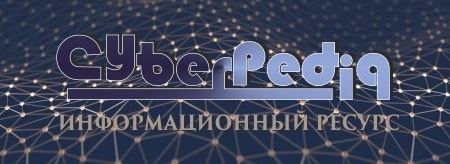
Кормораздатчик мобильный электрифицированный: схема и процесс работы устройства...
Двойное оплодотворение у цветковых растений: Оплодотворение - это процесс слияния мужской и женской половых клеток с образованием зиготы...
Топ:
Устройство и оснащение процедурного кабинета: Решающая роль в обеспечении правильного лечения пациентов отводится процедурной медсестре...
Выпускная квалификационная работа: Основная часть ВКР, как правило, состоит из двух-трех глав, каждая из которых, в свою очередь...
Эволюция кровеносной системы позвоночных животных: Биологическая эволюция – необратимый процесс исторического развития живой природы...
Интересное:
Берегоукрепление оползневых склонов: На прибрежных склонах основной причиной развития оползневых процессов является подмыв водами рек естественных склонов...
Что нужно делать при лейкемии: Прежде всего, необходимо выяснить, не страдаете ли вы каким-либо душевным недугом...
Как мы говорим и как мы слушаем: общение можно сравнить с огромным зонтиком, под которым скрыто все...
Дисциплины:
![]() |
![]() |
5.00
из
|
Заказать работу |
|
|
МЕТОДИЧЕСКОЕ ПОСОБИЕ
по выполнению практических работ
Дисциплина: ОП.02 Техническая механика
Раздел 3 Детали машин
Согласовано: | Разработал: |
Руководитель методической службы ____________ Н.В. Дмитриева «___»__________2020 | Преподаватель ____________ А.Н. Иванов «___»__________2020 |
Председатель ПЦК 23.02.04 ____________ А.Н. Иванов «___»__________2020 |
2020
Рецензенты:
Преподаватель ГАПОУ БАСК__________С.Г. Кольцова
Директор ООО «Автомастер» __________ С.П. Белоусов Содержание
Введение | 4 |
Практическая работа № 8 Расчет разъемных и неразъемных соединений на срез и смятие. | 6 |
Практическое занятие № 9 Кинематический и силовой расчет передачи. | 12 |
Практическое занятие № 10 Расчет зубчатой передачи. | 17 |
Практическая работа № 11 Расчет передачи винт-гайка. | 23 |
Практическая работа № 12 Расчет клиноременной передачи. | 24 |
Практическая работа № 13 Расчет цепной передачи. | 26 |
Практическая работа № 14 Расчет вала на прочность по эквивалентным напряжениям | 27 |
Список литературы | 28 |
Приложения | 29 |
Введение
Методическое пособие по выполнению практических работ по общепрофессиональной дисциплине ОП.02 Техническая механика» предназначено для обучающихся по специальности 23.02.04 Техническая эксплуатация подъемно-транспортных, строительных, дорожных машин и оборудования (по отраслям).
Дисциплина ОП.02 Техническая механика состоит из трех разделов: «Теоретическая механика», «Сопротивление материалов» и «Детали машин». По рабочей программе учебной дисциплине предусмотрено на практические занятия 28 часов. И охватывают все разделы и темы дисциплины ОП.02 Техническая механика.
Данное методическое пособие способствует освоению обучающимися умений и знаний, а так-же формированию общих и профессиональных компетенций:
|
Код ПК, ОК | Умения | Знания |
ОК 01, ОК 02, ОК 04, ПК 2.3, ПК 3.2, ПК 3.3, | - выполнять основные расчеты по технической механике; - выбирать материалы, детали и узлы, на основе анализа их свойств, для конкретного применения; - выполнять испытания материалов и конструкций | - основы теоретической механики, сопротивления материалов, деталей машин; - основные положения и аксиомы статики, кинематики, динамики и деталей машин; - элементы конструкций механизмов и машин; - характеристики механизмов и машин |
Методическое пособие позволяет выполнять практические работы, как в рамках учебного урока, так и дома, самостоятельно. Для этого в приложениях приведена вся необходимая справочная информация: Параметры электродвигателей, Механические характеристики сталей, Размеры и значения мощности и коэффициентов для клиновых ремней. Для более полного ознакомления с темами учебного курса приведен список рекомендуемой литературы.
Работа выполняется обучающимися в соответствии с индивидуальным вариантом, в ученической тетради для практических работ или с использованием ПК. Вариант состоит из двух цифр – порядкового номера обучающегося в журнале. По одной цифре выбирается схема, а по другой числовые значения параметров. После выполнения каждая практическая работа защищается преподавателю. Схемы вычерчивается с помощью карандаша и линейки с соблюдением масштаба.
При оформлении работы необходимо соблюдать принятые обозначения и последовательность записей, руководствуясь действующим стандартом предприятия и требованиями ЕСКД.
Раздел 3 Детали машин
Практическая работа № 8
Практическая работа № 9
Кинематический и силовой расчет передачи
Цель работы – научиться:
1 Читать кинематические схемы комбинированных приводов.
2 Подбирать двигатели (в том числе электрические) по заданным параметрам привода.
|
3 Определять передаточные числа различных передач. КПД и способы его повышения.
Задание
1 По полученному варианту выбрать схему привода и параметры передачи.
2 Подобрать оптимальный электродвигатель
3 Произвести кинематический расчет привода
4 Произвести силовой расчет привода
Порядок выполнения работы
1 Ознакомиться с данными методическими указаниями.
Вычертить предложенную схему привода исполнительного органа, согласно первой цифре варианта (таблица 4). Из таблицы 3 выписать (согласно второй цифре варианта) параметры привода (на выходном валу).
Таблица 3 Параметры привода
Вторая цифра варианта | P2, кВт | n2, мин-1 | Вид зубьев |
0 | 1,0 | 100 | прямозубая |
1 | 1,5 | 140 | косозубая |
2 | 2,0 | 180 | прямозубая |
3 | 2,5 | 220 | косозубая |
4 | 3,0 | 260 | прямозубая |
5 | 3,5 | 300 | косозубая |
6 | 4,0 | 340 | прямозубая |
7 | 4,5 | 380 | косозубая |
8 | 5,0 | 420 | прямозубая |
9 | 5,5 | 460 | косозубая |
Таблица 4 Схемы привода исполнительного органа
0 | 1 |
2 | 3 |
4 | 5 |
2 Подбор электродвигателя
2.1 Определяем общий КПД привода по формуле 9
ηобщ = ηр.п. ·ηз.п, (9)
где: ηр.п. – КПД ременной передачи, 0,92…0,97;
ηз.п. – КПД зубчатой передачи, 0,96…0,98 – цилиндрическая, 0,95…0,97 – коническая.
2.2 Определяем требуемую мощность электродвигателя
Pэ.д. = P2 / ηобщ, (10)
2.3 Рассчитываем ориентировочную частоту вращения электродвигателя nэ. Выбираем передаточное число ступеней (для клиноременной передачи iр.п . = 2…7, для зубчатой iз.п . = 1; 1.25; 1.6; 2; 2.5; 3.15; 4; 5; 6.3).
iобщ = iр.п. · iз.п ., (11)
nэ = n2 · iобщ, (12)
2.4 По полученным значениям Pэ и nэ выбираем электродвигатель (приложение 1 и 2).
3 Кинематический расчет
3.1 Уточняем общее передаточное число привода
i´общ = nэ.д. / n2, (13)
3.2 Производим разбивку i´общ по ступеням привода. Окончательно принимаем стандартное значение передаточного числа зубчатой передачи редуктора i´з.п, тогда передаточное число ременной передачи:
i´р .п . = i´общ / i´з .п ., (14)
3.3 Определяем частоту вращения и угловые скорости валов:
вал электродвигателя:
ωэ.д. = π · nэ.д. / 30, (рад/с) (15)
|
ведущий вал редуктора:
n1 = nэ .д . / i´р .п ., (16)
ω1 = ωэ.д. / i´р.п ., (17)
ведомый вал редуктора:
n2 = n1 / i´з .п ., (18)
ω 2 = ω 1 / i´з .п ., (19)
4 Производим силовой расчет
4.1Крутящие моменты на валах привода:
вал электродвигателя:
Мэ.д. = Рэ.д. / ωэ.д., (Н·м) (20)
ведущий вал редуктора:
М1 = Мэ.д. · i´р.п. ·ηр.п ., (21)
ведомый вал редуктора:
М2 = М1 · i´з.п. · ηз.п., (22)
Вывод
В выводе необходимо указать результаты работы. Насколько оптимально удалось подобрать электродвигатель. Какие параметры имеют ременная и зубчатая передачи.
Контрольные вопросы
1 Преимущества и недостатки ременной передачи?
2 Преимущества и недостатки зубчатой передачи?
3 Преимущества и недостатки прямозубой, косозубой, шевронной передачи?
4 Что такое передаточное число и как оно определяется?
5 Что такое КПД и способы его повышения?
6 От каких параметров зависит требуемая мощность электродвигателя?
7 Типы передач?
8 Типы электродвигателей?
9 Из каких элементов состоит предложенная кинематическая схема?
Практическая работа № 10
Расчет зубчатой передачи
Цель работы – научиться:
1 Правильно подбирать материал для зубчатых колес учитывая все факторы.
2 Назначать режимы термообработки зубчатых колес.
3 Определять основные параметры зубчатых передач.
4 Владеть основными формулами расчета передач.
5 Разбираться во всем многообразии существующих зубчатых передач.
Задание
Расчет зубчатой передачи производить по ранее полученным схеме и данным в практической работе №9
1 Подобрать материал для изготовления зубчатых колес.
2 Определить допускаемые напряжения.
3 Определить расчетные коэффициенты.
4 Рассчитать межосевое расстояние и основные параметры передачи.
5 Расчет основных размеров зубчатых колес.
Порядок выполнения работы
|
1 Ознакомиться с данными методическими указаниями.
Подбор материалов для зубчатых колес
По приложению 3 выбираем материал для изготовления шестерни и колеса и назначаем термообработку. Рекомендации: Следует выбирать более распространенный и дешевый материал и назначать термообработку различную для шестерни (большую) и колеса (меньшую). Из табличных данных выбираем примерно среднее значение твердости как наиболее вероятное. При этом для лучшей приработки зубьев и равномерного их изнашивания необходимо чтобы твердость зубьев шестерни была больше твердости зубьев колеса, и выполнялось условие:
НВ1 = НВ2 + 20…30, (23)
- для прямозубых цилиндрических и конических передач;
НВ1 = НВ2 + 60…80, (24)
- для косозубых, шевронных передач и для конических передач с круговыми зубьями.
2 Определяем допускаемые напряжения
2.1 Допускаемые контактные напряжения
[σН] = (σН0 / [ sН]) · КН L, (25)
где: σН0 – предел контактной выносливости рабочих поверхностей зубьев (Приложение 4);
[ sН] – допускаемый коэффициент безопасности, [ sН] = 1,1 – при однородной структуре материала (нормализация, улучшение, объемная закалка), [ sН] = 1,2 при неоднородной структуре (поверхностная закалка, цементация, азотирование и др.);
КН L – коэффициент долговечности, КН L = 1 – при длительной работе передачи, КН L ≤ 2,6 – для нормализованных и улучшенных колес (кратковременно работающие передачи), КН L ≤ 1,8 – при поверх-ностном упрочнении (кратковременно работающие передачи).
При расчете цилиндрических и конических прямозубых передач в качестве допускаемого напряжения принимают [σН] того зубчатого колеса, для которого оно меньше; как правило, это [σН]2, т.е.
[σН] = [σН]2, (26)
При расчете зубчатых передач цилиндрических косозубых, шевронных и конических с круговым зубом используют среднее допускаемое контактное напряжение:
[σН] = 0,45 ([σН]1 + [σН]2), (27)
Это напряжение не должно превышать: для цилиндрических косозубых и шевронных колес 1,23[σН]2; для конических колес 1,15[σН]2. Если эти условия не выполняются, то принимают
[σН] = 1,23[σН]2 или [σН] = 1,15[σН]2.
2.2 Допускаемые напряжения изгиба
[σ F] = (σ F0 / [ sF]) · КН L · К Fc, (28)
где: σ F0 – предел выносливости зубьев при изгибе (Приложение 4);
[ sF] – допускаемый коэффициент безопасности, [ sF] = 1,75 – для колес изготовленных из поковок и штамповок, [ sF] = 2,3 – из литых заготовок;
КН L – коэффициент долговечности, при длительно работающей передаче КН L = 1;
К Fc – коэффициент, учитывающий влияние двустороннего приложения нагрузки; К Fc = 1 при одностороннем приложении нагрузки (передача не реверсивная); К Fc = 0,7…0,8 при двустороннем приложении нагрузки (передача реверсивная).
|
3 Определяем расчетные коэффициенты
3.1 Коэффициент ширины венца колеса относительно меж-осевого расстояния (для цилиндрической передачи)
ψа = b2 / aw, (29)
принимают из ряда стандартных чисел: 0,1; 0,125; 0,16; 0,2; 0,25; 0,315; 0,4; 0,5; 0,63; 0,8 (СТ СЭВ 229 – 75) в зависимости от положения колес относительно опор:
ψа
При симметричном расположении…… 0,4…0,5
При несимметричном расположении… 0,25…0,4
При консольном расположении одного
или обоих колес………………………... 0,2…0,25
Для шевронных передач………………. 0,4…0,63
Для открытых передач………………… 0,1…0,2
3.2 Коэффициент ширины зубчатого венца (для конической передачи)
ψ d = 0,166 √ iз.п.2 + 1, (30)
3.3 Коэффициенты неравномерности распределения нагрузки по ширине зубчатого венца
КНβ = К Fβ = 1, (31)
- для прирабатывающихся цилиндрических прямозубых и косозубых колес, прямозубых конических колес;
КНβ = К Fβ = 1,1, (32)
- для конических передач с круговыми зубьями.
Вывод
Указать основные параметры зубчатой передачи, которые рассчитали в этой практической работе.
Контрольные вопросы
1 Типы механических передач, их назначение и характеристики
2 Основные геометрические параметры зубчатых передач?
3 Понятие корригирования?
4 Виды разрушения передачи?
5 По каким параметрам оптимизируют конструкцию зубчатых колес?
6 Конические зубчатые передачи. Область применения.
7 Силы в зацеплении различных зубчатых передач?
8 Какие потери определяют КПД зубчатой передачи?
9 От каких характеристик материала зависят контактная выносливость и допускаемые контактные напряжения?
10 Какие формы зубьев применяют?
Практическая работа № 11
Расчет передачи винт-гайка
Практическая работа № 12
Задание
Расчет клиноременной передачи производить по ранее полученным схеме и данным в практической работе №9
1 Рассчитать диаметры шкивов.
2 Определить межосевое расстояние.
3 Рассчитать и подобрать ремень.
4 Определить необходимое количество ремней.
Порядок выполнения работы
1 Ознакомиться с данными методическими указаниями.
По таблицы приложения 5 определяем профиль ремня и минимальный* диаметр ведущего шкива.
Определяем диаметр ведомого шкива по формуле 59
D2 = D1 · i´р.п., (59)
где: D1 – диаметр ведущего шкива, мм;
D2 – диаметр ведомого шкива, мм;
i´р.п. – уточненное передаточное число ременной передачи (см. практическая работа №9)
Диаметры шкивов необходимо округлить до стандартного (ГОСТ с 20889-90 до ГОСТ 20898-90), мм: 63, 71, 80, 90, 100, 112, 125, 140, 160, 180, 200, 224, 250, 280, 315, 355, 400, 450, 500, 560, 630, 710, 800, 900, 1000, 1120, 1250, 1400, 1600, 1800, 2000, 2240, 2500.
* Необходимо помнить: чем больше диаметр ведущего шкива – тем больше передаваемая им мощность.
2 Определяем межосевое расстояние
Минимальное межосевое расстояние,мм:
А min = 0.55(D1 + D2) + h, (60)
где: h – высота сечения ремня.
Максимальное межосевое расстояние, мм:
А max = 2(D1 + D2), (61)
3 Определяем необходимую длину ремня при принятом межосевом расстоянии:
Lp = 2 A + π(D1 + D2)/2 + (D2 – D1)2/4 A, (62)
Найденное значение расчетной длины ремня округляем до стандартного по ГОСТ 1284-98 (см. приложение 5).
4 Определяем необходимое число клиновых ремней
z = N / (N0· k1· k2), (63)
где: N – мощность на ведущем валу, кВт;
N0 – Мощность передаваемая одним ремнем, кВт (приложение 6);
k1 – Коэффициент, учитывающий значение угла обхвата (приложение 7);
k2 – Коэффициент, учитывающий влияние режиме работы (приложение 7).
Вывод
Необходимо указать количество и размер выбранных клиновых ремней. Диаметры ведущего и ведомого шкивов.
Контрольные вопросы
1 Принцип действия ременной передачи?
2 Типы ремней, преимущества и недостатки каждого типа?
3 Какие силы возникают в ветвях ремня?
4 Напряжения в ремне?
5 Какие виды скольжения возникают в ременной передачи?
6 Почему клиновые ремни способны передавать большие нагрузки, чем плоские?
7 Область применения ременных передач?
8 В чем особенность передач зубчатыми ремнями?
9 Область применения зубчатоременных передач?
10 Способы натяжения ремней?
Практическая работа № 13
Расчет цепной передачи
Практическая работа № 14
Список литературы
Печатные издания
1.Эрдеди А. А., Эрдеди, Н. А. Техническая механика. 5-е изд./- М.: Издательский центр «Академия», 2018. - 528 с.
2.Асадулина, Е. Ю. Техническая механика: сопротивление материалов: учебник и практикум для СПО / Е. Ю. Асадулина.- М.: Юрайт, 2017. – 290 с.
Электронные издания (электронные ресурсы)
1. Лукьянов, А.М. Техническая механика [Электронный ресурс]: учебник / А.М. Лукьянов, М.А. Лукьянов. - Электрон. дан. - М.: УМЦ ЖДТ, 2014.
3.Миролюбов, И.Н. Сопротивление материалов. Пособие по решению задач [Электронный ресурс]: учебно-методическое пособие / И.Н. Миролюбов, Ф.З. Алмаметов, Н.А. Курицин [и др.]. - Электрон. дан. - СПб.: Лань, 2014.
Дополнительные источники
1. Олофинская В.П. Техническая механика: Курс лекций с вариантами практических и тестовых заданий. – М.: ФОРУМ, 2017. - 348 с.
2 ГОСТ 2 105 – 95 «Единая система конструкторской документации (ЕСКД). Общие требования к текстовым документам.
Приложения
Приложение 1
Основные параметры асинхронных электродвигателей
с фазным ротором серии АК
Тип двигателя | Мощность, кВт | Частота вращения, мин-1 | Момент инерции, кг·м2 | Масса, кг | Ммах/Мном |
АК 51-4 АК 52-4 АК 60-4 АК 61-4 АК 62-4 | 2,5 4,5 7 10 14 | 1370 1400 1400 1420 1420 | 0,05 0,065 0,11 0,14 0,16 | 84 105 125 145 160 | 2 2 2 2 2,4 |
АК 71-4 АК 72-4 АК 81-4 АК 82-4 АК 91-4 АК 92-4 | 20 28 40 55 75 100 | 1420 1420 1440 1440 1460 1460 | 0,28 0,33 0,63 0,75 1,22 1,90 | 235 260 400 440 640 710 | 2,5 2,5 2,6 2,8 2,8 3 |
АК 51-6 АК 52-6 АК 60-6 АК 61-6 АК 62-6 | 1,7 2,8 4,5 7 10 | 905 920 925 940 940 | 0,05 0,065 0,19 0,24 0,28 | 82 103 125 145 160 | 2 2 1,8 1,8 2 |
АК 71-6 АК 72-6 АК 81-6 АК 82-6 АК 91-6 АК 92-6 | 14 20 28 40 55 75 | 950 950 965 965 970 970 | 0,44 0,53 0,93 1,15 2,70 3,13 | 235 260 400 440 640 710 | 1,8 2 2 2,2 2,3 2,5 |
АК 61-8 АК 62-8 АК 71-8 АК 72-8 АК 81-8 АК 82-8 АК 91-8 АК 92-8 | 4,5 7 10 14 20 28 40 55 | 700 700 700 700 710 710 720 720 | 0,24 0,28 0,40 0,50 0,90 1,10 2,60 3,25 | 145 160 235 260 400 440 640 710 | 1,8 1,9 1,8 1,9 1,9 2 2 2,2 |
Продолжение 2
Основные параметры короткозамкнутых электродвигателей трехфазного тока единой серии АО2
Тип двигателя | Мощность, кВт | Частота вращения, мин-1 | Момент инерции, кг·м2 | Масса, кг |
АО2-11-2 АО2-12-2 АО2-21-2 АО2-22-2 АО2-31-2 АО2-32-2 | 0,8 1,1 1,5 2,2 3 4 | 2815 2815 2860 2860 2880 2880 | 0,0013 0,0015 0,0028 0,0035 0,0082 0,0100 | 17,5 19,2 23,5 27,5 35 43 |
АО2-41-2 АО2-42-2 АО2-51-2 АО2-52-2 АО2-61-2 АО2-62-2 АО2-71-2 | 5,5 7,5 10 13 17 22 30 | 2900 2900 2900 2900 2900 2900 2900 | 0,019 0,025 0,038 0,045 0,075 0,110 0,140 | 62 74 95 110 128 144 166 |
АО2-11-4 АО2-12-4 АО2-21-4 АО2-22-4 АО2-31-4 АО2-32-4 АО2-41-4 | 0,6 0,8 1,1 1,5 2,2 3 4 | 1360 1360 1400 1400 1430 1430 1450 | 0,0018 0,0021 0,0042 0,0055 0,0100 0,0125 0,023 | 17,5 19,2 23,5 27,5 35 43 62 |
Примечание. Для всех двигателей Ммах/Мном = 2,2
Приложение 3
Продолжение приложения 3
Приложение 4
Приложение 5
Размеры клиновых ремней (по ГОСТ 1284-98)
Приложение 6
Значения N 0 для клиновых ремней
Приложение 7
Значения коэффициента k1
Значение коэффициента k 2
МЕТОДИЧЕСКОЕ ПОСОБИЕ
по выполнению практических работ
Дисциплина: ОП.02 Техническая механика
Раздел 3 Детали машин
Согласовано: | Разработал: |
Руководитель методической службы ____________ Н.В. Дмитриева «___»__________2020 | Преподаватель ____________ А.Н. Иванов «___»__________2020 |
Председатель ПЦК 23.02.04 ____________ А.Н. Иванов «___»__________2020 |
2020
Рецензенты:
Преподаватель ГАПОУ БАСК__________С.Г. Кольцова
Директор ООО «Автомастер» __________ С.П. Белоусов Содержание
Введение | 4 |
Практическая работа № 8 Расчет разъемных и неразъемных соединений на срез и смятие. | 6 |
Практическое занятие № 9 Кинематический и силовой расчет передачи. | 12 |
Практическое занятие № 10 Расчет зубчатой передачи. | 17 |
Практическая работа № 11 Расчет передачи винт-гайка. | 23 |
Практическая работа № 12 Расчет клиноременной передачи. | 24 |
Практическая работа № 13 Расчет цепной передачи. | 26 |
Практическая работа № 14 Расчет вала на прочность по эквивалентным напряжениям | 27 |
Список литературы | 28 |
Приложения | 29 |
Введение
Методическое пособие по выполнению практических работ по общепрофессиональной дисциплине ОП.02 Техническая механика» предназначено для обучающихся по специальности 23.02.04 Техническая эксплуатация подъемно-транспортных, строительных, дорожных машин и оборудования (по отраслям).
Дисциплина ОП.02 Техническая механика состоит из трех разделов: «Теоретическая механика», «Сопротивление материалов» и «Детали машин». По рабочей программе учебной дисциплине предусмотрено на практические занятия 28 часов. И охватывают все разделы и темы дисциплины ОП.02 Техническая механика.
Данное методическое пособие способствует освоению обучающимися умений и знаний, а так-же формированию общих и профессиональных компетенций:
Код ПК, ОК | Умения | Знания |
ОК 01, ОК 02, ОК 04, ПК 2.3, ПК 3.2, ПК 3.3, | - выполнять основные расчеты по технической механике; - выбирать материалы, детали и узлы, на основе анализа их свойств, для конкретного применения; - выполнять испытания материалов и конструкций | - основы теоретической механики, сопротивления материалов, деталей машин; - основные положения и аксиомы статики, кинематики, динамики и деталей машин; - элементы конструкций механизмов и машин; - характеристики механизмов и машин |
Методическое пособие позволяет выполнять практические работы, как в рамках учебного урока, так и дома, самостоятельно. Для этого в приложениях приведена вся необходимая справочная информация: Параметры электродвигателей, Механические характеристики сталей, Размеры и значения мощности и коэффициентов для клиновых ремней. Для более полного ознакомления с темами учебного курса приведен список рекомендуемой литературы.
Работа выполняется обучающимися в соответствии с индивидуальным вариантом, в ученической тетради для практических работ или с использованием ПК. Вариант состоит из двух цифр – порядкового номера обучающегося в журнале. По одной цифре выбирается схема, а по другой числовые значения параметров. После выполнения каждая практическая работа защищается преподавателю. Схемы вычерчивается с помощью карандаша и линейки с соблюдением масштаба.
При оформлении работы необходимо соблюдать принятые обозначения и последовательность записей, руководствуясь действующим стандартом предприятия и требованиями ЕСКД.
Раздел 3 Детали машин
Практическая работа № 8
Расчет разъемных и неразъемных соединений на срез и смятие
Цель работы:
1 Ознакомиться с методикой расчета шпоночных соединений
2 Научиться рассчитывать и подбирать шпонку под конкретную нагрузку
Порядок выполнения задания:
1 Ознакомиться с основными положениями подбора шпоночных соединений
2 Выполнить индивидуальное задание
3 Ответить на контрольные вопросы
Общие положения:
Основным критерием работоспособности шпоночных соединений является прочность. Шпонки выбирают по таблицам ГОСТов в зависимости от диаметра вала, а затем соединения проверяют на прочность. Размеры шпонок и пазов подобраны так, что прочность их на срез и изгиб обеспечивается, если выполняется условие прочности на смятие, поэтому основной расчет шпоночных соединений – расчет на смятие. Проверку шпонок на срез в большинстве случаев не производят.
Соединения призматическими шпонками (рисунок 1) проверяют по условию прочности на смятие, на смятие рассчитывают выступающую из вала часть шпонки:
, (1)
где Ft - сила, передаваемая шпонкой:
Ft= 2·103 T/ d, (2)
АСМ - площадь смятия
При высоте фаски шпонки f = 0,06h площадь смятия:
, (3)
следовательно,
, (4)
где Т - передаваемый момент, Н·м;
d - диаметр вала, мм;
h, t1 - высота шпонки и глубина паза на валу, мм (см. таблицу 1)
[ ]см — допускаемые напряжения смятия (см. ниже);
lp — рабочая длина шпонки; для шпонок с плоскими торцами lp=l, со скругленными торцами lp=l – b
При проектировочных расчетах после выбора размеров поперечного сечения шпонки b и h по таблице 1 определяют расчетную рабочую длину lp шпонки.
Длину шпонки со скругленными торцами l=lp+b или плоскими торцами l=lp назначают из стандартного ряда (см. таблицу 1).
Длину ступицы lСТ принимают на 8...10 мм больше длины шпонки. Если длина ступицы больше величины 1,5d, то шпоночное соединение целесообразно заменить на шлицевое или соединение с натягом.
Рисунок 1 Расчетная схема соединения призматической шпонкой.
Соединения сегментными шпонками (рисунок 2) проверяют на смятие:
, (5)
где l=lp - рабочая длина шпонки;
(h – t1)- рабочая глубина в ступице.
Сегментная шпонка узкая, поэтому в отличие от призматической ее проверяют на срез.
Условие прочности на срез:
, (6)
где b — ширина шпонки;
[ ]ср — допускаемое напряжение на срез шпонки (см. ниже).
Таблица 1 Размеры шпонок призматических по ГОСТ 23360-78
Диаметр вала d, мм | Сечение шпонки b | Глубина паза, мм | Радиус закругления r или фаска s | ||
Вала t1 | Втулки t2 | ||||
10…12 12…17 17…22 22…30 | 4 ![]() ![]() ![]() ![]() | 2,5 3 3,5 4,0 | 1,8 2,3 2,8 3,3 | 0,08-0,16 0,16-0,25 0,16-0,25 0,16-0,25 | |
30…38 38…44 44…50 50…58 58…65 | 10 ![]() ![]() ![]() ![]() ![]() | 5,0 5,0 5,5 6,0 7,0 | 3,3 3,3 3,8 4,3 4,4 |
0,25-0,4 | |
65…75 75…85 85…95 95…110 110…130 | 20 ![]() ![]() ![]() ![]() ![]() | 7,5 9,0 9,0 10,0 11,0 | 4,9 5,4 5,4 6,4 7,4 |
0,4-0,6 | |
Примечания 1 Длины шпонок выбирают из ряда 6, 8, 10, 12, 14, 16, 18, 20, 25, 28, 32, 36, 40, 45, 50, 56, 63, 70, 80, 90, 100, 110, 125, 140, 160, 180, 200, 250. 2 Материал шпонок – сталь чистотянутая для шпонок с | |||||
Рисунок 2 Соединение сегментной шпонкой
1- винт установочный, 2 – кольцо замковое пружинное
Стандартные шпонки изготовляют из специального сортамента среднеуглеродистой чистотянутой стали с
600 Н/мм2 - чаще всего из сталей 45, Ст6.
Допускаемые напряжения смятия для шпоночных соединений при
стальной ступице [ ]см = 130...200 Н/мм2; при чугунной — [
]см= 80...110 Н/мм2;
Большие значения принимают при постоянной нагрузке, меньшие - при переменной и работе с ударами.
При реверсивной нагрузке [σсм] снижают в 1,5 раза. Допускаемое напряжение на срез [ ср] = 70...100 Н/мм2.
Большее значение принимают при постоянной нагрузке.
Перепад диаметров ступеней вала с призматическими шпонками назначают из условия свободного прохода детали большего посадочного диаметра d2 без удаления шпонки из паза на участке меньшего диаметра d1 (рисунок 3).
Рисунок 3 Ступенчатый вал с одинаковыми шпонками
При наличии нескольких шпоночных пазов на валу их располагают на одной образующей (рисунок 3).
Из удобства изготовления рекомендуется для разных ступеней одного и того же вала назначать одинаковые по сечению шпонки, исходя из ступени меньшего диаметра (рисунок 3)
Прочность шпоночных соединений при этом оказывается вполне достаточной, так как силы Ft1 и Ft2 действующие на шпонки, составляют:
Ft1= 2·103 T/ d1, (7)
Ft2= 2·103 T/ d2, (8)
но d2> d1 следовательно, Ft2< Ft1
При необходимости двух сегментных шпонок их ставят вдоль вала в одном пазу ступицы. Постановка нескольких шпонок в одном соединении сильно ослабляет вал, поэтому рекомендуется перейти на шлицевое соединение.
Пример 7 Расчет шпоночного соединения
Выбрать тип стандартного шпоночного соединения стального зубчатого колеса со стальным валом (рисунок 4) и подобрать размеры шпонки. Диаметр вала d = 45 мм. Соединение передает вращающий момент Т= 210 Н.м при спокойной нагрузке.
Для соединения вала с колесом принимаем призматическую шпонку со скругленными концами (исполнение 1).
Размеры шпонки и паза на валу принимаем по таблице 12 для диаметра вала d = 45 мм принимаем размеры сечения шпонки b = 14 мм; h = 9 мм. Глубина паза на валу t1= 5,5 мм.
Рисунок 4 Соединения призматическими шпонками
Допускаемое напряжение для стальных деталей соединения при спокойной нагрузке [ ]см=150 Н/мм2
Расчетную длину шпонки, мм, находим из формулы (5):
Длина шпонки, мм:
l = lp + b = 21 + 14 = 35
Согласуя со стандартом принимаем l=36 мм. (см. таблицу 1)
Длина ступицы колеса, мм:
l ст = l +10 мм = 36 + 10 = 46 < 1,5d что допустимо.
Задание к самостоятельной работе
Спроектировать стандартное шпоночное соединение стального зубчатого колеса со стальным валом (рисунок 4) и подобрать размеры шпонки. Диаметр вала d, мм. Соединение передает вращающий момент Т, Н.м. Исходные данные принять из таблицы 13 согласно номеру варианта
Таблица 2 Исходные данные
№ | d, мм | T, Н.м | [σ]СМ, Н/мм2 | Исполнение шпонки | № | d, мм | T, Н.м | [σ]СМ, Н/мм2 | Исполнен |
|
|
Наброски и зарисовки растений, плодов, цветов: Освоить конструктивное построение структуры дерева через зарисовки отдельных деревьев, группы деревьев...
Поперечные профили набережных и береговой полосы: На городских территориях берегоукрепление проектируют с учетом технических и экономических требований, но особое значение придают эстетическим...
Биохимия спиртового брожения: Основу технологии получения пива составляет спиртовое брожение, - при котором сахар превращается...
Адаптации растений и животных к жизни в горах: Большое значение для жизни организмов в горах имеют степень расчленения, крутизна и экспозиционные различия склонов...
© cyberpedia.su 2017-2024 - Не является автором материалов. Исключительное право сохранено за автором текста.
Если вы не хотите, чтобы данный материал был у нас на сайте, перейдите по ссылке: Нарушение авторских прав. Мы поможем в написании вашей работы!