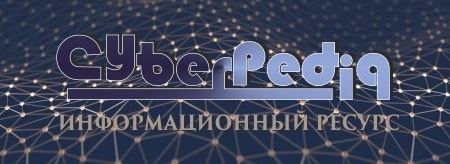
Организация стока поверхностных вод: Наибольшее количество влаги на земном шаре испаряется с поверхности морей и океанов (88‰)...
Автоматическое растормаживание колес: Тормозные устройства колес предназначены для уменьшения длины пробега и улучшения маневрирования ВС при...
Топ:
Основы обеспечения единства измерений: Обеспечение единства измерений - деятельность метрологических служб, направленная на достижение...
Когда производится ограждение поезда, остановившегося на перегоне: Во всех случаях немедленно должно быть ограждено место препятствия для движения поездов на смежном пути двухпутного...
Устройство и оснащение процедурного кабинета: Решающая роль в обеспечении правильного лечения пациентов отводится процедурной медсестре...
Интересное:
Национальное богатство страны и его составляющие: для оценки элементов национального богатства используются...
Отражение на счетах бухгалтерского учета процесса приобретения: Процесс заготовления представляет систему экономических событий, включающих приобретение организацией у поставщиков сырья...
Уполаживание и террасирование склонов: Если глубина оврага более 5 м необходимо устройство берм. Варианты использования оврагов для градостроительных целей...
Дисциплины:
![]() |
![]() |
5.00
из
|
Заказать работу |
|
|
Содержание.
1.Введение 3
2.Исходные данные 6
3.Характеристика сварной конструкции 7
4.Выбор способа сварки 9
5.Изучение особенности сварки стали 16Г2АФ.
Определение принципиальной схемы технологического процесса 12
6.Выбор сварочных материалов 15
7.Выбор основного и вспомогательного сварочного оборудования 18
8.Разработка технологического процесса сварки 29
8.1 Подготовка металла и конструкции к сборке и сварке 29
8.2 Сборка 31
8.3 Сварка 33
8.4 Подогрев металла 35
8.5 Контроль качества сварных соединений 36
8.6 Охрана труда при сварке в среде защитных газов 38
9. Список использованной литературы 43
|
Введение
Механизированная дуговая сварка в СО2- дуговая сварка, при которой подача плавящегося электрода или присадочного материала, а также относительное перемещение дуги и изделия выполняются механизмами, в качестве защитного газа поступающей в зону сварочной дуги используется углекислый газ (СО2) или смеси (80% Ar +20% СО2), (СО2+ О2).
Преимущество сварки в среде защитных газов заключается в следующем:
Недостатки сварки в среде защитных газов заключается в следующем:
• Вероятность нарушения газовой защиты на открытом воздухе и сквозняке
• Разбрызгивание электродного металла, особенно при сварке в углекислом газе
• Необходимость жидкостных систем охлаждения при сварке на режимах с повышенной мощностью
Сварка в среде защитных газов широко используется при изготовлении строительных металлических конструкций в заводских условиях и при возведении их на стадии укрупнения и окончательного монтажа.
Исходные данные.
Вид свариваемой конструкции - двутавровая балка.
Тип соединения - стыковое.
Характеристика шва - двухсторонний стыковой с полным проплавлением.
Положение шва — горизонтальное, нижнее
Условия производства — температура металла 20°С без кантовки.
3. Характеристика сварной конструкции.
Рисунок 1- Балка двутавровая.
Длина 3200мм (длина секций 1600мм);
Полка: ширина 700 мм, толщина 25 мм;
Стенка: высота 1000 мм, толщина 20 мм;
Сталь марки 16Г2АФ (t8/5 - 15-30 с).
Таблица 1 - Химический состав стали 16Г2АФ по ГОСТ 19281-89 (Прокат из стали повышенной прочности).
|
Массовая доля элементов, % | |||||||
С углерод | Mn марганец | Si кремний | Cr хром | Ni никель | Cu медь | V ванадий | N азот |
0,14..0,20 | 1,3…1,7 | 0,3…0,6 | Не более 0,40 | Не более 0,30 | Не более 0,30 | 0,08…0,14 | 0,015…0,030 |
Массовая доля серы не превышает 0,040%, фосфора- 0,035%.
Таблица 2- Механические свойства стали.
Класс прочности по ГОСТ 19281-89 | Предел текучести,
| Временное сопротивление,
| Относительное удлинение,
| Ударная вязкость KCU, Дж/см2, при температуре, °С | ||
+20 | -40 | -70 | ||||
Не менее | ||||||
440 | 440 | 590 | 19 | Не норм. | 39 | 29 |
Выбор способа сварки.
Рис.2 Механизированная сварка в защитном газе, схема процесса.
При среднесерийном и крупносерийном производстве элементов металлических конструкций сварку желательно осуществлять механизированными или автоматизированными методами.
При выборе вида сварки необходимо учитывать, что экономически и технически применение механизированной сварки для выполнения стыковых соединений целесообразно при длине швов более 300 мм, для сварки угловых швов при их длине более 1-1,5 м. Длина швов, выполненных механизированными методами сварки, неограниченна.
В тех случаях, когда при изготовлении возможно позиционирование («кантовка») изделия, лучшее формирование шва обеспечивается при сварке в нижнем положении и в «лодочку». Следует учитывать также, что механизированная сварка в углекислом газе возможна во всех пространственных положениях
Механизированная сварка в углекислом газе (СО2) является основной и наиболее распространенной технологией сварки плавлением на предприятиях машиностроительной отрасли. Она является экономичной, обеспечивает достаточно высокое качество сварных швов, особенно при сварке низкоуглеродистых и низколегированных сталей, требует более низкой квалификации сварщика, чем ручная дуговая сварка.
Защитный газ, выходя из сопла, вытесняет воздух из зоны сварки. Сварочная проволока подается вниз роликами, которые вращаются двигателем подающего механизма. Подвод сварочного тока к проволоке осуществляется через скользящий контакт.
Учитывая, что защитный газ активный и может вступать во взаимодействие с расплавленным металлом, механизированная сварка в углекислом газе имеет ряд особенностей. В качестве защитных газов применяют инертные (аргон и гелий) и активные (углекислый газ, водород, кислород и азот) газы, а также их смеси (Аг + Не, Аг + CO2, Аг + О2, CO2+ О2 и Др.).
|
При высокой температуре углекислый газ разлагается на окись углерода и кислород. В целом такая среда является окислительной по отношению к большинству компонентов металлов. Поэтому углекислый газ, защищая расплавленный металл от взаимодействия с воздухом, не может исключить окисление его компонентов. Сведение к минимуму влияния окислительных свойств газовой фазы на состав металла шва и его формирование является основной задачей.
Выбор сварочных материалов
Выбор вида и марки сварочного материала зависит от:
· марки свариваемой стали;
· вида сварки;
· условий эксплуатации конструкций, т.е. группы конструкций и климатического района, в котором эксплуатируется конструкция.
Сварочные материалы должны обеспечивать свойства металла шва на уровне свойств свариваемой стали.
Расход сварочных материалов (проволоки и электродов) рассчитывают по уравнению:
где М – расход электродов или проволоки, г;
F н – площадь наплавленного металла шва, см2;
γ – плотность стали (равна 7,8 г/см3);
Кр – коэффициент расхода, учитывающий неизбежные потери металла на угар, разбрызгивание и относительный вес электродного покрытия.
Таблица-3. Зависимость коэффициента расхода сварочных материалов от способа сварки.
Способ сварки | Коэффициент расхода Кр |
Автоматическая сварка под флюсом | 1,05 |
Механизированная, проволокой сплошного сечения в защитных газах Порошковой проволокой | 1,10-1,15 1,5-1,7 |
Ручная дуговая сварка покрытыми электродами | 1,05-1,07 |
Наиболее широко применяется проволока Св-08Г2С легированная кремнием и марганцем по ГОСТ 2246-70. В большинстве случаев ее выпускают диаметром 0,8-2,0 мм.
Для сварки стали 16Г2АФ мы будем использовать проволоку Св08Г2С-0
диаметром 1,2 мм, предназначенную для сварки (наплавки), с омедненной поверхностью.
Таблица 4. Химический состав проволоки Св-08Г2С-О по ГОСТ 2246-70, %
С углерод | Mn марганец | Si кремний | Cr хром | Ni никель | S сера | P фосфор |
0,05-0,11 | 1,80-2,10 | 0,70-0,95 | Не более 0,20 | Не более 0,25 | 0,025 | 0,03 |
Сварочные материалы, к которым относятся электроды, флюсы, сварочная проволока могут быть первопричиной брака при сварке, если их хранение не организовано. Поэтому к хранению сварочных материалов предъявляются определенные требования. Электроды, флюсы, сварочная проволока должны храниться в специальных сухих отапливаемых помещениях при температуре не ниже 15°С и относительной влажности не более 50%.
|
Сварочная проволока должна храниться в условиях, исключающих ее загрязнение и окисление. Не всегда это удается выполнять в производственных условиях, поэтому в цехах применяют специальные зачистные машины для подготовки сварочной проволоки перед сваркой. Сварочная проволока для сварки приходит к потребителю протравленной химическим способом, кассеты с проволокой упаковывают в герметически запаянные полиэтиленовые пакеты откуда предварительно откачивают воздух.
В качестве защитных используются активные газы (СО2) или смеси: 70% аргона и 30% углекислого газа (или кислорода) – для сварки углеродистых сталей; 80% аргона и 20% углекислого газа – для сварки легированных сталей.
Углекислый газ. При нормальном атмосферном давлении удельная плотность углекислого газа 0,00198г/см3. При давлении 7,53МПа углекислый газ сжижается. Температура сжижения газа при атмосферном давлении – 78,5о С. Хранят и транспортируют углекислый газ в стальных баллонах под давлением 6–7МПа. В стандартный баллон ёмкостью 40дм3 вмещается 25кг жидкого СО2, которая при испарении даёт 12 625дм3 газа. Жидкий СО2 занимает 60 – 80% объёма баллона, остальной объём заполнен испарившимся газом. Получают СО2 получаемую из отбросных газов производств аммиака, спиртов, а также на базе специального сжигания топлива и других производств. Жидкая двуокись углевода высшего и первого сортов применяется преимущественно для нужд сварочного производства.
Объемная доля двуокиси углерода высшего сорта (СО2), %, не менее 99,8%.
Объемная доля двуокиси углерода первого сорта (СО2), %, не менее 99,5%.
Массовая доля воды двуокиси углерода высшего и первого сорта отсутствует по ГОСТ 8050-85.
Баллоны для углекислого газа окрашены в черный цвет с желтой надписью. Давление в баллоне 25 кг/см2 Баллоны изготавливаются из цельных труб.
Баллоны делятся на 3 категории:
Малой вместимости – до 12 л.
Средней вместимости – от 12 до 40 л.
Большой вместимости – от 40 л.
На баллонах верхняя часть не окрашивается или вывешивается шайба, где указываются все данные о баллоне.
Рис.12 Термокарандаш.
Для зачистки сварных швов перед наложением последующих валиков и удаления брызг используем угловую шлифмашинку Makita 9566CV. 1,4кВт, 4000-10000 об./мин., диаметр диска 150 мм, двойная защитная изоляция, автоматическое отключение щёток, плавный пуск.
|
Рис. 13. Шлифовальная машина Makita 9566CV
Технические характеристики:
Потребляемая мощность - 1400 Вт
Макс. частота вращения диска – 4000-10000 об./мин.
Макс. диаметр диска марки PUREVA 430493 (толщ. 5мм) – 150 мм
Резьба шпинделя – М14x2
Масса – 1,2 кг
Сетевой шнур – 2,5 м
Выбираем фаскосниматель СНР-12 для снятия фаски на листовой стали под сварку. Возможна разделка односторонних и двухсторонних кромок. Скорость подачи равна скорости вращения фрезы. Обработка производится путем скалывания кромки специальной фрезой, качество получаемой поверхности - грубое.
Фаскосниматель может комплектоваться фрезами для работы с углеродистой, низколегированной и легированной сталью, а также алюминием.
Рис. 14 Фаскосниматель.
Баллон для углекислого газа предназначен для транспортировки и хранения углекислоты. Баллон для углекислоты комплектуется кольцом горловины, вентилем, предохранительным колпаком и опорным башмаком. Корпус углекислотных баллонов окрашивается эмалевой краской черного цвета. На баллон наносится надпись «УГЛЕКИСЛОТА» желтого цвета. Углекислотные баллоны емкостью 40 литров изготавливаются из стали марки –30ХГСА, 45, Д. ГОСТ 949-73.
Рис. 15 Балон для углекислого газа.
Сварочная маска (Щиток защитный лицевой) - Средство индивидуальной защиты лица работающих от воздействия опасных и вредных производственных факторов. Мы выбираем сварочную маску НН7 PREMIER Favori®T 2 фирмы РОСОМЗ.
Рис. 16 Сварочная маска.
В комплектацию сварочной маски входит Светофильтр – Смотровое стекло, ослабляющее интенсивность вредного излучения в оптической части спектра. Выбираем степень затемнения светофильтра С5.
Подготовка металла и конструкции к сборке и сварке.
Требования к сырью, материалам:
Материалы для изготовления деталей и сборочных единиц должны иметь документальное подтверждение их соответствия требованиям государственных стандартов, а также требованиям конструкторской документации.
Материалы должны быть очищены от загрязнений, окалины, коррозии, заусенцев и других дефектов. Поверхности не должны иметь вмятин и прочих повреждений.
Сварочные материалы, применяемые для сварки, должны обеспечивать механические свойства металл шва и сварного соединения (предел прочности, относительное удлинение, ударная вязкость) не ниже предельного показателя перечисленных свойств металла основных элементов конструкции, установленного для данной марки стали ГОСТ 19281 – 89. Острые кромки на деталях должны быть притуплены.
Требования к сварным соединениям:
Основные типы и конструктивные элементы швов сварных соединений должны соответствовать ГОСТ 14771-76
Свариваемые кромки должны быть сухими, не иметь заусенцев, трещин и других дефектов, видимых вооруженным глазом. Детали, поступающие на сварку, должны быть очищены от грязи, масла, окалины, коррозии.
Требования к сварным швам:
Сварные швы не должны иметь дефектов в виде трещин, пор, непроваров, несплавлений по кромкам, наплывов, прожогов, шлаковых включений, подрезов и др.
В целях избегания образования в швах пор и других включений торцевые
поверхности кромок и прилегающие к ним зоны металла шириной 25—30 мм
подлежат очистке от ржавчины, краски, масляных и других загрязнений. Очистку выполняют абразивными материалами или инструментом, а также газопламенной обработкой.
По окончании сварочных работ сварные швы и прилегающие к ним поверхности основного металла должны быть очищены от оксидной пленки и сварочных брызг.
Разделку кромок берем по ГОСТ 14771-76; сварных соединений С15.
Рисунок -17. Разделка кромок.
Стыковое соединение с К-образной разделкой кромок. С двумя симметричными скосами кромок С15. Что уменьшит затраты времени и энергии на разделку нижней кромки.
Сборка
Для изготовления сварных конструкций требуется правильная сборка
деталей свариваемого изделия, т.е. их правильная взаимная установка и
закрепление. Сборка может осуществляться прихватками или в специальных сборочно-сварочных приспособлениях. Прихватки представляют со-
бой короткие швы.
В строительных конструкциях используются два вида соединения сортового проката и холодногнутых профилей: накладками и встык.
Встык - основной вид соединения. Сборка и сварка соединений сортового проката этим способом проводятся до установки деталей в конструкцию. Соединения накладками можно выполнять в процессе общей сборки.
Для того, чтобы обеспечить высокое качество сборки на стеллажах (рис. 18), необходимо строго соблюдать определенную последовательность выполнения работ
.
Рис. 18. Сборка встык двутавровой балки
Сварка.
Большое значение для уменьшения внутренних напряжений и деформаций при сварке швеллеров и балок имеет соблюдение правильной последовательности наложения швов и направления сварки. В соединениях в первую очередь сваривают стенки, а затем полки. Перед наложением шва с обратной стороны абразивным кругом из места зазора удаляют шлак.
Сварные швы двутавровой балки соединяемые накладками, выполняются в последовательности, указанной на рис.19. Положение сварки –горизонтальное.
Рис-19 Сварка встык двутавровой балки. Последовательность сварки швов.
Если в первую очередь сварить стыки поясов, то стык стенки придется выполнять в условиях жесткого закрепления, что может способствовать образованию трещин в процессе сварки. Когда вначале сваривают стык стенки, в стыках поясов возникает высокий уровень остаточных напряжений
растяжения, что может снизить усталостную прочность при работе на изгиб.
Для облегчения условий сварки стыка участки поясных швов балки длиной
L иногда не доваривают, а выполняют их после сварки стыковых швов. Так как поперечная усадка свариваемого последним шва будет восприниматься элементом длиной L, то значение остаточных напряжений окажется меньше, чем при жестком закреплении.
Номер слоя | Марка сварочной проволоки | Диаметр сварочной
Проволоки ![]() | Iсв A | Uдуги В | Vсв См/с | Расход Газа СО2 л/мин. | Род тока Полярность | Положение сварки |
Корневой Заполняющий Облицовочный | СВ08Г2С | 1,2 | 160-180 230-300 220-250 | 22-24 | 0,2-0,3 | 8-16 | Постоянный Обратная | Горизонтально-вертикальное |
Таблица 6. Параметры режима механизированной сварки, с использованием сварочной проволоки Св08Г2С.
Площадь сечения швов представляет собой сумму площадей элементарных геометрических фигур, их составляющих.
+(25
2)+((0.75
)
=194
При наших режимах за один проход мы перекрываем около 30 , поэтому при такой площади сечения делаем 6 проходов по 3 с каждой стороны.
Перед наложением каждого слоя необходимо производить контроль температуры металла с помощью термокарандаша (как написано выше).
При горизонтально-вертикальной сварке двутавровой балки существует несколько особенностей которые заключаются в колебательных движениях при сварке различных проходов сварного шва.
Сварку корневого шва производим без каких либо колебательных движений что в полной мере заполняет зазор шва сварочным металлом и не прожигает кромки.
После первого и последующих проходов необходимо зачистить кромки от окисной пленки и сварочных брызг.
Сварку заполняющего шва производим с помощью возвратно-поступательных движений. Этот способ хорошо разогревает металл и дает более глубокое проплавление.
Сварку облицовочного шва производим с помощью криволинейного движения с выпуклостью в сторону не сваренного участка (елочкой). Придает шву заключительное эстетическое формирование без наплывов, подрезов и неровностей.
Подогрев металла
t8/5= ·
· К;
t8/5= ·
· 1=30,4 с.
= 2,5 - толщина свариваемого металла, см;
- коэффициент теплопроводности для низколегированной стали.
С=3,6 ДЖ/см- удельная объемная теплопроводность.
Тн =100- начальная температура металла;
К = 1 - коэффициент приведения, учитывающий различные условия теплоотвода стыковых и угловых швов от расплавленного металла в основной металл.
- эффективная погонная энергия Дж/см;
=
Дж/см;
=0,7-эффективный КПД процесса нагрева металла дугой для сварки в СО2;
=230 А- сила сварочного тока;
=24 В- напряжение дуги;
= 0,3 (см/сек)-скорость сварки
Список использованной литературы.
Маслов В. И. Сварочные работы Изд. центр «Академия», 1999. - 240 с
ГОСТ 12.3.003-86 «Работы электросварочные. Требования безопасности».
Содержание.
1.Введение 3
2.Исходные данные 6
3.Характеристика сварной конструкции 7
4.Выбор способа сварки 9
5.Изучение особенности сварки стали 16Г2АФ.
Определение принципиальной схемы технологического процесса 12
6.Выбор сварочных материалов 15
7.Выбор основного и вспомогательного сварочного оборудования 18
8.Разработка технологического процесса сварки 29
8.1 Подготовка металла и конструкции к сборке и сварке 29
8.2 Сборка 31
8.3 Сварка 33
8.4 Подогрев металла 35
8.5 Контроль качества сварных соединений 36
8.6 Охрана труда при сварке в среде защитных газов 38
9. Список использованной литературы 43
Введение
Механизированная дуговая сварка в СО2- дуговая сварка, при которой подача плавящегося электрода или присадочного материала, а также относительное перемещение дуги и изделия выполняются механизмами, в качестве защитного газа поступающей в зону сварочной дуги используется углекислый газ (СО2) или смеси (80% Ar +20% СО2), (СО2+ О2).
Преимущество сварки в среде защитных газов заключается в следующем:
Недостатки сварки в среде защитных газов заключается в следующем:
• Вероятность нарушения газовой защиты на открытом воздухе и сквозняке
• Разбрызгивание электродного металла, особенно при сварке в углекислом газе
• Необходимость жидкостных систем охлаждения при сварке на режимах с повышенной мощностью
Сварка в среде защитных газов широко используется при изготовлении строительных металлических конструкций в заводских условиях и при возведении их на стадии укрупнения и окончательного монтажа.
Исходные данные.
Вид свариваемой конструкции - двутавровая балка.
Тип соединения - стыковое.
Характеристика шва - двухсторонний стыковой с полным проплавлением.
Положение шва — горизонтальное, нижнее
Условия производства — температура металла 20°С без кантовки.
3. Характеристика сварной конструкции.
Рисунок 1- Балка двутавровая.
Длина 3200мм (длина секций 1600мм);
Полка: ширина 700 мм, толщина 25 мм;
Стенка: высота 1000 мм, толщина 20 мм;
Сталь марки 16Г2АФ (t8/5 - 15-30 с).
Таблица 1 - Химический состав стали 16Г2АФ по ГОСТ 19281-89 (Прокат из стали повышенной прочности).
Массовая доля элементов, % | |||||||
С углерод | Mn марганец | Si кремний | Cr хром | Ni никель | Cu медь | V ванадий | N азот |
0,14..0,20 | 1,3…1,7 | 0,3…0,6 | Не более 0,40 | Не более 0,30 | Не более 0,30 | 0,08…0,14 | 0,015…0,030 |
Массовая доля серы не превышает 0,040%, фосфора- 0,035%.
Таблица 2- Механические свойства стали.
Класс прочности по ГОСТ 19281-89 | Предел текучести,
| Временное сопротивление,
| Относительное удлинение,
| Ударная вязкость KCU, Дж/см2, при температуре, °С | ||
+20 | -40 | -70 | ||||
Не менее | ||||||
440 | 440 | 590 | 19 | Не норм. | 39 | 29 |
Выбор способа сварки.
Рис.2 Механизированная сварка в защитном газе, схема процесса.
При среднесерийном и крупносерийном производстве элементов металлических конструкций сварку желательно осуществлять механизированными или автоматизированными методами.
При выборе вида сварки необходимо учитывать, что экономически и технически применение механизированной сварки для выполнения стыковых соединений целесообразно при длине швов более 300 мм, для сварки угловых швов при их длине более 1-1,5 м. Длина швов, выполненных механизированными методами сварки, неограниченна.
В тех случаях, когда при изготовлении возможно позиционирование («кантовка») изделия, лучшее формирование шва обеспечивается при сварке в нижнем положении и в «лодочку». Следует учитывать также, что механизированная сварка в углекислом газе возможна во всех пространственных положениях
Механизированная сварка в углекислом газе (СО2) является основной и наиболее распространенной технологией сварки плавлением на предприятиях машиностроительной отрасли. Она является экономичной, обеспечивает достаточно высокое качество сварных швов, особенно при сварке низкоуглеродистых и низколегированных сталей, требует более низкой квалификации сварщика, чем ручная дуговая сварка.
Защитный газ, выходя из сопла, вытесняет воздух из зоны сварки. Сварочная проволока подается вниз роликами, которые вращаются двигателем подающего механизма. Подвод сварочного тока к проволоке осуществляется через скользящий контакт.
Учитывая, что защитный газ активный и может вступать во взаимодействие с расплавленным металлом, механизированная сварка в углекислом газе имеет ряд особенностей. В качестве защитных газов применяют инертные (аргон и гелий) и активные (углекислый газ, водород, кислород и азот) газы, а также их смеси (Аг + Не, Аг + CO2, Аг + О2, CO2+ О2 и Др.).
При высокой температуре углекислый газ разлагается на окись углерода и кислород. В целом такая среда является окислительной по отношению к большинству компонентов металлов. Поэтому углекислый газ, защищая расплавленный металл от взаимодействия с воздухом, не может исключить окисление его компонентов. Сведение к минимуму влияния окислительных свойств газовой фазы на состав металла шва и его формирование является основной задачей.
Изучение особенности сварки стали 16Г2АФ. Определение принципиальной схемы технологического процесса.
Сталь 16Г2АФ: Сталь низколегированная конструкционная марганцово-ванадиевая. Степень раскисления - Сп.
Высокопрочная сталь 16Г2АФ за счет комплексного микролегирования и специальной обработки (контролируемой прокатке) обладает высокой прочностью, низким порогом хладноломкости, хорошей свариваемостью и используется при сооружении таких сварных конструкций, как резервуары высокого давления, железнодорожные и автомобильные мосты, магистральные трубопроводы. Под действием сварочного источника тепла в металле происходит изменение структуры и трансформация сульфидов и оксидов железа и марганца. Появление в стали 16Г2АФ структуры бейнита и мартенсита при скоростях охлаждения свыше 20°С/с приводит к уменьшению ударной вязкости участка зоны термического влияния (ЗТВ) а также влияет и на характер распространения трещины. Так как оксисульфидные включения являются главными концентраторами напряжений в структуре, их форма и размеры также существенно влияют на зарождение и траекторию движения трещины. Разрушение сварных конструкций чаще всего происходит именно в ЗТВ, структура и свойства которой зависят от параметров термического цикла сварки. Так, при быстрых скоростях охлаждения ( =95
С/с) неметаллические включения не успевают полностью раствориться в матрице. С уменьшением скорости охлаждения, когда металл более длительное время находится при высоких температурах, наблюдается более полное растворение включения (
=65
С/с). При средних скоростях охлаждения (
=43
С/с) происходит полное растворение строчечных включений и выделение их в виде мелкодисперсных цепочек. При дальнейшем уменьшении скорости охлаждения происходит коалесценция включений с образованием сначала более крупных частиц, расположенных в строчку (
= 25
С/с), а затем и сплошных строчечных включений (
= 15
С/с). Сварка стали с пределом текучести более 390 МПа (16Г2АФ) требует особого внимания. При повышенном содержании легирующих элементов и особенно углерода в стали проявляется чувствительность металла к образованию малопластичных закалочных структур. Образование закаленных участков в сочетании с высоким содержанием диффузионного водорода в металле шва и наличием остаточных сварочных напряжений может поспособствовать образованию холодных трещин.
В нашем случае сталь низколегированная класса прочности 440 с карбо-
нитридным упрочнением. Она имеет высокие значения эквивалентного углерода Сэкв = 0,50%:
Сэкв =С+ +
+
=
0.17+ +
=0.504%
> 0.45%
Параметр трещинообразования Pc=0.417
Pc = Pсм + +
Сталь 16Г2АФ толщиной 25 мм содержит: С - 0.17%, Si - 0.4%,
Mn - 1.5%, Cr - 0.2%, Ni - 0.1%, Cu - 0.2%, V - 0.12%.
Pсм = C + +
+
+ 5В =
=0,17+ +
+
=0,292
Pc = 0,292 + +
=0.417
0,4> 0.3
Результат указывает на склонность стали к образованию холодных трещин.
Предотвратить появление закалочных структур можно путём регулирования термического цикла сварки и получения цикла со сниженной до требуемого уровня скоростью охлаждения металла. Это может быть достигнуто посредством принудительного нагрева стали в месте сварки, а также путём повышения эффективной погонной энергии за счёт увеличения силы сварочного тока и уменьшения скорости сварки.
Подогрев зоны сварного соединения перед сваркой или в процессе сварки уменьшает градиент температурного поля и снижает скорость охлаждения, чем в значительной степени способствует уменьшению внутренних напряжений и вероятности образования горячих и холодных трещин.
Tподогр.= 350
[C]=[Cc] (1+0.005
e)= 0.504
(1+0.005
25)=0.567
Tподогр.= 350 =350
=200
Необходимость предварительного подогрева определим, позже рассчитав значение Т8/5, учитывая параметры режима сварки.
Выбор сварочных материалов
Выбор вида и марки сварочного материала зависит от:
· марки свариваемой стали;
· вида сварки;
· условий эксплуатации конструкций, т.е. группы конструкций и климатического района, в котором эксплуатируется конструкция.
Сварочные материалы должны обеспечивать свойства металла шва на уровне свойств
|
|
Адаптации растений и животных к жизни в горах: Большое значение для жизни организмов в горах имеют степень расчленения, крутизна и экспозиционные различия склонов...
Своеобразие русской архитектуры: Основной материал – дерево – быстрота постройки, но недолговечность и необходимость деления...
Археология об основании Рима: Новые раскопки проясняют и такой острый дискуссионный вопрос, как дата самого возникновения Рима...
Поперечные профили набережных и береговой полосы: На городских территориях берегоукрепление проектируют с учетом технических и экономических требований, но особое значение придают эстетическим...
© cyberpedia.su 2017-2024 - Не является автором материалов. Исключительное право сохранено за автором текста.
Если вы не хотите, чтобы данный материал был у нас на сайте, перейдите по ссылке: Нарушение авторских прав. Мы поможем в написании вашей работы!