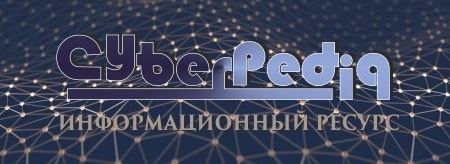
Индивидуальные очистные сооружения: К классу индивидуальных очистных сооружений относят сооружения, пропускная способность которых...
Биохимия спиртового брожения: Основу технологии получения пива составляет спиртовое брожение, - при котором сахар превращается...
Топ:
Марксистская теория происхождения государства: По мнению Маркса и Энгельса, в основе развития общества, происходящих в нем изменений лежит...
Когда производится ограждение поезда, остановившегося на перегоне: Во всех случаях немедленно должно быть ограждено место препятствия для движения поездов на смежном пути двухпутного...
Определение места расположения распределительного центра: Фирма реализует продукцию на рынках сбыта и имеет постоянных поставщиков в разных регионах. Увеличение объема продаж...
Интересное:
Финансовый рынок и его значение в управлении денежными потоками на современном этапе: любому предприятию для расширения производства и увеличения прибыли нужны...
Влияние предпринимательской среды на эффективное функционирование предприятия: Предпринимательская среда – это совокупность внешних и внутренних факторов, оказывающих влияние на функционирование фирмы...
Берегоукрепление оползневых склонов: На прибрежных склонах основной причиной развития оползневых процессов является подмыв водами рек естественных склонов...
Дисциплины:
![]() |
![]() |
5.00
из
|
Заказать работу |
|
|
Схема предусматривает, что бумага для гофрирования вырабатывается из композиции: 50% лиственной полуцеллюлозы и 50 % химико-термомеханическая массы с нейтральной проклейкой. Готовая продукция выпускается в упакованных рулонах.
Бисульфитная полуцеллюлоза из приемного бассейна (24) поступает на размол на дисковой мельнице МДС-33 (20), где размалывается до 32 0ШР, затем насосом перекачивается в композиционный бассейн (15), куда также подается химико-термомеханическая масса. Из композиционного бассейна масса перекачивается в машинный бассейн (14), куда подается крахмал для придания жесткости бумажному полотну. Затем масса перекачивается в бак постоянного уровня (БПУ) (13), который предназначен для поддержания постоянного напора массы, перелив из БПУ возвращается в машинный бассейн. Из БПУ волокнистая суспензия подается в смесительный насос (12) откуда масса поступает для очистки от тяжелых включений на вихревые очистители (11). Очистка производится в две ступени. После очистки масса поступает в смесительный насос (12), туда же подается клей АКД эмульсия Ультрасайз 200 для нейтральной проклейки.
Используем нейтральную проклейку бумажной массы. В качестве агентов для нейтральной проклейки бумаги доминирующее положение занимают синтетические проклеивающие материалы, в частности димеры алкилкетенов (АКД).
Смесительным насосом масса направляется для очистки в узлоловители закрытого типа УЗ - 15(10) первой ступени.
Очищенная масса с первой ступени очистки поступает в напорный ящик, а отходы сортирования поступают на вторую ступень очистки на плоские вибрационные сортировки СВО-01(37). Отсортированная масса со второй ступени очистки поступает в напорный ящик,а отходы уходят в гидроразбиватель типоразмера НG-45(35).
|
Очищенная масса после узлоловителей с концентрацией 0,98 % поступает в напорный ящик(9),
Из напорного ящика разбавленная волокнистая масса непрерывным потоком вытекает на бесконечную сетку, формование полотна происходит между двумя сетками. На сеточном столе масса теряет большую часть содержащейся в ней воды. Двух-сеточное формование улучшает процесс обезвоживание которе происходит на гидропланках и отсасывающих ящиках. Сухость полотна после регистровой части (пакеты гидропланок) (8) составляет 3,5 %. Сухость полотна после сосунной части (отсасывающие ящики) (7) составляет 14 %. Оборотная вода от регистровой части машины по желобам и сливам отводится в сборник регистровых вод (36). Оборотная вода от отсасывающих ящиков отводится в сборник сосунных вод (24).
После отсасывающих ящиков бумага содержит еще сравнительно много влаги и поэтому не обладает прочностью, достаточной для передачи бумажного полотна в прессовую часть машины. Поэтому бумажное полотно вместе с сеткой пропускают еще через гауч-вал(6), где сухость бумажного полотна возрастает до 22 %. Диаметр вала 1120 мм, длина вала 6800 мм. Перед гауч-валом имеются две краевые отсечки (водяные ножи) - для обрезания неровных кромок сырого бумажного полотна, и одна переводная, используемая для разрезания бумажного полотна при заправке бумаги. Между отсасывающими ящиками над сеткой установлен легкий ровнительный валик, который применяется для улучшения просвета бумаги и уплотнения ее структуры.
Далее бумажное полотно с помощью пересасывающего вала передается в прессовую часть (5) бумагоделательной машины, где происходит дальнейшее обезвоживание. Прессовая часть состоит из пересасывающего съемного вала, прямого двухвального, трехвального и пресса с удлиненной зоной прессования. Пересасывающий съемный вал имеет общее сукно с верхним валом прямого двухвального пресса. По этому сукну полотно передается с сеточной части в трехвальный пресс, в первую зону прессования между валом с глухими отверстиями и отсасывающим валом. Затем во вторую зону между отсасывающим и гладким валами, далее с помощью воздушной заправки переходит на пресс с удлиненной зоной прессования, а потом в сушильную часть. Сухость полотна после прессовой части 43%. При отжиме влаги на прессах изменяется ряд свойств бумаги: повышается объемный вес, снижается пористость, воздухопроницаемость, впитывающая способность, увеличивается механическая прочность по сопротивлению разрыву, излому и продавливанию.
|
После прессовой части мокрое бумажное полотно поступает в сушильную часть (4)бумагоделательной машины, где удаляется оставшаяся после отжима на прессах влага. Сушильная часть бумагоделательной машины состоит из вращающихся, обогреваемых изнутри паром и расположенных обычно в два ряда сушильных цилиндров. Движущееся бумажное полотно прижимается к нагретой поверхности цилиндра при помощи сушильных сеток, улучшающих теплопередачу и предотвращающих коробление и сморщивание поверхности бумаги при сушке.
Размеры сушильной поверхности, число цилиндров и скорость движения бумажной ленты выбирают с таким расчетом, чтобы бумага, пройдя сушильную часть машины, успела высохнуть до сухости бумажного полотна, согласно ГОСТу 7377-85 на готовую продукцию.
Сушильная часть машины разделена по пароснабжению на группы:
I группа первичного пара - цилиндры с 24 по 52;
II группа вторичного пара: - цилиндры с 13 по 23;
цилиндры с 53 по94;
III группа третичного пара - цилиндры с 1 по 12.
Параметры пара по группам:
I группа, давление 0,09 МПа;
II группа, давление 0,21 МПа;
III группа, давление 0,34 МПа.
Пар из главного паропровода после РОУ, с постоянным давлением 4,2 кПа и температурой 150 0C, поступает в I сушильную группу по пару с 9 по 28 сушильные цилиндры. Паровоздушная смесь с I сушильной группы и сукносушителей поступает в 1-ый пароотделитель, из которого пар подается во II группу по пару, а конденсат - в сборник. В пароотделителе уровень поддерживается автоматически. Во II группу по пару врезан первичный пар для создания перепада давления и поддержания температурного графика сушки.
Со II сушильной группы по пару конденсат попадает во 2-ой пароотделитель и самотеком - в сборник, пар же подается в III группу по пару.
|
Паровоздушная смесь с III сушильной группы поступает в 3-ий водоотделитель, пары вскипания из последнего поступают на конденсатор, а конденсат возвращается снова в водоотделитель. Из 3-его водоотделителя конденсат подается в бак конденсата.
Для удаления воздуха из конденсата и достижения малого давления в конденсаторопроводе III группы, чем достигается соответствующая температура первых цилиндров, 3-ий водоотделитель соединен с вакуум-насосом бумагоделательной машины. Конденсат из 1-ого конденсатоотделителя поступает во 2-ой конденсатоотделитель, далее в бак конденсата.
В конце сушильной части бумагоделательной машины установлены два холодильных цилиндра, для охлаждения и увлажнения бумажного полотна. Они делают бумажное полотно более мягким и эластичным, что важно для обработки в машинном каландре, предотвращают электризацию сухой бумаги при трении о валы каландра и при намотке. Сухость бумажного полотна после сушильной части 93 %.
Далее бумажное полотно поступает на мягкий каландр с пневмоприжимом (3). Здесь полотно приобретает особые свойства: паро-, водо- и жиронипроницаемость, улучшение печатных свойств, гладкости, блеска и внешнего вида. Каландр приводится в движение через нижний вал. Верхние валы вращаются за счет трения от нижнего вала.
Бумагоделательная машина завершается накатом (2) с устройством автоматической подачи тамбурных валиков, осуществляющим наматыванием бумаги в рулоны. При этом должна быть обеспечена равномерная и плотная намотка, что создает условия для хорошей сохранности бумаги при ее транспортировании, обработки и переработки.
Затем направляется на продольно-резательный станок (1). Рабочая ширина продольно-резательного станка 6300 мм, наибольший диаметр наматываемого рулона - 1200 мм. Прижим и опускание вала пневмогидравлический.
Сухой брак от машины перерабатывается в гидроразбивателе (35), который включается автоматически при обрывах на машине. Далее брак подмалывается на пульсационной мельнице (34), после которой размолотый брак поступает в бассейн брака (27).
Мокрый брак, непрерывно поступающий из гауч-мешалки (25), направляется на сгуститель мокрого брака (28), от которого без подмола направляется также в бассейн брака (27). Из бассейна брак через дозирующие устройства поступает на составитель композиции (15).
|
Схемой предусматривается максимальное использование оборотной воды. Регистровая вода собирается в сборнике и используется на разбавление массы в смесительном насосе. Необходимое количество массы во всасывающую линию смесительного насоса отбирается при помощи специальной дозирующей задвижки с электроприводом, имеющей дистанционное или автоматическое управление. Этой задвижкой регулируется вес 1 м2 бумаги.
Для стабильной работы смесительного насоса уровень воды в сборнике регистровой воды поддерживается постоянным, вследствие перелива избытка регистровой воды в соседний сборник - сборник избыточных вод. Часть регистровой воды подается на разбавление отходов до необходимой концентрации после вихревых очистителей первой и второй ступени.
Вода из отсасывающих ящиков собирается в сборнике сосунных вод (25). В свою очередь избыток воды из сборника сосунных вод переливается в сборник избыточных вод (28). В этот же сборник поступает вода, отходящая от сгустителя мокрого брака. Часть сосунной воды используется на разбавление отходов до необходимой концентрации после узлоловителей первой ступени и на разбавление мокрого брака в гауч-мешалке (25).
Оборотная вода из сборника избыточных вод расходуется в гидроразбивателе. Вся остальная избыточная оборотная вода направляется на флотационную ловушку (30) для улавливания волокна и наполнителя. Сюда же подается ПАА для лучшего улавливания мелкого волокна и наполнителя. Уловленное волокно возвращаются в основной поток производства. Они направляются в бассейн массы, откуда с концентрацией 4%, подаются на составитель композиции. Осветленная вода частично может быть использована на спрыски сетки.
Подача свежей воды предусматривается обычно туда, где оборотная вода по технологическим соображениям не может быть использована, например, на отсечку полотна на сеточном столе, на спрыски отсасывающих валов и сукномоек в прессовой и сушильных частях, в сальники и на заливку вакуум-насосов, в сушильные цилиндры, на охлаждение подшипников вспомогательного оборудования, а также на промывку оборудования. При наличии теплой воды от теплорегенерационной установки вентиляционной системы бумагоделательной машины ее направляют в сборник теплой воды, откуда она поступает для очистки на сеточном фильтре, а затем используется взамен свежей холодной воды для промывки сукон, на спрыски кромок, на отсечки, а также в других местах, где ее применение целесообразно.
|
|
Археология об основании Рима: Новые раскопки проясняют и такой острый дискуссионный вопрос, как дата самого возникновения Рима...
Особенности сооружения опор в сложных условиях: Сооружение ВЛ в районах с суровыми климатическими и тяжелыми геологическими условиями...
Кормораздатчик мобильный электрифицированный: схема и процесс работы устройства...
Папиллярные узоры пальцев рук - маркер спортивных способностей: дерматоглифические признаки формируются на 3-5 месяце беременности, не изменяются в течение жизни...
© cyberpedia.su 2017-2024 - Не является автором материалов. Исключительное право сохранено за автором текста.
Если вы не хотите, чтобы данный материал был у нас на сайте, перейдите по ссылке: Нарушение авторских прав. Мы поможем в написании вашей работы!