кромок более склонны к деформации, чем без скоса кромок и соединения с симметричной двусторонней разделкой кромок менее склонны к деформациям, чем с односторонней разделкой кромок. Для предотвращения продольного прогиба соединений применяют предварительный обратный выгиб свариваемых элементов, который подбирают опытным путем.
Для устранения остаточных деформаций применяют ударную и тепловую правку. Чтобы не повредить поверхность, алюминиевые соединения правят ударами резиновых и деревянных молотков. Правку стальными молотками можно выполнять только через алюминиевые или деревянные подкладки. Тепловую правку применяют для тех алюминиевых соединений, работоспособность которых не ухудшается сопровождающим нагрев разупрочнением, например, при правке малонагруженных элементов или конструкций из отожженного металла. Максимальная температура подогрева должна быть не выше температуры отжига для применяемого алюминиевого сплава.
К числу технологических особенностей сварки алюминия необходимо отнести и предварительный подогрев. Он имеет важное значение в виду того, что окисная пленка на поверхности свариваемых алюминиевых металлоконструкций прекрасно адсорбирует влагу и необходимо применять меры по удалению этой влаги. Если этого не делать, то в сварном соединении могут возникнуть дефекты. Поэтому, свариваемые кромки перед сваркой подогревают, используя газовые горелки (восстановительное пламя), горячий воздух или электроконтактные нагреватели.
Перед сваркой электрод необходимо подготовить. Царапины и следы шлифования оказывают большое влияние на проводимость электрода, поэтому заточку необходимо выполнять таким образом, чтобы на рабочем конце риски от заточного камня располагались только в продольном направлении. Если заточка электрода произведена на крупнозернистом абразивном круге или поперек оси электрода, гребни царапин, образовавшиеся при обработке, могут расплавиться при сварке и вызвать загрязнение сварного шва.
Вольфрам имеет большую твердость, чем большинство абразивных кругов, следовательно, и обрабатывать его нужно на алмазном круге или абразивном круге из боразона. На абразивном круге, на котором производится заточка вольфрамовых электродов, не должны обрабатываться никакие другие материалы. Частицы инородного материала, оставшиеся между зернами абразивного круга, затираются в царапины при заточке электрода. При сварке они постепенно переходят в сварочную ванну, вызывая тем самым загрязнение металла зоны сварки [12].
Известно, что форма заточки рабочей поверхности вольфрамового электрода определяет такие характеристики сварочной дуги, как распределение энергии и давление, оказываемое на сварочную ванну. Благодаря этому можно обеспечить благоприятное воздействие на процесс сварки. С увеличением давления, которое определяется величиной притупления заострённой части рабочей поверхности электрода, повышается глубина проплавления и улучшается форма шва [9].
Заточка электродов - тема, на которую существует множество дискуссий. Существует множество мнений и теорий об остроте конца электрода. При различной величине угла заточки электрода α изменяется ширина сварного шва, величина зоны термического влияния, устойчивость процесса сварки, глубина проплавления [11]. Согласно теории сварочных процессов, геометрическая форма рабочей поверхности электрода зависит от рода тока. Поскольку при сварке на постоянном токе прямой полярности большая часть энергии выделяется в свариваемом изделии, для электрода предпочтительна коническая форма с острым или притуплённым концом. При этом угол заточки должен составлять 14…60°, а длина конуса заточки должна быть равна 2…2,5 диаметрам электрода (рисунок 15). Электродом с заостренным концом предпочтительно сваривать очень тонкие металлы (0,125-1,0 мм). Вольфрамовые электроды марки ЭВЧ и электроды, легированные лантаном, подготовленные для сварки на переменном токе, имеют сферическую или шарообразную форму рабочего конца электрода, что является причиной оплавления ранее заострённой рабочей части электрода. Диаметр сферы должен быть не более 1,5 диаметра электрода.
Рисунок 16 – Требования к заточке рабочей поверхности вольфрамового электрода
При большом сварочном токе и малом размере сферы возможна эрозия электрода и загрязнение металла сварного шва вольфрамовыми включениями. При большом диаметре сферы и малом сварочном токе дуга подвержена хаотическому перемещению за счёт блуждания катодных пятен.
При сварке более толстого металла желательно притуплять конец электрода, иначе может произойти перегрев и расплавление кончика электрода, вызывая при этом загрязнение металла сварного шва.
Постановка задачи на проектирование технологического процесса.
На основании вышеприведенного анализа были сделаны следующие выводы:
• для изготовления каркаса вибростенда целесообразно применение дюралюминия повышенной прочности системы А1–Сu–Мg с легируемыми добавками марганца марки ВАД1 (Д24);
• применение в конструкции каркаса дюралюминия повышенной прочности дает значительный выигрыш в массе изделия, при этом сохраняются прочностные характеристики на уровне конструкционных углеродистых сталей;
• применение сварки неплавящимся электродом в среде инертных газов позволяет добиться требуемых высоких прочностных характеристик сварных соединений.
На основании сделанных выводов были поставлены следующие задачи на проектирование технологического процесса:
• рассчитать режимы сварки, выбрать необходимые сварочные материалы, на основании этого подобрать оборудование;
• подобрать необходимую технологическую оснастку;
• разработать планировку участка для сборки-сварки каркаса вибростенда.
Исходными данными для проектирования являются чертеж каркаса вибростенда, материал коленчатого вала – ВАД1, годовая программа выпуска – 2000 шт.
Рисунок 17 – Чертеж каркаса вибростенда
Конструкторский раздел
|
|
Состав сооружений: решетки и песколовки: Решетки – это первое устройство в схеме очистных сооружений. Они представляют...
Общие условия выбора системы дренажа: Система дренажа выбирается в зависимости от характера защищаемого...
Семя – орган полового размножения и расселения растений: наружи у семян имеется плотный покров – кожура...
Таксономические единицы (категории) растений: Каждая система классификации состоит из определённых соподчиненных друг другу...
© cyberpedia.su 2017-2024 - Не является автором материалов. Исключительное право сохранено за автором текста.
Если вы не хотите, чтобы данный материал был у нас на сайте, перейдите по ссылке: Нарушение авторских прав. Мы поможем в написании вашей работы!